Технология неконцентрированной азотної кислоты
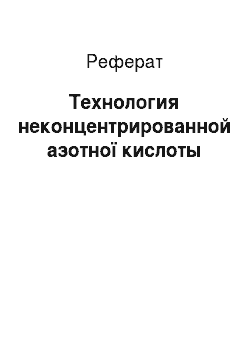
Попередня очищення газів збільшує тривалість роботи каталізатора. Однак згодом каталізатор поступово отруюється і вихід NO знижується. Для видалення отрут і забруднень сітки періодично регенерують у вигляді обробки їх 10−15% розчином соляної кислоти. 5. Час контактування. Оптимальний час контактування визначається швидкістю окислення аміаку. Найчастіше швидкість окислення визначають… Читати ще >
Технология неконцентрированной азотної кислоты (реферат, курсова, диплом, контрольна)
Міністерство загального користування та професійного образования.
Російської Федерации.
Пермський державний технічний университет.
Хіміко-технологічний факультет.
РЕФЕРАТ за курсом технології неорганічних речовин на тему:
Технологія неконцентрированной азотної кислоты.
Виконав: студент групи ХТБ-95.
Нагірний О.В.
Проверил:
Островський С.В.
Пермь, 1998.
Введение
… …3 1. Сировинна база технології… …3 2. Сучасне стан технології виробництва неконцентрированной азотної кислоти… …5 3. Обгрунтування оптимальних параметрів основного технологічного процесса…10 4. Технологічна схема виробництва, аппаратурное оформлення основних технологічних процесів… …14 5. Перспективи розвитку й удосконалення технологии…20 Список використаної літератури… …22.
Азотна кислота за обсягом виробництва посідає серед інших кислот друге місці після сірчаної кислоти. Усі зростаючий обсяги виробництва HNO3 пояснюється величезним значенням азотної кислоти і його солей для народного хозяйства.
Азотна кислота одна із вихідних продуктів щоб одержати більшості азотсодержащих речовин. До 70−80% її кількості витрачається отримання мінеральних добрив. Одночасно азотна кислота застосовується і при отриманні вибухових речовин майже всіх видів, нітратів та інших технічних солей; у промисловості органічного синтезу; в ракетної техніці, як у різних процесах та у багатьох інших галузях народного хозяйства.
Промисловістю виробляється некоцентрированная (до 60−62% HNO3) і концентрована (98−99% HNO3) кислота. У невеличких обсягах випускається реактивна і азотна кислота особливої чистоти. У виробництві вибухових речовин нитрованием толуолу, уротропина, ксилола, нафталіну та інших цих продуктів застосовують концентровану азотну кислоту. Для отримання добрив споживається зазвичай разбавленная азотна кислота.
Основними виробниками азотної кислоти є США, Франція, ФРН, Італія, Іспанія, і Англія. Перед цих країн 70-ті роки доводилося понад 75% усієї спродукованої тоді кислоти. До 80 років виробництво азотної кислоти в капіталістичних країнах стабілізувалося. Зараз зростання виробництва відбувається поза рахунок удосконалювання й відновлення технології, і навіть організації випуску азотної кислоти в странах.
1. СИРОВИННА БАЗА ТЕХНОЛОГИИ.
Основною сировиною для неконцентрированной азотної кислоти нині є аміак, повітря і вода. Допоміжними матеріальними і енергетичними ресурсами є каталізатори окислення аміаку і очищення відпрацьованих газів, природного газу, пар і электроэнергия.
Аміак. У умовах є безцветный газ з різким запахом, добре розчинний у воді й інших розчинниках, утворює гемиі моногидраты. Поворотним етапом у розвитку виробництва синтетичного аміаку стало застосування великого зараз у промисловості методу отримання водню конверсією метану, що міститься в природному газі, в попутних нафтових гази та продуктах нефтепереработки.
Зміст домішок в рідкому аміаку регламентується ГОСТ 6221–82. Найтиповішими домішками є вода, мастила, катализаторная пил, окалина, карбонат амонію, розчинені гази (водень, азот, метан). При порушенні ГОСТ які у аміаку домішки можуть потрапити до аммиачноповітряну суміш і знизити вихід оксиду азота (II), а водень і метан можуть змінити межі взрываемости АВС.
Повітря. Для технічних розрахунків приймають, що сухе повітря містить [%, про]: N2 — 78,1, О2 — 21,0, Ar2 — 0,9; Н2О- 0,1−2,8.
У повітрі можуть бути присутні також сліди SO2, NH3, CO2. У районі промислових майданчиків повітря забруднене пилом різного походження, а також різноманітними компонентами неорганізованих газових викидів (SO2, SO3, H2S, С2H2, Cl2 та інших.). Кількість пилу повітря становить 0,5−1,0 мг/м3.
Вода. Використовується у виробництві азотної кислоти для зрошення абсорбционной колони, розробки пара при утилізації тепла в казанахутилизаторах, для охолодження реакційних апаратів. Для абсорбції оксидів азоту використовують найчастіше паровий конденсат і хімічно очищену воду. У деяких схемах дозволено застосовувати конденсат сокового пара аміачної селітри. У кожному разі вода, використовувана для зрошення колон, має утримувати вільного аміаку i твердих суспензій, зміст хлорид-иона має не більше 2мг/л, олії трохи більше 1мг/л, NH4NO3-не більш 0,5 г/л. Хімічно очищена вода для котлів-утилізаторів має відповідати вимогам ГОСТ 20 995–75.
Технічна вода, призначена це про людське тепла в теплообменниках і охолодження устаткування (зворотний вода), повинна відповідати наступним требованиям:
Жорсткість карбонатная, мэкв/кг Не більш 3,6.
Зміст зважених речовин, мг/кг Не більш 50.
Значення pH 6,5- 8,5.
Кисень. Застосовується переважно у виробництві концентрованої азотної кислоти методом прямого синтезу. У окремих випадках використовується для збагачення АВС і при отриманні неконцентрированной азотної кислоты.
2. СУЧАСНЕ СТАН ТЕХНОЛОГІЇ ВИРОБНИЦТВА НЕКОНЦЕНТРИРОВАННОЙ.
АЗОТНОЇ КИСЛОТЫ.
Азотна кислота головним чином її природна сіль — натрієва селітра відомі з давнини. У 778 р. Арабський учений Гебер описав спосіб приготування «міцної горілки» (так називалася тоді азотна кислота) шляхом перегонки селітри з квасцами. У перші прописи із виробництва азотної кислоти з селітри було укладено М. В. Ломоносовым.
На початок ХХ століття природна селітра була єдиною джерелом отримання азотної кислоти. Цей процес відбувається грунтується ось на наступній реакции:
NaNO3 + H2SO4 = HNO3 + NaHSO4.
Удосконалений варіант цього отримання азотної кислоти стало те, що розкладання селітри сірчаної кислотою вироблялося в вакуумі (залишкове тиск до 650 мм вод.ст.). У цьому температура розкладання селітри знижувалася до 80−1600С; тривалість отгонки кислоти скорочувалася до 6 годинників та досягався вихід азотної кислоти близька до теоретичного. Витрата пального для обігріву реактора становила близько 120 кг/т HNO3. Такий спосіб отримання азотної кислоти, повністю залежить від імпорту чилійської селітри, згодом був оставлен.
На початку ХХ століття було вирішено винятково важлива проблема зв’язування атмосферного азоту, що було людству новий невичерпний джерело сировини для азотсодержащих сполук. Відомо, що над кожним квадратним кілометром земної поверхні повітря міститься близько 8000 тис. тонн азоту. Завдання перетворення інертного азоту в хімічно активні речовини (NO, NO2, HNO3) розв’язано нелегку для результаті послідовних зусиль багатьох ученых.
Ще 1781 р. Кэвендиш внаслідок електричного розряду в повітрі отримав окисли азоту. У 1814 р. В.М. Каразін запропонував про «низведении електрики з верхніх верств атмосфери для селітри». Перший патент на спосіб отримання азотної кислоти з допомогою електричного розряду повітря і перетворення окислів азоту в нітрити й у нітрати було отримано Лефебр в 1859 г.
У 1901 р. Було належить початок фіксації азоту повітря на полум’я електричної дуги (дугового метод). У 1902 р. У споруджено завод по фіксації атмосферного азоту з допомогою електричної дуги, виникає при пропущенні між електродами струму силою 0,75 чи напругою 8000 в печі конструкції Брэдлея і Ловджоя. Через недосконалість конструкції печі і великого витрати електроенергії завод закрили в 1904 г.
Виробництво азотної кислоти дуговим методом цікаво тим, що у ньому використовували дешеве вихідне сировину — повітря. Аппаратурное оформлення процесу досить нескладно. Проте задля його здійснення вимагалося дуже багато електроенергії, що досягає 70 000 квт*ч на 1 т N2 (це відповідає 64 т умовного топлива).
Нарешті, в 1913 р. з урахуванням численних робіт було освоєно промисловий метод синтезу аміаку з простих речовин, який одержав значне поширення й у час зайняв чільне місце у виробництві пов’язаного азоту. Згодом вдалося розв’язати проблему отримання азотної кислоти з аммиака.
Нині промислового виробництва азотної кислоти складає основі контактного окислення синтетичного синтетичного аміаку. Процес складається з основних стадій: отримання окису азоту та переробка їх у азотну кислоту.
Стадія окислення аміаку в окис азоту загалом виражається уравнением.
4NH3 + 5O2 = 4NO + 6H2O.
Стадія окислення окису азоту у вищі окисли азоту NO та переробки їх в азотну кислоту то, можливо представлена уравнениями.
2NO + O2 = 2NO2.
3NO2 + H2O = 2HNO3 + NO.
Сумарну реакцію не враховуючи побічних реакцій, проходять з освітою елементарного азоту NO та інших сполук, можна сформулювати уравнением.
NH3 + 2O2 = HNO3 + H2O +421,2 кдж.
Відповідно до послідовністю цих стадій розглянемо технологію виробництва азотної кислоты.
Дослідження свідчать, що з окислюванні аміаку в різних катализаторах і залежно та умовами ведення процесу можна було одержати окис азоту, елементарний азот і закис азота:
4NH3 + 5O2 = 4NO + 6H2O +907,3 кдж.
4NH3 + 4O2 = 2N2O + 6H2O +1104,9 кдж.
4NH3 + 3O2 = 2N2 + 6H2O +1269,1 кдж.
З іншого боку, можливі й інші побічні реакції, що проходять із освітою азоту й без участі каталізатора. До таких реакцій ставляться розкладання окису азоту та взаємодія аміаку з окисом азоту. У газах після окислення аміаку може бути також непрореагированный аммиак.
Термодинамические розрахунки зміни вільної енергії показують, що наведені вище основні реакції не можуть іти практично остаточно. Отже, при окислюванні аміаку як у процесі, може протікати в декількох напрямах, склад кінцевих продуктів визначатиметься передусім виборчої здатністю каталізатора. Відповідно підбираючи каталізатор й умови ведення реакції, можна змінити й склад одержуваних продуктов.
З використанням як каталізатор платини вихід окису азоту в інтервалі температур 700−8500С може становити 97−98%. Каталізатори з платинових сплавів найкращі для виборчого окислення аміаку в окис азота.
Реакція окислення аміаку до окису азоту йде із незначною зміною обсягу, тому зміна тиску не надає істотного впливу рівноважний вихід продуктів взаємодії. Великі величини константи рівноваги цієї реакції (1053 при 9000С) свідчить про практичної її необоротності при промислових умовах здійснення процесса.
Платиновим катализаторам надають сітчасту форму, що дозволяє застосовувати контактні апарати простого типу. Зазвичай катализаторные сітки виготовляють з дроту діаметром 0,05−0,09 мм. Відповідно до Держстандарту 3193−59 для виготовлення сіток застосовуються сплави наступного складу: Pt+4%Pd+3,5%Rh (для контактних апаратів, які працюють при атмосферному тиску) і Pt+7,5%Rh (для конвертерів, працюючих при підвищеному тиску). При окислюванні аміаку під атмосферним тиском встановлюють від 2 до запланованих 4 сіток (зазвичай 3 прим.). У апарати працюючі під тиском 8 ат, закладають від 16 до 18 сеток.
У оптимальних умовах ступінь перетворення аміаку в окис азоту на однієї сітці може становити 86−90%, двома сітках — 95−97%, на трьох — 98%.
На нових сітках високий рівень конверсії досягається не відразу, а протягом кількадобового роботи за 6000С. Процес активації сіток при 9000С закінчується через 8−16 годин. Поверхня платинових сіток в процесі експлуатації сильно разрыхляются, гладкі блискучі нитки стають губчатыми і матовими. Внаслідок цього сильно розвивається поверхню каталізатора, що зумовлює підвищенню його активності. З часом розпушення поверхні платинових сіток призводить до їхнього сильному руйнації та очі великою втрат платини. Додавання до платині родію й паладію має двояке значення: по-перше, підвищується активність каталізатора, по-друге, зменшуються втрати катализатора.
У промисловості застосовуються комбіновані каталізатори, в яких поруч із платиною використовують і інші, дешевші матеріали. Розроблений ГИАПом комбінований двоступінчастий каталізатор складається з сітки потрійного сплаву (перша щабель) і шару неплатинового каталізатора завтовшки 50−65 мм (другий ступінь). Застосовуючи железохромовый каталізатор, у другого ступеня окислення можна досягти 96%-ного перетворення аміаку в окис азота.
Нитрозные гази, отримані контактним окисленням аміаку, містять переважно окис азоту, з якої при подальшому окислюванні виходять вищі окисли азоту. Освіта їх протікає за такими уравнениям:
2NO + O2 = 2NO2.
NO + NO2 = N2O3.
2NO2 = N2O4.
Із зниженням температури рівновагу всіх таких реакцій зміщується вправо. При низьких температурах, наявності надлишку кисню і часу достатньому задля встановлення рівноваги, очікується переходу всіх окислів азоту в четырехокись N2O4. Коли кисню або за несталому рівновазі в нитрозных газах можуть бути присутні одночасно на всі зазначені окисли (NO, N2O3, NO2 і N2O4).
Пятиокись азоту N2O5 з окислів за умов окислення не утворюється: закис азоту N2O киснем повітря далі не окисляется.
Окисли азоту переробляють в неконцентрированную азотну кислоту у вигляді їх поглинання з газової фази водою чи розведеною азотної кислотою. І тому нитрозные гази охолоджують і скеровують в поглотительные башти чи абсорбционные колони, де відбувається окислювання NO і поглинання які утворилися окислів азоту. Залежно та умовами охолодження і окислення у газовій фазі можуть бути присутні різні окисли азоту, які реагують із жовтою водою по реакциям:
2NO2 + H2O = HNO3 + HNO2 +27,73 ккал.
N2O4 + H2O = HNO3 + HNO2 +14,13 ккал.
N2O3 + H2O = 2HNO2 +13,3 ккал.
З практичного погляду має значення, що реагує з водою — двоокис чи четырехокись азоту, оскільки їхнє взаємного перетворення дуже великий, а кількість які виникають з NO2 і N2O4 азотистої і азотної кислот одинаково.
Процес отримання азотної кислоти пов’язані з розчиненням у питній воді NO2, N2O4 і N2O3. У газової фазі внаслідок взаємодії водяної пари з окислами азоту утворюється також незначна кількість азотної і азотистої кислот.
Азотистая кислота малоустойчива і розкладається із заснуванням азотної кислоти і окису азоту по сумарною реакции.
3HNO2 = HNO3 + 2NO + H2O -18ккал.
Розрахунки вчених показують, що з умовах рівноважний зміст азотистої кислоти в розведеною азотної кислоті обмаль. Швидкість розкладання азотистої кислоти на підвищення температури різко зростає, але й при звичайній температурі швидкість цієї реакції дуже велика.
Сумарні реакції освіти азотної кислоти з урахуванням розкладання азотистої кислоти описуються уравнениями.
3NO2 + H2O = 2HNO3 + NO.
3N2O3 + H2O = 2HNO3 + 4NO.
По літературним даним, при ступеня окислення газу менш 50% розчини азотної кислоти поглинають окисли азоту як NO+NO2. При високої ступеня окислення газу відбувається поглинання окислів азоту як NO2. З огляду на невелика кількість трехокиси азоту в газі, зазвичай всі розрахунки проводять з рівняння реакции.
Розрахунок рівноважного складу окислів азоту над азотної кислотою показує, що з парциальном тиску двоокису азоту 0.1 ат отримання азотної кислоти, має концентрацію більш 60% HNO3, практично важко. Присутність у газової фазі окису азоту зміщує рівновагу реакції вліво. Тож у виробничих умовах при атмосферному тиску важко давалися кислоту з концентрацією вище 50%, а при 8 ат — більш 60%.
Головними чинниками, визначальними високу швидкість освіти азотної кислоти, є проведення абсорбції під тиском при знижених температурах із застосуванням багатих за змістом окислів азоту нитрозных газів й створення умов повнішого дотику газу з жидкостью.
3. ОБГРУНТУВАННЯ ОПТИМАЛЬНИХ ПАРАМЕТРІВ ОСНОВНИХ ТЕХНОЛОГІЧНИХ ПРОЦЕССОВ.
Усі промислові засоби одержання азотної кислоти засновані на контактному окислюванні аміаку киснем повітря із наступною переробкою оксидів азоту в кислоту шляхом поглинання їх водою. Головними стадіями виробництва неконцентрированной азотної кислоти є очищення сировини, каталітичне окислювання аміаку, утилізація тепла, вихід із нитрозного газу реакційної води, доокисление окису азоту у вищі окисли, абсорбція їх водою чи розведеною азотної кислотою, очищення газових выбросов.
Оптимальні умови окислення аміаку: Температура. Реакція аміаку на платині починається при 1450С, але протікає малим виходом NO й утворенням переважно елементарного азоту. Підвищення температури призводить до збільшення виходу окису азоту NO та зростанню швидкості реакції. У інтервалі 700−10 000С вихід NO то, можливо до 95- 98%. Час контактування у разі підвищення температури від 650-до 9000С скорочується приблизно п’ять разів (від 5*10−4 до 1,1*10−4сек).
Необхідний температурного режиму процесу може підтримуватися за рахунок тепла реакцій окислення. Для сухий аммиачно-воздушной суміші, що містить 10% NH3, при ступеня конверсії 96% теоретичне підвищення температури газу становить приблизно 7050С або близько 700С за кожен відсоток аміаку в вихідної суміші. Застосовуючи аммиачно-воздушную суміш, що містить 9,5% аміаку, можна з допомогою теплового ефекту реакції досягти температури порядку 6000С, для ще більшого підвищення температури конверсії необхідний попередній підігрів повітря, або аммиачно-воздушной суміші. Слід враховувати, що підігрівати аммиачно-воздушную суміш можна тільки до температури не вище 150−2000С за нормальної температури що гріє газу трохи більше 4000С. Інакше можлива дисоціація аміаку або його гомогенне окислювання із заснуванням елементарного азота.
Верхня межа підвищення температури контактного окислення аміаку визначається втратами платинового каталізатора. Якщо 9200С втрати платини певною мірою компенсуються зростанням активності каталізатора, то вище цієї температури зростання втрат каталізатора значно випереджає збільшення швидкості реакции.
Відповідно до заводським даним, оптимальна температура конверсії аміаку під атмосферним тиском становить близько 8000С; на установках, працюючих під тиском 9 ат, вона дорівнює 870−9000С. Тиск. Застосування підвищеного тиску і при отриманні розведеною азотної кислоти переважно пов’язане з прагненням збільшити швидкість окислення окису азоту NO та переробки образующейся двоокису азоту в азотну кислоту.
Термодинамические розрахунки доводять, що й за підвищеному тиску рівноважний вихід NO близький до 100%. Однак, висока ступінь контактування у разі досягається лише за велику кількість катализаторных сіток і високої температуре.
Останнім часом з промисловою умовах на багатошарових катализаторах при ретельної очищенні газів і температурі 9000С вдалося довести ступінь конверсії аміаку до 96%. При виборі оптимального тиску слід пам’ятати, що коли підвищення тиску спричиняє зростання втрат платини. Це збільшенням температури каталізу, застосуванням багатошарових сіток і посиленням їх механічного руйнації під впливом великий швидкості газа.
3. Зміст аміаку в суміші. Для окислення аміаку зазвичай застосовують повітря, тому зміст аміаку в суміші визначається змістом кисню повітря. При стехиометрическом відношенні О2: NH3=1,25 (зміст аміаку в суміші з повітрям становить 14,4%) вихід окису азоту не значний. Для збільшення виходу NO потрібно певний надлишок кисню, отже зміст аміаку в суміші має бути менше 14,4%. У заводський практиці зміст аміаку в суміші підтримують не більше 9,5−11,5%, що він відповідає відношенню O2: NH3=2(1,7.
Сумарна реакція, визначальна потреба у кисні при переробці аміаку в азотну кислоту.
NH3+2O2=HNO3+H2O дає ставлення O2: NH3=2, що він відповідає змісту аміаку в вихідної суміші, рівному 9,5%. Це засвідчує тому, що передвиборне збільшення концентрації аміаку в суміші вище 9,5% зрештою зрештою не призведе до зростання концентрації NO, позаяк у цьому випадку в адсорбционную систему доведеться вводити додатковий воздух.
Якщо ролі вихідних реагентів застосовувати аммиачно-кислородную суміш, то відповідність до рівнянням сумарною реакції можна було б збільшити концентрацію у ній аміаку до 33,3%. Проте застосування високих концентрацій аміаку утруднено тим, що такі суміші взрывчаты.
4. Вплив домішок. Платинові сплави чутливі до домішкам, які мають аммиачно повітряної суміші. У присутності 0,0002% фосфористого водню у газовій суміші ступінь конверсії аміаку знижується до 80%. Менш сильними контактними отрутами є сірководень, ацетилен, хлор, пари мастил,. пил, яка містить окисли заліза, окис кальцію, пісок, і др.
Попередня очищення газів збільшує тривалість роботи каталізатора. Однак згодом каталізатор поступово отруюється і вихід NO знижується. Для видалення отрут і забруднень сітки періодично регенерують у вигляді обробки їх 10−15% розчином соляної кислоти. 5. Час контактування. Оптимальний час контактування визначається швидкістю окислення аміаку. Найчастіше швидкість окислення визначають як збільшується кількість окисленого аміаку (кг) на одиницю поверхні (м2) на добу (напруженість каталізатора). Тривалість дотику газу з каталізатором, або контактування визначають по рівнянню t=Vсв/W де t — час перебування газу катализаторной зоні, сек;
Vсв — вільний обсяг каталізатора, м3;
W — об'ємна швидкість умовах контактування м3*сек-1.
Максимальна ступінь перетворення аміаку в окис азоту досягається за цілком певному часу контакту газу з каталізатором. Оптимальним часом контактування можна вважати чи, у якому досягається максимальний вихід NO, а кілька менше, оскільки економічно вигідно працювати у більшої продуктивності за рахунок зниження виходу продукту. У практичних умовах час контакту аміаку з каталізатором коливається не більше 1−2*10−4сек.
6. Змішування аміаку з повітрям. Повна однорідність аммиачноповітряної суміші, що надходить зону контактування, одна із основних умов для отримання високого виходу окису азоту. Хороше змішання газів має значення як задля забезпечення високого рівня контактування, а й охороняє від небезпеки вибуху. Конструкція і обсяг змішувача мають у повною мірою забезпечувати хороше перемішування газу та виключати проскакування аміаку окремими струменями на катализатор.
Оптимальні умови окислення окису азота:
Залежність константи рівноваги реакції 2NO+O2=2NO2 (+26,92 Ккал) від температури виражається рівнянням: lgK= lg ((PNO2*PO2)/PNO2)=- 5749/T+1,751lgT-0,0005T+2,839. При зниженні температури і підвищення тиску газу рівновагу реакції зміщується вправо. При температурах нижче 2000С і тиску 1 ат окислювання окису азоту може здійснюватися на 100%, отож у умовах реакцію можна як необоротну, яка убік освіти азоту. При температурах вище 7000С відбувається повна дисоціація NO2 на окис азоту та кислород.
Оптимальні умови абсорбції окислів азоту і при отриманні розведеною азотної кислоты:
1. Температура. Усі реакції, які у абсорбционной системі, крім розкладання азотистої кислоти, супроводжуються виділенням тепла, тому їх рівновагу зміщується вправо при зниженні температури. Завдяки цьому зниження температури сприяє збільшення концентрації продукционной кислоти. З іншого боку, зниження температури сприятливо позначається на продуктивності системи, бо за цьому зростає швидкість окислення NO. Зниження температури з 40 до 00С дозволяє продуктивність установки удвічі раза.
Насправді температуру абсорбції підтримують не більше 20−400С. Подальше зниження температури хоч і сприятливо б'є по процес, але водночас приводить до підвищення енергетичних витрат і збільшення кількості розчинених у азотної кислоті окислів азоту, які із жовтою водою не взаємодіють, й у остаточному підсумку, теряются.
2. Тиск. Підвищення тиску навіть у невеликий мері дозволяє значно прискорити процес освіти HNO3 і скоротити реакційний обсяг. Також підвищення тиску дозволяє ступінь поглинання окислів азоту. Для систем, працюючих під атмосферним тиском, вона становить 93−97%, при тиску 8 ат -96−99%. У промисловості знайшли застосування установки, у яких абсорбція окислів азоту проводиться під різними давлениями: 1; 1,2; 1,7; 3,5; 4; 5; 7; 9 ат.
ТЕХНОЛОГІЧНІ СХЕМИ ВИРОБНИЦТВА І АППАРАТУРНОЕ ОФОРМЛЕНИЕ.
Методи виробництва розведеною азотної кислоти може бути підрозділені втричі основні групи: виробництво під атмосферним тиском, виробництво під підвищеним тиском і комбіновані методи виробництва азотної кислоти (окислювання аміаку виробляється під атмосферним тиском, абсорбція під підвищеним давлением).
На мал.1 представлена схему одержання розведеною азотної кислоти під атмосферним давлением.
Задля чистоти від сторонніх газів і механічних забруднень повітря промивається водою в скруббере, фільтрується через з матерії фільтри і що з аміаком подається до системи вентилятором, в улиті якого відбувається змішання повітря і аміаку у властивому співвідношенні. До надходження на каталізатор газову суміш вкотре фільтрують через поролитовый чи картонний фільтр, розміщені верхню частину контактного апарату. Контактний апарат монтується безпосередньо на котле-утилизаторе. На виході з котла-утилизатора температура нитрозных газів знижується з 800 до 1600С. Подальше охолодження нитрозных газів виробляється у двох послідовно включених водяних холодильниках. На виході з швидкісного холодильника за нормальної температури 400С відокремлюється конденсат, у якому 2−3% азотної кислоти. Оскільки при охлаждении газів у них окис азоту швидко окислюється і температура знову підвищується, гази проходять другий холодильник, у якому відокремлюється конденсат, у якому вже 25−30% азотної кислоти. Охолоджені нитрозные гази з допомогою вентилятора подаються у абсорбционную систему, що складається з 6−8 веж. У останню у процесі газу вежу подається вода. Кожна вежа системи зрошується кислотою відповідної концентрації. Циркуляція орошающей кислоти здійснюється за допомогою відцентрових насосів, які представляють їх у вежі через водяні холодильники. Нитрозный вентилятор подсасывает до системи повітря такій кількості, щоб зміст кисню в вихлопних газах підтримувалося не більше 3,5−5%. Ступінь поглинання окислів азоту в вежах кислотною абсорбції становить 92- 94%. Залишки окислів азоту уловлюються далі в лужних вежах. Між системами кислої і лужної абсорбції встановлено пустотіла окислювальна вежа, призначена підвищення ступеня окисленности NO до 50−60%.
Основним недоліком систем, працюючих під атмосферним тиском, є використання значних реакційних обсягів при відносно малій продуктивності установки.
Схема азотно-кислої установки, яка під тиском 8 ат, приведено на мал.2. Повітря, очищений від домішок в башне-скруббере і матер’яному фільтрі, стискається в турбокомпрессоре, однією валу з яким перебуває рекуперационная турбіна. Стиснутий до 8 ат за нормальної температури 110−1200С повітря надходить через фільтр на змішання з аміаком в змішувач, частина повітря направляють у абсорбционную колонну.
Газоподібний аміак, який із випарника 20, проходить фільтр 19 і надходить у змішувач 18.
Окислювання аміаку киснем повітря ввозяться контактному апараті 17, після чого отримані нитрозные гази розладнуються в паровому казані 16 і змішане із додатковим повітрям вступають у холодильникконденсатор 13. У холодильнике-конденсаторе внаслідок охолодження нитрозных газів до 40−500С і конденсації водяної пари утворюється 50−53%-ная азотна кислота, яка, пройшовши фільтр для уловлювання частинок платини 15, відводиться із системи чи іде на тарілку, відповідну концентрації цієї кислоты.
Нитрозные гази з сепаратора 14 направляються під перший тарілку абсорбционной колони 10 сітчастого чи колпачкового типу. Колона зрошується чистим конденсатом, подаваним насосом 2. Для відводу выделяющегося тепла на тарілках на кілька рядів покладені змеевики, якими циркулює що охолоджує вода. Вихлопні гази з колони проходять брызгоуловитель 11, підігрівник 8, де нагріваються пором чи нитрозными газами.
Пуск системи виробляється під розрідженням, створюваним паровим эжектором 9. Продукционная 54−58%-ная кислота, що містить 2−4% розчинених окислів азоту, піддається продувке в окремому аппарате.
У системі описаного типу рекуперируется до 40% енергії, витраченої на стиснення повітря. До основним недоліків установок, працюючих під підвищеним тиском, слід віднести підвищений витрати і великі втрати платинового катализатора.
Економічність установок такого типу значною мірою визначається застосовуваним тиском. Оскільки різниця у виробничих витратах за зміни тиску невелика, рекомендується вибирати систему з найменшими капітальними витратами. Мінімальними капітальними витратами, по закордонним даним, характеризуються установки, працюючі під тиском 6−9 ат. Зміна тиску у тому інтервалі позначається істотно на економіці процесса.
Велике поширення нашій країні та країнах Західної Європи отримали комбіновані схеми виробництва розведеною азотної кислоти, в яких, певною мірою, усуваються недоліки, властиві системам, працюючим під атмосферному і підвищеним давлением.
Сутність комбінованого способу у тому, що окислювання аміаку і охолодження нитрозных газів проводять під атмосферним тиском, а переробку окислів азоту в кислоту — під підвищеним тиском. Завдяки цьому скорочуються втрати платинового каталізатора при щодо невеликих реакційних объемах.
У порівняні з розглянутими схемами новим виглядом устаткування комбінованих систем є турбокомпрессоры для стискування нитрозных газів, виготовлені з кислотостойкой стали. З іншого боку, після компресора може бути встановлений окисний обсяг; у своїй тепло окислення окису азоту використовується для підігріву вихлопних газів, які направляються рекуперационную турбину.
Нині нашій країні прийнято системи із тиском конверсії аміаку один ат і тиском абсорбції 3,5 ат.
Основна апаратура систем для розведеною сірчаної кислоты.
Контактні апарати. У промисловості набули поширення комбіновані агрегати для окислення аміаку під атмосферним тиском (рис.3). Агрегат складається з картонного фільтра I, контактного апарату II, котла-утилизатора 7 і экономайзера 8.
Аммиачно-воздушная суміш вступає у агрегат зверху і, пройшовши касети картонного фільтра 2, через вікна центральної труби потрапляє у вхідний конус контактного апарату. Задля підтримки однаковою температури і рівномірного розподілу навантаження лежить на поверхні каталізатора газова суміш проходить розподільну грати 3. Унизу циліндричною частини апарату на колосникової решітці розташовані платиноидные катализаторные сітки 4, а під ними — неплатиновые сітки 5. Діаметр робочої частини катализаторных сіток 2800 мм. Нижче каталізатора розташований шар порцелянових кілець 6, виконують роль акумулятора тепла.
Нижня частина контактного апарату, футерованная жаростойким цеглою, безпосередньо сполучається з верхньої частиною казана утилізатора III.
Нитрозные гази, пройшовши казан, экономайзер і охолоджувач, відводяться з частині апарату. Харчовий вода подається в трубки частині экономайзера. У верхню частину казана відводиться пар під тиском 40 ат з температурою 4500С. Агрегат виготовляється з хромонікелевої стали.
На рис. 4 показаний одне із типів контактних апаратів, працюючих під тиском до 9 ат. Апарат складається з верхнього конуса 7, нижнего конуса (чаші) 11 і хвостовій присоединительной труби 1. Нижний конус і труба обладнані водяний сорочкою 3. Між конусами на колосниках з нихрома перебувають катализаторные сітки. Для виготовлення контактних апаратів застосовуються нержавіючі хромоникелевые сталі та ніхром. Розміри апаратів квадратного перерізу 350×350 мм діаметр апаратів до 500 мм круглого сечения.
Абсорбционные колони. Для абсорбції окислів азоту під атмосферним тиском застосовують насадочные абсорбционные колони із нержавіючої сталі. Діаметр їх сягає 8 м; висота 29 м (рис 5). Колона складається з зварного корпусу 4, заповненого кільцями Рашига, колосникової грати 2 і разбрызгивающего устрою 1. Нитрозный газ надходить вниз колони, а відводиться у верхній частині його. Орошающая кислота рухається противотоком по відношення до газовому потоку. Для абсорбції нитрозных газів під підвищеним тиском застосовуються абсорбционные колони тарельчатого типу з колпачковыми чи ситчатыми тарілками. Пристрій колони з ситчатыми тарілками показано на рис. 6.
Колона є зварної циліндричний вертикальний посудину діаметром 3 метрів і заввишки 45 м, виготовлений із стали марки IXI8H9Т. Ситчатые тарілки 1 у кількості 40 прим. розташовані за висотою колони на різних відстанях друг від друга. Отвори діаметром 2 мм розміщені тарілках в шаховому порядку. Під час проходження через таку тарілку газу знизу вгору й за рідини згори донизу на тарілці утворюється піна з великою поверхнею розділу фаз, що сприяє інтенсифікації масообміну. Для перетікання рідини з тарілки на тарілку служать переливні патрубки 4.
Для відводу тепла, выделяющегося у процесі абсорбції нитрозных газів, на тарілках розміщені охолодні змеевики 2, у яких циркулює вода. Загальна що охолоджує поверхню в колоні сягає 500 м².
ПЕРСПЕКТИВИ РОЗВИТКУ І ВДОСКОНАЛЕННЯ ТЕХНОЛОГИИ.
До сучасним тенденціям розвитку технології виробництва азотної кислоти ставляться: забезпечення найбільшої надійності конструкцій апаратури і машинних агрегатів; підвищення ступеня кислої абсорбції, і навіть ступеня використання тепла хімічних реакцій і к.п.д. енергії стиснутих газів; збільшення швидкості процесу всіх його етапах, зниження шкідливих викидів в атмосферу.
З іншого боку значний вплив на економіку виробництва надає потужність застосовуваних установок, підвищення якої призводить до зниження витрат за будівництво азотно-кислотных систем. Підвищення потужності установок зумовлює необхідність підвищення тиску (особливо на стадії абсорбции).
Важливою проблемою розвитку азотної кислоти є підвищення його концентрації, що дозволяє спростити методи отримання аміачної селітри та інших азотних удобрений.
Істотне зниження азотної кислоти то, можливо досягнуто при зменшенні втрат платинового каталізатора. Для цього він проводяться випробування ефективних фільтрів для уловлювання платинової пилу, випробовуються каталізатори з підвищеним змістом Pd і Rh, проникають у виробництво комбіновані катализаторы.
СПИСОК ВИКОРИСТАНОЇ ЛИТЕРАТУРЫ.
1. Атрощенко В.І., Каргин С.І. Технологія азотної кислоти. М.: Химия,.
1970. 496с.
2. Софронов О. Л. Технологія пов’язаного азоту. Пермь.1973.
3. Довідник азотчика, т.1. М.: Хімія, 1986.
4. Довідник азотчика, т.2. М.: Хімія 1987.
5. Атрощенко В.І. та інших. Курс технології пов’язаного азоту. М.: Химия,.
1969. 384с.
6. Ведерников М. И., Кобозев В. С., Рудой І.В. Технологія сполук пов’язаного азоту. М.: Хімія, 1967. 418с.