Ознайомча практика
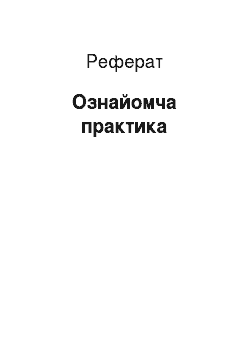
При ремонті виконуються такі заходи: розтин люків і обстеження обличкування і секционирующих ґрат; обстеження розподільній ґрати, центрального склянки, вузла введення катализаторопровода через розподільну грати; огляд очищення циклонів; ремонт футерівки; перевірка вм’ятин корпусу; демонтаж секционирующих ґрат; демонтаж закалочных змійовиків і опорних балок; зняття обличкування за висотою… Читати ще >
Ознайомча практика (реферат, курсова, диплом, контрольна)
року міністерство освіти Російської Федерации.
Кузбасский Державний Технічний Университет.
Хіміко-технологічний факультет.
Кафедра ХТТТ і Э.
Отчёт.
по екскурсійної практиці на КОАО «Азот».
Виконав Проверил.
Кемерово 2001.
|Исторические інформацію про КОАО |3 | |"Азот". … | | |Одержання аміачної селітри (цех № 13)… |5 | |Ремонтно-механічний |9 | |цех… | | | 3.1. Ремонт апаратів повітряного |9 | |охолодження… | | | 3.2. Ремонт реакційних |10 | |апаратів… | | | 3.3. Ремонт кульових барабанних |12 | |млинів… | | | 3.4. Ремонт теплообмінних |13 | |апаратів… | | | 3.5. Ремонт ёмкостных |14 | |апаратів…| | |. | | |Список використаної літератури | | |Додаток, А | |.
1. Історичні інформацію про КОАО «Азот».
25 березня 1945 р. урядом СРСР ухвалено постанову щодо будівництва Кемерово Новокемеровского хімічного комбінату. Вже 6 квітня 1945 р. з’явилися перші будівельники. До 1949 р. вже був побудована будівельна база. Цех аммина (цех 6.38) і уротропина.
У 1956 р. в цеху 6.38 отримали першу продукцію що є компонентом ракетне паливо. У 1960 р. почали працювати цехи із виробництва аміаку. У 1962 р. запрацювала першу чергу капролактаму. У 1968 р. — друга чергу капролактаму з вугільного бензолу потужністю 60 тис. тонн на рік. 1972;го р. третя чергу капролактаму з нафтового бензолу такою ж потужністю. У цей час розпочав виробництво сірчаної кислоти. У 1979 р. — сульфенамид «Ц». 1974 р. — диафен «ФП».
Розгромна замовна стаття програма по хімізації населення змусила запустити 3 агрегату аміаку: — 1979 р. перший агрегат потужністю 450 тис. тонн на рік. — в 1984 р. другий агрегат більш модернізований. — 1987 р. третій агрегат.
У цей самий період дві черги азотної кислоти, дві черги селітри і карбаміду. Розпочате було будівництво по карбамиду екологи заборонили, й устаткування довелося продати. Також на «Азоті» існують: — цех із виробництва вуглеамонійних кислот. — цех теплопостачання. — цех водопостачання. — цех електропостачання. — цех нейтралізації відходів виробництва. — цех зв’язку. — цех з доставки продукції. — 6 ремонтних цехів. — база матеріально-технічного постачання. — центрально-заводская лабораторія. — цех контрольно-вимірювальних приладів. — цех № 31 — цех знесолювання води. — очисні споруди. — служба безопасности.
КОАО «Азот» займається такими видами діяльності: — азотна промисловість. — посередницькі послуги з купівлі продажу. — оптової торгівлі. — роздрібна торгівля. — наукова діяльність. — зовнішня торгівля недержавного підприємства. — займається орендою і цінними паперами. — є своє друкарня. — громадське харчування. — общестроительная організація. — медицина.
На заводі стану на 1 січня 2001 р. працює 12 188 людина їх виробничого персоналу близько 11 000. Загальний фонд заводу на 1 січня 2001 р. становив 5.467.000.000 руб.
Кемеровское ВАТ «Азот» нині є найбільшим хімічним підприємством Західного Сибіру, випускаючи понад 40 кримінальних найменувань продукції. КОАО «Азот» виробляє капролактам, мінеральних добрив, сірчану і азотну кислоти, ионообменные смоли, сульфенамид «Ц», диафен.
«ФП». Підприємство забезпечує мінеральною поживою сільському господарстві Сибіру та Середню Азію, виконує велику програму експортних поставок мінеральних добрив, капролактаму, іонообмінних смол та у країни Західної Європи, Азіатсько-Тихоокеанського региона,.
Америки, Китай. Продукція органічного синтезу надходить на заводи, що виробляють пластмаси, барвники, хімічне волокно і лікарських препаратів. Продукція КОАО «Азот» конкурентоспроможна й послуговується великий попит на світовому та внутрішньому ринку. У травні 1995 року у Копенгагене.
КОАО «Азот» вручили міжнародний приз «Золотий Глобус» за високу якість продукції, а вересні 1999 року в міжнародної выставке.
«Химия-99» КОАО «Азот» завоювало «Диплом за високу якість продукции».
2. Одержання аміачної селітри (цех № 13).
Аміачна селітра NH4NO3 — безкольорове кристалічний речовина, що містить 60% кисню, 5% водню і 35% азоту. Технічний продукт містить щонайменше 34,0% азота.
Основні фізико-хімічні властивості аміачної селитры:
|Плотность, т/м3: | | |справжня |1,690 — 1,725 | |насипна при вологості гранульованого продукту 1% і 20 | | |градусів: | | |при щільною упаковці |1,164 | |при нещільної упаковці |0,826 | |Температура плавлення, градусів |169,6 | |Теплота плавлення, кДж/кг |73,21 | |Теплота освіти при 25 градусів і 0,101 МПа, кДж/моль |365,6 |.
У промисловості широко вживається лише метод отримання аміачної селітри із синтетичної аміаку і розведеною азотної кислоти. Метод отримання аміачної селітри з аміаку коксового газу та розведеною азотної кислоти перестали застосовувати як економічно невыгодный.
Виробництво аміачної селітри є многостадийным. У зв’язку з цим намагалися отримувати аміачну селітру безпосередньо з аміаку, окислів азоту, кисню і водяної пари по реакции:
4NH3 + 4NO2 + O2 + 2H2O = 4NH4NO3.
Проте від надання цього способу довелося відмовитися, оскільки поруч із аміачної селітрою утворювався нітрит амонію — хитливий і вибухонебезпечний продукт.
У невеличких кількостях аміачну селітру отримують шляхом обмінного розкладання солей (конверсійні способи) по реакциям:
Ca (NO3)2 + (NH4)2CO3 = 2NH4NO3 + vCaCO3.
Mg (NO3)2 + (NH4)2CO3 = 2NH4NO3 + vMgCO3.
Ba (NO3)2 + (NH4)2CO4 = 2NH4NO3 + vBaCO4.
NaNO3 + (NH4)2CO4 = 2NH4NO3 + Na2SO4.
Технологічна схема агрегату АС-72 представлена на рис. 1. прил.А.
Аппаратурное оформлення процесса.
Апарат ИТН призначений щоб одержати розчину аміачної селітри шляхом нейтралізації 58 — 60% азотної кислоти газоподібним аміаком з допомогою тепла реакції для часткового випарювання води з розчину під атмосферним тиском по реакции:
NH3 + HNO3 = NH4NO3 + Qккал.
Безпека процесу нейтралізації забезпечується автоматичними блокуваннями, прекращающими подачу сировини в апарати ИТН при порушеннях співвідношення витрат азотної кислоти і газоподібного аміаку або за зростанні температури в реакційної зоні вище 180 градусів; щодо останнього в.
ИТН автоматично подається конденсат водяного пара.
Підігрівник азотної кислоти призначений для підігріву 58 — 60% азотної кислоти від температури, коли він він зберігається складі, до температури 80 — 90 градусів рахунок тепла сокового пара з апарату ИТН.
Підігрівник газоподібного аміаку призначений для нагріву аміаку до 120 — 180 0С.
Донейтрализатор призначений для донейтрализации аміаком надлишкової кислотності розчину аміачної селітри, безупинно що надходить з апарату ИТН, і вводяться у ролі добавки сірчаної і фосфорної кислот.
Выпарной апарат у ньому отримують висококонцентрований плав до однієї ступень.
Підігрівник повітря выпарного аппарата.
Выпарной апарат призначений для выпарки розбавлених розчинів от.
30 — 50 до 92% під атмосферним давлением.
Промывное і фільтруюче устаткування призначені для відмивання пилу аміачної селітри, уносимой повітрям з вежі, аерозольних частинок аміачної селітри з паро-воздушной суміші выпарного апарату, повітря з веж, сокового пара з апаратів ИТН, і навіть аміаку з цих потоков.
Нагнітач повітря на выпарной апарат відцентрового типа.
Воздуходувки йдуть на охолодження аміачної селітри встановлюються 3 высоконапорных відцентрових вентилятора.
Витяжні вентилятори для отсоса паро-воздушной суміші після промивних скрубберов на грануляционных вежах осьового типа.
Насоси для перекачування плаву призначені для перекачування 99 -.
99,9% плаву при 185 0С.
Грануляційна вежа вона з трьох частин: верхня частина — з стелею і переходником до промывному скрубберу; середня частина — власне корпус; нижня частина — з прийомним конусом. Продукт вивантажується на реверсивний конвеєр через прямокутну щілину в нижньому корпусе.
Апарат для охолодження гранул в киплячому шарі призначений для охолодження гранул які виходять із грануляційної вежі від 110 — 120 до 40 -.
45 0С.
Під псевдоожижением розуміється процес переходу шару зернистого матеріалу в «текучого» стан під впливом потоку ожижающего агента — повітря. Якщо під шар гранул з певній швидкістю подавати повітря, гранули починають інтенсивно переміщатися щодо одне одного й шар їх неабияк зростає обсягом. Після досягнення певній швидкості найбільш дрібні гранули починають залишати кордону шару і відносяться потоком повітря. Таке явище відбувається, якщо тиск потоку повітря перевищує силу тяжкості гранул. Опір шару матеріалів майже залежить від швидкості газу та одно вазі матеріалу, що припадає на одиницю площади.
Киплячий шар гранул набуває властивості, властиві краплинної рідини. Температура всього обсягу киплячого шару гранул, як і будь-яка киплячій рідини, практично одинакова.
Основні засади автоматизації великотоннажних агрегатов.
Сучасні великотоннажні агрегати хімічних виробництв випливає низка специфічних особливостей, які треба враховувати під час розробці систем автоматизації таких об'єктів: — послідовна технологічна структура з жорсткими зв’язками між окремими стадіями процесу за відсутності проміжних ёмкостей; - велика продуктивність окремих апаратів, розрахована на повну потужність агрегату; - територіальна рассредоточенность робочих місць аппаратчиков.
Велика міць і послідовна структура агрегату задають підвищені вимоги до надёжности контролю, регулювання та питаннями захисту, оскільки вихід із ладу окремого елемента часто призводить до її повної зупинці агрегату як наслідок, до великим економічним потерям.
Територіальна роз'єднаність робочих місць за великому числі взаємозалежних вузлів регулювання утрудняє координацію дій апаратників. Тож потрібно єдина технічна система з урахуванням всіх взаємозв'язків і взаємовпливу окремих пристроїв друг на друга.
Результатом цього є відмови від традиційних приміщень щитових на окремих стадіях процесу, концентрація управління у руках одну людину. Зосередження всієї необхідної інформації та управління агрегатом до рук одного оператора вимагає організації раціонального її уявлення. І тому всіх адміністративних органів управління регуляторами і виконавчими механізмами розміщені пульті; відразу ж виконано мнемосхема провадження з вмонтованими у неї кнопками виклику параметрів і сигнальними лампами.
Для зниження психологічної навантаження на оператора, викликаної інформаційної насиченістю, пульт снабжён системою сигналізації відхилень параметрів від норми і політичною системою групового виклику. Це дозволяє оператору за відсутності сигналів вибірково перевіряти стан різних параметрів, а за наявності сигналу одним натисканням кнопки викликати для контролювання всіх параметрів, що з порушеним параметром. За необхідності додаткову інформацію оператор отримує з записуючих приборов.
Система автоматизованого управління технологічним процессом.
(САУ ТП) включає у собі такі підсистеми: — інформаційна підсистема варта уявлення оператору інформації про перебіг технологічного процесу, його режимі, про кількісних і якісних показниках матеріальних й енергетичних потоків; - підсистема сигналізації все лампочки на мнемосхемах; - підсистема автоматичного регулювання забезпечує стабілізацію основних технологічних параметрів процесу своєчасне зняття обурень, що виникають у процесі; - підсистема аварійного захисту служить задля унеможливлення аварій через відмов у системі регулювання чи хибних дій оператора; - підсистема дистанційного управління забезпечує безпосереднє вплив оператора на процес; - обчислювальна підсистема забезпечує математичну і логічний обробку інформації з заданим алгоритмам, неї в цілому або частково переносяться функції інформаційної підсистеми, і навіть функцію контролю роботи підсистеми аварійної защиты.
САУ ТП агрегатів аміачної селітри є інформаційно-насиченими й використовують досить великий парк вимірювальних приладів та перетворювачів в агрегаті АС — 72 їх 650 единиц.
3. Ремонтно-механічний цех.
Ремонтно-механічний цех займається ремонтом хімічного устаткування. Тут працюють близько 400 робочих. У цеху представлені різні види устаткування, починаючи з фрезерного верстати й до сучасного комп’ютерного оборудования.
Тут ремонтують різного устаткування, розглянемо його особенности.
3.1. Ремонт апаратів повітряного охлаждения.
У апаратах повітряного охолодження найбільшому зносу піддаються трубні секції і редуктор. Апарати мають великі габарити і як розташовані від поверхні землі, тому найбільш трудоёмкими ремонтними операціями є демонтаж і монтаж секцій, кришок секцій, зняття і установка редуктора і електродвигуна. Для проведення монтажних робіт використовуються крани в автомобільному і пневмоколесном ходу.
Спочатку демонтують трубні секції, потім колесо вентилятора, та був редуктор.
Характерними ушкодженнями редуктора є поломка зубів конічній пари шлицев провідною шестерні, утомлююча выкрашивание і абразивний знос підшипників редуктора, порушення герметичності редуктора і витік масла.
Стан зубчастого зачеплення редуктора перевіряють візуально. При поломки зубів шестерні заміняють. На лопатах вентилятора можливо поява тріщин. Зазвичай дрібні тріщини зашпаровують эпоксидальной смолою, та був проводять статичну баланс. Форсунки вузла зволоження повітря прочищають. За необхідності окремі форсунки заменяют.
При ремонті трубного пучка допускається установка пробок на 15% трубок у кожному потоці пучка. При виході з експлуатації понад п’ятнадцять % трубок усі вони замінюються повністю. Правка вм’ятин в трубах здійснюється з допомогою наступного пристосування: штанга продевается через трубу до упора оправлення у вм’ятину. Після цього штангу надягають шайба і гайка. При завинчивании гайки альтанка здійснює випрямлення вмятого участка.
Зібраний апарат випробовують протягом 8 часов.
3.2. Ремонт реакційних аппаратов.
Більшість реакційних апаратів є нестандартним обладнанням і розробляється для конкретної реакції з урахуванням її особенностей.
Ремонт реактора високого тиску. При експлуатації реактора виникають ушкодження корпусу, плакирующего шару, термопар, ізоляції, що найчастіше призводить до порушення герметичності. При розбиранні апарату проводиться відключення трубопроводів, демонтаж арматура, вивантаження каталізатора. Усі шпильки вывёртываются контролю заміна. Через пригара шпильок їхнього вывёртывания необхідні великі крутящие моменту, що зумовлює пошкодження різьби в гнёздах і необхідності нарізки різьби з великим диаметром.
Термопари при розбиранні видаляються. Гільзи для термопар піддаються испытанию.
Уплотняющая поверхню затвора за необхідності полірується, металева прокладка заменяется.
Ремонт корпусу апарату починається із зовнішнього огляду. За відсутності видимих дефектів може здійснюватися вибірковий магнітний і ультразвукової контроль. За наявності механічних ушкоджень кісткової та тріщин проводиться вибірка дефектного металу шліфувальної машинкою з періодичним магнітним контролем.
Можливі такі способи відновлення корпусу: 1) зняття поверхового наклёпа з повреждённого місця та скругление дефектного місця з плавним переходом на поверхню корпусу зниження концентрації напруг; 2) розбирання ушкоджень чи розточення отворів до неповреждённого металу із наступною компенсацією ослабленого місця з допомогою електрозварювання; 3) видалення пошкодженою царги із наступною вваркой нової царги чи стыковкой і зварюванням рахунок зменшення довжини корпусу — лише за великої площі ушкодження корпуса.
Ремонт штуцеров може бути шляхом установки гільзи. Гільза приваривается по обидва боки до штуцеру.
Зібраний апарат піддається гидравлическому испытанию.
Ремонт реакторно-регенераторного блоку з псевдоожиженным шаром каталізатора. У процесі роботи реакторно-регенераторного блоку зношуються: корпус, підбійка, циклонная група, змеевики гарту, секционирующие ґрати, розподільна камера і десорбционный стакан.
При ремонті виконуються такі заходи: розтин люків і обстеження обличкування і секционирующих ґрат; обстеження розподільній ґрати, центрального склянки, вузла введення катализаторопровода через розподільну грати; огляд очищення циклонів; ремонт футерівки; перевірка вм’ятин корпусу; демонтаж секционирующих ґрат; демонтаж закалочных змійовиків і опорних балок; зняття обличкування за висотою псевдоожиженного шару, ремонт циклонів; монтаж обличкування і підбійка; монтаж секционирующих тарілок; ремонт розподільній ґрати; монтаж опорних балок під змеевики і установка змійовиків; закриття люків і випробування; ревізія арматури; контроль стінок циркуляційних линий.
При серйозних пошкодженнях в виконати ремонт може включатися часткова заміна корпусу апарату і циркуляційних линий.
Циклони, як і реакторах, і у регенераторах працюють у важких умовах, піддаються інтенсивному абразивному зносу потоком катализаторной пилу за високої температури. Термін служби циклонів від 2 до.
8 місяців. Вследствии вібрації і високої температури у циклонів спостерігається порушення герметичності зварних швів. При ремонті проводиться заварка швів, приварку накладок і вставок. Для чистки поверхні в бункерах циклонів прорізають лючки чи роблять съёмные элементы.
Основний складністю ремонту змійовиків гарту є скрутний доступу до них під час виробництва зварювальних робіт всередині реактора. Освіта тріщин відбувається внаслідок истирания змійовиків каталізатором і прогорании за високої температури. Опори змійовиків руйнуються через часткового відкладення ними коксу або під впливом вибраций.
Секционирующие ґрати трубчастого типу зношуються потоком каталізатора. Найбільший знос труб посідає бічні части.
Характерні порушення у розподільній камері - освіту тріщин в розподільній ґратам по сварным швах у місцях кріплення ґрати до обечайке камери, й по монтажного шву ґрати, обрив ребер жёсткости всередині камери. Це спричиняє просыпанию каталізатора в днище камери. Освіта тріщин відбувається внаслідок термічних напруг, які під час пуску й зупинці аппаратов.
Корпуси реактори й регенератора — основні які мають конструкції. При руйнуванні футерівки відбувається перегрів корпусів із наступною деформацією їх під впливом власної ваги. Тому працездатність обличкування і футерівки — важливий чинник нормальної роботи реактора. Руйнування футерівки відбувається під впливом потоків каталізатора, проникаючих під облицювання у місцях недостатньою герметизації чи разі завалення облицовки.
Руйнування транспортних ліній всередині реактори й регенератора наслідок коксообразования в свищах і трохи дрібних тріщинах. У клапанів внаслідок інтенсивного истирания каталізатором часто виходить із ладу сідло і голівка. Зношуються також штоки клапанов.
3.3. Ремонт кульових барабанних мельниц.
Кульові млини застосовуються для помелу різноманітних продуктов.
З іншого боку, у деяких процесах разом з помелом здійснюється змішання компонентів суміші. Робітниками органами млини, піддаються найбільшому зносу, є броня і кульки. Зносу піддаються також підшипники, система їх мастила, привод.
Перед початком ремонту до зупинки млини проводиться вимір вібрації млини і редуктора.
У процесі роботи кулі піддаються зносу із зменшенням їхніх діаметра. Кулі, досягли мінімально припустимого діаметра при сортування відбраковуються. Кількість загружаемых в млин куль має відповідати паспорту млини, тому за мінімального завантаження кулі взвешиваются.
Броня млини складається з окремих броньових плит, які з марганцевої стали. При 50% знос броня заменяется.
Якщо броню не змінювати, вона починає при подальшому знос ламатися і випадати. Торцевая броня навіть за наскрізному знос ремонтується шляхом вварки вставок з листової сталі чи шляхом заміни окремих плит. Іноді спостерігається заклинювання куль в зазорі між плитами. Їх вибивають чи розрізають газової горілкою. Крім сталевої використовується гумова броня, що сприяє глушению шуму під час роботи млини. Термін служби гумового покриття перебувають у кілька разів вищий, ніж сталевих броньових плит.
У зубчастого віденця від дії ударних навантажень послаблюються болтові сполуки, зношуються зуби, підвищуються радіальне і осьове биения.
Невеликі дефекти зубів завариваются наплавкой і зачищаются наждаковим колом. При знос зубів до 30% їх товщини вінець потрібно повернути на 180.
0, щоб зуби працювали неизношенной стороною. Зубцюватий вінець з двостороннім зносом зубів замінюється новым.
Випробування млини після ремонту залежить від следующем.
Здійснюється поузловое випробування електродвигуна з редуктором протягом 2 годин, маслосистемы за тридцяти хв., агрегату загалом без завантаження млини кулями протягом 2 годин. При випробуванні перевіряється відсутність ударів у головній звичайною зубчастою передачі, відсутність витоку олії через підшипники, замеряются підвищення температури олії проходячи його через підшипники, вібрація підшипників приводних шестерні, редуктора і електродвигуна. Далі проводиться випробування млини під нагрузкой.
3.4. Ремонт теплообмінних аппаратов.
У процесі тривалої роботи теплообменные апарати піддаються забруднення і зносу. Поверхня їх покривається накипом, олією, відкладеннями солей і смол, окислюється тощо. п. Зі збільшенням відкладень зростає термічне опір стінки і погіршується теплообмен.
Знос теплообмінного апарату виявляється у наступному: зменшення товщини стінки корпусу, днища, трубних ґрат; выпучины і вм’ятини на корпусі і днищах; свищи, тріщини, прогары на корпусі, трубках і фланцах; збільшення діаметра отворів для труб в трубної ґратам; прогин трубних ґрат і деформація трубок; заклинювання плаваючих головок і ліквідовують ушкодження їх струбцин; ушкодження линзовых компенсаторів; ушкодження сальниковых пристроїв, катковых і пружинних опор; порушення гідроі термоизоляции.
Підготовка до ремонту включає виконання таких заходів: знижується надлишкове тиск до атмосферного і апарат звільняється з продукту; відключається арматура і ставляться заглушки усім підводять і отводящих трубопроводах; проводиться продування азотом чи водяникам пором із наступною промиванням водою і продувкой повітрям; виконується аналіз на наявність отруйних і вибухонебезпечних продуктов.
Далі виконуються такі роботи: зняття кришок апарату, люків, демонтаж обв’язки і арматури; виявлення дефектів вальцовки і зварювання, і навіть цілісності трубок гідравлічною і пневматичним випробуваннями на робочий тиск; часткова зміна чи відключення дефектних трубок, кріплення труб вальцовкой чи зварюванням; ремонт футерівки і антикорозійних покриттів деталей із застосуванням часткової заміною; ремонт чи заміна износившейся арматури, трубопроводів, регулювання запобіжних клапанів; зміна ущільнень розбірних сполук; вилучення трубок, чистка поверхні корпусу апарату і теплообмінних трубок, зачистка отворів в трубної ґратам, зачистка кінців трубок; заміна частин корпусу, днищ і зношених деталей; виготовлення нових трубок; монтаж трубного пучка і вальцовка труб в ґратам; ремонт плаваючих головок; монтаж резьбовых сполук; гідравлічне випробування межтрубной і трубної частин апарату пробним тиском; пневматичне випробування аппарата.
Очищення трубок від відкладень включає у собі обробку як внутрішніх, і зовнішніх поверхонь. Використовуються такі методи очищення: хімічні - застосовуються очищення від накипу 5 — 15% розчином соляної кислоти з додаванням інгібіторів; абразивні - поділяються на механічний (шомполы, свёрла, щётки, різці), гидропневматический (чистка здійснюється звичайною зубчастою металевої втулкойшомполом), гидромеханический (струменем води високого тиску) і піскоструминний; спеціальні - ультразвуковой.
Ремонт трубного пучка той самий, як й у апаратах повітряного охлаждения.
Корпус апарату, який має різноманітні выпучины і вм’ятини, виправляється ударами кувалди по мідної підкладці. Якщо неможливо усунути вищезазначені дефекти ударами і нагріванням, то повреждённые частини, або видаляються, чи них ставляться накладки.
Дефектні штуцери і трубні ґрати під час досягнення максимальних величин зносу і прогину заменяются.
Свищі й тріщини усуваються шляхом заварки чи постановкою накладок з попереднім видаленням дефектного участка.
З допомогою кольорової дефектоскопії визначають довжина і становище кінців тріщин, виявлених у корпусі. Ці кінці до заварки засверливают свёрлами. За появи гнездообразных тріщин повреждённые місця вирізаються і закриваються латками без гострих углов.
3.5. Ремонт ёмкостных аппаратов.
І тому типу апаратури характерні ушкодження цілісності і форми. Підготовлений до ремонту апарат озирається. Ділянки поверхні апарату і зварні шви, у яких виявлено несквозные тріщини, перевіряються керосином.
Тріщини глибиною менше половини товщини стінки обробляються вирубкою зубилом до чистого металу і завариваются. Наскрізні вузькі тріщини й тріщини глибиною понад половина товщини стінки обробляються протягом усього товщину металу вирубкою зубилом чи газовим різаком. Ділянки зі наскрізними проржавлениями і широкими тріщинами ремонтуються шляхом вирізки металу і приварки заплат.
Невеликі вм’ятини і выпучины вирізаються і би їхнє місце ввариваются заплаты.
Днище і нижній пояс резервуара можуть руйнуватися внаслідок поділу емульсії та накопичення грошових води. Відстояна вода містить солі, що сприяє підвищенню виразкової корозії. Корозія днища може бути настільки значної, що його доводиться заміняти новым.
При капітальний ремонт здійснюється заміна ушкоджених корозією аркушів чи поясів стінки, покриття чи днища резервуара.
Підготовка резервуара до ремонту полягає у відключенні резервуара загальної заводський схеми, очищенні резервуара від нафтопродукту, зачистці, пропарке, вентиляції і видаленні що залишилася бруду — пісок, окалина.
Дах резервуара піддається з боку інтенсивної корозії. За появи на покрівлі окремих отворів, коли покрівля має ще достатньої міцністю й безпекою в експлуатації, проводиться локальний ремонт покрівлі. За появи суцільний корозії змінюється все покрытие.
Список використаної литературы:
1. Виробництво аміачної селітри в агрегатах великий одиничної потужності/ М. Є. Іванов та ін. — М.: «Хімія», 1990.
2. Технологія ремонту хімічного оборудования/В. І, У. С.
Шеин — Л.: «Хімія», 1977.