О надійності валів УЭЦН і виборі матеріалів їхнього виготовлення
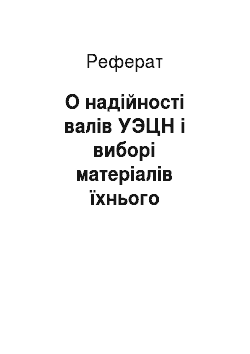
Более ніж дворічні поставки валів зі сталі ХМ-12 на ВАТ «НК „Роснафта“ — Пурнефтегаз», ВАТ «Ноябрьскнефтегаз» і ЗАТ «Новомет — Перм» показали високу надійність роботи заглибних помп з тими валами. Вали зі сталі ХМ-12 були встановлено на розробленої колективом ВАТ «НК „Роснафта“ — Пурнефтегаз» здвоєної модульної секції з функціями гідрозахисту і газосепаратора МС-ПГ-53 (патенти РФ № 23 908,44 729… Читати ще >
О надійності валів УЭЦН і виборі матеріалів їхнього виготовлення (реферат, курсова, диплом, контрольна)
О надійності валів УЭЦН і виборі матеріалів їхнього изготовления
В.Л. Александров Условия експлуатації установок відцентрових электронасосов (УЭЦН) в нафтових свердловинах пред’являють жорсткі вимоги до матеріалів, у тому числі виготовлені їх деталі, зокрема вал насоса. Аналітичні дослідження свідчать, що з його ненадійністю при експлуатації пов’язано понад 40 кримінальних % виходів із ладу всього агрегату [1]. Вал насоса піддається тривалого впливу крутящего моменту, зокрема імпульсного характеру, в агресивному кислотному середовищі з температурою більш 80 °З. Основним матеріалом для валів УЭЦН більш 20 років є нержавіюча сталь 03Х14Н7 В. Аналіз причин виходу з експлуатації валів показує, що їх недостатня надійність, особливо у свердловинах глибиною понад 2.000 м, обумовлена передусім неточністю вибору діаметра й не дуже високими експлуатаційними характеристиками стали 03Х14Н7 В у цих умовах. При статичному розрахунку міцність валу конструктори користуються відомої залежністю діаметра від краю плинності при кручении (як гранично припустимого напруги) і крутящего моменту після запровадження коефіцієнта запасу міцності для обліку втоми металу. Точність розрахунку залежить від правильності ухвали і використання тих параметрів і рівня невизначеності запасу прочности.
При виборі матеріалу для валів перевагу віддають почав із вищим межею витривалості по довідковим даним, у разі - за результатами випробувань стандартної агресивному кислотному середовищі. Реальна робоча середовище істотно відрізняється від стандартної многокомпонентностью — концентрацією у водному розчині солей, іонів хлору, розчиненої сірководню, кисню, величиною рН, наявністю нафтопродуктів, різними родовищах зазначені характеристики різні [2]. Тому запровадження коефіцієнта запасу міцності для обліку впливу втоми металу і агресивності робочої середовища Демшевського не дозволяє правильно вибрати діаметр і матеріал валу, оскільки малий запас міцності можуть призвести до недостатньою надійності валу при експлуатації і передчасному руйнації від коррозионной втоми чи імпульсної перевантаження, надлишок — до їх зниження економічних характеристик насоса, оскільки збільшення діаметра на 8−10% знижує к.п.д. насоса на 4−6% [3].
Надежность роботи валу можна підвищити, якщо розрахунку і випробуваннях матеріалу враховувати максимально наближені до експлуатаційним умови. З цього за виготовленні валів для ремонтних баз ВАТ «НК „Роснафта“ — Пурнефтегаз» і ВАТ «Ноябрьскнефтегаз» розробила методику визначення припустимого діаметра валу у кожному сечении і добору матеріалу щодо його виготовлення з єдиною метою забезпечення надійної роботи насоса. Виходили речей, що вплив навантаження на вал можна умовно розділити на два этапа:
— усталений режим роботи насоса, коли вал працює лише за умов коррозионной втоми при кручении;
— робота при імпульсних перегрузках.
На першому етапі надійність роботи матеріалу валу пропонується оцінювати з його межі витривалості, певному на зразках при кручении з урахуванням 107 циклів в температурно-коррозионных умовах робочої рідини. Цей параметр значно залежить від численних характеристик агресивності робочої рідини. Тому до накопичення необхідних довідкових матеріалів для дотримання умов моделювання робочих умов усталостные випробування слід здійснювати робочої рідини того родовища, котрій призначений насос. Межа витривалості значно менше краю плинності матеріалу, й у пружною області якого є напругою, нижче якого утворюються осередки пошкоджуваності. У зв’язку з відзначеним мінімальний діаметр валу, певний при розрахунку міцність межею витривалості матеріалу як у гранично допустимому напрузі, забезпечує надійність валу першому етапі праці та не вимагає необгрунтованих запасів прочности.
На першому етапі - при що встановилася режимі роботи насоса діючий крутний момент відповідає максимальної потужності насоса і розраховується в залежність від напору, подачі робочої рідини й снаги тертя в насосе'.
На другому етапі вал дбає про скручування та її діаметр пропонується визначати по гранично допустимому напрузі, за який обраний межа плинності матеріалу, певний під час випробування на крутіння, точніше, величина 0,9 тт, оскільки вал повинен працювати у пружною області напруг, а межа плинності відповідає початку пластичної деформації, рівної 0,3%. Імпульсний розрахунковий крутний момент може бути, по крайнього заходу, не нижче пускового моменту насоса Учитывая, що імпульсні перевантаження виникають як під час пуску, а й за засміченні робочої рідини частинками гірських порід, розмиванні пласта та інших подібних впливах, які можна подолані з допомогою надлишкового моменту сил пружності валу, імпульсний крутний момент розраховується за формуле Диаметр валу визначається по відповідним кожному за етапу роботи допускаемым напругам і крутящему моменту. У цьому задля встановлення припустимого діаметра выточек чи середнього діаметра шлицев мусить бути зроблено поправка на коефіцієнт чутливості до концентрації напруг у залежність від радіуса закруглений в выточках і шлицах та міцності матеріалу валу. Із двох мінімальних діаметрів, отриманих для усталостного навантаження при що встановилася режимі роботи насоса й у крутіння при імпульсної перевантаження крутящего моменту, вибирається більший та перевіряється коефіцієнт запасу міцності стосовно що допускаються напруг до розрахунковим кожному за етапу. У цьому обрані допущені напруги повинно перевищувати розрахункові будь-якому сечении вала.
Анализ кількох поломок валів з допомогою розробленої методики показує, що вал діаметром 17 мм зі сталі 03Х14Н7 В, має межа плинності при розтягненні 850 Н/мм2, за величиною дотичних напруг, які виникають за що встановилася режимі, в УЭЦН на глибині 2000 м працює на межі витривалості з коефіцієнтом запасу міцності трохи більше 3%. Імпульсні перевантаження крутящего моменту, пов’язані з пуском насоса, вал витримує по основному діаметру з коефіцієнтом запасу міцності проти допускаемым напругою 0,9 тт не понад п’ятнадцять % та практично не витримує, якщо врахувати концентрацію напруг в кінцевих шлицах. За невеликої імпульсної перевантаження проти межею плинності при кручении починається пластична деформація шлицев (скручування) з подальшим виходом валу з експлуатації. Отже, загальноприйнята методика розрахунку валу відповідає умовам експлуатації. Використання запропонованої методики дозволяє зробити висновок правильність обраного діаметра і матеріалу валу, і навіть про їхнє відповідність умовам експлуатації. Збільшувати діаметр валу зниження дотичних напруг від усталостного навантаження чи імпульсних перевантажень нераціонально. Однак точно можна використовуватиме валу більш міцну при кручении і усталостном нагружении коррозионно-стойкую сталь.
В час найбільш надійніші перспективні для валів УЭЦН нержавіючі высокопрочные стали мартенситно-аустенитного десь із класу високої в’язкістю руйнації та потенційної здатність до зміцнення завдяки виділенню дисперсних частинок, мають межа плинності при розтягненні 1,15 — 1,50 кН/мм2 і ударна в’язкість KCU+2O°C щонайменше 0,07 кН-м/см2. Мартенситно-аустенитная структура стали відповідає найбільшої в’язкості та міцності, оскільки пластини мартенситу в почав із змістом вуглецю менш 0,03% оточені тонкими прошарками грузького аустеніту, задерживающего розвиток зародкових тріщин. Мартенситная структура, особливо з виділеннями дисперсних частинок интерметаллидных чи надлишкових фаз під час термообробки стали, обумовлює її високу міцність. Таку структуру з різними співвідношенням мартенситу і аустеніту, і навіть різними елементами для зміцнення мартенситу мають стали серії ГМ американського стандарту ASTM, зокрема сталь ХМ-12, за вартістю відповідна стали 03Х14Н7 В. Порівняльні даних про властивості сталей 03Х14Н7 В і ХМ-12 наведено малюнку.
Предел плинності при розтягненні стали ХМ-12 залежно від режиму термообробки і її хімічного складу не більше марочного їх може становити 1,15−1,30 кН/мм2, тобто. на 40−60% вище, ніж стали 03Х14Н7 В, при ударної в’язкості 0,08−0,12 кН-м/см2. При кручении межа витривалості і межа плинності при кручении відповідно на 30 і 38% вище, ніж в стали 03Х14Н7 В.
Более ніж дворічні поставки валів зі сталі ХМ-12 на ВАТ «НК „Роснафта“ — Пурнефтегаз», ВАТ «Ноябрьскнефтегаз» і ЗАТ «Новомет — Перм» показали високу надійність роботи заглибних помп з тими валами. Вали зі сталі ХМ-12 були встановлено на розробленої колективом ВАТ «НК „Роснафта“ — Пурнефтегаз» здвоєної модульної секції з функціями гідрозахисту і газосепаратора МС-ПГ-53 (патенти РФ № 23 908,44729, 2 221 322), виробництво якої освоєно ТОВ «Каурі» по ліцензійному договору використання винаходи. Модульна секція адаптована до насосам американської фірми «Центрилифт» і вітчизняним насосам, зібрано однією валу, що виключає фланцевое з'єднання і передачу обертання шлицевой муфтою. Виняток із конструкції системи цих двох чинників зменшує вібрацію, передану від вузла газосепаратора до насмокчу. Використання стали ХМ-12 як матеріалу валу модульної секції підвищує її надійність в эксплуатации.
Таким чином, розроблена методика дозволяє вибрати матеріал виготовлення валу, відповідний умовам експлуатації, й точніше визначити її припустимий діаметр у кожному сечении без запровадження необгрунтованих запасів міцності. Через війну може бути підвищено термін їхньої служби валу, надійність роботи насоса та її к.п.д. Пріоритет методики встановлено заявкою отримання патенту РФ.
Список литературы
1. Кудряшов СІ. Підвищення надійності заглибних систем УЭЦН з прикладу досвіду експлуатацію у ВАТ «Юганскнефтегаза/Нефтяное господарство. — 2005. — № 6. — З. 126−127.
2. Перекуповування О. Г., Семенов У. М., Павлов П. В. Розрахунок коефіцієнта коррозионной активності середовища під час проектування промислових трубопроводів Нафтова господарство. — 2005. -№ 6.-С. 130−131.
3. Розрахунок і конструювання нафтопромислового оборудования/Л.Г. Чичеров, Г. В. Молчанов, A.M. Рабинович та інших. — М.: Надра, 1987.-146 с.
4. Михайлов О. К., Малашенко В. В. Конструкції і розрахунок відцентрових насосів високого тиску. — М.: Машинобудування, 1971. — 223 с.
Журнал «Нафтове господарство» № 5, 2006.