Термічна обробка сталі
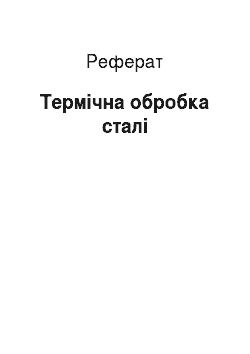
За середнього показника (нагрівання не більше 300−500() і високому (500−700() відпустці сталь зі стану мартенситу переходить відповідно стан троостита чи сорбита. Що відпустку, тим менше твердість відпущеної сталі та тим більше коштів її пластичність і в’язкість. Події у своїй зміна властивостей стали можна простежити по кривим діаграми, наведеної на рис. 4. При високому відпустці сталь отримує… Читати ще >
Термічна обробка сталі (реферат, курсова, диплом, контрольна)
року міністерство освіти Російської Федерации.
ППЛ № 43.
Реферат.
Термічна обробка стали.
Виконав учень 223 группы.
Чупахін Евгений.
Проверил:
Емельянцев Александр
В’ячеславович р. Балаково.
2003 г.
1. Основи теорії термічної обработки…3.
2. Відпал і нормализация…7.
3. Гарт і отпуск…10.
4.
Список литературы
…16.
1. Основи теорії термічної обработки.
Термічна (теплова) обробка полягає у зміні структури металів і сплавів шляхом нагрівання їх і наступного охолодження з тим чи іншого швидкістю; у своїй досягаються істотні зміни властивостей тим більше ж хімічний склад сплаву. |[pic] | |Рис. 1. Діаграми стану системи Fe — | |Fe3C |.
Термічна обробка сталі та чавуну полягає в явищах вторинної кристалізації стосовно лініях (див. мал.1) GOS (A3), SE (Aст) і РК (А1).
Зміни структури в різних швидкостях охолодження аустенита.
При повільному охолодженні эвтектоидной стали лінією РК (у точці Ar1) станеться повне розпадання аустеніту із заснуванням перліту. Розпадання складається з таких етапів: 1) перетворення (-заліза в (-залізо, тобто. перегрупування атомів з грати гранецентрированного куба (-заліза в грати центрованого куба (- заліза з одночасним зміщенням атомів вуглецю, що у твердому розчині (-заліза; 2) виділення з твердого розчину (аустеніту) дрібних частинок цементита.
(Fe3C); 3) укрупнення частинок цементита в платівки, розміри яких вимірюються від малих часткою мікрона за кілька мікронів, і більше більш-менш повне розпадання аустенита.
При прискоренні охолодження до 50 град/сек розпадання аустеніту не встигає закінчитися, розміри платівок цементита досягають лише десятих часткою мікрона і помітні лише за великих увеличениях. Така структура називається сорбитом (на вшанування Г. В. Сорби — англійського естествоиспытателя).
При прискоренні охолодження до 100 град/сек повністю встигає завершитися лише другий етап розпадання аустеніту, а третій, етап зупиняється в на самому початку. У результаті сума платівок цементита вимірюються стотисячними і мільйонними частками міліметра. Така структура носить назва троостита (під назвою Л. Трооста — французького хіміка). Наявність найтонших платівок цементита можна знайти з допомогою електронного мікроскопа. |[pic] | |Рис. 2. Залежність становища | |критичних точок эвтектоиднной| |стали швидкості охолодження. |.
При швидкості охолодження 150−200 град/сек встигає завершитися лише перегрупування атомів заліза, тому вуглець залишається як твердого розчину в (-залозі. Ця структура називається мартенситом (на вшанування А. Мартенса — німецького металловеда).
Підбиваючи підсумки сказаного, зауважимо, що перліт, сорбит і троостит по структурі є двухфазную суміш (феррита і цементита) і відрізняються одна від друга дисперсностью цементита; мартенсит ж однофазен, це твердий розчин вуглецю в (-железе.
Структура перліту, получающаяся при повільному охолодженні сплавів, називається рівноважної, як та інші структури. На відміну від рівноважної, структури сорбита, троостита і мартенситу, отримувані при прискорених охлаждениях, називаються неравновесными.
Зрушення критичних точок при охлаждении.
Збільшення швидкості охолодження викликає зниження критичних точок (по відношення до їх становищу з діаграми рівноваги, див. рис. 66). Зрушення температур збільшується з прискоренням охолодження, що видно на рис. 2. Крива A’r показує, що переохолодження аустеніту зростає при прискоренні охлаждения.
При повільному охолодженні переохолодження невелика (верхні точки кривою A’r), і структура стали залишається перлитной. Платівки цементита в перлите тим менше, що більше швидкість охолодження, і за подальшому прискоренні охолодження структура дедалі більше наближається до сорбиту. При швидкості охолодження, яка потрібна на отримання структури сорбита ((50 град/сек), аустенит переохлаждается понад 100(і фазове перетворення їх у сорбит станеться за нормальної температури близько 600((точка З на кривою A’r). Перетворення на троостит станеться при переохолодженні аустеніту на (180((точка Т).
Швидкість охолодження V1 (150 град/сек) відповідає початку появи мартенситу у структурі стали. Частина лінії A"r, характеризує перетворення «аустенит — мартенсит», — пряма. Це свідчить про сталість температури при перетворення (близько 240(для эвтектоидной стали) незалежно від подальшого збільшення швидкості охлаждения.
Отже, крива A’r характеризує розпадання аустеніту на дві фази: феррит і цементит, а відрізок A"r — перехід аустеніту в мартенсит. При швидкостях охолодження V1 до V2 охолоджена сталь містить троостит і мартенсит (перетворення відбувається відповідно до лінії A’r і лінії A"r). При швидкостях охолодження, перевищують V2 (нижче лінії A"r), поруч із мартенситом буде трохи залишкового (не колишнього) аустенита.
Изотермическое розпадання аустеніту. |[pic] | |Рис. 3. Діаграма изотермического | |розпадання аустеніту эвтектоидной | |стали |.
Спостереженнями встановлено, як і швидкість, і характеру розпадання аустеніту залежать від ступеня його переохлаждения.
На рис. 3 приведено діаграма изотермического розпадання аустеніту эвтектоидной углеродистой стали. Діаграма побудовано координатах «Температура — логарифм часу» (час відкладається на абсциссе по логарифмічною шкалою), що дозволяє простежити за часом перетворення від часткою секунди до діб, і более.
Припустимо для простоти, що за 0,5 сік вдається остудити зразок зі стану аустеніту до будь-який температури: від точки Ar1 до 0(і від. Прохолоджуючи зразок до 700(і витримуючи його за цієї температурі, зауважимо, що протягом часу до точки H1 в аустените ніяких перетворень не відбувається. З часу, відповідного точці H1, починається розпадання аустеніту. Період часу до точки H1 називається инкубационным періодом. Розпадання аустеніту закінчується повністю вчасно точки К1, коли аустенит перейшов у перліт. Швидкість подальшого охолодження важить на структуру зразка, тому за точкою К1 лінія обрывается.
Спостерігаючи зразком, охолодженим зі стану аустеніту до температури 650(і завдаючи на діаграму точки початку H2 і кінця K2 розпадання аустеніту, зауважимо, що і інкубаційний період, і період розпаду аустеніту зменшилися, а результаті розпаду вийшов сорбит.
Для зразка, охолодженого до температури близько 500(, одержимо на діаграмі відповідно точки Н3 і К3 розпадання аустеніту, а структура стали представлятиме троостит. При зростання кількості подібних дослідів визначиться ряд точок початку будівництва і закінчення перетворення аустеніту. Поєднуючи ці точки, одержимо дві криві перетворення аустеніту; криву I — початку перетворення в різних температурах і криву II — кінця перетворення за ті самі температурах.
При охолодженні зразків зі швидкістю вище критичної за нормальної температури 240((лінія MН) починається перетворення аустеніту в мартенсит; перетворення всього аустеніту в мартенсит відбувається за подальшому зниженні температури, і закінчення цього перетворення для эвтектоидной углеродистой стали настане лише за температурі -50(.
Розглянувши діаграму (рис. 3), відзначимо у результаті таке. Верхня частина діаграми характеризує изотермическое розпадання аустеніту в суміш феррита і цементита. Лівіше кривою I перебуває полі, відповідальна переохлажденному аустениту, область між кривими I і II визначає час розпаду переохлажденного аустеніту, правіше кривою II перебуває полле продуктів розпаду аустеніту: перліту, сорбита і троостита. Інкубаційний період розпаду аустеніту змінюється залежно від рівня переохолодження останнього: спочатку зменшується до деякою критичної величини, та був знову збільшується. Цей період кожної температури визначається абсциссой кривою I — початку розпадання аустеніту. Крива II показує, що тривалість перетворення також залежить від температури переохолодження. Пряма Mн є кордоном між верхньої та нижньої частинами діаграми. Ця пряма характеризує початок мартенситного перетворення аустеніту і відповідає прямому ділянці кривою A"r (див. рис. 2).
Нижня частина діаграми показує, що з перекладу всього залишкового аустеніту в мартенсит необхідно знижувати температуру стали до лінії Mк (кінець мартенситного перетворення). Криві изотермического розпадання аустеніту мають форму літери З повагою та називають С-образными кривими. Форма цих кривих встановлено професором С. С. Штейнбергом та інші радянськими учеными.
Для доэвтектоидной і заэвтектоидной сталей С-образные криві смещениы вліво проти кривими эвтектоидной стали; прямі Км і Км перша розташовані вище, а другий — нижче, ніж для эвтектоидной стали.
Властивості стали зі структурою мартенситу, троостита, сорбита чи перлита.
Розглянемо спочатку властивості структур эвтектоидной стали. |[pic] | |Рис. 4. Діаграма зміни | |механічних властивостей эвтектоидной стали| |у різних станах від перліту до | |мартенситу |.
Мартенсит — сама стати рішуча й сама тендітна структура.
Твердість мартенситу HB=600−650 (HRC=62−66), а пластичні властивості при розтягненні ((і () і ударна в’язкість (а) близькі нанівець. Щільність мартенситу менше, ніж щільність інших структур, і як 7,75 г/см3. У зв’язку з збільшенням обсягу стали при мартенситном перетворення виникають напруги, особливо в нерівномірному охолодженні деталі. Мартенсит магнитен й володіє найбільшої здатністю зберігати у собі залишковий магнетизм, тому заготівлі магнітів заливають в мартенсит.
Тростит і сорбит — проміжні структури між перлитом і мартенситом, тому їх властивості будуть середніми між властивостями перліту і мартенситу. На рис. 4 наведено криві зміни твердості HB, краю міцності (у і відносного подовження (эвтектоидной сталі у різних станах від перліту до мартенсита.
Властивості структур неэвтактоидной стали від властивостей тієї ж структур эвтектоидной сталі у залежність від змісту вуглецю, проте характер зміни властивостей структур від перліту до мартенситу хоча б, як і у эвтектоидной стали.
Вивчивши питання теорії термічної обробки стали, познайомимося з її видами: отжигом і нормалізацією, загартованістю і отпуском.
2. Відпал і нормализация.
Після виливки, прокатки і кування сталеві заготівлі розладнуються нерівномірно результатом чого є неоднорідність структури та властивостей в різних місцях заготовок, і навіть поява внутрішніх напруг. Крім того, при затвердевании виливки виходять неоднорідними за складом внаслідок ликвации.
Отжиг.
Отжигом називають нагрівання та повільний охолодження стали. Академік А. А. Бочвар дав визначення структури з неравновесного стану на більш рівноважний (повернення, чи відпочинок, рекристаллизационный відпал, чи рекристаллизация, відпал зі зняттям внутрішніх напруг і дифузний відпал, чи гомогенізація); відпал другого роду — на зміну структури сплаву у вигляді перекристалізації близько критичних точок для одержання рівноважних структур; до отжигу другого роду належить повний, неповний і ізотермічний отжиги.
Нижче розглянуті перелічені види отжига стосовно стали.
Повернення (відпочинок) стали — нагрівання до 200 — 400(, зменшення чи зняття наклепа. За повернення спостерігається зменшення спотворень у кристалічних ґратах у кристаллитов і часткове відновлення фізико-хімічних свойств.
Рекристаллизационный відпал (рекристаллизация) стали відбувається за температурах 500 — 550(; відпал зі зняттям внутрішніх напруг — при температурах 600 — 700(. Ці види отжига знімають внутрішні напруги в отливках від нерівномірного охолодження їх частин, соціальній та заготівлях, опрацьованих тиском (прокаткою, волочінням, штампуванням) за температур нижче критичних. При рекристаллизационном отжиге з деформованих зерен виростають нові кристали, ближчі один до равновесным, внаслідок твердість стали знижується, а пластичність і ударна в’язкість збільшуються. Для повного зняття внутрішніх напруг у стали потрібна температура щонайменше 600(.
Охолодження після витримки при заданої температурі має бути досить повільним: при прискореному охолодженні знову виникають внутрішні напряжения.
Дифузний відпал застосовується у тому випадку, як у стали спостерігається внутрикристаллическая сегрегація. Вирівнювання складу в зернах аустеніту досягається дифузією вуглецю та інших домішок в твердому стані, поруч із самодиффузией заліза. Через війну сталь стає однорідної по складу (гомогенної), тому дифузний відпал називає також гомогенизацией.
Температура гомогенізації має бути досить високої, проте не можна допускати пережога і оплавлення зерен. При пережоге кисень повітря окисляє залізо, проникаючи в товщу його, утворюються кристаллиты, роз'єднані окисными оболонками. Плавлення в металі усунути не можна, тому перепалені заготівлі є остаточним браком.
При диффузионном отжиге зазвичай зерна занадто укрупнюються, що можна виправляти наступною повною отжигом (на дрібне зерно).
Повний відпал пов’язані з фазової перекристаллизацией і подрібненням зерна за температур точок АС1 і АС2. Призначення його — поліпшення структури стали для полегшення наступної опрацювання різанням, штампуванням чи загартованістю, і навіть отримання мелкозернистой рівноважної перлитной структури в готової деталі. Для повного отжига сталь нагрівають на 30−50(вище температури лінії GSK поволі охолоджують. |[pic] | |Рис. 5. Грубозерниста | |структура доэвтектоидной | |стали. |.
Після отжига надлишковий цементит (в заэвтектоидных сталях) і эвтектоидный цементит мають форму платівок, тому й перліт називають пластинчатым.
При отжиге на табличний перліт заготівлі залишають в печі до охолодження, найчастіше при частковому підігріванні печі паливом, щоб швидкість охолодження була більше 10−20(в час.
Отжигом також досягається здрібнення зерна. Грубозерниста структура, наприклад, доэвтектоидной стали (рис. 5), виходить при затвердевании внаслідок вільного зростання зерен (при повільному охолодженні виливків), а також у результаті перегріву стали. Ця структура називається видманштетовой (під назвою австрійського астронома А. Видманштеттена, відкрив в 1808 р. таку структуру на метеорном залозі). За такої структури міцність заготівлі низька, і структура характерна тим, що включення феррита (світлі ділянки) і перліту (темні ділянки) містяться у вигляді витягнутих пластин під різними кутами друг до друга. У заэвтектоидный сталях видманштетова структура характеризується штрихообразным розташуванням надлишкового цементита.
Роздрібнення зерна пов’язані з перекристаллизацией (-заліза в (-залізо; при охолодженні і зворотному переході (-заліза в (-залізо мелкозернистая структура сохраняется.
Отже, при отжиге на табличний перліт одночасно забезпечується мелкозернистая структура.
Неповний відпал пов’язані з фазової перекристаллизацией лише за температурі точки АС1; його після гарячої обробки тиском, коли в заготівлі мелкозернистая структура. |[pic] | |Рис. 6. Мікроструктура | |зернистого перліту (X500)|.
Відпал на зернистий перліт застосовують зазвичай для эвтектоидных і заэвтектоидных сталей, з метою підвищення пластичності і в’язкості сталі та зменшення її твердості. Для отримання зернистого перліту сталь нагрівають вище точки АС1 і витримують недовго, щоб цементит розчинився у аустените в повному обсязі. Потім сталь охолоджують до температури трохи нижче Ar1 і витримують за такої температури кілька годин. У цьому частки що залишився цементита служать зародками кристалізації для выделяющегося цементита, який наростає округлими (глобулярными) кристаллитами, розсіяними в феррите (рис. 6).
Властивість зернистого перліту істотно відрізняються від властивостей пластинчастого убік меншою твердості, але більшої пластинчатости і в’язкості. Особливо це стосується заэвтектоидной стали. У якій весь цементит (як эвтектоидный, і надлишковий) виходить як глобулей. |[pic] | |Рис. 7. Схема изотермического отжига і изотермической гарту. |.
При изотермическом отжиге після нагріву і витримки сталь швидко охолоджують до температури трохи нижче точки А1 (рис. 7) і витримують при цієї температурі до розпадання аустеніту на перліт, після чого охолоджують надворі. Застосування изотермического отжига значно скорочує час і підвищує продуктивність. Наприклад, звичайний отжыг легованої стали триває 13−15 год, а ізотермічний — всього 4−7 год. Схема изотермического отжига приведено на рис. 7.
Нормалізація. При нормалізації сталь охолоджується над печі, як із отжиге, але в повітрі в цеху. Нагрівання ведеться до перекристалізації (на 30−50(вище точок Ас3 і Аст), внаслідок сталь набуває мелкозернистую і однорідну структуру. Твердість і міцність стали після нормалізації вище, ніж після отжига.
Структура низьковуглецевої сталі після нормалізації феррито-перлитная, така сама, як і після отжига, а й у середньоі высокоуглеродистой стали — сорбитная; нормалізація може замінити перша — відпал, а другий — загартування з великим відпусткою. Часто нормалізацією готують сталь для гарту. Термічну обробку деяких марок углеродистой і легованих сталей закінчують нормализацией.
3. Гарт і отпуск.
Мета гарту й відпустки стали — поліпшення її свойств.
Гарт з відпусткою потрібна для дуже багатьох деталей і виробів. Вона полягає в перекристалізації стали при нагріванні до температури вище критичної; після достатньої витримки нині температурі завершення гарту слід швидке охолодження. Таким шляхом запобігають перетворення аустеніту в перлит.
Загартована сталь має нерівноважну структуру мартенситу, троостита чи сорбита.
Найчастіше при загартуванню сталь різко охолоджують на мартенсит. Для пом’якшення дії гарту сталь відпускають, нагріваючи до температури нижче точки А1. При відпустці структура сталі з мартенситу гарту перетворюється на мартенсит відпустки, троостит відпустки чи сорбит отпуска.
Температурні умови гарту. Температура нагріву стали при загартуванню та ж, що й за повному отжиге: для доэвектоидной стали 30−50(вище точки Ас3, для заэвтектоидной — на 30−50(вище точки Ас1.
При нагріванні доэвтектоидной стали до температури між точками Ас1 і Ас3 (неповна гарт) у структурі швидко охолодженою стали, поруч із загартованими ділянками, житиме нерастворенный феррит, різко що знижує твердість і міцність. Тож доэвтектоидной стали обов’язкова повна гарт (нагрівання вище точки Ас3).
У заэвтектоидной стали надлишкової фазою є цементит, котрий за твердості не поступається мертенситу і навіть за його; тому сталь досить нагріти на 30−50(вище точки Ас1.
Нагрівати вироби, особливо великі, потрібно поступово, щоб уникнути місцевих напруг і тріщин, а час витримки нагрітого вироби має бути достатнім, щоб перехід перліту в аустенит повністю завершився. Тривалість витримки зазвичай дорівнює чверті загальної тривалості нагревания.
Охолодження деталей при загартуванню. Швидкість охолодження деталей при загартуванню має бути таким, щоб деталь вийшла заданої структури. Швидкість V2 (див. рис. 2), забезпечує мартенситную структуру (з залишковим аустенитом, не без троостита), називається критичної швидкістю закалки.
Оскільки С-образные криві доэвтектоидной і заэвтектоидной сталей зміщені вліво проти кривими эвтектоидной стали, критична швидкість гарту їхня вища, й одержання структури мартенситу досягається важче, а деяких марок вона недостижима.
Легирующие компоненти в стали полегшують загартування, бо за цьому Зобразні криві зміщуються вправо, і критична швидкість понижается.
При швидкості охолодження менше критичної у структурі загартованою стали, поруч із мартенситом, буде троостит, а при подальшому зменшенні швидкості виходять структури троостита чи сорбита без мартенсита.
Різкість гарту (отримання мартенситу без троостита) залежить від природи температури охолоджувальної середовища. Охолодження струменем повітря, або холодними металевими плитами дає іду загартування на сорбит. Найбільш поширене охолодження деталей зануренням в воду, лужні чи кислі розчини, олію, розплавлений свинець та інших. У цьому виходить різка чи помірна гарт (на мартенсит чи троостит).
Що Охолоджує здатність води різко змінюється залежно від неї температури; якщо це здатність при 18(б сприйняти як одиницю, то, при 74(вона мати коефіцієнт 0,05.
До різким охладителям належить 10%-ный розчин NaOH у питній воді, при 18(його коефіцієнт -2,0; до помірним — мінеральні олії з коефіцієнтом 0,2−0,25.
При загартуванню використовують різноманітні прийоми охолодження залежно від марки стали, форми і збільшення розмірів деталі технічних вимог до ним.
Проста гарт щодо одного охладителе (переважно у воді чи водних розчинах) виконується шляхом занурення до нього деталі до охолодження. При охолодженні необхідно звільняти деталь від шару пара хороший теплоизолятор. Такий спосіб гарту самий распространенный.
Для отримання високої твердості також найбільшою глибини загартованого шару для углеродистой стали застосовують охолодження деталей при інтенсивному обрызгивании.
Переривчастої загартованістю називають таку, коли він деталь охолоджують послідовний у двох середовищах: перша середовище — що охолоджує рідина (зазвичай вода); друга — повітря чи олію. Різкість такий гарту менше, ніж предыдущей.
При східчастої загартуванню деталь швидко занурююється у соляної розплав і охолоджують до температури трохи вища МН (див. рис. 3), короткий час витримують і далі охолоджують надворі. Витяг забезпечує вирівнювання температури від поверхні до серцевині деталі, що зменшує напруги, які під час мартенситном превращении.
Спосіб занурення деталей в закалочную ванну повинна бути такою, щоб при загартуванню вони, як можна менше жолобилися. Деталі з великим ставленням довжини до діаметру чи ширині (напилки, свердла та інших.) слід занурювати в охолоджувач вертикально.
Изотермическая гарт. Изотермическая гарт (гарт у гарячих середовищах) полягає в изотермическом розпаданні аустеніту; охолодження ведеться не дуже до кімнатної температури, а до температури трохи вища початку мартенситного перетворення (200−300(, залежно від марки стали). У ролі охолоджувача використовують соляні розплави чи нагріте до 200−250(олію. При температурі гарячої ванни деталь витримується тривале час, поки підуть інкубаційний період, і розпадання аустеніту. У результаті виходить структура голчастого троостита, який за твердістю близького до мартенситу, а більш грузького і міцного. Наступне охолодження виготовляють воздухе.
При изотермической загартуванню спочатку потрібно швидке охолодження зі швидкістю щонайменше критичної, щоб уникнути розпадання аустеніту в умовах, відповідальних перегину С-образной кривою (див. рис. 7). Отже, за цим методом можна гартувати лише невеликі (приблизно, діаметром до 8 мм) деталі з вуглецевої сталі, оскільки запас енергії в важчих деталях не дозволить досить швидко їх остудити. Не належить, проте, до легированным сталям, більшість марок яких має значно менші критичні швидкості гарту. Великим перевагою изотермической гарту є можливість рихтовки (виправлення викривлень) виробів під час інкубаційного періоду розпадання аустеніту (який триває кілька хвилин), коли сталь ще м’яка і пластична. Після изотермической гарту деталі вільні внутрішніх напруг не мають трещин.
Види поверхневою гарту. При поверхневою загартуванню вище критичної температури нагрівається лише тонкий поверхневий пласт деталі, а всередині метал майже нагрівається. Після гарту деталі мають твердий поверхневий пласт і в’язку серцевину. |[pic] | |Рис. 8. Схема гарту з допомогою газової | |пальники. |.
Гарт з допомогою газової пальники схематично показано на рис. 8. Кислородно-ацетиленовое полум’я газової пальники з температурою близько 3200(іде на поверхню закаливаемой деталі швидко нагріває до температури вище критичної. Після горілкою з трубки на поверхню деталі іде струмінь води, гартуючи нагрітий шар стали.
Спосіб цей успішно застосовується для гарту поверхневого шару зубів великих шестерні, схильних до сильному зносу. |[pic] | |Рис. 9. Схема індукційною гарту. |.
Гарт струмами високої частоти методом В. П. Вологдина знайшла дуже широке використання у промисловості, оскільки вирізняється високою продуктивністю, легко піддається управлінню і відданість забезпечує хороше якість. Закаливаемая деталь 5 (рис. 9) міститься у індуктор (котушку) 4, яким пропускається струм високої частоти. Струм надходить через трансформатор 3 від машинного генератора 1, приводимого у обертання електродвигуном 2. Порушуваний причому у деталі струм має найбільшу щільність у поверхні, і швидко нагріває поверхню деталі. Коли нагрівання закінчено, деталь обрызгивается водою з індуктора, який цього робиться полым з отверстиями.
Заради покращання коефіцієнта потужності високочастотної установки включені конденсатори 6.
Регулюючи потужність струму та палестинці час витримки, можна обмежити нагрівання на товщину від часткою міліметра до десятків миллиметров.
Машинні генератори із частотою струму до 10 кГц зазвичай застосовують для гарту на глибину понад 2 мм. При загартуванню на глибину менше 2 мм користуються високочастотними ламповыми генераторами, створюють струм дуже високої частоти, що можна змінювати залежно від особливостей закаливаемых деталей.
Дефекти гарту. До цих дефектів належить: тріщини, повідці, чи коробление і обезуглероживание.
Головна причина тріщин і повідці - нерівномірне зміна обсягу деталі при нагріванні і, особливо, при різкому охолодженні. Інша причина — збільшення обсягу при загартуванню на мартенсит.
Тріщини виникають оскільки напруги при нерівномірному зміні обсягу окремих місцях деталі перевищують міцність металу у цих местах.
Кращим способом зменшення напруг є повільне охолодження близько температури мартенситного перетворення (точка МН). При конструюванні деталей необхідно враховувати, що наявність гострих кутів і різких змін перерізу збільшує внутрішня напруга при закалке.
Коробление (чи повідця) виникає також від напруг у результаті нерівномірного охолодження і виявляється в викривленнях деталей. Якщо такі викривлення невеликі, є підстави виправлені, наприклад, шлифованием. Тріщини і коробление може бути запобігти попереднім отжигом деталей, рівномірним і поступовим нагріванням їх, і навіть застосуванням східчастої і изотермической закалки.
Обезуглероживание почав із поверхні - результат вигоряння вуглецю за вищого і тривалому нагріванні деталі в окислительной середовищі. Для запобігання обезуглероживания деталі нагрівають в відновлювальної чи нейтральній середовищі (восстановительное полум’я, муфельные печі, нагрівання в рідких средах).
Обробка холодом — нового вигляду термічної обробки. Цей метод розроблений у Радянському Союзі (праці С. С. Штенберга, О.П. Гуляєва і Н.А. Минкевича) підвищення твердості стали шляхом перекладу залишкового аустеніту загартованою сталі у мартенсит. Це виконується при охолодженні стали до температури нижньої меартенситной точки МК (див. рис. 3).
Холодом обробляють углеродистую сталь, що містить більш 0,5% З, у якої температура мартенситового перетворення (точка МК) перебуває нижче 0(, і навіть легированную сталь, наприклад, быстрорежущую.
Відпустку стали пом’якшує дію гарту, зменшує чи знімає залишкові напруги, підвищує в’язкість, зменшує твердість і слабкість стали. Відпустку виробляється шляхом нагріву деталей, загартованих на мартенсит до температури нижче критичної. Причому у залежність від температури нагріву можна отримати стану мартенситу, троостита чи сорбита відпустки. Ці стану дещо відрізняються відповідних станів гарту структурою і властивостями: при загартуванню цементит (в троостите і сорбите) виходить у вигляді видовжених платівок, як і пластинчатом перлите. При відпустці він виходить зернистим, чи точковим, як і зернистому перлите.
Перевагою точкової структури є сприятливе поєднання міці й пластичності. При однаковому хімічний склад і однаковою твердості сталь з точкової структурою має значно більше високе відносне звуження (і ударну в’язкість а, підвищену подовження (і межа плинності (т порівняно з сталлю з пластинчастим структурой.
Мартенсит гарту має нестійку тетрагональную грати, а мартенсит відпустки — стійку центровану кубічну грати (-железа.
Відпустку поділяють на низький, середній і високий залежно від температури нагрева.
При низькому відпустці (нагрівання до температури 200−300() у структурі сталі у основному залишається мартенсит, який, проте, змінюється грати. Крім того, починається виділення карбідів заліза з твердого розчину вуглецю в (-залозі і початкова скупчення їх з’являється невеличкими групами. Це спричиняє у себе деяке зменшення твердості і підвищення пластичних і в’язких властивостей стали, і навіть зменшення внутрішніх напруг у деталях. Для низького відпустки деталі витримують протягом визначеного часу зазвичай, у олійних чи соляних ваннах. Якщо низького відпустки деталі нагрівають на повітрі, то тут для контролю температури часто користуються квітами мінливості, що з’являються лежить на поверхні деталі. Поява цих квітів пов’язані з інтерференцією білого світла плівках окисла заліза, виникаючих на поверхні деталі у її нагріванні. У інтервалі температур від 220 до 330(в залежність від товщини плівки колір змінюється від ясно-жовтого до сірого (табл.). Низький відпустку застосовується для ріжучого, вимірювального інструмента і зубчастих колес.
Таблиця |Колір мінливості |Температура, |Колір мінливості |Температура, | | |(З | |(З | |Світло-жовтий |220 |Фіолетовий |285 | |Солом'яний |240 |Васильково-синий |395 | |Коричнево-желтый |258 |Ясно-синій |315 | |Червоні-червону-червоне-червона-коричнево-червоний |265 |Сірий |330 і від | |Пурпурно-червоний |275 | | |.
За середнього показника (нагрівання не більше 300−500() і високому (500−700() відпустці сталь зі стану мартенситу переходить відповідно стан троостита чи сорбита. Що відпустку, тим менше твердість відпущеної сталі та тим більше коштів її пластичність і в’язкість. Події у своїй зміна властивостей стали можна простежити по кривим діаграми, наведеної на рис. 4. При високому відпустці сталь отримує найкраще поєднання механічних властивостей, підвищення міцність, пластичність і в’язкість, тому високий відпустку стали після гарту в мартенсит називають ковальських штампів, пружин, ресор, а високий — багатьом деталей, схильні до дії високих напруг (наприклад, осей автомобілів, шатунів двигателей).
Для деяких марок стали відпустку виробляють після нормалізації. Цей належить до мелкозернистой легованої доэвтектоидной стали (особливо нікелевої), має високу в’язкість і тому погану оброблюваність ріжучим інструментом. Заради покращання обрабатываемости виробляють нормалізацію стали за підвищеної температурі (до 950−970(), внаслідок що хоче набуває велику структуру (визначальну кращу оброблюваність) і водночас підвищену твердість (через малої критичної швидкості гарту нікелевої стали). З метою зменшення твердості виробляють високий відпустку цієї стали.
1. Технологія металів і конструювання матеріали. В.М. Никіфоров, Москва,.
1968, Вид. «Вищу школу». 2. Матеріалознавство. А.Є. Лейкін, Б.І. Родін, Москва, 1971, Вид. «Вища школа».