Суперфінішування
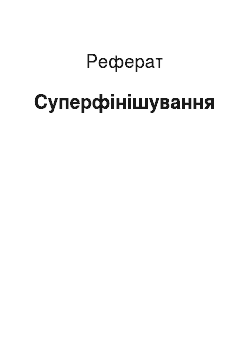
Суперфинишированию піддаються поверхні деталей, встановлених як і центрах (рис. 1.7, а), і на опорних валках, т. е. бесцентровым методом (рис. 1.7,6). Можна суперфинишировать положисті конічні поверхні, навіщо при центровою обробці голівка з бруском розгортається на необхідний кут, а при бесцентровой — використовуються спеціальні профільні опорні валки. Для суперфиниширования внутрішніх поверхонь… Читати ще >
Суперфінішування (реферат, курсова, диплом, контрольна)
Міністерство спільного освітнього і професійної освіти Російської Федерации.
Волгоградський державний технічний университет.
Кафедра «» Технології матеріалів ««.
Реферат.
Тема: «» Суперфиширование «» .
Выполнил:
Студент грн. М-434.
Просін Д.А.
Проверил:
Петрова В.Ф.
Волгоград 2000.
ОСНОВНІ ЗАКОНОМІРНОСТІ ПРОЦЕСУ СУПЕРФИНИШИРОВАНИЯ.
Загальні ознаки і Особливості процесу суперфиниширования.
Нині в серійному та масовому виробництві під час виготовлення відповідальних деталей пред’являються високі вимоги до точності й діють шорсткості поверхні: некруглость менш 1 мкм, хвилястість менш 0,2 мкм, нецилиндричность і непрямолинейность котра утворює менш 2—5 мкм, параметр шероховатости.
Ra= 0,02— 0,8 мкм, відсутність дефектного шару металу (структурнофазових змін, напруг розтяги, мікротріщин), певні значення параметрів форми микронеровностей і опорною поверхности.
Забезпечення цих вимог досягається з допомогою таких процесів абразивною обробки, як хо-нингование і суперфиниширование брусками з традиційних і надтвердих абразивних матеріалів. Ці процеси належать до процесам доводки; хонингование виробляється при одночасно виконуваних обертальному і возвратнопоступальному рухах інструмента (голівки з брусками), суперфиниширование— під час обертання заготівлі та коливальному русі бруски. Суперфинишная голівка з бруском чи заготівля може виконувати також рух подачі вздовж осі заготівлі. На рис.
1.1 приведенa схемa робочих рухів. При суперфинишировании притиск бруски здійснюється з допомогою гідравлічних чи пневматичних систем.
При контакті робочої поверхні бруски з оброблюваної поверхнею заготівлі відбувається царапание металу одночасно великою кількістю абразивних частинок. Розмір таких частинок при суперфинишировании—5—20 мкм, середня кількість частинок лежить на поверхні бруски 0.004−0.005 зерен на 1 мм². Основними видами взаємодії абразивних зерен з металом є микрорезание зі зняттям найтонших стружок і тертя з пластичним відтискуванням металу. Для інтенсивного різання необхідно, щоб абразивний брусок самозатачивался шляхом скалывания і виривання затупившихся зерен з зв’язки. З використанням брусків з надтвердих абразивних матеріалів (алмазу, эльбора) зерна тривалий час со;
[pic].
/ — деталь; 2 — брусок (V.— окружна швидкість деталі. P. S —осьова подача, Оос — швидкість осьової подачі, n— частота коливанні бруски, а — розмах коливань, ас — кут сетки).
храняют свою гостроту, переважає микроскалывание зерен, а не виривання их, что значно підвищує стійкість брусков.
Шляхом вибору оптимальних характеристик брусків та митного регулювання параметрів обробки (швидкості, тиску) можна управляти процесом обробки, здійснюючи на першої стадії триваюче різання металу у протягом досить багато часу, який буде необхідний виправлення похибок форми заготівлі, видалення вихідної шерехатості й дефектного шару. Швидкість знімання металу у своїй становить 2—4 мкм/с. Для отримання поверхні з малої шорсткістю (0,04—0,08 мкм), і навіть до створення сприятливого мікрорельєфу поверхні деталей і упрочненного поверхневого шару металу процес обробки завершальній стадії то, можливо переведений у режим переважаючого межового тертя, у якому з'їм металу різко скорочується, а брусок вигладжує оброблювану поверхню. Такий перехід можна здійснити, змінюючи параметри обробки: підвищуючи окружну швидкість заготівлі чи інструмента, знижуючи тиск бруски і частоту коливань бруска.
Раніше застосовували процес обробки брусками з самопрекращением різання і знімання металу був некерованим не міг забезпечувати стабільного якості деталей, оскільки самопрекращение знімання металу часто відбувається набагато раніше, ніж видаляється додача, необхідний виправлення похибок форми і усунення дефектного слоя.
На відміну від шлифования, у якому контактна поверхню становить незначну частину робочої поверхні кола, при суперфинишировании брусок постійно зтикається з деталлю у всій робочої поверхні, причому у початковий час брусок прирабатывается до оброблюваної поверхні. Такий контакт пари брусок — заготівля сприяє підвищенню продуктивності обробітку грунту і точності форми деталей. Тиск при суперфинишировании лежить на поверхні контакту бруски з деталлю становить 0,1—1 МПа, що у 10—100 разів менша, ніж тиск при шліфуванні. Швидкість різання при обробці брусками 10—100 м/мин, т. е. в 15—100 разів менше, аніж за шліфуванні. Через війну при суперфинишировании тепловиділення у зоні обробки значно нижчі від, аніж за шліфуванні, а контактна температура не превышает.
60—100 °З. Отже, відсутні фізичні причини освіти у поверхневому шарі мікротріщин і прижогов, і навіть залишкових напруг растяжения.
. При суперфинишировании з пружним (через пружину) поджимом бруски жорсткість системи мала, а сила різання практично постійна, незалежно від форми заготівлі, унаслідок чого відбувається незначне виправлення похибок форми. Нині розробити й подати широко застосовуються конструкції суперфинишных головок з жорсткішою гідравлічної системою притискання бруски, що значно підвищують продуктивність і точність обработки.
Характерним ознакою процесу суперфиниширования є підвищена частота (20—50 гц) коливань абразивного бруска.
Коливальне рух інтенсифікує процеси та різання металу, і самозатачивания бруски, створює більш однорідний микрорельеф з не меншою шорсткістю обробленою поверхні. Нині розроблено й використовуються верстати і голівки для зовнішнього суперфиниширования внутрішніх поверхонь (наприклад, доріжок качения зовнішніх кілець підшипник вв).
Області застосування операції суперфиниширования.
Суперфиниширование застосовують у ролі фінішної операції, переважно при обробці зовнішніх поверхонь деталей, експлуатованих за умов тертя ковзання чи качения; часом суперфинишированием обробляють також внутрішні і торцовые поверхні, наприклад доріжки качения зовнішніх кілець радіальних і наполегливих підшипників качения. Зазвичай, суперфиниширование виробляють після операцій шлифования, а нетермообрабо-танных деталей — після операцій тонкого точения.
Суперфинишированию піддаються поверхні деталей, встановлених як і центрах (рис. 1.7, а), і на опорних валках, т. е. бесцентровым методом (рис. 1.7,6). Можна суперфинишировать положисті конічні поверхні, навіщо при центровою обробці голівка з бруском розгортається на необхідний кут, а при бесцентровой — використовуються спеціальні профільні опорні валки. Для суперфиниширования внутрішніх поверхонь (отворів) невеличкий довжини (рис. 1.7, б) деталь встановлюють в патроні, а брусок закріплюють у спеціальній державке, яку вводять у обрабатываемое отвір. При суперфинишировании внутрішніх сферичних поверхонь (рис. 1.7,г), переважно жолобів кілець шарикоподшипников, деталь обертається, а брусок робить коливальне рух щодо центру хитань, обраного те щоб радіус хитань збігався з радіусом желоба.
Суперфиниширование пласких торцевих поверхонь (рис. .7,д) виконується з допомогою обертового •шлифовального кола, дерево якого не може здійснювати також коливальне рух. Вісь обертання кола, зазвичай, зміщена але відношення до оси.
[pic].
Рис. 1.7. Схеми суперфиниширования деталей різної конфігурації: а—цилиндрических і конічних (в центрах), б—цилиндрических і положистих конічних (на опорних валках); в—отверстии; р— внутрішніх сферичних поверхонь; буд — пласких торцевих поверхонь, е — випуклих торцевих поверхонь деталі. Після обробітку опуклих торцевих поверхонь (рис. 1.7, е) вісь кола нахиляється стосовно осі деталі під деяким углом.
Широке поширення суперфиниширование отримала виробництві підшипників для доводки доріжок качения кілець і роликів. У автомобільної і тракторної промисловості суперфинишированием обробляють шийки колінчастих і розподільних валів, поршневі пальці, вали коробок передач, штоки амортизаторів. У станкостроении суперфиниши-руют шпиндели і пиноли, інших галузях машинобудування — гладкі і ступінчасті вали, осі, ротори, калібри та інші детали.
Вибір брусків для суперфиниширования.
Однією з умов найефективнішого здійснення операції суперфиниширования є правильний вибір розмірів брусков.
Робочу ширину бруски У (рис. 4.1, а) вибирають залежно від діаметра оброблюваної деталі D, т. е.
У= (0,4— 0,7) D,.
причому з увел.
Рис. 4.1. Форма й розміри брусків для суперфиниширования.
ичением діаметра деталі ставлення B/D зменшується. З використанням надмірно широких брусків не можуть доступ мастильно-охолодної рідини до зони обробітку грунту і видалення відходів, що зумовлює погіршення якості поверхні деталі. З іншого боку, за дуже великої дузі контакту бруски з деталлю спостерігається обламування крайок бруски, особливо на початку обробки, коли зусилля різання різко змінюються під впливом похибок геометричній форми детали.
Таблиця 4.7.
Вибір ширини і кількості брусків для суперфиниширования.
Для обробки деталей великих діаметрів треба використовувати два бруски (рис. 4.1, б) і більше, використовуючи при цьому спеціальні державки. У табл. 4.7 наведено дані про вибору оптимальних ширини і кількості брусків при суперфинишировании залежно від діаметра деталі. Після обробітку деталей зі шпоночными канавками, пазами, вікнами ширина бруски мусить бути щонайменше полуторной ширини канавки чи паза (рис. 4.1, в), а при обробці разверток (рис. 4.1, р) під бруском має одночасно перебувати щонайменше трьох зубьев.
Довжина бруски L становить 1,5—3 його ширини У. При більшої довжині може бути перекіс бруски стосовно осі деталі, що зумовлює його нерівномірному зношування й погіршенню якості поверхні деталі. Після обробітку коротких відкритих ділянок деталей без подовжньої подачі довжина бруски мусить бути рівної довжині оброблюваної поверхні, що сприяє отриманню правильної геометричній форми деталі (рис. 4.1,.