Ремонт редуктора заднього моста
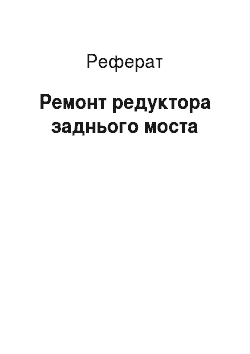
Загальний додача визначається сумою межоперационных припусков, т.к. під час виготовлення заготовок та його механічної обробці розміри що неспроможні бути точно витримані, виникає необхідність огранивать відхилення від заданих розмірів заготовок і точність обробки поверхонь на проміжних операціях. Таке відхилення встановлюють з допомогою операційних допусків. Загальний додача змінюється… Читати ще >
Ремонт редуктора заднього моста (реферат, курсова, диплом, контрольна)
| | |До У Р З Про У Про Й П Р Про Є До Т | | | | | |Учень | |Спеціальність | |Оцінка захисту ____________________________ | | | |2003 рік |.
А М Р, А Р З До І Й П Про Л І Т Є Х М І Ч Є З До І Й До Про Л Л Є Д Ж.
РЕМОНТ РЕДУКТОРА ЗАДНЬОГО МОСТА АВТОМОБІЛЯ ВАЗ.
ВІДНОВЛЕННЯ ВАЛУ ВЕДУЩЕГО.
До У Р З Про У Про Й П Р Про Є До Т.
КП 1705.199.03.000.ПЗ.
Руководитель.
МІНЬКО А.М.
Учащийся.
КАМЕНЯРІВ В.А.
г.Ангарск-2003 год.
ЗАТВЕРДЖЕНО: на циклової комісії Голова ______________ «_____» ____________ 200___г.
ЗАВДАННЯ для курсового проектування по навчальної дисциплине.
«Ремонт автомобілів і двигателей».
Студенту ______________ курсу ___________________________группы.
Ангарського промислового політехнічного колледжа.
КАМЕНЩИКОВУ Владлену Олександровичу Тема завдання Ремонт редуктора заднього мосту автомобіля ВАЗ. Відновлення валу ведучого. Запровадження: Короткий опис питань, розроблених в проекте.
Обгрунтування доцільності восстановления.
1. Організація ремонта.
1. Опис пристрої і послідовності розбірки складальної одиниці редуктора заднього моста.
2. Очищення і мийка деталей редуктора заднього моста.
3. Дефектация і сортування деталей складальної одиниці редуктора заднього моста.
2. Расчетно-технологическая частина проекту: ___________________________ 2.1 послідовність операції усунення дефектів 2.2 Вибір устаткування 2.3 Вибір робочого (ріжучого) і измер. инстр. 2.4 Розрахунок режим роботи з операціям 2.4.1 Операція токарная 2.4.2 Операція наплавочная 2.4.3 Операція токарная 2.4.4 Операція шлифовальная 2.5 Технічне нормування верстатних работ.
3. Техніка безпеки і протипожежні заходи і під час ремонту складальної одиниці, і відновлення деталі______________ ____________________________________________________________________ 4. Графічна частина проекту виконується двома аркушах формату А1 (594- 841). 4.1. Складальний креслення ремонтованій складальної единицы.
Формат А1 (594−841).
Допускається виконання складального креслення на форматі А2 (420−597) ____________________________________________________________________ 4.2. Технологічна карта. 4.2.1. Робочий чи ремонтний креслення відновлюваної деталі А3 (297−420).
__________________________________________________________ 4.2.2. Маршрутна карта На оновлення деталі формат А3 (297−420). ____________________________________________________________________ 4.2.3. Ескізи до операцій 4 прим. формат А4 (210−297).
Дата видачі ______________________ Термін закінчення____________________ Зав. відділенням____________________ Викладач ____________________.
Запровадження — 5.
1.1. Схема розбірки валу ведучого — 6 1.2. Очищення і мийка деталей які входять у К.П. з описом застосовуваного устаткування, процесу мийки, сучасних мийних засобів режимів мийки. — 8 1.3. Дефектация — 11 2 Расчетно-технологическая частина — 12 2.1. Послідовність операцій, виконуваних усунення дефектів ;
12 2.2. Вибір устаткування — 14 2.3. Вибір інструментів — 15 2.4. Розрахунок режимів роботи з операціям — 16 2.4.1 Операція токарная попередня — 16 2.5. Технічне нормування верстатних робіт — 19 2.6. Операція токарная остаточна (чистова) — 21 2.7. Операція шлифовальная — 21 2.8. Технічне нормування — 23 2.9. Операція наплавочная — 25 2.10. Технічне нормування шліфувальних робіт — 25 Література — 27.
У процесі експлуатації автомобіля його працівники властивості поступово погіршуються через зношування деталей. Справним вважають автомобіль, який відповідає всі вимоги нормативно-технологической документації. Працездатний автомобіль на відміну від справного повинен відповідати тільки тим вимогам виконання яких дозволяє вживати його за призначенню без загрози національній безпеці движения.
Ушкодженням називають перехід авто в несправні, але працездатні стану. Відмовою називають перехід автомобіля в неработоспособное состояние.
Поточний ремонт автомобілів виробляють на АТП. Вони повинні забезпечувати гарантовану працездатність автомобіля пробігу іншого чергового планового ремонту але з менш пробігу іншого чергового ТО-2. При тривалої експлуатації автомобілів досягають такої міри якщо їх ремонт за умов АТП стає неможливим чи економічно недоцільним, у разі вони скеровуються в авторемонтні підприємства (АРП).
Основними джерелами економічно ефективними і КР автомобілів є використання оснащеного ресурсу їх деталей.
Формулировка.
Близько 70−75% деталей автомобілів що надійшли до КР може бути використані повторно, або без ремонту, або після відновлення. До до них відносяться більшість найскладніших і дорогих деталей, а так ж вали, осі, цапфы і другие.
Вартість відновлення цих деталей пізніше вбирається у 10−50% вартості їх виготовлення. Це досягається лише за наявності, централізованого ремонту за умов АРП з спеціально обладнаними виробничими цехами ділянками і відділеннями. У цьому досягається велика економія металу і енергетичних ресурсів. Останнім часом АРП або закриваються, або перепрофілюються через малої ефективності чи неконкурентоспроможності з автомобільними заводами і автомобільними іноземними производствами.
Цілеспрямована робота заводу виготовлювача підвищення ресурсу рам і кабін і доведення їх передчасно служби а/м сприяє різкого зменшення сфери застосуванню КР полнокомплектным автомашинам (Камаз, ЗиЛ). Це тенденція розвитку авторемонтного виробництва викликає функції АРП, що стає переважно підприємством щодо капітального ремонту агрегатов.
1.1 Опис пристрої і послідовність розбірки складальної единицы.
Розбирання це сукупність операцій виділені на роз'єднання об'єктів ремонту (а/м і агрегатів) на складальні одиниці, і деталі в певної технологічної последовательности.
Розбірку а/м і АГР виконують у послідовності передбаченої картами технологічного процесу чи графічними схемами.
У процесі розбирання необхідно використовувати стенди, съемники пристосування, і інструменти, що дозволяють центрировать котрі знімаються деталі рівномірно розподіляти зусилля щодо їх периметру. При выпрессовки підшипників, сальників, втулок, застосовують оправлення і выколотки з м’якими наконечниками. Якщо выпряссовывают підшипник з ступецы чи склянки то зусилля докладають до наружнему кільцю, а під час зняття з валу до внутрішнього, забороняється користуватися ударним інструментом. Кріпильні деталі (гайки, болти, шпильки) вкладають сітчасту тару, для кращої очищення в мийних установках чи встановлюють по своїх місцях. Відкриті порожнини і отвори для оливи й палива закривають кришками і пробками. Найбільш типовими з операції при розбірки є вывертывание гвинтів, шпильок, болтів, гайок, зняття зубчастих коліс, шківів, муфт, подшипников.
Разборочные роботи складаються з основних та допоміжних. Основні - це операції розбірки резьбовых і пресових сполук. Допоміжні - це переміщення, установка, кріплення, разбираемых изделий.
Для розбірки резьбовых сполук застосовують інструмент ручний та механізованої. До ручному ставляться гайкові ключі наступних видов:
— з відкритою зевом двох сторонний;
— кільцеві двосторонні накладные;
— торцевые зі змінними головками;
— спеціальні (коловоротные).
Поводить момент на отвертывание гайок і болтів визначають по формуле.
М=Ко d2ср,.
де Ко — коефіцієнт враховує стан резьбового сполуки 0,5;
0,8. d2ср — середній діаметр різьби (мм).
Для вывертывания шпильок використовують шпильковерты. Розбирання сполук з гарантованим натягом виробничим шляхом докладання осьового зусилля чи використання теплових деформацій (нагрівання деталей). потрібний прес для сталевих соединяемых деталей.
[pic].
Для чавунної ступецы з сталевого вала:
[pic].
Z — відносний натяг.
D — діаметр ступецы l — довжина посадки/.
Посадки з попереднім нагріванням (450−5000С) застосовують для деталей значних размеров.
[pic].
(- коефіцієнт лінійного розширення = 0,0001.
1.2 Очищення і мийка редуктора заднього моста.
Принципова схема мийки редуктора заднього моста.
На принципової технологічної мийки очищення редуктора заднього мосту включно з очищенням від пластичних смазок.
Задля чистоти і знежирення застосовують миючі засоби й спеціальне устаткування. Як мийних засобів застосовують синтетичні миючі кошти (СМЗ) типу лабомид чи МС, а за її відсутності водні розчини каустику і кальционированной соди. Найчастіше миючий розчин приготавливают з трьох-чотирьох різних лужних добавок і одного-двох найменувань синтетичних поверхнево-активних речовин. Як лужних добавок застосовують їдкий натр (каустик), кальционированную соду, рідке скло, три натрій фосфат, три поліфосфат. ПАР застосовують для кращого змочування поверхні, для кращого відриву із поверхні забруднення (эмульгирование), для кращого подрібнення забруднення (диспертирование). Задля чистоти деталей необхідний певний рівень лужності розчину pH=11.5−13.5. Для мийки в мийних камерах, длу усунення пенообразования в розчин вводять 0,2−0,3% пеногасящих добавок (дизпаливо, гас, уайтспирит).
Склад СМЗ. Застосовуваних при механізованої мойке.
Таблиця. |Компоненти |Марка і склад СМЗ (в%) | |мийних засобів | | | |МС-6 |МС-8 |МС-15 |Лабомид-101 |Лабомид-203 | |Сода |40 |38 |44 |50 |50 | |кальционированн| | | | | | |на | | | | | | |Три поліфосфат |25 |25 |24 |30 |30 | |натрію | | | | | | |Метасиликат |29 |29 |28 |16,5 |10 | |Синтанол |6 |- |- |3,5 |8 | |(ДС-10) | | | | | | |Синтамид 5 |- |8 |- |- |- | |Акильсульфаты |- |- |- |- |2 | |Оксифос |- |- |8 |- |- |.
Робоча місце дефектовщика.
1 — Контейнер; 2 — рольганг; 3 — слюсарний стіл; 4 — прес; 5 — стіл дефектовщика; 6 — куль управління; 7 — шафу з контрольно-вимірювальним інструментом; 8 — монорейка; 9 — поворотно-консольный кран; 10 — візок з підйомним столом; 11 — спрямовуюча; 12 — приводная станція візки; 13 — контейнер для металобрухту; 14,15 — рухливі захоплення; 16 — пишуча машинка; 17 — стіл для инструмента.
1.3 Дефектация і сортування деталей з описом організації робочого місця контроллера-дефектовщика і заповненням відомості дефектации деталей по ГОСТ 3.1175−79.
Основними завданнями дефектации і сортування деталей являются:
— контроль деталей визначення їх технічного состояния;
— сортування деталей втричі групи (придатні, підлягали відновленню і негодные);
— накопичення про розмірах дефектации і сортування з використання її за вдосконаленні технологічних процессов.
Дефектацию деталей виробляють шляхом їх внешнегшо огляду, ні з допомогою спеціального інструмента, пристосувань, приладів та устаткування. Результати дефектации і сортування фіксують шляхом маркування деталей фарбою. Придатні - зеленої, потребують відновлення — жовтої, негідні - червоною. Придатні деталі після дефектации скеровуються в комплектовочный ділянку підприємства міста і далі на складання агрегатів і автомобилей.
Технічні умови на дефектацию деталей складаються як карт, котрі за кожної деталі окремо містять такі сведения:
— загальні інформацію про детали.
— перелік можливих дефектов.
— способи виявлення дефектов.
— допустимі без ремонту размеры.
— способи усунення дефектов.
Найбільшу складність розробки технічних умов на дефектацию деталей представляє визначення величини припустимого розміру деталі, тобто. dдоп=dн-Идоn, де dдоn — припустимий діаметр, Иdon — припустимий знос, dн — диметр номінальний. Допустимим зносом деталі називається такий її знос, у якому деталь, будучи встановленої, після капітального ремонту на автомобіль, працюватиме до наступного капремонту і його знос не перевищить граничного. Граничним зносом називається такий знос деталі, при якому її подальше використання неможливо. Її відновлюють чи заміняють нові. Величина граничного зносу деталі може бути оцінена щодо процесу перебігу її зносу залежно від напрацювання з моменту наступу форсованого зносу. Питання визначенні припустимого зносу зводиться до відшуканню його такого рівня, яка забезпечує безвідмовну роботу автомобіля протягом чергового межремонтного пробігу. 2. Расчетно-технологическая часть.
Шар металу, снимаемый з заготівлі у процесі механічної обробки щоб одержати деталі відповідної кресленню називається припуском на обробку. Спільним припуском називають шар матеріалу необхідний виконання всієї технологічних переходів, які забезпечують обробку даної поверхні від чорнової заготівлі до готової детали.
Загальний додача визначається сумою межоперационных припусков, т.к. під час виготовлення заготовок та його механічної обробці розміри що неспроможні бути точно витримані, виникає необхідність огранивать відхилення від заданих розмірів заготовок і точність обробки поверхонь на проміжних операціях. Таке відхилення встановлюють з допомогою операційних допусків. Загальний додача змінюється на величину допуску що передувала операції. Наприклад, додача на чистову обробку може коливатися на величину допуску чорнової обработки.
2.1 Схема розташування припусков і допусків на обробку деталей.
Рис. Схема розташування припусков і допусків на обробку деталі. Номінальний додача для шлифования складається з основного припуска і величини допуску для чистового обтачивания, т. е.
Z3=Z3+S2; мм,.
де Z3 — основний додача на шліфування (0,1−0,2) мм. на сторону.
Приймаю 0,15 мм.
S2 — допуск для чистового обтачивания дорівнює (0,3−0,4)Z2, де Z2 — основний додача на чистовое обточування дорівнює 0,2 мм., отсюда.
Z3=0,15+0,6=0,21.
Номінальний додача на чистовое обточування складається з основного припуска і допуску на черновое обтачивание.
Z2=Z2+S; S=(0,3−0,4)Z1,.
де Z1 — додача на черновое обточування дорівнює 0,2−2мм. Приймаю 2 мм., звідси Z1=0,8 мм. на сторону.
Загальний додача на механічну обробку на сторону.
Zобщ=Z3+Z2+Z1=3,01 мм.
Приймаю 3 мм.
Тоді діаметр заготівлі d3=46мм.
Діаметр заготівлі приймається відповідно до ГОСТ за довідником Конструктора-Машиностроение ТОМ1, Ануфьев, с. 130.
Якщо заготівля вибирається діаметром більш ніж розрахунковий, то, при чорнової (попередньої) обробці знімається шар металу проходження до номінального розміру, під чистовое обточування. 2.2 Маршрутна карта На оновлення валу редуктора заднього мосту автомобіля ВАЗ.
(Найменування і послідовність операций).
1. Операція токарная (зі зняттям задирок і задиров).
1. Встановити деталь до центрів (рифлений і обертався), закрепить.
1. Точити поверхню (1) витримуючи d=29мм. і l=30мм.
2. Зняти деталь.
2. Операція наплавочная.
1. Встановити деталь до центрів токарно-винторезного верстата з наплавочной голівкою на суппорте.
1. Точити поверхню (1) витримуючи d=36мм. і l=30мм.
2. Зняти деталь.
3. Операція токарная (предварительная).
1. Встановити деталь до центрів токарно-винторезного станка.
1. Точити поверхню (1) витримуючи d=32мм. і l=30мм.
2. Точити поверхню (2) витримуючи d=30,4 мм. і l=30мм.
2. Зняти деталь.
4. Операція шлифовальная.
1. Встановити деталь до центрів токарно-винторезного станка.
1. Точити поверхню (1) витримуючи d=30мм. і l=30мм.
2. Зняти деталь.
5. Операція контрольная.
1. Встановити деталь на призмы.
1. Перевірити числові значення розмірів відновлюваних поверхонь відповідно до робочим чертежом.
2. Зняти деталь. 2.3 Операція токарная.
Для отримання відновленої поверхні деталі вищого якості і однорідної за матеріалом рекомендується перед наплавкой її протачивать усунення нерівностей і задиров. Поверхні рекомендується протачивать із зменшенням діаметра від номінального на 1−2мм. Приймаю 1 мм, тобто. набік 0,5 мм.
Призначаю режими обробки. Глибина різання t=0,5 мм., подача P. S приймається залежно від потужності верстата, жорсткості системи СНІД, міцності що краючою пластини різця і державки, приймаю S=0,4мм/об [2], с. 266, Табл.11. Подача коригується по паспортним даним верстата, т.к. для токарной операції приймаю токарно-гвинторізний верстат 16К20, то S=0,4мм/об. Швидкість різання розраховується за формуле:
[pic].
де Сv — коефіцієнт різання і за зовнішньому подовжньому точении прохідними різцями з матеріалом що краючою частини різця Т15К6 (титану 15%, кобальту 6% й інше карбід вольфраму). Приймаю Сv=350.
Приймаю m=0,2, х=0,15, у=0,35.
Кv — коефіцієнт враховує вплив матеріалу заготівлі, стан поверхні, матеріалу інструменту та т.д. У навчальних цілях приймаю рівний 1.
[pic].
Частота обертання деталі розраховується за формуле:
[pic].
При розрахунку отримали n=2692.
Розрахункова частота обертання шпинделя коригується з паспортними даними верстата 16К20 і приймаю 1600. 2.4 Операція наплавочная.
Автоматична вибродуговая наплавлення служить на відновлення зношених поверхонь. Основною перевагою є невеличкий нагрівання деталі (близько 1000С, мала зона термічного впливу, можливість отримання наплавленного металу з необхідної твердістю і зносостійкості без додаткової термічної обработки.
Рис. Автоматична вибродуговая наплавка.
1. Оброблювана деталь. 2. Механізм подачі дроту. 3. Барабан з дротом. 4. Мундштук. 5. Схема двигуна на шляху подання проволоки.
Сутність процесу АВДН залежить від періодичному замиканні і размыкании що під струмом электродной дроту і поверхні деталі. Кожен цикл вібрації поволоки включає у собі 4 послідовно які протікають процесса:
— короткий замыкание;
— відрив електрода від детали;
— електричний разряд;
— холостий ход.
При відриві електрода від деталі їхньому поверхні залишається частинка приварившегося металу. Як джерела струму застосовують низьковольтні генератори типу АНД 500/250 і АНД 1000/500.
Як наплавочных головок застосовують УАНЖ — 5,6; ВДГ — 5 електромагнітні вібратори, або КУМА — 5 з механічним вибратором.
Як дроту застосовують Нn-60, 80, Св-08.
Швидкість наплавки визначається дослідним шляхом залежно від швидкості подачі электродной проволоки.
v=(0,4−0,7)vn.
або за формуле:
[pic].
де d — діаметр электродной дроту (приймається залежно від товщини наплавочного шару) при товщині 3,5 мм. d=2,5 vn — швидкість подачі l 3,5мм/мин. Приймаю 3м/мин — 50 мм/с.
До — коефіцієнт переходу электродной дроту в наплавленный метал (0,8−0,9) h — задана товщина наплавки;
P.S — Крок наплавки, залежить від d дроту. Приймаю 2,8 мм/об.
По паспортним даним верстата 16К20 максимальна подача 2,8мм/об.
а — коефіцієнт, враховує відхилення фактичної площі перерізу наплавленного шару від площі прямокутника з висотою h. Приймаю 1.
[pic].
Це значення відповідає вимогам на наплавку, де значення межах від 5 до 20 мм/с.
Частота обертання деталі розраховується за формуле.
[pic] і дорівнює 13 об./хв. Т.к. nmin шпинделя верстата 16К20 становить 12,5 об./хв, то близькі до цієї величині розрахункові частоти обертання округляються до 12,5 об./хв, або верстат устатковується додатковим редуктором що знижують частоту обертання шпинделя до 1−20 об./хв, або до розрахункового значення. 2.5 Операція токарная попередня (черновая).
Режим обробки t=Z1=2мм.
Швидкість подачі розраховується за формуле:
[pic].
Считаем.
[pic].
тоді частота обертання шпинделі дорівнюватиме (dн/4 мм).
[pic].
Частота обертання дорівнюватиме n=1618. Приймаю n=1600.
Тоді справжня швидкість v буде равна.
[pic].
Насправді ж швидкість дорівнює v=101 м/мин.
Сила різання. Прийнято розкладати на складові по осях координат верстата (див. рис.).
FZ — тангенциальная (окружная).
FY — радиальная.
FX — осевая.
FZ=10 Cр tx Sy vn Кр; Н.
де Порівн — коефіцієнт різання [2] Табл.22 с. 273.
Ср=300, х=1, y=0,75, n=-0,15, Кр=1 Звідси випливає, что.
FZ=10 300 21 0,50,75 161−0,15 1= 1664 Н.
Тоді потужність різання розраховується за формуле:
[pic].
Потужність електродвигуна р.n.ф.
Рdв = Рр/(=4,3/0,75=57 кВт.
По паспортним даним потужність двигуна токарно-винторезного верстата 16К20 8 кВт.
Якщо навантаження верстата 75% і більше, то верстат обраний правильно. При меншою завантаженні необхідно ухвалити верстат меншою потужності двигуна, в іншому разі збільшується споживання реактивної енергії, тобто. зменшується СОS. 2.6 Операція токарная остаточна (чистовая).
Приймаю режим обработки.
T=Z2=0,8 мм.
S=0,5.
N=1600 мин-1.
2.7 Операція шлифовальная.
Зовнішнє круглий шліфування виконується трьома способами:
— способом подовжньої подачи.
Рис. .Поздовжня подача.
При зовнішньому круглому шліфуванні способом подовжньої подачі додача на обробку знімається протягом кількох проходів. Шліфувальний коло обертальне рух навколо своєї осі і поступальний у бік оброблюваної деталі. Поступальний рух шлифовального круга.
— способом поперечної подачі При зовнішньому круглому шліфуванні методом поперечної подачі шліфувальний коло обробляє одночасно всю довжину вращаемой деталі без подовжнього переміщення круга.
— способом глибинного шлифования.
При глибинному шліфуванні коло, встановлений на повну глибину шлифования має обертальне рух і поступальний вздовж обертання детали.
Весь додача при глибинному шліфуванні (0,1−0,3мм) знімається за проход.
Основні параметри різання при шлифовании.
— швидкість руху обертання деталі Vg (12−25).
— глибина шлифования за кожен хід чи подвійний хід при круглому шліфуванні t=0,01 мм.
— поздовжня подача Sn однією оборот деталі в частках ширини круга.
Sn=(0,3−0,7)В.
Для обробки поверхні при шліфуванні застосовуються образивные кола з зовнішнім діаметром від 80 до 500 мм; У — від 6 до 80 прямого профілю та непорушністю РМ чи СМ2.
Твердість оцінюється за показниками відповідності з ГОСТом.
Ефективна потужність при шліфуванні з подовжньої подачею розраховується за формуле:
Р=Cn*Vg*t*S*d,.
де Cn r — 0,75 (2) 303 табл.5 x — 0,85 y — 0,7 d — діаметр шлифования.
При даному способі шлифования приймається В=10 мм.
Глибина різання вираховується за формулою: t=Sв, мм.
Кількість проходів I=Z3/t=0,2/0,01=20 2.8 Технічне нормирование.
У нормируемое час входять всі затрати робочого дня включаючи в склад технико-обоснованной норми на операцію (Те) і необхідну роботи відповідно до технологічним процесом (тв1 Тdon Tn. з).
Технічна норма штучно-калькуляционного часу розраховується за формуле.
Тшк=То+Тв+Тdon+Тnз/П, мин.
Тш=То+Тв+Тdon,.
де Те — основне (машинне час) — цей час у перебігу якої відбувається зміна форми, розмірів, внутрішніх властивостей деталі (мин).
Тв — допоміжне час — цей час затрачуване дії що забезпечує виконання дане роботи. До нього ставляться: установка, закріплення, зняття деталі, налагодження устаткування, перестановка інструмента, обмір детали.
Тon=То+Тв.
Оперативне час — цей час у протягом якого виконується робота, безпосередньо спрямовану виконання даної операции.
Тdon — додаткового часу складається з часу на організаційно-технічне обслуговування робочого місця й часу відпочивати та особисті надобности.
У організаційно-технічне обслуговування робочого місця входять такі роботи: швайка аж інструмента, мастило верстата, правка шлифовального кола … …
Тdon=(То+Тв)к/100мин,.
де До — ставлення Тdon до Те (%) встановлюється кожної операции.
Тnз — подготовительно заключне час, затрачуване робочим підготовку до роботі. Його тривалість залежить від организации.
2.8.1 Технічне нормирование.
Операція — токарная предварительная.
То=l*i/s*n.мин, де l=l+y.
Y — величина проходу різця на врізування і перебег, для токарних робіт y=5, мм.
L=30+5=35, мм.
То=35*1/0,5*1600=35/800=0,04 мм.
Тв — розраховується за формуле:
Тв=Тв.уст+Тв.пр+Тв.изм.(мин),.
де Тв. уст — час на установку деталі переважно залежить від безлічі та способів кріплення. Тв. уст=0,5−1. хв. Принимаем.
Тв.уст=1. мин.
Тв.пр — час на прохід 0,5−1мм беру 1 мин.
Тв.изм — час на вимір 0,5−1 хв. Приймаю 1 мин.
Тв=1+1+1=3мин.
Додаткове время:
Тdon=((То+Тв)*К)/100;мин.
К=8%.
Тdon-((0,4+3)*8)/100−0,24часа-14секунд.
Час поштучна однією операцию.
Тш=То+Тв+Тdon.
Тш=0,04+3+0,24=3,28 (3мин 16 сек.).
Поштучна час На оновлення деталі визначається по формуле.
Тш=То+Тв+Тdon=0,9+3,5+0,39=4,79 мин.
Загальне поштучна время.
Тш.общ=Тш1+Тш2+Тш3+Иш4=.
=3,28+2,93+3,28+4,79==14,28 хв. 2.9 Операція наплавочная (технічне нормирование).
Основний час для наплавки, розраховується за формуле.
То=l*i/n*S.
To=30*1/12,5*2,8=0,85.
Допоміжне час розраховується за формуле:
Тв=Тв1+Тв2+Тв3 де Тв1 — допоміжне час що з установкою, і зняттям детали.
Тв2 — допоміжне час що з переходом (0,7 мм на 1 погонний метр наплавленного валика).
L=П*D*l/1000*S.
L=3.14*29*30/1000*2.8=l M.
Тв=1мин+0,7м=1,7=1,42мин.
Додаткове время.
Тdon=(То+Тв)*К/100.
де К=11−15%.
Тdon =(0,85+1,7)*15/100=0,38.
Тш=То+Тв+Тdon=0,85+1,7+0,38=2,93.
2.10 Технічне нормування шліфувальних работ.
Основний час при круглому зовнішньому шліфуванні при поперечне подачі на подвійний хід розраховується за формуле.
То=21*Z3/n*Sn*Sв, мин.
L=l+B L=30+10=40 n=318*V/d=318*25/30=265.
У — ширина шлифовального круга.
То=2*40*0,21/n*Sn*0.01=0.9 мин.
Час вспомогательное.
Тв=Тв.су+Тв.гр
1. С. И. Румянцев та інші, Ремонт автомобілів, м., Транспорт, 1988;327с.
2. Ю.А.абрамов та інші, Довідник технолога машинобудівника Том 2, М.,.
Машинобудування, 1986;496с.
3. Г. А. Броневич, Курсове і дипломне проектування, М., Стройиздат, 1973;
240с.
4. И. Я. Корчанов, Технологія і організація ремонту й будівельних машин і устаткування, М., Стройиздат, 1990;351с. ———————————;
Сальник.
КП 1705.199.03.000.ПЗ.
Ізм Ліст № документа Підпис Дата.
Лист.
КП 1705.199.03.000.ПЗ.
Щит тормоза.
Подшипник.
КП 1705.199.03.000.ПЗ.
Ізм Ліст № документа Підпис Дата.
Лист.
Редуктор заднього мосту (мийка в мийною камере).
Мийка деталей редуктора перед спеціальними очистками.
Очищення від накипу і зажадав від нагара.
Очищення від осмолений.
Очищення від коррозии.
Очищення від пластичних смазок.
Мийка деталей після спеціальної очистки.
КП 1705.199.03.000.ПЗ.
Ізм Ліст № документа Підпис Дата.
Лист.
КП 1705.199.03.000.ПЗ.
Ізм Ліст № документа Підпис Дата.
Лист.
КП 1705.199.03.000.ПЗ.
Ізм Ліст № документа Підпис Дата.
Лист Номинальный додача на шлифование Допуск для чистового обтачивания Допуси при шлифовании.
КП 1705.199.03.000.ПЗ.
Ізм Ліст № документа Підпис Дата.
Лист.
КП 1705.199.03.000.ПЗ.
Ізм Ліст № документа Підпис Дата.
Лист.
КП 1705.199.03.000.ПЗ.
Ізм Ліст № документа Підпис Дата.
Лист.
КП 1705.199.03.000.ПЗ.
Ізм Ліст № документа Підпис Дата.
Лист.
КП 1705.199.03.000.ПЗ.
Ізм Ліст № документа Підпис Дата.
Лист.
Лист.
КП 1705.199.03.000.ПЗ.
Ізм Ліст № документа Підпис Дата.
КП 1705.199.03.000.ПЗ.
Ізм Ліст № документа Підпис Дата.
Лист.
Z.
X.
Y.
X.
Y.
Z.
КП 1705.199.03.000.ПЗ.
Ізм Ліст № документа Підпис Дата.
Лист.
КП 1705.199.03.000.ПЗ.
Ізм Ліст № документа Підпис Дата.
Лист.
КП 1705.199.03.000.ПЗ.
Ізм Ліст № документа Підпис Дата.
Лист.
КП 1705.199.03.000.ПЗ.
Ізм Ліст № документа Підпис Дата.
Лист.
КП 1705.199.03.000.ПЗ.
Ізм Ліст № документа Підпис Дата.
Лист.
КП 1705.199.03.000.ПЗ.
Ізм Ліст № документа Підпис Дата.
КП 1705.199.03.000.ПЗ.
Ізм Ліст № документа Підпис Дата.
Лист.
КП 1705.199.03.000.ПЗ.
Ізм Ліст № документа Підпис Дата.
Лист.
Лист.
Черновое обтачивание.
Чистовое обтачивание.
Шлифование Номинальный додача на чистовое обтачивание Окончательный размер Номинальный розмір під шлифование Номинальный розмір під чистовое обтачивание.
КП 1705.199.03.000.ПЗ.
Ізм Ліст № документа Підпис Дата.
Лист.
Задній мост.
Гальмівний барабан.
Гайки кріплення щита гальма выталкивателем.
Осі з маслоотражателем.
Редуктор
Пластина крепления.
подшипника.
Запірне кольцо.
Уплотнительное кольцо.
Фланец.
Болти кріплення редуктора.
КП 1705.199.03.000.ПЗ.
Ізм Ліст № документа Підпис Дата.
Лист Редуктор заднього моста.
АПК 6 ТОРА1.