Регенерация азотної і сірчаної кислоты
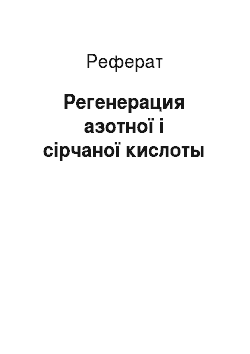
Великим перевагою установок з зовнішнім обігрівом є відсутність чи мінімум туману сірчаної кислоти, образующейся в результаті роботи концентраторів другого типу, і навіть отримання сірчаної кислоти з фортецею до 98%. Завдяки виключенню необхідності очищення вихлопних газів від кислотного туману, з’являється можливість здешевити технологічний процес у результаті виходу з технологічної схеми… Читати ще >
Регенерация азотної і сірчаної кислоты (реферат, курсова, диплом, контрольна)
ВВЕДЕНИЕ
3.
1. Аналітична частина 4.
1.1. Техніко-економічне обгрунтування обраного методу виробництва 4 1.2 Патентна частина 8 1.3 Вибір та обґрунтування району будівництва 13.
Географічні і кліматичні дані регіону. 14.
2. Расчетно-технологическая частина 15.
2.1. Опис технологічної схеми 15 2.2 Принцип роботи колони концентрування H2SO4 18 2.3. Стандартизація. Технологічна характеристика сировини, напівфабрикатів, готового продукту. ГОСТ і технічні вимоги. 20.
Властивості готових продуктів, сировини й напівфабрикатів. 22 2.4. Хімізм основних та побічних реакцій [4] 23 2.5 Інженерні рішення 27 2.6. Розрахунок матеріального балансу відділення концентрування HNO3 [1] 27 2.7. Розрахунок теплового балансу [7] 33.
3. Техніко-технологічна частина 44.
3.1. Вибір і розрахунок продуктивності основного і допоміжного устаткування технологічної схеми 44 3.2 Розрахунок кількості апаратів 45.
4. Конструктивно-механические розрахунки 46.
4.1 Розрахунок числа щаблів контакту фаз концентратора [5] 46 1.2. Гідродинамічний розрахунок 50.
1.2.1. Розрахунок першої у процесі газового потоку щаблів контакту фаз [5].
4.2.2. Розрахунок гідродинамічних характеристик другого продажу та наступних у процесі газу щаблів вихоровий колони [5] 53 4.3. Механічні розрахунки основних деталей та вузлів вихоровий колони [6], [7] 57.
5. Вибір та обґрунтування схеми автоматизації виробничого процесу 62.
Загальні інформацію про типовий мікропроцесорної системі. 63 Технологічний процес регенерації відпрацьованих кислот 64 Опис контурів 66.
Регулювання рівня напорном баку 66.
2 Регулювання температури охолодженою кислоти зі зміни подачі хладагента. 66.
Регулювання співвідношення витрат при автоматизації топки 67.
4. Контур контролю тиску 67.
5. Регулювання концентрації кислот 68 9. Економічне обгрунтування проекту 89.
Розрахунок нормувальних оборотних засобів: 91.
Розрахунок чисельності та фонду зарплати: 92.
Розрахунок фонду зарплати основних виробничих робочих 93.
Розрахунок фонду З.П. допоміжних робочих (черговий персонал) 95.
Розрахунок річного витрати електроенергії (у проекті) 97.
Кошторис цехових витрат 100.
Порівняльні техніко-економічні показники виробництва 102.
6. Безпека і екологічність проекту. 72.
Аналіз виробництва. 72 Індивідуальні засоби захисту 72 Шум і вібрація 74 Вентиляція 75.
Розрахунок вентиляції 76 Метеорологічні умови 76 Пожежна профілактика 77 Висвітлення 79.
Розрахунок природного освітлення 79.
Розрахунок штучного висвітлення. 80.
Электробезопасность 81.
Захисні заходи у электрооборудовании 82.
Статична електрика і молниезащита. 83.
Молниезащита 83.
Розрахунок молниезащиты 83 Безпека технологічного процесу. 85 Екологічність проекту 85 2.8 Розрахунок матеріального балансу концентрування H2SO4 39 2.9. Розрахунок теплового балансу вихоровий колони 40.
7. Будівельно-монтажна схема будинку цехи і компонування устаткування 86.
8. Генеральний план. Пояснення до схемою генерального плану. 88.
Укладання 103.
Список використаних джерел 104.
Додаток, специфікація 106.
Перечень умовних скорочень, позначень, застосовуваних проекте.
АК — азотна кислота.
СК — сірчана кислота.
НКЛ — нитрокаллоксилин.
ОК — відпрацьована кислота.
СКУ — вихрове контактне устройство.
АСУТП — автоматизовані системи управління технологічним процессом.
УВМ — управляюча обчислювальну машину ЗАПРОВАДЖЕННЯ [1].
Нині розвиток виробництв, які використовують суміш азотної і сірчаних кислот як нитрующего агента, призвело до отриманню величезних кількостей відпрацьованих кислотних сумішей. Ці суміші з економічної точки зору необхідно регенерувати й у необхідних розрахункових концентраціях повертати знову на виробничий цикл, цим здешевлення одиницю собівартості готової продукции.
Склад потрійних сумішей HNO3 -H2SO4 — H2O, вступників на регенерацію, коливається у досить межах. У одних випадках вони представляють сильно розбавлені кислотні суміші із вмістом азотної кислоти 5−10%, в інших випадках відпрацьовані кислоти містять 1−2% азотної кислоти і 65−70% сірчаної кислоти, у якій розчинено окисли азоту N2O3, що утворюють нитрозилсерную кислоту HNSO5.
Регенерація таких сумішей є певні труднощі й вимагає пошуки нових і нових засобів, щоб забезпечити нормальне ведення процесу разгонки відпрацьованих кислот, і навіть отримання азотної і сірчаної кислот, що за своїми якостям і технічними характеристиками не поступаються свіжим кислотам застосовуваним для нитрации.
Початковою щаблем регенерації відпрацьованих кислот був частиною їхнього денитрация. Цей процес відбувається залежить від виділенні їх кислотною суміші азотної кислоти і окислів азоту, які у суміші. У результаті проведення процесу денитрации виходить 68−70% сірчана кислота, яка надходить на концентрування, після чого, у разі потреби, то, можливо знову спрямована у цикл нитрации.
1. Аналітична часть.
1.1. Техніко-економічне обгрунтування обраного методу виробництва [2], [3].
У сучасному технології для концентрування сірчаної кислоти застосовуються два виду установок:
— з зовнішнім обогревом;
— з безпосереднім зв’язком греющих газів з кислотой.
До настановам зовнішнього обігріву ставляться казани, звані реторти, установки типу Бюшинга, Паулинга, Фришера, і навіть Майснера. Вони відбувається обігрів кислоти через стіну у апаратах колонного типу, установки вакуум-аппаратов та настанови Дюпон плівкового типа.
До настановам з безпосереднім зв’язком гарячих газів з кислотою ставляться установки Кесслера; широкого розповсюдження набули апарати типу Хемико, працюють у режимі барботирования газів через шар сірчаної кислоти і апарати Вентури трубного типа.
Суть процесу концентрування в апаратах цього залежить від роздрібненні кислоти на краплі завдяки потоку гарячого газа.
Обидва виду технологій отримання концентрованої сірчаної кислоти мають як позитивні, і негативні сторони, які потрібно враховувати в виборі характеру виробництва, у кожному окремому проекті - з урахуванням економічних показників і наявність трудових і сировинних ресурсов.
Великим перевагою установок з зовнішнім обігрівом є відсутність чи мінімум туману сірчаної кислоти, образующейся в результаті роботи концентраторів другого типу, і навіть отримання сірчаної кислоти з фортецею до 98%. Завдяки виключенню необхідності очищення вихлопних газів від кислотного туману, з’являється можливість здешевити технологічний процес у результаті виходу з технологічної схеми дорогих электрофильтров. Але у концентрировании сірчаної кислоти, наприклад, в ретортах до 96% фортеці і від, відбувається їх швидке зношування через високе температури кипіння сірчаної кислоти, яка сягає t=300оC. З іншого боку, при високих температур збільшується випаровування і розкладання сірчаної кислоти, що веде до втрати кількості і якості сірчаної кислоти. Ці недоліки враховані і усунуті в установках типу Майснера, де концентрування відбувається під вакуумом. Установки Майснера дуже компактні проти ретортными установками Паулинга. Під час проектування виробництв одному й тому ж потужності, установки з колонами Майснера займають менш 40% площі, потрібну для установки реторт Паулинга. Проте установки Майснера мають дуже серйозний недолік через малої продуктивності (вихід готового продукту становить до 13−15 т на добу.). До іншому браку належить розтріскування ферросилидовых царг, що виявляється у процесі експлуатації даної установки, і навіть порушення ущільнення між царгами. До вад колон Майснера належить і необхідність будівництва котельних для вироблення водяної пари, які у колонах. Отже, цей тип установок може бути застосований лише у випадках необхідності концентрування невеликих кількостей сірчаної кислоти й у отримання при цьому сірчаної кислоти високої концентрації (до 98%).
Проблема розтріскування ферросилидовых матеріалів і проблему появи неплотностей було вирішено з приходом установок із застосуванням нагрівальних труб і методу водою, що плівки в установках типу Дюпон. У цих установках застосована новий технічний рішення, у вигляді монтажу устаткування з урахуванням механічних і термічних напруг ферросилида, то є або на ковзанках, або на пружинних підвісках. Перевагою належить простота устрою, виконання й обслуговування. Ці установки по продуктивності ставляться до середніх, досягаючи до 25 т/добу. До недоліків цього виду установок належить забруднення внутрішніх поверхонь труб з часом, що зумовлює зниження їх теплопропускной здатності Німеччини та необхідності їх періодичної прочищення і промивання із застосуванням великої кількості води. У нашій країні початковий період розвитку отримання высококонцентрированной сірчаної кислоти установки цього користувалися не дуже популярна, але, в зв’язки України із бурхливим зростанням промисловості, споживає СК у величезних кількостях, установки першого типу були переважно витіснені установками другого типу — з безпосереднім зв’язком греющих газів з кислотою, а установки з зовнішнім обігрівом функціонують й у час в одиничних экземплярах.
Одне з представників установок другого типу установки Кесслера, в яких значно полегшено передача тепла від топочных газів до сірчаної кислоті. Концентрируемая кислота не доводиться до точки кипіння, а велика, відкрита поверхню контакту газу та кислоти максимизирует інтенсивність процесу массопередачи і теплопередачі. З іншого боку, перевагою установок Кесслера був частиною їхнього можливість будь-якою місцевому вигляді палива: газоподібному, рідкому, твердому, значно збільшує сировинні можливості невпинного переходу з однієї виду палива на разі необхідності в інший. До вад насамперед належить необхідність періодичної чистки рекуператора з розвантаженням насадки, а також велика втрата СК з отходными газами, що становить близько 2−2,5%. Дані апарати мають невелику продуктивність — 20 т/добу. У останнім часом установки Кесслера переважно витіснила концентраторами барабанного типу. У апаратах цього концентрування виробляється шляхом барботажа гарячих газів через упариваемую кислоту, як і шарі кислоти, і у зоні бризок, де на кількох поверхні крапель відбувається хороша теплопередача. До нашого часу вони вважалися найбільш зручними, вже економічними і практичними для концентрування сірчаної кислоти. Основний вид палива тих установок — мазут. Однак у останнім часом у зв’язку зі збільшенням виробництва газу, останній став широко застосовуватися у концентраторах барабанного типа.
Перевагою цих концентраторів ставляться краще використання тепла переробка великої кількості кислоти. Дані концентратори мають і кілька суттєвих недоліків, які можуть бути усунуті без корінних змін конструкції. Перший недолік залежить від підтримці суворого температурного режиму топочных газів, оскільки збільшення його навіть на 10 ОС досить швидко руйнує барботажные труби першої камери концентратора і, отже, збільшуються втрати СК через її термічного розкладання, що є 10−15% від загальної кількості СК, що йде на концентрирование.
Другим, дуже серйозним недоліком, є освіту парів і туманів СК, улов яких вимагає і застосування громіздких і дорогих споруд — электрофильтров, причому самі электрофильтры теж мають недоліки — вони здійснюють неповний улов сірчистих газів і окислів азоту, що викидаються у повітря; вартість їх дуже висока і становить до 30% витрат за всю установку. З огляду на викладені переваги та недоліки, з’явилися нові швидкісні концентратори, в яких потоком гарячого газу рідина переважно розбивається на дрібні краплі. До сформування такого процесу концентрування СК в капельном стані використовують апарати Вентури.
Таблиця № 1 — Видаткові коефіцієнти отримання 92,5% сірчаної кислоты.
|Показатели |Барботажный |Труби Вентури | | |концентратором | | |Паливо, кг |70 |44,5 | |Вода (t=25 ОС) |7 |6,5 | |Ел. енергія, кВт. год |18 |16,6 |.
Застосування цих труб має низку переваг: при невеликих розмірах вони мають велику продуктивність, що дозволяє знизити капітальні витрати на 1 тонну концентрованої кислоти проти барботажным концентратором. Перевагою цього і те, що як низька температура кипіння кислоти зменшує ступінь розкладання у її концентрировании зменшує туманообразование, що в результаті приводить до зменшення необхідного обсягу газоочистки.
Вихрова ферросилидовая колона істотно відрізняється віднині які у промисловості систем концентрування СК. Процес ввозяться режимі без освіти туманів сірчаної кислоти і сірчистого ангідриду, що різко знижує газові викиди. Конструктивне виконання концентратора дозволяє з допомогою додаткових брызгоуловительных і абсорбційних щаблів здійснювати зниження газового викиду до санітарних норм без электрофильтров і скрубберов.
1.2 Патентна часть.
Для проведення патентних досліджень визначається предмет пошуку по темі дипломного проекту, підлягає исследованию.
Предмет пошуку: «Регенерація відпрацьованих кислот. «.
Пошук проходить за вітчизняному патентному фонду, з наявності фонду у бібліотеці КГТУ. Глибина пошуку — 5 років, починаючи з 1994 року й всередину без пробелов.
Джерело інформацію про вітчизняних винаходи по Міжнародної класифікації винаходи МПК:
С01В17/88, С01В17/90, С01В21/24, С01В21/22, С01В21/38, С01В21/40, С01В21/44.
Метою досліджень є з’ясування рівня розвитку техніки в цій сфері й аналіз застосовності прогресивності рішень на дипломному проекте.
Для складання повного списку винаходів, причетних до темі пошуку, користуються річними систематичними покажчиками до офіційним бюллетеням.
Номери охоронні документи, причетних до темі пошуку, заносяться в таблицу.
Таблиця № 2 — Список охоронні документи |Індекс МПК |№№ охоронних |№№ БІ |Країна |Назва | | |документів |чи ИЗР |видачі |винаходи | | | | |патенту | | | | |1994 рік| | | |С01В17/88 |2 016 842 |14 |РФ |Спосіб | | | | | |концентрування | | | | | |H2SO4 | |С01В21/24 |2 022 917 |21 |РФ |Спосіб отримання | | | | | |окису азоту | |С01В21/26 |1 102 183 |6 |РФ |Спосіб окислення | | | | | |аміаку | |С01В21/38 |2 009 996 |6 |РФ |Спосіб отримання | | | | | |азотної кислоти | | | |1993 рік| | | |С01В17/22 |1 805 095 |12 | |Спосіб | | | | | |регенерації | | | | | |відпрацьованою | | | | | |H2SO4 | |С01В21/38 |1 809 774 |14 | |Спосіб зниження | | | | | |змісту | | | | | |оксидів азоту в | | | | | |хвостових газах | | | | | |виробництва | | | | | |слабкої азотної | | | | | |кислоти | | | |1992 рік| | | |С01В21/22 |1 675 202 |33 |РФ |Спосіб отримання | | | | | |закису азоту | |С01В21/26 |1 636 332 |11 |РФ |Спосіб очищення | | | | | |газоподібного | | | | | |монооксиду азоту | | |1 698 187 |46 |РФ |Спосіб отримання | | | | | |могооксида азоту | |С01В21/24 |1 650 575 |19 |РФ |Спосіб | | | | | |двухступенчатого | | | | | |окислення аміаку| |С01В21/38 |1 664 740 |27 |РФ |Спосіб | | | | | |автоматичного | | | | | |управління | | | | | |процесом очищення| | | | | |хвостових газів | | | | | |від оксиду азоту | |С01В21/40 |1 668 291 |29 |РФ |Спосіб | | | | | |переробки | | | | | |окислів азоту в | | | | | |неконцентрированн| | | | | |ую азотну | | | | | |кислоту | | | |1991 рік| | | |С01В21/90 |1 712 304 |6 |СРСР |Спосіб очищення | | | | | |сірчаної кислоти | |С01В17/88 |1 723 030 |12 |СРСР |Спосіб | | | | | |концентрування | | | | | |і очищення сірчаної | | | | | |кислоти | | | |1990 рік| | | |С01В21/40 |15 641 114 |18 |СРСР |Спосіб | | | | | |ректифікації | | | | | |суміші «азотна | | | | | |кислота | | | | | |-четырехокись | | | | | |азоту «| | |1 593 691 |35 |СРСР |Спосіб очищення | | | | | |газової суміші від | | | | | |оксидів азоту | |С01В21/46 |1 586 997 |31 |СРСР |Спосіб | | | | | |регенерації | | | | | |відпрацьованою | | | | | |20−50% азотної | | | | | |кислоти |.
У розроблюваний план найбільш підходять такі изобретений:
(11) 2 016 842 (13) С1.
(51) 5С01В17/88.
(21) 4 945 951/26.
(72) Махоткин А. Ф., Халитов Р. А., Іванов Г. А., Газизов Ф. М., Куликов В. В., Зарипов І.Р., Лаптєв В.И.
(71) Казанський Державний Технологічний Университет.
(54)(57).
1. Спосіб концентрування сірчаної кислоти, до складу якого багатоступеневе пряме контактування вихідної кислоти з потоком гарячих топочных газів у режимі противотока і наступне сепарирование, відмінне тим, що з метою запобігти освіти сірчанокислого туману в відведених газах, газожидкостную суміш з кожної щаблі піддають поділу на рідинної і дисперсний потоки із подачею останнього для наступної щабель, а жидкостного — на попередню стосовно напрямку потоку газів щабель, причому концентрацію сірчаної кислоти в дисперсном потоці підтримують рівної 0,6−1,4 кг/м3.
2. Спосіб по п. 1, що б тим, що ведуть у 3−4 ступени.
(11) 1 541 188 (51) С01В17/90.
(21) 3 741 076/23−26 (22) 11.05.84.
(71) Горьковський Політехнічний институт.
(72) Пастухова Г. В., Кім В.П., Петрушков А. А., Катраев О. Н., Казанцев В. П., Никандров І.С., Овчинников В.Д.
(53) 661.254.
(54)(57) Спосіб очищення концентрованої сірчаної кислоти від оксидів азоту обробкою восстановителем за підвищеної температурі, що б тим, що із метою зниження витрати відновлювача й отримання утилизируемого відходу оксиду азоту, як відновлювача використовують уротропін в стехиометрическом кількості на відновлення азотистого ангідриду до оксиду азота.
(11) 1 699 901 (51) С01В17/88.
G05Д27/00.
(21) 66.012.-52.
(75) Кабатов Г. С., Алексєєв Ю.В., Шевців А.Д.; (54)(57) Спосіб управління процесом концентрування сірчаної кислоти в массобоменном колонному апараті шляхом виміру температури в останній у процесі кислоти щаблі массообменной колони, регулювання витрати палива на піч по температурі топочных газів, стабілізації витрат розведеною сірчаної кислоти, повітря на піч, температур топочных газів і концентрованої сірчаної кислоти, котра тим, що з метою підвищення якості продукту та зниження викидів шкідливих речовин у атмосферу, температуру топочных газів, поданих у піч, коректують по температурі в останній у процесі кислоти щаблі массообменной колонны.
(11) 1 809 774 (51) В01Д53/14, С01В21/38, С01В21/40.
(22) 4 913 954/26 (22) 25.02.91.
(72) В. А. Линев, В.І. Герасименко, А. А. Черкасов, М. П. Решетюк, Г. С. Николаев.
(71) Виробниче об'єднання «Куйбышевазот «.
(73) Виробниче об'єднання «Куйбышевазот «.
(54)(57) Спосіб зниження змісту оксидів азоту в хвостових газах виробництва слабкої азотної кислоти, до складу якого абсорбцію нитрозных газів водним розчином азотної кислоти з последующм відновленням впроваджуються зі стадії абсорбції хвостових газів, містять домішки оксидів азоту, аміаком, що б тим, що із метою зниження змісту шкідливі речовини в хвостових гази та витрати аміаку, водний розчин азотної кислоти, перед абсорбцією обробляють озонокислородной сумішшю, що містить 40−60 р. озону на 1 м³ хвостового газу, який вводимо зі стадії абсорбции.
(11) 1 688 291 (51)5 С01В21/40.
(21) 4 648 035/28 (22) 07.02.89.
(53) 661.56.
(72) А. Ф. Мараховский, О. Н. Золотарьов, В. К. Кисельов, В. А. Степанов, Н. П. Перепадья, В. В. Истомин.
(71) Харківський Інститут інженерів комунального будівництва, Горловское виробниче об'єднання «Стірол », кооператив «Супутник » .
(54)(57) Спосіб переробки оксидів азоту в неконцентрированной азотної кислоті до складу якого їх абсорбцію поглиначем, що містить азотну кислоту, попередньо оброблену магнітним полем напруженістю 1500- 2500 Еге, що б тим, що з метою підвищення ступеня переробки, разом з магнітної обробкою здійснюється аэрирование поглинача повітрям чи газової сумішшю, що містить 90−99% кисню протягом 20−40 хв. При питомому витратах повітря, або газової суміші 0,2−2,0 м³, на 1 м поглинача в час.
Заключение
.
Патентні дослідження з фонду винаходів показали, що сама розроблялася, проте увагу розробників до досліджуваної темі нерівномірно за літами. Пік винахідницької активності посідає 1992 рік. Під час розробки теми основну увагу приділяли підвищення якості готового продукту, зниження матеріальних витрат, поліпшенню технології процесу. Розробки стосуються як вдосконалення всієї технологічної схеми, а й окремих операцій виробничого циклу і устаткування нього, зміна методів управління процесом на окремих стадиях.
Для аналізу оброблено 5 винаходів, які мають безпосередній ставлення до досліджуваної темі. Вони розроблено методи регенерації і утилізації відпрацьованою кислоти, у своїй вирішуються завдання екології з допомогою замкнутості цикла.
1.3 Вибір та обґрунтування району строительства.
При виборі місця будівництва враховується географічне розташування, наявність з корисними копалинами, рельєф, кліматичні умови. Важливим чинником є наявність водойм задля забезпечення безперервного підвода води, сировини, шляхів для безпечної, екологічної та дешевої доставки цього сировини й другигх напівфабрикатів від постачальників, і навіть відвантаження готової продукції, розвиненою інфраструктури, достатня енергетична база. Слід зазначити також важливість добре розвиненою наукової бази щодо підготовки фахівців у даному виробництві й наявності вона дуже обмежена робочої сили з урахуванням технологічних особливостей і параметрів даного процесу. Враховуючи всі перелічені вище чинники, вибираємо для будівництва виробництва для регенерації відпрацьованих кислот р. Казань, як великий науково-технічний, навчально-виробничий і сировинної пункт. Казань — столиця Татарстану. Татарстан перебуває у середині Поволжья.
Географические і кліматичні дані региона.
За шириною Татарстан займає середнє становище, по довготі його територія зрушена ближчі один до Уралу. Такий стан республіки визначається помірної континентальностью клімату, що надає великий вплив попри всі чинники природних ресурсов.
Клімат в Татарстані помірний. Середня температура холодного періоду — 14,5 ОС, теплого +19,9 ОС. Переважна напрям вітру — северозахідний. Відносна вогкість повітря влітку µ=63%, взимку µ=86%. Глибина замерзання грунту 16 метри. Середній сніговий покрив 35 див., кількість опадів протягом року 449 мм.
Місто пов’язані з залізничними, водними, автомобільними шляхами з районами — постачальниками і споживачами. Цех по регенерації відпрацьованих кислот лежить у безпосередній близькості до залізничного вузла «Станція Табірна », що полегшує доставку сировини й матеріалів для перевезення в залізничних вагонах і цистернах. Достатня і енергетична база. Електроживлення йде з систем електропостачання мережі «Татэнерго » .
Вода в цеху використовується для технологічних цілей: в теплообменниках, для промивки обладнання. Джерелом води є ріка Волга і артезіанський колодец.
Виробництво лежить у плотнонаселенном районі Татарстану — місті Казань, що забезпечує стабільний приплив робочої силы.
У Казані є низка навчальних закладів, які готують виробничі кадри. Інженерні кадри готуються в КГТУ.
Проте, враховуючи екологічну ситуацію тощо, зокрема підвищену фонову концентрацію шкідливих речовин у атмосфері, будівництво нового хімічного підприємства біля республіки припустиме лише при вдосконаленні установок для знешкодження відходів виробництва та відомості цих відходів до мінімального количеству.
Проектом передбачена очищення відведених газів базового провадження з метою охорони навколишнього среды.
2. Расчетно-технологическая часть.
2.1. Опис технологічної схемы.
Процес поділу відпрацьованих кислотних сумішей і концентрування слабкої HNO3 ведуть у колоні концентрування ГБХ (9). По трубопроводу 6.0. потрійна кислотна суміш вступає у сховище відпрацьованих сумішей (2).
З сховища відпрацьовані кислоти насосом (27) подаються у напірний бак (5). У напірних баках підтримується постійний рівень кислот, також вони мають переливную лінію, через яку надлишок кислот відводиться знову на сховища відповідних кислот. З напірного бака відпрацьовані кислоти через ротаметр (8) вступають у підігрівник (7), де підігріваються до t=80- 100 ОС. З метою зменшення кількості пара, який вводимо в колону, підігрів в подогревателе ведеться глухим пором, що надходять трубопроводом 3. З подогревателя відпрацьована потрійна суміш надходить на 6−9 царги (вважаючи згори) колони ГБХ, а слабка HNO3 (48−50%) трубопроводом 6.3 вступає у сховище слабкої HNO3 (2). З сховища (1) слабка HNO3 насосом (26) подається на 10 царгу колони ГБХ (9). Технічна H2SO4 (91−92%) з відділення концентрування слабкої H2SO4 перекачується у сховищі (3) концентрованої H2SO4 і звідси насосом (28) подається в напірний бак (6), з якої з t=(20−30 ОС) надходить на 4−6 царги колони (9). Усі три кислоти подаються у колону ГБХ одночасно. Також разом з подачею кислот для отгонки HNO3 і окислів азоту з суміші кислот й підтримки температурного режиму процесу, в днище колони (9) подають нагрітий водяний пар трубопроводом 2.3 з температурою рівної 250ОС абсолютне тиск нагрітого пара на трубопроводі 1,5 атм. Пара в колону подають із таким розрахунком, аби вміст HNO3 і окислів азоту в розведеною H2SO4, що з колони не перевищувало 0,03%.
Випаровування HNO3 з відпрацьованих сумішей кислот відбувається поза рахунок H2SO4, яка під'єднує себе воду, знижуючи цим парціальний тиск водяних парів в суміші. Випаровування HNO3 відбувається у середині колони, що з 11−13 царг HNO3, вільна від води, але з великим змістом окислів азоту в пароподібному вигляді піднімається в верхні царги колони № 6−9, де осушується H2SO4, водою, що вниз. Барботируя через шар H2SO4, пари HNO3 проходять царги 3−5, де звільняються й від бризок H2SO4. Звільнені від вологи пари HNO3 вступають у верхні дві царги колони — дефлегматор, де відбувається отдувка окислів азота.
Після проходження колони пари HNO3 з t (85−95 ОС) з кришки колони (9) вступають у конденсатор (10), у якому з допомогою охолодження до t=30−40 ОС відбувається конденсація HNO3 з пароподібного стану на рідке. Сконденсировавшись, охолоджена міцна HNO3 стікає у єдиний колектор конденсатора (10) й, оскільки вони містять дуже багато окислів азоту, то назад повертається у дефлегматор колони ГБХ (9), де, зустрічаючись із гарячими газами, що йдуть з четвертої царги колони, нагрівається до t=85 ОС. Звільнена від окислів азоту міцна 96−98% HNO3 вступає у холодильник (11) і охолоджена до t=30−40 ОС стікає до збірника концентрованої азотної кислоти (12), звідки іде складу і до потребителю.
Сірчана кислота, поступово насичуючи водою, стікає по царгам вниз. H2SO4, маючи контакт із нитрозными газами від прогнилою HNO3 утворює нитрозилсерную кислоту. З 20 по 22 царги (у зоні гідролізу) за нормальної температури H2SO4 150−160 ОС відбувається гідроліз нитрозилсерной кислоты.
Слабка 68−70% сірчана кислота із часткою оксидів трохи більше 0,003%, отримувана у процесі гідролізу з 22 царги колони з t=160−170 ОС, перекачується у відділення концентрування сірчаної кислоты.
Дистиляція HNO3 з відпрацьованих кислот і його концентрування супроводжується виділенням нитрозных газів. Це призводить як до значних збитків HNO3, до забруднення довкілля. Тому після конденсатора (10) несконденсировавшиесяя пари HNO3 направляються вентилятором (24) в поглотительные вежі (20−22), зрошувані кислотами різних концентраций.
Кожен абсорбера встановлено циркуляційні насоси (31), що з частині кожного абсорбера через холодильники (23) подають кислоту на зрошення, причому концентрація орошающей кислоти послідовно зростає зі колони (22) до (20). Вода для зрошення абсорбционной системи подається за останній у процесі абсорбер.
Охолодження циркулюючої кислоти необхідно тому що за взаємодії їх у вежі з окислами азоту вона нагрівається, а поглинаються окисли азоту краще, ніж холодніше кислота.
Температура поглинає кислоти 25−35 ОС.
Пари HNO3 і окисли азоту входить у абсорбер знизу, а орошающие кислоти згори, тобто рухаються противотоками. Орошающая кислота, контактуючи на поверхні насадки з нитрозными газами, стікає вниз, прохолоджуючи окисли азоту NO та поглинаючи HNO3. Циркуляція триває до того часу, поки вода, поглинаючи окисли азоту та пара, не перетвориться на слабку 48−50% HNO3, полі що хоче виводиться з добірки, а цикл накачують свіжу воду. Слабка HNO3 після абсорбера направляють у холодильник слабкої HNO3, де охолоджується до t=35 ОС, потім вступає у збірник (25) і насосом (34) перекачується в сховище (2) концентрування HNO3.
Через війну водної абсорбції зміст окислів азоту в газах знижується до 0,1−0,3%. Для остаточної доочищення гази вентилятором (28) направляють у абсорбер (22), зрошувану міцної H2SO4, котра надходить по трубопроводу 6.1. Після цього абсорбера гази із вмістом NOx 0,01−0,03% викидаються у повітря, а отримувана у своїй H2SO4 насосом перекачується на склад.
Концентрування відпрацьованою 70% H2SO4 ввозяться вихоровий ферросилидовой колоні (17), шляхом безпосереднього дотику гарячих топочных газів і кислоти. Гарячі гази, нагріті в топці (16) до t=800−900 ОС подаються на першу у процесі газового потоку щабель колони. Повітря в топку нагнітається воздуходувкой (32) а природного газу в топку подається трубопроводом 5,7. Відпрацьована 70% сірчана кислота з температурою 150−170 ОС з колони ГБХ відділення денитрации насосом (29) через проміжну ємність (14) подається п’ять щабель вихоровий колонны.
Контактування гарячих газів і кислоти в колоні ввозяться противоточном режимі. Топочные гази, вступники на першу щабель, піднімаючись вгору, взаємодіють в вихровому потоці з H2SO4 і десорбируют з її воду. H2SO4 перетікає з рівня на щабель вниз, міцнішає та виходить із першому місці контакту фаз як продукционной 91−92% H2SO4 в холодильник (19). З холодильника H2SO4 насосом перекачується у відділення денитрации у сховищі сірчаної кислоти (3).
Гарячі гази принаймні руху на колоні вгору віддають тепла і насичуються парами води. Температура відведених газів після верхньої брызгоуловительной щаблі становить 110−130 ОС.
Далі що відходять гази розладнуються до t=60−70 ОС в эжектирующем устрої (17) колони. Потім що відходять гази із вмістом кислих газів (0,1−0,2 г/м3) через трубу викидів (30) викидаються у повітря. Концентрування H2SO4 на щаблях вихоровий колони ввозяться высокотурболизированном вихровому висхідному жидкостном потоці, що дозволяє інтенсифікувати теплообменные процеси та підвищити надійність сепарації фаз при підвищених швидкостях газу, запобігти перегрів і розкладання сірчаної кислоти до сірчистого ангідриду (рис. 2.1).
2.2 Принцип роботи колони концентрування H2SO4.
Робота полягає в наступних принципах: 1. Застосування прямоточного взаємодії газової і переробки рідкої фаз у зоні контакту за збереження противоточного руху потоку по апарату загалом. 2. Використання вихрового руху газожидкостного потоку у зоні контакту фаз, забезпечує максимальну турбулизацию потоку, відновлення метафазной поверхні, широкий діапазон стійкості роботи контактних щаблів, і навіть ефективну сепарацію рідини на полі відцентрових сил. 3. Застосування вранішнього руху фаз у зоні контакту, забезпечує максимальний діаметр багатоступінчастих аппаратов.
Принцип прямоточного руху газової і переробки рідкої фаз ввозяться вихровому контактному устрої (рис. 2.2.), що складається з тарілки 3, на яку встановлено завихритель 5, і контактного патрубка 4.
Завихритель газового потоку розташований всередині контактного патрубка і виготовлений вигляді циліндра, має 8 тангенциально розташованих лопаток 6, їхнім виокремленням між собою тангенціальні щілини для проходу газа.
У частині контактного патрубка 4 є прорізу для проходу рідини. Завихритель розташований на нижньої царге 1, а контактний патрубок — верхній царге 2 щаблі. Подача рідини на щабель ввозяться нижню царгу, та її вихід із верхньої царги.
Контактирующий газ входить у щілину між лопатками завихрителя і набуває вращающее рух. Сірчана кислота з вышележащей щаблі по лінії перетікання вступає у нижню царгу щаблі, протікає через прорізу контактного патрубка у внутрішнє порожнину між завихрителем і внутрішньої стінкою контактного патрубка. Потік кислоти поділяється на 2 частини. Частина кислоти эжектируется всередину завихрителя і звідти вилітає з нього у вигляді крапель і струменів. Основна частина рідини розкручується газожидкостным потоком і рухається спіраллю вгору по внутрішньої стінці контактного патрубка. При цьому рідинна плівка безупинно бомбардируется краплями і струменями кислоти, вылетевшими з завихрителя і безупинно багаторазово оновлює свою поверхню. Виходить з щілин завихрителя свіжий газовий потік утворює вихори рідини, які зливаються і рухаються спіраллю в вихідному потоці як высокотурбулированного шару рідини, переважна більшість якого відсікається від газового потоку під вышележащей царгой, яка є отбойником. Частина сірчаної кислоти несеться газовим потоком на вышележащую ступень.
Кількість уносимой кислоти визначається видатками газової і переробки рідкої фаз, вступників на щабель. за рахунок віднесення певної кількості H2SO4 з рівня на щабель здійснюється такий розподіл концентрацій сірчаної кислоти на щаблях, коли він величини пересыщения парів сірчаної кислоти на щаблях не досягають критичного значення й виключаються умови освіти туману сірчаної кислоти. Отсепарированная у верхній царге сірчана кислота перетікає через зовнішній гидрозатвор на нижню царгу нижележащей щаблі. Сірчана кислота перетікає з рівня на щабель вниз, концентрується і надходить у нижню частина колони. У першій щаблі кислота газовим потоком як крапель і струменів по тангенциальному каналу вступає у днище колони, де розкручується газовим потоком й порушується як высокотурбулированного шару рідини, струменів, бризок по внутрішньої стінці днища колони вгору, до зони сепарації, розташовану між першою і другий сходами. Отсепарированная міцна (91−93%) сірчана кислота перетікає через штуцер із зони сепарації трубопроводом в холодильник.
Газовий потік, контактуючи на щаблях з кислотою, віддає їй своє тепло, звільняється з бризок кислоти в брызгоуловительных щаблях і з змістом кислих компонентів не більше санітарної норми викидається через трубу викиду газів у атмосферу.
2.3. Стандартизація. Технологічна характеристика сировини, напівфабрикатів, готового продукту. ГОСТ і технічні требования.
Технологічний процес регенерації відпрацьованих кислот дозволяє отримати концентровану HNO3 і H2SO4, від проводять мовлення вимогам відповідних стандартов.
1. Азотна кислота концентрована Таблиця № 3 — Технічні характеристики на HNO3 по ГОСТ 701–78 |№ |Найменування показників |Норми | | | |Вищий |I сорт |II сорт| | | |сорт | | | | |Зміст HNO3, в %, щонайменше |98,9 |98,2 |97,5 | | |Зміст H2SO4, в %, щонайменше |0,04 |0,05 |0,06 | | |Зміст окислів азоту N2O4, в %, не |0,2 |0,3 |0,3 | | |більш | | | | | |Зміст прокаленного залишку, в % |0,005 |0,015 |0,03 |.
2. Кислота сірчана технічна регенерированная (купоросное олію) Таблиця № 4 — Технічні умови на H2SO4 по ГОСТ 2184–77 |№ |Найменування показників |норми | | |Зміст H2SO4, в %, щонайменше |91,0 | | |Зміст нітросполук, в %, щонайменше |0,2 | | |Зміст прокаленного залишку, в % |0,4 | | |Зміст окислів азоту N2O3, в %, трохи більше |0,01 | | |Зміст заліза, в %, трохи більше |0,2 |.
3. Відпрацьовані і вичавлені кислоти є потрійну суміш азотної і сірчаної кислот, і навіть води. Таблиця № 5 — Склад потрійних сумішей |№ |Найменування складових частин |Відпрацьованою |Витисненою | | | |кислоти |кислоти | | |Азотна кислота, в % |15−22 |15−22 | | |Сірчана кислота, в % |35−40 |35−40 | | |Окисли азоту, в % |4−5 |0,5−1,0 | | |Вода, в % |33−46 |37−49,5 |.
4. Слабка сірчана кислота Таблиця № 6 Склад слабкої H2SO4 повинен відповідати умовам Держстандарту 1500−78 |№ |Найменування складових частин |Норми | | | | | |1. |Зміст сірчаної кислоти, в % |67−70 | | | | | |2. |Зміст азотної кислоти, в % |0,03 | | | | |.
Паливо (природний газ).
Природний газ має відповідати вимогам по ГОСТ 5542–70 Таблиця № 7 Технічні умови природного газу |№ |Найменування показників на 100 грн. Газа |Норми | | | | | | |Зміст сірководню в грн., трохи більше |2 | | |Зміст аміаку в грн., трохи більше |2 | | |Зміст синильної кислоти в грн., трохи більше |5 | | |Зміст смол і пилу в грн., трохи більше |0,1 | | |Зміст нафталіну в грн., трохи більше |10 | | |Зміст кисню в грн., трохи більше |1 |.
Природний газ використовується щоб одержати тепла при концентрировании кислот.
Сірчана кислота концентрована мусить бути виготовлено в відповідно до вимог справжнього стандарту технологічного регламенту, затвердженим у установленому порядку. По фізико-технічною показниками СК має відповідати нормам, зазначених у таблиці 8 по ГОСТ 2184–77.
Таблица № 8 |№ |Найменування показників |норма | | | |Контактна |Олеум вищий | | | |вищий |I сорт |вищого гатунку |I | | | |сорт | | |сорт | | |Зовнішній вид |Не нормується |Масляниста | | | | |рідина без | | | | |механічних | | | | |домішок | | |Масова частка моногидрата|92,5 |94 |92,5 |94 | | |(H2SO4), в % | | | | | | |Масова частка вільного |- |- |24 |24 | | |сірчаного ангідриду (SO3) в| | | | | | |%, щонайменше | | | | | | |Масова частка заліза, не |0,006 |0,015 |0,006 |0,01 | | |більш | | | | | | |Масова частка залишку |0,02 |0,03 |0,02 |0,03 | | |після прокаливания, %, не| | | | | | |більш | | | | | | |Масова частка |Не нормується |Не нормується | | |нітросполук, %, не | | | | |більш | | | | |Масова частка окислів |0,5 |0,0001 |0,0002 |0,0005 | | |азоту (N2O3), %, трохи більше| | | | | | |Масова частка миш’яку |0,8 |0,1|0,8 |0,1| | |(As), %, трохи більше | | | | | | |Масова частка хлористых |0,0001 |0,0005 |Не нормується | | |сполук, в %, трохи більше | | | | | |Масова частка свинцю |0,001 |0,01 |0,0001 |0,001| | |(Pb), %, трохи більше | | | | | | |Прозорість |Не нормується |Розведення | | |Колір в мл. розчину, |1 |2 |Не нормується | | |порівняння | | | |.
Властивості готових продуктів, сировини й полуфабрикатов.
1. Азотна кислота концентрована HNO3 в чистому вигляді - безбарвна рідина з їдким, ядушливим запахом; має питому вагу 1,5 гр/см3; 100% HNO3 плавиться за нормальної температури -42 ОС; кипить за нормальної температури +86 ОС. HNO3 на всі метали, крім срібла і платини. Зберігається і транспортується в алюмінієвих цистернах. На світу повільно розкладається з виділенням кисню і двоокису азоту NO2. Туман азотної кислоти і окису азоту як NO2, N2O3 викликає важкі отруєння. ГДК у робочої зоні - до 5 мг/м3 .
2. H2SO4 технічна, регенерированная. H2SO4 в чистому вигляді - прозору безбарвну рідину. Питома вага — 1,81−1,84 гр/см3. Температура кипіння безводній сірчаної кислоти 275 ОС, Температура плавлення 10,45 ОС.
Концентрована СК на холоді не діє метали, тому її можна зберігати в ємностях із чорного металу. ГДК туманообразной кислоти в повітрі робочої зони 1мг/м3. ].
2.4. Хімізм основних та побічних реакцій [4].
При що встановилася в денитрационной колоні ГБХ равновесном процесі, HNO3 з суміші кислот, що надходить у колону на тарілку випаровування, частково забирають нижележащие тарілки, звідки знову відганяється на тарілку випаровування. У процесі дистиляції, тобто отгонки HNO3 з потрійний суміші, поднимающиеся вгору пари збагачуються більш летючим компонентом — HNO3, а рухливу вниз рідина преходит менш летючий компонент — вода.
Процес випаровування HNO3 відбувається переважно у неповній середній частини колони. H2SO4, пройшовши цю зону, містить у собі розчинені окисли азоту, перехідні з потрійний суміші. Навіть у потрійний суміші було б розчинених окислів азоту, то, при частковому розкладанні HNO3 відбувається виділення окислів, які взаємодіючи з H2SO4, утворюють нитрозилсерную кислоту:
2H2SO4 + N2O3 = 2HNSO5 + H2O + 86 250 Дж.
Діоксид чи четырехоксид азоту, реагуючи з концентрованої H2SO4, утворює нитрозилсерную кислоту і азотну кислоту:
2NO2 + H2SO4 = HNSO5 + HNO3.
Процес розкладання нитрозилсерной кислоти із окислів азоту характеризується як процес денитрации. Проте термін «денитрация «служить для позначення процесу, зворотного этерификации. У разі більш правильно процес розкладання нитрозилсерной кислоти називати процесом гидролиза:
2HNSO5 + 2H2O = 2H2SO4 + 2HNO2.
2HNO2 = H2O + N2O3 (жид).
N2O3 (жид) = N2O3 (газ).
N2O3 (газ) = NO (газ) + NO2(газ).
Азотистая кислота (HNO2), що настає при гідролізі нейстойчива і распадается:
2HNO2 = H2O + HNO3 + 2NO.
Нитрозилсерная кислота є досить стійким з'єднанням, яке при концентраціях H2SO4 вище 70% не розкладається повністю навіть за температурі кипіння. При розведенні H2SO4 водою відбувається гідроліз нитрозилсерной кислоти, ступінь якої збільшується зі зниженням концентрації H2SO4 і підвищення температури .
Таблиця № 9 — Залежність ступеня розкладання HNSO5 від концентрації H2SO4 при 15−20 ОС |Концентрація |Ступінь разложения|Концентрация |Ступінь розкладання| |H2SO4, % |HNSO5, % |H2SO4, % |HNSO5, % | |98 |1,1 |81 |19,4 | |95 |4,0 |80 |27,7 | |92 |7,3 |70 |49,8 | |90 |12,4 |57,5 |100,0 |.
Як очевидно з залежності, починаючи з концентрації 57,5% H2SO4, нитрозилсерная кислота повністю відсутня. Відпрацьована H2SO4, що з колони, повинна містити мінімально можливу кількість окислів азоту. Це необхідно як щоб уникнути втрат N2O3, а й усунення нитрозилсерной кислоти, яка має сильно які руйнують свойствами.
Тому гідроліз HNSO5 в колоні ГБХ є важливим стадією процесу. Зі збільшенням температури, ступінь гідролізу HNSO5 збільшується. Утворений при розкладанні азотистої кислоти монооксид азоту незначно розчиняється в розведеною H2SO4. Гідроліз нитрозилсерной кислоти ведуть із допомогою перегрітого пара до 250 ОС водяної пари, що подається з таким розрахунком, щоб розведення кислоти конденсатом відповідало масової частки H2SO4 68−70%. У відпрацьованою H2SO4 міститься до 0,03% HNO3 і розчинених окислів азоту. Останні утворюють з H2SO4 до 0,01% HNSO5.
Після стадії денитрации слабка H2SO4 вирушає на стадію концентрування. У процесі концентрування розведеною H2SO4, наявні у ній домішки, зокрема, продукти неповного згоряння палива (коли концентрування ведеться безпосереднім зв’язком упариваемой кислоти з топочными газами), викликає розкладання H2SO4 внаслідок її відновлення до SO4. Відновлення переважно у день рахунок вуглецю, що міститься в примесях й у паливі по уравнению:
2H2SO4 + З = СО2 + 2SO2 + 2 H2O.
У результаті відбуваються деякі втрати кислоти у її упаривании. У процесі разгонки потрійний суміші в колоні утворюються нитрозные гази, що надходять на поглинання в абсорбери. Найпоширеніший спосіб поглинання нитрозных газів водою із заснуванням слабкої HNO3. На поглинання надходять нитрозные гази різного рівня окислення. Окисли азоту, які у нитрозных газах NO2, N2O4, N2O3 реагують із жовтою водою, але монооксид NO неспроможна реагувати з і для перекладу їх у HNO3 слід попередньо окислити його діоксиду азота:
2NO2 + H2O = HNO3 + HNO2 + 116 кДж.
N2O4 + H2O = HNO3 + HNO2 + 59,2 кДж.
N2O3 + H2O = 2HNO3 + 55,6 кДж.
Процес поглинання нитрозных газів водою пов’язані з розчиненням у ній діоксиду азоту, четырехоксида і трикосида азоту із заснуванням HNO3 і азотистої кислоты.
У газової середовищі вследствии взаємодії водяної пари з нитрозными газами, також виходить HNO3 і азотистая кислота, але у значному кількості. Новоутворена з допомогою нитрозных газів азатитсая кислота — малоустойчивое соединение.
2HNO2 = HNO3 + 2NO + H2O — 75,8 кДж.
Сумарна реакція освіти HNO3:
2NO2 + H2O = HNO2 + HNO3.
3HNO2 = HNO3 + 2NO + 2H2O.
____________________________________.
3NO2 + H2O = 2HNO3 + NO.
N2O3 + H2O = 2HNO2.
3HNO2 = HNO3 + H2O + 2NO.
_______________________.
3N2O3 + H2O = 2HNO3 + 4NO.
Позаяк у нитрозных газах міститься незначна кількість триоксида азоту, зазвичай технологічні розрахунки роблять за NO2. Як це випливає з формул 2/3 поглиненої діоксиду азоту йде освіту HNO3, 1/3 його виділяється як монооксиду азота.
Звідси випливає, що з поглинанні водою нитрозных газів неможливо тотальність NO2 перетворити на HNO3, позаяк у кожному циклі завжди 1/3 NOх буде виділятися в газову фазу. Монооксид азоту для подальшої переробки може бути окислен киснем до двоокису азоту по уравнению:
2NO + O2 = 2 NO2.
Получающаяся двоокис азоту знову реагує із жовтою водою, перетворюючись на 2/3 в HNO3, а выделившаяся окис азоту знову мусить бути окислена. Таким чином, весь процес поглинання розпадається на цілий ряд послідовно які протікають реакцій окислення NO в NO2 і отриману освіту HNO3 з NO2.
Проте, вказані поглинання є досконалими і нитрозные гази перед викидом у повітря слід додатково очистити від окислів азоту. Звідси випливає, що у останньому абсорбере зрошення ведеться не водою, а концентрованої сірчаної кислотою, яка до 0,003% поглинає окисли азоты, выбрасываемые у повітря гази відповідають санітарним нормам.
Через війну поглинання виходить нитрозилсерная кислота:
2 H2SO4 +N2O3 = 2 NHSO5 + H2O + 20 611 кал.
H2SO4 + 2 NO2 = NHSO5 + HNO3 + 5709 кал.
2.5 Інженерні решения.
У цей дипломний проект вводиться низка змін, вкладених у поліпшення технології переробки кислот і очищення відведених газов.
1. На фазі улову окислів азоту та парів азотної кислоти передбачається впровадження додаткової абсорбції відведених газів концентрованої H2SO4. сірчана кислота реагує з окислами азоту, створюючи нитрозилсерную кислоту, які потім знову направляють у колону ГБХ для переробки. Що Відходять гази з гаком змістом окислів азоту, викидаються в атмосферу.
2. Процес регенерації відпрацьованою кислоти перекладений автоматизоване управління із застосуванням УВМ, що знижує небезпека технологічного процесу підвищує якість продукції. Подача кислот в колону ГБХ автоматизовано. Передбачено автоматичне відключення подачі компонентів у разі аварии.
2.6. Розрахунок матеріального балансу відділення концентрування HNO3 [1].
Відділення денитрации і концентрування азотної кислоты.
Склад відпрацьованих кислот, вступників на денитрацию: як від нитрации HNO3 16−26%.
H2SO4 46−66%.
H2O 18−28% б) від абсорбционной установки.
HNO3 50%.
H2O 50%.
Вихідні дані для расчета.
— концентрація міцної азотної кислоти — 98%.
— концентрація сірчаної кислоти, що надходить колону — 91%.
— концентрація відпрацьованою кислоти, котра виходить з колони — 70%.
Розрахунок складено 1 тонну умовної відпрацьованою кислоти, котра надходить в колону ГБХ, враховуючи, що ОК — 80%, а суміш азотної кислоти та води — 20%.
Вибираємо середній склад кислот:
HNO3 27%.
H2SO4 45%.
H2O 28%.
Приймаємо, що у відпрацьованою кислоті 3% АК як окислів азоту пов’язані в нитрозилсерную кислоту за реакцією (1):
2H2SO4 + N2O3 [pic]2HNSO5 + H2O (1).
Перерахувавши склад кислот, получим:
HNO3 — 25%.
H2SO4 — 45%.
H2O — 26,1%.
N2O3 — 0,9%.
HNSO5 — 3%.
Усього — 100%.
У процесі разгонки кислотних сумішей і гідролізу HNSO5 в колоні протікають такі реакции:
— розкладання HNSO5.
2HNSO5 + H2O = 2H2SO4 + NO2 (2).
— розкладання HNO3.
2HNO3[pic]2NO2 + H2O + ½O2 (3) 2HNO3[pic] N2 + H2O + 2*½ O2 (4).
— розкладання N2O3 N2O3(газ) [pic]NO (газ) + NO2 (газ) (5).
В колону ГБХ надходить: 1. Відпрацьована кислота у кількості 1000 кг, У цьому числе:
HNO3 — 250 кг.
H2SO4 — 450 кг.
H2O — 261 кг.
N2O3 — 9 кг.
HNSO5 — 30 кг. 2. Купоросное олію 91% - x кг. 3. Перегрітий пар — у кг. 4. Повітря, подсасываемый з помещения Из колони виходить: 1. Разбавленная 70% H2SO4=[pic]кг 2. Міцна 98% HNO3 = [pic]=242,3 кг 3. Нитрозные гази, а колоні ½ кількості (1,5%) HNO3 розкладається до NO2 за реакцією (3) 242,3×0,015 = 3,64 кг. У цьому утворюються газоподібні речовини: NO2=[pic]=2,65 кг H2O =[pic]=0,52 кг O2 = [pic]=0,46 кг. б) за реакцією (4) розкладається Ѕ кількості (1,5%) HNO3 до N2: N2=[pic]=0,81 кг. H2O = [pic]=0,52 кг. O2 = [pic]=2,3 кг в) при розкладанні N2O3 за реакцією (5): NO2=[pic]=5,45 кг NO = [pic]= 3,55 кг р) при розкладанні HNSO5 за реакцією (2): NO2=[pic]=5,43 кг NO = [pic]= 3,54 кг.
Выделившаяся у процесі реакції сірчана кислота знову ввійде до складу відпрацьованою кислотною суміші і їх у останньої становитиме 450 кг. буд) з нитрозными газами несеться 1% HNO3: 242,3×0,01 = 2,42 кг.
Через війну гідролізу виходить таку кількість сухих нитрозных газів (не враховуючи подсоса повітря): | |g, кг |u, м3 | | | | | |NO2 |13,5 |6,87 | |NO |7,09 |5,29 | |N2 |0,81 |0,65 | |O2 |2,76 |1,93 | |HNO3 |2,42 |0,86 | |Усього |26,58 |15,6 |.
Подсос повітря uпод через неплотности сполук царг колони приймаємо рівним 100% обсягу сухих газів uпод = 15.6 м3, зокрема: N2=0,78*15,6=12,17 м³; O2=0,21*15,6=3,28 м³; чи N2=[pic]=15,21 кг; O2=[pic]=4,68 кг;
Разом: uпод=19,89 кг.
Приймаємо, що подсасываемый повітря надходить при t=20 ОС, відносна вологість 80%.
Кількість водяних парів, що у колону з повітрям (14,61*0,8)10−3*19,89=0,23 кг, де d0 = 14.61 [pic] - влагосодержание.
Усього повітря: 19,89+0,23=20,12 кг.
Кількість і склад сухих газів, які виходять із колони з урахуванням подсоса повітря: | |g, кг |u, м3 | | | | | |NO2 |13,5 |6,87 | |NO |7,09 |5,29 | |HNO3 |2,42 |0,86 | |N2 |16,02 |12,82 | |O2 |7,44 |5,21 | |Усього |46,47 |31,11 |.
Кількість водяної пари, що йдуть з колони (за конденсатом) з нитрозными газами при t=35 ОС.
H2O = [pic], для v= 30 м³ p=1,8 мм. Рт. У розділі ст — парціальний тиск води над 98% HNO3 при t=35 ОС p=133.3*1.8=239.9 Па.
H2O = [pic] кг обсягом v=[pic] нм3.
Загальний склад газів, вступників на поглинання: | |g, кг |u, м3 | | | | | |NO2 |13,5 |6,87 | |NO |7,09 |5,29 | |N2 |16,02 |12,82 | |O2 |7,44 |5,21 | |H2O |0,07 |0,057 | |HNO3 |2,42 |0,86 | |Усього |46,54 |31,12 |.
Таблиця № 10 — Зведений матеріальний баланс відділення концентрування HNO3 |Прихід: | | |1. Відпрацьована кислота |1000 кг. | |2. Купоросное олію |x кг. | |3. Перегрітий пар |у кг. | |4. Повітря через неплотности |19,89 кг. | |Разом: |1019,89+х+у | |Витрата: | | |1. Слабка H2SO4 70% |(450+х)/0,7 кг. | |2. Міцна HNO3 98% |242,3 кг. | |3. Нитрозные гази |46,54 кг. | |Разом: |(931,70+х)/0,7 |.
Прирівнюючи прихід до витраті, отримуємо рівняння матеріального баланса.
1019,89+х+у=931,7+[pic] у=0,43х-88,19.
2.7. Розрахунок теплового балансу [1].
Позаяк у рівнянні матеріального балансу входить розпад пара (у), то визначатимемо його з допомогою рівняння теплового расчета.
Вихідні данные:
1. Температура відпрацьованою кислоти, що надходить колону — 90 ОС.
2. Температура H2SO4 91% - 20 ОС.
3. Температура відпрацьованою кислоти H2SO4 70% - 170 ОС.
4. Температура які виходять із колони HNO3 і нитрозных газів — 85 ОС.
5. Температура HNO3 98% з конденсатора, що надходить у колону — 40.
ОС.
Температура міцної HNO3 98%, котра виходить з колони в холодильник 85 ОС.
6. Температура подсасываемого повітря 20 ОС.
Прихід тепла: 1) З відпрацьованою кислотою Q=q1*c1*t1=1000*2.22*90=119 800 кДж; (47 732.2 Ккал) c1=2,22[pic] - питома теплоємність відпрацьований кислоти за нормальної температури 90 ОС.
2) З перегрітою пором, теплосодержание якого за t=220 ОС одно 700.8 кДж; Q2=700,8*у 3) Теплота від H2SO4 складається з фізичної теплоти [pic] і теплоти розведення [pic].
[pic]=[pic]+[pic].
Фізична теплота визначається по формуле.
[pic]=[pic]=[pic]х кДж/(8.4x ккал).
[pic]=1,759 кДж/кг град — питома теплоємність H2SO4 91% при t=20 ОС.
Теплота розведення H2SO4 [pic]определяется різницею теплот розведення до70% і 91%.
Питома теплота розведення g=[pic]([pic]); n=H2O/H2SO4.
У H2SO4 з масової часткою 91%, моль:
H2SO4 = x 0,91/98 = 0,0094 х.
H2O = x 0,09/18 = 0,005 x n = 0,005 х/0,0094 x =0,53.
У H2SO4 70% моль:
Приймемо (450+х)/0,7=z.
H2SO4=z 0.7/98 = 0,007 z.
H2O = z 0.3/18 = 0,016 z n = 0,016 z/0.007 z = 2.38.
Питома теплота розведення [pic] H2SO4 з масової часткою 100% до 91%:
[pic]=[pic]=4066,1 [pic](17 036,8 [pic]).
Задовільно теплота розведення [pic] H2SO4 з 100% до 70%.
[pic] = [pic][pic]=10 174[pic](42 628,9 [pic]).
Питома теплота розведення з 91% до 70%:
[pic]=42 628.9−17 036.8=25 592.1[pic](6107.9 ккал).
[pic]=17,8*25 592,1=455 539,4 кДж (108 720,6 ккал).
[pic]=35,18х + 455 539,4 кДж (8,4*х + 108 720,6 Ккал) 4) З HNO3 98%, що надходить із конденсатора в колону з t=40 ОС.
[pic]=[pic] = 242,3*40*1,93=18 705,56 кДж (4464,3 Ккал) 5) З повітрям, подсасываемым із приміщення з t=20 ОС.
[pic]=[pic]=19,89*1*20=397,8 кДж (94,94 ккал).
[pic]= 1 кДж/кг град — питома теплоємність воздуха.
Загалом у колону прихід тепла, кДж.
[pic]+[pic]+[pic]+[pic]+[pic]=199 800 + 700,8 у + 35,18х + 455 539,4 + 18 705,56 + 397,8 = 674 442,76 + 35,18х + 700,8у.
Витрата тепла.
1) З парами HNO3 98%, які виходять із колонны:
[pic]=[pic]=0.98*242.3*1.936*85=39 075.43 кДж=9325,9 Ккал 2) На випаровування HNO3: [pic]=0,98*242,3*i=0,98*242,3*483=114 690,28 кДж=27 372,38 Ккал, де i=483кДж/кг — теплота випаровування 1 кг кислоты.
На випаровування 4% H2O, які у HNO3:
[pic]=[pic]*0,98*242,3*i=[pic]*0.98*242.3*2259=22 350.36 кДж, де i=2259 кДж/кг — теплота парообразования воды.
[pic]=[pic]+[pic]=114 690,28+22 350,36=137 040,64 кДж = 32 706,6 Ккал 3) Теплота, уносимая з 70% H2SO4 при t=150 ОС.
[pic]=([pic])*2,09*150=201 535,71+447,86х кДж.
[pic]=2,09 кДж/кг град — питома теплоємність H2SO4 70% 4) З HNO3 98%, уносимой з колони з t=85 ОС в холодильник:
[pic]=[pic]=242,3*1,93*85=39 749,32 кДж = 9486,71 Ккал 5) На нагрівання подсасываемого повітря із приміщення загалом до t=90 ОС.
[pic]=19.89(90−20)=1392.3 кДж 6) На закріплення які у відпрацьованою кислоті слабкої HNO3 у її масової частці в смеси:
[pic]*100%=49%.
Питома теплота для HNO3: g=n*8974/(n+1.737) ккал/моль.
У кислоті з масової часткою 49%, моль:
HNO3=250*0,49/63=1,94; H2O =250*0,51/18=7,08 n=7.08/1.94=3.65.
Питома теплота розведення для HNO3 98%:
[pic]ккал/моль=25 476,86 кДж/моль.
У кислоті з масової часткою HNO3 98%, моль:
HNO3=0,98/63=0,016; H2O =0,02/18=0,001 n=0.001/0.016=0.069.
Питома теплота розведення для HNO3 98%.
[pic]ккал/моль=1436,59 кДж/моль.
Теплота закріплення HNO3, що у відпрацьованою кислоті з 49% до 98%: [pic]=(25 476,86−1436,59)[pic]=89 017,7 кДж=21 245,27 Ккал 7) Теплота, уносимая з нитрозными газами: [pic]=[pic]q7*c7*t, де зудільні теплоємності газів з t=85 ОС |NO2 |13,5*0,75*85=865,92 кДж | |NO |7,09*0,996*85=600,2 кДж | |N2 |16,02*1,04*85=1416,17 кДж | |O2 |7,44*0,923*85=583,71 кДж |.
H2O 0,07*1,373*85 = 8,17 кДж.
HNO3 2,42*1,8*85 = 370,26 кДж.
Усього: 3843.73 кДж 8) Довколишню середу колона ГБХ протягом 1 години втрачає порядку 800 ккал.
(33 520 кДж). За умов подачі в колону 92 кг/хв потрійний суміші і формування колони 60 тиг в сутки.
Втрати тепла в навколишню среду:
[pic]=[pic]=6072,46 кДж.
Усього витрата тепла, кДж:
[pic]+[pic]+[pic]+[pic]+[pic]+[pic]+[pic]+[pic]=39 075,43+137 040,64+2015 35,71+447,86х+39 749,32+1392,3+89 017,7+3843,73+6072,46=517 727,29+447,86х.
Прихід приравним до расходу:
674 442,76+35,18х+700,8у=517 727,28+447,86х у=0,59х-223,62.
Вирішуємо спільно рівняння матеріального і теплового балансов:
0,43х-88,19=0,59х-223,62 х=847 у=276,11.
Таблиця № 11 — Матеріальний баланс денитрации і концентрування HNO3.
Розрахунок складено 1 тонну відпрацьованою кислоти |Прихід |Витрата | |статті приходу |кг |% |статті витрат |кг |% | |Відпрацьована |900 |42 |Міцна HNO3 98% |242,3 |11,3 | |кислота | | | | | | |50% HNO3 |100 |4,7 |Слабка HNO3 70% |1852,86 |86,5 | |Купоросное олію |847 |39,52 |Нитрозные гази |46,54 |2,2 | |Перегрітий пар |276,11 |12,88 | | | | |Повітря через |19,89 |0,93 | | | | |неплотности | | | | | | |Усього: |2143 |100 |Усього: |2143 |100 |.
Таблиця № 12 — Тепловий баланс концентрування азотної кислоти |Прихід |Витрата | |статті приходу |КДж |статті витрат |кДж | |З відпрацьованою |199 800 |З парами HNO3 98% |39 075,43 | |кислотою | | | | |З перегрітою паром|193 497,89 |На випаровуванні HNO3 |137 040,64 | |Теплота від H2SO4 |485 336,86 |З H2SO4 70% |581 546,53 | |91% | | | | |З HNO3 50% |18 705,56 |З HNO3 98% |39 749,32 | |з конденсатора | | | | |З повітрям |397,8 |На нагрівання повітря |1392,3 | | | |На закріплення |89 017,7 | | | |слабкої HNO3 | | | | |З нитрозными |3843,73 | | | |газами | | | | |Довколишню среду|6072,46 | |Усього: |897 738,11 |Усього: |897 738,11 |.
На 1 тонну відпрацьованою кислоти доводиться в 4.127 рази більше міцної 98% HNO3. Перелічимо на 1 тонну готового продукту 98% HNO3.
Таблиця № 13 — Норми витрати сировини для 1 тонни готового продукту 98% HNO3 |Прихід |Витрата | |статті приходу |кг |% |статті витрат |кг |% | |Відпрацьована |3714,3 |41,97 |Міцна HNO3 98% |1000 |11,3 | |кислота | | | | | | |50% HNO3 |412,7 |4,73 |Слабка HNO3 70% |7654,87 |86,5 | |Купоросное олію |3492,48 |39,52 |Нитрозные гази |194,69 |2,2 | |Перегрітий пар |1138,24 |12,88 | | | | |Повітря через |79,54 |0,9 | | | | |неплотности | | | | | | |Усього: |8849,6 |100 |Усього: |8849,6 |100 |.
2.8 Розрахунок матеріального балансу концентрування H2SO4.
Исходные дані: 1. Температура кислоти на вході 150 ОС 2. Температура кислоти не вдома 250 ОС 3. Температура димових газів на вході 900 ОС 4. Температура димових газів не вдома 130 ОС.
1. Втрати при концентрировании становлять 0,06%, їх 50% на разложение.
SO2 і 50% - втрачається на вигляді парів сірчаної кислоти У вихревую колону надходить разбавленная сірчана кислота (з урахуванням потерь):
Gразб = G (1−0,0006) = 7654,87*0,9994 = 7650,28 кг.
в тому числі води: [pic] = Gразб (1-[pic]) = 7650,28(1−0,7) = 2295,08 кг. У колону подається кислота (враховуючи моногидрат): Gпр = G (1−0.0006)[pic] = 7650,28*0,7 = 5355,2 кг. 2. При концентрировании сірчана кислота розкладається по формуле:
H2SO4 = SO2 + H2O + ½O2 Qразл = 228 900 кДж/кмоль — теплота розкладання H2SO4. Втрати від розкладання становлять 50% загальних втрат чи 0,03%:
Gпот = Gт*0,03/100 = 7650,28*0,0003 = 2,3 кг.
3. Втрати внаслідок віднесення сірчаної кислоти з димовими газами становлять також 50% загальних втрат (0,03%).
Gун = 0,0003*7650,28 = 2,3 кг.
4. Загальні втрати від составляют:
Gпот = Gун + Gразл = 2.3*2 = 4.6 кг.
5. Під час розкладання сірчаної кислоти утворюється: H2SO4 = SO2 + H2O + ½O2 [pic] = 98; [pic] = 64 SO2 = [pic] = 1,5 кг. O2 = [pic] = 0,38 кг. H2O = [pic] = 0,42 кг. 6. У колоні випарюються воды:
Gвых = Gразл[(1-Gисх/100)-(1-Gк/100)] = 7650.28[(1−70/100)-(1−91/100)] = 1606,56 кг. 7. Вихід 91% продукционной H2SO4: Gкон= GразлGразл[(1-Gисх/100)-(1-Gк/100)] ] = 7650.28−1606.56=6043.76 кг. 8. Прихід кислоти по моногидрату: Gпр = Gисх[pic] = 7650,28*0,7 = 5355,2 кг.
2.9. Розрахунок теплового балансу вихоровий колони [4].
Прихід тепла:
1. з розведеною сірчаної кислотою 70% при t = 150 ОС.
Q1 = QпрHпр = 7654.87*342 = 2 617 934.76 кДж = 624 805,43 Ккал. Hпр = 342 кДж/кг — энтальпия вихідної кислоты.
2. З димовими газами, які надійшли з топки:
Q2 = [pic] = 31,37х*1,45*900 = 40 937,85х кДж = 9770,37 Ккал. V2 = 31,37 м3 — обсяг газів С2 = 1,450 кДж/м3 град Общий прихід тепла: Qобщ = Q1+ Q2 = 2 617 934,76+40 937,85х кДж.
Витрата тепла.
1. З продукционной кислотою при 250 ОС:
Q1 = Ck*Hk = 5355.2*458 = 2 452 681.6 кДж = 585 365,54 Ккал Hк = 458 кДж/кг — энтальпия сірчаної кислоти 91%.
2. З водяникам пором виділяється при выпаривании і разложении:
Q2 = Cвп*Hвп = 1606.98*2737.7 = 4 399 429.15 кДж = 1 049 983.09 Ккал Gвп = Gуп + Gразл = 1606,56 + 0,42 = 1606,98 кг. Hвп = 2737,7 кДж/кг — энтальпия водяної пари Gуп і Gразл — з матеріального баланса.
3. З димовими газами, зникаючими з t = 30 ОС: Q3 = [pic] = 31,37х*1,336*130 = 5448,34х кДж = 1300,32 Ккал. V2 — обсяг димових газів на м3 спалюваного газу С2 = питома теплоємність димових газів при t=130 ОС С2 = 1,336 кДж/м3 град.
4. На випаровування сірчаної кислоти: Q4 = Gисп + Hисп=2,3*511,2=1175,76 кДж=280,61 Ккал Нисп=511.2 кДж/кг — питома теплота парообразования сірчаної кислоты.
5. З парами сірчаної кислоты:
Q5 = Gисп + H = 2,3*201,4=463,22 кДж=110,55 Ккал М — энтальпия 100% сірчаної кислоти за нормальної температури відведених газів 130 ОС.
6. На розкладання сірчаної кислоты:
Q6 = [pic] = [pic]=5372,14 кДж = 1282 ккал.
7. З продуктами розкладання сірчаної кислоти внаслідок розкладання сірчаної кислоти за нормальної температури відведених газів 130 ОС образуются:
[pic]=1,5 кг.; =0,38 кг.; [pic]=2,3 кг Q7 = ([pic]*[pic] + [pic]*[pic])t=(0.963 + 0.353)130 = 171.08 кДж = 40,83 ккал.
8. При концентрировании сірчаної кислоти (дегідратації) від 70% до 91% витрачається тепла:
Q8=Gуп (Q70%- Q91%) Q70% = 427,4 кДж/кг — теплота розведення до70% Q91% = 157,3 кДж/кг — теплота розведення до 91% Q8 = 5355,2(427,4−157,3)=1 446 439,52 кДж = 345 212,3 ккал.
9. Втрати тепла в довкілля приймемо 1% від загальної кількості витрати тепла на концентрировании сірчаної кислоты:
Q= 2 452 681,6 + 4 399 429,15 + 5448,34х + 463,22 + 1175,76 + 5372,14 + 171,08 + 1 446 439,52 = 5 853 050,87 + 5448,34 x кДж Qд = 58 530,51 + 54,48 x к`Дж Qрасх = 5 911 581,38 + 5502,82 x кДж.
10. Для визначення витрати паливаприравниваеме прихід тепла до витраті: Qобщ = Qрасх.
2 617 934,76+40 937,85х=5 911 581,38+5502,88х.
35 435,03х=3 293 646,62 х=92.95.
11. Визначаємо годинникове кількість і склад газів, вступників на установку з топки. Таблиця № 14 — Кількість і склад газів з топки |гази |м3 |кг. | |CO2: 1,27*92,95 |118,5 |231,87 | |N2: 24,43*92,95 |2270,77 |2838,46 | |O2: 4,03*92,95 |374,59 |535,13 | |H2O: 2,68*92,95 |249,11 |200,17 | |Усього |3012,52 |3805,63 |.
12. Визначаємо годинникове кількість газів, що йдуть з установки: Таблиця № 15 — Годинникове кількість газів |гази |м3 |кг. | |CO2: [pic]*х=1,27*92,95 |118.05 |231.87 | |N2: [pic]*х=24,43*92,95 |2270.77 |2838.46 | |O2: [pic]=374,59+0,38*22,4/32 |374.86 |535.51 | |SO2: [pic]22.4/64 |0,53 |1,5 | |H2O: [pic]+[pic] |2249,43 |1807,58 | |H2SO4: [pic]*22,4/98 |0,53 |2,3 | | | | | |Усього |5014,7 |5417,22 |.
Таблица № 16 — Матеріальний баланс концентрування сірчаної кислоти |Прихід |Витрата | |статті приходу |кг |% |статті витрат |кг |% | |Гази з топки |3805,63 |33,2 |Гази в аотмосферу |5417,22 |46,26| |Сірчана кислота 70%|7654,87 |66,8 |сірчана кислота 91%|6043,72 |52,72| | | | |Пари сірчаної |2,3 |0,02 | | | | |кислоти | | | |Усього: |11 460,5 |100 |Усього: |11 460,5 |100 |.
Таблица № 17 — Тепловий баланс концентрування сірчаної кислоти |Прихід |Витрата | |статті приходу |КДж |Статті витрати |кДж | |З сірчаної кислотою |2 617 934,76 |З сірчаної кислотою |2 452 681,6 | |70% | |91% | | |З димовими газами |6 423 107,92 |З водяником пором |4 399 429,15 | | | |З димовими газами |672 179,0 | | | |На випаровування |1175,76 | | | |сірчаної кислоти | | | | |Теплота разложения|5372,14 | | | |З продуктами |171,08 | | | |розкладання | | | | |Теплота |1 446 439,52 | | | |дегідратації | | | | |Втрати в |63 594,43 | | | |довкілля | | |Усього: |9 041 042,68 |Усього: |9 041 042,68 |.
3. Техніко-технологічна часть.
3.1. Вибір і розрахунок продуктивності основного і допоміжного устаткування технологічної схемы.
З заданої продуктивності проектованого провадження у готової продукції (98% HNO3) визначаємо добову і годинну продуктивність основного апарату цеха-колонны ГБХ.
Псут=[pic], где.
Пгод-10 000 т/рік n — час на: ремонт і простої оборудования.
Псут=[pic]=29,85 т/сут.
Пчас=[pic]=1,24 т/час.
При отгонке концентрованої HNO3 певного складу витрата безводній H2SO4 залежить від масової частки H2SO4 в розведеною HNO3, при цьому витрати H2SO4 тим більше, чим сильніший розбавлена HNO3. Для однієї й тією самою вихідної разбавленнной HNO3 питома витрата H2SO4 назад пропорційний її ступеня концентрації. Відповідно до розрахунком по трикутним диаграммам (услович — Температура кипіння суміші на палицях) при масової частці HNO3 48−50% та програмах технічної H2SO4 91−92% співвідношення HNO3: H2SO4 становить 1:32 при вихідної HNO3 50% і H2SO4 92%. З сказаного вище, річна продуктивність по H2SO4 дорівнюватиме 32 000 т/год.
[pic]=[pic].
Розрахуємо добову і годинну продуктивність вихоровий колонны:
Псут=[pic]=95.52 т/сут.
Пчас=[pic]=3,98 т/час.
3.2 Розрахунок кількості аппаратов.
n=[pic].
Пгод — річна производительность.
Пчас — годинна производительность.
КІО — коефіцієнт використання оборудования.
Тэф — ефективний фонд часу роботи апарату, год Денитрационная колона ГБХ Тэф=8040 час/год КИО=0,95 Пгод=10 000 т/рік Пчас=1,24 т/час n=[pic]=1.1 прим Вибираємо 1 апарат Вихрова колонна.
Тэф=8040 ч/год.
КИО=0,9.
Пгод=32 000 т/год.
Пчас=3,98 т/час n=[pic]=1.1 шт.
Вибираємо 1 апарат Абсорбер для улову парів азотної кислоти і окислів азота:
Тэф=8760−1404 =7365 ч.
КИО=0,86.
Пгод=5 337 000 т/год.
Пчас=5 337 000/7356 =725,5 т/час n=[pic]=3,8 прим Вибираємо 4 абсорбера.
4. Конструктивно-механические расчеты.
4.1 Розрахунок числа щаблів контакту фаз концентратора [5].
Визначення числа щаблів концентратора сірчаної кислоти при концентрировании від 70% мас до 91−92% мас H2SO4 проводимо аналітичним методом. При нагріванні сірчаної кислоти до 260−280 ОС продукционную 92% H2SO4 можна отримати одному щаблі. Однак цьому зміст сірчаної кислоти в парах сягає 30−50 г/м3, що зумовлює значному газовому викиду. Для зменшення вмісту у парах, сірчану кислоту концентрують в 2−3 східчастих апаратах, проте, при цьому пересыщение парів H2SO4 у другого ступеня перевищує критичне значення більш, ніж у 30 раз: Sкр>[pic]=3,3, це відбувається освіту туману сірчаної кислоти. Концентрація кислот на другий щаблі до роботи концентратора як без освіти туману сірчаної кислоти повинна бути 85−90% мас, температура 240 ОС.
Аналітичне визначення числа щаблів, концентрації та температур H2SO4 на щаблях концентратора, працюючого без освіти туману, представлено в таблиці .
Таблиця № 18 — Кількість щаблів, концентрації та температури сірчаної кислоти на щаблях концентратора. | |Сходинки концентратора | | |1 |2 |3 |4 |5 | | | | | | | | |1. Температура газу, ОС | | | | | | |на вході |850 |230 |210 |190 |175 | |не вдома |230 |210 |190 |175 |160 | |2. Концентрація H2SO4, % | | | | | | |на вході |88 |84 |80 |75 |70 | |не вдома |92 |88 |84 |80 |75 | |3. Температура H2SO4, ОС |220 |200 |180 |165 |150 | |Тиск насичених парів H2SO4, | | | | | | |Па | | | | | | |на вході |200 |56 |16 |2,2 |0,47 | |не вдома |960 |200 |56 |16 |2,2 | |5. Пересыщение, P. S | |4,8 |3,57 |3,5 |7,3 | |6. критичний стан, Sкр | |4,5 |6 |7,1 |12,27 | |7. Ставлення: P. S: Sкр | |1,07 |0,6 |0,5 |0,6 |.
Беручи рівними ефективності щаблів вихоровий колони по температурі, массоотдаче у газовій і переробки рідкої фазах для процесів десорбции водяної пари і абсорбції парів сірчаної кислоти, задаємось розподілом концентрації (xi) і температур (ti) сірчаної кислоты.
Таблиця № 19 | |Сходинки концентратора | | |1 |2 |3 |4 |5 | | | | | | | | |1. Температура газу, ОС | | | | | | |на вході |850 |250 |210 |190 |175 | |не вдома |250 |210 |190 |175 |170 | |2. Концентрація H2SO4, % мас. | | | | | | |на вході |89 |85 |81 |76 |70 | |не вдома |92 |89 |85 |81 |76 | |3. Тиск насичених парів H2SO4, | | | | | | |Па | | | | | | |на вході |250 |56 |16 |2,2 |0,47 | |не вдома |980 |250 |56 |16 |2,2 | |4. Пересыщение, P. S |3,8 |4,5 |3,5 |7,3 | | |5. Критичний пересыщение, Sкр |4,3 |6 |7,1 |12,27 | | |6. Ставлення: P. S: Sкр |0,88 |0,75 |0,49 |0,59 | | |7. Брызгоунос на 1 кг поданого на |0,319 |0,318 |0,317 |- |- | |щабель кислоти | | | | | |.
1. Визначаємо витрати СК на щаблях вихоровий колони [Li, (i=1−5)] Li=Li+1*[pic], кг/час.
Кількість слабкої H2SO4, що надходить у колону (з матеріального балансу) становить: L6= 7654.9 кг, температура кислоти t6=150 ОС, концентрація C6=70%, [pic]=1,494 т/м3.
Кількість сірчаної кислоти, що надходить із п’ятої четверту щабель: L5=[pic][pic]=7654.9*0.7/0.75=7143 кг/ч (4687,5 м³ /год) X5=0,75; t5=165 ОС, [pic]=1,524 т/м3.
Кількість СК, що надходить з четвертої на третій щабель: L4=[pic][pic]=7143*0.75/0.8=6696.6 кг/ч (4273.49 м3 /год) X4=0,8; t4=180 ОС, [pic]=1,567 т/м3.
Кількість СК, що надходить з третьої другу щабель: L3=[pic][pic]=6696,6*0.8/0,84=6377,7 кг/ч (4059,6 м³ /год) X3=0,84; t3=200 ОС, [pic]=1,571 т/м3.
Кількість СК, що надходить із другий на першу щабель: L2=[pic][pic]=6377,7*0.84/0,88=6087,8 кг/ч (3848 м3 /год) X2=0,88; t2=220 ОС, [pic]=1,582 т/м3.
Кількість продукционной СК, котра виходить з першої ступени:
L1 =[pic][pic]=6087,8*0.88/0,92=5823,1 кг/ч (3653,14 м³ /год) X1=0,92; t1=250 ОС, [pic]=1,594 т/м3.
По рівнянню і табличным значенням (таблиця № 19) визначаємо равновесные концентрації парів сірчаної кислоти на щаблях колони: [pic], Па.
Розраховуємо значення пересыщения парів H2SO4 на щаблях колони: S=yi-1/yi; і = 2−5.
По рівнянню [pic][5].
Розраховуємо значення критичного пересыщения парів H2SO4 на щаблях колони Sкр-Sкр5.
Визначаємо співвідношення Si/ Sкрi на щаблях колони. При Si/Sкрi [pic]1 відбувається освіту туману H2SO4, а при Si/Sкрi.