Шкідливі вікіді прокатного виробництва
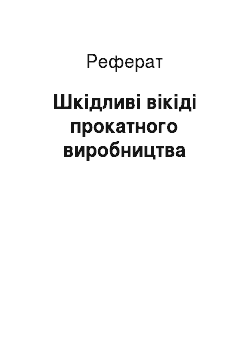
Выбросы цехів гарячої прокатки Основним джерелом організованих шкідливих викидів в цехах гарячої прокатки є нагрівальні печі криниці. Нагрівальні устрою опалюються природним, коксовым, доменним газами та його сумішшю. Деякі печі трубопрокатних цехів опалюються рідким паливом — мазутом. Кількість продуктів згоряння в нагрівальних печах і криницях залежить від теплової роботи цих агрегатів і… Читати ще >
Шкідливі вікіді прокатного виробництва (реферат, курсова, диплом, контрольна)
Выбросы у чорній металлургии.
Чимало підприємств металургійної промисловості, у Донецькому регіоні побудовано ще роки індустріалізації не враховуючи екологічних вимог. Ця обставина разом із быстрорастущим автотранспортом зумовлюють значні складнощі у виконанні завдання захисту атмосферного повітря на Донецькому регіоні. Боротьба пылегазовыми викидами у чорній металургії потребує великих капітальних і експлуатаційних витрат і ускладнюється тим, що викиди утворюються усім стадіях металургійного перерозподілу й найчастіше носять неорганізований характер. Найбільшим джерелом забруднення навколишнього середовища у чорній металургії є агломераційне виробництво. Аглофабрики викидають у повітря близько 50% усієї кількості оксиду вуглецю (ЗІ) і сірчистого ангідриду (502), понад двадцять % оксидів азоту (N0*) і пилу. Зазвичай аглофабрнки викидають 1—6 млн м3/ч аглогазов, містять 17% кисню, і навіть шкідливі речовини: СО—12,5, О2 — ОД МО*—-0,2, пил — 0,25 г/м3 (середні дані про аглофабрике заводу «Азовсталь»). Порівняно невеличка аглофабрнка заводу «Азовсталь», наприклад, має у собі 2 машини з майданом спечення 62,5 м³ кожна, загальної продуктивністю 1,62 млн т агломерату на рік. Річний обсяг викидів становить 6,46−109 мэ/год, зокрема шкідливі речовини: пил— 1600, оксид вуглецю — 80 800, діоксид серы—-5200, оксиди азоту — 1300 т/рік. Для істотне зменшення викидів цієї аглофабрики Інститутом газу АН УРСР і Маріупольським філією Укргіпромезу розроблено нестандартне рішення, що полягає в знешкодженні аглогазов в казанах ТЕЦ. Аглогазы з температурою 80 °З, запиленістю до 250 мг/м3 і змістом кисню 16—18% з двох трубопроводах довжиною 600 м, діаметром 3,0 м, прокладеними по естакаді, прибувають вентиляторам, потім у воздухонагреватели і горелочные устрою котлів ТЕЦ. У цьому оксид вуглецю аглогазов згоряє до діоксиду, а внаслідок бал актування зони горіння інертними компонентами аглогазов зменшується освіту оксидів азоту в топці казана. Викладене має експериментальне підтвердження. При спільну роботу аглофабрики і ТЕЦ зменшується загальний р викид оксиду вуглецю у повітря на 77, оксидів азоту — на 35, пилу— на 20%. Удільні витрати палива на ТЕЦ знижуються на 3 — 5% з допомогою використання фізичного тепла аглогазов і дожигания ЗІ. Кошторисна вартість будівництва цією системою оцінювався у цінах 1990 р. більш 6,0 млн. крб., термін окупності — 0,7 року, економічний ефект від участі запобігання шкоди в народному господарстві — 6,9 млн руб./год. Робота неодноразово включалася в республіканську науково-технічну програму РН.85.02 «Охорона повітряного басейну», проте виконувалася. Реалізація цієї розробки при порівняно невеликих капітальних витратах міг би швидко істотно оздоровити обстановку в повітряному басейні р. Маріуполя. Це ж рішення застосовно й у Коммунарска, де аглофабрика і ТЕЦ є ще ближче — з відривом 150 м, т. е. капітальні витрати буде ще менше Для інших аглофабрик регіону треба використовувати відомі рішення, реалізовані і частково у СРСР і рекомендовані комісією по чорної металургії країн — членів РЕВ. Це — рециркуляция аглогазов, що дозволяє на 30% знизити викиди ЗІ і N0* у повітря, известкововапнякова відмивання 5О2, і навіть технологічні заходи: застосування «ліжку» заввишки 20—40 мм, що знижує образрвание пилу вп’ятеро, збільшення висоти шару, двухслойное збирання шихти. Під час упорядкування загального плану розвитку та реконструкції чорної металургії регіону слід подивитися на питання про можливість збільшення частки котунів на шихті доменних печей, т. е. часткової заміні агломашин екологічно більш «чистими» обжиговыми машинами. Відомо, що деякі країнах, наприклад, США, частка котунів на шихті становить 70—75%, тоді як і СРСР вона, житлом становить 30—35%. Таке рішення щодо суті означала б ліквідацію зазначеного джерела викидів. Іншим значним джерелом забруднень залишається доменне виробництво, яке викидає 30% всієї пилу, ЗІ —25, SО2—15, N0,—10, СmНn—11% (інше кількість вуглеводнів викидає коксохімічне виробництво). Рудний двір, бункерная естакада, під бункерні приміщення неорганізовано викидають пилюку у кількості ~70 г/т чавуну. Для нейтралізації її необхідні регулярне зволоження штабелів, поливання їх вапняковим розчином, установка місцевих отсосов і электрофильтров. Особливо бажано застосовувати укриття випускних жолобів і подачу викидів через электрофильтры, бо в час випусків виділяється дуже багато пилу -— 430 г/т чавуну, 65% якої осідає в цеху, решта кількість через вентиляційні отвори викидається завезеними на територію заводу я далі. Необхідно забезпечити запобігання пылегазовых викидів з межконусного простору доменних печей і герметизацію основного металургійного устаткування. Потужним джерелом викидів оксиду азоту є мартенівські печі. Вони викидають понад 1200 т МО*/млн т стали. Технологічних способів запобігання освіти N0* в печах немає. Донецьким філією НВО «Энергосталь» розроблений аммначно-каталити-ческий спосіб відновлення оксидів азоту в що йдуть газах, який впроваджується на деяких металургійних заводах. Вартість встановлення* невідь що велика, проте вона локальну завдання. У регіоні потрібно зосередити кошти й можливості на впровадженні методу аммиачно-каталитической очищення газових викидів на агломашн-нах і ТЕЦ, як це робиться там, в частковості, в Японія. У металургійній промисловості країни, а регіоні особливо, слід прискорити виведення з експлуатації мартенівських печей. Окремо необхідно зупинитися на двухванных мартенівських печах Коммунарского металургійного заводу і заводу «Запоріжсталь». Це найбільші джерела забруднення цехів та міст пилом, оксидами вуглецю і азоту. Кількість відведених газів звичайних мартенівських печей ємністю 200—900 т становить відповідно 40— 95 тис. м3/ч із вмістом пилу 5—б г/м3. Двухванная піч 2×300 т викидає газів від 150 до 220 тис. м3/ч, т. е. в 1,5—2,2 рази більше найбільшої мартенівської печі, а зміст пилу в газах під час продувки сягає 20—25 г/м3, т. е. в 3—4 разу вищу. Отже, двухванные печі є у 6—8 раз більш потужними по порівнянню зі звичайними мартеновскими печами джерелами пилу. Суха пылеочистка вимагає герметизації тракту і сповненого дожигания ЗІ, зміст що його що йдуть газах може становити 20%, що небезпечно. Мокра очищення за схемою котел-утилизатор — труба Вентурн — каплеуловн-тель вимагає значних капітальних вкладень, енерговитрат зв споруди шламового господарства, порівнянного з таким інших печей цеху. Для двухванных печей немає прийнятних технічних рішень щодо зменшенню викидів, і повинно бути виведені нз експлуатацію у першу чергу. Як у мартенівських печах, і у конверторах необхідно застосовувати двох’ярусні кисневі фурмы, що дозволяє як дожечь частина оксиду вуглецю й одержати додаткове тепло, а й одночасно знизити винесення пилу і віднесення заліза на 35—40%. І тому непотрібен додаткових капітальних вкладень і экспуатационных витрат. Зниження викидів пилу в конверторах досягається, за даними Дніпропетровського металургійного інституту, збільшенням частки брухту. Це технологічне захід слід ширше застосовувати на заводах регіону. Інститут газу АН УРСР розробляє устрою для підігріву брухту в совках до 500—600 °З. Зменшення викидів в прокатному виробництві, хоча вона вважається щодо благополучним з екологічної погляду, пов’язується в першу чергу зі зниженням витрати палива на нагрівання металу. Кардинальним рішенням є перехід на безперервну разливку сталі та ліквідацію нагрівальних криниць і методичних печей. Реалізація цього шляху вимагає часу й істотних витрат. Є й тимчасове рішення, що полягає використання розробленого Інститутом газу методу непрямого радіаційного нагріву (КРН) металу з допомогою плоскопламенных горілок. Застосування КРН знижує на 10—15% витрати на нагрівання, на 30— 50% чад металу, під час спалювання газу пласкокаменных пальниках кількість які виникають оксидів азоту менше на 25—30%, аніж за використанні тунельних і факельных горілок. Метод КРН зараз є основним в прокатному виробництві там, з розробок Інституту газу АН УРСР він широко впроваджений що на деяких заводах у СРСР («Електросталь», Іжевський, Череповецький металургійні заводи та інших.) за кордоном — в Алжирі, Угорщини. У 1986 р, на Донецькому металургійному заводі метод КРН застосували в одній осередку нагрівальних криниць, що було реальний економічний ефект 70 тис. крб. зв поліпшило якість нагріву. До нашого часу пальники здійснюються лише на Дослідному підприємстві Інституту газу АН УРСР. Необхідна організація їх виробництва, у системі машинобудівних заводів, обслуговуючих металургію. Необхідно розробити працювати програми реконструкції пічного господарства прокатних цехів регіону. Досить широке застосування в допоміжних цехах металургії зв в машинобудівному виробництві отримав метод електрошлакового перевала (ЭШП).Для очищення викидів ЭШП від фтористих сполук застосовується мокрий метод, зокрема заводі «Азовсталь» Інститутом газу АН УРСР розроблений значно більше ефективний сухий метод зв створена установка очищення викидів ЭШП в киплячому шарі, організовано дрібносерійне виробництво установок одному з госпрозрахункових підприємств АН УРСР. Метод забезпечує ступінь очищення по фтору 99, по пылн — 90% при обсязі газів * 600 м3/ч. У коксохімічному виробництві найбільше пылн зв шкідливих газів утворюється під час завантаженні і розвантаження печей, транспортуванні вугілля й коксу, при гасінні коксу фенольнымн водами, в суш ильных відділеннях вуглезбагачувальних фабрик, відділеннях конденсації і уловлювання продуктів коксування. У виробництві коксу слід ширше застосовувати технологію бездимною завантаження, зволоження шихти до 8— 10%, отсос газів, утворювані за мінімального завантаження, в газосборники коксовій зв машинної сторін батареї, инжекцней їх пором чи коксовым газом, і навіть беспылевую видачу з отсосом, очищенням і дожиганием газів. Великий ефект дає що застосовується повсюдно там зв на деяких заводах СРСР сухе гасіння коксу рециркулирующими в замкнутої системі інертними газами (СО2 до 10, ЗІ —8—14, Н2— 1— 2, О2 — 1%, інше — азот). Утилизируемое тепло цих газів використовується для пара, зокрема для пароинжекции при бездимною завантаженні, в такий спосіб частково реалізується замкнута безвідходна технологія виробництва коксу. Значні кількості забруднюючих атмосферу компонентів викидають ТЕЦ металургійних заводів. Їх у середньому атмосферу надходить 17—20% усієї кількості пилу й діоксиду сірки, 25—39% оксиду азоту. Оксиди азоту викидаються як NO, який за взаємодії з озоном повітря перетворюється на сім разів більш токсичний NO2. Вочевидь, що ТЕЦ як великі забруднювачі атмосфери насамперед мають оснащатися досконалим пылеулавливающим устаткуванням. Існують способи часткового (на 40— 60%) придушення освіти NO в топках котлів. Ці засоби знижують максимальну температуру у зоні горіння. Вони полягають у застосуванні рециркуляції до зони горіння димових газів чи двухступенчатого розтягнутого спалювання палива й не потребують значних капітальних видатків. По розробкам Інституту газу АН УРСР методи впроваджені я освоюють багатьох котлоагрегатах систем Міненерго СРСР й УРСР, зокрема в системах Київенерго, Мосенерго та інших. УкрГИПРОмез при консультації Інституту газу АН УРСР виконав кілька проектів переобладнання парових котлів ТЕЦ металургійних заводів на режими двухстадийного спалювання палива, що дозволить на 30—60% знизити викид оксидів азоту у повітря. Аналогічні рішення можна буде застосувати й у заводів Донецького регіону. Необхідно зупинитися двома загальних питаннях. У сімдесятих роках розглядалася можливість корінний реконструкції Донецького металургійного заводи на екологічно значно більше чисте металургійне виробництво, заснований на процесі прямого отримання заліза, минаючи доменний процес. Передбачалося використовувати багаті залізні руди Куксунгурского родовища Донецькій області. Були виконані техніко-економічні і технологічні розробки й представлені в Уряд знаходяться відповідні пропозиції. Очевидно, є необхідність розглянути це запитання наново, враховуючи що з’явився при цьому час, досвід Оскольського електрометалургійного комбінату, і навіть територіальну можливість будівництва шахтних печей прямого отримання заліза. Маріупольським філією УкрГИПРОмеза, Інститутом газу АН УРСР та ін. ще 1976 р. розроблено заходи щодо ліквідації підвищеного забруднення атмосферного повітря р. Маріуполя шкідливими речовинами зв захисту біологічного життя Азовського моря шкідливих стоків. Було визначено обсяг та терміни необхідних ДКР і розробки головних зразків газоочистного устаткування, хімічної водоочищення, автоматичних газоаналізаторів і контролю. Капітальні вкладення виконання заходів щодо захисту атмосферного повітря тоді оцінювалися приблизно 320 млн крб. при терміні окупності в розмірі 5 років. Тоді ж були поставлені питання перед Госкомгидрометом СРСР включення Маріупольського промислового району в місць впровадження перших вітчизняних систем моніторингу. Звісно ж необхідним повернутися до розгляду цих питань знову, тим паче, які можна багато використовувати раніше виконану работы.
Вредные викиди прокатних цехів в атмосферу.
У прокатному виробництві, як та інших виробництвах, є організовані технологічні і неорганізовані викиди. Основний джерело технологічних викидів — нагрівальні криниці, печі і машини вогневої зачистки. Джерела неорганізованих викидів: нагрівальні криниці під час відкривання кришок, нагрівальні печі при недостатньою тязі, робочі клети, ножиці для різання металу, вогнева і механічна зачистки заготовок, видалення шлаку в шлакових коридорах у нагрівальних пристроїв і др.
Выбросы цехів гарячої прокатки Основним джерелом організованих шкідливих викидів в цехах гарячої прокатки є нагрівальні печі криниці. Нагрівальні устрою опалюються природним, коксовым, доменним газами та його сумішшю. Деякі печі трубопрокатних цехів опалюються рідким паливом — мазутом. Кількість продуктів згоряння в нагрівальних печах і криницях залежить від теплової роботи цих агрегатів і як 700−1000 м3/т нагреваемого металу. При спалюванні газу в нагрівальних пристроях повітря мало забруднюється. При спалюванні серосодержащего палива (мазуту, коксового і коксодоменного газів) у повітря надходить сірчистий ангідрид, кількість якого залежить від змісту сірки палива та її расхода.
Неорганізовані викиди цехів гарячої прокатки Вредные неорганізовані викиди в відділеннях нагрівальних криниць виділяються з осередків (під час відкривання кришок криниць) і шлакових коридорів (під час видалення шлаку). З натурних вимірів, виконаних цехах блюминга і слябинга працівниками Московського інституту «Сантехпроект », було встановлено, що з недостатньою тязі в які прориваються відведених газах нагрівальних криниць міститься окис вуглецю у кількості до 150 г/т прокату. Удільні викиди пилу в прокатних цехах блюминга і слябинга становлять 50 г/т, через витяжні ліхтарі викидається 15% цієї кількості, тобто. приблизно 11 г/т прокату, у своїй частку відділення нагрівальних криниць доводиться 7 г/т, але в відділення стану 4, г/т. У шлакових коридорах нагрівальних криниць рекуперативного типу загазованість незначна, запиленість також невелика — загалом 2−8 мг/м3. Проте за спуску шлаку запиленість біля ковшів підвищується до 15- 20 мг/м. Неорганізовані викиди листопрокатных і крупносортных цехів містять окис вуглецю і пыль.
Технологічні викиди в відділеннях вогневої зачистки металла Общее удільне кількість окису вуглецю, выделяющейся з пічного відділення за недосконалої конструкції горелочных пристроїв і недостатньою тязі (вибивання газів з робочого простору), становить до 200 г/т прокату. Питома кількість пилу, выделяющейся через ліхтарі, становить середньому до 16 г/т прокату і по 0,27 г/м2 прокатываемого аркуша. Загальне удільне кількість пилу, яке вирізняється при прокатці металу, становить 100 г/т, чи 1,8 г/м2 .
Для видалення поверхневих дефектів з прокатних заготовок застосовують вогневу зачистку на спеціальних машинах вогневої зачистки (MOЗ). Питома обсяг газів, отсасываемых від МОЗ слябинга, становить 35 м3/м2 поверхні сляба, як від блюминга 45 м3/м2 поверхні блюма (при глибині зачищаемого шару 2−3 мм). Ці обсяги відповідають 5−6-кратному розведення повітрям, подсасываемым через газозаборное пристрій, і може бути зменшено внаслідок поліпшення конструкції витяжного парасолі. Удільні величини шкідливі речовини, що викидаються з продуктами згоряння від МОЗ, віднесені до 1 м² зачищаемой поверхні заготівлі при глибині зачистки 1 мм, при обсязі отсасываемых газів 13 м³ (м3*мм) і витратах кисню під час зачистки 3,3 м3/(м2- мм) становлять, р: пилу 40; ЗІ 0,8; S02 0,4; NO 0,5. Процес травлення залежить від видаленні окалини із поверхні металу шляхом обробки її розчинами. При травленні, крім окислів, розчиняються і метали. У цьому утворюється водень, який, віддаляючись з ванної як пухирців, захоплює з собою певна кількість травильного розчину, що визначає склад шкідливих викидів. Неорганізовані викиди в цехах гарячої прокатки виділяються при відкриванні нагрівальних криниць (незгорілі продукти згоряння), через неплотности (забиваються гази з печі), при прокатці металу (утворюється пил). Неорганізовані викиди окису вуглецю як нагрівальних криниць сягають 150 г/т прокату, і з выбивающимися газами нагрівальних печей (при недостатньою тязі) до 200 г/т.
На підприємствах проблему обеспыливания намагалися вирішити, застосовуючи гидрообеспыливание, здійснюване за допомогою форсунок з тонким розпиленням води, механічним і пневматичним, рівномірним зрошенням місць пылевыделения через дырчатые труби тощо. п. Але такі способи не дали позитивних результатов.
Загрязнение води в прокатному производстве Наилучшие результати досягаються при смыве пилу компактній струменем води в місці її створення. Вода подається на прокатываемый метал у місці виходу його з валків і відводиться зі спеціального жолобу. При прокаті аркуша завтовшки 2 мм ступінь обеспыливания 98—99%. У цьому додаткового, небажаного охолодження аркуша мало відбувається. При гидросмыве орієнтовний витрата води дорівнює, м3/ч: на блюмінгу 40, слябинге 30, однією житло листового стану 6—10, безперервного сортопрокатного стану і один прохід на раскатном стані. Підвищення продуктивність праці в машинобудівної промисловості призвело до для пошуку досконаліших СОЖ. У зв’язку з цим виникла гостра потреба у створенні методичних підходів до прискореної оцінці токсичності і надзвичайну небезпеку СОЖ на стадії розробки. Лабораторією токсикології Інституту гігієни праці та профзахворювань АМН СРСР було розроблено й апробована схема первинної оцінки токсичності й правничого характеру шкідливого впливу СОЖ, куди входять вивчення токсичності речовини при одноразовому запровадження, дослідження місцевого, кожно-резорбтивного і сенсибилизирующих ефектів [1]. З метою токсикологічної характеристики нових зразків СОЖ дослідження проведено відповідність до розробленими методичними вказівками й рекомендаціями, але тривалості експерименту, правилам запровадження СОЖ, кількості обстежуваних тварин за групі [1, 2]. Дослідження проведено на чотирьох видах тварин (пацюки, миші, морські свинки, кролики). Усі досліджені нові СОЖ ставляться до IV класу малонебезпечних сполук, їх сенсибилизирующие і кожно-резорбтивные властивості не виявлено. Аналіз результатів експерименту свідчить, що, зазвичай, СОЖ малотоксичны під час введення в шлунок і внутрибрюшинно; вони допущені до виробничим испытаниям.
Проведенная токсикологічна експертиза СОЖ показала, що дія на шкіру є головним показником, щодо якої слід виробляти відбір хімічних речовин у цій природі для виробничих випробувань за умови їхньої низької токсичности.
Для обгрунтування ГДК СОЖ потрібно значно більше часу й економічних витрат. Справжня експертиза дозволяє скоротити терміни своєчасного відбору речовин, котрим необхідна розробка ГДК. Проте застосування СОЖ у низці виробництв супроводжується високими температурними режимами, що небезпека може провадити до деструкції мастил й освіті багатокомпонентних газо-паро-аэро-зольных сумішей. Воно потребує спеціального вивчення у плані гігієнічної оцінки застосування СОЖ. Проведені дослідження свідчить про низькою токсичності вивчених СОЖ, відмінності у тому хімічному составе.