Создание як дослідження шпаклювальних паст з урахуванням УПС і АВС
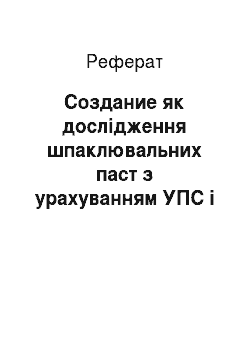
Блочно-суспензионный процес проводять за періодичної схемою у двох апаратах, наділених мешалками і сорочками. У першому розчиняють каучук в стиролі і паралельно ведуть полімеризацію у своїй до ступеня перетворення стиролу 30—40%, як описано вище. Упродовж цього терміну повністю закінчується інверсія фаз, й частки дискретної фази ущільнюються і підлітків набувають опірність коалесценции… Читати ще >
Создание як дослідження шпаклювальних паст з урахуванням УПС і АВС (реферат, курсова, диплом, контрольна)
РЕФЕРАТ.
Ця навчально-дослідницька робота містить 28 сторінок, 1 малюнок, 8 таблиц.
СТИРОЛ, ПОЛІЕФІРНІ СМОЛИ, ПОЛІСТИРОЛ, ЛИСТЯ, ДИМЕТИЛАНИЛИН, ПЕРЕКИС БЕНЗОИЛА, ІНІЦІАТОР, ПРИСКОРЮВАЧ, ШПАКЛЁВКА, ЗАПОВНЮВАЧ, ОТВЕРДИТЕЛЬ.
Метою згаданої роботи є підставою розробка шпаклевочной композиції з урахуванням ненасиченої полиэфирной смоли ПН — 1. Робота містить аналітичні і патентні дослідження; опис матеріалів і методик досліджень; заключение.
Області застосування пластичних мас в народному господарстві дуже різні: товари народного споживання, деталі машинобудування, приладобудування, радіо — і телеапаратури тощо. Часто пластмаси використовують як самостійний конструкционный материал.
Останніми десятиліттями переробка пластмас в вироби інтенсивно розвивається у хімічної промисловості, а й у інших галузях народного господарства. Створюються нові композиції матеріалів, вдосконалюються методи їхньої організації переработки.
РЕФЕРАТ 3.
ЗАПРОВАДЖЕННЯ 4.
1.АНАЛИТИЧЕСКИЕ І ПАТЕНТНІ ДОСЛІДЖЕННЯ 6.
1.1. Аналітичний огляд 6.
1.1.1. Шпатлевки 6.
1.1.2. Хімічні методи підготовки поверхні 8.
1.1.2.1. Знежирення 8.
1.2. Патентна проробка 10.
2. МАТЕРІАЛИ І МЕТОДИКА ДОСЛІДЖЕНЬ 13.
2.1 Матеріали, використовувані у роботі та його характеристика 13.
2.1.1. Стірол 13.
2.1.2. Сополимеры стиролу 14.
2.2. Ненасичені полиэфиры. 19.
2.2.1. Полималеинаты і полифумараты 20.
2.2.1. Властивості полиэфирной смоли ПН — 1 21.
2.3. Методика дослідження. 21.
3. ЕКСПЕРИМЕНТАЛЬНА ЧАСТИНА. 23.
3.1. Методи отримання зразків і аналіз отриманих результатів. 23.
3.1.1 Вивчення кінетики полімеризації. 23.
3.1.2 Склад 1 23.
3.1.3 Склад 2 25.
3.1.4 Склад 3 26.
3.1.5 Склад 4 27.
4. ВИСНОВОК 29.
СПИСОК ВИКОРИСТАНИХ ИСТОЧНИКОВ 30.
1.АНАЛИТИЧЕСКИЕ І ПАТЕНТНІ ИССЛЕДОВАНИЯ.
1.1. Аналітичний обзор
1.1.1. Шпатлевки.
Шпатлевки, шпаклівки (Surfacers, Spachtelmassen, enduits de Surface)-лакокрасочные матеріали, застосовувані вирівнювання (шпатлевания) окрашиваемой поверхні перед нанесенням її у покривних верств. Крім пленкообразующих речовин, шпатлевки містять наповнювачі і розчинники; до складу можуть також входити пігменти, пластифікатори, отвердители та інших. Розрізняють лаковые, масляні і клейові шпатлевки, одержувані відповідно з урахуванням лаків, олиф, водних розчинів природних клеїв. Як наповнювачів в Ш. використовується крейда, тальк, каолін, барит та інших.; у складі шпатлевок для термостойких покриттів вводять микрослюду, микроасбест. Для пигментирования шпатлевок застосовують цинкові білило, литопан, і навіть дешеві природні кольорові пігменти — охру, мумію і др.
Від ін. пигментированных лакофарбових матеріалів (грунтівок, фарб) Ш. відрізняються великим змістом сухого залишку (до 80%), і навіть значно більше високим ставленням кількості наповнювачів і пігментів до пленкообразующему (зазвичай від 5:1 до 12:1).
Отримують шпатлевки як і фарби, — диспергированием (перетиром) наповнювачів і пігментів у відповідній сполучному. Шпатлевки завдають на поверхню спеціальної лопаткой-шпателем (дерев'яним, металевим або з пластмаси) чи товстим шматком гуми. При розведенні невеликою кількістю розчинника є підстави завдані розпиленням з допомогою краскораспылителя з діаметром сопла 2,5 мм. Або поливом. Зазвичай шпатлевки завдають по грунтовочному прошарку, бо з причин меншого змісту пленкообразующего воно поступаються грунтовкам по адгезионным властивостями. Деякі шпатлевки з урахуванням алкідних чи эпоксидных смол, і навіть Si-органических смол, містять добавку алкидной, мають досить хорошою адгезией до металам і може бути завдані безпосередньо на окрашиваемую поверхню; такі шпатлевки називаються грунтшпатлевками.
Товщина покриттів, які виникають під час шпатлевок (зазвичай до 300мкм.), значно більше, ніж у випадку нанесення грунтівок чи фарб. Отже, пленкообразование шпатлевок супроводжується більшої усадкой. Товщина верств найбільш высоконаполненных шпатлевок (про квач), що застосовуються заповнення отворів, вибоїн, щілин, може становити 1 мм. Ці шпатлевки завдають зазвичай, у кілька прийомів (з проміжної сушінням), бо за нерівномірному высыхании.
товстого шару покриття, можливо його розтріскування. Шпатлевки повинні утворювати рівний шар, він сторонніх включень, подряпин та інших. видимих дефектів. Висохлий шар шпатлевки може бути доречний під час шлифования абразивною шкуркою. Лаковые шпатлевки застосовують головним чином машинобудуванні; клейові і масляні - переважно у будівництві. /1/.
Таблиця 1.1.
Характеристика лакових шпатлевок.
Заповнення Режими сушіння (отверждения) Окрашиваемые поверхности.
Температура, ?З Тривалість, год.
1 2 3 4.
Алкидная (завдають розпиленням) 18−2380 241 Загрунтовані металеві і деревянные.
Алкидная (завдають розпиленням) 135−145 0.5 Незагрунтованные і загрунтовані металлические.
Алкидно-стирольная (те) 18−23 2 Загрунтовані металеві і дерев’яні (виправлення металевих дефектов).
Поліефірна (завдають розпиленням чи поливом) 18−2360 101 Загрунтовані дерев’яні щити для меблів, деталі музичних инструментов.
Поліефірна (те) 5070 20.-2.51.5 Незагрунтованная фанера, древесно-стружечные плиты.
Нитроцеллюлозная 18−23 2,0−2,5 Загрунтовані деревянные.
Перхлорвиниловая 18−23 2,0−2,5 Загрунтовані металеві і дерев’яні, оштукатурені фасади зданий.
Продовження таблиці 1.5.
1 2 3 4.
Si-органическая 200−210 3 Стеклопластик.
Si-органическая 18−2390−100 481−2 Незагрунтованные металеві, котрі піддаються короткочасному нагріванню до 700°.
Эпоксидная 80−85 1 Стеклопластик.
Эпоксидная 18−2365−70 247 Загрунтовані і незагрунтованные металлические.
1.1.2. Хімічні методи підготовки поверхности.
Підготовка поверхні хімічними методами залежить від її обробці водними розчинами кислот, лугів, солей і комплексних сполук, і навіть органічними растворителями.
Застосування хімічних методів підготовки дозволяє забезпечити високу адгезію покриттів до полімерним матеріалам внаслідок видалення зі своїми поверхні забруднень знежиренням і цього підвищення ступеня шорсткості поверхні (травлення), і навіть модифицирования.
Хімічні методи обробки водними розчинами найчастіше використовують із підготовки поверхні перед хімічної металізацією. Перед нанесенням лакофарбових матеріалів поверхню обезжиривают з допомогою органічних розчинників; використання у цьому випадку водних розчинів небажано, оскільки вимагає додаткових операцій нейтралізації, промивання і сушки./3/.
1.1.2.1. Обезжиривание.
Знежирення — процес обробки поверхонь з єдиною метою видалення жирових та інших забруднень (отвердитель эпоксидных смол, восків, застосовуваних при пресуванні реактопластов; пластифікаторів для вальцевания матеріалів, кремнійорганічних рідин, використовуваних як розділювальних мастил при лиття під тиском), сильно погіршують адгезію покриттів до та його декоративні властивості. Забруднення розподіляються лежить на поверхні нерівномірно; іноді їх важко помітити визуально.
Знежирення виробляють із допомогою органічних розчинників чи водних розчинів лугів у присутності эмульгаторов.
Знежирення органічними розчинниками. Для знежирення застосовують розчинники, добре що розчиняють забруднення, але інертні стосовно пластмасі, тобто які викликають її набрякання чи розчинення. Бажано, щоб розчинники швидко зникали, були токсичними і пожежобезпечними. На жаль більшість розчинників горючи і вибухонебезпечні, крім хлорованих і фторированных вуглеводнів, які проте мають підвищену токсичностью.
За дотримання предельно-допустимых концентрацій навіть токсичні розчинники, такі, наприклад, як трихлорэтилен, можна використовувати для знежирення деяких полімерних матеріалів (поліолефінів, поликарбонатов, полістиролу, поливинилхлорида).
Для видалення розділювальних мастил, які з суміші спирту з гліцерином, касторової олії чи стеарата цинку, застосовують суміш розчинників (% об.):
Таблиця 1.2.
Суміш растворителей.
Етанол 50 Бутанол 15.
Этилацетат 25 Целлозольв 10.
Кремнийорганические розділювальні мастила видаляють промиванням виробів на 2% - ном розчині карбонату калію в спирті з добавкою невеликої кількості змочувального речовини. З метою знежирення вироби протирають чистими серветками, змоченими розчинниками, занурююється у ванну з негорючими розчинниками (наприклад, трихлорэтиленом) чи піддають обробці методом струйного розпорошення з форсунок. Дрібні деталі обробляють в барабанах. Тривалість знежирення в ваннах і барабанах може бути зменшена під час використання ультразвука./3/.
Лужне знежирення застосовують на підготовку пластмас, виготовлених з урахуванням полімерів, стійких до щелочам. Лужне знежирення не можна застосовувати в обробці фенопластов і склопластиків. Луги сприяють перетворенню рослинних і тварин жирів і воску в водорозчинні мила і эмульгируют мінеральні олії. Для прискорення емульгування й відокремлення від поверхні твердих забруднень в лужні склади додають неіоногенні емульгатори, зазвичай оксиэтилированные алкилфенолы (ОП-7, ОП-10)*. Вони зручні тим, що ні утворюють піни і добре змиваються із поверхні пластмассы.
Для знежирення з допомогою лугів рекомендується використовувати солі лужних металів — тринатрийфосфат, карбонат натрію (соду), щоб забезпечити сталість pH розчину. Ефективність знежирення збільшується на підвищення температури розчину до 60−80?С, бо за подальше підвищення температури ефективність змінюється незначительно.
Режими знежирення пластмас лужними розчинами різних складів наведені у таблиці 1.7.
Таблиця 1.3.
Поїзди (г/л) і режими знежирення пластмас лужними растворами.
Поїзди, N Фосфат натрію Карбонат натрію Гидроокись натрію Емульгатор Режим обезжиривания.
ОП-7 ОП-10 Некаль Контакт Петрова Анионо-активное речовина мило Температу-ра,?С Тривалість, мин.
1 — - - - 10 — - - - 18−22 1−10.
2 20 — - - - 20 — - - 30−40 5.
3 — 10 — - 3 — - - - 60−70 10.
4 20 20 — - 3 — - - - 60 15.
5 30 — 80 — 2 — 40 — - 70−80 2−3.
6 19 — - 2,5 — - - - - 18−22 2−3.
7 — 2 — - 2** - - 2** - 80−90 20−30.
8 — 2 — - - - - - - 70−80 30−60.
9 — - - - - - - - 2 40 85−20.
*Замість гідроокису натрію можна використовувати 25%-ный розчин гідроокису аммония.
**До складу N7 можна вводити лише з зазначених эмульгаторов.
Примітка. Лужні розчини складу N6 застосовують для знежирення полівінілхлориду; N7 — полиамидов; N8 — поліолефінів; N9 — полиэфиров.
Там, коли застосування лужних розчинів недостатньо, для знежирення можна використовувати водні розчини емульгаторів, наприклад ОП-7 чи ОП-10 (склад N1). Знежирення водними розчинами проводитися окунанием чи розпиленням (в ваннах, струменевих камерах і барабанах).
Після закінчення лужного знежирення поверхню старанно промивають гарячої водой./3/.
1.2. Патентна проработка.
Ведеться велика кількість досліджень у сфері створення нових композицій з урахуванням сополимеров стирола.
Наприклад, у роботі /1/ розроблено композиції з гетерогенної пошарово — неоднорідною структурою з урахуванням эпоксидной смоли ЕД — 20, полістиролу і двох розчинників для захисних покриттів від корозії. Досліджено ступінь розшарування покриття залежно від летючості розчинника, товщини шару, температури та інших кінетичних факторов.
У /2/ патенті представлені нові розробки у сфері технології блокових стирольных сополимеров (СПЛ) структури стирол — бутадиен / изопрен — стирол для теплостійких чутливих до тиску клеїв. Це досягається гидрированием розміщених у середині блоків полидиена. Описано умови гидрирования СПЛ. Зроблено з порівняльного аналізу властивостей чутливих до тиску клеїв з урахуванням гидрированных СПЛ і СПЛ традиційної структуры.
У американському патенті /3/ описані чутливі до тиску клеї - розплави з мінімальним окрашиванием містять (%): 5 — 30 сополимеров з кінцевими стирольными блоками і серединними этиленбутиленовыми чи этиленпропиленовыми блоками (зміст диблоксополимеров >35%, ступінь зшивки 20 г/10 хв, зміст стирольных ланок 10 — 30%), 5 — 50 сополимеров з кінцевими стирольными блоками при ступеня зшивки 65 — 100%, 10 — 40 рідких пластифицирующих олій і 20 — 60 полімерних добавок збільшення клейкості. Міцність при отслаивании з точки 180? клейового шару з клею — расплава.
У патенті /4/ описано застосування антиаксидантов в клеї з урахуванням сополимера стиролу. Щоб запобігти фарбування защищаемой липкими стрічками ПВ в клейовою шар по основі блок — сополимера стиролу (стирол — бутадиен — изопрен) вводять антиоксиданти (стерически утруднені одне — і многоядерные феноли, містять в про — і/або п — прикінцевих положеннях до ВІН — групі бензилтиоэфирные групи і/або фенилэфиракрилатные групи [4,6 — бис (октилтиометил) — про — крезол, 2 — тре — бутил — 6 — (3 — тре — бутил — 2 — ВІН — 5 — метилбензил) — 4 — метоксифенилакрилат тощо. п.] чи стерически утруднені лактоны).
У патенті /5/ описаний клей з урахуванням блок — СПЛ стиролу. Зазначені смужки для склеювання із можливістю расклеивания без руйнації та забруднення субстрату містять клей з урахуванням блок — сополимера стиролу і 30−60% эластомеров, модифікованих кислотою і / чи ангідридами (переважно малеиновыми) клейова маса може містити та інші добавки, наприклад, що б клейкість, і навіть пластифікатори і наполнители.
У наступних трьох патентів /6/ /7/ /8/ розглянута рецептура герметизирующего состава.
Герметизирующий склад /9/ використовують із герметизації і ущільнення будівельних конструкцій, і навіть для приклеювання всіх видів плиток, лінолеуму, дерева, металів, гум. Сутність винаходи: склад містить мас. год.: бутадиенстирольный термоэластопласт, наповнений полистиролом, із вмістом останнього 3−80 мас. %, 30−70; сополимер бутадієну і стиролу із вмістом пов’язаного стиролу 60−65 мас. %, блокового стиролу 30−34 мас. % 30−70; адгезив 10−40; заповнювач 40−70; тиксотропная добавка 3.0−5.0; антиоксидант 0.5−1.5; розчинник 240−300.
Герметизирующая композиція /10/ використовується для герметизації і ущільнення будівельних конструкцій і приклеювання будівельної плитки, лінолеуму, дерева, металів, гум. Сутність: композиція включає, мас. год.: бутадиен-стирольный термоэластопласт, наповнений полистиролом із вмістом яке наповнювало полістиролу 3−80 мас. % чи бутадиен-стирольный термоэластопласт розгалуженого будівлі із вмістом пов’язаного стиролу 27−31 мас. % - 1000; адгезив 10.0−30.0; заповнювач — 40−70; тиксотропная добавка 3.0−8.0; антиоксидант — 0.5−1.5; сополимер изопрена (бутадієну) зі стиролом лінійного будівлі чи звездообразного будівлі 10−30; органічний розчинник 260−310.
Герметик /11/ використовують із герметизації і ущільнення будівельних конструкцій, приклеювання всіх видів плитки, лінолеуму, дерева, металів, гуми. Сутність: герметик включає, мас. год. бутадиенстирольный термоэластопласт, наповнений полистиролом із вмістом яке наповнювало полістиролу 3−80 мас. % 100, адгезив 10.0−40.0; заповнювач 40.0−70.0; тиксотропные добавки 3.0−5.0; антиоксидант 0.5−1.5; органічний розчинник 260.0−340.0.
Діяльність /12/ запропоновані клеи-расплавы багатоцільового призначення утворюють залежно від основного блоксополимера (БСПЛ) жорсткі чи еластичні клейові сполуки, містять (%) 15−35 БСПЛ структури ПССПЛ бутадієну і стиролу ПС (в'язкість 25%-го розчину в толуоле >1000 сП, зміст блоків СПЛ < 35%), 2−30 полімерів, блокуючих кінцеві групи БСПЛ, 30−70 добавки підвищення клейкості, 0−30 олій і 0−3 антиоксиданта.>
2. МАТЕРІАЛИ І МЕТОДИКА ИССЛЕДОВАНИЙ.
2.1 Матеріали, використовувані у роботі та його характеристика.
2.1.1. Стирол.
Стірол (винилбензол, фенилэтилен), С6Н5СН = СН2 — безбарвна рідина зі своєрідним запахом. Нижче наведені деякі фізичні властивості стирола:
Таблиця 2.1.
Фізичні властивості стирола.
Щільність при 20? С, г/см3 0,9060.
Температура, ?С.
плавлення — 30,628.
кипіння 145,2.
спалахи 34.
Показник заломлення 1,5468.
Критич. тиск, Мн/м2 (кгс/см2) 4 (40).
Критич. температура, °З 373.
Критич. обсяг, см3/г 3,55.
В’язкість при 20° С, мн? сек/м2, чи cпз 0,781.
Тиск парів при 20? С, н/м2 (мм рт. ст.) 652 (4,9).
Задовільно. теплоємність, кдж/(кг?К) [кал/(г?°С)].
рідина при 20? С 1,695 (0,4039).
пар при 25 °C 1,183 (0,2818).
Поверхове натяг при 20° С, мп/м, чи дин/см 32,2.
Темп-рный коэфф. об'ємного розширення при 25 °C, ?С-1 9,719?10−4.
Теплота освіти (рідина) при 25 °C, кдж/кг (кал/г) 147,6 (35,22).
Теплота полімеризації (жидк-жидк.), кдж/кг (кал/г) 716 (171).
Теплота випаровування при 140 °C, кдж/кг (кал/г) 368 (87,7).
Стірол змішується із більшістю органич. розчинників, наприклад, з нижчими спиртами, ацетоном, ефіром, сероуглеродом; в.
багатоатомних спиртах розчинний обмежено. Розчинність стиролу у питній воді 0,032% (щодо маси) при 25 °C, води в стиролі 0,070%. У суміші з повітрям в об'ємних концентраціях 1,1—6,1% утворює вибухонебезпечні суміші. Стірол легко полимеризуется і сополимеризуется з большинством.
мономерів по радикальному і ионному механізмам. На повітрі стирол окислюється із заснуванням перекисів, ініціюючих полімеризацію стиролу, бензальдегида і формальдегида.
Кількісно стирол визначають приєднанням оцтовокислою ртуті до вінілової зв’язки й з наступним титруванням ртуті в продукті приєднання розчином роданистого аммония.
Основний метод отримання стиролу— каталітичне дегидрирование этилбензола, одержуваного каталітичним (А1С13, BF.,) жидкофазным алкилированием бензолу этиленом в м’яких умовах. Дегидрирование проводять у струмі водяної пари при 500—630°С на окисных катализаторах (железо-магниевых чи хромо-цинковых) в реакторах різних типів — адиабатическом з нерухомим шаром каталізатора, трубчатом изотермическом чи секційному. Вихід стиролу більш 90% від теоретичного. Задля чистоти стиролу від этилбензола, бензолу і толуолу застосовують четырехступенчатую ректифікацію під вакуумом.
Менш поширений синтез стиролу з одночасним отриманням окису пропилену (окислювання этилбензола в гидроперекись, реакція з пропиленом у присутності нафтената молібдену, дегидратация що утворюється метилфенилкарбинола). У Японії розроблений економічний процес экстрактивной ректифікації стиролу, що утворюється при піролізі бензину на етилен; ректифікації піддають фракцію, що містить до 35%С.
Технічний стирол містить 99,6—99,8% основного продукту, і навіть етилбензол, изопропилбензол, сірку, перекису, альдегиды.
Стірол інертний стосовно конструкційним матеріалам крім міді її сплавів, які розчиняються в стиролі і забарвлюють його. При зберіганні у стиролі накопичується розчинений полімер і перекису. Якісно полімер визначають осадженням великим надлишком сухого метанолу (10 мл СН3ОН на 1—2 мл стиролу). Помутніння розчину при сильному струшуванні свідчить про присутність полімеру. Стірол зазвичай інгібірують третбутилпирокатехином. Інгібітори видаляють перегонкою мономера в вакуумі чи промиванням розведеною лугом (після чого мономер старанно висушують). Транспортують стирол в сталевих цистернах. Зберігають у сталевих ємностях під азотної подушкой.
Припустима концентрація стиролу повітря не вище 0,5 мг/м3. Запах стиролу відчувається за більш низьких концентраціях. Підвищені концентрації стиролу викликають сльозотеча, тривале вдихання його парів негативно діє функцію печени./27/.
2.1.2. Сополимеры стирола.
Стірол легко сополимеризуется із більшістю вінілових сомономеров «див. табл. 2.2».
Таблиця 2.2.
Константи сополимеризации стиролу (r1) з декотрими сомономерами (r2).
Сомономер r1 r2 Температура, ?З Метод сополимеризации.
Акрилонитрил 0,4 0,04 60 Радикальна в массе.
Акрилонитрил 0,3 0,02 50 Аніонна в р-ре.
Акриловая кислота 0,15 0,25 60 Радикальна в массе.
Бутадиен 0,5 1,4 50 Радикальна в эмульсии.
Бутадиен 0,05 20 50 Аніонна в р-ре.
Бутилакрилат 0,76 0,15 60 Радикальна в массе.
Винилацетат 50 0,01 60 «Те же».
Дивинилбензол 0,65 0,60 60 ««.
Малеиновый ангідрид 0,02 0,0 60 ««.
Метилакрилат 0,75 0,18 60 ««.
Метилметакрилат 0,54 0,49 60 ««.
?-Метилстирол 1,18 0,36 50 ««.
?-Метилстирол 0,05 2,90 0 Катионная в р-ре.
Таким шляхом вдасться одержати матеріали, які характеризуються вищими теплостойкостью, опором удару, стійкістю до дії розчинників, ніж полістирол загального призначення, й те водночас зберігають характерні для полістиролу свойства—твердость, формоустойчивость, приємний зовнішній вигляд і легкість переробки. У ми-ровом виробництві полистирольных пластиків, які включають полістирол, пінополістирол і сополимеры, містять понад 50 відсотків% стиролу, питому вагу ударопрочного сополимера стиролу з каучуком становить близько 45%, сополимера стиролу, — акрилонитрил — каучук (АБС-пластик) — 15 — 20%, інших сополимеров стиролу— 3—5%.
Ударопрочные сополимеры стиролу (ударопрочный полістирол) — група композиційних матеріалів з урахуванням стиролу і каучука.
Властивості й структура. Ударопрочный полістирол— твердий непрозорий продукт білого кольору. Вона має двухфазную структуру «див. рис. 2.1»: безперервна фаза (матриця) освічена полистиролом, дискретна (микрогель) — овальної форми частинками розміром 1—5 мкм. оточеними тонкої плівкою щепленого сополимера стиролу— каучук; всередині частинок міститься окклюдированный полістирол. Матеріал має властивостями термопласта і зберігає свою структуру в розплаві; при переробці частки дискретної фази (микрогеля) орієнтуються у бік докладання напруги сдвига.
Микрогель можна відокремити від матриці шляхом розчинення полістиролу у належному розчиннику і центрифугування нерозчинною фази. Микрогель має властивостями блоксополимера полістиролу — каучук, наприклад, має дві температури стеклования, характерні кожному за гомополимера. У той самий короткий час він частково зшитий і розчиняється в жодному розчиннику, хоча й дуже набухає. Крім микрогеля, деякі сорти ударопрочного полістиролу містять частки щепленого розчинної сополимера стиролу— каучук. Зазвичай зміст каучуку враховуючи вихідну суміш становить від 3 до 12%. Через війну щеплення полистирольных ланцюгів на каучук і окклюзии при освіті микрогеля обсяг дискретної фази в готовому матеріалі зростає у 3—4 разу проти обсягом каучуку і як 10—40% від загального обсягу. Властивості готовий матеріал багато чому визначаються саме обсягом микрогеля.
При температуpax вище 230 °C і великих напругах зсуву частки микрогеля можуть бути зруйновані; у своїй механічні властивості ударопрочного полістиролу різко ухудшаются.
При однаковому змісті каучуку ударна міцність ударопрочного полістиролу в 5—10 разів більше, ніж суміші полістиролу з каучуком. Це пов’язано з більшої однорідністю дискретної фази, збільшенням її обсягу результаті окклюзии полістиролу Прищеплену сополимер стиролу — каучук діє і як ефективний стабілізатор твердої емульсії полімерполімер (яку має готовий продукт), підвищуючи адгезію микрогеля до матричному полистиролу.
При однаковому змісті вихідного каучуку обсяг мпкрогеля в ударопрочном полистироле можна змінювати, варіюючи умови отримання матеріалу. При збільшенні змісту микрогеля ударна в’язкість і відносне подовження досягають максимуму (при змісті 20 — 30%), міцність при розтягненні знижується, модуль пружності зростає. Прочностные властивості залежать також від молекулярної є і молекулярно-массового розподілу (ММР) матричного полістиролу, від розміру частинок микрогеля, ступеня щеплення і рівня зшивання частинок микрогеля. Молекулярні характеристики матриці впливають на властивості матеріалу як і, як і властивості полістиролу. При синтезі ударопрочного полістиролу молекулярна маса матриці має бути меншою молекулярної маси полістиролу загального призначення, одержуваного у своїй (цієї мети вводят.
Рис 2.1 Структура ударопрочного полистирола.
регулятори молекулярної маси), щоб компенсувати збільшення в’язкості розплаву ударопрочного полістиролу через наявність микрогеля [для матриці зазвичай Mw = (200−270}?103, Мn=(70−100)-103]. Через війну в’язкість розплаву ударопрочного полістиролу мало відрізняється від в’язкості полістиролу загального призначення. Оптимальний розмір частинок микрогеля 1−5 мкм. Відхилення від результатів цих розмірів, і навіть неоднорідність за величиною призводять до зниження прочностных властивостей материала.
Є кілька гіпотез, пояснюють збільшення ударної міцності тендітного полістиролу при освіті дискретної фази. За однією з них частки микрогеля здатні знижувати концентрацію напруг, виникаючих на кінці тріщини, зростання під впливом ударної навантаження. Збільшення частки щепленого сополимера підвищує ударну міцність матеріалу; на підвищення ступеня зшивання (наприклад, під час введення вулканизующего агента) збільшується модуль пружності і знижуються ударна в’язкість і відносне подовження. Нижче наведені деякі властивості литьевых зразків ударопрочного ПС:
Таблиця 2.3.
Властивості литьевых зразків ударопрочного ПС.
Властивість Значение.
Щільність при 20° С, г/см3 1,05−1,08.
Міцність при розтягненні, Мн/м2 (кгс/см2) 30−45 (300−450).
Модуль пружності, Гн/м2 [кгс/см2] 2−2,5 [(20−25)?103].
Ударне в’язкість, кдж/м2, чи кгс? см/см2.
без надрізи 35−70.
з надрізом 7−15.
Теплостойкость по Мартенсу, °З 65−74.
Твердість при Бринеллю, Мн/м2 (кгс/мм2) 100−150 (10−15).
Відносне подовження, %… 15−40.
Электрич. властивості ударопрочного полістиролу таку ж, як в полистирола.
З упровадженням каучуку знижується стійкість до окислювання і УФ-излучению через наявність непредельных зв’язків; матеріал стабілізують запровадженням антиоксидантів фенольного типу, двоокису титана.
Одержання. Для отримання ударопрочного полістиролу найбільшого поширення отримали полімеризація у своїй так званий блочно-суспензионный метод.
У першому випадку бутадиеновый чи бутадненстирольный каучук подрібнюють на дробарці і за кімнатної температурі розчиняють в стиролі, вводять регулятори молекулярної маси (димера ?-метилстирола, меркаптани), стабілізатори (полигард) для каучуку. Зміст каучуку в розчині їх може становити 4—15%. При нагріванні розчину і (чи) запровадження ініціаторів (наприклад, перекису бензоила) паралельно протікають 2 процесу — гомополимеризация стиролу і щеплення стиролу на каучук.
Щеплення на каучук відбувається внаслідок відриву радикалами, утвореними під час розпаду ініціатора, чи радикалами стиролу рухливих атомів водню від метиленової групи молекули каучуку, що у ?-становищі стосовно подвійний зв’язку. Середня довжина щеплених полистирольных ланцюгів та його ММР близькі до відповідним параметрами полістиролу. Подвійні зв’язку каучуку цьому етапі мало расходуются.
Реакційна система залишається гомогенної до накопичення у ній 2—3% полістиролу. По термодинамічним причин здебільшого два полімеру несумісні загалом розчиннику (ефект Добри) і расслаиваются, створюючи дві фази. Кожна фаза є розчин відповідного полімеру загалом розчиннику та практично зовсім позбавлений іншого полімеру. Дискретну фазу в цій стадії процесу утворює розчин полістиролу в стиролі, безперервну фазу — розчин каучуку і щепленого сополимера в стиролі. При підвищенні змісту полістиролу в реакційної системі настає момент, коли обсяги фаз стають приблизно рівними. Відбувається інверсія фаз, після якого дискретну фазу утворює розчин каучуку і щепленого сополимера в стиролі, а безперервну — розчин полістиролу в стиролі. Оскільки в’язкість каучуковою фази набагато вища в’язкості полистирольной, а в’язкість реакційної системи визначається основному в’язкістю безупинної фази, то інверсія фаз супроводжується стрибкоподібним зниженням в’язкості системы.
Через високої в’язкості інверсія утруднена і протікає остаточно лише за інтенсивному перемішуванні. Розмір і форма частинок каучуковою фази залежить від геометрії судини і мішалки, швидкості зсуву, концентрації та молекулярної маси каучуку, молекулярної маси полістиролу, кількості що утворився сополимера. При інверсії що настає дискретна фаза захоплює (окклюдирует) певна кількість полістиролу. При ступеня перетворення стиролу 30—40% двухфазная система стає стійкою, і величину дискретних частинок перестає залежати та умовами перемішування. Отже, структура ударопрочного полістиролу формується на стадії інверсії фаз.
Наприкінці процесу, коли зміст стиролу значно зменшується, відбувається часткове зшивання дискретної фази, набирає структуру зшитого микрогеля. І на цій стадії продукт є розплав ударопрочного полістиролу, що містить небагато непрореагировавшего стиролу (0,5—10%).
У техніці процес здійснюють по безупинної схемою аналогічно полімеризації стиролу. Часто ще плавної регулювання температурного режиму (в завершальній стадії) сополимеризацию ведуть у присутності розчинника — толуолу, этилбензола (10—30% від безлічі реакційної середовища). Режим процесу розраховують в такий спосіб, щоб інверсія фаз повністю протікала щодо одного апараті при контрольованих умовах перемішування. На наступних стадіях важливо, щоб структура дискретної фази не зруйнувалася через зависоких швидкостей зсуву чи високої температури. Непрореагировавший стирол і розчинник видаляють в вакуум-камере чи вакуум-шнек машині. Продукт гранулируют.
Блочно-суспензионный процес проводять за періодичної схемою у двох апаратах, наділених мешалками і сорочками. У першому розчиняють каучук в стиролі і паралельно ведуть полімеризацію у своїй до ступеня перетворення стиролу 30—40%, як описано вище. Упродовж цього терміну повністю закінчується інверсія фаз, й частки дискретної фази ущільнюються і підлітків набувають опірність коалесценции (слипанию); реакційну систему годі й перемішувати. Під тиском інертного газу її передавливают на другий апарат, у якому деминерализованную води і стабілізатори суспензії, і запроваджують додаткову кількість ініціатора. Реакційну масу суспендируют у питній воді при інтенсивному перемішуванні, та інформаційний процес ведуть при 95 — 120оС під тиском до граничною ступеня припинення стиролу. Ударопрочный полістирол, у якому 0,1% З., відділяють від води та обробляють як продукт суспензионной полимеризации.
Оскільки вартість каучуку приблизно 3—4 разу вищу, ніж полістирол, а збільшення змісту каучуку призводить до зниження міцності при розтягненні, модуля пружності і атмосферостойкости композиційної матеріалу, доцільно домагатися найбільшого ефекту зміцнення за мінімальної змісті каучука.
Щеплення стиролу для цієї эластомеры протікає значно складніше. Застосовують спеціальні методи — химнческую модифікацію эластомера, додають сшивающие агенти. І все-таки продукти мають порівняно дешевше ударної міцністю, ніж сополимеры з урахуванням каучуку. Прозорий гетерогенний матеріал можна отримати роботу, зменшуючи розмір частинок дискретної фази до значення, меншого довжини хвилі падаючого світла, чи підбираючи склад фаз в такий спосіб, щоб показники заломлення їх збіглися. Перший шлях непридатний і при отриманні ударопрочного полістиролу. Каучук має показник заломлення 1,52. Для зниження показника заломлення матриці частина стиролу заміняють метилметакрилатом (співвідношення 30: 70). Отже вдасться одержати ударопрочный сополимер з прозорістю 70—75%. Сополимеризацию проводять за безупинної схемою в розчині ароматичного вуглеводнів (наприклад, в толуоле) чи з періодичної схемою блочно-суспензионным методом.
2.2. Ненасичені полиэфиры.
Хоча перші ненасичені полиэфиры фумаровой і малеиновой кислот отримано близько дев’яносто років тому, вперше виробництво полімерів розпочався початку сорокових років. Важливим етапом, що його широкому практичного застосування полималеинатов і полифумаратов, було відкриття здібності цих полімерів сополимеризоваться з вініловими мономерами із отриманням цінних конструкційних материалов.
У сорокові роки з’явилися повідомлення про виробництві полімерів полимеризацией і сополимеризацией диаллилфталата до інших аллиловых складних ефірів. З 1947—1948 рр. Радянському Союзі технічне значення придбали полиэфиракрилаты — полімери, синтезовані полимеризацией олигомерных ефірів з кінцевими акрильными, метакрильными та інші ненасиченими группами.
2.2.1. Полималеинаты і полифумараты.
Найбільше застосування знайшли ненасичені полиэфиры, одержувані доликонденсацией ненасичених дикарбоновых кислот, найчастіше малеиновой і фумаровой з многоатомными спиртами.
Зазвичай це ненасичені полиэфиры використав вигляді їх 60—75%-ных розчинів у різних мономерах, при сополиме-рязации із якими утворюють неплавкі і нерозчинні полімери просторового будівлі. Такі розчини ненасичених полиэфиров в непредельных мономерах називають ненасиченими полиэфирными смолами. Використання ненасичених полиэфиров у вигляді їхнього розчинів забезпечує, по-перше, повніше отверждение ненасыщенного полиэфира, а, по-друге, знижує в’язкість ненасичених полиэфиров, полегшуючи їх використання у ролі зв’язуючого для армованих материалов.
Ненасичені поліефірні смоли від багатьох інших термореактив пых полімерів тим, що вони можуть закаліть при кімнатної чи порівняно невисокою температурі без виділення будь-яких побічних продуктів. Це дозволяє виготовляти їх вироби (зокрема, армовані пластики) при низьких тисках, що є велике значення з економічної, і із технологічної точок зору. Ненасичені поліефірні смоли одержують у дві стадия1. Спочатку здійснюють поликонденсацию малеиновой чи фу-маровой кислот чи його суміші з модифицирующей насиченою дикарбоновой кислотою із будь-яким гликолем (этиленглико-лем, диэтиленгликолем, пропиленгликолем, триэтиленгликолем, бутиленгликолем чи його сумішами). Реакцію проводять у розплаві вихідних компонентів при 170—230 °З в інертної середовищі або за нижчих температурах (160—195 °З) у присутності розчинників, їхнім виокремленням азеотропные суміші (наприклад, ксилол) з выделяющейся у процесі реакції водой:
Слід враховувати, що з поліконденсації, залежно та умовами проведення процесу відбувається у більшої або меншою мірою ізомеризація цис-изомерных малеинатных ланок на більш стійкі транс-изомерные фумаратные ланки, зміст що у кінцевому продукті визначає багато його властивості (твердість, теплостойкость зв ін.). По Суті, під час використання в поліконденсації як кислотного агента малеиновой кислоти виходять полиэфиры, які становлять разнозвенные полімери, що є сополимерами малеиновой і фумаровой кислот. Ступінь перетворення залежить як від природи гликоля, і та умовами поліконденсації і може становити 70—90%.
Для полегшення видалення води реакційну масу перемішують, тож під кінець реакції нагрівають ввакуумі. Щоб прискорити процес, іноді використовують каталізатори (солі металів; мінеральні і органічні кислоти, наприклад n-толуолсулъфокислоту, і др.).
Швидкість поліконденсації залежить від складу вихідних речовин. У реакціях малеїнового ангідриду з різними гликолями активність гликолей зростає у послідовності 1,2-пропиленгликоль < диэтиленгликоль < этилентликоль загалом тривалість поліконденсації залежно від природи вихідних мономерів і умов проведення процесу становить 6—20 год, кислотне число одержуваного полімеру одно; 25—45 мг КОН/г полімеру. Молекулярну масу полим-ера можна регулювати запровадженням на певної стадії процесу у реакційну суміш монокарбоновых кислот чи одноатомных спиртів (наприклад, оцтовий ангідрид, циклогсксанол). Нерідко така добавка покращує наступну сумісність ненасыщенного полиэфира з мономером. Синтез ненасичених полиэфиров зазвичай ведуть у апаратах із нержавіючої сталі чи емальованих. Технологічна схема виробництва аналогічна отриманню інших полиэфиров>
2.2.1. Властивості полиэфирной смоли ПН — 1.
Нижче наведені деякі показники властивостей отвержденного прлиэфира марки 1ВД-1:
Щільність при 20оС, кг/м8…1210—1250.
Що Руйнує напруга на вигині, МПа. … 70—100.
Модуль пружності на вигині, МШ … 2200—2800.
Ударне в’язкість, кДж/м2… 6—12.
Твердість по Бриннелю, МН/м2…140—180.
Теплостойкость по Віка, °С…85—120.
Питома об'ємне електричне опір, Ом-м. …1 1О12—5 1018.
Диэлектрическая проникність при 10е гц… …4,4—5,2.
Електрична міцність, кВ/мн… 13—19.
Практичний цікаві і азотомісткі ненасичені полиэфиры з урахуванням малеїнового ангідриду, модифицирующей дикарбоновой кислоти (фталевого ангідриду, адипиновой кислоти та інших.), гликоля звичайного типу (этиленгликоль, диэтиленгликоль) і двухатомного спирту, що містить у собі третинний азот, зокрема, N — фенил-бис (?-окси-этил) аміну. Наявність у реакційної суміші такого азотсодержащего двухатомного спирту дозволяє скоротити тривалість поликонденсацин в виробничих умовах перетворюється на 1,5— 2 рази, й цим продуктивність установки по синтезу ненасичених полиэфиров на 30—40%. Такі азотомісткі ненасичені полиэфиры відрізняються підвищеною сумісністю зі стиролом, легше отверждаются, а отвержденные продукти характеризуються високими фізико-механічними показателями.
2.3. Методика исследования.
Перший етап дослідження складається з вибору наповнювачів ініціаторів прискорювачів і приготування кількох пробних сумішей з їхньої основе.
Для вивчення кінетики полімеризації можна буде використовувати такі доступні ініціатори радикальної полімеризації: перекис бензоила, перекис дикумила, перекис метил-этил кетона. Прискорювачі їм диметиланилин, солі кобальту, нафтэлат кобальту, відповідно. Планується вивчити кінетику полімеризації стиролу і полиэфира ПН — 1 у присутності даних ініціаторів. Також слід оцінити колір отриманих полімерів та його придатність на приготування шпатлёвочной пасти. Вивчити вплив наповнювача на кінетику процесу деяких інших закономерности.
3. ЕКСПЕРИМЕНТАЛЬНА ЧАСТЬ.
3.1. Методи отримання зразків і аналіз отриманих результатов.
3.1.1 Вивчення кінетики полимеризации.
Таблиця 3.1 Склад смесей.
Инициатор/ускоритель Инициатор/ускоритель/Полиэфирная смола ПН 1 Инициатор/ускоритель/Стирол.
Перекис бензоила/диметил анілін 1%/1%/98% 2%/2%/96%.
Мітив етил кетон/нафтэнат кобальту 1%/1%/98% 2%/2%/96%.
Перекис дикумила/Co+2 1%/1%/98% 2%/2%/96%.
Таблиця 3.1 Найкращі результати полімеризації.
Инициатор/ускоритель Поліефірна смола ПН 1 Стирол.
Перекис бензоила/диметил анілін 5 хв Сталося розігрівання 36 год Маса Дуже пожелтела.
Мітив етил кетон/нафтэнат кобальту 10 хв Маса стемніла 156 год Колір змінився слабо.
Перекис дикумила/Co+2 30 хв Маса стемніла 125 год Колір майже изменился.
Як очевидно з експериментальних даних полімеризація стиролу при кімнатної температурі проходить вкрай повільно й як сполучне для шпатлёвки не годиться. Кращим вибором є композиції з урахуванням полиэфиров.
3.1.2 Склад 1.
Перший етап отримання шпатлёвки: додаємо наполнитель,.
тиксотропную добавку полиэфирную смолу і прискорювач, старанно перемешиваем кашку у склянці. Як наповнювача використовується ZnO2, тиксотропная добавка — кизельгур, прискорювач — диметил анілін, поліефірна смола — ПН — 1.
Отвердитель готують за такою методиці: ініціатор (перекис бензоиза) розчиняють в бензолі до насыщения.
До шпатлёвке додають отвердитель, перемішують суміш, з допомогою шпателя намазують на зразки подряпин на УПС.
Згодом можемо з візуальним спостереженням дійшли висновку, що зразки з великим змістом полиэфира вже затвердели.
Рецептура клею — шпатлевки представленій у таблиці 2.4.
Таблиця 2.4 Рецептура клею — шпатлевки з урахуванням ПН — 1.
Інгредієнт Склад шпатлевки, %.
1 2 3 4 5.
1 Шпатлёвка 95%.
ZnO2 23% 33% 43% 53% 63%.
Поліефірна смола ПН 1 70% 60% 50% 40% 30%.
Кизельгур 5% 5% 5% 5% 5%.
Диметил анілін 2% 2% 2% 2% 2%.
2 Отвердитель 5%.
Розчинник ПБ 80% 80% 80% 80% 80%.
Перекис бензоила 20% 20% 20% 20% 20%.
Було візуально виявлено, деякі зразки шару шпатлёвки має малої усадкой, досить хорошою адгезией, хорошою твёрдостью, низькою схильністю до растрескиванию.
Помічено також, що при отверждении полиэфира перекисом бензоила/диметил аніліном відбувається сильне пожелтение, яку практично неможливо усунути подкрашиванием органічними красителями.
Було визначено такі закономерности:
* З измененнием концентрації ініціатора в отвердителе чи самого отвердителя швидкість отверждения вдавалося сильно изменять.
* Додавання стиролу до шпатлёвке у різних концентраціях зумовлювало поліпшенню змочування поверхні УПС але зменшенню твердості покрытия.
* Додавання болше ніж 2% - вв диметиланилина забарвлювало шпат в жовтий колір тоді як, смола ПН — 1 не впливала на цвет.
* Спроба додати розчин УПС до шпатлёвке щоб змінити її колір сприяла расслаиванию композиції і слоевому отверждению.
* Колір шпатлёвки не вдається вирівняти органічними красителями.
3.1.3 Склад 2.
Перший етап отримання шпатлёвки: додаємо заповнювач отримання шпатлёвки: додаємо заповнювач, тиксотропную добавку полиэфирную смолу і прискорювач, старанно перемешиваем кашку у склянці. Як наповнювача використовується ZnO2, тиксотропная добавка — кизельгур, прискорювач — нафтэнат кобальту, поліефірна смола — ПН — 1.
Отвердитель перекис метилэтил кетона.
До шпатлёвке додають отвердитель, перемішують суміш, з допомогою шпателя намазують на зразки подряпин на УПС.
Через 70 хвилин зразки затвердевают.
Рецептура клею — шпатлевки представленій у таблиці 2.4.
Таблиця 2.4 Рецептура клею — шпатлевки з урахуванням ПН — 1.
Інгредієнт Склад шпатлевки, %.
1 2 3 4 5 6.
Компонент 1 Шпатлёвка 99% Шпатлёвка 98%.
ZnO2 30% 40% 50% 30% 40% 50%.
Поліефірна смола ПН 1 63% 53% 43% 63% 53% 43%.
Кизельгур 5% 5% 5% 5% 5% 5%.
0.3% розчин нафтэната кобальту 1% 1% 1% 1% 1% 1%.
Компонент 2 Отвердитель 1% Отвердитель 2%.
Мітив етил кетона перекис 100% 100% 100% 100% 100% 100%.
Було візуально виявлено, що зразки шару шпатлёвки мають малої усадкой, досить хорошою адгезией, хорошою твёрдостью, низькою схильністю до растрескиванию.
Оскільки спочатку для шпатлёвки бралися компоненти кольором які від виробів із ПС, було проведено експерименти по додаванню органічних барвників із єдиною метою вирівнювання відтінків. З візуальних спостережень можна дійти невтішного висновку, що Росії вдалося отримати хороше забарвлення. Шпатлёвка подається окраске.
Було визначено такі закономерности:
* Зі збільшенням концентрації отвердителя швидкість отверждения вдавалося сильно увеличивать.
* Додавання стиролу до шпатлёвке у різних концентраціях зумовлювало поліпшенню змочування поверхні УПС але зменшенню твердості покрытия.
* Спроба додати розчин УПС до шпатлёвке щоб змінити її колір сприяла расслаиванию композиції і слоевому отверждению.
* Варіювати твердість і можливість композиції до отверждению можна буде змінюючи концентрацію окису цинка.
* Шпатлёвка подається забарвленні органічними красителями.
* Швидкість отверждения сильно знижується за наявності в полиэфире чи ZnO2 влаги.
3.1.4 Склад 3.
Приготуємо для аналізу три композиції складом зазначених у таблиці 2.5.
Перший етап отримання шпатлёвки: растворяем в стиролі стружку з УПС, додаємо до розчину полиэфирную смолу, прискорювач, кизельгур, окис цинку старанно перемешиваем кашку у склянці. Як прискорювача — нафтэнат кобальту, поліефірна смола — ПН — 1.
Отвердитель перекис метилэтил кетона.
До шпатлёвке додають отвердитель, перемішують суміш, з допомогою шпателя намазують на зразки подряпин на УПС.
Через 70 хвилин зразки затвердевают.
Рецептура клею — шпатлевки представленій у таблиці 2.5.
Таблиця 2.4 Рецептура клею — шпатлевки з урахуванням ПН — 1.
Інгредієнт Склад шпатлевки, %.
1 2 3.
Компонент 1 Шпатлёвка 99%.
ZnO2 0% 10% 20%.
Розчин УПС/стирол — 3/1 44% 34% 24%.
Поліефірна смола ПН 1 50% 50% 50%.
Кизельгур 5% 5% 5%.
0.3% розчин нафтэната кобальту 1% 1% 1%.
Компонент 2 Отвердитель 1%.
Мітив етил кетона перекис 100% 100% 100%.
Було зроблено такі наблюдения:
* Шпатлёвка з часом расслаивалась на дві фази: розчин полиэфира в стиролі і розчин УПС в стироле.
* Окис цинку отбеливает композицію, надаючи верствам її матовості, хоча лист УПС блакитнуватий зі слабко помітним глянцем на поверхности.
* При малої концентрації ZnO2 колір шпат має такий самий як і поліефірна смола (рожевий), отже, приготувати композицію з урахуванням даних інгредієнтів не удастся.
3.1.5 Склад 4.
Приготуємо для аналізу композиції складом зазначених у таблиці 2.6.
Перший етап отримання шпатлёвки: растворяем парафін в полиэфирной смолі, додаємо прискорювач, кизельгур, окис цинку старанно перемешиваем кашку у склянці. Як прискорювача — нафтэнат кобальту, поліефірна смола — ПН — 1.
Отвердитель перекис метилэтил кетона.
До шпатлёвке додають отвердитель, перемішують суміш, з допомогою шпателя намазують на зразки подряпин на УПС.
Через 70 хвилин зразки затвердевают.
Рецептура клею — шпатлевки представленій у таблиці 2.6.
Таблиця 2.4 Рецептура клею — шпатлевки з урахуванням ПН — 1.
Інгредієнт Склад шпатлевки, %.
1 2 3 4 5 6.
Компонент 1 Шпатлёвка 99%.
ZnO2 25% 15% 5% 25% 15% 5%.
Білий парафін 20% 30% 40% 30% 40% 50%.
Поліефірна смола ПН 1 50% 50% 50% 40% 40% 40%.
Кизельгур 4% 4% 4% 4% 4% 4%.
0.3% розчин нафтэната кобальту 1% 1% 1% 1% 1% 1%.
Компонент 2 Отвердитель 1%.
Мітив етил кетона перекис 100% 100% 100% 100% 100% 100%.
Було візуально виявлено, що зразки шару шпатлёвки мають малої усадкой, досить хорошою адгезией, хорошою твёрдостью, низькою схильністю до растрескиванию.
Оскільки спочатку для шпатлёвки бралися компоненти кольором які від виробів із УПС, було проведено експерименти по додаванню органічних барвників із єдиною метою вирівнювання відтінків. З візуальних спостережень можна дійти невтішного висновку, що Росії вдалося отримати хороше забарвлення. Шпатлёвка подається окраске.
Було визначено такі закономерности:
* Зі збільшенням концентрації отвердителя швидкість отверждения вдавалося сильно увеличивать.
* Варіювати твердість і можливість композиції до отверждению можна буде, змінюючи концентрацію парафина.
* Шпатлёвка подається забарвленні органічними красителями.
* Парафін додав шпатлёвке оптичні якості аркуша УПС.
* Парафін знижує твердість відкинутого полиэфира.
* Парафін обмежена розчиняється в смолі ПН-1.
* Композиції, мають великий вміст парафіну ніяк не намазуються на поверхню листа.
* Щоб надати кольору ще на шпат можна додавати органічні красители.
Приблизний хімічний склад шпатлёвки для аркуша з УПС приведено у заключении.
4.
ЗАКЛЮЧЕНИЕ
.
У результаті був опредёлён оптимальний хімічний склад композиції для шпаклевания аркуша з ударопрочного полістиролу і АВС. Рекомендовані співвідношення реагентів наведені у таблиці 4.1.
Таблиця 4.1.
Рецептура клею — шпатлевки з урахуванням ПН — 1.
Інгредієнт Зміст %.
Шпатлёвка 99%.
ZnO2 10%.
Білий парафін 40%.
Поліефірна смола ПН 1 45%.
Розчин нафтэната кобальту 0.3% 1%.
Кизельгур 4.9%.
Барвник 0.1%.
Отвердитель 1%.
Перекис метилэтилкетона 100%.
Якщо потрібно збільшити швидкість отверждения рекомендується збільшити кількість який додається отвердителя вдвічі. При низькою в’язкості шпату припустимо збільшення концентрації ZnO2. Для зниження твердості рекомендовано збільшити концентрацію парафина.
СПИСОК ВИКОРИСТАНИХ ИСТОЧНИКОВ.
1. Миколаїв А. Ф. Технологія пластичних мас. Л., Хімія, 1977, з. 238−261.
2. «Технологія пластичних масс»: Под редакцією академіка В. В. Коршака.-Москва:Химия, 1985;559с.
3. Коршак У. У. Разнозвенность полімерів. М., Наука, 1977. 301 с.
4. Бёниг Р. У. Ненасичені полиэфиры. Пер. з англ./Под ред. Л. Р. Сєдова. М., Хімія, 1968. 254 с.
5. Коршак У. У. Термостійкі полімери. М., Наука, 1969. 416 с.