Hазработка системи регулювання, контролю та реєстрації споживання енергоносіїв піччю швидкісного нагрева
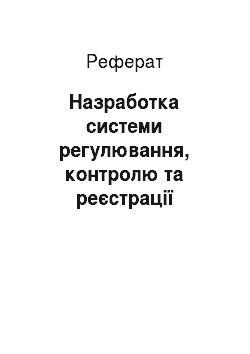
KOBE STEEL (предприятие-разработчик теорії диференційованої термічної обробки прокатних валків — ДТО) рекомендує наступний режим нагріву: до 960(С по металу за 3ч і витримка протягом 1ч за нормальної температури поверхні валка 960(С. швидкість нагріву (менш 140(С/ч) досить низька і обмежується, очевидно, можливостями застосовуваної системи опалення з радіаційними пальниками. За такої нагріванні… Читати ще >
Hазработка системи регулювання, контролю та реєстрації споживання енергоносіїв піччю швидкісного нагрева (реферат, курсова, диплом, контрольна)
[pic]1 ТЕХНОЛОГІЧНА ЧАСТЬ.
Світовий ринок пред’являє дедалі більше високі вимоги до показників якості опорних валків прокатних станів (твердість, глибина загартованого шару, розподіл залишкових напряжений).
Відомі такі технології гарту прокатних валків: в электромасляных ваннах, струмами промислової частоти, струмами високої частоти, регульованим охолодженням водою, водовоздушной сумішшю і др.
Однією з таких процесів є диференційована термічна обробка (надалі - ДТО) опорних валків прокатних станів. Технологічний процес ДТО спрямовано зниження енерговитрат при нагріванні валка до температури гарту з допомогою нагріву не всього обсягу валка, а лише поверхового (закаливаемого) слоя.
Суть ДТО ось у чому (схема і етапи режиму ДТО наведено малюнку 1):
Малюнок 1.1 — Схема і етапи режиму ДТО.
Етап 1 — попередній підігрів валка.
Виробляється в термічної печі з выкатным подом переведення матеріалу серцевини валка на більш пластичное стан, здатне витримати високі розтягують напруги при наступному інтенсивному нагріванні в печі швидкісного нагріву (надалі - ПСН).
Раціональна среднемассовая температура попереднього підігріву для всіх типорозмірів валків у межах Тп (500(С. За більш низьких температурах велика небезпека руйнації валка при швидкому нагріванні бочки зза недостатньою пластичності слабко прогрітої серцевини валка. Зі збільшенням температури попереднього підігріву підвищуються залишкові напруги після ДТО і, отже, зростає ймовірність руйнації валка після закінчення режиму. Необхідна рівномірність температури печі наприкінці підігріву (5(С.
Етап 2 — градиентный нагрівання в ПСН.
Параметри нагріву валка визначаються маркою стали, вимогами по глибині активного (загартованого) шару, рівнем тріщиностійкості металу центральній частині валка і розмірами можливих дефектів металургійного происхождения.
Оптимальна температура нагріву Тн вибирається з розрахунку отримати максимальну закаливаемость, тобто. максимальну твердість структури, образующейся в поверхневому шарі валка при загартуванню. Оптимальний режим нагріву складається з максимально інтенсивного нагріву поверхні бочки до температури Тн і витримці при даної температурі до прогріву на задану глибину. Обмежити інтенсивність нагріву можуть або можливість устаткування (потужність ПСН) або високі розтягують напруги, які творяться у центральної зоні валка при інтенсивному нагреве.
Етап 3 — витримка задля забезпечення прогріву бочки валка на задану глибину в ПСН.
Тривалість витримки за підтримки температури бочки валка на рівні температури нагріву Тн заздрості від бажаної глибини прогріву поверхневого шару. Натомість, оптимальна величина прогріву залежить від прокаливаемости сталі та інтенсивності подальшого охлаждения.
Етап 4 — транспортування валка з ПСН в спрейерную установку.
Тривалість перенесення валка з ПСН до спрейерной установці повинна бути зведена до мінімуму. Це пов’язано з тим, що у повітрі поверховий шар валка швидко втрачає тепло.
Етап 5 — інтенсивне водне охолодження в спрейерной установке.
Виробляється з максимально можливої щільністю зрошення із єдиною метою формування найсприятливішої структури та максимальної глибини активного слоя.
Етап 6 — м’яке регульоване водовоздушное охолодження в спрейерной установці з отогревом поверхности.
Аналізуючи цей етап триває примусовий теплосъем із поверхні валка теплового потоку, що надходить з внутрішніх верств. Тривалість водовоздушного охолодження визначається за умовою досягнення среднемассовой температури валка Т0 (температури копежа).
Етап 7 — відпустку в печі з выкатным подом.
Температура і тривалість відпустки визначаються з вимог на твердість бочки валка.
Новокраматорський машинобудівний завод — лідер вітчизняного машинобудування — одна із провідних постачальників валків прокатних станів для України, і у країни близького і далекого зарубіжжя. Заводом успішно освоєно перелічені вище технологии.
Технологія ДТО реалізована дільниці ДТО, що включає у собі дві термічні печі з выкатным подом, піч швидкісного нагріву, спрейерную установку.
Автоматизована систему управління технологічним процесом ДТО побудовано базі устаткування фірми «SIEMENS» по ієрархічної структуре.
1. Теоретичні відомостей про етапі диференційованої термічної обробки прокатних валків — градиентном нагріванні в печі швидкісного нагрева.
Параметри нагріву валка визначаються маркою стали, вимогами по глибині активного шару, рівнем тріщиностійкості металу центральній частині валка і розмірами можливих дефектів металургійного походження. Розглянемо докладніше чинники, що впливають вибір параметрів нагрева.
Оптимальна температура нагріву ТН вибирається з розрахунку отримати максимальну закаливаемость, тобто. максимальну твердість структури мартенситу і залишкового аустеніту, образующейся в поверхневому шарі валка при загартуванню. Зі збільшенням температури нагріву ТН в легованих валковых сталях збільшується ступінь розчинення карбідів як наслідок, підвищується прокаливаемость сталі та твердість мартенситной матриці. Та заодно одночасно збільшується зміст залишкового аустеніту в загартованою структурі, що веде до їх зниження твердості. Дія цих двох протилежно спрямованих чинників спричиняє до появи максимуму на кривою залежності твердості загартованою структури стали заданого складу від температури нагрева.
Додатковим чинником, яке обмежує ТН згори, є негативний вплив перегріву до зростання зерна аустеніту і, отже, бруталізація структури мартенситу після гарту. З іншого боку, підвищення температури нагріву збільшує рівень максимальних растягивающих залишкових напруг. Для стали 90ХФ оптимальної температурою нагріву при ДТО є ТН (920(С, для стали 75ХМ ТН (950(С.
Оптимальний режим нагріву складається з максимально інтенсивного нагріву поверхні бочки до температури ТН і витримці при даної температурі до прогріву на задану глибину вище температури аустенизации АС3. Обмежувати інтенсивність нагріву можуть або можливість устаткування (потужність печі швидкісного нагріву — ПСН), або високі розтягують напруги, які творяться у центральної зоні валка при інтенсивному нагреве.
KOBE STEEL (предприятие-разработчик теорії диференційованої термічної обробки прокатних валків — ДТО) рекомендує наступний режим нагріву: до 960(С по металу за 3ч і витримка протягом 1ч за нормальної температури поверхні валка 960(С. швидкість нагріву (менш 140(С/ч) досить низька і обмежується, очевидно, можливостями застосовуваної системи опалення з радіаційними пальниками. За такої нагріванні виникаючі максимальні розтягують напруги, створених наприкінці витримки, дуже малі (не більше 180 МПа всім діаметрів). Отже, з погляду безпеки режим градиентного нагріву істотно менш напружений, ніж режим попереднього підігріву. При заданому режимі поверхневий пласт валків різних діаметрів прогрівається на 140−160 мм.
Проектируемая ПСН, обладнана швидкісними пальниками, за даними базового варіанта може забезпечити швидкість підйому температури поверхні бочки валка до 300(С/ч (по металу). Для визначення раціонального діапазону параметрів нагріву розробниками базового варіанта (фірма «Термосталь» р. Санкт-Петербург) виконано цикл розрахунків нагріву валків з стали 75ХМФ до 950(С поверхнею бочки з варіюванням діаметра валків D=1200, 1600, 2000 мм, температури попереднього підігріву ТП=400, 450, 500(С і швидкості нагріву по металу VН=100, 200, 300(С/ч. У цьому фіксувався критичний розмір дефекту всім режимов.
Результати підрахунків наведено малюнку 1.2, де добре видно вплив масштабного чинника: зі зростанням діаметра форма залежності критичного дефекту від швидкості нагріву змінюється на протилежну. Якщо діаметра 1200 мм ДКР зменшується зі збільшенням швидкості нагріву, для діаметра 1600 мм залежність немонотонна, то тут для діаметра 2000 мм розмір критичного дефекту збільшується зі зростанням VН.
При виборі оптимального поєднання ТП і VН попередньо можна керуватися формальним обмеженням до рівня допустимих дефектів по ОСТ 24.023.33−86 «Ультразвукової контроль ВХП», який допускає для валків діаметром понад 1200 мм одиночні несплошности з еквівалентним діаметром до 200 мм. Беручи це обмеження, видно з малюнка 1.2, що «застосування максимально можливої інтенсивності нагріву (300(С/ч по металу) припустимо при ТП=480(С, 450(С і 400(С для валків діаметром відповідно 1200, 1600 і 2000 мм.
Малюнок 1.2 — Розподіл температури в поверхневому шарі валків діаметром 1200, 1600 і 2000 мм зі сталі типу 75ХМФ наприкінці градиентного нагрева.
Слід сказати, що реальний проектування режиму нагріву можна тільки після визначення реально можливої максимальної інтенсивності нагріву під час теплотехнических випробувань ПСН, і навіть реальної тріщиностійкості металу у серцевині валків із різних марок стали, підданих улучшению.
Тривалість витримки за підтримки температури бочки валка на рівні температури нагріву ТН залежить від бажаної глибини прогріву поверхневого шару до температури аустенизации АС3. Натомість, оптимальна величина прогріву залежить від прокаливаемости сталі та інтенсивності охолодження. Суть процесу в следующем.
При збільшенні глибини аустенизированного шару росте, і глибина загартованого шару, але до певної величини, обмеженою можливостями стали (прокаливаемостью) і спрейерной установки (максимальної інтенсивністю охлаждения).
Зростання глибини прогріву понад цього оптимального значення призводить до нагромадженню зайвого тепла в валку, що починає знижувати швидкість охолодження за українсько-словацьким кордоном загартованого шару, підвищує температуру на осі валка і призводить до зростання залишкових напруг. Коротенько Україні цього принципу слід охарактеризувати так: годі було прогрівати валок більше необходимого.
Для ілюстрації малюнку 1.3 для валка діаметром 1200 мм показані залежності глибини аустенизированного шару LА і загартованого шару LЗ (загартованим шаром умовно прийнято шар твердістю вище 45HS, що відповідає наявності у структурі щонайменше 50% бейнитно-мартенситной суміші) від тривалості нагріву за нормальної температури поверхні ТН=950(С (сталь 75ХМФ) і ТН=920(С (сталь 90ХФ). Нагрівання до температури ТН проводився зі швидкістю 300(С/ч по металу, охолодження — з максимально можливої для даної спрейерной установки, що передбачає проводити охолодження з максимальної щільністю зрошення від 1.14 кг/м2(с (валок діаметром 2000 мм) до 1.9 кг/м2(с (валок діаметром 1200 мм).
Малюнок 1.3 — Залежність глибини аустенизированного шару LЗ (чи температури центру ТЦ (б) від тривалості прогріву при градиентном нагріванні валка діаметром 1200 мм.
З малюнка 1.3 видно, що передвиборне збільшення тривалості прогріву понад 1 год мало збільшує глибину загартованого шару для валка зі сталі 75ХМФ і 90ХФ. У цьому прогрів понад 1.5 год навіть знижує глибину загартованого шару в валку зі сталі 90ХФ. Додатковим аргументом на користь обмеження тривалості нагріву є такий факт, що з витримці температура центру зростає досить інтенсивно, що супроводжуватися збільшенням залишкових напряжений.
При виборі оптимальної тривалості прогріву треба враховувати, що зі зростанням витримки за нормальної температури аустенизации збільшуються залишкові напруги в валку після гарту, тому цей параметр треба обирати з урахуванням обмежень до рівня залишкових напряжений.
Натомість, рівень залишкових напруг можна визначити, лише обравши режим охолодження, який залежить від режиму нагріву. Отже, параметри нагріву і охолодження виявляються взаємозалежними. Це означає необхідність багатоваріантних (многопараметрических) розрахунків на стадії проектування режиму визначення оптимальних значень параметрів ДТО.
2. Призначення, структура і склад АСУ ПСН.
1.2.1 Назначение.
ПСН варта швидкісного нагріву бочки валка (попередньо підігрітого в печі з выкатным подом до температури 400−550© із постійною швидкістю 100−300(С/ч (по металу) до температури гарту 920−970(С і наступної витримкою протягом 45−60 хв. Через війну нагріву в ПСН в валку формується градиентное розподіл температури з прогревом поверхневого шару на задану глубину.
Спрейер призначений для регульованого охолодження бочки валка, при цьому першому етапі використовується інтенсивне водне охолодження з максимальним витратою води протягом 30−60 хв. З другого краю етапі застосовується м’яке водо-воздушное охолодження із регульованим витратою води протягом 75- 145 мин.
Устаткування системи управління (СУ) ПСН призначено керувати тепловим режимом печі швидкісного нагріву в ручному й автоматизованому режиме.
Устаткування СУ спрейера призначено керувати режимом охолодження на спрейерной установці в ручному й автоматизованому режиме.
Устаткування системи управління призначено до роботи на наступних умовах: — номінальне значення кліматичних чинників довкілля по ГОСТ 15 150;
69, ГОСТ 15 543–70 для кліматичного виконання У; - температура довкілля +5(С до +50(С, довкілля не вибухонебезпечна, із вмістом коррозионно-активных агентів у атмосфері типів I і II по ГОСТ 15 150–69, верхня концентрація інертної пилу (зокрема. токопроводящей) повітря трохи більше 10 мг/м (; - харчування здійснюється від трехфазной мережі змінного струму; - коливання напруги харчування щодо номінального не більше 0,85 -.
1,1; - за способом обслуговування шаф і пультів з розміщеними у яких технічними засобами АСУ виконані одностороннього обслуговування з доступом попереду; - за захистом персоналу від поразки електричним струмом при дотику до електроустаткування й у зменшення перешкод в ланцюгах управління застосована система шин для заземлення і вирівнювання потенціалу PE, заземлення екранів кабелів і проводов.
1.2.2 Структура і склад АСУ.
Робота автоматизованих системам управління СУ ПСН і СУ спрейера полягає в засадах управління технологічними процесами з використанням одного микропроцессорного контролера, здійснює одночасне управління обома установками у реальному масштабі часу. Для зв’язок між окремими електронними пристроями системи управління (контролер, децентралізована периферія, панель оператора і промисловий комп’ютер) організовані локальні мережі управління MPI і Profibus DP (Європейський стандарт EN 50 170).
Архітектура системи управління побудована по дворівневої схеме:
— нижній рівень управления;
— середній рівень управления.
Нижній рівень управління (НУУ) включає у собі модулі микропроцессорного контролера SIMATIC S7 — 315 DP з цифровими і аналоговими входами-выходами та її децентралізовану периферію (віддалені входы-выходы), об'єднану мережею PROFIBUS DP. Устаткування НУУ здійснює збирати інформацію з пультів, шаф і датчиків, її попереднє опрацювання і передачу на середній рівень управління, і навіть видачу управляючих впливів на виконавчі механізми установки в залежність від алгоритму управления.
Середній рівень управління (СУУ) є промисловий комп’ютер SIMATIC RI25P, панель оператора ОР7 і микропроцессорный контролер SIMATIC S7−315DP об'єднані мережею MPI. Устаткування СУУ призначено для введення параметрів технологічного процесу, програмного управління, контролю, діагностику і протоколювання ходу технологічного процесу .
До складу системи управління входят:
— шафу контроллера;
— шафу електроустаткування, КВП і А;
— шафу компьютерный;
— пульт управления;
— датчики технологічних параметрів й електрообладнання на механізмах ПСН і спрейерной установки.
1.2.3 Управління тепловим режимом ПСН з допомогою системи управління з урахуванням микропроцессорного контроллера.
Систему керування тепловим режимом ПСН реалізована за принципами управління технологічним процесом як реального часу з урахуванням микропроцессорного контролера і послуг призначена на вирішення наступних задач:
— підготовки й завдання змінних технологічного процесу настройки параметрів регулирования;
— управління автоматикою безпеки печи;
— управління розжигом горелок;
— регулювання температури поверхні бочки прокатного валка чи температури печи;
— регулювання співвідношення «газ-воздух»;
— регулювання тиску у робочому просторі печи;
— візуалізації, контролю, діагностику і протоколювання ходу технологічного процесса.
До складу системи управління функціонально входять такі подсистемы:
— підсистема виміру технологічних параметров;
— підсистема візуалізації, контролю, діагностику і протоколирования;
— підсистема автоматичного регулирования;
— підсистема автоматики безопасности.
;
1.2.4 Підсистема виміру технологічних параметров.
Підсистема виміру технологічних параметрів варта збирання та опрацювання інформації від аналогових і дискретних датчиків технологічного процесса.
До контрольованим аналоговим параметрами относятся:
— температура газової середовища у трьох точках робочого простору печи.
(близько торцевих стінок і посередині печи);
— температура поверхні нагреваемого металла;
— температура відведених газів перед димовим клапаном;
— температура відведених димових газів після повітряного клапана на дымопроводе;
— тиск у робочому просторі печи:
— витрати на печь;
— витрата повітря на печь;
— становище заслінок газу, повітря і дымоудаления.
Контроль температури у робочому просторі печі здійснюється з допомогою термопар типу ТПР-1788.
Контроль температури нагреваемого металу виробляється автоматичним оптичним пирометром ARDOCELL PZ20 фірми Siemens.
Контроль температури відведених газів здійснюється з допомогою термопар ТХА-2388.
Тиск в печі вимірюється вимірювальним перетворювачем «Сапфир-22МДИВ».
Витрата газу та повітря вимірюється перед регулюючими органами комплектом приладів, які з зондів вимірювання витрати SDF фірми SKI і вимірювальних перетворювачів SITRANS P фірми Siemens, розміщених по місцеві на трубопроводах газу та повітря. Застосування зондів зумовлено необхідністю мінімізації втрат тиску з повітряному тракту печі і більш широким тоді як вимірювальними діафрагмами діапазоном виміру. Програмою контролера передбачається зменшення миттєвих (поточних) вимірів значень витрат газу та повітря для згладжування пульсації результатов.
Положення заслінок газу, повітря і видалення диму, пов’язаних через тяги з виконавчими механізмами контролюється блоками БСПТ-10 умонтованими в МЭО.
До контрольованим дискретним параметрами ставляться інформаційні сигналы:
— ситуацію і стан допоміжних механізмів печи;
— мінімальне і забезпечити максимальне відкриття МЭО;
— наявність спрацьовування електромагнітних клапанів горелок;
— наявність контролю смолоскипа горілок і сигналів з датчиків автоматики безопасности;
— поточний стан кнопок управления.
Інформації про становищі й стані допоміжних механізмів печі надходить на входи контролера з сухих контактів проміжних реле і служить з метою диагностики.
Сигнали про мінімальному і максимальному відкритті МЭО надходять при спрацьовуванні їх вбудованих кінцевих вимикачів і служать обмеження ходу виконавчих механизмов.
Наявність спрацьовування електромагнітних клапанів фірми Kromschroeder контролюється умонтованими покажчиками положения.
Наявність полум’я смолоскипа горілок контролюється приладами Ф34.3.
Поточне стан кожної кнопки управління постійно відстежується контролером і їх зміні виробляються дії відповідність до функціональним призначенням відповідної кнопки.
1.2.5 Підсистема візуалізації, контролю, діагностику і протоколирования.
Підсистема візуалізації, контролю, діагностику і протоколювання варта організації доступу в діалоговому режимі операторатехнолога й майстра КВП й О печі до виконання операцій передбачених технологією під час роботи ПСН. До складу підсистеми функціонально входять промисловий комп’ютер SIMATIC RI 25P (комп'ютер) і панель оператора SIMATIC OP7 (панель оператора ОР7), працюючі під керівництвом контролера SIMATIС S7−315 DP (контролер), усе обладнання фірми Siemens.
Комп’ютер і панель оператора ОР7 виконують функцію відображення змінних технологічного процесу (температура, тиск тощо.), введення технології, параметрів (завдання регуляторам, настроечные коефіцієнти і т.д.) і служать як для видачі управляючих команд на контролер під управлінням оператора-технолога.
Для майстра КВП й О передбачена можливість зміни настройки параметрів регуляторів, параметрів вентиляції, розжига тощо., і навіть зміни конфігурації комп’ютера та панелі оператора ОР7 (роботу з аварійними повідомленнями, зміна паролів, установка часу й т. д).
Працюючи ПСН система діагностики контролера здійснює безупинної контролю над станом механізмів і параметрів технологічного процесу управляє видачею текстових повідомлень на монітор комп’ютера та панель оператора ОР7, і навіть світловий і звуковий сигнализацией.
Після запуску режиму печі по температурно-временному графіку здійснюватися протоколювання ходу технологічного процесу із записом на жорсткий диск пам’яті промислового компьютера.
1.2.6 Підсистема автоматичного регулирования.
Підсистема автоматичного регулювання варта управління тепловим режимом печі і включає у собі три контуру регулирования:
— контур регулювання температури печи,.
— контур регулювання співвідношення «газ-воздух»;
— контур регулювання тиску в печи.
Регулювання температури в печі здійснюється шляхом на виконавчий механізм, пов’язаний регульованої тягою з заслінкою на газопроводі, у функції зміни температури печі по температурнотимчасовому графіку нагріву. Завдання регулятору формується в контролері по алгоритму управління у вигляді одиничних значень залежно від заданої технології (зміна завдання температури за швидкістю чи у времени).
Регулювання співвідношення «газ — повітря» здійснюється шляхом на виконавчий механізм, пов’язаний регульованої тягою з заслінкою на повітряному трубопроводі, до функцій каскадної схеми регулювання співвідношення газо-повітряної суміші. За цією схемою провідний регулятор (температури) працює у функції зміни температури печі по температурно — тимчасовому графіку нагріву і навіть формує поточне завдання відомому (співвідношення «газ-воздух») за графіком співвідношення витрат газу та повітря, а ведений регулятор своєю чергою формує котра управляє вплив на виконавчий механизм.
Регулювання тиску у робочому просторі печі ввозяться функції підтримки постійним заданого тиску в печі, шляхом впливом на виконавчий механізм пов’язаний регульованої тягою з заслінкою дымоудаления.
Елементи підсистеми автоматичного регулювання уніфіковані і складаються з безконтактних тиристорных реверсивних пускателей ПБР і виконавчих електричних механізмів МЭО. Контроль становища виконавчого органу ведеться через токовый датчик зворотного зв’язку та индицируется на відповідному екрані комп’ютера чи панелі оператора ОР7.
Управління виконавчими механізмами можливо, й при відключених регулятори — в ручному режимі, дистанційно, із технологічної клавіатури панелі оператора ОР-7 чи з клавіатури компьютера.
1.2.7 Підсистема автоматики безопасности.
Підсистема автоматики безпеки варта експлуатацію у складі устаткування печі швидкісного нагріву. Функціонально апаратна частина автоматики безпеки працює автономно від контролера і управляє електромагнітом, які встановлюються за на предохранительно-запорном клапані на введення газу до печи.
Схема безпеки реалізована з урахуванням контролера «LOGO!» фірми Siemens. Контролер «LOGO! «є логічне пристрій з 12 дискретними входами (24В), 8 релейными виходами і реалізують алгоритм управління отсечным газовим клапаном печі і аварійної звуковий і світловий сигнализацией.
Включення електромагніта отсечного газового клапана здійснюється кнопкою «Отсечной клапан. Включити». Включення отсечного клапана можливе тому випадку, а то й виконуються умови відсічення газа.
Відсічення газу ввозяться наступних случаях:
— при зниженні тиску газу після регулятора тиску нижче припустимого предела;
— у разі підвищення тиску газу після регулятора тиску вище припустимого предела;
— при зниженні тиску повітря на воздухопроводе печі нижче припустимого предела;
— при натисканні кнопки «Отсечной клапан. Отключить»;
— при натисканні кнопки «Аварійний стоп»;
— при сигналі від контролера «Газ відключити» (даний сигнал видається контролером при погасании смолоскипів горілок або за падінні тиску в печі нижче аварійно припустимого предела).
При спрацьовуванні отсечного клапана видається звуковий сигнал і загоряється лампа, сигнализирующая причину відсічення газа:
— при зниженні тиску газу після регулятора тиску нижче припустимого краю — лампа «Тиск газу мало»;
— у разі підвищення тиску газу після регулятора тиску вище припустимого краю — лампа «Тиск газу велико»;
— при зниженні тиску повітря на воздухопроводе печі нижче припустимого краю — лампа «Тиск повітря мало»;
— при натисканні кнопки «Отсечной клапан. Відключити», при натисканні кнопки.
«Аварійний стоп» і за сигналі від контролера «Газ відключити» — лампа «Відсічення газа».
3. Аналіз наявної системи управління і завдання проектирования.
Існуюча в базовому варіанті систему управління піччю ПСН має поруч достоїнств і повним вад. До переваг слід віднести централізоване управління всім ділянкою ДТО від однієї контролера, високий рівень автоматизації процесу нагріву валка і механізації загрузочно-разгрузочных работ.
До вад такої системи можна віднести такі: — застосування електроприводів обертання і орієнтування, мають значні габарити, вартість будівництва і які мають значно меншою надійністю тоді як аналогічними гідравлічними приводами;
— застосування електричних регулюючих механізмів в магістралях подачі газу та повітря, які забезпечують регулювання на вельми вузькому диапазоне;
— відсутність синхронізації роботи приводів і регуляторів подачі газо-повітряної смеси;
— відсутність споживання енергоносіїв (газу і электроэнергии);
— використання у системи управління дорогого імпортного оборудования.
Отже, проектируемая система мусить бути, наскільки можна позбавлена від цих коштів недоліків чи, по крайнього заходу, зводити їх до мінімуму. Основними завданнями проектування являются:
— розробка яка стежить системи регулювання, контролю та реєстрації споживання енергоносіїв зниження собівартості кінцевий продукт — валків для прокатних станов;
— заміна електричних приводів на гідравлічні, які мають меншими габаритами (непотрібен установки редукторів та інших передатних механізмів), вартістю (реалізовані на апаратурі вітчизняних) і надежностью;
— установка регуляторів подачі газо-повітряної суміші з пропорційним електричним управлінням, які забезпечують регулювання широтою діапазону із високим точностью;
— забезпечення синхронізації роботи приводів і регуляторів подачі підтримки процесу прогріву валка з оптимальними параметрами;
— забезпечення мінімальних витрат за установку самої системи з допомогою можливо мінімального зміни вже існуючої - тобто. без зміни загальної структури ділянки загалом і печі зокрема. ———————————- [pic].
Т, (С Расстояние від поверхні, мм.
[pic].
Глубина шару, мм.
Продолжительность прогрева, ч.
[pic].
Продолжительность прогрева, ч Тц,(С а).
б).
T.
(.
Tп.
Tн.
Tо.