Організація інструментального господарства на деревообробному виробництві
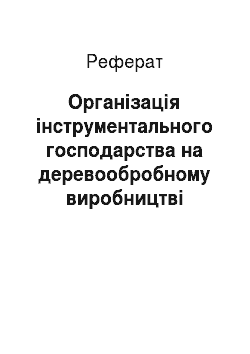
Вступ На даному етапі розвитку економіки більшість підприємств залежать від раціонального використання основних фондів держави. Основні фонди держави є однією із найважливіших складових будь-якого виробничого процесу, адже від їх величини залежать об'єм виробництва, потужність, а від обсягу використання обладнання і випуск готової продукції. На даний момент є актуальним забезпечення ефективного… Читати ще >
Організація інструментального господарства на деревообробному виробництві (реферат, курсова, диплом, контрольна)
Дипломна робота Організація інструментального господарства на деревообробному виробництві.
1. Загальна частина.
1.1 Вступ На даному етапі розвитку економіки більшість підприємств залежать від раціонального використання основних фондів держави. Основні фонди держави є однією із найважливіших складових будь-якого виробничого процесу, адже від їх величини залежать об'єм виробництва, потужність, а від обсягу використання обладнання і випуск готової продукції. На даний момент є актуальним забезпечення ефективного використання основних фондів. Вихід з ситуації, яка склалася вимагає пошуку нових варіантів господарювання, нових підходів, експериментів. Але складність виникає в тому, що більшість підприємств володіють старими основними фондами і не мають коштів на їх модернізацію. Актуальність цієї проблеми полягає також в тому, що продукція, яка збувалась централізовано тапер не може знайти свого покупця через не конкурентоспроможність, а також дуже високу ціну в порівнянні з іноземними аналогами виробництва.
Крім того підвищення використання основних фондів, зумовлене тим, що величина їх зростає, а віддачі немає. Оскільки діюче обладнання працює не в повну потужність, а нове обладнання в більшості випадків за своїми характеристиками мало відрізняється від діючого, проте його вартість набагато вища і це призводить до того, що на більшості підприємств не замінюють нове обладнання на діюче. Саме тому потрібно робити нові вкладення які спрямовуватимуться на реконструкцію і модернізацію діючих підприємств. При цьому вони сприятимуть покращенню використання діючих основних фондів, забезпечуватимуть повну потужність обладнання на більш прогресивне і високопродуктивне.
Зважаючи на те, що основні фонди — це матеріально-технічна база будь-якого підприємства, тому покращення їх використання приведе до більш ефективно підвищення виробничого процесу. Дбайливе використання основних фондів є базою для підвищення прибутків і зниження собівартості.
Необхідність теми дослідження полягає також в тому, що з переходом економічної системи від командно-адміністративної до ринкової, занепадає машинобудівна та оборонна галузь України, через скорочення військових замовлень. На цю проблему неодноразово звертали увагу Уряд та Верховна Рада України.
Сучасний етап розвитку економіки вимагає більше нових підходів, експериментів і аналізу ефективності використання основних засобів.
Коротка характеристика підприємства.
Дипломне проектування виконується на підприємстві ТзОВ «Женець» (далі Товариство), яке створене на засадах договору між Учасниками і здійснює свою діяльність з метою задоволення сучасних потреб у продукції, роботах, послуга, що ними постачаються, та реалізація, на основі одержаного прибутку, соціальних та економічних інтересів Учасників та членів трудового колективу Товариства.
Воно спеціалізується на випуску віконних та деревинних блоків, розпилу лісоматеріалу на бруси, дошки, виробництві меблів. Вся продукція виробляється на замовлення. Підприємство складається з виробничого цеху, в якому також знаходиться ремонтне і відділення для загострення, складів сировини і готової продукції, цеху для розпилювання деревини і приміщення для збору готової продукції. Виробничий цех обладнаний наступними верстатами: кругло пильний: ЦДК4−3, Ц6−2, ЦПА-40, власного виготовлення; стрічково пильний: ЛС80−6 і власного виготовлення; фугувальний СФ4; рейсмус ний СР6−6, фрезерні ФСШ1А і два ФС; свердлильний в торець і два СВА-3; чотирьох бічний С10−2.
Сировину підприємство закуповує на підприємствах Коломийського і Надвірнянського районів. На підприємство сировину завозять автомашини.
1.3 Характеристика існуючої системи організацій інструментального господарства і обґрунтування теми дипломного проекту.
Інструментальне господарство — це самостійна служба деревообробного підприємства, основним завданням якого являються:
Визначення потреб підприємства в деревообробному, абразивному і алмазному інструментах; визначення кількості в контрольно-вимірювальним, пилоправ ним інструментам і обладнанням використовуваним при підготовці ріжучого інструменту. Запланована купівля і забезпечення виготовлення власними силами ріжучих інструментів та забезпечення виробництва ріжучими інструментами; організація підготовки ріжучого інструменту, організація експлуатації ріжучого інструменту і технічний нагляд за його експлуатацією; забезпечення робочих місць ріжучим інструментом; організація нагляду і зберігання ріжучого, абразивного і алмазного інструменту.
Система організації інструментального господарства підприємства.
Інструментальне господарство — це самостійна служба деревообробного підприємства, основним завданням якого являються:
визначення потреб підприємства в деревообробному, абразивному і алмазному інструментах; визначення кількості в контрольно-вимірювальним, пилоправ ним інструментом і обладнанням використовуваним при підготовці ріжучого інструменту. Запланована купівля і забезпечення виготовлення власними силами ріжучих інструментів та забезпечення виробництва ріжучими інструментами; організація підготовки і ремонту ріжучого інструменту; організація експлуатації ріжучого інструменту і технічний нагляд за його експлуатацією; забезпечення робочих місць ріжучим інструментом; організація нагляду і зберігання ріжучого, абразивного і алмазного інструменту.
Система організації інструментального господарства на підприємстві може бути централізованою, децентралізованою і змішаною вибір системи проводиться при проектуванні нового чи реконструкції існуючого підприємства з врахуванням об'ємів і виду виробництва, кількості і територіального розміщення виробничих цехів підприємства. Відрізняють особливості централізованої системи — централізація управління всім центральним господарством і підготовки основного інструменту (не менше 70%-80% всієї кількості) в одному інструментальному цеху. Децентралізована система характеризується децентралізованим управлінням підготовки інструменту: в кожному виробничому цеху знаходиться підлегла начальнику інструментальна майстерня. Змішана система передбачає централізовану підготовку 30%-70% інструмента для ряду цехів і децентралізовану для решти. Використання цієї системи виправдано при не високій стійкості інструменту великих об'ємів підготовки і труднощах при транспортуванні важкого інструменту (круглих пил великого діаметру, стрічкових пил розпилювання колод, стругальних ножів). Переважно на підприємствах виділяють територіально-інструментальну майстерню лісопильного цеху, а інструменти всіх решти підготовляють централізовано-інструментальному цеху.
На діючих підприємствах, особливо великих необхідно добитися прогресивної централізованої системи організації інструментального господарства. Досвід централізованого управління і єдиної відповідальності за весь комплекс робіт по забезпеченню ріжучим інструментам найбільш передові підприємства, довів існування переваги централізації, дозволяючи: ефективно використовувати комплексну систему організації виробітку, праці, управління і заробітною платою; зменшити плинність кадрів; спеціалізувати робочих до підготовки окремих видів інструментів; використати метод співпраці професії; використати систему без дефективної праці; підвищити коефіцієнт робочого часу; покращити завантаження обладнання; перейти до підготовки інструменту в одну зміну (з видачею підготовленого інструменту в другу і третю зміни, через інструментально-роздаточні відділи); організувати контроль якісної підготовки інструменту; покращити умови для запуску нової техніки і заходів по підвищенню рівня інструментальної справи.
В майбутньому намічається відкриття централізованих цехів підготовки ріжучих інструментів, що обслуговують 25−30% підприємств. Це дозволить скоротити необхідну кількість обладнання, паралельно з цим застосовувати нові прогресивні конструкції ріжучого інструмента і технологічні режими підготовки його до роботи. Все це приведе до покращення якості інструменту і зменшенню необхідності інструменту не менш як на 25−30%.
При децентралізованій підготовці інструментальної системи організації господарства основним структурним підрозділом являється інструментальна майстерня, завідуюча головним механіком. При централізованій системі інструментальне господарство також включає наступні структурні підрозділи: інструментальну лабораторію; інструментальний цех; заточні майстерні; інструментально-роздаточне відділення; центральний інструментальний склад.
На підприємстві застосована децентралізована система організації інструментального господарства. Одним із недоліків цієї організації є те, що інструменти підготовляються до роботи в різних місцях. І це безпосередньо впливу на те, що інструмент довше перебуває у різних інструментальних цехах. Приміщення для підготовки інструменту недостатньо освітлене природнім світлом, що суттєво впливає на якість заточки чи іншої операції. Поганим є також те, що дуже мале приміщення для загострення і зварювальних верстатів. В приміщеннях для загострення працюють лише два робітника, які перевантажені роботою. З огляду на ці проблеми виникає проблема у розробці нового відділення для загострення інструменту.
Нова розроблена інструментальна майстерня дасть змогу пришвидшити підготовку інструменту до роботи, покращити освітлення, а також і підвищити якість підготовки інструменту до роботи.
Інструментальна лабораторія організовується переважно на меблевих і деревообробних підприємствах з великим об'ємом випуску продукції при необхідності розробки спеціального ріжучого інструменту і різних приспосіблень. Вона існує: розробка конструкцій і технологій виготовлення інструменту; вибір режиму підготовки і експлуатації інструменту; розробку доходів підвищення роботоздатності інструменту.
2. Технологічна частина.
2.1. Технологічний процес підготовки дереворізального інструменту.
Є три види пил: рамні пили, стрічкові і круглі.
Рамні пили — інструменту вигляді тонкої полоси на одній із кромок нарізані зуби. Їх використовують на лісопильних рамах для розпилювання колод і брусів на дошки. Рамні пили здійснюють повздовжне розпилювання, якщо поверхність пропилу паралельна волоскам деревини.
Рамні пили закріплюють комплексом в пильну рамку здійснюючи зворотно-поступальний рух від кривошипно-шатунного механізму. Цей рух пили являється головним.
В залежності від технологічного призначення розрізняють пили для вертикальних, горизонтальних і тарних лісорам. Пили для вертикальних лісопильних рам бувають двох типів: 1 — з планками (для лісопильних рам з нормалізованими пильним рамками і захватами); 2 — без планок (для лісопильних рам з ненормалізованими пильним рамками). На лісопильних підприємствах до цих пил прикріплюють планки захвати. Пили для тарних лісопильних рам — призначені для розпилювання тонкомірного круглого лісоматеріалу і брусів висотою 220 мм. Пили для горизонтальних лісопильних рам виготовляються на деревообробних підприємствах. Для збільшення жорсткості пили доцільно застосовувати пили мінімально доступною довжиною.
Стрічкові пили представляють собою інструмент у вигляді безкінченної стальної стрічки, на одній із кромок нарізані зуби. Стрічкові пили використовуються для повздовжньої розпилки колод, пиломатеріалів, а також для криволінійного розпилювання деревини, фанери і інших дерев’яних матеріалів. Головна перевага стрічкових пил — мала товщина стрічки, а значить менша ширина пропилу.
Промисловість випускає стрічкові пили для розпилювання деревини на столярних і ділильних стрічково-пильних верстатах, а також для розпилювання колод і брусів. Стрічкова пила як і рамка складається із полотна і зубчастого вінця.
Полотно стрічкової пили характеризується товщиною b, шириною В, і довжиною L (мм). Вузькі стрічкові пили використовують на столярних стрічкових верстатах для повздовжнього і поперечного розпилювання деревини і для випалювання криволінійних деталей. Широкі стрічкові пили застосовують при розпилюванні товстих дощок на більш тонкі.
При виборі товщини треба пам’ятати наступне: чим менша товщина пили менші відходи деревини в стружці, менша сила різання, але менша і жорсткість пили; чим товстіша пили, тим більше навантаження згибу при згинах стрічки на шківах.
Круглі пили представляють собою диск, на периферії якого сформовані зуби. Ці пили використовують для поздовжнього в поперечного розпилювання деревини і дерев’яних плит (ДВП, ДСТП, фанера, щити). В залежності від того де розташований центр пили, розрізняють дві основні схеми розпилювання круглою пилою: з верхнім і нижнім розміщенням пили. Промисловість випускає декілька типів круглих пил. Відрізняються вони різним технологічним призначенням. Найбільш поширені і універсальні пили з плоским диском. Вони бувають стальними з устаткуванням пластин твердих сплавів. В залежності від профіля зубів пили з плоским диском використовують для поздовжнього і поперечного розпилювання, фанери, ДВП, ДСТП, облицювальних щитів.
Пили з конічним диском бувають ліво-, і право, двосторонні. Вони використовуються для повздовжнього розпилювання пиломатеріалів на тонкі дощечки (до 15 мм). Лівосторонні (конус, зліва відносно руху подачі) призначені для відпилювання дощечка з лівої сторони дошки, а правосторонні з правої. Двохсторонні конічні пили застосовуються для розпилювання широких дощок товщиною до 40 мм. Обмеження по товщині зв’язані з тим, що канонічна частина пили повинна відігнути відпиляну дощечку. Конічні пили більш стійкі в роботі і зменшують кількість стружки приблизно в 2 рази по відношенню з плоскими пилами, за рахунок меншої товщини периферійної частини пили. Стругальні пили застосовують для чистової, повздовжньої і поперечної розпилювання деревини. Свою назву вони отримали в зв’язку з тим, що забезпечують шорсткість поверхні, так і процес поздовжнього фрезерування (по старій термінології - процес стругання). Висока якість поверхні пояснюється тим, що зуби струганих пил не розводять і не плющать. Для зменшення тертя пили об стінки пропила диск пили має бокові звуження під малим кутом (біля 0,5°). Це пили з зворотнім конусом (звужуються до центру пили). Стругальні пили мають більшу ширину пропилу, чим плоскі і тим більше конічні пили.
Фрези.
Фрезерувальний інструмент має багаточисельні конструктивні форми. Це пояснюється багатьма видами робіт, які можуть здійснюватись за допомогою фрез (формування плоских і профільних зовнішніх поверхонь деталей, обробка шипів, лазів і гнізд, копіювання …). Фрези — основний інструмент (ріжучий) повздовжньо — фрезерних, фрезерних-шипорізних, свердлильно-фрезерних, фрезерно-копіювальних, фрезерно-брусочних верстатів. Загальним для фрез являється кількість крутних навколо осі ріжучих елементів, кожна точка леза яка описує в обробному матеріалі циклопедіальну територію.
Фрези являють собою корпус встановлений на шпиндель верстатці формованими на ньому ріжучими елементами (зуби). Фрези класифікуюся по конструктивним ознакам: способу кріплення на верстаті, формі і розташуванні ріжучих кромок відносно осі обертання; способу сполучення ріжучого елемента з корпусом; формі задньої поверхні ріжучого елемента. За способом кріплення на верстаті розрізняють 2 види фрез: насадні і кільцеві.
Насадні фрези центральним отвором насаджують на шпиндель верстату. Для кращого забезпечення співвісності фрези інколи оснащують центруючими лонгами. Кінцеві фрези мають хвостовик для закріплення в патроні верстату.
По орієнтуванні ріжучих кромок фрези діляться на: циліндричні, торцево-канонічні і профільні. В профільних фрезах ріжуча кромка має криволінійні і прямолінійні ділянки і описує поверхню обертання складеного профілю. По способу сполучення ріжучого інструменту з корпусом фрези поділяються на: цільні, збірні і складні. Цільні фрези виготовляються із однієї заготовки, чи з корпусу з нерозмінним з'єднаним з ним ріжучим інструментом. При нероздільному з'єднанні ріжучий інструмент виготовляють у вигляді пластини з зносостійкого матеріалу. З'єднання пластини з корпусом із конструкційної сталі здійснюється за допомогою пайки. Цільні фрезери характеризуються високою врівноваженістю і точністю, що дозволяє експлуатувати їх при високій частоті обертання шпинделя. Збірні фрези складаються із корпуса, виготовленого із конструктивної сталі і закріпленим на ньому ріжучим елементом. Ножеві вали поздовжньо фрезерних верстатів близькі конструктивно збірним циліндричним фрезам. Складні фрези представляють собою комплект цільних чи збірних насадкових фрез установлених на один шпиндель і призначених для обробки складних профілів.
По способу закріплення і форми ріжучого елементу збірні фрези є різними. При роз'ємному з'єднанні ріжучий елемент (ніж) завжди утримується на корпусі силою тертя, для виникнення якої використовують гвинтові, клинові або клемні механізми.
По формі задньої поверхні ріжучого елемента розрізняють фрези з прямолінійними і криволінійними затилом. Фрези з прямим затилом називають гостоконічними. Вони прості у виготовленні, але по мірі експлуатації перетинок змінюються кутові параметри зубів і профіль оброблюваної деталі.
Використання таких фрез раціонально при відносно невеликому числі перетинок, наприклад при оснащенні зубів пластинками із стійкого матеріалу.
Ножі - ріжучі інструменти плоскої форми. Застосовують як самостійні ріжучі інструменти і як частина збірного ріжучого інструменту. Технологічне призначення ножів різне: покращення плоских і профільних поверхонь фрезерування (ножі для фрезерування), отримання струганого (стругані ножі), лущеного (лущильні ножі), для рубки шпона (ножі, ножиці) і для отримання стружки у випуску ДСП (стружні ножі).
Всі ножі виготовляють у вигляді пластин. По конструкції, до ножів дуже схожі нарамні лінійки лущильних і стругальних верстатів. Зажині лінійки також являють собою пластини з робочою фаскою. В залежності від способу кріплення у верстаті лінійки, так як і ножі, бувають без вирізів і з вирізами різної конфігурації. Профілі затискних лінійок по довжині відповідають довжині ножів лущильних і стругальних верстатів. Затисні лінійки служать для притискання шпону в процесі різання з ціллю передутворення появи в ньому тріщин.
Умови роботи ножів для фрезерування деревини аналогічні умовам збою фрези.
Умови роботи всіх міцних ножів дуже своєрідні і показують свій вплив на потреби до підготовки і експлуатації.
Свердла.
Свердління — це процес різання деревини обертовими ріжучими елементами з одночасною подачею в напрямку паралельному осі обертання. Кожна точка ріжучої крапки описує в деревині гвинтову поверхню. Свердління застосовують для отримання наскрізних отворів, або гнізд круглого січення.
Свердла — ріжучий інструмент у формі стержня з ріжучими елементами на торцевій частині. Основні частини свердла: робоча частина; шийка, хвостовик. Хвостовик циліндрична чи конічна частина свердла, яка служить для його закріплення в передачі крутного моменту. Циліндри від прокручування в патроні. Конічний хвостовик закінчується лапкою, виконуючи роль упора при вибиванні свердла із отвору шпинделя. Свердла з конічним хвостовиком швидше за все застосовують в обробці металів. Шийка проміж уточна частина, яка з'єднує хвостовик з робочою частиною свердла.
Робоча частина свердла складається із напрямної і головки. Напрямна служить для направлення свердла при роботі. Сформована на ній канавка необхідна для виведення стружки. Свердління глибоких дірок (глибиною більше діаметрів свердла) за один прохід можливо лиш при гвинтовій канавці.
Ріжуча частина (головка) складається з одної чи двох ріжучих кромок утворених пересіканням передньої і задньої поверхонь. Свердла з одною ріжучою кромкою випробовують на собі несиметричне навантаження, що приводить до зміщення і биття свердла при великих швидкостях подачі. Положення ріжучих кромок визначається в основному направленням свердла відносно волокон. Для свердління деревини вздовж волокон ріжуча кромка утворює з віссю свердла кут x03C6 = 40−45° (кут при вершині свердла 2×03C6 = х80−90°). Для свердління дерев’яних плит і деревини в поперек волокон характерно до осі ріжучих кромок до осі свердла (2×03C6 = 180°). Крім того, ріжуча частина таких свердл, має підрізний і направляючий центр.
2.2 Заходи по введенню твердосплавного інструменту.
Використання твердосплавного інструменту являється ефективним методом економії робочого часу та матеріальних ресурсів. Використання твердого сплаву дозволяю в десятки разів підвищити стійкість дереворізального інструменту і поліпшує якість обробки деталей. Досвід експлуатації таких інструментів на деревообробних підприємствах показав високу ефективність їх застосування на масових операціях, особливо при обробці клеєної деревини, плит і пластиків.
Крім того, ефективність твердосплавного інструменту в значній мірі залежить від технології його виготовлення і підготовки до роботи. Весь технологічний процес по виготовленню інструменту з твердого сплаву потребує великих трудозатрат при підготовці його до роботи і складається з трьох етапів: підготовчий (виготовлення корпусів, вибір і підготовка пластин твердого сплаву), закріплення пластин на корпусі, обробка інструменту з ціллю отримання кінцевих лінійних та кутових параметрів.
3. Розрахункова частина.
3.1 Програма цеху і режими його роботи.
Таблиця 3.1.
Характеристика обладнання та ріжучого інструменту.
№.
п/п Назва обладнання Марка верстату Кількість верстатыв Коротка характер-рис Назва різального інструме-нту Кількість інструменту Розмір інструменту Мате-ріал інстру-менту Примітка.
1 2 3 4 5 6 7 8 9 10.
1 Круглопильний верстат ЦА-2А 1 N=11,4кВт п=2870хв-1 пила кругла 1 Dmax= 450 мм 9ХС.
ВК15.
2 Круглопильний верстат ЦА-2 3 N=11,4кВт п=2870хв-1 пила кругла 1 Dmax= 450 мм 9ХС.
ВК15.
3 Круглопильний верстат для поперечного розпилювання ЦКБ-5 2 N3=14,6кВт п=1725хв-1 пила кругла 3 Dmax= 700 мм 9ХС.
З нижнім розміщенням пили.
4 Повздовжньо — фрезерний читирьохсторонній верстат С16−4А 2 N=21,3кВт п=6000хв-1 ніж 1 Ширина 160 мм, В=80 мм Сталь40Х.
5 Фрезерний верстат Ф-4 3 N=4,5кВт п=6000−8000хв-1 Фреза 1 Dmax= 80−150 мм Х6В9.
6 Фрезерний верстат Ф-5 1 N=7кВт п=6000−8000хв-1 Фреза 1 Dmax= 80−150 мм 9ХС.
ВК15.
7 Фрезерний карусельний верстат Ф2К-2 2 N=23,3кВт п=6000хв-1 Фреза 2 D= 125 мм Х6-ВФ.
8 Свердлильно-пазувальний верстат СВА-2 2 N=2,2кВт п=6000−8000хв-1 Свердло 4 D= 40 мм ХС.
9 Токарний верстат ТП-40 3 N=1,5кВт п=250−1010хв-1 Різець 22 В=25 мм, L=110 мм.
3.2 Розрахунок основного обладнання.
Обладнання для інструментальної дільниці повинно бути ефективним і сучасним.
Заточувальне обладнання для підготовки дереворізального інструменту вибираємо виходячи з умов його економічно доцільності для виробництва.
Добре зарекомендували напівавтоматичні верстати марки Т4ПК, Т4ПКз, П4КП15 для заточування круглих пил.
Для заточування дискових пил з пластинами із Т/С Т4ПТ4, 3Д642Е, 3Б642.
Кількість заточувальних верстатів для інструментальної майстерні визначаємо по формулі, шт.
(3.1.).
де S — необхідна кількість обладнання даного виду для підготовки дереворізального інструменту, шт.
n — кількість інструменту одного виду, що експлуатується, шт.
k — коефіцієнт випадкової поломки інструменту.
ti — норма часу на дану операцію підготовки інструментів, хв.
Fi — коефіцієнт, що характеризує періодичність виконання даної операції по відношенню до заточки.
Т — стійкість інструменту (год.).
G — кількість одночасно підготовлюваних інструментів, шт.
m — коефіцієнт змінності підготовки інструменту коефіцієнти взяті з [2] ст. 275−279, табл. 59, 60.
Розрахунок обладнання проводимо на кожний тип інструменту.
1. Проводимо розрахунок необхідної кількості обладнання для заточки 4 дискових пил з напайками пластин з Т/С.
шт.
ti Fi = (0,05 · 10 + 0,05 · 15 + 0,05· 40 + 0,05 · 15+ 0,05 · 20 + 0,05 · 30 + 0,05 · 50 + 4 · 1 + 10 · 0,1) = 31,75 хв.
Проводимо розрахунок необхідної кількості обладнання для заточки 2 дискових пил.
шт.
ti Fi = (15 · 0,2 + 15 · 0,25 + 40 · 0,25 + 10 · 1 + 4 · 1 + 10 · 0,1) = 31,75 хв.
3. Розрахунок необхідної кількості обладнання для 7 фрезерних плоских ножів L=600.
шт.
ti Fi = (4 · 1 + 1 · 1+5 · 1) = 10 хв.
4. Розрахунок необхідної кількості обладнання для 7 цільних фрез.
шт.
ti Fi = (15 · 1 + 4 · 1 + 6 · 1) = 25 хв.
5. Розрахунок необхідної кількості обладнання для 5 фрез з напайками із Т/С.
шт.
ti Fi = (20 · 1 + 6 · 1 + 6 · 1) = 32 хв.
6. Розрахунок необхідної кількості обладнання для 2 свердл.
шт.
ti Fi = (8 · 1) = 8 хв.
7. Розрахунок необхідної кількості обладнання для 14 токарних різців.
шт.
3.3 Вибір допоміжного обладнання.
Для заточки свердл і дискових пил і фрез з напайками із Т/С вибираємо верстат — 3М642Е.
Для заточки дискових пил вибираємо верстат Т4ПА-6.
3. Для заточки затилованих фрез вибираємо верстат — Т4ФА-2.
4. Для заточки свердл і токарних різців вибираємо універсальний заточний верстат — Н/О.
5. Для заточки плоских фрезерних ножів вибираємо 2 верстати Т4Н6−8.
Розрахунок додаткового обладнання.
Оскільки на виробництві застосовуються інструменти (пили, ножі, фрези), що потребують додаткової підготовки, ми повинні вибрати ряд додаткової підготовки, ми повинні вибрати ряд додаткового обладнання.
1. Верстат для вальцювання круглих пил ПВ-35 — 1 шт.
2.Верстат для розводки зубів круглих пил РПК8 — 1 шт.
3. Верстат для обрізки і насічки зубів круглих пил — ПШ6 — 1 шт.
Універсальний заточувальний верстат н/о.
Таблиця 3.2.
Перелік обладнання інструментальної дільниці.
№.
п/п Назва обладнання Кількість штук Марка Потужність кВт Загальна потужність кВт.
1 2 3 4 5 6.
1 Універсальний заточувальний верстат 1 3М642Е 2,5 2,5.
2 Напівавтоматичний заточувальний верстат 1 Т4ПА-6 1,3 1,3.
3 Заточувальний верстат 2 Т4ФА-2 3,42 3,42.
4 Напівавтоматичний заточувальний верстат 2 Т4Н6−8 2,225 4,45.
5 Універсальний верстат 2 Н/О 1,2 2,4.
6 Верстат для вальцювання круглих пил 1 ПВ-35 1,5 1,5.
7 Верстат для розводки зубів круглих пил 1 РПК8 1,2 1,2.
8 Верстат для обрізки і насічки зубів і круглих пил 1 ПШ-3М 1,0 1,0.
17,7.
З метою ефективного використання обладнання зупиняємо свій вибір на користь більш нових, а значить продуктивніших верстатів.
3.4 Розрахунок річної кількості верстатного інструменту.
Розрахунок річної кількості верстатного інструменту провадимо по формулі, шт.
шт. (3.2.).
[1] ст. 195.
де N — кількість годин роботи інструменту в рік.
n — число однакових інструментів в комплектів на верстат, шт, а — величина допустимого сточування інструмента, мм в = зменшення робочої частини інструменту за 1 переточку, мм.
t — тривалість роботи інструменту без переточки, год.
g — процент на поломку і непередбачувані витрати кількість годин роботи інструменту в рік визначаємо по формулі.
N = Тзм · Dр · і · Кр, год (3.3.).
[2] ст. 73.
де Тзм — тривалість зміни, год.
Dр — число робочих днів в році (260).
і = змінність роботи обладнання (і = 1).
Кр — коефіцієнт використання робочого часу (0,8).
N = 8 · 260 · 1 · 0,8 = 1664 год.
Розрахунок річної кількості інструменту для 5 верстатів Ц-6.
шт.
Розрахунок річної кількості інструменту для верстату ЦА-2А.
шт.
Розрахунок річної кількості інструменту для трьох верстатів ЦА-2.
шт.
Розрахунок річної кількості інструменту для двох верстатів ЦКБ-5.
шт.
Розрахунок річної кількості інструменту для 2-х верстатів С16−4А.
шт.
при довжині ножа 600 мм, вибираємо3,5 ножа на 1 верстат Розрахунок річної кількості інструменту для 3-х верстатів Ф-4.
шт.
Розрахунок річної кількості інструменту для верстату В-5.
шт.
Розрахунок річної кількості інструменту для 2-ох верстатів Ф2К-2.
шт.
Розрахунок річної кількості інструменту для 2-ох верстатів СВА-2.
шт.
Розрахунок річної кількості інструменту для 3-ох верстатів ТП-40.
шт.
Розрахунок річної кількості інструменту для 2-ох верстатів ТВ63.
шт.
Розрахунок річної кількості інструменту для 2-ох верстатів ТД20.
шт.
Коефіцієнт [1] стор. 196.
Кількість інструменту, які необхідні для роботи цеху в рік.
Пили дискові стальні - 20 шт.
Пили дискові з напайками пластин із Т/С — 4 шт.
Фрези з напайками із пластин Т/С — 1 шт.
Фрези цільні - 15 шт.
Ножі плоскі фрезерувальні L=600 — 44 шт.
Свердла — 14 шт.
Різці токарні - 88 шт.
Таблиця 3.3.
Характеристика різального інструменту.
№.
п/п Назва обладнання Марка верстату Кількість.
верстатыв Дереворізальний інструмент Кількість дереворізального інструменту Річна кількість дереворіз-зального інструменту.
1 2 3 4 5 6 7.
1 Круглопильний верстат ЦА-2А 1 Пила кругла з напайкою Т/С 1 1.
2 Круглопильний верстат ЦА-2 3 Пила кругла з напайкою Т/С 1 3.
3 Круглопильний верстат для поперечного розпилювання ЦКБ-5 2 Пила дискова 1 20.
4 Повздовжньо — фрезерний читирьохсторонній верстат С16−4А 2 Ніж 3,5 44.
5 Фрезерний верстат Ф-4 3 Фреза цільна 1 9.
6 Фрезерний верстат Ф-5 1 Фреза з Т/С 1 1.
1 2 3 4 5 6 7.
7 Фрезерний карусельний верстат Ф2К-2 2 Фреза цільна 2 6.
8 Свердлильно-пазувальний верстат СВА-2 2 Свердло 1 14.
9 Токарний верстат ТП-40 3 Різець 2 38.
10 Токарний верстат ТВ-63 2 Різець 2 25.
11 Токарний верстат Та-20 2 Різець 2 25.
3.5 Розрахунок кількості абразивного інструменту.
Кількість абразивного інструменту для чорнової і чистової заточки визначаємо за формулою:
шт. (3.4.).
де ва — розхід абразивного інструменту на одне заточування, шт.
Р — розрахунок річної потреби різального інструменту, шт.
— число переточувань за весь період служби інструменти.
Коефіцієнт [3] стор. 281 табл. 63.
1. Розраховуємо кількість абразивного інструменту для чорнової і чистової заточки круглих пил з напайками пластин із Т/С.
шт.
2. Розраховуємо кількість абразивного інструменту для чорнової і чистової заточки дискових пил.
шт.
3. Розраховуємо кількість абразивного інструменту для чорнової і чистової заточки фрез з напайками із пластин Т/С.
шт.
4. Розраховуємо кількість абразивного інструменту для чорнової і чистової заточки кінцевих фрез.
шт.
5. Розраховуємо кількість абразивного інструменту для чорнової і чистової заточки свердл.
шт.
6. Розраховуємо кількість абразивного інструменту для чорнової і чистової заточки токарних різців.
шт.
3.6 Розрахунок інших необхідних матеріалів.
Розраховуємо кількість доводочних брусків.
1. Розраховуємо кількість брусків для дискових стальних пил.
шт.
2. Розраховуємо кількість брусків для плоских фрезерних ножів.
шт.
3. Розраховуємо кількість брусків для цільних стальних фрез.
шт.
4. Розраховуємо кількість брусків для свердл.
шт.
5. Розраховуємо кількість брусків для токарних різців.
шт.
Складаємо відомість на абразивний інструмент Таблиця 3.4.
Відомість на абразивний інструмент.
№.
п/п Назва абразивного документу Тип, форма Кіль-кість Основні розміри.
1 2 3 4 5.
1 Заточка пил ЧТ 20 300×10×32.
2 Заточка свердл і кінцевих фрез ЗП 7 150×8×32.
3 Заточка фрезерних плоских ножів ЧЦ 54 200×80×75.
4 Заточка пил і фрез із Т/С 12А2 2 125×40×32.
5 Доводочні бруски БЧ 444 150×20×10.
6 Заточка ткарних різців ПП 81 150×20×10.
[3] ст. 53−55 табл. 8.
3.7 Розрахунок чисельної кількості робітників і складання штатної відомості.
Необхідну кількість робітників визначаємо по формулі:
чол. (3.5.).
Де R — кількість робітників в одну зміну для підготовки інструменту одного виду.
L — кількість інструменту одного виду, що підлягає підготовці в одну зміну, шт.
а — коефіцієнт, що враховує втрати часу на нормативні роботи, а = 1,15 — пил, а — 1, 07 — ножів, фрез, свердл.
Тзм — тривалість зміни, хв.
0,7.
n — число операції підготовки інструменту одного виду.
ti — середній час однієї конкретної операції, хв.
Fi — коефіцієнт періодичності даної операції.
Gi — кількість інструменту одночасно підготовлених на одному верстаті.
Кількість інструменту одного виду, що потребують підготовки в зміну, шт.
(3.6.).
де Z — кількість інструменту одного виду, експлуатується одночасно, шт.
t — тривалість зміни, год.
k — коефіцієнт випадкових втрат.
Т — стійкість інструменту, год.
[3] ст. 274−276 таблиця 59−60.
1. для пил з напайками з пластин із Т/С.
шт.
2. для пил дискових стальних.
шт.
3. для плоских фрезерних ножів.
шт.
4. для фраз з напайками із пластин Т/С.
шт.
5. для стальних цільних фрез.
шт.
6. для свердл стальних.
шт.
7. для токарних різців.
шт.
1. Кількість робітників, що необхідні для заточки пил з пластинами із Т/С.
чол.
2. Кількість робітників, що необхідні для заточки дискових пил.
чол.
3. Кількість робітників, що необхідні для заточки плоских фрезерних ножів.
чол.
4. Кількість робітників, що необхідні для заточки фрез з пластинами із Т/С.
чол.
5. Кількість робітників, що необхідні для заточки стальних цільних фрез.
чол.
6. Кількість робітників, що необхідні для заточки стальних свердл.
чол.
7. Кількість робітників, що необхідні для заточки токарних різців.
чол.
В загальному приймаємо 5 чоловік Таблиця 3.5. .
Штатна відомість робітників заточної дільниці.
№.
п/п Назва спеціальності Кількість робітників Розряд робочих Тариф за 1 год.
1 2 3 4 5.
1 Заточник 1 ІІІ 0,806.
2 Заточник 1 VІ 1,035.
3 Заточник-пилоправ 1 ІV 0,876.
4 Заточник 2 V 0,925.
Всього 5.
Вибір допоміжного устаткування При виборі допоміжного обладнання необхідно передбачити.
1. Слюсарний верстат з лещатами.
1 робоче місце для контролю і правки інструменту.
5 шаф для інструменту для кожного робітника.
3.8. Експлуатація обладнання При підготовці деревообробного інструменту до роботи персонал інструментального цеху повинні строго дотримуватись правил експлуатації обладнання, а також техніки безпеки і виробничої санітарії.
Загальні правила по техніці безпеки при роботі з різальним інструментом наступні:
1. Переносити різальний інструмент можна тільки в спеціальних футлярах, або в спеціальних ящиках.
2. Бокові поверхні пильних дисків повинні бути гладкими і мати тріщин, не допускається відсутність дво або більше зубів. Дискові пили повинні бути збалансованими.
3. При встановленні і доводці різального інструменту на верстаті, його шпинделі і оправка повинні бути закріплені нерухомо. Загвинчувати гайки закріплення різального інструменту дозволяється тільки стандартними ключами.
4. Абразивні круги повинні закріплятись на валу боковими шайбами діаметром не менш половини діаметра круга. Між шайбами і кругом повинні бути встановлені еластичні прокладки.
5. Круги, на заточних верстатах, повинні бути огороджені стальним кожухом товщиною 3−5 мм. Перед установкою шліфувальний круг оглядають, щоб збутися тріщин, вибоїн і інших дефектів. А потім випробовують на випробувальному розривному стенді. Число обертань при випробуванні повинно бути на 50% більше робочого числа.
6. Заточний верстат повинен бути забезпечений спеціальним козирком — екраном, оберігаючи оці робітника від абразивного і металічного пилу. Цей козирок-екран повинен бути змонтований з пусковим приспосібленням. При відсутності екрана працювати без захисних окулярів заборонено.
7. щоб виключити травми через розрив абразивного інструменті при заточуванні, заборонено находитися не проти кругу в площині його обертання.
8. Чистку, змащування, регулювання і ремонт заточного верстата, можна проводити тільки при повній зупинці шліфувального круга. Зупиняти круг руками, або іншим стороннім предметам, суворо заборонено. Всі робітники повинні твердо знати і виконувати всі правила по техніці безпеки і промислової санітарії.
Розрахунок площі цеху, планування розташування робочих місць і обладнання.
Розрахунок площі цеху.
Приміщення цеху повинно бути досить просторим та відповідати всім санітарним нормам, які до нього ставляться. Виробничі площі цеху визначаються:
Fц = 1,2 — 1,25 (FВ + FД + FМ + FП), кв.м. (3.7.).
де Fц — загальна площа цеху.
1,2 — 1,25 — коефіцієнти на проходи і проїзди під верстатне обладнання.
FВ — площа під верстатне обладнання, м2.
FД — площа допоміжного обладнання, м2.
FІМ — площа індивідуальних кафів, м2.
FП — площа побутових приміщень.
Площа під верстатне обладнання, м2.
(3.8.).
де g — площа одного верстату, м2.
n — кількість одиниць обладнання, шт.
По аналогічній формулі вираховуємо площу додаткового обладнання.
Площу основного обладнання розраховуємо виходячи із норми 8−12 м2 на одиницю обладнання, допоміжного 5 м² на одиницю, індивідуальних кафів — 0,5 м² тоді.
FВ = 10 · 8 = 80 м².
FД = 2 · 5 = 10 м².
Fім = 5 · 0,5 = 2,5 м².
Площу побутових приміщень визначаємо графічним способом виходячи з умов «Санітарних норм проектування промислових підприємств» СН245−71. Так для 5 працюючих необхідно 2 санвузли з умивальником, 2 умивальники, 1 умивальник, 2 душеві клітки з приміщенням для переодягання.
Товщина перегородок 0,25 м.
Fс = 3,3 · 5,25 = 17,33 м³.
Fк = 9 м².
Fкв = 30 м².
де Fс — площа санвузлів, умивальників, душових, м2.
Fк — площа курилки, м2.
Fкв — площа кімнати відпочинку, м2.
Тоді Fм =Fс + Fк + Fкв, м2 (3.9.).
Fп = 17,33 + 9 + 30 = 56, 33, м2.
Площа цеху, м2.
Fд = 1,2 · (80 + 10 + 2,5 + 56,33) = 178,8 м².
Виходячи з стандартних розмірів панелі перекриття 12, 18, 24 м вибираємо панель довжиною 12 м. Отже, ширина цеху 12 м.
Довжину знаходимо виходячи з умови.
L = Fц/В, м.
де L — довжина цеху.
Fц — площа цеху, м2.
В — ширина цеху, м.
L = 178,8: 12 = 14,88 = 15 м.
Отже, оптимальна площа цеху дорівнює.
Fц = В · L, м2 (3.10.).
Fц = 15 · 12 = 180 м².
Висота цеху Н в інструменталці по нормі становить — 6 м.
Тоді об'єм цеху визначаємо:
Vц = Fц · Н, м3 (3.11.).
Vц = 180 · 6 = 1080 м³.
Організація прийому зберігання і видачі дереворізального інструменту.
Робочі місця забезпечуються різальним інструментом через ІРК.
В цехах деревообробки, постачання різальним інструментом робочих місць і повернення його на перепідготовку доручають верстатникам.
Різальний інструмент здається на заточування верстатником в спеціальну комору, де взамін отримує заточений інструмент. Різальний не заточений інструмент поступає в інструментальний цех, де заточується і знову попадає в комору для заміни не заточеним інструментом.
4. Енергетична частина.
4.1 Розрахунок необхідної силової електроенергії.
Розрахунок необхідної силової електроенергії проводимо по формулі.
кВт · год. (4.1.).
де Wу — загальна встановлена потужність електродвигунів обладнання, кВт Т — час роботи електродвигунів в рік, год.
Кс — коефіцієнт, що враховує завантаження обладнання на період зміни Кс = 0,8.
— коефіцієнт втрати в електромережі.
(1,06 — 1,08).
Т = N · n · t, год. (4.2.).
де N — кількість змін роботи.
n — кількість змін роботи.
t — тривалість зміни роботи Т = 260 · 1 · 8 =2080 год.
тоді.
Wc =17,77· 0,8 · 2080 · 1,07.
Wc = 31 639, кВт · год.
Розрахунок витрат електроенергії на освітлення .
Розрахунок витрат електроенергії на освітлення провадимо по формулі.
кВт · год. (4.3.).
де Р — потужність всіх ламп, кВт.
Т — час роботи лампи в рік, год.
К — коефіцієнт одночасної роботи лампи, 0,98.
— коефіцієнт втрат в електромережі.
= 1,06.
Для інструментальної дільниці вибираємо люмінесцентні лампи освітлюваністю 150 лК, при цьому їх потужність буде становити.
36 Вт на 1 м² площі цеху.
потужність всіх ламп, Вт.
Рл = Fу · Р (4.4.).
де Р — потужність однієї лампи, Вт.
Рл =180 · 36 = 6480= 6,48 кВт.
Час роботи Т лампи в рік на даній географічній широті (широта по Харків) при однозмінній роботі обладнання — 410 год.
Тоді.
Wo = 6,5 · 410 · 0, 98· 1,06.
Wo = 2768,4 кВт · год.
[4] ст. 89−90.
Розрахунок природного освітлення.
Розрахунок природного освітлення включає в себе розрахунок площі вікон, та розмір віконних блоків.
Площу вікон розраховуємо по формулі.
Fу, м2 (4.5.).
де Fо — площа всіх вікон в цеху, м2.
Fу — площа підлоги цеху, м2.
· 180 = 36, м2.
Кількість віконних блоків вираховуємо по формулі.
шт. (4.6.).
де В — кількість вікон, шт.
Fб — площа віконного блоку, м2.
Віконний блок вибираємо виходячи з його стандартного ряду ширина — 2943 мм.
довжина = 1782 мм віконний блок з внутрішнім відкриванням стулок тоді.
Fб = 2943 · 1782 =5,3 м².
Отже, кількість блоків.
= 7 блоків.
Розрахунок пари на опалення .
Розрахунок витрат на опалення проводиться по формулі:
т (4.7.).
де П — витрати на пари на опалення в рік, т.
Q — розхід тепла, ккал/год.
in — теплоємність пари, 630 ккал/кг.
t — час роботи опалення в рік, год.
Для нашої географічної широти опалювальний сезон триває 210 днів. Розхід тепла на 1 м³ об'єму становить 20 ккал/год. В неробочий час температура в цеху понижується, вентиляція не працює і розхід пари зменшується.
Орієнтовано в неробочий час пари становить 50% від робочого.
Об'єм цеху становить 1080 м³.
а) розхід тепла в робочий час на 1 год Qp = 20 · 1080 = 221 600 ккал/год.
б) розхід тепла на 1 год в неробочий час.
Qн = 21 600 · 0,5 = 10 800 ккал/год.
в) час опалення в цеху в робочий час за рік (враховуючи, що з 210 днів — 60 вихідних).
tр = (210 — 60). Тзм, год. (4.8.).
де Тзм — тривалість зміни, год.
tр = (210 — 60) · 8 = 1200 год.
г) час опалення в робочий день в неробочий час.
tр = (210 — 60) · 16 = 2400 год.
д) час опалення в неробочі дні.
tнд = 60 · 24 = 1440 год.
тоді розхід пари на опалення в робочий час.
т Розхід пари в неробочий час і вихідні дні.
т Загальний розхід пари в рік Пз = 41,15+65,83 = 106,98 т.
[2] стор.
Розрахунок води на санітарно-побутові та технологічні потреби.
а) Витрати води душовими кабінами, м3/рік, по формулі:
(4.9.).
де 500 — розхід води окремим душем, л.
n — кількість душевих кліток, шт.
0,75 — час дії душу, год/зміни.
N — кількість зміни у році.
м3.
б) витрати води умивальниками, м3 в рік.
(4.10.).
де 200 — розхід води одним умивальником, л.
m — кількість умивальників, шт.
0,75 — тривалість дії умивальника год/зміну.
N — кількість змін в рік.
м3.
в) витрати води на господарсько-побутові потреби, м3/рік.
(4.11.).
де 25−45 — витрати води на одного працюючого в зміну, л.
k — кількість працюючих, чол.
N — кількість змін в році.
м3.
г) загальна кількість води на інструментальний цех, м3 на рік Аз = Ад + Ау + Агп (4.12.).
Аз = 195 + 117 + 32,5 = 344,5 м³.
5. Охорона праці.
5.1 Значення охорони праці і довкілля в забезпеченні безпечних і здорових умов праці та нормальної екологічної обстановки.
Значення охорони праці і навколишнього середовища в забезпеченні безпечних і здорових умов праці і нормальної екологічної обстановки.
Значення охорони праці в забезпеченні безпечних і здорових умов праці, підвищення її безпечності сильно впливають на продуктивність праці, якість і собівартість продукції.
Згідно з КЗпП підприємства для підвищення міроприємств по охороні праці виділяють кошти і необхідні матеріали. Розхід цих коштів і матеріалів не по призначенню суворо забороняється.
Забезпечення безпечних умов праці накладається на адміністрацію підприємства. Адміністрація повинна випроваджувати сучасні засоби техніки безпеки, попереджувати виробничий травматизм і забезпечувати санітарно-гігієнічні умови, запобігаючи виникненню професійних захворювань працюючих і службовців. Також адміністрація зобов’язана проводити організаційну роботу по забезпеченню безпечних і здорових умов праці (планування і фінансування різних міроприємств по охороні праці, проведення інструктажу по техніці безпеки і виробничій санітарії).
Питання по охороні праці і навколишньому середовищі приділяється значна увага. На охорону праці виділено згідно з даними приведеними в колективному договорі кошти на проведення наступних заходів по охороні праці:
санітарно-курортне лікування і відпочинок;
на медичне обслуговування;
видача працівникам з шкідливими умовами праці кисломолочних продуктів чи їх замінників;
видача одноразової матеріальної допомоги;
безкоштовна видача спецодягу, спецвзуття та інших ЗІЗ;
надання додаткової оплачуваної відпустки працівникам з шкідливими умовами праці.
На дільниці, яка проектується, можуть статися такі небезпечні факти, як пожежа, травматизм, шум, отруєння парами масел.
Значної шкоди на організм людини, на виробництві, завдає шум і вібрація. При роботі верстатів створюється табельний широкополосний шум з рівнем 80−85Дб. До основних джерел шуму відносяться електродвигуни верстатів, зубчасті передачі, клиноремінні передачі, підшипники кочення. Найбільше шуми впливають на роботу мозку, що приводить до стоми, порушується сприйняття оперативної інформації, уповільнюється реакція і т.д.
Майже всі перераховані джерела шуму являються джерелами вібрації, яка також небезпечні для людини. Під дією вібрації порушуються функції серця, центральної нервової системи і т.д. Найбільш небезпечними є одночасна дія вібрації і шуму на організм людини.
Для охолодження і змазки вузлів обладнання використовують МОР, і масла, які виділяють токсичні гази, пари, шкідливі для організму людини.
5.2.Забезпечення нормальних умов праці.
5.2.1 Номенклатура санітарно — побутових приміщень.
Перш за все забезпечення нормальних умов праці основується на точному дотримуванні і виконуванні усіма працюючими правил техніки безпеки.
Метеорологічні умови виробничого середовища складаються з температури навколишнього середовища, повітря, його вологості, швидкості руху і відбиття від нагрітих предметів. Ці параметри повинні відповідати нормативам ДСТУ 12.1.005−78 (загальні санітарно-гігієнічні вимоги до повітря робочої зони).
Раціональне освітлення виробничих приміщень, робочих місць має досить важливе значення, воно полегшує працю, знижує небезпеку травматизму. Освітленість нормується згідно Сніп-ІІ-4−79. Освітлення здійснюється через вікна, при недостатньому освітленні використовується штучне. По СніПу-ІІ-4−79 визначаємо розряд зорової роботи.
Для обміну повітря і забезпечення чистоти використовується приточно-витяжна вентиляція. Через труби діаметром 500 мм виводиться з цеху забруднене повітря, а для попадання чистого повітря в цех з підвітряного боку відкривають пройоми. В системі вентиляції використовують вентилятори осьового типу уЗ-04 і радіальні у4−76.
Культурно-побутові приміщення повинні відповідати стандартним нормам. При перервах в 30 хв. їдальня повинна знаходитись 300 метрів від основних приміщень, а при перерві 1 год. — 600 м.
Робітники забезпечуються спеціальним одягом за рахунок виробництва, по встановленим нормам на певний період. Спецодяг зберігається в гардеробі. Для покращення умов праці на дільниці розміщений фонтан для пиття води, аптечки першої медичної допомоги закріплені на висоті 1,5 м біля столу контролера ВТК.
Таблиця 5.1.
Номенклатура санітарно-побутових приміщень.
№.
п/п Назва приміщення Назва побутового обладнання Норма площі на 1 чол по СНіП Кількість працюючих Всього площі Фактична площа «битовки» м2.
1 2 3 4 5 6 7.
1 Гардероб Шафа подвійного розміщення 50×40. Шафа одно дверна.
2 Душеві сітки.
3 Умивальники креми.
4 Кімната гігієни кабіни 1×1,45.
5 Автомати газ води.
5.2.2 Оптимальні значення метеорологічних умов в робочих зонах виробничих приміщень.
Таблиця 5.2.
Оптимальні значення метеорологічних умов в робочих зонах виробничих приміщень.
Характеристика приміщень Категорія робіт Період року Темпера-тура x00BAС Відно-сна воло-гість Швидкість руху повітря м/с.
1 2 3 4 5 6.
Приміщення характерні незначними надлишками явної теплоти 23Вт/м2 Середньої важкості холодний 17−19 60−30 найбільше 0,3.
теплий 20−25 60−30 0,4−0,6.
5.2.3 Характеристика штучної вентиляції.
Таблиця 5.3. .
Характеристика штучної вентиляції.
Приміщення Тип вентиляції (витяжної,.
приточної, притяжний відсос) Вентиляційне обладнання Кратність повітряного обміну.
1 2 3 4.
Цех Приточна Ц3−0,4; Ц4−76 К=3.
5.2.4 Засоби індивідуального захисту працівників.
Таблиця 5.4. .
Засоби індивідуального захисту працівників Шкідливий виробничий фактор Призначення СИЗ Назва СИЗ (марка, характеристика) Професія працюючих.
1 2 3 4.
Механічні пошкодження органів зору і дихання Захист органів.
зору і дихання Окуляри захисні ГОСТ 12.4.003.-74 Наладчики технологічного обладнання.
Шум і вібрація Захист органів слуху і внутрішніх Вкладиші (знижують рівень шуму від 5−20 Дб).
Віброзихисні пластини.
(захищають робоче місце оператора) Оператори.
5.3 Забезпечення безпеки технологічних процесів монтажу і експлуатації обладнання.
Без строгої трудової і виробничої дисципліни і точного виконання інструкцій по охороні праці неможливе забезпечення безпечних і здорових умов праці, тому охороні праці на усіх ділянках роботи приділяють особливу увагу.
На спроектованій ділянці використовується середнє промислове обладнання. Без використання підйомо-транспортних механізмів, без проведення земляних і бетонних робіт монтаж обладнання не можливий. Для монтажу використовують автокрани, тельдофний кран, засоби малої механізації. При роботі з підйомними механізмами особливу увагу треба звертати на стан приладів, обмежувач вантажопідйомності, болтові і зварні з'єднання.
Монтаж штучного освітлення зв’язаний з використанням з напругою до 1000 в. при монтажі освітлення використовують спеціалізовані транспортні пересувні засоби. роботи слід проводити після ознайомлення робітників з технікою безпеки при роботі на висоті, а також обов’язково при виключеному джерелі струму і справним інструментом.
5.3.1 Технічні міри захисту виявлення потенційнонебезпечних виробничих факторів.
Таблиця 5.5.
Технічні міри захисту виявлення потенційнонебезпечних виробничих факторів.
Небезпечний фактор виробничого середовища Спроектований.
чи вибраний захисний.
пристрій Технічна характеристика пристрою чи засобу Місце установки на плані чи агрегаті строки використання.
1 2 3 4.
Опік під час ізоляційних робіт Індивідуальні засоби захисту Діелектричні рукавиці ТУ-38−40 632−72. чоботи резинові діелектричні ТУ-38−1-108−97−70 Місце виявлення Небезпека електро-травматизму ІЗЗ, заземлення Рукавиці резинові діелектричні ТУ-38−40−632−72 провід чи штирі заземлення Верстати, кран-балка.
5.4 Пожежна безпека.
Проаналізувавши літературні джерела і можливі причини виникнення пожежі враховуючи пожежну безпеку технологічно процесу згідно СНіП-ІІ 09−02−85 інструментальний цех по пожежній, вибуховій і вибухопожежній небезпеці відноситься до категорії 1 В.
При виборі електрообладнання, яке необхідно встановити в приміщенні цеху і за його межами враховують степінь пожежної небезпеки цеху.
5.4.1 Пожежонебезпечні властивості використовуваних засобів і матеріалів.
Таблиця 5.6.
Пожежонебезпечні властивості використовуваних засобів і матеріалів.
Найменування речовини Температура Засоби гасіння.
1 2 3.
Масло 180−240 Піною, вуглекислотою, порошковими речовинами, піском.
5.4.2 Первинні засоби пожежегасіння Таблиця 5.7.
Первинні засоби пожежегасіння.
Будівельні приміщення, установки Категорія по СНіП Захищена площа, м2 Первинні засоби пожежегасіння.
Вуглики-слотний вогнегасник Пінний хімічний Ящик з піском Проти по-жежний щит.
1 2 3 4 5 6 7.
Цех 1 В.
5.5 Охорона довкілля.
Характеристика і аналіз можливих джерел забруднення навколишнього середовища.
В проектовані й дільниці потенціальними джерелами забруднення навколишнього середовища будуть: пари масел, МОР, залишки безпеки, погано очищена побутова і промислова вода.
5.5.1Характеристика викидів в атмосферу.
Таблиця 5.8. .
Характеристика викидів в атмосферу.
Виробни-цтво Назва стаціонарних джерел виділення шкідливих речовин Назва викидів шкідливих речовин ПОК м2/м3 Характеристика джерел викиду Об'єм газопові-тряної суміші на виході джерела % вміст шкідли-вих речовин в викидах.
Висота, м Діаме-тр, м.
1 2 3 4 5 6 7 8.
Деревообробне Котельні Сажа, дим 5 1,5 1 0,1 20.
Промислові води Хімічні і механічні домішки Хім. і мех. домішки 10.
до 3.
В повному виробництві передбачені екологічно чисті технологічні процеси і обладнання, ефективні установки очистки газу. Всі джерела викидів цехів обладнані мокрими тепловловлювачами типу ПВМ.
Розробляється питання очистки зимових газів котелень.
Конструктивна частина.
Заточні малогабаритні головки застосовуються для періодичного переточування ріжучого інструменту. Прцес переточування ріжучого інструменту малогабаритними заточними головками проводять без знімання інструменту з робочого місця, тобто безпосередньо при закріпленні їх в різцетримачі, або в спеціальних приспосібленнях верстату, що дозволяє виключити переналаштуванняінструменту на задані операції механічної обробки. При цьому використовують алмазні і кубонітові круги (50−70 мм., форми ЧК, Т і ПП з звичайною або спеціальною формою робочої поверхні.
Для конструкцію заточної головки з електричним приводом використовують машина свердлильну моделі ИЭ1008, в тому числі електродвигун 3, виключатель 1 і шнур з штепсельним з"єднанням для підключення заточної головки до електромережі. Ручка 4, жорско прикріплена до корпусу 2, забезпечує зручність використання заточної головки при заточуванні різних видів інструментів.
Література.
[1] Кучеров, Палипов, «Станки и инструменты лесопильно-дереообрабатывающего производства». Лесная промышленность", м. 1970 г — 560 ст.
[2] Дипломное проектирование (для студентов-заочников). Щелкова, 1990 г.
[3] Зотов, Швырев «Подготовка и эксплуатация дереворежущего инструмента». Лесная промышленность", М, 1986 г — 301 ст.
[4] Минин, Стрежнев «Курсовое и дипломатическое проектирование по производству мебели», Лесная промышленность, М, 1979 г -112 ст.