Машины для роздрібнення, сортування і мийки кам'яних материалов
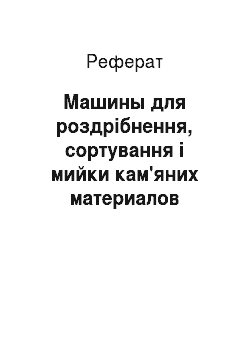
Встановлено ротор 2, відбійна плита 4, поворотна 5 і выдвижная колосниковая грати 6. Ротор складається з однієї чи кількох дисків, закріплених спільною для приводном валу. Дроблення матеріалу здійснюється під впливом удару у ній молотків 3 масою 15…20 кг, шарнірно закріплених до дискам обертового ротора, і співудару шматків з плитами і колосниковыми гратами. Становище колосниковых решіток і… Читати ще >
Машины для роздрібнення, сортування і мийки кам'яних материалов (реферат, курсова, диплом, контрольна)
МОСКОВСЬКИЙ КОЛЕДЖ ГРАДОСТРАИТЕЛЬСТВА і ПРЕДПРИНИМАТЕЛЬСТВА.
Реферат.
По дисциплине:
«Будівельні машины».
на тему:
МАШИНИ ДЛЯ РОЗДРІБНЕННЯ, СОРТУВАННЯ І МИЙКИ КАМ’ЯНИХ МАТЕРИАЛОВ Выполнил: студент 3 курса.
Групи С-3−99. спеціальність СЭЗС.
Рушихин А.И.
МОСКВА. 2001 г.
| | | |Запровадження |3 | | | | | | | |Машини для роздрібнення кам’яних матеріалів. |4 | | | | |1.1 Щековые дробарки. | | |1.2 Конусні дробарки. | | |1.3 Валковые дробарки. | | |1.4 Роторні і молотковые дробарки | | | | | | | | |Машини для сортування кам’яних матеріалів. |13 | |2.1 Нерухомі грохоты. | | |2.2 Барабанні грохоты. | | |2.3 Эксцентриковые грохоты. | | |2.4 Інерційні виброгрохоты. | | | | | | | | |Машини для мийки кам’яних матеріалів. |16 | | | | |3.1 Гидромеханический класифікатор. | | |3.2 Гідравлічний класифікатор. | | | | | | | | | Укладання. |17 | | | | | | | | Список літератури. |18 |.
Будівельні машини нині невід'ємний елемент у сфері побічно або безпосередньо до пов’язану зі будівництвом. Дозволяють поліпшити і проконтролювати якість будівництва. Прискорити терміни будівництва. Полегшити працю людини у як частково, і у цілому автоматизуючи процес виробництва, у деяких отраслях.
У цьому рефераті описується одне із класів будівельних машин «машини для роздрібнення, сортування і мийки кам’яних матеріалів». Наводяться деякі даних про роботі і конструктивних особливостях. Як влаштовані, як працюють. Дані ох продуктивності і ресурсах.
Машини для роздрібнення кам’яних материалов.
У її зведенні щорічно споживається дуже багато кам’яних матеріалів: щебеню, гравію і піску. Більшість цих матеріалів використовується на приготування бетону. Видобуток піску і гравію виробляється у природних відкладеннях механічним чи гідравлічною способом, а щебеню природний каменю шляхом роздрібнення висаджених скельних порід. Видобувні кам’яні матеріали переробляються на камнедробильных і промывочно-сортировочных заводах, потім у вигляді готового продукту стандартного якості доставляються потребителю.
Якість щебеню характеризується зерновим складом, формою зерен, механічної міцністю і змістом шкідливих примесей.
Залежно від крупности зерен щебінь поділяють на фракції 5…10; 10…20; 20…40 і 40…70 мм. З іншого боку, для будівництва допускаються фракції 3…10; 10…15; 15…20 мм для балластного шару залізничної колії 25…50 мм. Для масивних бетонних споруд верхній межа крупности може становити 120…150 мм. За формою зерен їх класифікують на лещадные, які мають ширина втричі і більше менше довжини, і кубо-образные. Дійові Держстандарти не допускають вміст у щебені і гравії зерен лещадной форми понад п’ятнадцять %. Щебінь з гравію отримують дробленням гравію і валунів. Вимоги до щебеню, отриманої з гравію, в основному таку ж, як до щебеню, отриманої з висаджених кам’яних порід. Механічна міцність щебеню визначається міцністю гірських порід, з що їх отримано. Розрізняють породи малої міцності 30…80 МПа, середньої — 80… 150 і високої — більш 150 МПа.
Піски за рівнем крупности поділяють по модулю крупности та інших показниками на великі, середні і малі. У процесі переробки нерудних матеріалів для звільнення піску в окремих випадках щебеню від глинистих та інших шкідливих частинок застосовують промивання та зневоднення. Зневоднення виробляють зниження вологості рівня, допускає його транспортування, та профілактики смерзания в зимове время.
Дроблення кам’яних матеріалів здійснюється додатком статичних і динамічних навантажень. Матеріали подрібнюють раздавливанием, руйнацією ударом, истиранием, раскалыванием, і навіть руйнацією вибухом. Багато випадках роздрібнення відбувається за одночасній дії розчавлювання і истирания.
Ступенем роздрібнення називають ставлення розміру найбільших, загружаемых в дробарку каменів до розміру максимальних зерен в продукті роздрібнення: I = Dmax/dmax.
Дроблення поділяють на велике (Dmax = 1200…1500 мм, dmax =100…300 мм), середнє (Dmax = 100…300 мм, dmax = 30… 100 мм), дрібне (Dmax = 30…100 mm, dmax = = 5…30 мм) і тонке (помел). Дроблення порід високої і середній міцності здійснюють раздавливанием, раскалыванием і ударом; помел — истиранием і ударом.
Залежно від рівня подрібнення матеріалів дробильні машини поділяють на дробарки і млини. Деякі машини можуть працюватиме, як дробарки як і млини (наприклад, валковые дробарки, бігуни). За принципом дії і конструктивним ознаками дробарки ділять на щековые, конусні, валковые, молотковые і роторні дробарки; млини — на барабанні, кульові, бегунковые і вібраційні. Різні типи дробарок дозволяють отримати певну, притаманну даної конструкції, ступінь роздрібнення: щековые — 2…8; валковые — 1,5…10; конусні — 3…8; молотковые — 5…30; млини — 10…20.
Вибір типу дробильного устаткування ведуть у залежність від максимальної крупности шматків вихідний матеріал, його міцності, необхідного ступеня роздрібнення і необхідної производительности.
Дроблення матеріалів ведуть у одну чи кілька стадій. Переважна поширення одержало стадийное роздрібнення, у якому матеріал подрібнюють в 2…3 прийому на дробилках різних типів. Уже кожної стадії роздрібнення отримують матеріал з необхідними розмірами шматків. Такі шматки відсіваються на гуркоті, встановленому перед дробарками різних стадій. Дробарки останніх стадій працюють, зазвичай, у замкненому циклі з виброгрохотом, у своїй матеріал крупніша заданого розміру повертається у таку ж дробарку для повторного роздрібнення (рис. 1). |[pic] | | | |Рис. 1. Типова схема | | |дробильно-сортировочной | | |установки: | | | | | |1 — вагонетка; | | |2 — плаский конвеєр; | | |3 — колосниковый гуркіт; | | |4 — щековая дробарка; | | |5 — виброгрохот; | | |6 — валковая дробарка; | | |7 — виброгрохот; | | |8 — бункер для піску і пилу; | | |9 — видатковий бункер; | | |10 — склади товарного щебеню |.
При одностадийном роздрібненні одержувані дрібні зерна заповнюють проміжки між великими і захищають їхнього капіталу від безпосереднього впливу дробящих органів машини, що супроводжується додатковим подрібненням матеріалу і витратою энергии.
Основними показниками роботи дробарок є: максимальна крупность роздрібнення, ступінь подрібнення, питома витрата енергії (кВт (ч/м3), продуктивність (м3/ч чи т/ч).
Щековые дробарки. Їх застосовують великого й середнього роздрібнення міцних і середній міцності порід на первинної і вторинної стадії роздрібнення. За характером руху рухомий щоки щековые дробарки поділяють на дробарки з простою й складним хитанням щеки.
Дробарка з простим хитанням щоки (рис. 2, а, б) полягає: |[pic] | | | | | | | | | |Рис. 2. Щековая | | |дробарка з простим| | |хитанням щоки: | | | | | |а — конструктивна| | |схема; | | |б — кінематична| | |схема; | | |в — схема | | |проходження | | |матеріалу через | | |розвантажувальну щілину;| | | | | |р — схема для | | |визначення | | |продуктивності| | |щековой дробарки | |[pic] [pic] |.
з зварного корпусу 1, у якому підшипниках встановлено эксцентриковый вал 7 з підвішеним щодо нього шатуном 8. Нижній кінець шатуна має спеціальні гнізда, у яких вільно вставлені кінці распорных плит 12 і 13. Протилежний кінець распорной плити 13 вставлено в гніздо рухомий щоки 3, підвішеною на осі 5. Кінець плити 12 впирається у клиновой упор регулировочного устрою 9. Потяг 11 і пружина 10 забезпечують зворотне рух рухомий щоки й утримують від випадання розпірні плити. До нерухомій 2 і рухомий щоках кріпляться дробящие плити 4 з вертикальним рифлением, які є основними робітниками органами щековых дробарок. Робітники поверхні дробящих плит і бічні стінки корпусу дробарки утворюють камеру роздрібнення. Дробящие плити встановлюють те щоб виступи однієї розташовувалися проти западин інший (рис. 2, в). Прихід дробарки складається з електродвигуна і многорядной клиноременной передачі з масивним шкивоммховиком 6.
Задля більшої пуску дробарок, і навіть пуску дробарок під завалом в останніх конструкціях дробарок застосований допоміжний привід (рис 3). |[pic] | | | | | | | | | |Рис. 3. Схема | | |допоміжний привід |.
Він з електродвигуна меншою потужності 4, зубчастого редуктора 3 з великим передаточным числом, обгонной муфти 2, з'єднаної з валом головного електродвигуна 1. Трогание з місця здійснюється допоміжним приводом. Після цього включається головний двигун, а допоміжний привід автоматично отключается.
Режим роботи дробарки змінюється регулюванням вихідний щілини з допомогою клинового чи іншого конструкції регулировочного устрою. Вихідну щілину вимірюють між вершиною і западиною дробящих плит в останній момент найбільшого видалення рухомий щоки. Ширина розвантажувальною щілини становить 40…120 мм для дробарок середнього роздрібнення і 100… 250 мм великого роздрібнення. При обертанні эксцентрикового валу рухлива щока проводиться в качательное, подібно маятникові, рух. За один оборот эксцентрикового валу рухлива щока, наближаючись до нерухомій, робить робочий хід (роздрібнення) і холостий хід, у якому продукт роздрібнення випадає через розвантажувальну щілину. Для щековых дробарок з простим хитанням щоки найхарактерніших виглядом руйнації матеріалу є розчавлювання, розколення і злам. Тому і застосовують великого й середнього роздрібнення високоміцних .порід на первинної стадії дробления.
Дробарка зі складною хитанням щоки (рис. 4) | |[pic] | |[pic] | | | | |Рис. 4. Кінематична схема щековой дробарки зі складною хитанням щоки: | |(а), її конструктивна схема (б) |.
за конструкцією простіше, ніж із простим хитанням, і має меншу масу. У ньому відсутня шатун, а рухлива щока 1 підвішена безпосередньо до эксцентриковому валу 2, у результаті точки рухомий щоки рухаються по эллиптическим траєкторіям з мінімальним різницею осей еліпса вгорі і максимальної внизу. Дроблення матеріалу відбувається внаслідок розчавлювання, розколювання, зламу і истирания матеріалу. Дробарки зі складним хитанням щоки застосовують для середнього та малого роздрібнення порід середньої фортеці. Складне рух рухомий щоки призводить до більш інтенсивному зносу дробящих плит і більше частої їх замене.
Недоліками щековых дробарок є циклічний характер їх і висока енергоємність процесу руйнації. Питома потужність [кВт/(м3/ч)] при мінімальної ширині розвантажувальною щілини сягає у дробарок з простим хитанням 1,2…4,6 і з складним хитанням щоки — 0,9…4,6.
Типорозмір щековой дробарки визначається розміром ширини У і довжини L завантажувального зіва дробарки. Величина У характеризує максимальну крупность шматків, загружаемых в дробарку (Dmax = 0,85 У), а величина L визначає основному її продуктивність. Вітчизняні щековые дробарки випускаються наступних типорозмірів: 400×600; 600×900; 900×1200; 1200×1500; 1500×2100; 2100×2500 мм, продуктивністю до 800 м3/ч.
Технічна продуктивність щековых дробарок (м3/ч) Пт = 60Vnrp, где V — обсяг матеріалу, выпадающий з зіва дробарки за оборот эксцентрикового валу, м3 (рис. 2, г);[pic]; n — число хитань рухомий щоки на хвилину; Rр = 0,3…0,7 — коефіцієнт, враховує розпушення дробимого материала.
Необхідно, щоб роздроблений матеріал за подвійний хід щоки встиг висипатися з розвантажувальною щілини, т. е. 60/(2n) =[pic], звідки число хитань щеки.
n = 665[pic]. Оскільки вільного падіння немає, то n = (600… 635)[pic], де l — хід рухомий щоки, м; (— кут захоплення, вона від коефіцієнта тертя матеріалу про щоки і як 19…23°; P. S = a + l — ширина розвантажувальною щілини, м (див. мал.2, р); a — розмір при сближенном становищі щік, м; l — довжина завантажувального зіва дробарки, м.
Конусні дробарки застосовують для роздрібнення порід з міцністю (сж до 300 МПа з високим рівнем абразивности. У цих дробилках матеріал раздавливается в камері роздрібнення робочим конусом, що чинять просторове хитання всередині нерухомого конуса (рис. 5, а, б). |[pic] |[pic] | | | | |[pic] | | | | | |Рис. 4. Конусная дробарка: | | |а) великого роздрібнення; | | |б) средного та дрібного роздрібнення; | | |в) профілі камер роздрібнення конусных, розмір | | |вихідний щілини |.
Кожного моменту одне з їхнім виокремленням дробящего конуса здається найбільш наближеним до поверхні нерухомого конуса, а протилежна їй утворює — найвіддаленішій. Отже, у будь-якій момент поверхні дробящих конусів, зближаючи, виробляють роздрібнення матеріалу, а зоні видалення цих поверхонь раніше роздроблений матеріал під впливом власної маси розвантажується через кільцеподібну випускну щель.
Процес роздрібнення в конусных дробилках, на відміну щековых, відбувається безупинно при послідовному переміщенні зони роздрібнення по окружності конусів, що сприяє більш рівномірним навантаженні механізму, і двигуна дробарки. Розмір найбільших шматків, які можна завантажені в дробарку, визначається радіальної шириною завантажувального отвори. Характеристика крупности роздрібнення і продуктивність дробарки залежить від радіальної ширини розвантажувального отверстия.
Розрізняють конусні дробарки великого, середнього та малого роздрібнення. Вони відмінними між собою способом встановлення і кутами конусности дробящих конусов.
У конусных дробилках великого роздрібнення (рис. 5, а) здрібнення матеріалу виробляється у кільцевому робочому просторі, утвореному двома конусами: нерухомим 2 і рухомим — дробящим 7. Перший закріплено до підставі дробарки 1. Дробящий конус щільно насаджений на вал 6, верхній кінець якого шарнірно з допомогою підвісного підшипника 4 кріпиться до траверсі 5, а нижній — вільно входить у стакан-эксцентрик 11. Останній може обертатися в вертикальному подшипнике 12 станини дробарки. Обертання склянціексцентрику передається від електродвигуна через горизонтальний вал 9 і конічну передачу-10. Дробящие конуси бронированы плитами 3 і побачили 8-го з износостойкой стали. Геометричні осі рухомого і нерухомого конусів утворюють кут до 2…30. При обертанні эксцентрикового склянки геометрична вісь рухомого конуса описує конічну поверхню з вершиною у точці підвісу валу, а сам конус робить кругові качання всередині нерухомого. Дроблення матеріалу відбувається у зоні, де поверхні конусів зближуються, а розвантаження — там, де ті поверхні расходятся.
Максимальна крупность шматків, завантажених в дробарку при У = 900, 1200 і 1500 мм, становить відповідно 750, 1000 і 1200 мм, а ширина розвантажувальною щілини — 125…225 мм.
Конусні дробарки для середнього та малого роздрібнення (рис. 5, б) значно різняться від дробарок великого роздрібнення передусім обрисом профілю робочого простору. Рухомий дробящий конус 7 має кут при вершині 80…100° «положистий конус», у дробарок великого роздрібнення цей кут становить 20…30° («крутий конус»). Нерухомий дробящий конус 3 також розширюється донизу, створюючи з забезпеченням рухомим «паралельну зону» (рис. 5, в), на своєму шляху через яку матеріал піддається кількаразовому стиску і дробленню до розміру, рівного вихідний щілини. Тому крупность продукту роздрібнення визначається шириною закритою, а чи не відкритої, як в дробарок великого роздрібнення, розвантажувальною щілини. Камери роздрібнення цих дробарок приймають менші за величиною шматки і видають дрібніший продукт. Найбільший розмір загружаемого шматка в дробарки середнього роздрібнення 60…300 мм при розмірі розвантажувального отвори 12…60 мм; у дробарок дрібного роздрібнення відповідно 8…170 мм при розмірі розвантажувального отвори 5…20 мм.
У цих дробилках інакше виконано опора дробящего конуса. Вал 6 (рис. 5. б), у якому насаджений дробящий конус, виконано консольным, які мають верхньої опори. Якщо в дробарок великого роздрібнення дробящий конус шарнірно підвішений до траверсі, те в дробарок для середнього та малого роздрібнення опора дробящего конуса лежить у центрі його качання і виконано вигляді сферичного подпятника 13 великого радіуса, сприймає як масу конуса і валу, і зусилля роздрібнення. Нижній кінець валу вставлено в эксцентриковую втулку 11, розміщену у склянці, які представляють одне зі станиною дробарки. Эксцентриковая втулка отримує обертання від електродвигуна через горизонтальний вал і конічну передачу. Матеріал надходить на диск-питатель 14 і рівномірно розподіляється з усього завантажувальному отверстию.
Дробарки для середнього та малого роздрібнення більш быстроходны. Кількість хитань дробящего конуса на хвилину — 215…350, у конусных дробарок великого роздрібнення — всього 80… 170.
Технічна продуктивність конусных дробарок (м3/ч) Пт=qb, де q — продуктивність, яка припадає на 1 мм вихідний щілини, м3/ч; для дробарок середнього роздрібнення q = 0,54 D2n, для дрібного роздрібнення q= l, 32 D2n; D — діаметр підстави рухомого конуса, м; п — частота кругових хитань, с-1; b —ширина вихідний щілини, мм.
Перевагами конусных дробарок є безперервність їх і відсутність холостого ходу. Енергоємність роздрібнення залежить від міцності продукту роздрібнення і рівня роздрібнення. При роздрібненні вапняків міцністю 60…80 МПа в дробилках великого роздрібнення і розмірі вихідних шматків 300…1500 мм при ширині вихідний щілини 50…200 мм енергоємність роздрібнення становить 0,27…0,75 кВт-ч/т.
Валковые дробарки. Робітниками органами валковой дробарки (рис. 6) |[pic] | |[pic] | | | | | | | | | |Рис. 6. Валковые дробарка: | | |а) Конструкція; | | |б) Схема дробарки. |.
є дві паралельних циліндричних валка 2 і 4, обертові назустріч одне одному. Потрапляє в робочу зону шматок матеріалу захоплюється тертям про поверхню валків і затягується у робочий простір, де піддається дробленню внаслідок розколювання, зламу і истирания. Поверхні валків виготовляють гладенькими й рифлеными. Валки монтуються на станині 1 в підшипниках 3 і шість. Підшипники одного або двох валків мають пружинні опори 5, які можуть опинитися переміщатися в направляють потрапляючи в дробарку не дробимого предмета. Обертання валка повідомляється від електродвигуна через клиноременную передачу із частотою 75…190 мин-1.
Найбільший розмір шматка матеріалу, загружаемого в дробарку, залежить від кута захоплення, що визначається діаметром валків і коефіцієнтом тертя про металеву поверхню валків. Для можливості захоплення гладенькими валками вихідного продукту зоні роздрібнення необхідно, щоб кут захоплення валків не перевищував кут тертя матеріалу про поверхню валків. Максимальний розмір шматків залежить від діаметра валків та розміру розвантажувальною щілини. Для виконання цих умов діаметр рівного валка удвадцятеро повинен перевершувати розмір каменю, а при рифлених поверхнях валків — удванадцятеро. Тому валковые дробарки застосовують лише вторинного роздрібнення порід середній і малої міцності, і навіть для подрібнення в’язких і вологих матеріалів. Ступінь подрібнення— 4…12. Типорозмір дробарки характеризують діаметром і довжиною валків. Продуктивність валковых дробарок (М3/Ч) ПT = 3600 aL (R, де, а — ширина розвантажувальною щілини, м; L — довжина валка, м; (— окружна швидкість, м/с; R — коефіцієнт, враховує використання довжини валків, ступінь розпушення матеріалу, нерівномірність подачі; R = 0,1…0,3 для м’яких, і R = 0,4… 0,5 для твердих пород.
Роторні і молотковые дробарки. Роторні дробарки застосовують для роздрібнення вапняку, доломіту, руд, мармуру та інших аналогічних матеріалів, які мають малої абразивностью. Їх випускають двох типів: для великого роздрібнення, що використовують на первинної стадії роздрібнення; для середнього та малого роздрібнення, використовувані на заключних стадіях роздрібнення. Робота таких дробарок полягає в принципі руйнації порід ударними навантаженнями. Роторні дробарки забезпечують отримання щебеню високої якості, переважно кубообразной форми, з одночасним збагаченням продукту роздрібнення, оскільки слабші складові порід піддаються значному подрібненню і отсеиванию від основних фракций.
Роторна дробарка є коробчатый корпус 3, у якому розміщені обертався із швидкістю ротор 1 з жорстко закріпленими на його зовнішньої поверхні билами 2 (рис. 7.). | |[pic] | | | | | | | |Рис. 7. | | |Роторна | | |дробарка. | |.
Обертання ротору повідомляється від електродвигуна через клиноременную передачу. Усередині корпусу підвішені відбивні плити 4 і аналогічних сім, нижня частина яких спирається на пружинно-регулировочное пристрій 5 і шість, що дозволяє регулювати ширину вихідний щілини, і навіть пропускати не дробимое тіло при його потраплянні у камеру роздрібнення. Дроблення матеріалу ввозяться результаті удару у ній бив і удару шматків про відбивні плити, ніж досягається висока (10…20) ступінь роздрібнення. Порівняно коїться з іншими типами дробарок роторні дробарки мають меншу металлоемкость, невеликі габарити, що у поєднані із високим рівнем роздрібнення зумовило застосування в пересувних дробильных установках. Розмір найбільшого шматка, загружаемого в дробарки великого роздрібнення, 800…1000 мм, середнього — 400…600 мм при окружної швидкості 20…35 м/с.
Для роздрібнення порід середньої міцності, і навіть м’яких матеріалів, як-от шлак, гіпс, крейда, глини, застосовують молотковые дробилки.
Молоткова дробарка (рис. 8) складається з зварного корпусу 1, у якому | |[pic] | | | | | | | |Рис. 8 | | |Молоткова | | |дробарка | |.
встановлено ротор 2, відбійна плита 4, поворотна 5 і выдвижная колосниковая грати 6. Ротор складається з однієї чи кількох дисків, закріплених спільною для приводном валу. Дроблення матеріалу здійснюється під впливом удару у ній молотків 3 масою 15…20 кг, шарнірно закріплених до дискам обертового ротора, і співудару шматків з плитами і колосниковыми гратами. Становище колосниковых решіток і відбійної плити — регульоване. Робочий зазор між внутрішньої поверхнею колосникової грати та ротором вибирають залежно від крупности продукту роздрібнення. При великому роздрібненні зазвичай він у півтора — майже удвічі більше поперечника максимальних шматків продукту роздрібнення, а при малому — у трьох — п’ять разів. Розмір найбільшого шматка матеріалу, загружаемого в молотковые дробарки, — 75…600 мм при окружної швидкості молотків 60 м/с. При обертанні ротора молотки під впливом відцентрових сил займають напрям лінією, що з'єднує вісь ротора з віссю обертання молотка. При ударі молотки повертаються навколо своєї осі у бік, протилежному обертанню ротора. Шарнирное кріплення молотків у молотковых дробарок істотно відрізняє їхню відмінність від роторних з жорстко закріпленими билами. Недоліком молотковых дробарок є швидкий знос молотків і колосниковых решіток. Вони теж можуть бути рекомендовані для подрібнення занадто в’язких (глинистих) вологих матеріалів, які забивають колосниковую решетку.
Машини для сортування кам’яних материалов.
Процес поділу маси чи суміші зерен природного походження на класи по крупности називається грохочением чи сортуванням. Грохочение здійснюють механічним, гідравлічною, повітряним і магнітним способами. Найбільш поширений механічний спосіб, у якому дробленую масу поділяють шляхом просіювання на грохотах. Основний частиною гуркоту є просеивающая поверхню. Вона виконується як сита з плетеної чи зварної сітки, і навіть решета, штампованого з листової сталі, чи литого з гуми. Сита і решета мали бути зацікавленими износостойкими, зберігати у процесі роботи незмінним розмір отворів, мати велику площа отверстий.
Розрізняють грохочение попереднє, проміжне, товарне (остаточне). Попереднє грохочение застосовують для грубої сортування на великі та малі шматки перед дробарками первинного роздрібнення. При проміжному грохочении з дробленого матеріалу відокремлюються більші шматки направлення в дробарки наступних стадій роздрібнення. При остаточному грохочении матеріал поділяють на фракції вже о відповідність до вимогами стандарту. Поділ матеріалу по крупности на фракції ввозяться результаті надання поверхні грохочения певних по частоті і амплітудою коливань, які забезпечують ефективне струшування матеріалу і проходження зерен через просеивающие поверхні. На грохотах можна встановлювати близько трьох сит. Сита мають одноплощинно (грохочение від дрібного до великому) чи ярусами (грохочение від великого до мелкому).
При грохочении від дрібного до великому (рис. 9) гуркіт має конструкцію простую,.
| |[pic] | |Рис. 9 | | |Схеми | | |розташування сит| | |на грохотах: | | |як від дрібного до | | |великому | | |б) від великого до| | |малому | | |в) | | |комбіноване | |.
удобную для огляду і ремонту сит. Недоліками такий схеми є велика довжина гуркоту, інтенсивний знос першого сита, низьку якість грохочения, оскільки дрібні частки захоплюються більшими. При грохочении від великого до малому досягаються високу якість сортування, більш рівномірне знос сит, проте погіршується можливість контролю над роботою гуркоту. Комбінована схема проти іншими займає проміжне ситуацію і є найбільш распространенной.
При переміщенні по просеивающей поверхні сит матеріал поділяється по крупности. Зерна матеріалу, перевищують розмір отворів сит, сходять із поверхні грохочения, створюючи верхній клас. Зерна матеріалу, минулі через отвори, називаються нижнім класом. Нижній клас кожного попереднього сита є вихідним матеріалом наступного розташованого його сита. При русі матеріалів по ситу в повному обсязі зерна розміром менше отвори сита можуть пролягти нього. Через війну верхній клас виявляється засоренным зернами нижнього класу. Ставлення (у відсотках) маси зерен, пройшли крізь сито, до кількості матеріалу той самий крупности, що міститься в вихідному матеріалі, називають ефективністю грохочения. Еталонне значення ефективності грохочения залежно від матеріалу та певного типу грохотов становить 86…91%.
По виконанню й типу приводу грохоты ділять на нерухомі колосниковые, барабанні які працюють, эксцентриковые і інерційні виброгрохоты.
Нерухомі грохоты. Такі грохоты є колосниковые грати з износостойкой почав із високим ударним опором. Їх застосовують для попереднього грохочения.
Барабанні грохоты. Вона має похилий, з точки 5…7°, обертався барабан, що з секцій з різними розмірами отворів. Завантаження ввозяться секцію з меншими розмірами отворів. При трьох секційному барабані отримують чотири фракції щебеню. Діаметри барабанів таких грохотов 600…1000 мм при довжині З…3,5 м. Частота обертання гуркоту залежить з його діаметра і як 15…20 мин-1. При більшої частоті грохочение припиняється. Продуктивність їх 10…45 м3/ч при потужності двигуна 1,7…4,5 кВт. У зв’язку з низькою якістю грохочения та очі великою витратою енергії барабанні грохоты мають обмежений применение.
Эксцентриковые грохоты. Гуркіт (рис. 10, а) складається з похилого під кутом 15…25° короби 1 з ситами 6 і побачили 8-го; шарнірно підвішеного до шейкам приводного эксцентрикового валу 7 з дебалансами 5 і спирається на пружини 2. Обертання валу передається від електродвигуна 3 через клиноременную передачу 4. Під час такої підвісці короби матеріал з його просеивающей поверхні отримує кругові коливання із постійною амплітудою, рівної подвійному эксцентриситету валу, за будь-якої навантаженні. Эксцентриковые грохоты виготовляють з цими двома ситами розміром 1500×3750 мм амплітудою коливань 3…4,5 мм частотою коливань 800…1400 в минуту.
| |[pic] | | | | | | | |Рис.10 Схеми | | |пласких грохотов: | | | | | |а) эксцентриковый | | |б) інерційний | | |похилий | | |в, р) інерційний | | |горизонтальний | |.
Інерційні виброгрохоты. Вони діляться на інерційні похилі (кут нахилу сит 10…25°) і інерційні горизонтальные.
Інерційний похилий виброгрохот (рис. 10, б) має приводний механізм, являє собою вал 6 з дебалансами 5, опертий на два підшипника, корпусу яких укріплені в стінках короби 1. Короб з ситами 7 і побачили 8-го спирається на підставу через пружні зв’язку 2. Форма коливань залежить розміщення неврівноважених мас і способу підвіски короби. Вони можуть бути круговими, еліптичними чи прямолінійними (грохоты з пластинчастими ресорами). Найбільш ефективні грохоты на пружинних опорах. Регулювання амплітуди коливань досягається змінними дебалансами. На відміну від эксцентриковых в інерційних грохотах зі збільшенням навантаження амплітуда коливання короби зменшується автоматично, захищаючи конструкцію від перевантажень. Такі грохоты застосовують для важких умов праці при товарному грохочении, і навіть для попереднього грохочения крупнокусковых матеріалів перед первинним дробленням (замість сит встановлюють колосниковые грати до одного ярус). Розміри просеивающей поверхні сит 1750×1450 мм, частота обертання валу вібратора порядку 800 мин-1, амплітуда коливань 3,7…4,5 мм.
Ефективне сортирование досягається з вибраторами спрямованого дії (рис. 10, в, г).
Інерційний горизонтальний виброгрохот має вибровозбудитель прямолінійно спрямованих коливань 9, змонтований на коробі з ситами. Збудник і двох паралельно розташованих дебалансных валів, одночасно що обертаються у різних напрямках. Обурює сила такого вібратора спрямована по прямий, перпендикулярної лінії, що з'єднує центри дебалансных валів, змінюється згідно із законом синуса. Кут дії між возмущающей силою і площиною сит становить 35…45°. Короб з ситами спирається на підставу через вертикальні пружини. Розміри просеивающей поверхні сит таких грохотов 1250×3000 мм, частота коливань 500… 700 в хвилину, амплітуда коливань 8… 12 мм, потужність приводного двигуна 5,5 кВт. Горизонтальні виброгрохоты з спрямованими коливаннями забезпечують велику питому продуктивність і вибрати кращу якість грохочения по порівнянню з наклонными.
Технічна продуктивність грохотов (мэ/ч) при проміжному і остаточному грохочении Пт = qAR1R2R3, де q — питома продуктивність 1 м² сита для певного розміру отворів (для отворів від 5 до70 мм змінюється від 12 до 82 м3/ч); А — площа сита, м2; R1 — коефіцієнт, враховує кут нахилу гуркоту (для горизонтальних грохотов з спрямованими коливаннями R1 = 1,0; для похилих при вугіллі нахилу 9…15° — 0,45…1,54); R2 — коефіцієнт, враховує вміст у даному продукті зерен нижнього класу (при змісті 10… 90% відповідно 0,58…1,25); R3 — коефіцієнт, враховує вміст у нижньому класі зерен менше [pic] розміру отворів сит (при змісті 10.90% відповідно 0,63…1,37).
При наближених розрахунках можна визначати продуктивність гуркоту як продуктивність жолоби з певною пропускною спроможністю Пт=3600bh (Rp, де b — ширина сита, м; h — товщина шару що сортується матеріалу, м (приймається рівної розміру вступників на сито шматків); (= 0,05…0,25 м/с — швидкість руху матеріалу вздовж жолоба; Rp = 0,4…0,5 — коефіцієнт розпушення материала.
Машини для мийки кам’яних материалов.
Заповнювачі бетону промивають видалення глинистих і органічних домішок і пилу. І тому використовують різні способи. Якщо крупность заполнителя вбирається у 70 мм, а забрудненість мала і домішки легко віддільні, то промивання поєднують з сортуванням. На гуркіт трубами з сопел подається вода під тиском 0,2…0,3 МПа. Витрата води 1,5… 5 м³ на 1 м³ промываемого материала.
Матеріали значущістю 300…350 мм промивають в циліндричних гравиемойках-сортировках, які з похилого барабанного обертового гуркоту з додатковою моющей секцією з глухий (без отворів) поверхнею. Вода на промивання подається разом із матеріалом. Витрата води до 2 м³ на 1 м³ промываемого матеріалу. Для сильно забрудненого гравію і щебеню, містять глинисті включення, застосовують мийні барабани з лопатями, закріпленими внутрішній поверхні барабана. Вода подається назустріч руху матеріалу. Діаметри барабанів — 1,5.2,0 м при довжині до 4,0 м, продуктивність установок — до 100 м3/ч.
Для мийки піску, відокремлення нього частинок менш 0,15 мм наступного зневоднення застосовують гідромеханічні і гідравлічні классификаторы.
Гидромеханический класифікатор є короб, всередині якого розміщена спіраль. При обертанні спіралі зважені у питній воді дрібні частки відводяться в нижню частина короби, а великі направляються спіраллю до верхньому разгрузочному вікна. Короб встановлюють з точки 16…18°. Діаметр спіралі 1000…1500 мм за частоти обертання 8…14 мин-1. Продуктивність класифікатора — до 200 т/ч.
Гідравлічні класифікатори (рис. 11, просто вважають для промивання і | |[pic] | | | | | | | |Рис.11 | | |Гідравлічні | | |класифікатори: | | | | | |а) вертикальний | | |б) горизонтальний | | |багатоканальний | |.
поділу піску на дві фракції. У цих установках пісок, попередньо змішаний із жовтою водою як пульпи, вводять у вертикальний класифікатор через патрубок 1 і диффузор 2 в збагачувальну камеру 3, де швидкість потоку суміші значно зменшується і великі частки випадають в класифікаційну камеру 5. По патрубку 6 в класифікаційну камеру подається чиста вода, створюючи в камері гвинтовій висхідний потік. Частинки піску (до 0,5 мм) відносяться які виходять потоком води горішнього сливному коллектору 4, а великі частки випадають з класифікаційної камери, обезвоживаются і чинять споживачеві. Гидроклассификаторы є напорными апаратами, тиск лише на рівні зливальний труби сягає 0,3 МПа. Продуктивність їх за грунту — 20… 300 м3/ч.
За необхідності промивання й міжнародного поділу зернистого матеріалу на кілька фракцій використовують горизонтальні багатокамерні гидроклассификаторы (рис. 11, б). Вихідний матеріал в пульпообразователе змішується з і вступає у пірамідальний лоток 9, а звідти — в прямокутне корито 8, розділена вертикальними перегородками чотирма камери. Поділ на фракції виходить за допомогою регулювання кількості води, поданого в класифікаційні камери знизу і котра утворює висхідні потоки. Вода, піднімаючись по камері, виносить частки піску, швидкість випадання котрих значно менша швидкість руху висхідних потоків. Принаймні нагромадження зважених частинок в камері щільність пульпи збільшується, унаслідок чого рівень води в гидростатической трубці 11 разом із поплавком 10 піднімається. Щойно поплавець упреться у верхній датчик, автоматично відкривається розвантажувальний клапан 7. Принаймні розвантаження поплавець опускається й вона стосується нижнього датчика, сигнали якого передаються механізму закриття клапана. Потім цикл роботи камери повторюється. Продуктивність по вихідному матеріалу— до 50 т/ч, витрата води — 4…6 м3/т.
Заключение
.
З цієї реферату ми дізналися одного із класів будівельних машин.
Також ми дізналися про конструктивних особливостях, про принципі роботи, про енергоспоживання, про принципі роботи, сферах применения.
1. Будівельні машини: Учеб. для вузів по спец. С86 ПГС/Д. П.
Волков, М. І. Альошин, У. ЯКрикун, Про. Є. Рынсков;
Під ред. Д. П. Волкова.—М.: Высш. шк., 1988.
2. Волков Д. П., Миколаїв З. М. Підвищення якості будівельних машин. М., 1984.
3. Домбровський М. Р., Гальперин М. І. Будівельні машины.
М., 1985.
4. Фиделев А. З., Гомілка. Ю. Ф. Будівельні машини. Київ, 1979.