Видобуток нафти фонтанним способом
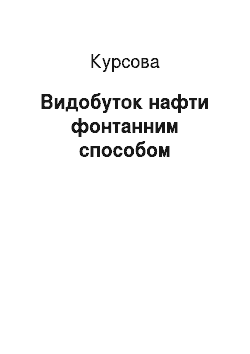
Парафіновідкладень В поясненні впливу магнітного поля на рухому середу є ряд гіпотез, які можна класифікувати на слідуючи три групи. Перша група, яка об'єднує більшість гіпотез, представляє собою дію магнітного поля на солі, які присутні в воді. Під впливом магнітного поля відбувається поляризація іонів і деформація, яка супроводжується зменшенням їх сольватації, що підвищує можливість їх… Читати ще >
Видобуток нафти фонтанним способом (реферат, курсова, диплом, контрольна)
МОіО України
Івано-Франківський національний технічний університет нафти і газу Курсова робота на тему: «Комплекс обладнання для видобутку нафти фонтанним способом»
Івано-Франківськ, 2001
Вступ Високими темпами нафтова промисловість почала розвиватися тільки в ХХ столітті, коли стали широко використовувати двигуни внутрішнього згорання, які потребують різноманітного палива і мастильних матеріалів. Особливо швидко почала розвиватися світова нафтова промисловість з тих пір, коли нафта і її продукти переробки стали використовуватись в якості сировини в нафтохімічній промисловості.
Нафта, газ і продукти їх переробки, на даному етапі становлення нашої держави, відіграють велику роль в розвитку економіки України. Тому темпам розвитку нафтової і газової промисловості постійно приділяється велика увага.
Незважаючи на різноманітні проекти по як найшвидшому забезпеченню України нафтою і газом, багатий досвід вітчизняної та зарубіжної промисловості.
1. Загальна частина
1.1 Аналіз комплексу обладнання для видобутку нафти фонтанним
способом Фонтанний спосіб експлуатації позволяє добувати із свердловин найбільшу кількість нафти при найменших затратах. Тому однією із головних задач при експлуатації свердловин цим способом є забезпечення можливості ділильного фонтанування свердловин, що зв’язане з раціональним використанням енергії пласта шляхом забезпечення високого ККД роботи фонтанного підйомника /3/.
Обладнання для експлуатації свердловин фонтанним способом складається з чотирьох основних частин: колони труб, обладнання низа колони, обладнання устя, тобто фонтанної арматури і обв’язки устьового обладнання, яке називається маніфольдами. Колона НКТ в деяких випадках оснащується клапанами-відсікачами або сідлами для установки вставних клапанів-відсікачів. Інколи в свердловини встановлюють ущільнювач.
Рідина і газ, які збираються ідуть із свердловини по НКТ і на усті відводяться арматурою в промислові комунікації /2/.
Устя закінченого буріння свердловини обладнано колонною головкою, яка з'єднує на поверхні закінчення обсадної колони і герметизує затрубний простір. На колоній головці кріпиться арматура для фонтанних свердловин. Основні параметри і типові схеми арматури вказані в ГОСТ 13 846–89.
Фонтанна арматура складається із трубної головки, фонтанної ялинки, запірних пристроїв з ручним, дистанційним і автоматичним керуванням, регулюючих приладів (дроселів) /4/.
Трубна головка монтується безпосередньо на колонній головці і призначена для підвищування одного чи двох рядів насосно-компресорних труб, герметизації на усті затрубного простору, а також для виконання технологічних операцій при освоєнні, експлуатації і ремонті свердловин. Трубна головка повинна позволяти подавати рідину чи газ в міжтрубний простір, контролювати тиск.
Колони підйомних труб підвішуються на різьбі і на клиновій підвісці.
Фонтанна ялинка монтується на трубній головці і призначається для направлення відібраних із свердловини рідин та газів в маніфольд, регулювання і контроль за роботою фонтанної свердловини, установці спеціальних приладів при спуску свердловинних приборів або скребків для очистки труб від парафіну, заміру тиску і температури середовища, а також для проведення різноманітних технологічних операцій.
Головні струни арматури закінчуються відвіднимі фланцями для кріплення до ліній маніфольда. На фланцях бокових відводів трубної і фонтанної ялинки передбачається отвори для подачі інгібіторів корозії і гідроутворення в затрубний простір і в стовбур ялинки.
Основними деталями і вузлами фонтанної арматури є: хрестовина 1, яка має два бокових відвода; трійник 2, який має один боковий відвід ;котушка чи перевідник 3; запірний пристрій 4, кран 5, манометр 6, дросель 7, відвідний фланець 8 /2/.
Хрестовина і трійник позволяють відводити рідину, яка добувається до маніфольду. На цих же деталях можна підвісити колону НКТ. Перевідник служить для підвішування НКТ і для переходу з одного розміру деталей арматури на інший.
Запірні пристрої служать для повного перекриття чи повного відкриття прохідного січення ствола чи відводу. Регулювання параметрів потоку відбувається за допомогою відкриття чи закриття замірного пристрою (дроселя). Дросель має корпус в який встановлено спеціальна чи замінна втулка з невеликим по діаметру отвором. Через отвір втулки проходить вся продукція свердловини. Підбором розміру отвору регулюється дебіт свердловини.
Допускається при необхідності додатково включати в фонтанну арматуру автоматичні запобіжні пристрої на бокових відводах ялинки, запірні пристрої з дистанційним керуванням на стволі ялинки, пристрої, які забезпечують можливість з'єднання свердловинного обладнання з наземною системою його керування /4/.
Деталі і вузли арматури з'єднуються між собою фланцями з ущільненням чи різьбою. Тому по цьому признаку фонтанна арматура поділяється на фланцеву і різьбову. Вертикальна, ствольна частина ялинки може мати відводи в одну сторону (через трійники) чи в дві сторони (через хрестовини). По цьому признаку фонтанна арматура поділяється на трійникового і хрестового типу.
Основні параметри арматури — діаметр прохідного січення стволової частини фонтанної ялинки і робочі тиски, на які розрахована фонтанна арматура.
В ГОСТі 13 846−89 встановленні робочі тиски Р (МПа): 14, 21, 35, 70, 105, 140, а також прохідні січення Dу (мм): 50, 65, 80, 100, 150.
У трійникової арматури при двох бокових відводах, верхній є основним робочим відводом. При виході його деталей із ладу, закривається стволовий запірний пристрій і рідина чи газ, направляється по нижньому відводу без зупинки роботи свердловини. Це зручно при необхідності ремонту верхнього відводу. Але розташування відводів по вертикалі збільшує висоту арматури, що ускладнює обслуговування фонтанної арматури.
Трійникову арматуру рекомендується використовувати при низьких і середніх тисках.
Для середніх і високих тисків ГОСТ рекомендує приймати хрестову арматуру /2/.
В арматурі приміняються слідуючи запірні пристрої: засувки клинові, засувки прямоточні, крани, вентилі.
Запірні пристрої перших трьох типів — основні в стволовій і відвідній частинах арматури. Вентилі встановлюються перед манометрами. Основна перевага клинової засувки — її простота. Але при відкритій засувці у прохідного каналу образується вихрові токи, втрати напору і можливість відкладення в ньому солей, парафіну і піску. При цьому ущільнюючі поверхні біля корпуса і клина інтенсивно омиваються з свердловини, що приводить до їх посиленої корозії.
Цих недоліків немає у прямоточній засувці. Клинове ущільнення у ній замінено шиберним з двома клапанами чи одношиберним.
Арматура устя свердловини з'єднується з промисловими трубопроводами маніфольдами, які складені з типових вузлових зборок. Маніфольди мають запірні пристрої, регулюючий штуцер, запобіжні клапани, хрестовини, трійники, вентилі для скидання тиску і приєднання приборів.
Внаслідок технічних умов експлуатації фонтанної арматури її хрестовини, трійники, перевідники, фланці і корпусні деталі запірних пристроїв виконуються тільки із сталі. Ущільнення між фланцями арматури виконується стальними кільцями.
Поширені литті і зварні деталі арматури. Приміняються сталі марок: Сталь 45, 40ХЛ, 40ХНЛ і інші леговані сталі. Для ущільнюючих кілець приміняються сталі марок: 08КП, Сталь 20, 30, 40 і леговані сталі.
Через втулки дроселів продукція свердловини проходить з великою швидкістю. При цьому продукція свердловини має великий вміст піску та агресивні рідини. Тому втулки виконуються із загартованих сталей та твердих сплавів /2/.
1.2 Опис фонтанної арматури на 70МПа робочого тиску Хрестовинна арматура для свердловин, які немають вмісту абразиву, з прохідним (умовним) отвором 50 мм, розрахована на робочий тиск 70МПа. Ялинка арматури має два змінних штуцера, що позволяє швидко їх замінити. Арматура розрахована, як на однорядний, так і на двохрядний підйомник.
Хрестова арматура значно нижча трійникової, що полегшує її обслуговування.
До недоліків хрестової арматури відносять те, що при виході із ладу одного із (отворів) відводів необхідно закривати нижній стволовий запірний пристрій та відповідно зупиняти свердловину /3/.
Фонтанна арматура на робочий тиск 70МПа виготовляється з прямоточними засувками з автоматичною подачею мастила по схемі 6 ГОСТ 13 846–89. в якості запірного пристрою приміняюєься прямоточна засувка типу ЗМАД і ЗМАДП з двопластинчатим шибером з автоматичною подачею мастила в затвор.
В залежності від типу арматура комплектується засувками з ручним, дистанційним і автоматичним керуванням, типу АФ6аВ — засувка з ручним, дистанційним і автоматичним керуванням; типу АФ6А — засувка з ручним і автоматичним керуванням; типу АФ6 — засувка з ручним керуванням. Засувки з дистанційним і автоматичним керуванням пневмоприводні (типа ЗМАДГ), вони мають дублююче ручне керування /4/.
Засувка прямоточна ЗМАД-50*700 з висувним зрівноваженим шпіндем, призначена для монтування в обладнання устя високодебітних нафтових свердловин.
Засувка складається із наступних основних деталей: корпус 1, в якому встановлюються дві направляючі щілини 4, які мають резервуари для спеціального ущільнюючого мастила і систему каналів для доступу мастила до ущільнюючих поверхонь.
Між направляючими щілинами встановлюються дві плашки 8, які зібрані з шістьох пружин і запобіжною фторопластовою втулкою 12. плашки мають спеціальні пази для з'єднання зі шпинделем 14 і штоком 9.
Шпиндель встановлюється в корпусі сальника 6 в підшипниках кочення, які зібрані на втулці різьбовій за допомогою кришки підшипника 20.
На шестигранник ходової гайки встановлюється маховик 22, який закріплюється кожухом 13.
Герметичність затвора засувки підвищується за рахунок застосування спеціального ущільнюючого мастила, яке в момент виникнення утічок подається до поверхні затвора автоматично за рахунок тиску середовища в корпусі засувки. Через два зворотних клапана в корпусі засувки резервуари в щілинах заповнюються мастилом.
При закритому положенні засувки тиск середовища в корпусі діє через поршень23, на мастило, яке заповнює кільцеву ї циліндричні канавки на щоці. При відкритому положенні засувки поршень із мастилом знаходиться в зрівноваженому положенні.
Через зворотний клапан 3, який розміщений в дні, корпус заповнюється мастилом ЛЗ-162, яке запобігає накопиченню у внутрішній частині грязі і робочого середовища. В випадку проникнення середовища в манжети 27, ущільнююче шпиндель і контргайки через зворотній клапан 3 нагнітається ущільнююча паста для ліквідації пропускання середовища /12/.
Засувка типу ЗМАДП з пневмоприводом відрізняється від засувки з ручним керуванням привідної частиною. Привідна частина складається із пневмоциліндра і дублюючого ручного керування, яке служить для керування засувкою у випадку відказу пневмосистеми. Електричний сигнал поступає з пульта керування на клапан пневмоприводу, клапан спрацьовує і газ під тиском поступає в верхню чи нижню площину пневмоциліндра засувки, при цьому засувка відкривається або закривається. Пневмопривод монтується безпосередньо на засувці. Для його живлення використовують повітря чи азот /3/.
Регулюючі дроселі позволяють безступенево регулювати тиск на виході фонтанної свердловини за рахунок осьового переміщення шпинделя 7 дроселя з насадкою 9, який входить в гніздо. Із-за змінного профілю насадки площа кільцевого отвору між гніздом і насадкою при переміщенні шпинделя змінюється від 3 до 35 мм, що позволяє регулювати розхід рідини чи газу.
При агресивних середовищах і великих розходах рідини насадка шпинделя і гніздо дроселя швидко зношуються. Для підвищення зносостійкості цих деталей вони виготовляються із спеціальних матеріалів. Однак і це не виключає необхідності в частих замінах регулюючого дроселя. Тому в подібних умовах приміняють змінні, втулкові дроселі з різними діаметрами отворів, які при зносі поверхні отвору знімаються з фонтанної арматури і замінюються новими /4/.
2. Спеціальна частина
2.1 Методи боротьби з відкладанням солей і парафіну при видобутку
флюїду Методи запобігання солевідкладеннь прийнято поділяти на фізичні, хімічні і технологічні /7/.
До технологічних способів можуть бути віднесені вибір води для заводнення продуктивних пластів, регулювання профілю в нагнітальних свердловинах, усунення порушень в цементному кільці і обсадної колоні, примінення роздільного відбору і збору рідини тощо.
До фізичних методів попередження відкладення солей і парафінів можуть бути віднесені механічна очистка, обробка рідини чи газу магнітним полем. Механічна очистка виконується за допомогою різних машин і механізмів (приспосіблень). Робочий інструмент машини-свердло і щітки, які обертаються зі швидкістю 200−250об/хв., при цьому в трубі циркулює рідина.
Головні недоліки цього способу є:
складність, дороговізна і велика кількість обладнання;
необхідність частого спускання машини в свердловину при інтенсивному соле і парафіновідкледенні;
довга тривалість очистки, тобто свердловину приходиться глушити;
суть хімічного методу заключається в закачці в свердловину хімічних інгібіторів. Інгібітори закачуються в затрубний простір за допомогою дозіруючих приспосіблень. Так наприклад для боротьби з відкладенням солей використовується інгібітори марки ИСБ-1, SP-181, ДПФ-1, для боротьби з парафіновідкладеннями — ХТ-48.
До недоліків хімічного методу слід віднести:
необхідна наявність складних дозіруючих пристроїв, які встановлюються на усті;
дороговізна окремих хімічних реагентів;
чутливість реагентів до зміни температури.
Недоліки приміняємих методів попередження і ліквідації соле і парафіноутворень в свердловині приводить до необхідності пошуку більш сучасних методів для забезпечення експлуатації родовищ без відкладення солей і парафінів.
2.2 Суть магнітного способу боротьби проти солеі
парафіновідкладень В поясненні впливу магнітного поля на рухому середу є ряд гіпотез, які можна класифікувати на слідуючи три групи. Перша група, яка об'єднує більшість гіпотез, представляє собою дію магнітного поля на солі, які присутні в воді. Під впливом магнітного поля відбувається поляризація іонів і деформація, яка супроводжується зменшенням їх сольватації, що підвищує можливість їх збільшення і в підсумку — утворення центрів кристалізації /6/.
По другій групі планується дія магнітного поля на приміси води, яка знаходиться у холодному стані.
Третя група об'єднує уявлення про можливість впливу магнітного поля на структуру води. Цей вплив, з однієї сторони може викликати зміну і агресію молекул води, а з другої - нарушити орієнтацію іонів водню в молекулах.
Під дією магнітного поля (декілька) небагато змінюється магнітне сприйняття водних розчинів, їх електропровідність і в’язкість. Відрізняється екстремальна залежність властивостей вод напруженні магнітного поля. Багато неорганічних і органічних матеріалів краще розтворяються в омагніченому водному розчині. Омагнічена вода слабше зношує більшість поверхонь.
Магнітне поле дає суттєвий вплив на кінетику процесів кристалізації, сприяючі масовому зараженню центрів кристалізації і в ряді випадків, утворенню кристалів з сильно розвинутою поверхневою структурою /9/. Ця обставина і служить в теперішній час, головним чином примінення магнітної обробки води в промисловій технології.
Суть магнітного методу заключається в тому, що нафтогазоносна рідина з визначеною швидкістю пропускається через пристрій, в якому створюється магнітне поле. В результаті дії магнітного поля рідина поляризується, втрачається здатність відкладати солі в вигляді осадків на стінках нафтопромислового обладнання, а виділяє ці солі у вигляді малодисперсних частинок «шлама».
Метод запобігання солевідкладень з використанням постійних магнітів запропонований АзНДПІнафтою.
В теперішній час розроблено декілька магнітних пристроїв. Цим питанням займається також УкрНДІгаз і ПечорНДПІнафта. Не дивлячись га деякі позитивні результати випробувань в деяких нафтодобувних районах, магнітні пристрої цих конструкцій не знайшли широкого застосування для попередження відложень. Очевидно, що основна причина в тому, що застосування магнітних пристроїв не запобігає повній боротьбі з солевідкладеннями на всьому шляху руху рідини в нафтопромисловому обладнанні. Оберігається лише невелика ділянка обладнання після встановлення установки магнітного пристрою.
2.3 Опис запропонованої конструкції омагнічуючого пристрою Особливістю розробленого пристрою /9/ є оригінальна конструкція проточної частини, яка забезпечує багатократну обробку нафти полем постійних магнітів.
Висока ефективність магнітної обробки досягається установкою в проточній частині пристрою шнека і гвинтовій частині, під дією якої прокачувальна рідина набирає гвинтовий рух, що збільшує час і тривалість в магнітному полі.
Омагнічуючий прилад (рис. 3.1) має циліндричний корпус 2, в якому встановлена магнітна система, яка складається із розміщених на шнеку 5 постійних магнітів 7, полюсних наконечників 4, упорів 3. Елементи магнітної системи фіксуються на шнеці гайкою 8. Ззовні магнітної системи встановлюється гвинтова стрічка 6. Магнітна система утримується в корпусі затискною гайкою 1. Постійний магніт 7, встановлюється однойменними полюсами один до одного.
Таке розміщення магнітних елементів забезпечує багаторазову обробку нафтового потоку і високу стабільність магнітних властивостей.
В розробленому магнітному пристрої використані керамічні магніти, які випускаються серійно, марки М22 РА220 по ОСТ 11 707,023−81/2, які мають високі магнітні властивості.
Зміна магнітних властивостей в часі для даного матеріалу магнітів практично відсутня. Для зниження розсіювання магнітного потоку плюсні наконечники виготовляються із низьковуглицевої сталі. Нафтовий потік при вході в пристрій розділюється на два потоки, один із яких рухається всередині магнітної системи по шнеку, а другій по гвинтовій стрічці.
3. Розрахункова частина
3.1 Розрахунок засувки ЗМАД-80*700
Дані для розрахунку:
Робочий тиск, Рр = 700кгс/см2 = 70МПа;
Умовний перехід Dу = 80 мм = 0,08 м;
Клас герметичності - 1;
Затвор засувки повинен бути герметичним в діапазонах тисків від 0 до 700атм.
Розрахунок зроблений по Молчанову Г. В., Молчанову А. Г. «Машины и оборудование для добычи нефти и газа» — М.: Недра, 1984.
Визначення зусиль, які діють на шпиндель:
Q = Q1 + 2Q2;
де Q1 — зусилля тертя об шків в кінці закриття і початку відкриття засувки;
В цей момент площина дії тиску, а відповідно і зусилля тертя будуть найменшими.
Q2 — сила тертя в сальнику;
Зусилля тертя плашок об щоки в кінці закриття засувок:
Q1 = (0,785D12Рр + 2Qкр) f;
де D1 — діаметр окружності канавки;
D1 = 90 мм = 0,09 м;
f — коефіцієнт тертя (кочення) спокою;
f = 0,15;
Qкр — граничне зусилля;
Qкр = F*q;
деF — площа контакту плашок, при закритому затворі засувки, F = 96 см²;
q — питомий тиск, який створюється пружинами на ущільнюючих поверхнях затвора, q = 25кгс/см2 = 2,5МПа;
Qкр = 96*2,5 = 240кгс = 2400Н
Q1 = (0,785*9,02 700 + 2*240)*0,15 = 6750кгс
Q1 = 67,5кН Сила тертя в сальнику:
Q2 = ?*dе*S*р;
де? — коефіцієнт тертя манжет при висоті комплекту манжет 18 мм (4 манжети),? = 0,2;
S = (Dме-dе)*0,5 = (6,0−4,0)*, 05 = 0,01 м;
деDме — діаметр манжет, Dме = 6,0 см = 0,06 м;
dе — діаметр шпинделя, dе = 4,0 см = 0,04 м;
Q2 = 0,2*4,0*1*700 = 560кгс = 5600Н;
Зусилля, яке діє на шпиндель:
Q = 6750 + 2*560 = 7870кгс = 78 700Н Враховуючи силу тертя між стінкою циліндра і поршнем, приймаємо:
Q = 7000кгс = 70 000Н
3.1.1 Визначення діаметра різьби шпинделя Трапецеєвідна різьба розраховується на стиск і кручення по формулі ЦКБА (центрального конструкторського бюро автоматизації):
де[?]пр — допустиме приведене напруження;
S — крок різьби;
Для сталі 40Х межа текучості ?т = 6700кгс/см2 = 670Мпа, при коефіцієнті запасу n = 3,
[?]пр = ?т/n = 6700/3 = 2233кгс/см2 = 223,3МПа к — коефіцієнт, який залежить від коефіцієнта тертя в різьбі, при f = 0,1 к = 1,17;
Приймаємо різьбу трапецеєвидну Тр38*6 по ГОСТу 9484−80:
d = 38 мм, d1 = 30 мм, dср = 35 мм, S = 6 мм
3.1.2 Визначення крутного моменту на маховику Крутний момент на маховику визначаємо за формулою:
Мкр = Мр + Мп;
Момент тертя в різьбі:
Мр =Q*tg (? + p)*dср/2
При коефіцієнті тертя f = 0,1
р = arctg f = 5?43'
? = arctg S/(?dср) = 3?8'
Мр =7870*tg (3?8' + 5?43')*3,5ср/2 =2110кгс*см Мр =211Н*м Момент тертя в підшипнику:
Мп = fп*Q* dве/2 = 0,004*7870*7,0/2 = 115кгс*см Мп = 11,5Н*м Крутний момент на маховику:
Мкр = 2110 + 115 = 2225 кгс*см = 222,5Н*м Зусилля на маховику, яке необхідно для закриття і відкриття засувки:
Qм = 2Мкр/Dм = 2*2225/47,5 = 93,7кгс = 937Н деDм — діаметр маховика
3.1.3 Розрахунок головки шпинделя Визначення напружень в головці шпинделя /10/.
Напруження зминання:
?см = Q/(2*l*B) = 7870/(2*3,5*0,65) = 1730кгс/см2 = 173МПа Напруження згину:
?зг = 3Q (M + n — 2m)/(4l*h2)
?зг = 3*7870(3,7 + 5,0 — 2*3,5)/(4*3,5*2,52) = 45,9МПа Напруження (згину) зрізу:
?ср = Q/(2h*l) = 7870/(2*2,5*3,5) = 45МПа Напруження розтягу шийки шпинделя:
?зг = Q/(0,785m2) = 7870/(0,785*3,52) = 81,8МПа Матеріал шпинделя Сталь 40Х, ?т = 670МПа
3.1.4 Розрахунок пружин шибера Між плашками шибера для створення попереднього часткового тиску на контактних поверхнях (пружинах) затвора встановлюються шість пружин.
Qпр = 2400Н Робоче навантаження одної пружини:
Qроб = Qпр/6 = 2400/6 = 400Н Визначення діаметра дротини /11/.
Висота пружини при Qроб, Нроб = 4 см.
Середній діаметр пружини Dср = 1,6 см Матеріал пружини Сталь 60С2 (ГОСТ 1419−82),
[?] = 750МПа Діаметр дротинки визначається по формулі:
деQст — зусилля стиску пружини,
Qст = 125*Qроб = 1,25*400 = 500Н;
Приймаємо d = 4 мм = 0,4 см = 0,4*10−2м
Індекс пружини m = Dcр/4 = 16/4 = 4
Крок пружини t = d + Qст/С1;
При d = 4 мм;? = 750МПа; С1 = 57,8
t = 4 + 50/57,8 = 4.86мм = 0,4*10−2м Приймаємо t = 5,4 мм = 0,54*10−2м Умова Dср/3? t? Dср/2 виконується.
Напруження стиску:
?ст = 2,55К1*Qст*Dср/d3? [?]доп;
деК — поправочний коефіцієнт, К = 1,403;
Фактичне навантаження при стиску до дотикання вниз витків:
Qст = С1(t — d) = 57,8(5,4 — 4) = 810Н
?ст = 2,55*1,403*81*1,6/0,43 = 72,4МПа
?ст? [?]ст.
Зазор між витками при Qроб:
? = (Qcт — Qроб)/С1 = (81 — 40)/57,8 = 0,71 мм
? = 0,071*10−2м Число робочих витків:
приймаємо n = 7
Вільна висота пружини:
Нев = n*t + 1,5*d = 7*5.4 + 1.5*4 = 43,8 = 0,043 м Висота пружини до дотикання витків:
Нст = (n + 1,5)d = (7 + 1,5)*4 = 0,034 м Довжина розгорнутої пружини:
L = 3,3Dcр*n1;
деn1 — повне число витків,
n1 = n + 2 = 7 + 2 = 9;
L = 3,3*1,6*9 = 47,5 см = 0,47 м
3.1.5 Розрахунок різьби корпуса і кришки Тиск в середині корпуса Р = 70МПа Площа, яка піддається тиску:
F = 0,785(Dнп2 — dшп2) = 0,785(162 — 42) = 0,0188 м²
Зусилля тиску робочого середовища:
Р = р*F = 700*188 = 1316кН Визначення діаметра і висоти нарізки /11/.
Зусилля, яке створює зріз витків:
Qроз = кm*?*d*к2*Н*? гв? Р;
декm — безрозмірний коефіцієнт, який враховує нерівномірність розподілення навантаження, кm = 0,56 (будемо рахувати, що d/S? 9);
к2 — коефіцієнт повноти різьби, к2 = 0,69, для трапецеєвидної різьби;
?гв — границя міцності матеріалу гайки на зріз (тобто матеріалу корпуса);
d — діаметр нарізки;
Н — висота нарізки
?гв = 0,6*?р = 0,6*700 = 420МПа
Hd = P/(кm*?*d*к2*?гв) = 131 600/(0,56*3,14*0,65*42)
Hd = 2,74 м Задаючись Н можливо визначити d і навпаки по конструктивним міркуванням приймаємо d = 220 мм = 0,22 м Тоді
Н = 2740/220 = 12,5 мм = 0,125 м По конструктивним міркуванням приймаємо Н = 0,69 м Тоді число витків:
Z = H/S = 69/20 = 3.45
3.2 Розрахунок штуцера Вихідні дані:
Робочий тиск — 70МПа Тиск випробування — 105МПа Діаметр проходу — 80 мм Осьове зусилля, яке діє на шпиндель при його переміщенні рівне:
Qо = Qшп + Тс, деQшп — виштовхуюча сила;
Тс — сила тертя в сальниковій манжеті;
Qшп = Рроб*?dc2/4 = 700*3,14*42/4 = 87,92кН деdc — діаметр шпинделя в сальнику,
dc = 4 см = 0,04 м;
Тс = ?dc*hc*?*Рроб, деhc — висота сальника,
hc = 1 см = 0,01 м;
? — коефіцієнт тертя (сталь по резині - за мастилом),? = 0,1
Тс = 3,14*4*0,1*700 = 8,782кН
Qо = 8792+879,2 = 96,712кН Найбільший крутний момент на маховику:
М = Мр + Ме, деМр — момент тертя в різьбі;
Ме — момент тертя в сальнику;
Мр = Qо*Lp,
деLp — плече моменту в різьбі;
Lp = dcp/2 *tg (?+?),
деdcp — середній діаметр шпинделя;
Різьба шпинделя — трапецеєвидна 36*6
dcp = 33 мм = 0,033 м
tg? = t/(?dcp) = 6/(3,14*33) = 0,038,? = 3?20'
? = arctg ?,? = 0,17 (для різьби поза середовищем і при слабому змащенні),? = 9?40'
Lp = 33/2 *tg 13? = 0,38*10−2м Тоді:
Мр = 9671*0,38 = 368Н*м Мс = Тс*dc/2 = 879,2*4/2 = 175,84Н*м
Визначаємо крутний момент на маховику:
М = 368+175,84 = 543,8Н*м
3.2.1 Розрахунок фланцевого з'єднання кришки в корпуса навантаження на шпильки від внутрішнього тиску визначається за формулою:
Qш = Рроб*?D2/4,
деD — зовнішній діаметр ущільнення стакана,
D = 7,5 см = 0,075 м
Qш = 700*(3,14*7,52/4) = 309,09кН Приймаємо шість шпильок М24 з площею поперечного січення по внутрішньому діаметру різьби f = 3,37 см².
Напруження розтягу в шпильках /10/:
?р = Qш/(z*f),
деz — число шпильок;
?р = 30 809,4/(6*3,37) = 152,8МПа Матеріал шпильок — Сталь 40Х ГОСТ 4543–82 з? т? 670МПа.
Коефіцієнт запасу міцності:
n = ?т/?р, n = 670/152,8 = 4,38
Основні розміри розрахованих фланців приведені в таблиці 3.1.
Граничне навантаження на фланець (рис. 3.2):
Qгр = 1,7*к*J*h2*?т, Дек — безрозмірний коефіцієнт, який визначається:
J — безрозмірний коефіцієнт, який визначається З другої сторони
Qпред = Qш*Пзф, ДеПзф — коефіцієнт запасу для фланця:
Пзф = 1,7к*J*h2* ?т/Qш Матеріал фланців — Сталь 25ХГСЛ з? т? 570МПа Результати розрахунку зведені в таблицю 3.2.
Таблиця 3.1. — Основні розміри фланців корпуса і кришки
Фланець | D0, м | Dш, м | Dп, м | d0, м | ?, м | ? 1, м | h, м | |
Корпус | 0.085 | 0.15 | 0.18 | 0.024 | 0.016 | 0.022 | 0.025 | |
Кришка | 0.065 | 0.15 | 0.18 | 0.027 | 0.012 | 0.018 | 0.025 | |
Таблиця 3.2. — Результати розрахунків фланців
Фланець | Qш, кН | Qтр, кН | к | J | Пзф | |
Корпус | 3,8 | 0,54 | 4,0 | |||
Кришка | 2,08 | 0,62 | 2,5 | |||
3.2.2 Розрахунок корпуса Еквівалентне напруження в циліндричній частині корпуса визначається:
Головні напруження в циліндричній частині розраховуємо по формулі Леме:
деR — зовнішній радіус циліндра, R = 60 мм;
r — внутрішній радіус циліндра, r = 33 мм;
деDу — зовнішній діаметр ущільнення корпуса,
Dу = 7,5 см = 0,075 м;
?3 = -Рроб = -70МПа Визначаємо еквівалентне напруження в циліндричній частині корпуса:
при розрахунку корпуса по радіальному тиску маємо:
Матеріал корпуса — Сталь 25ХГСЛ з? т? 570Мпа
4. Охорона праці
4.1 Забезпечення нормальної роботи при монтажі і експлуатації
обладнання Устя фонтанної свердловини оснащується стандартною арматурою, після встановлення якої опресовується на тиск не перевищуючи допустимій тиск для опре совки експлуатаційної колони. Результати опре совки оформлюються актом.
Під вихідними лініями фонтанної арматури, розміщені на висоті, встановлюються надійно укріплюючи опори, які запобігають падінню лінії при її від'єднанні під час ремонту, а також вібрації від ударів струй.
Фонтанну арматуру монтують з повним комплектом шпильок і на ущільненнях, які забезпеченні технічними умовами. Необхідно провірити правильність дії показника на засувках, відміченого на корпусі засувки числа оборотів для повного відкриття і закриття.
Для виміру буферного тиску і тиску в затрубному просторі встановлюються манометри з трьохходовими кранами.
Нафтопроводи прокладаються з безшовних стальних труб, які з'єднанні зваркою.
Для обслуговування верхньої частини фонтанної арматури споруджуються площадки, які виконанні із металічних листів, які виключають можливість проковзування.
Для монтажу обладнання застосовують грузопідйомні механізми, спеціальні інструменти, які забезпечують безпечну роботу.
Для безпечної і нормальної експлуатації фонтанних свердловин є дотримання встановленого технологічного режиму роботи свердловини, тому необхідно контролювати всі прояви свердловини і зміни в її роботі (тиск в затрубному просторі, на буфері і трапі, дебіт нафти).
Для запобігання удару струї нафти перед заміною штуцера, потік повинен бути переведен з робочого на резервний вихід, закрита засувка на робочому виході, після чого зменшений тиск до атмосферного в струні за штуцером через вентиль, який встановлений на лінії.
Для дослідження свердловини необхідно вимірювати тиск на вибої свердловини і швидкість руху рідини. Тому необхідно виміряти тиск на вибої глибіним манометром. Глибиний манометр спускається через спеціальний лубрікатор, який встановлюється на фонтанній арматурі після зняття з неї буфера з манометром.
4.2 Забезпечення пожежної безпеки і охорони довкілля Згідно будівних норм і правил (СНиП 90−81) комплекс обладнання на тиск 70МПа для видобутку нафти фонтанним способом можна віднести до пожежної категорії Г.
На виробничій площадці повинно бути місце для встановлення протипожежних засобів.
До роботи на усті свердловини по усуненню відкритого нафтового фонтана допускається робітники воєнізованих частин, загонів і працівники підприємств, які пройшли спеціальну підготовку, які забезпеченні необхідними засобами захисту і відповідним спецодягом, за працюючими на усті свердловини для їх безпеки встановлюються безперервний нагляд.
Аварії на фонтанних свердловинах приводять до складних наслідків. Тому всі роботи на фонтануючих свердловинах ведуться при строгому дотриманні правил охорони навколишнього середовища.
При порушенні герметичності обладнання устя фонтанної свердловини відбувається утічка нафти, забруднюється територія навколо свердловини, в результаті чого виникає небезпека пожежі і отруєння нафтовим газом. Тому необхідно вести систематичний нагляд за обладнанням устя.
Для того, щоб запобігти розливу нафти із-за розгерметизації остьового обладнання необхідно встановлювати аварійні засувки. Ці засувки закриваються при будь-яких відхиленнях від нормальної експлуатації свердловини. На всіх свердловинах на випадок відкритого фонтанування робиться обваловка.
обладнання свердловина арматура штуцер
Література
1. Анурьев В. И. Справочник конструктора-машиностроителя, том 1; 3 — М.: Машиностроение, 1978
2. Раабен А. А. Монтаж и ремонт бурового и эксплуатационного оборудования, — М.: Недра, 1975
3. Юдин Е. Я. Охрана труда в машиностроении, — М.: Машиностроение, 1976
4. Бухаленко Е. М. Техника и технология промывки скважин, — М.: Недра, 1982
5. Молчанов Г. В., Молчанов А. Г. Машини и оборудование для добычи нефти и газа, — М.: Недра, 1984
П Приложение Рисунок 1.1 — Схема фонтанної арматури
1 — хрестовина; 2 — трійник; 3 — перевідник; 4 — запірний пристрій;
5 — кран; 6 — манометр; 7 — дросель: 8 — відвідний фланець