Московський НПЗ
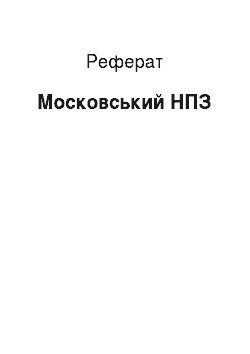
Электрообессоливающие установки проектують двухступенчатыми: в электродегидраторах 1-ой щаблі видаляється 75−80% (мас.) солоною води та 95- 98% (мас.) солей, а электродегидраторах 2-ой щаблі — 60−65%(масс.) відстояної емульсійної води та приблизно 92%(масс.) отстоявшихся солей. Кількість встановлюваних электродегидраторов при двухступенчатом обессоливании залежить від обсягу й якості (тобто… Читати ще >
Московський НПЗ (реферат, курсова, диплом, контрольна)
Історія завода.
1 апреля1938 р. На Московському крекинг-заводе було запроваджено експлуатацію перша крекинг-установка зі лужної очищенням. Основні етапи переозброєння за 50 років від початку роботи: 1 етап: збільшення обсягу нафтопереробки, організація системи підготовки нафти для переробки, розробка конструкції сферичних электродегидраторов. 2 етап: впровадження сучасних вторинних технологічних процесів з одночасним збільшенням потужності з переробки нафти, розвиток нафтохімічних процесів. 3 етап: освоювалися і вдосконалилися вторинні процеси, розробка й освоєння вітчизняних поліпропілену та інших пластмас. 4 етап: будівництво і введення пускових комплексов.
30 травня 1939 р. Введено в експлуатацію друга крекинг-установка. У 1940 року прийнятий у експлуатацію асфальто-вакуумный цех. 5 червня 1941 року прийнятий у експлуатацію спеціальний цех, який складався з газофракционирующей установки N 45 та настанови полімеризації N 29. З 21 листопада 1942 року Московський державний крекинг-завод став заводом N 91 села Капотня Ухтомського району Московській області. У 1943 році корабельню перейменований на завод N 413. У 1948 року пущено в експлуатацію установку по алкілування бензолу пропиленом на фосфорном катализаторе. У вересні 1952 року завод N 413 Миннефтехимпрома СРСР перейменований на Московський нафтопереробний завод. У 1955 року вводять у експлуатацію нову обессоливающую установку з кульовим электродегидратором. До 1956 року потужність заводу було збільшено на 88%. Впроваджувалася автоматизація технологічних процесів. У 1957 року перша промышелнная піч беспламенного горіння була пострена і пущено в експлуатацію на АВТ-3. У 1963 року вступ до лад нафтопроводу Ярославль — Москва, введення якого забезпечував перекачування до 7 млн. т. Нафти. Потужність підприємства було доведено до 5 млн. т. нафти. У 1968 року з урахуванням власного поліпропілену заводу створили цех по його переробці в вироби. У 1967 року впроваджений процес каталітичного риформінгу і отримано неетилований бензин АІ-93. У 1972;му році реконструкція заводу, у яких має бути досягнуто повне забезпечення світлими нафтопродуктами, бітумом і котельням паливом. З 1976 року після реконструкції заводу запроваджені установки ЭЛОУ-АВТ-6, каталітичного крекирования Г-43−107, риформирования бензинов.
У 1997 року ВАТ «Московський НПЗ» ввійшло до складу «Центральної паливної компанії» (ЦТК).
Московський НПЗ випускає нафтового топлива, битумы, нефтехимическую продукцию, включая серу, полипропилен і вироби з поліпропілену. Близько 80% вироблюваної продукції реалізується у Москві і области, 10−15% экспортируется, 5−10% відвантажується до інших країн та західні райони СНГ.
Нині Московський НПЗ забезпечує на 70% потреби Москви й області в высокооктановом бензині, задовольняє близько сорока% потреби вреактивном паливі та на 100% в малосернистом дизельному паливі, мазуті і битуме.
Протягом років Великої Вітчизняної війни, не перебазируя і зупиняючи виробництво, працюючи за умов прифронтового міста, забезпечував випуск палива потреб фронту. За героїчний працю в часи війни колективу 14 раз присуджувалося переходить Червоний прапор Державного комітету оборони, передане згодом заводу у вічне зберігання, а до 40-річчя перемоги завод нагородили орденом війни 1-ой степени.
Високий рівень технології, досвід минулого і кваліфікованість персоналу забезпечують безпеку виробництва, що підтверджено ліцензіями Держтехнагляду Росії, на право здійснення 5 видів діяльності підвищеної опасности: эксплуатация, проектування ремонт устаткування, підготовка кадрів для вибухонебезпечних производств.
Московський НПЗ має найвищу Росії частку високооктанових бензинів, у своїй не використовуючи свинецсодержащие добавки, єдина Росії випускає все автобензини і по 70% дизельного палива лише на рівні європейських норм екологічними показателям.
За свої 60 років завод жодного разу зупинявся, працюючи цілодобово, і переробив більш 350 мільйонів тонн нефти.
Стуктура виробничого потенциала:
— Сучасні екологічно розвинені технологии.
— 42 технологічні установки.
— Перевага потужностей вторинних процесів: частка гидрогенизационных процесів очищення бензиновых, средних і вакуумних дистсллятов-55%, деструктивных процессов-25%.
Штатний состав.
— Близько 4000 человек.
— Стабільний колектив висококваліфікованих специалистов.
— Частка спеціалістів із вищою та середнім спеціальним образованием-44% від загальної кількості работающих.
— У тому числі на робочих должностях-35% від загальної кількості рабочих.
Асортимент випуску продукції більш 190 найменувань, у цьому числе:
_Неэтилированные автомобільні бензини з поліпшеними екологічними характеристиками.
— Реактивне топливо.
— Літні і зимові дизельні палива з поліпшеними екологічними характеристиками.
— Котельне топливо.
— Дорожні й будівельні битумы.
— Скраплені газы.
— Екологічно чисті поліпропілен, вироби з поліпропілену і поліетилену 150 наименований.
Установки первинної переробки нефти.
ЭЛОУ-АВТ-6.
Комбінована установка атмосферновакуумнойпереработки нафти з пердварительным обессоливанием і вторинної перегонкою бензину призначена на переробку сирої нафти для одержання продуктів первинної перегонки і полуфабрикатов-сырья установок каталітичного риформинга, газофракционирования, бітумної, гидроочисток, дизельного топлива, авиакеросина, каталитического крекинга.
АВТ-3.
Атмосферно-вакуумная установка АВТ-3 варта переробки збезводненої і обессолинной нафти для одержання продуктів первинної перегонки: компонента прямогонного автомобиля, бензина, компонентов дизельного тооплива «літнього» і «зимового», важкого вакуумног газойля, гудрона, компонента топкового мазуту, авіакеросину і вакуумного дистилята для каталітичного крекинга.
ВИСБРЕКИНГ З БЛОКОМ ПІДГОТОВКИ СЫРЬЯ.
Блок вісбрекінгу призначений для привращения гудрону в котельне пальне з низькою в’язкістю і температурою застывания. Внедрения процесу виброкрекинга показало високу працездатність прийнятої схеми глибокої переробки нафтового сырья. Дистиллятные фракції втягуються у виробництві світлих нафтопродуктів, а залишок використовується для котельного палива стабільного якості. У цьому належне оформлення технологічного процесу дозволяє мінімізувати коксообразование на стінках реакційної аппаратуры.
Установки вторинної переробки нефти.
КАТАЛІТИЧНИЙ РИФОРМИНГ.
Л-35−11/300 і Л4−35−11/1000.
На АТ «Московський НПЗ» эксплатируются 2 установки каталітичного риформінгу Л-35−11/300 і Л4−35−11/1000, працівники жорсткому режимі з періодичної регенерацією каталізатора. Впровадження ефективних каталізаторів є найменшим витратним засобом підвищення якості продуктов, эксплуатационных показників і рентабельності установки, тому при чергових перевантаженнях вітчизняні каталізатори було замінено на зарубежные (R-56 фірми ЮОПи).Достигнутые результати щодо виходу й якості риформата дозволили Московському НПЗ освоїти виробництво товаарных неэтилкрованных «міських» бензиновАИ-80эк, АИ-92эк, АИ-95эк з поліпшеними екологічними свойствами, отвечающими європейських норм EN-228.
ГИДРООЧИСТКА ДИЗЕЛЬНОГО ТОПЛИВА.
24−5, Л4−24−2000.
Установки виробляли малозернистое дизельне пальне з змістом сірки не вище 0.2%.Для переходу на випуск моторних палив сулучшенными екологічними показниками (вміст сірки трохи більше 0.05% мас) каталізатори ГО-70 замінені більш ефективні Ketjenfine-752−1.30 і Kenjenfine-840−30 фірми «AKZO NOBEL», щоб забезпечити глибину знесірчення дизельного палива більш 95% масс.
БИТУМНОЕ ПРОИЗВОДСТВО.
Битумное виробництво призначено щоб одержати дорожніх в’язких і будівельних бітумів. У основу технології покладено метод безперервного окислення сировини в трехсекционных апаратах колонного типу. Відповідним добором сировини можна було одержати окислені бітуми різних марок. Завод производит:
— дорожні грузлі бітуми БНД 69/90 і БНД 40/60.
— будівельні бітуми БН 70/30.
До складу виробництва входять також котел-утилизатор і компресорне господарство щоб одержати технічного і КИПовского повітря, естакада для наливу бітумів в залізничні бункери і цистерни для наливки бітумів в автоцистерны.
КОМБІНОВАНА УСТАНОВКА КАТАЛІТИЧНОГО КРЕКИНГА.
Г-43−107 введена в экспулатацию в 1938 року. Ухвалений основу технології набір процесів визначається наступним складом установки:
— гидроочистка сырья.
— каталітичний крекинг.
— абсорбція і газофракционирование.
— утилізація тепла і теплоснабжение.
— очищення димових газів від катализаторной пыли.
АСУ ТП установки включает:
— распредилительную систему управления.
— систему аварійної сигналізації і блокування PLC.
— математичне і програмное обеспечение.
КОМПЛЕКС ВИРОБНИЦТВА ПОЛИПРОПИЛЕНА.
Включає 4 установки:
— підготовки сировини й концентрування полипропилена.
— полимеризации.
— грануляции.
— встановлення і відвантаження готової продукции.
ЦЕХ ПЕРЕРОБКИ ПОЛИПРОПИЛЕНА.
Установка зневоднення і знесолення нафт на НПЗ.
Зміст солей в нефтях, вступників на нафтопереробні заводи, обычносоставляет 500 мг/л, а води — не більше 1% (мас.). На переробку ж допускають нафти, у яких вміст солей вбирається у 20 мг/л та води 0,1% (мас.). Вимоги до обмеження змісту солей та води в нефтях постійно зростають, бо тільки зниження солей з 20 до 5 мг/л дає значну економію: приблизно вдвічі збільшується міжремонтний пробіг атмосферно-вакуумных установок, скорочується витрати, зменшується корозія апаратури, знижуються витрати каталізаторів, поліпшується якість газотурбінних і котельних палив, коксов і битумов.
Більшість води в вступників на НПЗ нефтях перебуває у вигляді емульсії, освіченою крапельками води з переважним діаметром 2 — 5 мкм. На поверхні крапельок з нафтової середовища адсорбуються смолисті речовини, асфальтены, органічні кислоти та його солі, розчинні не в нафті, і навіть высокодисперсные частки тугоплавких парафінів, мулу і глини, добре смачиваемых нафтою. З часом товщина адсорбційної плівки збільшується, зростає її механічна міцність, старішає емульсії. Щоб запобігти цього явища на багатьох промислах в нафту вводять деэмульгаторы. Деэмульгаторы використовують і за термохимическом, і за электрохимическом зневодненні нафт. Витрата деэмульгаторов кожної нафти визначається експериментально — коштує від 0,002 до 0,005% (мас.) на 1 т нефти.
Руйнуючи поверхнустную адсорбционную плівку, деэмульгаторы сприяють злиттю (коалесценции) крапельок води до більших краплі, які за відстої емульсії відокремлюються швидше. Цей процес відбувається пришвидшується при підвищених температурах (зазвичай 80−1200С), бо за цьому розм’якшується адсорбційна плівка і підвищується її розчинність не в нафті, збільшується швидкість руху крапельок і знижується в’язкість нафти, тобто. поліпшуються умови для злиття і осідання крапель. Слід зазначити, що з температурах більш 1200С в’язкість нафти змінюється мало, тому ефект дії деэмульгаторов збільшується незначительно.
Найбільш стійкі дрібнодисперсні нафтові емульсії руйнуються з допомогою електричного струму. При вплив електричного поля крапельки води, перебувають у неполярной рідини, поляризуються, витягуються в еліпси з протилежно зарядженими кінцями і притягуються друг до друга. При зближення крапельок сили тяжіння виростають до величини, що дозволяє стиснути і розірвати відділяють їх плівку. Насправді використовують перемінний електричний струм частотою 50 Гц і напругою 25−35 кВ. Процесу электрообезвоживания сприяють деэмульгаторы підвищена температура. У уникнення випаровування води, соціальній та цілях зниження газообразования электродегидраторы — апарати, у яких проводиться електричне зневоднення і знесолювання нафт — працюють при підвищеному тиску. На НПЗ експлуатуються электродегидраторы трьох типів: циліндричні вертикальні з круглими горизонтальними електродами і подачею нафти на межэлектродное простір; такі апарати встановлено на электрообессоливающих установках ЭЛОУ 10/2; кульові з кільцевими електродами і подачею нафти з-поміж них; вони застосування на установках ЭЛОУ 10/6 (продуктивністю 2 млн. тонн нафти в рік); горизонтальні з прямокутними електродами і подачею нафти на низ апарату під шар отсоявшейся воды.
Характеристики электродегидраторов:
|Показники |Вертикальне |Кульової |Горизонтальні | | | |ЭДШ-600 |1ЭГ-160 ЭГ-160 | |Диаметр, м |3 |10,5 |3,4 3,4 | |Объем, м3 |30 |600 |160 160 | |Припустима | | | | |температура, 0С |70−80 |100 |110 160 | |Розрахунковий | | | | |давление, МПа |0,34 |0,69 |0,98 1,76 | |Производительност| | | | |ь, т/ч |10−12 |230−250 |180−190 200−250 | |Напруга між | | | | |электродами, кВ | | | | | |27−33 |32−33 |22−24 22−24 | |Напруженість | | | | |електричного | | | | |поля, кВ/см |2−3 |2−3 |1,0−1,5 1,0−1,5 |.
Электрообессоливающие установки проектують двухступенчатыми: в электродегидраторах 1-ой щаблі видаляється 75−80% (мас.) солоною води та 95- 98% (мас.) солей, а электродегидраторах 2-ой щаблі - 60−65%(масс.) відстояної емульсійної води та приблизно 92%(масс.) отстоявшихся солей. Кількість встановлюваних электродегидраторов при двухступенчатом обессоливании залежить від обсягу й якості (тобто. змісту води, солей та стійкості емульсії) оброблюваної нафти, від типу, і продуктивності апарату. Для сучасних электрообессоливающих установок проектують лише горизонтальні электродегидраторы, що входять у склад комбінованих установок ЭЛОУ-АТ і ЭЛОУ-АВТ. Перевагами горизонтальних апаратів є: велика площа електродів, отже й велика питома продуктивність (обсяг нафти одиницю перерізу апарату); менша вертикальна швидкість руху нафти, отже, і найкращий відстій води; можливість проведення процесу за більш високих температур і тисках. Подача сирої нафти на низ апарату забезпечує її додаткову промивання та проходження крізь два електричних поля: слабке — між дзеркалом води та нижнім електродом і сильне — між електродами. Підвищення напруги між електродами понад припустимого (22−24кВт) небажано, оскільки це викликає протилежний ефект — диспергирование крапельок води та збільшення стійкості эмульсии.
Апарати і технологимческие потоки на двоступінчастої обессоливающей установці з горизонтальними электродегидраторами показані на схемою. Вогка нафту насосом 1 прокачивается через теплообмінник 2, парові підігрівники 3 і з температурою 110−1200С вступає у электродегидратор 1-ой щаблі 4. Перед насосом 1 в нафту вводиться деэмульгатор, а після подогревателей 3 — розчин луги, який насосом 7. З іншого боку, в нафту додається відстояна вода, яка відводиться з электродегидратора 2- ой сходи й закачується в инжекторный змішувач 5 насосом 13. З допомогою насоса 8 передбачена також подача свіжої води. У инжекторном смесителе 5 нафту рівномірно перемішується зі лугом і води. Розчин луги вводиться подолання сірководневою корозії для нейтралізації кислот, які у нафту за кислотною обробці свердловин, а вода — для вимивання кристалів солей.
Нафта вступає у низ электродегидратора 4 через трубчастий розподільник 21 з перфорированными горизонтальними відводами. Знесолена нафту виводиться з электродегидратора згори через колектор 19, конструкція якого аналогічна конструкції розподільника. Завдяки такому розташуванню устрою введення та виведення нафти забезпечується рівномірність потоку з усього перерізу апарату. Відстояна вода відводиться через дренажні колектори 22 в каналізацію чи додатковий відстійник 12 (у разі порушення процесу відстою). З відстійника насосом 14 рідка суміш повертається у процес. З электродегидратора 1-ой щаблі згори в повному обсязі обезвоженная нафту надходить під тиском в электродегидратор 2-ой щаблі. У диафрагмовом смесителе 10 потік нафти промивається свіжої хімічно очищеної водою, поданого насосом 8. Вода для промивання попередньо нагрівається в паровому подогревателе 9 до 80- 900С; витрата води становить 5−10% (мас.) не на нафту. Обессоленая і обезвоженная нафту з верхи электродегидратора 2-ой щаблі відводиться з установки в резервуари знесоленої нафти, але в комбінованих установках вона нагрівається, і подається в ректификационную колону атмосферної установки.
Рівень води в электродегидраторах поллерживается автоматично, Частина води, що надходить каналізацію з электродегидраторов 1-ой і 2-ой щаблі, проходить оглядові ліхтарі 15 контролю якості отстоя.
Показники роботи двухступенчатых ЭЛОУ в різних нефтях:
|Завод, нефть |Зміст до ЭЛОУ |Зміст після |Витрата | |(щільність d420) | |ЭЛОУ |деэмульгатора | | | | |(г/т) |.
води,% солей, мг/л води,% солей, мг/л |Московський НПЗ, | | | | |Дисольван + | |ромашкинская |1,00 |1220 |0,1 |10 |ОЖК (25) | |(0,868) | | | | | | |Омський НПЗ, | | | | |Дисольван чи| |тюменська (0,858)|1,20 |180 |0,1 |3 | | | | | | | |ОЖК (20) | |Новоуфимский НПЗ,| | | | | | |тюменська | | | | |ОЖК чи | |(0,860) |1,1 |200 |0,08 |6 |сепарол (30) | | | | | | |ОЖК чи | |арланская |0,4 |697 |0,15 |10 |сепарол (30) | |(0,890) | | | | | | |Красноводский, | | | | | | |котуртепинская | | | | | | |(0,858) |0,51 |456 |Відсутність |49* |Дисольван (8) |.
*Нафта промивається морської водой.
Техніко-економічні показники роботи установки ЭЛОУ 10/6 і лідером блоку горизонтальних электродегидраторов на комбінованої установці ЭЛОУ-АВТ-6:
|Показатели |Три ЭЛОУ 10/6 |Блок ЭЛОУ-АВТ-6 | |Продуктивність, | | | |тис. тонн на рік |6000 |6000 | |Кількість электродегидраторов |6 |8 | |Витрата пара на нагрівання сировини, | | | |тис. МДж |900 |- | |Витрата електроенергії, | | | |тыс.мВт*ч |1,64 |0,79 |.
Установка ЭЛОУ-АВТ-6.
Установка ЭЛОУ АВТ-6 проиводительностью 6 млн. т/год здійснює процеси зневоднення і знесолення нафти, її атмосферно-ваккуумную перегонку і вторинну перегонку бензина. Схема цієї установки представлена малюнку. Вихідна нафту після змішання з деэмульгатором, нагріта в теплообменниках1, чотирма паралельними потоками проходить за два щаблі горизонтальних электродегидраторов 2, відбувається знесолювання. Далі нафту після додаткового нагріву в теплообменниках направляють у отбензинивающую колону 3. Тепло вниз цієї колони підводиться гарячої струменем XV, циркулюючої через піч 4. Частково отбензиненная нафту XIV з колони 3 після нагріву в печі 4 направляють у основну колону 5, где здійснюється ретефикация з отриманням парів бензину згори колони, трьох бічних дистилятів VIII, IX і X з отпарных колон 6 і мазуту XVI знизу колони. Овод тепла в колоні здійснюється верхнім испаряющим зрошенням і двома проміжними циркуляционными орошениями. Суміш бензинових фракцій XVIII з колон 3 і п’яти іде стабілізацію в колону 8, де згори відбираються легкі головні фракції (рідка голівка), а знизустабільний бензин XIX. Последний в колонах 9 піддається вторинної перегонці із отриманням вузьких фракцій, використовуваних як сировини для каталітичного риформінгу. Тепло вниз стабілізатора 8 і колон вторинної перегонки 9 підводиться циркулюючими флегмами XV, нагреваемыми в печі 14. Мазут XVI з основний колони 5 в атмосферної секції насосом подається в вакуумну піч 15, звідки з температурою 420 З направляетсю в вакуумну колону 10. У нижню частину цієї колони подається перегрітий водяну пару XVII. Згори колони водяну пару разом із газоподібними продуктами розкладання вступає у поверхневі конденсатори 11, звідки гази розкладання отсасываются трехступенчатыми пароэжекторными вакуумними насосами. Залишкове тиск у колоні 50 мм рт. У розділі ст Бічним погоном вакуумної колони служать фракції XI і XII, які насосом через теплообмінник і холодильник направляють у ємності. У перетинах вакуумної колони організовано проміжне циркуляционное зрошення. Гудрон XIII знизу вакуумної колони відкачують насосом через теплообмінник 1 і холодильник в резервуари. Апаратура й устаткування АВТ-6 займають майданчик 265×130м, чи 3.4га. У будинку розміщені підстанція, насосна для перекачування води та компресорна. Блок ректифікаційної апаратури примикає до одноярусному залізобетонному постаменту, у якому, як і установці АТ-6, встановлено конденсационнохолодильна апаратура і проміжні ємності. Під першим ярусом постаменту розташовані насоси технологічного призначення для перекачування нафтопродуктів. Як вогневих нагрівачів мазуту, нафти і циркулюючої флегмы застосовані многосекционные печі загальної теплової потужністю близько 160 млн. ккал/ч з прямим склепінням, горизонтальним розташуванням радиантных труб двостороннього опромінення та нижньої конвекционной шахтою. Печі споживають рідке паливо, сжигаемое в форсунках з повітряним распылом. Передбачено зокрема можливість використання як палива. Нижче наведені техніко-економічні показники установок АВТ різної продуктивності (на 1 т.нефти.):
Продуктивність, млн. т/год.
1 2 3 6.
Паливо жидкое, кг 38.5 30.7 32.4 27.7.
Электроэнергия, квт. ч 2.62 2.26 5.68 3.97 Вода, м3 21.7 15.5 8.51 4.47 Пара водяной (со стороны), млн. Ккал 0.11 0.09 0.008 — Експлуатаційні расходы, руб/год 1.0 0.79 0.63 0.44 Капітальні витрати, крб 1.76 1.30 1.24 1.05 Витрата металу на апаратуру, кг 1.86 1.64 1.26 0.58 Продуктивність праці в 1 раб., тыс. т 33.6 66.7 75.0 66.7.
Коротка характеристика технологічного оборудования Печи трубчасті факельные Теплопроизводительность печей:30.3, 38.52, 20.85, 29.66 млн. ккал/ч Призначені для нагріву сировини до температупы випаровування необхідних фракцій під час переходу нагрітого сировини в ректификационную колонну Колонна попереднього испарения Диаметр-5000мм; высота-32 500мм; розрахункове давление-8кг/см; розрахункова температура-240/360C; 24 тарілки клапанные, 2-х поточные-10шт, 4-х ппоточные-14шт; матеріал FG36TxTCr13.
Вакуумная колонна Высота-33 600ммм; Dч-4500мм, Dс-9000; Dф-3000мм; Розрахунковий давление-40 мм. рт. ст; розрахункова температура-400С; МатеріалFG36T/12.
Атмосферная колонна Длина-5000мм; высота-52 500мм; розрахункове давление-6 мм.рт. ст; Розрахункова температура-290−400С; 50 тарілок 2-х потокові клапанные; МатеріалFG36TxCr13.
Теплообменники Порядка 250−300С Призначені передачі тепла з більш нагрітого тіла менш нагрітому. У теплообменниках нагрівається вихідне сировину, яке надходить на переробку, а теплоносителями служать продукти переробки нафти та нагріті залишки Застосування теплообмінників дозволяє заощаджувати паливо, расходуемое на підігрів сировини, і навіть воду, подаваеммую для охолодження дистилятів. Трубчастий теплообмінник складається з корпусу, куди вмонтовано пучок трубок малого діаметра. Кінці трубок развальцованны у двох трубних ґратах. По трубкам прокачивается яке підігрівається сырье, по межтрубному простору у протилежному направлении-нагревающий пролукт. Теплопередача відбувається після поверхню трубок.
Барометрический конденсатор Температура-150 З Застосовують для конденсації парів нафтових дистилятів. Для охлаждния нафтових дистилятів після конденсації призначені холодильники.
Отпарная колонна Длина-2000мм;высота-28 500мм; розрахункове давление-6 кг/см; Розрахункова температура- 190 З; 6 клапанных 2-х потокових тарілок; Матеріал FG36T/13x7Cr.
Вторичной перегонки бензина Высота-45 880мм, длина-3600, давление-8 кг/см, Температура-200 З, 60 тарілок клапанные 2-х потокові, Материал-St52−3N.
Ректификационная колона блоку вторинної перегонки бензина Высота-45 840мм, длина3400, давление-8 кг/см, температура-120 З, 60 тарілок клапанные, материал-St52−3N.
Стабилизациооная колонна Высота-34 570мм, длина-3452мм, 40 тарілок клапанные-20 штук 2-х потокові, 20 штук- 4-х потокові, материал-St52−3N, Dн-3400мм, Dв-2600мм, давление-16 кг/см, температура-210 С.
Теплообменник нагріву нефти Длина-11 100мм, диаметр-1200мм, давление-ТП-40, температура-МП-450, матеріал- 16ГС-12 16ГС-120 8×13.
Ремонт установки АВТ.
За графіком трубчасту установку зупиняють на планову чистку і ремонт. І тому зі швидкістю 25−30 град/ч знижують температуру сировини на виході з вакуумної печі, припиняють відбір бічних фракцій та різко знижують вакуум. Залишок вакуумної колони відкачують в ємність. Воду з холодильників спускають, а залишений у неї і теплоообменниках продукт видувають пором через вакуумні бачки в запасну ємність. Останніми виключають вакуумні апарати і прилади, які під вакуумом. Коли температура сировини виході з вакуумної печі впаде до 3000С, гасять форсунки і припиняють введення повітря на піч; далі знижують температуру в атмосферної печі зі швидкістю 30 град/ч. При температурі 2400С переходять на циркуляцію нафти, при 2000С припиняють подачу палива й повітря на атмосферную піч, при 1500С припиняють подачу пара в колону, а при 100- 1100С припиняють циркуляйию сировини й видувають вміст труб печі в колону і далі через холодильник в ємність. Після 6−8-часовой продувки печей пором відкривають люки в топке.
Розрізняють три виду ремонту: поточний, середній та капітальний. Поточний ремонт проводиться повсякденно під час роботи установки. Середній ремонт ведеться за закінчення циклу робіт і 2−4 дня. Капітального ремонту проводиться переодически і радіомовлення продовжується триваліший время.
За середнього показника ремонті труби печей і теплообмінних апаратів очищають від відкладень, притирают несправні засувки, набивають сальники на вентилях, переглядають поплавки регуляторів рівнів, змінюють кишені для термопар, чистять водні холодильники від накипу, очищають пробки двійників і промащують їх графітової мастикою і др.
При капітальний ремонт змінюють чи відновлюють основну апаратуру установки. Часто при капітальному ремноте вдосконалюють технологічну схему процесу реконструюють установку. Капітального ремонту проходить за заздалегідь розробленого графіку. Обсяг робіт та його тривалість встановлюються дефектної декларації. Матеріалом упорядкування цієї відомості служать запис у книзі операторів, усні й зауваження і спостереження механіка. За підсумками цих записів становлять квартальний і річний графіки ремонта.
ВАКУУМНІ КОЛОННЫ.
ВАКУУМНА КОЛОНА УСТАНОВКИ ЭЛОУ-АВТ-6 НА МОСКОВСЬКОМУ НАФТОПЕРЕРОБНИМ ЗАВОДЕ Материал F036T/13x7Cr Габарити: высота-33 600мм діаметр (год)-4500мм діаметр (з)-9000мм діаметр (ф)-3000мм.
Vреакц. производства-1150м (3) Тарілки 1) 1.2,3,4,5,6,7,13,14,21,22,23,и 24 клапанные 2) 4а-глухая тарілка 3) 15,16,17-ситчатые тарілки 4) 7а-сборно-распределительная тарілка 5) замість 18 та19 тарілки встановлено струйный сепаратор 6) між 7а та дванадцяти тарілками встановлено перекрекрестноточная насадка.
T верхине вище 180 З Т низуне вище 380 З Ростаточное — щонайменше 40 мм.рт.ст. Витрата верхнього циркуляційного зрошеннятрохи більше 300 (м 3)/год Витрата середнього циркуляційного зрошеннятрохи більше 350 (м3)/ч Витрата фракції 420−500 З трохи більше 150 (м3)/ч в лінію СЦО Витрата перегрітого пара — трохи більше 6400 кг/ч.