Разработка настінного поворотного крана
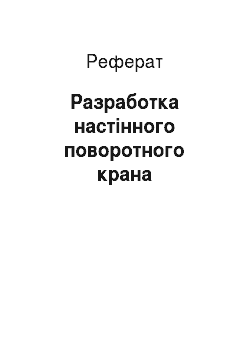
СР — це ремонт, виконаний на відновлення исправностей і часткового відновлення ресурсу устаткування заміняючи чи відновленням складових частин. 1. Всі роботи, пов’язані з ТЕ. 2. Огляд і заміна зношених деталей: канатів, підшипників, блоків, муфт. 3. Огляд і заміна шпоночных і болтовых сполук. 4. Заміна окремих вузлів та його вивірка (відкрита левередж). 5. Ремонт і регулювання гальма (колодочный… Читати ще >
Разработка настінного поворотного крана (реферат, курсова, диплом, контрольна)
Утверждено.
Предметної комиссией.
____________________.
Председатель________.
ЗАВДАННЯ ДЛЯ КУРСОВОГО ПРОЕКТИРОВАНИЯ По предмета: Устаткування Учневі Кошелеву Олександра Миколайовича Спеціальність 1701 Курс 5 Група ЗМ — 051 Тема завдання: Розробити настінний поворотний кран грузоподъёмностью 25 кн., швидкістю піднесення вантажу 16 м/мин, на висоту 6 м при вильоті стріли крана L = 4,5 метрів і середньому режимі роботи ПВ = 25%. Курсової проект виконується наступного объёме:
1. Пояснювальна записка.
1. Розрахунок і вибір каната, поліспаста вантажний подвески.
2. Вибір і розрахунок механізмів піднесення, повороту і переміщення кранової тележки.
3. Добірка й розрахунок гальмівний системы.
4. Підбір елементів привода.
5. Підбір металлоконструкций.
2. Графічна частина проекта.
Ліст 1. Чертёж загального виду крана Ф. А 1.
Ліст 2. Складальний чертёж механізму переміщення Ф. А 1.
Ліст 3. Робітники креслення деталей Ф. А 1.
Дата выдачи.
15.01.04.
Термін окончания.
04.05.04.
Преподаватель.
Зав. отделением.
1.
Введение
.
2. Технологічний раздел.
1. Розрахунок подъёмного механизма.
2. Розрахунок механізму поворота.
3. Розрахунок механізму передвижения.
4. Розрахунок металлоконструкции.
5. Розрахунок валов.
6. Вибір шпоночного соединения.
7. Розрахунок і вибір муфт.
8. Вибір і перевірка подшипников.
3. Система технічного обслуговування і ремонту настінного поворотного крана.
1. Призначення СТО і РТО.
2. Визначення категорії ремонтної труднощі й періодичності проведення СВ. і КР.
3. Упорядкування структури ремонтного цикла.
4. Визначення переліку робіт з СТО і РТО.
5. Найбільш зношувані вузли і деталі, їх причини методи предосторожности.
6. Упорядкування технологічних карт на дефектацию і ремонт деталей.
7. Упорядкування технологічних карт на монтаж.
8. Порядок монтажа.
9. Карта настінного поворотного крана.
10. Вибір сорти масла.
11. Порядок експлуатації крана.
12. Правила ТБ під час роботи ГПМ.
4.
Список литературы
.
1.
Введение
.
Грузоподъёмная машина варта пересування вертикалі, і передачі вантажів з однієї точки до іншої з допомогою обслуговуючої машины.
Грузоподъёмные механізми працюють періодично, чергуючи робоче движение.
— переміщення вантажу на одній з площин — з холостим ходом. Після захоплення вантажу з допомогою тієї чи іншої грузоподъёмного органу, грузоподъёмные механізми піднімають (опускають) його за деяку высоту.
Після розвантаження грузозахватные пристосування вхолосту повертаються до початкове положення для захоплення нового вантажу та циклу повторяется.
Грузоподъёмные машини знаходять широке застосування на підприємствах легкої промисловості, і навіть під час виробництва ремонтно-монтажных і вартість будівельних работ.
Машини для вертикального і горизонтального переміщення вантажів діляться на дві групи: крани мостового типу, і поворотні крани. Найпростішим типом поворотного крана є кран з обертовою колоною, але такі крани здебільшого встановлюють біля стіни і вони теж мають кут повороту трохи більше 1800.
Більше сучасної конструкцією поворотного крана обслуговування відкритих, і навіть закритих площ є настінний поворотний кран з кранової тележкой.
Механізм повороту здійснюється за допомогою відкритої звичайною зубчастою передачі, наведеній в рух від ручного привода.
Механізм переміщення кранової візки здійснюється також вручну з допомогою ланцюгової передачи.
Механізм піднесення здійснюється за допомогою электропривода.
Фундаменти даних різновидів кранів повинні відповідати всі вимоги з метою забезпечення безпеки работы.
2. ТЕХНОЛОГІЧНИЙ РАЗДЕЛ.
1. Розрахунок подъёмного устройства.
1. Визначаю тип каната.
1. Визначаю розривне зусилля в канате.
Sразр? Smax*n [2;29] (2.1),.
Де n — коефіцієнт запасу міцності, за середнього режимі роботи n = 5.
Smax — максимальне натяг каната в полиспасте (кН).
Smax = З тар * (1-?бл)/(1- ?блin) [2;29] (2;2),.
де стар — вагу вантажу чи грузоподъёмность, кН.
?бл — ККД блоку = 0.97 in — кратність поліспаста = 2.
Smax = 25*(1 — 0.97)/(1 — 0/972) = 12.5 кН.
Sразр = 12,5 * 5 = 62,5 кН.
З разрывного зусилля вибрали канат типу ТК 6×19 діаметром 9.3 мм, з разрывным зусиллям 62,9 кН (ГОСТ 3070 — 74).
2.1.1.2 Визначаємо геометричні розміри блоков.
Dбл? Kd * dk [2;26] (2.3),.
де Kd — запас міцності каната при динамічних навантаженнях Kd = 20 dk — діаметр каната dk = 9.3.
Dбл = 20 * 9.3 = 186 мм, r = (0.6 год 0.7) * dk [2;125] (2.4),.
де r — радіус канавки під канат, мм.
r = 0.6 * 9.3 = 5.58 мм; [2;125] (2.5).
hk = (1.5 год 2) *dk hk — висота канавки під канат, мм hk = 1.5 * 9.3 = 18.2 мм.
вк = (1.6 год 3) * dk [2;125] (2,6).
вк — ширина канавки, мм вк = 3 * 9,3 = 27,9 мм.
зст = 2 * вк + 3 [2;125] (2,7).
де зст — довжина маточини, мм зст = 2 * 27.9 + 3 = 58.8 мм.
2.1.1.3Определяем геометричні розміри барабана.
Dб? Dбл [2;125] (2.8).
де Dб — діаметр барабана, мм.
Dбл — діаметр блоку, мм.
Приймаємо Dб = Dбл = 186 мм. Канат намотується на барабан до одного слой.
L = Lk * t (? * m[ Dб + dk * m]) [3;18] (2.9).
де L — робоча довжина барабана, м t — крок навивки каната на барабан, т.к. барабан гладкий t = dн.
Lk = H * im [2;30] (2.10).
де Lk — довжина каната, м h — висота піднесення вантажу, м H = 6 м.
Lk = 6 * 2 = 12 м.
L = 12 * 0.0093/ 3.14 (0.186 + 0.0093 * 1) = 0.182 м.
Lобщ = L + Lkp + ?lбб [3;13] (2.11).
де Lобщ — загальна довжина барабана, мм.
Lкр — довжина, необхідна для кріплення каната, мм.
Lkp = 4 * t [3;19] (2.12).
Lkр = 4 * 9.3 = 37.2 мм.
Lбб — довжина борту барабана.
Lбб = 1,5 * 9,3 = 13,95 мм.
Lобщ = 182 + 37.2 + 13.95 * 2 = 247.1 мм.
4. Визначаємо товщину стінки барабана.
? = 0.02 * Dб + (6 год 10) [2;31] (2.14).
? = 0.02 * 186 + 6 = 9.8 мм.
2.1.1.5 Кріплення каната.
Канат кріпиться до стінки барабана з допомогою планок. По нормам.
Держгіртехнагляду число крепёжных гвинтів має не менше двух.
Планки мають канавки трапециидальной форми з кутами нахилу = 400. При коефіцієнті тертя сталь про сталь? = 0.16 і вугіллі обхвати 2-х запаяних витків каната? = 4?. Знаходимо силу тертя каната на місці крепления.
Fkp = ?max/Lf? [2;32] (2.15).
де L — підставу = 2.71.
Fkp = 12 500/4.53 = 2759.4 H.
F3 = Fkp/(f + f1) [2;33] (2.16).
де F3 — сила затяжки притяжных гвинтів, М f1 — приведений коефіцієнт тертя м/д барабаном і планкою = 0.22.
[2;33].
F3 = 2759.4/(0.16 + 0.22) = 7261.6 H.
d гвинта = 1.2 * dk [2;33] (2.17).
де d гвинта — діаметр притяжных болтів, мм d гвинта = 1.2 * 9.3 = 11.16 мм.
Приймаємо болти для притиснення планок різьблені М 12 зі сталі СП 3 з допускає напругою [?] = 80 МПа.
? Сум = 1.3F3/z?d1*0.5 + Mu/z * 0.1 * d13? [?p] [2;33] (2.18).
де ?торб — сумарне напруга стискування і розтяги, МПа d1 = середній діаметр різьби гвинтів, мм z — число винтов.
? Сум = 1.3 * 7.26 * 1.6 * 4/2 * 3.14 * 102 +.
2759.4 * 9.3/2 * 0.1 * 103 * 2 = 72.4 МПа.
Міцність гвинтів обеспечивается.
[pic].
Рис. 2.1 Ескіз барабана.
Таблиця 2.1.
Розміри барабана, мм |Lбар |L |Lkp |Lбб |Dб |? | |247.1 |182 |32.2 |13.95 |186 |9.8 |.
5. Залежно від діаметра каната вибираємо розміри профілю струмка блока.
[pic].
Рис. 2.2 Профіль блока.
Таблиця 2.2 Розміри профілю блоку |80 |14 |25 |9 |5.4 |.
2.6.3 Вибираємо параметри шпоночного сполуки для валу барабана механізму підняття з таблиці До 42.
Таблица 2.8 Параметри шпонок валу. |L |h |B |t1 |t2 | |100 |14 |25 |9 |5.4 |.
2.6.4 Перевірочний розрахунок шпонки під вал барабана механізму подъёма.
?див = 2Мк/[d (0.9 * h — t1) L]? [?см].
где Км — рухаючись момент = 1162 М * м d — діаметр валу = 62 мм = 0.062 м h — висота шпонки = 14 мм = 0.014 м t1 — робоча глибина в пазе валу = 9 мм = 0.009 м L — довжина шпонки = 100 мм = 0.1 м [?див] = 80 МПа — дозволене напруга стискування? див = 2 * 1162/[0.062(0.9 * 0.014 — 0.009)0.1] = 7.5 МПа? див? [?див] 7.5МПа? 80 МПа.
2.7 РОЗРАХУНОК І ВИБІР МУФТ.
2.7.1 Визначаємо расчётный момент на валу двигуна механізму подъёма.
Тр = Кр * Мк1? Т [6;220] (2.81).
где Кр — коефіцієнт режиму навантаження = 1.25 Мк1 — крутний момент на валу двигуна = 35 М * м Т — номінальний поводить момент встановлений стандартом = 63 М * м Тр = 1.25 * 35 = 43.75 М * м < Т = 63 М * м.
2.7.2 Визначаємо радіальну силу викликану радиальным смещением.
Fм = С? r * ?r [6;222] (2.82).
где С? r — радіальна жёсткость муфти? r — радіальне усунення Fм = 800 * 0.2 = 400 М Вибираємо муфту пружну (ГОСТ 21 425 — 93) втулочно-пальцевую з гальмівним шкивом з єдиною метою економії габаритних розмірів всього механізму [pic].
Рис. 2.12 Муфта.
Таблиця 2.9 Параметри муфти втулочно-кольцевой. |L |d |D | |70 |24 |100 |.
2.8 ВИБІР І ПЕРЕВІРКА ПОДШИПНИКОВ.
2.8.1 Для валу під барабан вибираємо кулькові радиально-упорные однорядные підшипники (ГОСТ 831 — 75) Цей підшипник найпридатніший т.к. на барабан діє велика радіальна сила, й у водночас осьова. Підшипники цього призначені до цих нагрузок.
Подшипник 36 210 dвн = 50 мм Dнар = 90 мм Bоб = 20 мм Вантажопідйомність 33.9 кН.
2.8.2 Визначаю сумарні сили, які діють підшипники в точках Проте й З, вишукуючи найбільш навантажений подшипник.
F = Ry2 + Rx2 [6;170] (2.83).
где Ry — реакція в вертикальної площині Rx — реакція горизонтальної плоскости В точці А: FА = Ray2 + Rax2 = 25 002 + 3430.82 = 4245 Н.
У точці З: FC = Rcy2 + Rcx2 = 25 002 + 9312 = 2667.7 Н Наиболее навантажений підшипник у точці А, розрахунок вестимемо по нему.
2.8.2.1 Визначаємо еквівалентну динамічну нагрузку.
RE = V * Fr * K? * K? [6;170] (2.84).
где V — коефіцієнт обертання Fr — радіальна навантаження підшипника K? — коефіцієнт безпеки K? — температурний коефіцієнт RE = 1 * 4245 * 1.2 * 1 = 5094 Н.
2.8.2.2 Визначаємо розрахункову грузоподъёмность подшипников.
Lгр = RE * 573 *? * Lh/108 [6;170] (2.85).
где? — окружна скорость.
? =? * n/30 [6;95] (2.86).
n — частота обертання барабана = 27.6 об./хв? = 3.14 * 27.6/30 = 2.9 рад/с Lh — необхідна довговічність підшипника для червячного редуктора? 5000 Lгр = 5094 * 573 * 2.9 * 5000/108 = 9300.5 М = 9.3 кН.
2.8.2.3 Визначаємо довговічність подшипника.
L10h = 106/? * 573 * (Lгр/RE)3? 10 000 [6;171] (2.87) де Lгр — грузоподъёмность підшипника L10h = 106/2.9 * 573 * (33.9/5.094)3 = 24 212.9 годину > 10 000час Придатність підшипників обеспечивается.
[pic].
Рис. 2.13 Подшипник Таблица 2.10 Параметри підшипника |d |D |в |r | |50 |90 |20 |2 |.
3. СИСТЕМА ТЕХНІЧНОГО ОБСЛУГОВУВАННЯ І РЕМОНТУ НАСТІННОГО ПОВОРОТНОГО КРАНА.
3.1 Призначення системи технічного обслуговування і ремонту технологічного оборудования.
СТО і РТО призначено підтримки обладнання робочому стані, виробляти планові ремонти в заздалегідь встановлених термінів, скорочувати час простою обладнання ремонті, забезпечувати мінімальні витрати при ремонтних работах.
СТО і РТО включає у собі: 1. Визначення видів ТЕ і Р 2. Структуру і тривалість ремонтних циклів 3. Визначення категорії ремонтної складності 4. Нормативи трудоёмкости робіт з ТЕ і Р 5. Впровадження наукову організацію праці (НЗП) 6. Типові добові норми витрат материала В СТО і РТО входять такі види планових ремонтів: 1. ТЕ — технічне обслуживание.
ТО1 — щомісячне обслуживание.
ТО3 — ось квартальне обслуживание.
ТО6 — піврічне обслуживание.
ТО12 — річне технічне обслуговування 2. СВ — середній ремонт 3. КР — капітальний ремонт.
3.2 Визначення категорії ремонтної труднощі й періодичність проведення СВ і КР.
Ремонтна складність — це умовний коефіцієнт, що свідчить про пристосованість устаткування до ремонту, характеризує конструктивні і технологічні особливості оборудования.
З огляду на конструктивні і технологічні особливості настінного поворотного крана, приймаємо категорію ремонтної складності Rм = 4 і періодичність КР і СВ з ТЕ КР = 36 міс. СВ = 12 міс. ТЕ = 3 мес.
3.3 Упорядкування структури ремонтного циклу КР — ТО3 — ТО3 — ТО3 — СВ — ТО3 — ТО3 — ТО3 — СВ — ТО3 — ТО3 — ТО3 — КР.
3.3.1 Визначення трудоёмкости під час проведення КР і СР.
Трудоёмкость ремонтних робіт — це складність і тривалість ремонтних робіт, виконуваних ремонтним персоналом, чол * час.
Тср = Rм * (tср * n) [10;238].
(3.1).
Ткр = Rм * (tкр * n) [10;238].
(3.2).
где tср і tкр — питома трудоёмкость при проведенні СВ і КР n — кількість ремонтів Rм — категорія ремонтної складності = 4 Тср = 4 * (23 * 1) = 92 чол * годину Ткр = 4 * (33 * 1) = 132 чол * час.
3.3.2 Визначаємо тривалість проведення КР і СР.
Dср = Rм * tср/n [10;238] (3.3).
Dкр = Rм * tкр/n [10;239] (3.4).
где n — кількість робітників у бригаді nср = 3 чол nкр = 4 чол Dср = 4 * 23/3 = 24.8 години = 3 зміни Dкр = 4 * 33/4 = 33 години = 4 смены.
3.4 Визначаємо перелік робіт з СТО і РТО.
3.4.1 Перелік робіт науковців при ТО:
ТЕ — це монтаж операцій із підтримці працездатності чи справності устаткування під час використання його за призначенням 1. Зовнішній огляд всіх механізмів, підшипників, огороджень і кріплень. 2. Огляд стану гальм, заміна колодок і регулювання. 3. Перевірка зносу окремих деталей, вузлів, канатів і гаків, з'єднувальних муфт, барабанів, кріплень. 4. Зовнішній огляд доступних частин металоконструкцій. 5. Перевірка справності мастильних систем. 6. Перевірка стану відкритих зубчастих передач. 7. Усунення дрібних несправностей. 8. Перевірка дії всіх механізмів. 9. Контроль правильності ведення записів у товстих часописах приёмки й успішного складання змін крановщиками.
3.4.2 Перелік робіт науковців при СР.
СР — це ремонт, виконаний на відновлення исправностей і часткового відновлення ресурсу устаткування заміняючи чи відновленням складових частин. 1. Всі роботи, пов’язані з ТЕ. 2. Огляд і заміна зношених деталей: канатів, підшипників, блоків, муфт. 3. Огляд і заміна шпоночных і болтовых сполук. 4. Заміна окремих вузлів та його вивірка (відкрита левередж). 5. Ремонт і регулювання гальма (колодочный гальмо). 6. Усунення дефектів металоконструкції (фарбування). 7. Розтин і огляд окремих вузлів (редуктор черв’ячний). 8. Виконання розпоряджень органів нагляду. 9. Ревізія блокової крюкової підвіски. 10. Перевірка правильності всіх механізмів й усунення виявлених дефектів. 11. Заміна мастила і мастильних систем. 12. Уточнення обсягу робіт наступного року ремонт.
3.4.3 Перелік робіт науковців при КР.
КР — це ремонт, що здійснюється до повного відновлення устаткування з заміною чи відновленням будь-яких його частин, включаючи базові частини. 1. Повна розбирання і заміна зношених деталей та вузлів механізмів (зубчаста передача, звёздочка, крюковая підвіска). 2. Ремонт металоконструкцій (огляд і фарбування балки колони). 3. Повна заміна всієї мастила і ремонт мастильних систем. 4. Заміна каната, ходових коліс, блокової крюкової підвіски. 5. Модернізація крюку. 6. Уніфікація деталей механізмів. 7. Виконання робіт з розпорядження органів нагляду. 8. Заміна відкритих передач на редукторах (черв'як і колесо). 9. Обкатка механізмів. 10. Фарбування металоконструкцій. 11. Заміна трафаретов, інструкцій, підписів, і покажчиків. 3.5 Найбільш зношувані вузли і деталі, їх причини. 1. Знос підшипникового вузла конструкції кріплення крана до стіни. 2. Знос ковзанки візки. 3. Знос підшипникового вузла нижньої опори крана. 4. Знос грузоподъёмного каната. 5. Знос поверхні грузоподъёмного барабана. 6. Знос канатоведущего блоку. 7. Знос підшипників під грузоподъёмный барабан. 8. Знос відкритої звичайною зубчастою передачі механізму поворота.
До причин зносу цих деталей пізніше відносять: виникнення великих зусиль й снаги тертя при підйомі вантажу, і навіть при повороті крана щодо своєї оси.
Також до причин зносу слід вважати і якість складання, швидкість руху сопрягаемых деталей, характері і рід мастила, якість обробки тертьових поверхностей.
До способам усунення можна віднести: своєчасну мастило вузлів і механізмів, і навіть регулярний огляд деталей і механизмов.
Більшість відповідальних деталей грузоподъёмных механізмів відновленню не підлягають, вони бракуються й заміняються налаштувалася на нові: підшипники, канати, крюки.
Деталі підлягали відновленню: блоки, вали, муфти, зірочки, металоконструкції відновлюються зварюванням поверхні, нарощуванням поверхонь з допомогою наплавки чи зварюванням, запровадженням додаткових елементів. Відновлення з допомогою обробки налаштувалася на нові ремонтні розміри виробляється вкрай редко.
3.6 Упорядкування технологічних карт на дефектацию і ремонт деталі. Таблиця 1. Технологічна карта на дефектацию детали.
[pic].
3.8 Порядок монтажа.
Спочатку виробляємо складання металоконструкції, тобто. до колоні кріпимо консоль, заздалегідь змонтовану з швелерів і куточків болтовыми соединениями.
У нижню частина колони запрессовываем вал, вже із заздалегідь запрессованным нею зубцюватим циліндричним колесом. Потім на верхню частина колони запрессовывается вал з напрессованной нею рамою для кріплення до стене.
Потім, на заздалегідь передбачену на стіні майданчик, встановлюють подпятниковую опору і жорстко зміцнюють її в болти. У всередину опори вкладається завзятий підшипник 112.
На вал, напрессованный на нижню частина колони, напрессовывают підшипник 1312. Потім із допомогою грузоподъёмного устрою (лебідки, автокран), піднімають і встановлюють колону в опорі і кріплять за раму до стене.
Потім встановлюють механізми повороту, на вал напрессовывают конічну і циліндричну шестерні і виробляють регулювання і центрацию ручного привода.
Потім на консолі, на заздалегідь размещённой у ньому майданчику встановлюється грузоподъёмный барабан. До нього через муфту кріпиться, заздалегідь зібраний, черв’ячний редуктор РГУ — 80. Вал редуктора через муфту з гальмівним шкивом сполучається з электродвигателем.
Потім встановлюється колодочный гальмо, гальмівним шкивом якого є муфта пружна втулочно-пальцевая з гальмівним шкивом.
Потім на консоль крана з допомогою грузоподъёмного механізму встановлюють заздалегідь зібрану кранову тележку.
Потім на консолі в заздалегідь закреплённые стійки встановлюється вал механізму переміщення у якому закріплені з натягом звёздочка і барабан.
Потім на металоконструкції встановлюють канатні блоки.
3.9 КАРТА МАСТИЛА НАСТІННОГО ПОВОРОТНОГО КРАНА |№ |Найменування |Сорт (вид) |Кількість |Переі- | |поз. |вузла |мастила |мастила |одичность | | | | | |(міс) | |1. |Редуктор |И-Т-Д — 460 |1.6 л |6 | | |РГУ — 80 | | | | | | |Консталин | | | |2. |Механізм |жировій |1.5 кг |6 | | |переміщення |УТ — 1 | | | | |візки | | | | | | |Солідол жировій| | | |3. |Відкрита | |0.1 кг |1 | | |левередж | | | | | | | | | | | |Верхня опора крана |Консталин | | | |4. | |жировій |0.1 кг |6 | | | |УТ — 1 | | | | |Підшипникові | | | | | |вузли барабана |Консталин | | | |5. | |жировій |0.1 кг |6 | | | |УТ — 1 | | | | |Крюковая підвіска | | | | | | |Солідол жировій| | | |6. |Нижня опора крана | |0.05 кг |1 | | | | | | | | | |Консталин | | | |7. | |жировій |0.1 кг |6 | | | |УТ — 1 | | |.
[pic].
Рис. 3.1 Кран.
3.10 Вибір сорти масла.
Вибір сорти олії залежить від значення контактного напруги в зубах і фактичною окружної швидкості колёс.
За таких значень для редуктора РГУ — 80 вибираємо олію И-ТД — 460.
Це призначено для змащування тяжелогруженых вузлів. Воно має антиокислительными, антикоррозионными, противоизносными і противозадирными присадками. Кінематична в’язкість олії при 400С у межах від 414 до506 мм2/с.
Для відкритої звичайною зубчастою передачі механізму повороту вибираємо консистентную мастило солідол жировій. Цей тип мастила застосовується при невеликих окружних швидкостях. Мастило наноситься періодично, через певний проміжок времени.
Для змащування підшипників приймаємо Консталин жировій УТ — 1. Цей тип мастила є найбільш распространённым для змащування підшипників працюючих при невеликих окружних швидкостях. Ця змащування має хорошими пластичними властивостями. Олія И-Т-Д — 460 — на рік — 3.2 кг Консталин жировій УТ — 1 — на рік — 3.6 кг Солідол жировій — на рік — 1.8 кг.
3.11 Порядок експлуатації крана До роботи з крані допускаються особи досягли 18 років і мають відповідний допуск даний вид робіт. Працюючи на крані неодмінною умовою виконання правил техніки безпеки. Проведення ТЕ і ремонтів необхідно здійснювати відповідність до технологічної та конструкторської документацією. Результати часткового і сповненого ТЕ і вивести результати всіх проведених випробувань необхідно заносити до наукового журналу по експлуатації і ремонту крана. КР проводиться кожні 3 року, а СВ проводиться щороку. ТЕ проводиться кожні 3 місяці, але незалежно від рівня цього необхідно проводити щомісячне ТЕ і візуальний огляд з усуненням дрібних дефектов.
Необхідно періодично перевіряти наявність мастила в тертьових частинах й механізми, і навіть надійність огороджень і кріплень металлоконструкций.
3.12 Правила ТБ під час роботи на грузоподъёмных кранах.
Грузоподъёмные машини повинні виготовлятися за типовими проектами спеціалізованих організацій чи спеціалізованих заводів, окремими випадках лише за узгодженням з міським управлінням округу Госгортехнадзора.
Грузоподъёмность та інші параметрів має відповідати державним стандартам.
Розрахунок на міцність має здійснюватися по дійсному режиму роботи. Механізми грузоподъёмных машин, саме механізм піднесення і вильоту стріли нічого не винні допускати довільного опускання вантажу і стрелы.
У вузлах механізмів передавальний крутний момент застосування пресових посадок не допускается.
Нерухомі осі, службовці для опори барабанів, блоків, обертових частин 17-ї та деталей мали бути зацікавленими надійно закріплені щоб уникнути перемещений.
Болтові, шпоночные і клиновые сполуки повинні прагнути бути предохранены від довільного розгвинчування чи роз'єднання. Металоконструкції повинні захищатися від коррозии.
Пересувні та вільно які стоять стреловые крани би мало бути стійкі під час роботи і за неробочому состоянии.
Реконструкція крана можлива лише за злагоді із заводом изготовителем.
Перед пуском якого або механізму повинен подаватися звуковий сигнал.
До на цьому вигляді устаткування не допускаються люди й не минулі спеціального навчання, переліку інструкцією, і які мають відповідного допуску до работе.
4.
СПИСОК ЛИТЕРАТУРЫ
.
4.1 Ерліх В.Д. «Подъёмнотранспортне устаткування легкій промисловості» Довідник — М. Легпромбытиздат, 1985 р. — 240 стор. ИЛ.
4.2 Додонов Б. П. «Грузоподъёмные і транспортні устрою» підручник для технікумів — М. Машинобудування, 1984 р. — 136 стор. ИЛ.
4.3 Руденко Н. Ф. «Курсове проектування грузоподъёмных машин» Вид. 3-тє, перераб. і доп. М. Машинобудування, 1971 р. — 464 стор. ИЛ.
4.4 Павлов Н. Г. «Приклади розрахунків кранів» Вид. 3-тє, перераб. і доп. Л. Машинобудування, 1967 р. — 345 стор. ИЛ.
4.5 Довідник «Редукторы».
4.6 Шейнблит А.Є. Навчальний посібник — «Курсове проектування деталей машин» Вид. 2-ге, перераб. і доп. Калінінград, Бурштиновий союз, 1999 р. — 454 стор. ИЛ.
4.7 Заводчиків Д.А. «Грузоподъёмные машини» Вид. 2-ге, перераб. і доп. М. Машинобудування, 1961 р. — 310 стор. ИЛ.
4.8 Андрєєв В.І. «Довідник конструктора-машиностроителя» Т — 1. Вид. 7-ме, перераб. і доп. М. Машинобудування, 1992 р. — 816 стор. ИЛ.
4.9 Якобсон М. О. «Єдина система ППР і раціональна експлуатація технологічного устаткування» Вид. 6-те, перераб. і доп. М. Машинобудування, 1967 р. — 590 стр.
4.10 Худих М. И. «Ремонт і монтують устаткування текстильної і легкої промисловості» Вид. 3-тє, перераб. і доп. М. Легпромбытиздат, 1981 р. — 304 стр.