Продольно-резательный верстат продуктивністю 350 т/сутки
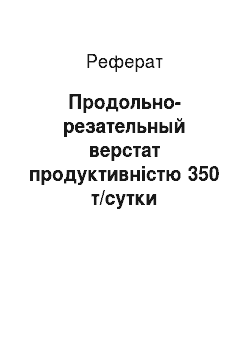
З метою зменшення кількості наматываемых рулонів на папероробної машині й разматываемых рулонів на продольно-резательном верстаті діаметр наматываемого рулону на накаті папероробної машини сягає 2000 — 2400 мм. Разматываемый рулон папери діаметром до 2400 мм встановлюють на стійках, званих розкатом. Для отримання по обидва боки паперового полотна однаковою ширини обрезаемых крайок рулон може… Читати ще >
Продольно-резательный верстат продуктивністю 350 т/сутки (реферат, курсова, диплом, контрольна)
АННОТАЦИЯ.
У дипломному проекті наведено аналіз існуючих конструкцій подовжньорізальних верстатів для картоноделательных машин і розглянуті такі основні вопросы:
— конструкції подовжньо — різальних станков;
— існуючі схеми подовжньо — різальних станков;
— механізми подовжньої резки;
— компонування і привід подовжньо — різальних станков.
У проекті запропонований варіант подовжньо — резательного верстата з нижньої заправкою полотна картона.
У результаті розробки проекту було зроблено технологічні і конструктивні розрахунки, розроблена автоматизована пневматична схема регулювання щільності намотки рулонів, розроблено заходи щодо безпеки об'єкта (розроблено схему отсоса пилу від ножів і зроблено розрахунок пневмотранспорта відходів від ПРС), і навіть наведено розрахунок економічної ефекту від запровадження проектованого подовжньо — резательного верстати на производство.
Дипломний проект сопровожден необхідними кресленнями, розробленими у відповідність до існуючими ГОСТами.
1. Запровадження … 3.
2. Техніко-економічне обгрунтування проекту … 10.
3. Технологічні розрахунки … 44.
4. Конструктивні розрахунки … 49.
5. Автоматизація … 70.
6. Економічна частина … 75.
7. Безпека об'єкта … 79.
8. Перелік використовуваної літератури … 90.
1.
ВВЕДЕНИЕ
.
Лісова і целюлозно-паперова промисловість є важливим «експортної «складової російської економіки. Пройшовши крізь нелегкий етап структурної трансформації під час 1991 — 1996 рр., лісова і целлюлознопаперова галузь Росії у час входить у новий етап якісного розвитку. Підприємства целюлозно-паперової промисловості в Росії 2000 року справили 3,4 млн. тонн папери, що у 12,5% більше, ніж 1999 року. У цьому обсяги виробництва картону становив 1,9 млн. тонн (21,4%). На целлюлозо-бумажную галузь доводиться 63% прибутку лісопромислового комплексу Росії. У цьому рентабельність галузі 2000 року становив 42%. Як у Мінпромнауки, на збільшення обсягів виробництва відбулося в зі зростанням російської промисловості України загалом, що спричинило підвищення попиту упаковку. Через це завантаження потужностей у целюлозно-паперової промисловості, у торік збільшилася на 3—5% проти 1999 роком, і досягла 75%. Поза тим, важливу роль зіграла сприятлива кон’юнктура світових цін, які у торік перевищували загалом п’ять% ціни 1999 року. За прогнозами експертів міністерства, темпи зростання обсягів виробництва цього року повинні сповільнитися, оскільки нині намічається тенденція до зниження цін на целюлозу і картон. Проте, аналітики очікують, у цілому за галуззю зростання виробництва перевищить 10%. Як повідомили прес-службі компанії «Илим Палп Ентерпрайз », 2002 року ця лесопромышленная корпорація планує збільшити виробництво зерна товарної своєї продукції 37,2% до 2 млн. 182 тис. тонн. Обсяг варіння целюлози має зрости на 41% проти показником 2001 року й скласти 2 млн. 151 тис. тонн. Збільшення випуску товарної продукції і на обсягу варіння целюлози пов’язана з тим, що спочатку 2002 року у корпорацію «Илим Палп Ентерпрайз «ввійшов Усть-Илимский ЛПК, що у 2002 року має випустити 533 тис. тонн товарної продукції, а обсяг варіння целюлози становитиме 572,9 тис. тонн.
Довідково: ЗАТ «Илим Палп Ентерпрайз «(Санкт-Петербург) зареєстровано 30 квітня 1992 року. Нині у корпорацію входять «Котласский ЦПК », «Братський ЛПК », «Санкт-Петербурзький картоннополіграфічний комбінат », «Усть-Илимский ЛПК «і 42 лісозаготівельних підприємства. Щорічний обсяг лісозаготівлі становить 8 млн. кубічних метрів. На підприємствах, які входять у ЗАТ «Илим Палп Ентерпрайз », виробляється 61% російської целюлози і 77% коробочного картона.
Картонна тара — це з стабільно зростаючих сегментів над ринком упаковки, яка передбачає розмаїття різних упаковок, починаючи з індивідуальної упаковки (коробки для шоколадних цукерок, печива, пачки сигарет) і до транспортної упаковкою (картонні коробки, ящики). Сьогодні, під час социально-этического, індивідуалізованого маркетингу, коли велика увагу приділяється як якості товару, а й якості упаковки товару, її дизайну, эргономичности, екологічну чистоту, інформативності тощо., попит на якісну споживчу і транспортну картонну тару серед вітчизняних виробників інтенсивно зростає. Тим більше що картон і папір є поширеними пакувальні матеріали, як у країні, і у багатьох європейських країнах. Наприклад, у Німеччині частка картонної і паперової тари серед пакувальних матеріалів становило 1995 року майже 40%, у Росії 1998 року — близько 38%.
Картонна тара є продуктом лісової, деревообробної і целюлозно-паперової промисловості, тому доцільно звернутися до даним в розвитку виробництва, у цій сфері. На рис. 1 видно динаміка виробництва лісової, деревообробної і целюлозно-паперової промисловості за січень-вересень 2001 року. Спад виробництва стався лише у лютому місяці на 1,7%. Середній зростання виробництва на січеньвересень 2001 року порівняно під аналогічною періодом 2000 року становить 2,5%. Мінекономрозвитку і торгівлі РФ прогнозує зростання виробництва продукції цієї галузі 2001 рік — 3,9%, на 2002 рік — 4,2%.
[pic] Дані Держкомстат РФ.
Однак у в таких галузях, як лісозаготівельна і деревообробна за ці 3 квартали стався спад виробництва на 1,9 і 1,5% відповідно. Тоді як целюлозно-паперова галузь показала особливо хороші результати — збільшити виробництво на 8,2%. Недарма вона приносить близько 63% прибутку усієї галузі, будучи однією з найбільш рентабельних галузей лесоперерабатывающего комплексу. Перспективним з цією галузі є і внутрішній ринок, як було зазначено, зростає попит на картонну тару зі боку вітчизняних виробників, і світовий ринок. Хоча останні тенденції світового фінансового ринку целюлозно-паперової продукції кілька тривожні, ще з минулого року її ціни на всі продукцію цієї галузі світовому ринку знижуються. Проте, експорту виробляється до 2/3 всієї виробленої продукции.
На рис. 2 відбито товарна структура целюлозно-паперової галузі й динаміка провадження у кожному товарному напрямку упродовж трьох кварталу 2001 року порівняно з цими аналогічного періоду 2000 року (джерело — Держкомстат РФ). Дані Держкомстат РФ.
Виробництво картонних ящиків зросло 18,5% та й склав 93,7 млн. кв. м., темпи зростання виробництва картонної тари перевищили темпи зростання картону загалом: виробництво картонної тари збільшилося на 16,6%, що становило 126 тис. тонн. У цілому нині цей період було виконано картону на 13,5% більше, як аналогічний період минулого року її, тоді як Мінекономрозвитку РФ прогнозує зростання виробництва картону 2002 року — на 11% (рис.3).
[pic].
На ринку відповідно до попитом, росте, і пропозицію картонної тари. Причому, аналітики прогнозують і подальше зростання виробництва. Найбільші виробничі центри цієї категорії продукції зосереджено Архангельської області, Алтайському і Красноярському краях — районах з оптимальним поєднанням виробничого і сировинного комплекса.
Але з зростанням на картонну тару підвищуються вимоги клієнтів до її якості. Високі стандарти якості характерні і світового фінансового ринку, де зі зниженням попиту, показник якості став особливо актуальним. Також зростає попит на якісну картонну тару і російському ринку. Природно, вимоги із боку клієнтів залежить від виду картонної упаковки, наприклад, вищі вимоги висуваються до індивідуальним упаковках, у цьому відіграє роль і товщина картону, його колір, однорідність, можливість нанесення краски.
Базуючись на вищесказаному, можна прогнозувати подальше динамічний розвиток целюлозно-паперової галузі загалом й інформаційного секторів картонної тари зокрема. Але як слідство збільшення сегмента ринку картонної тари очікується підвищення рентабельності підприємств, які працюють у напрямі, та його інвестиційної привлекательности.
Попри те що, що у останнім часом спостерігається витіснення пакувальних картонів полімерними матеріалами, у деяких сегментах галузі картони досі залишаються незамінними, з своїх переваг, таких як, можливість декорування і конструювання, невеличкий вагу, міцність. Картони порівняно недорогі, а головне, универсальны.
Картонна споживацька тара залишається, у Росії, високоефективним виглядом упаковки, і тому останні кілька років виробництво коробочного картону Російській Федерації збільшилася 3,5 раза.
Коробковий картон — це друге (після гофрокартону) вид картону, входить у групу тароупаковочного картону. Коробковий картон — це масовий вид картону, проте, його частка у загальному обсязі виробництва картону всіх видів нижче, ніж в гофрокартону (64%) і як близько 18%. Разом з тим, в ціннісному вираженні частка коробочного картону можна з гофрокартоном. Коробковий картон використовується виготовлення споживчої тари. Окремі марки коробочного картону можуть використовуватися виготовлення прокладок і решіток в картонні ящики. Для забезпечення високу якість упаковки необхідно суворо дотримуватися технологію виготовлення напівфабрикату усім дільницях його производства.
Сировиною виготовлення картону є білена целюлоза, макулатура й інші волокнисті напівфабрикати, відсоткове співвідношення для сировини не завжди однаковий, залежно від марки виготовленого картона.
Основна наматываемая продукція картон хром — ерзац макулатурний, готовий до виготовлення коробок, пачок і той споживчої тари з барвистій печаткою та без неї, випускається по ТУ 13−281 020−97−90 і коробковий картон виготовлення коробок без друку по ТУ 13−028−1020- 99−90 і СТП 2−63−91.
Картон хром — ерзац макулатурний має відповідати вимогою ГОСТ 7933.
Картон виготовляється наступних марок:
МО — крейдований для офсетного і типоофсетного способів печати.
МР — крейдований для глибокого способу печати.
М — не крейдований для офсетного, типоофсетного і високого способів печати.
Картон виготовляється в рулонах, в аркушах, в бобінах, в коробках чи пачках правильної геометричній форми, залежно від подальшого застосування. Розміри по ширині і діаметру рулонів і бобин і формати листового картону встановлюються за узгодженням із замовником. Картон повинен вироблятися з обрізаними крайками, що їх рівними і чистими. Кількість обривів має бути мінімальним і перевищувати встановлених стандартів. Ці вимоги мають забезпечувати проектируемым подовжньорезательным станком.
З іншого боку, продольно-резательные верстати повинні задовольняти наступним требованиям:
— надежность;
— безпека продукції та зручність обслуживания;
— эргономичность конструкции;
Виконання усіх перелічених вище вимог до продольно-резательным верстатів забезпечує надійну роботу устаткування й високу якість картонних напівфабрикатів. Що у своє чергу позитивно впливає конкурентоспроможність своєї продукції, як на, і на зарубіжні ринки сбыта.
2. Техніко-економічне обгрунтування проекта.
2.1. Загальні сведения.
Для друкування і переробки папери повсюдно застосовують ротаційні машини, у зв’язку з цим у загальному виробництві папери рольова папір займає місце. Деякі види папери (газетна, мішкова, кабельна та інших.) майже зовсім випускаються в рулонах. Рольова папір, не подвергающаяся опорядженні на суперкаландре, з накату папероробної машини краном передається на встановлений за нею продольно-резательный станок.
Раніше цидулка із накату надходила на перемоточно-сортировочный верстат. У цьому верстаті, що має лише гуркіт і накат, здійснювалася перемотування папери, склейка обривів й дуже звана сортування (видалення бракованих ділянок полотна). Нині потреба у установці перемотносортувальних верстатів відпала внаслідок поліпшення якості намотки рулонів і зменшення кількості обривів на папероробної машины.
Продольно-резательные верстати — найбільш швидкохідні із усіх машин паперового виробництва: їхнє сягає 1500 — 1800 м/мин, а окремих випадках більш 2400 м/мин. Усі вали цих верстатів мали бути зацікавленими динамічно врівноважені і перевірені на критичну скорость.
Найбільш доцільною щодо загальної компонування і маневрування під час роботи є підставою установка одного продольно-резательного верстата на одну бумагоделательную машину. І тут продуктивність верстата має відповідати продуктивності папероробної машини, для якій він призначений, плюс достатній розрив, ніж лімітувати її работу.
До конструкції продольно-резательного верстата пред’являються вимоги рівномірної щільності намотки рулонів, чистоти і порядку гладкості їх торцевих поверхонь, легкого поділу рулонів (не залучаючи клинів), зручною і швидкої заправки папери, механізованого знімання і опускання рулонів і безпеки роботи з станке.
2.2. Схеми продольно-резательных станков.
Продольно-резательные верстати, що з’явилися ще наприкінці ХІХ століття, поділяються на два типу: периферичної і комбінованої намотки. У верстатах першого типу наводяться у обертання які мають вали, куди спирається наматываемый рулон, як і забезпечує периферичну намотку. Іноді, при швидкості понад 800 — 1000 м/мин, встановлюють окремі електродвигуни для приводу прижимного і ножового валів, але ці не змінює самого принципу наматывания.
На верстатах з комбінованої намоткой приводними не є лише які мають вали, а й наматываемый рулон. У цих верстатах одночасно використовуються принципи осьової і периферичної намотки. Щільність намотки на цих верстатах можна регулювати широтою діапазону, від тугий до м’якої (в межах як одного, і різних рулонів). І тому потрібно змінити ставлення крутящих моментів, переданих несучим валам і наматываемому рулону, і навіть величину лінійного тиску між рулоном і несучими валами. Співвідношення крутящих моментів змінюють з допомогою електродвигунів, встановлених на намоточном і несучих валах, чи у вигляді механічного диференціала з гальмом одному з несучих валів. Верстати з комбінованої намоткой не знайшли поширення через складність їх конструкції. Вони застосовуються лише за необхідності перематывания однією й тому самому верстаті різних видів папери, потребують як тугий, і м’якої намотки.
Багато наявних схем периферичної намотки то, можливо зведено до двох принциповим схемами: з верхньої та нижньої заправкою папери. Верстати з верхньої заправкою мають кілька основних конструктивних решений:
і з ножовим валом, які є і прижимным (рис. 2.2.1).
Рис. 2.2.1 Схема продольно-резательного верстата з верхньої заправкою з ножовим валом;
1- разматываемый рулон; 2 — бумаговедущий вал; 3 — механізм подовжньої різання; 4 — що має вал; 5 — наматываемый рулон.
з ножовим валом і окремо встановленим прижимным валом (рис. 2.2.2).
Рис. 2.2.2. Схема продольно-резательного верстата з верхньої заправкою з ножовим валом і окремо встановленим прижимным валом;
1- разматываемый рулон; 2 — бумаговедущий вал; 3 — механізм подовжньої різання; 4 — що має вал; 5 — наматываемый рулон; 6 — прижимной вал.
в) з окремо розташованими ножами і двома бумаговедущими валами доі після механізму подовжньої різання (рис. 2.2.3).
Рис. 2.2.3 Схема продольно-резательного верстата з верхньої заправкою з окремо розташованими ножами і двома бумаговедущими валами доі після механізму подовжньої резки;
1- разматываемый рулон; 2 — бумаговедущий вал; 3 — механізм подовжньої різання; 4 — що має вал; 5 — наматываемый рулон; 6 — прижимной вал.
На всіх верстатах з верхньої заправкою папери разматываемый рулон встановлюють на тамбурному устрої, де є гальмо, створює необхідне натяг папери. Папір заправляється згори по бумаговедущим валикам і расправочной дузі, проходить механізмом подовжньої різання, огинає прижимной вал і намотується на намоточный валик. Наматываемый рулон спирається на два приводних несучих валу. У міру збільшення діаметра наматываемого рулону вісь його переміщається догори. Поруч із рулоном переміщаються прижимной вал і механізм подовжньої резки.
Верстати з нижньої заправкою мають багато конструктивних рішень. Частіше застосовуються такі схеми станков:
і з заправкою між несучими валами і окремо що стоять (рис. 2.2.4).
Рис. 2.2.4 Схема продольно-резательного верстата з нижньої заправкою між несучими валами і окремо що стоять ножами;
1- разматываемый рулон; 2 — бумаговедущий валик; 3 — механізм подовжньої різання; 4 — що має вал; 5 — наматываемый рулон; 6 — прижимной вал.
з заправкою на передній що має вал і з ножовим валом, розташованим під несучими валами (рис 2.2.5).
Рис. 2.2.5 Схема продольно-резательного верстата з нижньої заправкою на передній що має вал і з ножовим валом;
1- разматываемый рулон; 2 — бумаговедущий валик; 3 — механізм подовжньої різання; 4 — що має вал; 5 — наматываемый рулон; 6 — прижимной вал; 7 — расправочная дуга; 8 — транспортер для заправки бумаги.
в) з пневматичній заправкою і ножовим валом, розташованим попереду несучих валів (рис. 2.2.6).
Рис. 2.2.6 Схема продольно-резательного верстата з нижньої заправкою з пневматичною заправкою і ножовим валом;
1- разматываемый рулон; 2 — бумаговедущий валик; 3 — механізм подовжньої різання; 4 — що має вал; 5 — наматываемый рулон; 6 — прижимной вал.
На верстатах з нижньої заправкою папір разматываемого рулону заправляється знизу по бумаговедущим валикам, проходить через стаціонарно встановлений механізм подовжньої різання, огинає передній що має вал чи заправляється між несучими валами і намотується на намоточный валик.
Розглянемо переваги та недоліки принципової схеми верстатів з верхньої та нижньої заправкою. Слід зазначити, і що якість роботи верстата залежить тільки від його схеми, а й від конструкції й надійності роботи основних його вузлів. При виборі схеми верстата треба враховувати зручність заправки і склейками папери, вплив схеми на якість намотки і поділ рулонів й умови безпеки роботи з станке.
Перевагою верстатів з верхньої заправкою є зручна заправка папери. І тут зайвими високо встановлювати які мають вали і плануємо влаштовувати поглиблення під верстатом, як це подекуди доводиться робити за верстатах з нижньої заправкою. При великих діаметрах наматываемого рулону заправка папери на верстаті з верхньої заправкою при обриві полотна на рулон діаметром більше 1000 — 1200 мм скрутна через високого розташування механізму подовжньої різання. Зазвичай. Рулони краще поділяються на верстатах з нижньої заправкою через стаціонарного розташування цих верстатах механізму подовжньої різання (на відміну верстатів з верхньої заправкою, де цей механізм принаймні намотування рулону переміщається догори). Стаціонарне розташування механізму подовжньої різання зменшує можливість осьового переміщення ножів, що виключає чи зменшує нахлестывание крайок полотна папери, і полегшує поділ рулонів. На верстатах з нижньої заправкою легше здійснити автоматичну (повітряну) заправку папери через стаціонарного розташування зони контакту рулону з несучим валом, де паперове полотно починає намотуватися на рулон.
При виборі схеми верстата слід обов’язково враховувати умови безпеки роботи з ньому. До небезпечним обслуговуючого персоналу ділянками. Де можливо потрапляння руки між валами, на верстатах з верхньої заправкою ставляться: ділянку контакту прижимного (ножового) валу з рулоном, де папір при обриві заправляють вручну, й ділянку контакту рулону з несучим валом з задньої боку станка.
На верстатах з нижньої заправкою небезпечним ділянку контакту рулону з переднім несучим валом. Тут, проте, можна встановити відкидне огородження, у якому робота на таких верстатах менш опасна.
Найкращі умови безпеки забезпечені на верстаті з нижньої заправкою, за наявності повітряної заправки, яка виключає ручну заправку папери на які мають вали, небезпечна лише зона контакту рулону з верхнім прижимным валом. Проте за роботі верстата не потрібно підправляти папір у цьому участке.
Усі нові верстати виготовляються з нижньої заправкою, бо за інших рівних умов стаціонарне розташування механізму подовжньої різання забезпечує краще поділ разрезаемых рулонов.
2.3. Основні вузли продольно-резательных станков.
2.3.1. Гуркіт і гальмо рулона.
З метою зменшення кількості наматываемых рулонів на папероробної машині й разматываемых рулонів на продольно-резательном верстаті діаметр наматываемого рулону на накаті папероробної машини сягає 2000 — 2400 мм. Разматываемый рулон папери діаметром до 2400 мм встановлюють на стійках, званих розкатом. Для отримання по обидва боки паперового полотна однаковою ширини обрезаемых крайок рулон може переміщатися воль своєї осі. На верстатах старої конструкції рулон переміщається щодо стійкий. На сучасних верстатах для більшої жорсткості системи стійки переміщаються щодо шин. Поруч із ручним переміщенням рулону застосовується й автоматичне з допомогою пневматичного регулятора з соплом. Струмінь повітря певного тиску потрапляє на чутливу мембрану. Зміщення крайки полотна перекриває струмінь повітря, що змінює тиск на мембрану. Це передається пневматичним циліндрам, перемещающим разматываемый рулон в осьовому напрямі. З цією самі цілі застосовуються і фотоелектричні регулятори. Принцип їхньої дії будується на зміні кількості відображеного світла від крайки папери під час усунення полотна. Цей імпульс передається электродвигателям, смещающим рулон в осьовому напрямі. Автоматичні устрою для осьового усунення рулону дозволяють працювати з не меншою шириною обрезаемой крайки (5−10 мм замість 20- 25 мм при ручному регулировании).
Підшипник з лицьової боку тамбурного валу можна переміщати перпендикулярно осі рулону. Це дозволяє визначити рулон як паралельно, і непараллельно несучим валам. Необхідність в непараллельной установці рулону виникає тоді, коли той кінець намотаний слабше, ніж другой.
Для хорошої якості намотки рулону і сталої роботи верстата натяг паперового полотна при наматывании має підтримуватися постійним. Розмір лінійного натягу залежить від міцності папери, зумовленої її розривної довжиною і весом.
Лінійне натяг папери на продольно-резательном верстаті зазвичай, у 5- 10 разів менша разрывного усилия.
На рис. 2.3.1, за даними фірми Блэк-Клозон, наведено графік залежності лінійного натягу папери, і картону ваги 1 м².
Рис. 2.3.1. Графік залежності лінійного натягу папери, і картону від ваги 1 м².
Натяг паперового полотна створюється з допомогою гальма, з'єднаний з тамбурным валом рулону. Щоб при обриві полотна на верстаті мінімізувати довжину размотанной папери, з допомогою цього ж гальма швидко зупиняють разматываемый рулон.
На продольно-резательных верстатах застосовують три типу гальм: механічні, вакуумні і електричні. З механічних гальм на широких верстатах частіше застосовують дискові гальма, але в вузьких — ленточные.
Дисковий гальмо (рис. 2.3.2) має нерухомий корпус, охлаждаемый проточній водою. На валу, вільно що проходить всередині корпусу, на направляють шпонках встановлено диски. Вони притискаються до торцевим поверхням корпусу з допомогою гвинтової і червячной передачі й маховика, розташованого із боку обслуговування верстата. З допомогою виделки чи муфти гальмівний вал з'єднаний із разматываемым рулоном.
Рис. 2.3.2. Схема дискового гальма продольно-резательного станка:
1- вал; 2 — корпус; 3 — диск; 4 — спрямовуюча півень; 5 — прокладка; 6 — куди входять муфта; 7 — тамбурный валик; 8 — маховик для притискання дисків; 9 — червячная передача; 11 — рычаг.
Натяг папери буде постійним при зменшенні гальмівного моменту по мері розмотування рулону. І тому на механічних гальмах необхідно вручну зменшувати зусилля притискання дисків, що ускладнює експлуатацію верстата. При обриві полотна папери гальмівний момент необхідно швидко вручну збільшити до якомога більшої предела.
Вакуумний гальмо є ящик, у якому створюється вакуум 0,19 — 0,39 кПа. Паперове полотно, що відбувається над ящиком, під впливом вакууму притискається для її поверхности.
Натяг папери залежить від радіуса разматываемого рулону і постійний за незмінної вакуумі. Слід враховувати. Що, крім вакуумного гальма, необхідно встановити що й механічний гальмо для гальмування разматываемого рулону при обриві бумаги.
Найкращим є електричне гальмування, здійснюване генератором постійного струму, сполученим з тамбурным валиком разматываемого рулону. Гальмівний генератор (рис. 2.3.3) при постійної лінійної швидкості папери розвиває постійну потужність незалежно від кутовий швидкості рулону і підтримує постійне натяг полотна.
Рис. 2.3.3. Гуркіт з гальмівним генератором:
1 і 2 — стійки розкату з лицьової і приводний сторін; 3 — маховик для переміщення рулону перпендикулярно його осі; 4 — тамбурный вал; 5 — разматываемый рулон; 6 — електродвигун з редуктором для переміщення рулону вздовж його осі; 7 — виделка для сполуки тамбурного валу з редуктором гальмівного генератора; 8 — редуктор; 9 — гальмівний генератор
Необхідна величина натягу регулюється з допомогою реостату. При обриві паперового полотна гальмівний генератор автоматично і швидко гальмує рулон. При заправці папери гальмівний генератор працює як розгінний двигун, унаслідок чого зменшується натяг папери, і зайвими в розвороті рулону, як із заправці вручну. Гальмівний генератор рекуперирует до 50−60% споживаної верстатом мощности.
Потужність гальмівного генератора раніше зазвичай вибирали з умови створення необхідного натягу папери під час роботи верстата. У період гальмування рулону при обриві полотна генератор працювали з 2−3 — кратною перегрузкой.
Встановлювати гальмівний генератор, з потужності, потребной для гальмування рулону під час обриву (з урахуванням 3−4 — кратної перевантаження), недоцільно, оскільки його потужність буде значної. Працюючи такий генератор буде завантажений лише з 15−20%, внаслідок чого воно буде малочувствительным до регулюванню. Тому поруч із гальмівним генератором доцільно встановлювати додатковий механічний гальмо, автоматично включающийся при обриві полотна, і навіть збільшити тривалість гальмування до 20−30 секунд. Збільшення тривалості гальмування не викликає значних втрат папери. Спостереження, проведені у виробничих умовах, показали, вага размотанной папери значно менше теоретично обчисленого по середньої швидкості і тривалості гальмування, оскільки через 2−3 секунди від початку гальмування папір большє нє скидається з рулону, а утворюються лише кілька десятків витків слабко намотаної папери, які потім зривають з рулона.
Коли у період розгону верстата, під час переходу від заправної до робочої швидкості, не передбачено примусовий привід разматываемого рулону, то полотні папери виникає додаткове натяг, яке підсумовується з натягом, створюваним гальмівним генератором.
Щоб уникнути виникнення великих динамічних натяжений при високих швидкостях верстатів і великих діаметрах разматываемого рулону необхідно або збільшити тривалість розгону до 90−120 секунд, або примусово приводити у обертання разматываемый рулон під час розгону станка.
Збільшення тривалості розгону недоцільно. Бо за цьому зменшується продуктивність верстати й збільшується цикл намотки. Доцільно, щоб у період розгону верстата гальмівний генератор працював у ролі розгінного двигателя.
Задля підтримки заданого натягу паперового полотна під час розгону й досвід роботи верстата постійним застосовується у ролі датчика пружинний бумаговедущий валик, переміщення якої визначається натягом бумаги.
2.3.2. Механізм подовжньої резки.
Одне з найважливіших вузлів верстата є механізм подовжньої різання. Якщо це механізм забезпечує рівний і гладкий рез, то рулони легко поділяються; ще, зменшується запиленість папери при печатании.
На продольно-резательных верстатах застосовують два методу різання: по принципу ножиць й під тиском. При краянні за принципом ножиць (рис. 2.3.4) папір проходить між ріжучими крайками двох ножів: чашечного і дискового. Чашкові ножі насаджені на обертовому валу. На широких верстатах цей вал має додаткову опору посередині зменшення його прогину. На трубі, встановленої впоперек верстата, є важелі задля зміцнення осей, на яких обертаються дискові ножи.
Рис. 2.3.4 Різка за принципом ножниц:
1 — вал нижніх ножів; 2 — підшипники валу; 3 — шестірня для приводу валу; 4 — нижній чашкове ніж; 5 — верхній ніж; 6 — ексцентрична вісь дискового ножа; 7 — підшипники верхнього ножа; 8 — спіральна пружина для притискання ножа; 9 — рукоятка для вимикання верхнього ножа; 10 — кронштейн верхніх ножей.
Они притискаються до чашечным ножам з допомогою пружин і наводяться у обертання тертям. Ножі відповідно необхідного формату (довжині) рулону встановлюють з точністю до [pic]перемещением чашечных ножів за валом і дискових — по трубі. Кількість встановлюваних ножів (4−8) залежить від заданої довжини рулонів. На верстатах з верхньої заправкою вал чашечных ножів наводиться у обертання ремінної чи ланцюгової передачею від прижимного валу, лежачого на рулоні, але в верстатах з нижньої заправкою — від несучих валів чи то з ближайщего бумаговедущего валика. Для отримання більш чистого і рівного реза швидкість ножів мусить бути на 10−20% вищою за швидкість руху бумаги.
При краянні методом тиску (рис. 2.3.5) паперове полотно охоплює нижній ножовий вал, якого верхні дискові ножі притискаються пружинами чи пневматичним устройством.
Рис. 2.3.5. Різка давлением:
1 — труба ножового валу; 2 — патрон; 3 — цапфа; 4 — корпус підшипника; 5 — підшипник; 6 — ножове кільце; 7 і побачили 8-го — гайка і контргайка ножового валу; 9 — верхній дисковий ніж; 10 — вісь верхнього ножа; 11 — підшипники верхнього ножа; 12 — важіль верхнього ножа; 13 — пружина для притискання ножа; 14 — кронштейн верхніх ножів; 15 — труба для установки кронштейнов Ножевой вал — трубчастий, нею прикріплять сталеві загартовані кільця високої твердості. На верстатах з верхньої заправкою ножовий вал, одночасно який є також прижимным, лежить на жіночих рулоні, приводящем його у обертання. На верстатах з нижньої заправкою ножовий вал наводиться у обертання від несе валу, іноді для приводу ножового валу встановлюють окремий электродвигатель.
Метод різання за принципом ножиць, який би чистіший і гладкий рез ще більшу зносостійкість ножів, поширений більше, ніж метод різання тиском. При краянні методом тиску утруднений добір співвідношення величин твердості кілець і дискових ножів. Якщо твердість кілець вище твердості ножів, останні затупляются. При зворотному співвідношенні величин твердості на кільцях утворюються риски.
Чашкові і дискові ніж виготовляють з хромонікелевої сталі, яка має високої износоустойчивостью. Твердість чашечных ножів по Роквеллу Rc = 58 (60, дискових Rc = 53 (55. При краянні папери без наповнювача ножі затачивают через 4 — 8 місяців. За наявності папері наповнювачів термін їхньої служби ножів скорочується більш як вдвое.
Компонування верстати на значною мірою залежить від прийнятого методу різання. При краянні за принципом ножиць папір неспроможна охоплювати ножовий вал, яким у окремих місцях розташовані чашкові ножі. І тут незалежно від виду заправки (верхньої чи нижньої) необхідно, щоб паперове полотно при розрізуванні перебував у натягнутому стані у прямому ділянці. Що досягається установкою двох валиків: бумаговедущего — до ножів, і прижимного — після нього (на верстаті з верхньої заправкою) чи двох бумаговедущих валиків (на верстаті з нижньої заправкой).
При краянні методом тиску папір може охоплювати нижній ножовий вал, у якому у всій його довжині прикріплять кільця. І тут кількість бумаговедущих валиків зменшується однією або двоє. Переваги ножового валу особливо за верстатах з верхньої заправкою, де механізм подовжньої різання розташований над наматываемым рулоном і переміщається догори зі збільшенням діаметра рулону. При краянні методом ножиць бумаговедущий і прижимной вали збільшують розміри і ваги переміщаються вузлів. Ножовий вал на верстатах з верхньої заправкою здійснює і функцію прижимного, унаслідок чого число валів зменшується і спрощується компонування станка.
Для використання за компонуванні верстата переваг різання методом ножиць і ножового валу створена конструкція ножового валу, на кільцях якого є сім — вісім ножових канавок (рис. 2.3.6) (за наявності семи-восьми ножових канавок, используе ;
Рис. 2.3.6 Ножовий вал:
1 — труба ножового валу; 2 — патрон; 3 — цапфа; 4 — корпус підшипника; 5 — підшипник качения; 6 — кришка підшипника; 7 і побачили 8-го — затяжна гайка і контргайка ножового валу; 9 — суцільне кільце; 10 — разъемное ножове кільце; 11 — верхній дисковий ніж; 12 — вісь дискового ножа; 13 — спіральна пружина для притискання ножа; 14 — рукоятка для вимикання верхнього ножа мых по черзі, ножові кільця можна шліфувати значно рідше, аніж за звичайних ножах). Верхній дисковий ніж зтикається з що краючою поверхнею ножовий канавки. Кільця з ножовими канавками (ножові кільця) може бути суцільними чи разъемными. Рознімні ножові кільця закінчуються конічними чи циліндричними хвостовиками, які входять у выточки суцільних кілець. Усю систему разъемных ножових і суцільних кілець закріплюють на валу з допомогою затяжних гайок. При зміні формату папери затяжні гайки отвинчивают на подвійну довжину хвостовика, знімають рознімні ножові кільця, зрушують суцільні кільця і встановлюють ножові кільця у необхідних місць за довжині валу. Проте виготовлення і шліфовка разъемных ножових кілець дуже складні. Тому часто їх роблять суцільними, а проміжні кільця — разъемными.
На нових подовжньо — різальних верстатах суцільні ножові кільця закріплюють з допомогою шпонок, переміщаються під тиском пневматичних шлангів (рис. 2.3.7).
Ножові кільця встановлено на основі всієї довжині валу. Зазор між кільцями дорівнює 8 — 10 мм. Оскільки кільцях є сім — вісім ножових канавок, то, при зміщення кілець на величину зазору можна розрізати полотно папери на рулони потрібної ширины.
При розрізуванні товстої папери малого об'ємного ваги на верстатах з верхньої заправкою канавки ножового валу, спирається на наматываемый рулон, залишають на папері відбитки. Тож такого паперу встановлюють окремий прижимной вал, від якої наводиться у обертання ножовий вал з допомогою клиноременной передачи.
Механізм подовжньої різання мають якнайближче до наматываемому рулону. Цим избегается можливе бічне усунення разрезаемых смуг папери за її русі. При зміщення смуг крайки полотен папери нахлестываются друг на друга, що перешкоджає поділ рулонів. Іноді щоб уникнути зазначеного усунення смуг перед наматываемым рулоном встановлюють роздільники (тонкі платівки) чи сферичні наконечники, які сприяють кращому поділу рулонов.
Рис. 2.3.7 Ножовий вал з пневматичним закріпленням нових колец:
1 — цапфа; 2 — підшипники; 3 — труба валу; 4 — пневматичний шланг; 5 — клавіша; 6 — суцільне ножове кільце; 7 — ніпель на шляху подання повітря; 8 — кінцеві втулки.
Зусилля різання для папери вагою 50 — 60 г/м2 вбирається у 0,98 — 2,94 М однією рез. Потужність, потрібна для різання папери, дуже мала і його при розрахунках пренебрегают.
Обрізані крайки паперового полотна видаляються спеціальним вентилятором, у якому є диск, розрив крайки. Вентилятор спрямовує крайки трубопроводами в размольный агрегат.
2.3.3. Механізми регулювання тиску між рулоном і несучими валами.
Збільшення діаметра наматываемого рулону значно підвищує продуктивність як продольно-резательных верстатів, а й машин, на якої використовуються рольова папір (наприклад, друкарський, мішкова і ін.), тому помітна тенденція збільшення діаметра наматываемого рулону до 1500 мм до 1800 мм. Проте за збільшенні діаметра рулонів повинні бути враховані умови для їхньої транспортування й можливості використання таких рулонів потребителями.
Щільність намотки рулонів на продольно-резательном верстаті переважно визначається лінійним тиском між рулоном і несучими валами. Тиск між рулоном і прижимным валом надає менший вплив на щільність намотки, оскільки багато часу намотування воно менше, ніж тиск між рулоном і несучими валами. Щільність намотки рулонів на подовжньорізальних верстатах вище, ніж накатах, через більшого лінійного тиску між рулоном і несучими валами і наявність двох несучих валів, створюють дві зони контакту з-поміж них і рулоном.
Тиск між рулоном і несучими валами за відсутності механізму регулювання зростає зі збільшенням діаметра рулону, хоча у меншою мірою, ніж вагу рулона.
Задля більшої необхідного лінійного тиску в початковий період намотки, коли вагу намотаної паперу на рулоні значний, застосовується прижимный валик.
Донедавна папір намотували лише з картонні гільзи зовнішнім діаметром 90 — 95 мм, одягнені на намоточный валик діаметром 70 мм. Намоточный валик є тонкостенную трубу з запрессованными по кінців цапфами. Після закінчення намотки рулону намоточный валик потім із нього витягують, що одній з важкі крейсери та досі майже механізованих операцій. На деяких верстатах механізація цієї операції зводиться до того що, що рулон разом із намоточным валиком опускають на транспортер, намоточный валик одним кінцем прикріплюють до спеціальної стійці отже транспортер, рухаючись разом із рулоном, стаскивает його з намоточного валика. Для зменшення зусилля витягування намоточного валика з рулону папери почали застосовувати розсувні трубчасті валики. Вони складаються з трьох-чотирьох секторів, які спираються гумовий шланг, куди для розсування валика подають повітря; при витягуванні валика повітря выпускают.
На Балахнинском комбінаті вперше почали застосовувати бесштанговую намотку, значно яка полегшує умови роботи з верстаті. І тут гільзи вільно надягають на дерев’яну качалку, довжина чим 100−150 мм менше загальної довжини рулонів. З торців гільзи затискаються конусами, обертовими на підшипниках качения. Погіршення якості намотки при бесштанговой намотке немає. У початковий період намотування при малому тиску прижимного валу великому натягу папери були поодинокі випадки викидання намотаного рулону. Проведені аналітичні дослідження свідчать, що найбільша можливість викидання рулону — на верстатах з верхньої заправкою, бо за таку схему горизонтальні складові окружних зусиль із боку несучих валів на рулон і рівнодіюча натягу папери діють у тому самому напрямку. На верстатах з нижньої заправкою це діють у різних напрямках, що практично нічого виключає можливості викидання наматываемых рулонов.
При діаметрі наматываемого рулону 1500 і 1800 мм лінійне тиск рулону на що має вал від власної ваги рулону становить 4,9 і 7,85 кН/м. Зменшити це тиск при бесштанговой намотке не можна, оскільки наматываемый рулон може бути вивішено. Навіть за наявності намоточного валика зусилля вивішування неспроможна зменшити лінійне тиск більш ніж на 0,98 кН/м через значних напруг вигину, що виникають у намоточном валике.
Якість намотки рулонів великого діаметра вистачає задовільним. У зв’язку з цим можна вважати, що щільністю намотки і лінійним тиском немає прямолінійною залежності. Мабуть, після певного лінійного тиску (може бути 2,94 — 3,92 кН/м) подальше його підвищення майже збільшує щільності намотки. Тому доцільно, щоб прижимной вал на початку намотки забезпечував лінійне тиск між рулоном і несучими валами 2,94 — 3,92 кН/м. Принаймні збільшення діаметра рулону до 800−1000 мм прижимной валик вивішується відповідно збільшення ваги рулонів. У цьому вся інтервалі діаметра наматываемого рулону лінійне тиск зберігається приблизно постійною (2,94 — 3,92 кН/м). Потім за подальшому наматывании прижимный вал вивішується постійно і внаслідок збільшення ваги рулону лінійне тиск між рулоном і несучими валами зростає до 4,9 — 7,85 кН/м.
На сучасних продольно-резательных верстатах застосовуються пневматичні і гідравлічні механізми вивішування прижимного валу. Так як у процесі збільшення діаметра рулону зусилля вивішування має зростати, встановлюються програмні регулятори давления.
Прижимной вал (а верстатах з верхньої заправкою — і механізм подовжньої різання) необхідно підняти на 50−100 мм, щоб було скотити рулон з несучих валів. Після укладання на які мають вали картонних гільз опускається прижимной вал. Піднесення і опускання прижимного валу раніше проводилися при допомоги маховика і ланцюгової передачі, але в сучасних верстатах — з допомогою циліндрів механізму вывешивания.
2.3.4. Які Мають валы.
Які Мають вали продольно-резательных верстатів є чавунні чи сталеві труби (рис. 2.3.8) діаметром 400−600 мм, залежно від ширини верстата, і на 150−200 мм більше ширини паперового полотна, що надходить на продольно-резательный верстат. Для полегшення врівноважування валів труби всередині растачивают. Відносний прогин робочої частини несучих валів не повинна перевищувати 1/10 000 — 1/12 000. Відстань між центрами несучих валів на 10−15 мм більше діаметра валу. За такої близькому відстані паперові (картонні гільзи), укладываемые на які мають вали, на початку намотки не заклиниваются.
На деяких верстатах встановлено рифлені вали. Іноді рифленим є лише перший у процесі папери вал. Рифи є спіральні канавки — праві в одній половині валу за довжиною, так і ліві - на другой.
Рифи збільшують коефіцієнт тертя між рулоном і несучими валами і зменшують шум під час роботи верстата, і навіть сприяють видалення повітря між рулоном і несучими валами.
Слід враховувати, що з сталкивании намотаного рулону з подовжньорезательного верстата він спирається лише з передній що має вал. Це подвоює навантаження на вал, але це навантаження є статичної, оскільки у її вплив вал не обертається, тому допущені напруги вигину може бути повышены.
Рис. 2.3.8. Які Мають валы:
1 — циліндр; 2 — диск зварного патрона; 3 і 4 — цапфы з лицьової і приводний сторін; 5 — щиток; 6 — підшипник качения; 7 — еластична муфта.
2.3.5. Прихід і споживана мощность.
У продольно-резательных звичайній (некомбинированной) намотки наводяться у обертання обидва несучих валу. При швидкості верстатів понад 1000 м/мин привід мають ще бумаговедущие прижимный і ножовий вали, що зменшує напруга в бумаге.
Під час роботи верстата тягові зусилля задля обертання бумаговедущего і ножового валів невеликі, і коли ці вали наводяться у обертання паперовим полотном, то додаткове натяг, що у паперовому полотні, не перевищує 0,0098 — 0,0196 кН/м однією валик. З іншого боку, цих умовах під час переходу від заправної до робочої швидкістю період розгону в полотні виникає додаткове динамічний натяжение.
Оскільки продольно-резательном верстаті є кілька бумаговедущих валиків, сумарне динамічний натяг може сягнути 0,392 — 0,49 кН/м, що неприпустимо. Цим і пояснюється необхідність приводу бумаговедущего і ножового валів на швидкохідних станках.
Для швидкого зупинки бумаговедущих валів при обриві паперового полотна на нових верстатах встановлено механічні гальма з пневматичним управлінням, розташовані всередині валу на приводний стороне.
Заправочну швидкість продольно-резательных верстатів зазвичай дорівнює 20−25 м/мин. Збільшення швидкості спрощує електричну схему приводу, але утрудняє заправку. Межа регулювання робочої швидкості становить 1:3 і 1:5. Перехід з заправної на робочу швидкість і підвищення робочої швидкості мали бути зацікавленими плавними. У старих конструкціях від електродвигуна наводився у обертання один що має вал, а другий — ремінної передачею першого. Проте через малого межцентрового відстані умови роботи ремінної передачі несприятливі, тому другий що має вал часто фактично наводився у обертання від рулону, а чи не від ремінної передачі. Більше досконалим є привід (рис. 2.3.9) при помощи.
Рис. 2.3.9. Прихід несучих валів від однієї электродвигателя:
1 і 2 — перший і другий які мають вали; 3 — редуктор; 4 і п’яти — провідна і відома шестерні; 6 — електродвигун редуктора, приводная шестірня якого з'єднана разом з двома зубцюватими колесами, натягнутими на цапфы несучих валов.
Велика щільність намотки рулонів характеризується швидкості другого по ходу папери несе валу, дещо більшій за (на 1−2%) швидкість першого несе вала.
На сучасних верстатах співвідношення швидкостей несучих валів регулюються з двох електродвигунів (рис. 2.3.10), встановлених за одним кожному несущому валу.
Рис. 2.3.10. Прихід несучих валів двох электродвигателей:
1 і 2 — перший і другий які мають вали; 3 — редуктор; 4 і п’яти — провідна і відома шестерні; 6 — электродвигатель.
Потужність між електродвигунами валів у разі розподіляється нерівномірно: двигун другого несе валу, який має більшу швидкість, споживає ще більшу мощность.
Регулювання щільності намотки зміною співвідношення швидкостей найефективніше на верстатах з нижньої заправкою, коли кут охоплення папером першого у процесі папери несе валу становить відповідно 1800 і 900, через відсутність ковзання між папером й першим несучим валом окружна швидкість рулону у разі дорівнюватиме окружної швидкості першого несе валу. Вища швидкість другого у процесі папери несе валу збільшить у своїй щільність намотки. На верстатах з верхньої заправкою і верстатах з нижньої заправкою малим кутом охоплення папером несе валу окружна швидкість рулону приблизно дорівнює полусумме окружних швидкостей несучих валів. Тоді окружна швидкість першого несе валу буде набагато меншою швидкості рулону, а другого несе валу — більше неї. У цьому випадку різна швидкість несучих валів не надасть помітного впливу щільність намотки.
Для швидкого зупинки верстата на сучасних верстатах застосовують электродинамическое гальмування електродвигунів. Для можливості зупинки наматываемого рулону у певному становищі відповідно місцеві склейками полотна папери встановлюється невеличкий механічний гальмо одному з несучих валов.
В багатьох випадках для опоряджувальних машин доцільна установка гідравлічних чи механічних варіантів (редукторів зі змінним передаточным числом). Вартість вариаторов нижче від вартості електродвигунів постійного струму з генераторами, а коефіцієнт корисної дії їхня вища і обслуговування проще.
Довжина намотаної папери (в метрах) враховується лічильником метражу, сполученим із несучим валом. При обриві паперового полотна электромагнитная муфта виключає лічильник. Імпульс для вимикання служить зміна сили струму, споживаного електродвигуном станка.
На подолання тертя в гальмі разматываемого рулону, т. е. на створення натягу полотна папери, витрачається до 60−80% використаної усією верстатом потужності. Чим більший натяг папери, тим більше коштів частка потужності, расходуемой на натяг, оскільки інша споживана потужність майже залежить від натягу бумаги.
Потужність, споживану продольно-резательными верстатами, визначають методом тягових усилий.
2.3.6. Механізми зіштовхування і опускання рулона.
Після намотки рулон необхідно зіштовхнути з несучих валів, опустити не підлогу та поцупити з нього намоточный валик чи дерев’яну качалку при бесштанговой намотке. Краном знімати рулон неможливо через малого діаметра цапф намоточного валика і розташування над рулоном прижимного валу. Замість які застосовувались раніше на вузьких верстатах ручного сталкивателя рулонів на сучасних верстатах встановлюють механічні чи гідравлічні сталкиватели.
Механізм зіштовхування (рис. 2.3.11) на сучасних станках.
Рис. 2.3.11. Механізм сталкивателя рулона:
1 — які мають вали; 2 — наматываемый рулон; 3 — циліндр; 4 — поперечний валик; 5 — поршень; 6 — шток і двох циліндрів, шарнірно закріплених на станинах. З штоками циліндрів пов’язаний валик. Розташований впоперек верстати й упирающийся при сталкивании в рулони бумаги.
Кілька похиле розташування циліндрів зменшує зусилля зіштовхування. Для верстата шириною 4200 мм при діаметрі циліндра 100 мм необхідне тиск повітря на циліндрі вбирається у 5 ати.
Найбільше застосування мають два устрою для опускання рулонів: прийомний харчування і опускающиеся лапы.
Перше пристрій (рис. 2.3.12) складається з приймального столу, який піднімається штоком циліндра. Повітря при підйомі стола.
Рис. 2.3.12. Механізм опускання рулону (прийомний стіл піднімається штоком цилиндра):
1 — які мають вали; 2 — намотаний рулон; 3 — прийомний стіл; 4 — циліндр; 5 — поршень; 6 — тяги, обмежують висоту підйому; 7 — выдвижная балка для перекатывания рулона.
подается у внутрішнє пустотілу частина поршня і крізь отвори, наявні в дні поршня, вступає у циліндр. Опускається прийомний стіл під впливом власної ваги та значимості рулону папери. Повітря у своїй витісняється у внутрішню пустотілу частина поршня, звідки по трубі випускається через вентиль в атмосферу.
Друге пристрій (рис. 2.3.13) складається з лап, розташованих впоперек верстата з відривом 800 — 1000 мм друг від одного й закріплених на наскрізному поперечному валу. Після закінчення намотки лапи піднімаються, ними зіштовхується рулон, потім, повертаючись, лапи опускають рулон на пол.
Рис. 2.3.13. Механізм опускання рулона:
1 — які мають вали; 2 — намотаний рулон; 3 — опускающиеся лапи; 4 — наскрізний поперечний вал; 5 — гідравлічний (пневматичний) циліндр; 6 — рулон, опущений на пол Сквозной вал повертається з допомогою гідравлічних (пневматичних) циліндрів чи то з електродвигуна з червячными редукторами.
2.4. Схема і несе спільний опис роботи проектованого станка.
Для проектованого верстата вибираємо таку принципову схему (рис 2.4.1).
[pic].
Рис. 2.4.1 Схема проектованого продольно-резательного верстата з нижньої заправкой;
1- разматываемый рулон; 2 — бумаговедущий валик; 3 — механізм подовжньої різання; 4 — що має вал; 5 — наматываемый рулон; 6 — прижимной вал; 7 — транспортер для заправки бумаги.
На подовжньо — резательном верстаті перемотується рулон картону, який із накату картоноробної машини. У процесі перемотування виробляється поздовжня різка на смуги стандартної ширини і намотка в рулони необхідного диаметра.
Процес переробки рулону на подовжньо — резательном верстаті полягає з цілого ряду послідовно виконуваних операцій. Рулон картону після виведення з накату картоноробної машини, встановлюється в стійках розкату. Корпусу підшипників тамбурного валу затискаються важелями з допомогою пневмоцилиндров; тамбурный вал сполучається з генератором приводу розкату муфтою включения.
Разматываемое з тамбурного валу полотно картону огинає бумаговедущий вал, відбувається за який апарату верхніми і нижніми ножами, огинає знизу що має вал. У цьому які мають вали і бумаговедущий вал працюють на рівні заправної швидкості і крайні верхні ножі перебувають у контакту з нижніми. Різка здійснюється за принципом ножиць. Для полегшення процесу проводки паперового полотна передбачено транспортер заправної. Після проводки полотна картону між несучими валами привід зупиняють. На які мають вали вкладають гільзи, затискають штоками кареток бесштанговой намотки і заправляють ними картон. Для расправления разрезаемого полотна перед несучими валами встановлено расправочный вал. Необхідна лінійне тиск між рулоном і несучими валами в початковий період намотки створюється прижимным валом. Щоб лінійне тиск залишалося приблизно постійним, зі збільшенням діаметра рулону, прижимной вал вивішується двома пневмоцилиндрами. Задля більшої безпечної роботи з верстаті встановлено огорожі. Після заправки полотна гільзи піднімають огородження, опускають прижимной вал, включають верхні ножі і вентилятор разрыватель. Верстат включають до роботи на заправної швидкості і упевнившись у нормальному ході процесу перемотування, розганяють до необхідного рівня робочої скорости.
На заправної швидкості верстат може працювати у опущеному огорожі рулону. Перехід на робочу швидкість і на робочої швидкості може функціонувати лише при піднятий ограждении.
Верстат за програмою розганяється, дбає про заданому рівні робочої швидкості і за досягненні необхідного діаметра рулону чи метражу паперу на рулоні, привід автоматично гальмується. Автоматичне управління окремими механізмами верстата здійснюється з допомогою кінцевих вимикачів, встановлених на станке.
Після зупинки верстата прижимной вал піднімається, розпрямляються штоки кареток бесштанговой намотки, вимикаються крайні верхні ножі, опускається огородження і стіл прийомний. Готові рулони зіштовхуються сталкивателем.
Задля більшої безперебійної роботи верстата встановлюється нагромаджувач. На нагромаджувач вкладаються рулони, котрі знімаються з накату машины.
3. Технологічні расчеты.
3.1. Визначення швидкості картоноробної машини по приводу.
По заданої продуктивності вибрати ширину машини та розрахувати робочу швидкість машини Vр:
[pic] де: Q — продуктивність машини, кг/сут, Q = 350 000 кг/сут b — ширина полотна на накаті, м, b = 4,2 м q — маса 1 м², г/м2, q = 300 г/м2 k1 — коефіцієнт завантаження роботи машини протягом доби (число годин фактичної роботи, зазвичай k1 = 22,5(23), год, k1 =22,5 k2 — коефіцієнт використання робочого ходу машини (облік неодружених ходів k2 = 0,95(0,98), k2 = 0,95 k3 — коефіцієнт виходу нетто товарної продукції з брутто всієї машинної продукції (облік обігового шлюбу, k3 = 0,88(0,98),, k3 = 0,88.
[pic].
Розрахувати швидкість машини по приводу:
[pic].
Швидкість по приводу уточнюється відповідно до табл. 2 [ 3 ] і законодавців береться, зазвичай, рівної найближчому більшого значению.
[pic].
3.2. Механізм подовжньої резки.
На продольно-резательных верстатах застосовують два методу різання: по принципу ножиць й під тиском. При краянні за принципом ножиць папір проходить між ріжучими крайками двох ножів: чашечного і дискового. При краянні методом тиску паперове полотно охоплює ножовий вал, на який прикріплять сталеві загартовані кільця високої твердості. До нього згори притискаються пружинами дискові ножі, здійснюють різання папери. Кількість ножів на одиницю більше кількості рулонів, оскільки за краях встановлюються додаткові ножі для обрізання кромок.
Найбільшого поширення набув метод різання за принципом ножиць, який би чистіший і гладкий рез ще більшу зносостійкість ножей.
При різанні за принципом ножиць установка ножів показано на рис. 3.2.1.
[pic].
Рис. 3.2.1 Установка дискових ножей.
1 — дисковий ніж; 2 — чашковий ніж; 3 — бумага.
Кут взаємного нахилу ножів змінюється від 2(2 до 2(1. Натомість, ці кути рівні (за умови рівності радіусів верхнього й нижнього ножей).
[pic].
[pic] де h — перекриття ножів, 0.0014 м r — радіус ножів, 0.315 м.
(- товщина паперового полотна, 0.001 м.
У розрахунках приймають середній кут нахилу ножів 2(ср
[pic].
Значимість перекриття ножів h приймають такий, щоб середній кут нахилу 2(ср не перевищував 150. Інакше які у місці зустрічі ножів сила витіснення матеріалу може перевищити силу тертя папери про ножі, що сприятиме небезпеки розриву крайок полотна та її обрыву.
3.3. Визначення швидкості ПРС.
Швидкість продольно-резательного верстата визначається, принаймні, трьома факторами.
Передусім, щодо швидкості ПРС необхідно виходити із продуктивності (швидкості) папероробної машини. Зазвичай, БДМ обслуговує один верстат. Тоді необхідна (мінімальна) швидкість подовжньорезательного станка где: Vм — швидкість БДМ по приводу, м/мин, Vм = 350 м/мин; tвсп — тривалість допоміжних операцій (установка та оренду рулонів, заправка і склейка при обривах тощо.), зазвичай становить 6 (8 хв, tвсп = 6 мин;
P.S — довжина намотаної папери, м; довжину паперу на рулоні можна визначити по формуле.
де: D — зовнішнє діаметр рулону на накаті БДМ, 2.2 м;
Dт — діаметр тамбурного валу, 0.42 м [ 5 ]; б — товщина паперового полотна, 0.001 м [ 6 ].
(- коефіцієнт запасу, (= 1,15.
Другий та третій чинники обмежують максимальну швидкість станка.
При обертанні рулону у його зовнішньому витку від дії відцентрових сил виникають розтягують напруги, які за досягненні деякою критичної швидкості Vпр можуть перевищити допущені напруги на розрив. Узявши за характеристику міцності картону його розривну довжину в машинному напрямі, можна визначити критичну швидкість, зумовлену відцентровими силами.
де L — розривна довжина картону в подовжньому напрямі, 6000 м g — прискорення сили тяжкості, g=9.81 м/с2.
У розрахунках необхідно ухвалити, що напруги в картоні нічого не винні перевершувати 20% краю його міцності. Тоді допускаемая швидкість наматывания.
З урахуванням майбутньої модернізації КРМ, для подальших розрахунків, приймаємо швидкість проектованого верстата рівної Vст = 2200 м/мин. = 36.7 м/с.,.
4. Конструктивні расчеты.
4.1. Вихідні дані для расчетов:
— обрезная ширина паперового полотна, м — 4.2.
— швидкість верстата max, м/мин — 2200.
— швидкість верстата min, м/мин — 945.
— швидкість заправочну, м/мин — 25.
— швидкість робоча, м/мин — 2200.
— діаметр несучих валів, м — 0.59.
— діаметр цапф несучих валів, м — 0.14.
— діаметр прижимного валу, м — 0.24.
— діаметр цапф прижимного валу, м — 0.08.
— коефіцієнт тертя качения в підшипниках — 0.02.
— максимальний діаметр наматываемого рулону, м — 1.5.
— максимальний діаметр разматываемого рулону, м — 2.2.
— коефіцієнт відносини лінійної швидкості прижимного валу і швидкості полотна — 1.02.
— коефіцієнт тертя рулону по несучим валам — 0.1.
4.2. Розрахунок потужності, споживаної продольно-резательным станком.
У продольно-резательных верстатах приводними є які мають вали, а при швидкості понад 1000 м/мин привід мають ще бумаговедущие, прижимный і ножовий вали як компенсація додаткових динамічних натяжений в паперовому полотні при розгоні станка.
Потужність, споживану верстатом визначають по формуле:
[pic] де Vcт — швидкість станка.
(Т — сума тягових докладає зусиль до подолання сил тертя в вузлах станка.
[pic] де Т1 — тягове зусилля задля подолання тертя в підшипниках несучих валов;
Т2 — тягове зусилля задля подолання тертя в підшипниках прижимного вала;
Т3 — тягове зусилля задля подолання тертя качения між рулоном і несучим валом;
Т4 — тягове зусилля задля подолання тертя між рулоном і прижимным валом;
Т5 — тягове зусилля задля подолання тертя в підшипниках тамбурного вала;
Т6 — тягове зусилля для намотування бумаги;
Т7 — тягове зусилля для размотки папери (зусилля натягу полотна);
Т8 — тягове зусилля задля подолання тертя в підшипниках бумаговедущего вала;
[pic] де f — коефіцієнт тертя в підшипниках, f = 0,02 d — діаметр цапфы несе валу, м.
D — діаметр несе валу, м.
Qo — загальне навантаження на що має вал, Н.
[pic] де Q — навантаження що має вал ваги рулона:
[pic] де Gрул — вагу наматываемого рулону, Н.
[pic] де b — обрезная ширина, 4.2 м.
(- об'ємний вагу намотаного полотна, рівний 550 кг/м3.
Dрул — діаметр наматываемого рулону, рівний 1.5 м.
(- кут між вертикаллю і лінією сполуки центрів валу і рулону, (= 200.
[pic].
Pд — динамічна навантаження від можливого эксцентриситета наматываемого рулона.
[pic] де У — обрезная ширина, 4.2 м.
(- об'ємний вагу намотаної папери рівний 550 кг/м3.
Vcт — швидкість верстата, 2200 м/мин = 36.7 м/с g — прискорення вільного падіння, 9.81 м/с2 e — додаткова навантаження від можливого эксцентриситета рулону, приймають рівним 0.003 (0.005, 0.005.
Gв — вагу несе валу, 1.4 104 Н.
[pic] де f — коефіцієнт тертя качения в підшипниках d — діаметр цапфы прижимного валу, 0.08 м.
D — діаметр прижимного валу, 0.24 м.
Q — навантаження підшипники прижимного валу, Н.
[pic] де q — лінійне тиск між прижимным валом і рулоном, однакову 4000 Н/м [1]; b — довжина робочої частини валу, 2.1 м.
[pic].
[pic].
Оскільки прижимной вал і двох секцій, тут маємо пари підшипників, тому Т2 = 112 М, тобто. вдвічі більше, отриманого при розрахунку результата.
[pic] де R — коефіцієнт тертя качения рулону папери по прижимному валу, рівний 2.
Dпр — діаметр прижимного валу, мм.
Dг — діаметр гільз, мм.
Q — тиск між валом і рулоном, 16 800 Нм.
[pic].
[pic] де R — коефіцієнт тертя качения рулону папери по прижимному валу, рівний 2.
Dн.в — діаметр несе валу, 590 мм;
Dр — діаметр наматываемого рулону, 1500 мм;
Q — навантаження що має вал від наматываемого рулона;
[pic].
[pic] де q — лінійне натяг однакову 20 кг/м = 200 М b — ширина наматываемого рулону, 4.2 м.
[pic].
[pic] де f — коефіцієнт тертя качения в підшипниках, 0.02 d — діаметр тамбурного валу, 0.42 м.
D — діаметр разматываемого рулону, 2.2 м.
Q — навантаження тамбурный вал, Н.
[pic] де Gбум — вагу разматываемого паперового полотна, 8.6 104 Н.
Gт.в. — вагу тамбурного валу, Н.
[pic] де (- щільність стали, b — довжина робочої частини валу, м.
Dн — зовнішнє діаметр тамбурного валу, м.
Dвн — внутрішній діаметр тамбурного валу, м.
[pic].
[pic].
[pic].
[pic] де q — лінійне натяг полотна, 20 кг/м = 200 Н/м b — ширина разматываемого рулона.
[pic].
[pic] де f — коефіцієнт тертя качения в підшипниках d — діаметр цапф бумаговедущего валу, м.
D — діаметр бумаговедущего валу, м.
Q — навантаження бумаговедущий вал.
[pic].
Рис. 4.2.1 Схема навантаження бумаговедущего вала.
[pic] де Qz — складова від натягу паперового полотна.
Gв — вагу бумаговедущего вала.
[pic] де (- щільність стали, 7800 кг/м3, b — довжина робочої частини валу, 4.45 м.
Dн — зовнішнє діаметр бумаговедущего валу, м.
Dвн — внутрішній діаметр бумаговедущего валу, м.
[pic].
[pic].
[pic].
Потужність споживана несучими валами:
[pic].
Потужність споживана раскатом:
[pic].
Потужність торможения:
[pic].
[pic].
[pic].
Потужність споживана ПРС.
[pic].
4. 2. Розрахунок механізму гальмування раската.
Для хорошої якості намотки рулону і сталої роботи верстата необхідно створити, й підтримувати постійним натягу паперового полотна. Величина лінійного натягу залежить від міцності папери, зумовленої її розривної довжиною і весом.
Натяг паперового полотна створюється з допомогою генератора, який при заправці працює як двигун, а при намотке рулону працює у гальмовому режиме.
Визначення гальмівного моменту на разматываемом рулоні до створення натягу паперового полотна визначається по формуле:
[pic] де q — лінійне натяг папери, 200 Н/м.
У — обрезная ширина, 4.2 м.
Dр — діаметр разматываемого рулону, 2.2 м.
[pic].
Визначення гальмівного моменту до швидшого зупинки разматываемого рулона:
[pic] де, Gр — вагу разматываемого рулону, Н.
[pic] де b — обрезная ширина, 4.2 м.
(- щільність намотаної папери, 550 кг/м3.
Dрул — діаметр разматываемого рулону, 2.2 м.
Vcт — швидкість станка,.
Dр — діаметр рулону в останній момент обриву, м g — прискорення вільного падіння, 9.81 м/с2 t — час гальмування, 3 с.
[pic].
Визначення гальмівного моменту падіння у разі екстреного гальмування в разі аварії або за нещасливий випадок визначається по формуле:
[pic].
Такого гальмівного моменту сам двигун створити неспроможна, для екстреного гальмування разматываемого рулону передбачаємо дисковий гальмо встановлений на приводном валу раската.
4.3. Розрахунок несучих валов.
Які Мають вали продольно-резательных верстатів є чавунні чи сталеві труби діаметром 400 (600 мм залежно від ширини верстати й довжиною на 150 (200 мм більше ширини полотна. Їх розрахунок на міцність і жорсткість роблять за загальноприйнятої методику розрахунку трубчастих валів. Відносний прогин робочої частини несучих валів ні перевищувати [pic]. Особливість їх розрахунку міцність у тому, що з визначенні навантаження, крім власної ваги і тиску рулону, враховують додаткову навантаження від можливого эксцентриситета рулону е, який приймають рівним 0,003 (0,005 м [ 4 ].
Рис. 4.3.1 Схема несе вала.
Перевірка валу на критичну швидкість при В0 = 4200 мм; Vст = 2200 м/мин.
[pic] де, g — прискорення вільного падіння fст — статичний прогин вала.
[pic] де Gв — вагу валу, Н,.
L — відстань між центрами підшипників валу, 4.6 м, b — довжина робочої частини вала.
Є - модуль пружності стали, 2.1 105 МПа = 2.1 1011 Па.
I — момент інерції поперечного перерізу сталевого валу, м4,.
I1 — жорсткість перерізу цапфы несе вала.
[pic] де D1 — діаметр несе валу, м d1 — внутрішній діаметр несе валу, м.
[pic].
[pic] де dц — діаметр несе вала,.
[pic].
[pic] де (- щільність стали, 7800 кг/м3,.
[pic].
З урахуванням ваги цапф приймаємо вагу валу рівним 14 000 Н.
[pic].
Робоча швидкість визначається по формуле:
[pic] де V — швидкість паперового полотна, 36.7 м/с.
R1 — радіус несе валу, 0.295 м.
[pic].
У уникнення резонансу робоча кутова швидкість має перевищувати 60 (80% критичної, т. е.
Умова выполняется!
4.4. Визначення відносного прогину вала.
Рис. 4.4. Схема навантаження несе вала.
Визначаємо силу тяжкості рулона:
[pic] де Dр — діаметр наматываемого рулону, 1.5 м dг — діаметр гильз,.
У — обрезная ширина,.
(- щільність намотки картону рівна 550 (650 кг/м3,.
[pic].
Знаходимо зусилля взаємодії несе валу і рулона:
[pic] де Рст — статична составляющая,.
Рд — динамічна составляющая,.
[pic] де mр — маса намотаного рулону, 4080 кг е — ексцентриситет рулону, 0.005.
(р — кутова швидкість наматываемого рулона.
[pic] де R — радіус рулона,.
(р — кутова швидкість наматываемого рулона.
[pic].
[pic].
[pic] де q1 — тиск між рулоном і несучим валом, q1 = 4000 Н/м,.
B0 — обрезная ширина, 4.2 м.
[pic].
[pic].
Визначаємо навантаження на підшипники валу не враховуючи зусилля натягу полотна:
[pic] де Gв — гравітація вала,.
Р1 — зусилля взаємодії несе валу і рулона.
[pic] де Rв — радіус вала,.
Rр — радіус рулону. з — відстань між центрами валов.
[pic].
Рівнодіюча всіх сил буде равна:
[pic].
Сила з урахуванням натягу буде равна:
[pic] де (- кут переходу полотна до валу.
Те — зусилля натягу полотна,.
[pic] де q — лінійне натяг паперового полотна.
[pic].
[pic].
Визначаємо прогин робочої частини вала:
[pic] де Р — навантаження вал,.
У — довжина робочої частини вала,.
L — відстань між осями подшипников,.
Є - модуль пружності стали, 2.1 105 МПа = 2.1 1011 Па.
I — момент інерції поперечного перерізу сталевого валу, м4,.
[pic].
Розмір відносного прогиба:
[pic].
[pic].
Умова выполняется!
4.5. Перевірка підшипників несучих валов.
Вибір підшипників виробляємо по динамічної грузоподъемности:
Визначаємо еквівалентну динамічну нагрузку:
[pic] де Fr — радіальна нагрузка,.
Fo — осьова навантаження, x — коефіцієнт радіальної навантаження, y — коефіцієнт осьової навантаження, к6 — коефіцієнт безпеки, кт — коефіцієнт температурный.
Значення «x» і «y» при цьому типу підшипників рівні: при.
Визначення довговічності і динамічної вантажопідйомності з формулы:
[pic].
[pic].
Для умов бажаної довговічності 100 000 годин, з отношения:
[pic] получаем:
[pic].
По необхідної динамічної вантажопідйомності сдин = 675.6 кН то, можливо підібрали радіально — сферичний роликовий підшипник із визначенням 3628 з габаритними розмірами 140×300×102 з розрахунковою довговічністю Lh =100 000 годинників та динамічної вантажністю 681 кН.
4.6. Розрахунок тамбурного вала.
4.6.1. Розрахунок валу на критичну скорость.
Працюючи верстата разматываемый рулон розташований на тамбурному валу. Оскільки швидкість ПРС може перевищувати швидкість машини у два — 3 разу, виникає небезпеку появи резонансу коливань тамбурного валу від статичного прогиба.
Перевірка валу на критичну швидкість при В0 = 4200 мм; Vст = 2200 м/мин.
[pic] де, g — прискорення вільного падіння, 9.81 м/с2 fст — статичний прогин валу з рулоном:
[pic] де Gв — вагу тамбурного валу, 6.37 103 кг.
Gб — вагу рулону папери (щільність намотаної папери (= 550 (650 кг/м3), 8777 кг = 86 073 H.
L — відстань між осями підшипників тамбурного валу, 5.17 м; b — ширина валу робоча, 4.45 м; а — довжина цапфы (відстань від центру підшипника до робочої частини вала).
[pic].
Ес — модуль об'ємної пружності стали, Па, Ес =2,1 105 МПа.
Ic — момент інерції поперечного перерізу сталевого тамбурного валу, м4,.
[pic] де Dн — діаметр тамбурного валу, м.
Dв — внутрішній тамбурного валу, м.
[pic].
Еб — модуль подовжньої пружності намотаного рулону папери (Еб =600(1000 МПа), 800 МПа = 0.008 1011 Па.
Iб — момент інерції поперечного перерізу рулону бумаги.
[pic] де Dрул — діаметр рулону, м.
Dв — діаметр тамбурного валу, м.
[pic].
[pic].
[pic].
Робоча частота вала:
[pic] де V — швидкість станка,.
R1 — радіус тамбурного вала,.
[pic].
Робоча кутова швидкість має перевищувати 60 (80% критичної, т. е.
Умова выполняется!
4.6.2. Розрахунок тамбурного валу на жесткость.
Розрахунок ведемо з умови прочности:
[pic] де Q — навантаження вал,.
У — довжина робочої частини вала,.
L — відстань між осями подшипников,.
Є - модуль пружності стали,.
I — момент інерції поперечного перерізу сталевого вала,.
Оскільки натяг полотна проти навантаженням ваги валу та значимості рулону мало — в розрахунку цією величиною пренебрегаем:
[pic] де Gв — вагу валу, 6.37 103 Н.
Gр — вагу рулону, 8.6 104 Н.
[pic].
[pic].
[pic].
Умова выполняется!
4.6.3. Розрахунок тамбурного валу на прочность.
Розрахунок ведемо з умови прочности:
[pic] де Мизг — изгибающий той час у небезпечному сечении,.
W — момент опору поперечного перерізу вала,.
[pic] де Qo — загальне навантаження на вал.
[pic] де Gв — вагу вала,.
Gр — вагу рулона,.
[pic] b — довжина робочої частини валу, l — відстань між осями подшипников,.
[pic].
[pic] де D — зовнішнє діаметр валу, м d — внутрішній діаметр валу, м.
[pic].
[pic].
Допускаемое напруга вигину [(-1] для сталевих труб на повинен перевищувати 150(160 МПа.
(=55.83 МПа < [(-1]=150 МПа.
Умова выполняется!
4.7. Розрахунок выталкивающего вала.
[pic].
Рис. 4.7.1. Схема выталкивающего вала.
[pic] де Gp — вагу рулону, Н.
(- кут між силами.
[pic].
[pic] де P. S — площа поршня.
Р — тиск у цилиндре.
L — довжина рычага.
[pic].
[pic] де D — діаметр поршня циліндра, равный:
[pic].
[pic].
Т. до. гидроцилиндров у механізму виштовхування два, то діаметр буде дорівнює 268 мм.
4.7.1. Розрахунок выталкивающего валу на прочность.
Розрахунок ведемо з умови прочности:
[pic] де Мизг — изгибающий той час у небезпечному сечении,.
W — момент опору поперечного перерізу вала,.
[pic] де Gв — вагу валу, М q — розподілена нагрузка,.
[pic] l — робоча довжина выталкивающего вала,.
[pic].
[pic] де D — зовнішнє діаметр валу, м d — внутрішній діаметр валу, м.
[pic].
[pic].
Допускаемое напруга вигину [(-1] для сталевих труб на повинен перевищувати 150(160 МПа.
(=50.2 МПа < [(-1]=150 МПа.
Умова выполняется!
4.8. Розрахунок гидроцилиндров спускного устройства.
[pic].
Рис. 4.8.1. Схема спускного устройства.
[pic] де р — тиск у гидроцилиндре,.
F — площа поршня гидроцилиндра.
[pic] де Gр — вагу рулону, Н.
Gc.у. — вагу спускного устройства,.
[pic].
Т. до. спускное пристрій має дві гидроцилиндра, діаметр кожного дорівнюватиме 195 мм.
5. Автоматизация.
5.1. Регулювання щільності намотки рулонов.
Задля більшої якісної щільності намотки рулонів на подовжньо — резательном верстаті застосовується прижимной вал, що забезпечує необхідне зусилля притискання наматываемого рулону картону до несучим валам, цим забезпечуючи постійне лінійне тиск і зчеплення несучих валів з наматываемым рулоном.
У початковий момент роботи необхідну лінійне тиск між рулоном і несучим валом забезпечується з допомогою притискання прижимного валу. В міру зростання діаметра наматываемого рулону зусилля притискання прижимного валу зменшується пропорційно зростанню маси наматываемого рулону. У час, коли необхідне лінійне тиск забезпечуватиметься вагою намотаного рулону, виникла потреба вивішування прижимного вала.
Пневматичні циліндри установлені з обох кінців прижимного валу дозволяють підтримувати постійним лінійне тиск між рулоном і прижимным валом при різної товщині паперового полотна з правого і лівого края.
Повітря (рис. 5.1.1.) з магістралі вступає у штоковые порожнини циліндрів через регулятори тиску 2РД і 3РД, настроювані вручну незалежно друг від друга для лицьової і приводний сторін. Контроль тиску стиснутого повітря після регуляторів 2РД і 3РД проводиться у разі манометрам 2 М і 3 М, встановленими як і регулятори на пульте.
Переміщення механізму прижимного валу здійснюється пневмоцилиндрами двостороннього дії, расположеннымми з лицьової і приводний боку. При підйомі прижимного валу включається електромагніт воздухораспределителя 10ВРЭ, стиснений повітря через регулятор 8РД і воздухораспределитель надходить в штоковые порожнини циліндрів, у своїй повітря з поршневих порожнин скидається у повітря через вентиль 2В9 і воздухораспределитель 9ВРЭ.
Рис. 5.1.1. Схема пневматична принципова регулювання щільності намотки рулонов.
При опусканні прижимного валу включаються електромагніти вентиля 2ВЭ і воздухораспределителя 9ВРЭ, стиснений повітря вступає у поршневі порожнини пневмоцилиндров, а штоковые — поєднано з аналітичними атмосферою через воздухораспределитель 10ВРЭ.
При ручному режимі роботи притиск валу здійснюється регулятором тиску 4РД, встановленим на пульті і настраиваемым вручну по манометру 4 М. У цьому включається електромагніт вентиля 2ВЭ, повітря вступає у поршневі порожнини, та якщо з штоковых порожнин повітря через воздухораспределитель 10ВРЭ стравливается в атмосферу.
Дроселі 8ДОК, 9ДОК, 13ДОК і 14ДОК дозволяють регулювати швидкість піднесення та опускання вала.
Для зупинки прижимного валу як підйому чи опускання у кожному проміжному становищі й за необхідності зняття притискання необхідно знеструмити все электромагниты.
Можливі режими роботи прижимного валу табл. 5.1.1 |Найменування |Режим |Електромагніти | |механізму |роботи | | | | |2ВЭ |10ВРЭ |9ВРЭ |4ВЭ |3ВЭ | |Прижимной вал |Зняти притиск |- |- |- |- |- | | |Підняти |- |+ |- |- |- | | |Опустити |+ |- |+ |- |- | | |Притиск автомат |+ |- |- |+ |- | | |Притиск ручний |+ |- |- |- |+ |.
5.2. Схема пневматична принципиальная.
Схема (рис. 5.2.1.) передбачає автоматичний притиск прижимного валу (зусилля притискання валу до рулону перебуває у функції від діаметра наматываемого рулону). На осі зірочки прижимного валу встановлено сельсин — датчик, електрично пов’язані з сельсин — приймачем, що у пульті. Вісь сельсин — приймача механічно пов’язані з віссю пневматичного перетворювача ПП, видавало пневматичний сигнал, пропорційний розі повороту сельсин — приймача, тобто. переміщенню прижимного валу. Вихідний сигнал перетворювача надходить для виходу пропорційного регулятора ПР. Вихідний сигнал регулятора пропорційний різниці тиску вхідного сигналу і тиску завдання, настраиваемого задатчиком ЗУ. Сигнал від пропорційного регулятора ПР надходить керовану мембрану регулятора 5РД (див. рис 5.2.1), що є підсилювачем цього сигналу по тиску і за потужністю. Стиснутий повітря про регулятора 5РД при автоматичному режимі притискання прижимного валу через вентиль 4В9 (електромагніт включений) вступає у поршневі порожнини пневмоцилиндров, виробляючи його притиск при намотке.
Регулятори РДФ встановлюють тиск харчування (Рпит. = 1,4 + 10% кгс/см2) пропорційно регулятора і пневмопреобразователя.
З допомогою задатчика ЗУ по манометру М, що є на пульті, встановлюють завдання на регулятор, відповідне необхідного прижиму.
Рис. 5.2.1 Схема пневматична принципиальная.
5.3. Опис приладів які у схемах.
2 М … 4М — манометр що складає загального призначення МОШ 1−100.
2РД … 3РД — пневмоклапан П-КР12−12.
6 В, 7В — вентиль запірний муфтовый 15 НЖ 6бк.
9ВРЭ, 10ВРЭ — пневмораспределитель В64−25М.
9ВРЭ-ЭМ, 10ВРЭ-ЭМ — электромагнит.
8РД, 9РД — пневмоклапан П-КР 25−11.
2ВЭ … 4ВЭ — вентиль мембранний з електромагнітним приводом 15КЧ888р СВМ-220 В.
4РД — пневмоклапан П-КР 16−12.
5РД — регулятор тиску С5.16.21.200.
3Ф — фільтр влагоотделитель 22−16Х40 ГОСТ 17 437–72.
8ДОК, 9ДОК, 13ДОК, 14ДОК — пневмодроссель 16−1 ГОСТ 19 485–74.
5 СМ, 6СМ — маслораспределитель В44−24.
6. Економічна часть.
6.1. Кошторис капітальних затрат.
За базу для порівнювати проектованого продольно-резательного верстата вибираємо верстат обрізної шириною 4200 мм фактичної робочої швидкістю 1100 м/мин.
Проектований продольно-резательный верстат відрізняється від базового простіший конструкцією валів. Вартість базового верстата з урахуванням переоцінки основних фондів 22 023 500 крб. Вартість проектованого верстата з урахуванням зміни конструкції валів 22 003 100 крб., причому, вартість двох несучих, бумаговедущего і тамбурного валів 800 000 руб.
Капітальні витрати визначаються розрахунком з урахуванням складання кошторису затрат.
табл. 6.1.1.
|№ |Найменування |Сума витрат, | |п/п |витрат |крб | |1 |Основне устаткування (які мають, бумаговедущий |800 000 | | |і тамбурный вали) | | |2 |Додаткові комплектуючі вироби |80 000 | |3 |Настановні витрати |90 600 | | |Усього витрат (До див) |970 600 |.
6.2. Розрахунок фактичної суми капітальних затрат:
Кф відрізняється від кошторисної Ксм залежно від рівня морального і фізичного зносу замінюваних деталей.
Оскільки старі вузли фізично й дуже застаріли й цілком замортизовані, всі вони здають у лом.
Кф = Ксм — Л= 970 600 — 9 500 = 961 100 крб, де Л — вартість брухту, крб., визначається по формуле:
Л = m Ц = 9.5 1000 = 9 500 крб. де m — маса (вагу) демонтируемых вузлів, 9.5 т.
Ц — ціна металобрухту, 1000 руб./т.
6.3. Розрахунок умовної річний экономии.
Зміна витрат за амортизаційні відрахування визначаємо по формуле:
[pic] де К1 і К2 — вартість базовий і проектованого верстата, рівна відповідно 22 023 500 крб. і 22 003 110 руб.;
А1 і А2 — річна продуктивність базовий і проектованого верстата, рівна 120 000 т/год;
Na — норма амортизаційних відрахувань, рівна 7%.
[pic].
Зміна витрат за ремонти визначається по формуле:
[pic] де сбал — вартість валів базового верстата, рівна 1 180 000 крб. кпр — вартість валів проектованого верстата, рівна 970 600 руб.
5.2 і 4.2 — видатки поточний ремонт до вартості обладнання відповідно доі після модернізації, %.
4.3 — видатки перегляд, %.
[pic].
Зміна витрат за электроэнергию:
[pic] де N1 і N2 — потужність двигунів базовий і проектованого верстата, рівна відповідно 250 і 200 кВт;
Qчас — годинна продуктивність, рівна 14,5 т/ч;
Ц — ціна 1 кВт год електроенергії, рівна 0,5 руб/кВт ч.
[pic].
Зміна відсотка шлюбу знаходимо через производительность:
Запланована продуктивність після модификации:
[pic] де, У — ширина обрезная, 4.2 м q — вагу 1 м², 350 грн. = 0.35 кг.
V — швидкість робоча (фактична), 1100 м/мин.
[pic].
Фактична продуктивність до модификации:
[pic].
Кількість шлюбу, що йде в бракомелку одно 4.2% від добової продуктивності. На проектованому верстаті кількість шлюбу зменшується в півтора раза.
Різниця між повної собівартістю продукції і на вартістю композиції, руб.:
2 000 — 1 200 = 800 руб.
Умовна економія по браку:
[pic].
Загальна сума умовно річний экономии:
[pic].
Коефіцієнт економічної эффективности:
[pic].
Річний економічний эффект:
[pic].
При нормативному коефіцієнті рівним Єн = 0.25 заходи щодо заміні валів досить эффективными.
7. Безпека объекта.
7.1. Аналіз умов труда.
Принаймні ускладнення системи «Людина-техніка» дедалі більше відчутніше стає економічні та соціальні втрати від невідповідності умов праці та техніки виробництва можливостям людини. Аналіз умов праці дільниці продольно-резательного верстата, призводить до висновку про потенційну небезпеку цієї ділянки. Суть небезпеки у тому, що вплив присутніх небезпечних і шкідливих виробничих чинників на людини, призводить до травм, захворювань, погіршення самопочуття і іншим последствиям.
На ділянці є такі шкідливі і небезпечні факторы:
1. механічні чинники, які характеризуються впливом на людини кінетичній, потенційної енергій і механічним обертанням. До них ставляться кінетична енергія рухомих і обертових тіл, шум, вибрация.
2. термічні чинники, які характеризуються тепловою енергією і аномальною температурою. До них належать температура нагрітих предметів, поверхонь й навколишнього среды.
3. електричні чинники, які характеризуються наявністю токоведущих частин оборудования.
4. мікрокліматичні чинники, які характеризуються наявністю в навколишньому повітрі пылевыделения.
Під час розробки заходів із поліпшення умов праці необхідно враховувати сув’язь чинників, які впливають формування безпечних умов труда.
7.2. Захист від рушійних частин, шуму й вибрации.
На проектованому верстаті передбачено огородження небезпечних місць верстата як-от: які працюють деталі верстата, муфти. При піднятою перегородці неможливо переключити швидкість верстата з заправної на робочу. Для екстреного гальмування під час нещасного разі передбачено пневматичний дисковий гальмо, який зупиняє продольно-резательный верстат за 0,5 с.
Шум і вібрація на виробничому ділянці завдає великої шкоди, шкідливо діючи на організм чоловіки й знижуючи продуктивність труда.
Шум — це безладне хаотичне поєднання хвиль різної частоти і интенсивности.
Шум виникає при механічних коливаннях. Розрізняють три форми впливу шуму на органи слуху: а) стомлення слуху; б) шумове травма; в) посередня тугоухость.
Для зниження шуму, виникає в цеху, передбачено: масивний бетонний фундамент, шумопоглащающие лаки, застосування звукоизолирующих кожухів і акустичних екранів на устаткуванні, що є джерелами підвищеного рівня шума.
7.3. Пожежна безопасность.
Пожежі на папероробних підприємствах складають велику небезпеку обману працюючих, і можуть заподіяти величезний матеріальним збиткам. До основним причин пожеж, які виникають за виробництві папери, можна віднести: порушення технологічного режиму, несправність електроустаткування (коротке замикання, перевантаження), самозаймання промасленому дрантя та інших матеріалів, схильних до самозаймання, недотримання графіка планового ремонту, реконструкції установок з відхиленням технологічних схем. На ділянці продольно-резательного верстата можливі такі причини виникнення пожежі: перевантаження дротів, коротке замикання, виникнення великих перехідних опорів, самозаймання різних матеріалів, сумішей і трансмісійних мастил, висока концентрація воспламеняемой суміші пилу з повітрям. Для локалізації і ліквідації пожежі внутрицеховыми засобами створюються такі умови попередження пожеж: курити лише у суворо відведених місцях, патьоки і розливи оливи й розчинника прибирати ганчірочками, ганчір'я повинна перебувати у спеціально пристосованому контейнере.
7.4. Электробезопасность.
Широке використання у промисловості електродвигунів, систем управління, що працюють у різних умовах, пов’язані з застосуванням електричної енергії і вимагає забезпечення електробезпеки, розробки заходів і коштів, які забезпечують захист від впливу електричного тока.
Електричний струм проходячи через організм, надає термічне, электролитическое, і біологічне вплив, викликаючи місцеві і спільні электротравмы. Основні причини впливу струму на людини являются:
— випадкове дотик чи наближення на небезпечне відстань до токоведущим частям;
— поява напруги на металевих частинах обладнання результаті ушкодження ізоляції чи хибних дій персонала;
— шаговое напруження у результаті замикання дроти на землю.
Існують такі основні захисту від поразки струмом, застосовувані окремо чи поєднанні друг з одним: недоступність токоведущих частин, захисне заземлення, застосування спеціальних электрозащитных коштів, зануление, захисне відключення, електричне поділ мереж різного напруги, застосування малого напруги, ізоляція токоведущих частин, вирівнювання потенциалов.
Одне з найбільш часто застосовуваної мірою захисту від поразки струмом є захисне заземление.
Заземлення — навмисне електричне з'єднання з землею металевих нетоковедущих частин, які можуть бути під напругою. Поділяють заземлители штучні, призначені з метою заземлення, і цілком природні - перебувають у землі металеві предмети для іншої мети. Для штучних заземлителей застосовують зазвичай вертикальні і горизонтальні електроди. Як вертикальних електродів використовують сталеві труби діаметром 3 (5 див і сталеві куточки розміром від 40×40 до 60×60 мм довжиною 3 (5 м. Також застосовують сталеві дротики діаметром 10 (20 мм довжиною 10 м. Для зв’язку вертикальних електродів і як самостійного горизонтального електрода використовують сталь перерізом не до 3,6×12 мм сталь круглого перерізу діаметром щонайменше 6 мм.
Як заземляющих провідників застосовують полосовую чи круглу сталь, прокладку яких виробляють відкрито за конструкцією будинку банку по спеціальних опорах. Заземлительное устаткування приєднується до магістралі заземлення паралельно окремими проводниками.
У електроустановках (ЕУ) напругою до 1000 У з ізольованій нейтралью й у ЕУ постійного струму з ізольованій середньої точкою застосовують захисне заземлення разом із контролем ізоляції чи захисне отключение.
У цих електроустановках мережу напругою до 1000 У, пов’язану з мережею напругою вище 1000 У через трансформатор, захищають від появи у цієї мережі високої напруги при ушкодженні ізоляції між обмотками нижчого і вищого напруги пробивним запобіжником, що може бути встановлено у кожному фазі за нижчого напруги трансформатора.
Захисний відключення застосовується у ролі основного чи додаткового захисту у разі, а то й може бути гарантована безпеку застосуванням захисного заземлення чи зануления чи його застосування викликає трудности.
Усі електродвигуни проектованого верстата мають захисне заземление.
7. 5. Висвітлення виробничого участка.
Правильно спроектована і виконане висвітлення виробничого ділянки покращує умови роботи, знижує стомлюваність, сприяє підвищенню продуктивність праці і забезпечення якості випущених напівфабрикатів, безпеки праці та зниження травматизму на участке.
Висвітлення робочого ділянки — важливий чинник створення нормальних умов праці. Залежно джерела світла виробниче висвітлення то, можливо два види природне, і искусственное.
Природний висвітлення підрозділяється на (бічне, здійснима через світлові отвори у зовнішніх стінах; верхнє, здійснима через аераційні і зенітні ліхтарі, отвори в перекриттях; комбіноване, коли горішнього висвітлення додається бічне. Штучне висвітлення то, можливо двох систем — загальне та комбіноване, коли до спільного висвітлення додається місцеве, що концентрує світловий потік безпосередньо на робочих местах.
Проектований верстат має загальне штучне освітлення з рівномірним розташуванням світильників тобто. з відстанями з-поміж них. Зона ножів і зона несучих валів висвітлюється двома рядами світильників. Світильники є дві штанги, закріплені з допомогою кронштейнів до станинам. До штангам підвішені світильники типу ПВЛ-2Х40.
7.6. Очищення повітряної среды.
Один із необхідних умов здорового і високопродуктивного праці - забезпечити нормальних умов і чистоту повітря дільниці. Необхідну стан повітря робочої зони може бути забезпечено виконанням певних заходів до основною з яких относятся:
1. Застосування технологічних процесів і устаткування, що виключатимуть освіту шкідливі речовини чи влучення в робочу зону.
2. Надійна герметизація устаткування, зокрема валів, де нагріваються підшипники, із поверхні яких випаровується масло.
3. Установка на проектованому ділянці устрою вентиляції чи кондиционирования.
4. Застосування коштів індивідуальної захисту, саме: спецодяг, який захищає тіло людини; захисні окуляри і фільтруючі засоби захисту; захисні мазі, який захищає шкіру рук від масел (при мастилі підшипників і деталей двигуна); захисні рукавиці (і під час транспортировочных работ).
Процес різання папери зазвичай супроводжується побічним явищем, негативно впливає на мікроклімат виробничого приміщення. Ці побічні явища називаються шкідливими виділеннями. До до їх числа і пылевыделение — виділення пилу у кількості, які обумовлюють запиленість понаднормово. На продольно-резательных верстатах використовується механічна різка папери, і внаслідок впливу механізму різання на полотно відбувається обрив волокон, що й утворюють пил. Вплив пилу на безпеку здоров’я обслуговуючого персоналу зумовлює застосування пневмотранспорта відходів. На рис. 10.5.1. показано схема видалення відходів різання на проектованому станке.
Рис. 7.6.1. Схема отсоса пилу від ножей.
1 — пылеприемники; 2 — гофровані шланги; 3, 5 — трубопровід; 4 — вентилятор; 6 — циклон.
7.7. Розрахунок пневмотранспорта відходів від ПРС.
Знаходимо секундний витрата відходів від транспортування кожної пари ножів по формуле:
[pic] де Vп — швидкість подачі паперового полотна, b — ширина розтину h — товщина паперового полотна.
(п — щільність паперового полотна.
[pic].
Кількість повітря, що слід просасывать через кожухопылеприемник однієї пари ножів, визначаємо по формуле:
[pic] де Gi — кількість відходів, отсасываемых від кожухопылеприемников,.
(b — щільність воздуха.
(- вагова концентрація аэросмеси.
[pic].
Знаючи витрата повітря, знаходимо внутрішній діаметр трубопроводу по формуле:
[pic] де Wb — середня швидкість повітряного потока,.
[pic] приймаємо внутрішній діаметр трубопроводу d = 0.08 м.
Загальне тиск, яке повинен розвивати вентилятор, складається з сумарних втрат тиску всасывающем і нагнітальним ділянках трубопровода.
Втрата тиск у загальному разі складається з: а) втрат на надання суміші кінетичній энергии:
[pic] б) втрат у місцеві опору — в кожухах пылеприемниках.
[pic] де (м — коефіцієнт місцевого сопротивления.
[pic] на поворотах (м =0,12.
[pic] у місцях врізки повітроводів (м =0,12.
[pic] в) втрат надходжень у прямолінійних участках:
[pic] де (- коефіцієнт опору трубопроводу під час руху у ньому чистого воздуха.
[pic] де di — внутрішній діаметр трубопровода.
[pic] де (і - динамічний коефіцієнт в’язкості для воздуха.
(е — еквівалентна шорсткість трубопроводу li — довжина ділянки трубопровода.
R — досвідчений коефіцієнт залежить від физико — механічних властивостей транспортного матеріалу і швидкості транспортирования.
[pic].
[pic].
[pic].
Загальний перепад давления:
(P=152,6+259,2+20,7+31,1+563,7=1027,3 Па.
За графіком підбираємо відцентровий пилової вентилятор Ц6−46 № 3 з комплектуючими двигунами А2 і А02 з такими параметрами n=2440 об./хв, Q=0,65 тис. м3/г.
Потім за графіку вибираємо циклон ЦН-11, одиночний, з перепадом тиску (Р=120 кг/м3; Q=0,45 тис. м3/г; D=250 мм; H=950 мм; m=115.72 кг.
8. Перелік використовуваної литературы.
1. Паперові і оздоблювальні машини, вид. 3-тє, испр. і доп.
Эйдлин І. Я. Вид-во «Лісова промисловість», Москва, 1970 г.,.
623 с.
2. Технологічний розрахунок процесів зневоднення на сеточной частини папероробних машин з допомогою ЭВМ.
Методичні вказівки до курсовому і дипломному проектированию.
Під ред. проф. І. Д. Кугушева. Сост. А. Є. Слуцький, А. П.
Спирин, Ю. М. Швеців; ЛТИ ЦБП, Л., 1988. 27 с.
3. Розрахунок основних конструктивних і технологічних параметрів продольно-резательных верстатів. Методичні вказівки з виконання самостійної роботи. Третьяков С. Ю., Калугин.
Ю.К., Ленінград, 1990. 14 с.
4. Довідник механіка целюлозно-паперового підприємства. Пожитков.
У. І., Калінін М. І., Старець І. З повагою та ін.; Під ред. канд. техн.
наук М. І. Калініна. — М.: Лісова пром-сть, 1983 р., 415 с.
5. Журнал «Папір життя й» № 3, 2002 р. вид. «Украина».
6. Експлуатація і ремонт папероробних машин. З. З. Киселев,.
М. ГосЛесБум. 1973 р, 320 с.
7. Вали папероробних і опоряджувальних машин. Эйдлин І. Я., М.
ГосЛесБум. 1961 р, 590 с.
8. Розділ «Охорона праці» в дипломних проектах студентів механічного факультету. Методичні вказівки. Сост.: Якимов.
У. І. — Л; ЛТИЦБП, 1985 р. 18 с.
9. ГОСТ 7933–75 «Картон коробочный».
10. Методичні вказівки до виконання контрольних робіт з курсу «Вентиляція і кондиціювання повітря целлюлозно — паперових підприємств». Сост.: Намісників І. У., Якимів У. И.
— Л; ЛТИЦБП, 1975 р. 46 с.
11. Дипломне проектування. Методичні вказівки. Порядок викладу і побудови пояснювальній записки. Сост.: Кугушев.
І. Д., Калугин Ю. До. — Л; ЛТИЦБП, 1986 р. 24 с.
12. Автоматика і автоматизація виробничих процесів целлюлозно — паперових виробництв, Буйлов Р. П., Дронин У. А.,.
Серебряков М. Р., М; Екологія 1995 р, 320 с.
13. Дипломне проектування, частина II. Порядок оформлення графічної частини (методичні вказівки). Сост.: Кугушев И.
Д., Калугин Ю. До. — Л; ЛТИЦБП, 1986 р. 32 с.
14. Обгрунтування типажу ПРС машин. Каупельсон Р. М. — Л; ЛТИЦБП,.
1965 р. 260 с.
15. Методи підвищення працездатності різальних аппаратов.
Кисилев З. З. М; Лісова промисловість, 1968 р., 280 с.
16. Устаткування ЦБП. Чичаев У. А.; М; Лісова промисловість, 1981 р., 330 с.
17. Економічне обгрунтування організації ремонту й модернізації з допомогою мережевих моделей. Терешкина Т. Р., Коваленка Ю.
До., Лапін Ю. І. -СПб; СПбГТУРП, 1993 г., 32 з ———————————- [pic].
[pic].
[pic].
[pic].
[pic].
[pic].
[pic].
[pic].
[pic].
[pic].
[pic].
[pic].
[pic].
[pic].
[pic].
[pic].
[pic].
[pic].
[pic].
[pic].
[pic].
[pic].
[pic].
[pic].
[pic].
[pic].
[pic].
[pic].
[pic].
[pic].
[pic].
[pic].
[pic].
[pic].
[pic].
[pic].
[pic].
[pic].
[pic].
[pic].
[pic].
[pic].
[pic].