Абз
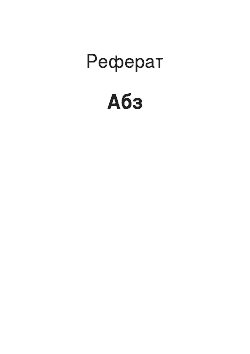
Для аналізованого району взимку переважають вітри південного, югосхідного і південно-західного напрямів. Влітку переважають вітри південного і північного напрямів (рис 1.2). Середня швидкість вітру на січень дорівнює 3,41 м/с. Максимум з середніх швидкостей по румбам на січень — 6,8 м/с. Середня швидкість вітру впродовж липня дорівнює 3,55 м/с. Максимум з середніх швидкостей по румбам впродовж… Читати ще >
Абз (реферат, курсова, диплом, контрольна)
Міністерство Спільного і Фахового Освіти Російської Федерации.
Ростовський державний будівельний университет.
Курсової проект дисциплине.
Виробничі підприємства транспортних сооружений.
АБЗ.
Расчетно-пояснительная записка.
111 774 РПЗ.
Виконав студент групи Д-327.
Стрижачук А. В.
Руководитель:
Литвинова Л. А.
Завідуючий кафедры:
Илиополов З. К.
Ростов-на-Дону.
1999 г.
Вихідні данные.
Довжина ділянки будівництва 10.
Ширина проїзній частині 7.
Товщина асфальтобетону 0,1.
Тип асфальтобетону В.
Щільність асфальтобетону 2.
Кількість змін 1.
Тривалість робіт 4.
Довжина транспортування 11.
Питома опір стали 0,12?10−4 Ом? м.
Климатическая характеристика району. 4 1. Обгрунтування розміщення АБЗ. 5 1.1. Порівняння часу остигання асфальтобетонної суміші згодом її доставки доречно укладання. 5 1.2. Джерела забезпечення АБЗ водою і електроенергією. Нормативні вимоги. 5 2. Режим роботи заводу і її. 5 2.1. Годинна продуктивність АБЗ, QЧ, т/ч. 5 2.2. Розрахунок витрати матеріалів. 6 3. Визначення довжини залізничної колії для прирельсовых АБЗ. 7 3.1. Кількість транспортних одиниць N, прибуваючих на добу. 7 3.2. Довжина фронту розвантаження L, м. 7 4. Склади мінеральних матеріалів. 7 4.1. Розрахунок щебеневих штабелів. 7 4.2. Вибір і розрахунок стрічкових конвеєрів. 7 4.3. Вибір типу бульдозера. 8 5. Битумохранилище. 9 5.1. Розрахунок розмірів битумохранилища. 9 5.2. Кількість тепла, необхідне нагріву бітуму у сховищі і приямку Q, кДж/ч. 9 5.3. Розрахунок електричної системи підігріву. 10 6. Визначення кількості битумоплавильных установок. 11 6.1. Годинна продуктивність казана ПК, м3/ч. 11 6.2. Розрахунок кількості котлів. 11 7. Розрахунок складу і устаткування подачі мінерального порошку. 11 7.1. Розрахунок місткості силосу в склад. 12 7.2. Розрахунок пневмотранспортной системи. 12 8. Розрахунок потреби в електричної енергії і воді. 16 8.1. Розрахунок потрібного кількості електроенергії. 16 8.2. Визначення загального витрати води. 16 8.3. Визначення витрати води На оновлення запасу в пожежному резервуарі, ЧПСШ, м3/ч. 16 8.4. Визначення діаметра труби водогінної мережі, dТР, м. 16 9. Технологічна схема приготування модифікованого бітуму. 17 Література. 18.
Кліматична характеристика района.
Кемеровська область лежить у III-ей дорожно-климатической зоне.
— зоні з великим зволоженням грунтів в окремі періоди годы.
Для району прокладання автомобільної дороги характерний клімат з «холодною взимку і надзвичайно теплим влітку, що це випливає з дорожно-климатического графіка (рис.
1.1).
Літо тепле: середньодобова температура найбільш спекотного месяца.
(липня) становить +18,4?С; зими холодні зі середньодобовій температурою найбільш холодного місяці (січня) -19,2?С. Негативні температури повітря бувають з 17 листопада до березня, а розрахункова тривалість періоду негативних температур Т=179 сут.
Абсолютний максимум температури повітря на року сягає +38?С, мінімум -55?С. Отже, амплітуда температури становить 93? С.
Річна середня добова амплітуда температури повітря буває июне.
(13,2?С), а максимальна у лютому (30,2?С).
Протягом року випадає 476 мм опадів; кількість опадів на рідкому і змішаному вигляді 362 мм протягом року; добовий максимум 46 мм. Середня за зиму висота снігового покрову становить 51 див, а число днів із сніжним покровом до 162 сут (період 03.11 — 13.04).
Для аналізованого району взимку переважають вітри південного, югосхідного і південно-західного напрямів. Влітку переважають вітри південного і північного напрямів (рис 1.2). Середня швидкість вітру на січень дорівнює 3,41 м/с. Максимум з середніх швидкостей по румбам на січень — 6,8 м/с. Середня швидкість вітру впродовж липня дорівнює 3,55 м/с. Максимум з середніх швидкостей по румбам впродовж липня — 4,4 м/с.
1. Обгрунтування розміщення АБЗ.
Завод буде розміщений поблизу залізничних колій, бо всі дорожньо-будівельні матеріали доставлятимуться по ним.
1.1. Порівняння часу остигання асфальтобетонної суміші згодом її доставки доречно укладки.
Необхідно порівняти час остигання суміші t1, год, згодом її доставки доречно укладання t2, год (t1?t2). де G — кількість суміші в кузові самоскида, для самоскида ЗИЛ-ММЗ;
555, G=4500 кг;
ССМ — теплоємність гарячої суміші, ССМ=1,1 кДж/(кг??С);
F — площа стінок кузова самоскида, для самоскида ЗИЛ-ММЗ-555.
F=11 м2; h — коефіцієнт теплопередачі, h=168 кДж/(м2?ч??С);
ТАБЗ — температура суміші при відправлення з АБЗ, ?С;
ПММ — температура суміші у її укладанні, ?С;
ТБ — температура повітря, ?З. де L — дальність транспортування, км; v — швидкість руху самоскида, v=40…60 км/ч.
1.2. Джерела забезпечення АБЗ водою і електроенергією. Нормативні требования.
Забезпечення АБЗ водою відбувається шляхом водозабору з водогінної мережі. Електроенергія постачається з міської мережі. АБЗ розміщують з подветренной боку до населеному пункту, з відривом не ближче 500 м від цього. Майданчик АБЗ має бути досить рівній, з ухилом 25−30‰, які забезпечують відвід поверхневих вод. Коефіцієнт використання площі може бути щонайменше 0,6, а коефіцієнт забудови — не менее.
0,4. Рівень грунтових вод — не вище 4 м.
При розміщення будинків та споруд біля заводу треба враховувати следующее:
1. Будівлі і споруди із підвищеною пожежної небезпекою слід ставити з подветренной боку стосовно іншим зданиям;
2. Будівлі і споруди допоміжного виробництва повинні розташовуватися у зоні цехів основного производства;
3. Складські споруди потрібно розташовувати з урахуванням максимального використання допомогою залізничних і інших під'їзних шляхів для навантажувальних, розвантажувальних операцій та забезпечення подачі матеріалу до основним цехах найкоротшим путем;
4. Енергетичні об'єкти потрібно розташовувати стосовно основним споживачам з найменшої протяжністю трубопроводу і ЛЭП;
5. При устрої тупикових доріг необхідна за кінці глухого кута передбачати петлевые об'їзди чи майданчики розміром не менее.
12×12 м. для розвороту автомобилей.
2. Режим роботи заводу та її производительность.
2.1. Годинна продуктивність АБЗ, QЧ, т/ч.
де П — необхідну кількість асфальтобетонної суміші, т;
Ф — плановий фонд часу. де 8 год — тривалість зміни; n — кількість смен;
22,3 — кількість робітників днів, у місяці; m — кількість місяців укладання смеси;
0,9 — коефіцієнт використання обладнання протягом смены;
0,9 — коефіцієнт використання обладнання перебігу m місяців. де k — коефіцієнт, враховує нерівномірний витрата суміші, k=1,1…1,5;
F — площа укладання асфальтобетонної суміші, м2, F=10 000?7=70 000 м2; h — товщина укладання асфальтобетонної суміші, м;
? — щільність суміші, ?=2,0…2,4 т/м3.
Отримане значення округляем до цілого числа і приймаємо змішувач типу ДС-617.
2 Розрахунок витрати материалов.
Вимоги до материалам.
Для приготування гарячої суміші застосовуються грузлі нафтові бітуми марок БНД 60/90, БНД 90/130. Щебінь треба використовувати природний каменю. Не допускається застосування щебеню з глинистих, вапняних, глинисто-песчаных і глинистих сланців. Піски застосовуються природні чи дробленные. Мінеральний порошок застосовується активізований і активізований. Допускається використовувати як мінерального порошку подрібнені металургійні шлаки і пилові відходи промисловості. Активізований мінеральний порошок одержують у результаті помолки кам’яних матеріалів присутності активизирующих добавок, як яких використовують суміші які з бітуму и.
ПАР у прийнятому співвідношенні 1:1.
Добова потреба матеріалів: де 8 год — тривалість зміни; n — число смен;
QЧ — годинна продуктивність заводу, т/ч (м3/ч);
Nki — потреба у Ki компоненті на 100 т асфальтобетонної смеси.
З огляду на природне зменшення (2% для щебеню, піску, бітуму і 0,5% для мінерального порошку) получаем:
Таблиця 1. Потреба АБЗ в мінеральних матеріалах. |Матеріал |Одиниця |Добова |Норма запаса,|Запас | | |измерени|потребность|дней |одноразового | | |я | | |зберігання | |Щебінь | м3 |72,2 |15 |1083 | |Мінеральний |т |24,7 |15 |387 | |порошок | | | | | |Бітум |т |18,1 |25 |452,5 |.
3. Визначення довжини залізничної колії для прирельсовых АБЗ.
1 Кількість транспортних одиниць N, прибуваючих в сутки.
де Qi — добова потреба, т (m=V??); k — коефіцієнт нерівномірності подачі вантажу, k=1,2; q — вантажопідйомність вагона, т;
?щ — щільність щебеню, ?щ=1,58 т/м3.
3.2. Довжина фронту розвантаження L, м.
де l — довжина вагона, l=15 м; n — число подач на добу, n=1…3.
4. Склади мінеральних материалов.
1 Розрахунок щебеневих штабелей.
Зазвичай для АБЗ проектуються склади щебеню і піску відкритого штабельного типу невеличкий ємності з погрузочно-разгрузочными механізмами (конвеєри, фронтальні навантажувачі). Під час проектування слід передбачити бетонне підставу чи підставу з ущільненого грунту, водовідведення від штабелів, розподільні стінки між штабелями, подачу матеріалів штабелі й у агрегат харчування ленточными транспортерами.
4.2. Вибір і розрахунок стрічкових конвейеров.
На АБЗ для безупинної подачі мінерального матеріалу використовують стрічкові і гвинтові конвеєри. Ленточными конвеєрами можна переміщати пісок, і щебінь в горизонтальному напрямку і з точки не превышающим.
22?. Виконують стрічкові конвеєри з кількох верств прогумованої бавовняною тканини. Ширина стрічки У, м, визначається по годинниковий продуктивності: де Q — годинна продуктивність, т/ч; v — швидкість руху стрічки, м/с;
? — щільність матеріалу, т/м3.
Вибираємо конвеєр типу С-382А (Т-44).
4.3. Вибір типу бульдозера.
Таблиця 2. Марка бульдозера та її характеристики. |Тип і марка |Мощность|Отвал | |машини |двигател| | | |я, кВт | | | | |Тип |Розміри, мм|Высота |Заглублени| | | | | |підйому, |е, мм | | | | | |мм | | |ДЗ-24А (Д-521А)|132 |Неповоротны|3640×1480 |1200 |1000 | | | |і | | | |.
Продуктивність ПЭ, т/ч обраного бульдозера:
де V — обсяг призми волочіння, V=0,5BH2=0,5?3,64?(1,48)2=3,987 м³, тут У — ширина відвалу, м; М — висота відвалу, м; kР — коефіцієнт розпушення, kР = 1,05…1,35. kПР — поправочний коефіцієнт обсягу призми волочіння, залежить від співвідношення ширини У і висоти М відвалу Н/В=0,41, і навіть фізико-механічних властивостей розроблюваного грунту, kПР=0,77; kВ — коефіцієнт використання машин за часом, kВ=0,8;
ТЦ — тривалість циклу, с;
ТЦ=tН+tРХ+tХХ+tВСП, тут tН — час набору материала,.
де LН — довжина шляху набору, LН=6…10 м; v1 — швидкість на першій передачі, v1=5…10 км/ч;
tРХ — час переміщення грунту, с,.
де L — дальність транспортування, м, L=20 м; v2 — швидкість другого передачі, v2=6…12 км/ч;
tХХ — час холостого ходу, с,.
де v3 — швидкість цього разу третьої передачі, v3=7…15 км/год; tВСП = 20 з;> ТЦ = 3,84 + 7,2 + 9,16 + 20 = 40,2 с;
5. Битумохранилище.
5.1. Розрахунок розмірів битумохранилища.
Для приймання й зберігання в’язких влаштовують ямные постійні й тимчасові битумохранилища лише закритого типу. Битумохранилища влаштовують на прирельсовых АБЗ з битумоплавильными установками.
Сучасні закриті битумохранилища ямного типу би мало бути захищені від доступу вологи як зовнішньої, і підземної шляхом устрою спеціальних будинків, дренажей чи навісів. Глибина ямного сховища допускається не більше 1,5−4 метрів за залежність від рівня грунтових вод.
Досягнення робочої температури застосовують электронагреватели.
Найбільш перспективний спосіб нагріву бітуму — розігрів в рухливих шарах з допомогою закритих нагрівачів. Для паркана бітуму з сховища влаштовують приймачі з боці чи центрі сховища. Отже, битумохранилище складається з власне сховища, приямку і устаткування підігріву і передачі битума.
Значення запасу одночасного зберігання бітуму округляем до 500, тоді середня площа F, м2 битумохранилища:
де Є — ємність битумохранилища, м3; h — висота шару бітуму, h = 1,5…4 м.
Потім, з значення будівельного модуля, рівного трьом, й стосунку довжини L до ширини У битумохранилища, рівного L/B = 1,5, призначаємо середні значення довжин Lср і Вср.
Оскільки стінки битумохранилища створюють із откосом:
5.2. Кількість тепла, необхідне нагріву бітуму у сховищі і приямку Q, кДж/ч.
де Q1 — кількість тепла, затрачуване на плавлення бітуму, кДж/ч.
де? — прихована теплота плавлення бітуму, ?=126 кДж/кг;
G — кількість подогреваемого бітуму, кг/ч, G = 0,1?Qсм, де Qсм.
— продуктивність обраного змішувача, кг/ч.
Q2 — кількість тепла, затрачуване на підігрів бітуму, кДж/ч:
де K — коефіцієнт, враховує втрати тепла через стінки сховища і дзеркало бітуму, K = 1,1;
Рб — теплоємність бітуму, Рб =1,47…1,66 кДж/(кг?єС);
W — зміст води в бітумі, W = 2…5%; t1 і t2 — для сховища t1 = 10єС; t2 = 60єС;
для приймача t1 = 60єС; t2 = 90єС.
Битумоплавильные агрегати призначені для плавлення, зневоднення і нагріву бітуму до робочої температури. Розігрів бітуму в битумохранилище виробляється у два этапа:
I етап: Розігрів бітуму донними нагревателями, вимощеними дно якої сховища до температури плинності (60єС), дно має ухил, бітум стікає в приямок у якому встановлено змеевик.
II етап: Розігрів бітуму в приямку до температури 90єС. Нагрітий бітум з допомогою насоса перекачується трубопроводами в битумоплавильные котлы.
5.3. Розрахунок електричної системи подогрева.
Споживана потужність Р, кВт:
У кожному блоці по шість нагрівачів. Потужність одного блоку: де n — кількість блоків нагрівачів, n = 3…4 шт.
Приймаємо матеріал у спіралі нагрівача полосовую сталь з ?=0,12?10;
6 Ом? м. Перетин спіралі S=10?10−6 м2.
Потужність фази, кВт:
Опір фази, Ом:
де U=380 В.
Довжина спіралі, м:
Розмір струму, А:
Щільність струму, А/мм2:
6. Визначення кількості битумоплавильных установок.
1 Годинна продуктивність казана ПК, м3/ч.
де n — кількість змін; kВ — 0,75…0,8;
VК — геометрична ємність казана для обраного типу агрегату, м3; kН — коефіцієнт наповнення казана, kН=0,75…0,8; tЗ — час заповнення казана, мин:
де ПН — продуктивність насоса (див. таблицю 3).
Таблиця 3. Тип насоса та її характеристики. |Тип насоса|Марка |Производит|Давление, |Потужність |Діаметр | | |насоса |ельность, |кгс/см2 |двигуна, |патрубків, мм| | | |л/мин. | |кВт | | |передвижно|ДС-55−1 |550 |6 |10 |100/75 | |і | | | | | |.
tН=270 хв — час випарювання і нагрівання бітуму до робочої температури; tВ — час вивантаження бітуму, мин:
де? — об'ємна маса бітуму, ?=1т/м3;
Q — годинна продуктивність змішувача, т/ч;
? — відсотковий вміст бітуму в смеси.
2 Розрахунок кількості котлов.
де ПБ — добова потреба у бітумі, т/добу; kП — коефіцієнт нерівномірності споживання бітуму, kП=1,2.
Вибираємо тип агрегата:
Таблиця 4. Тип агрегату та її характеристики. |Тип |Робочий |Встановлена мощность,|Расход |Виробляй| |агрегата|объем, л |кВт |палива, |-тельност| | | | |кг/ч |и, т/ч | | | |э/дв. |э/нагр. | | | |ДС-91 |30 000?3 |35,9 |90 |102,5 |16,5 |.
Розрахунок складу і устаткування подачі мінерального порошка.
Для подачі мінерального порошку використовують два виду подачі: механічну і пневмотранспортную. Для механічної подачі мінерального порошку до видаткової ємності застосовують шнеко-элеваторную подачу.
Застосування пневмотранспорта дозволяє приймати значно більшу продуктивності праці, схоронність матеріалу, дає можливість подавати мінеральний порошок, як за горизонталлю, і по вертикали.
Недолік — велика енергоємність. Пневматичне транспортування залежить від безпосередній вплив стиснутого повітря на переміщуваний матеріал. По способу роботи пневмотранспортное устаткування ділиться на всасывающее, нагнетательное і всасывающенагнетательное. У випадку пневмотранспортная установка включає компресор з оліюі влагоотделителем, воздухопроводы, контрольновимірювальні прилади, завантажувальні устрою які подають матеріал щодо встановлення, розвантажувальні пристрої і системи фільтрів. Для транспортування мінерального порошку пневмоспособом використовують пневмовинтовые і пневмокамерные насоси. Пневмовинтовые насоси використовують із транспортування мінерального порошку на відстань до.
400 м. Недолік — низький термін їхньої служби швидкохідних напірних шнеков.
Камерні насоси переміщають мінеральний порошок на відстань до 1000 м.
Можуть застосовуватися у поєднанні з силосними складами. Включають у собі кілька герметично закритих камер, у верхній частині якої є загрузочное отвір з побудовою щодо його герметизації. До складу лінії подачі входить склад, устаткування, що забезпечує переміщення мінерального порошку складу до видаткової ємності і видаткова емкость.
1 Розрахунок місткості силосу в склад.
Рекомендується зберігати мінеральний порошок в складах силосного типу із метою запобігання додаткового зволоження, що призводить до комкованию та зниження його якості, і навіть до скруті транспортування. Потрібна сумарна місткість силосів складу SVс, м3 становить: де GП — маса мінерального порошка;
?П — щільність мінерального порошку, ?П=1,8 т/м3; kП — коефіцієнт обліку геометричній ємності, kП=1,1…1,15.
Кількість силосів вираховується за формулою: де VC — місткість одного силосу, м3; V=20, 30, 60, 120.
2 Розрахунок пневмотранспортной системы.
Для транспортування мінерального порошку до видаткової ємності приймається механічна чи пневматична система.
Для транспортування мінерального порошку можна використовувати пневмовинтовые чи пневмокамерные насоси. Подача в пневмотранспортную установку стиснутого повітря здійснюється компресором. Потрібна продуктивність компресора QК, м3/мин, составляет:
де QВ — витрата, необхідний забезпечення необхідної продуктивності пневмосистемы, м3/мин.
де QМ — продуктивність пневмосистемы, QМ = 0,21?QЧ = 0,21?34,6.
= 7,3, т/ч, QЧ — годинна продуктивність АБЗ;
µ — коефіцієнт концентрації мінерального порошку, µ=20…50;
?У — щільність повітря рівна 1,2 кг/м3.
Потужність на привід компресора NК, кВт:
де ?=0,8 — ККД привода;
Р0 — початкова тиск повітря, Р0=1 атм;
РК — тиск, яке має компресор, атм.
де ?=1,15…1,25;
РВ=0,3 атм;
РР=НПОЛ+1 — робочий тиск в смесительной камері подає агрегату, атм, НПОЛ — повне опір пневмотранспортной системи, атм;
де НП — дорожні втрати тиску в атм;
НПОД — втрати тиску підйом, атм;
НВХ — втрати тиску введення мінерального порошку в трубопровід, атм. Колійні втрати давления:
де k — досвідчений коефіцієнт сопротивления:
де vВ — швидкість повітря залежить від µ; при µ=20…50 відповідно vВ=12…20 м/с; dТР — діаметр трубопроводу, м:
? — коефіцієнт тертя чистого повітря про стінки трубы:
де? — коефіцієнт кинематической в’язкості повітря, м2/с, ?=14,9?10;
6.
LПР — наведена довжина трубопроводів, м:
де SlГ — сума довжин горизонтальних ділянок пневмотрассы, м,.
SlГ=3+3+4+4+20+20=54;
SlПОВ — довжина, еквівалентна сумі поворотів (колін), м,.
SlПОВ=8?4=32 (кожне коліно приймаємо рівним 8 м);
SlКР — довжина, еквівалентна сумі кранів, перемикачів. До кожного крана приймають 8 м, SlКР=8?2=16;
Втрати тиску подъем:
де ??У — 1,8 кг/м3 — середня щільність повітря на вертикальному ділянці; h — висота підйому матеріалу, м. Приймається 12…15 м, залежно від типу асфальто-смесительной установки.
Втрати тиску при введення мінерального порошку в трубопровод:
де? — коефіцієнт, залежить від типу завантажувального устрою. Для гвинтових насосів слід сприймати? = 1, для пневмокамерных? = 2; vВХ — швидкість повітря при введення мінерального порошку в трубопровід, м/с:
?ВХ — щільність повітря при введення мінерального порошку, кг/м3:
Тогда:
За формулою (29) знаходимо NК:
З проведеного розрахунку виробляється добір подає агрегату по табл. 11 [4].
Таблиця 5. Тип подає агрегату та її характеристики. |Тип і |Производи|Дальность |Витрата |Діаметр |Установленн| |марка |-тельност|транспортирования,|сжатого |трубопровод|ая | |насоса|ь, м3/ч |м |повітря |а, мм |потужність, | | | | | | |кВт | | | |по |по | | | | | | |горизонт|вертикал| | | | | | |алі |і | | | | |К-2305|10 |200 |35 |22 |100 | |.
Розрахунок механічної системи подачі мінерального порошка.
Механічна система представленій у вигляді шнеко-элеваторной подачи.
Подаючий агрегат — шнек.
Продуктивність шнека QШ, т/ч становить: де? — коефіцієнт заповнення перерізу жолоба, ?=0,3;
?М — щільність мінерального порошку в насипному вигляді, ?М=1,1 т/м3;
DШ — діаметр шнека, приймаємо 0,2 м; t — крок гвинта, t=0,5DШ=0,1 м; n — частота обертання шнека, об./хв ;
kН — коефіцієнт, враховує кут нахилу конвеєра, kН=1.
Потужність приводу шнека N, кВт визначається по формуле:
де L —довжина шнека, м L=4 м;
? — коефіцієнт, що характеризує абразивность матеріалу, для мінерального порошку приймається ?=3,2; k3 — коефіцієнт, що характеризує трансмісію, k3=0,15;
VМ=t?n/60= 0,1 — швидкість переміщення матеріалу, м/с;
?У — коефіцієнт тертя, який приймає для підшипників качения рівним 0,08; qМ=80?DШ=16 кг/м — погонная маса винта.
Продуктивність елеватора QЭ, т/ч визначається з выражения:
де і — місткість ковша, становить 1,3 л;
? — коефіцієнт наповнення ковшів матеріалом, ?=0,8; t — крок ковшів, м (0,16; 0,2; 0,25; 0,3; 0,4; 0,5; 0,6; 0,63); vП=1,0 м/с — швидкість підйому ковшей.
Необхідна потужність приводу элеватора:
де h — висота підйому матеріалу, м, приймається 14 м; kК — коефіцієнт, враховує масу рухомих елементів, kК=0,6;
А=1,1 — коефіцієнт, враховує форму ковша;
С=0,65 — коефіцієнт, враховує втрати на зачерпывание.
Таблиця 6. Тип елеватора, і його характеристики. |Тип |Ширина |Вместимост|Шаг |Скорост|Шаг |Мощность|Произво-| |элевато|ковша, |и ковша, л|ковшей,|ь цепи,|цепи, |, кВт |дительно| |ра |мм | |мм |м/с |мм | |сть м3/ч| |ЭЦГ-200|200 |2 |300 |0,8…1,2|100 |2,0 |12…18 | | | | | |5 | | | |.
8. Розрахунок потреби в електричної енергії і воде.
1 Розрахунок потрібного кількості электроэнергии.
Потрібне кількість електроенергії NЭ, кВт определяется:
де kС — коефіцієнт, враховує втрати потужності, kС=1,25…1,60;
SРС — сумарна потужність силових установок, кВт;
SРВ — те, внутрішнього висвітлення, кВт,.
SРВ=5?269,89+15?318+9?132+20?72=8,75;
SРН — те, зовнішнього висвітлення, кВт,.
SРН=1?644+3?837+5?50=3,41;
Примітка: добові норми витрат електроенергії на 1 м² беремо по табл. 12 методичних вказівок. cos?=0,75.
2 Визначення загального витрати воды.
Загальний витрата води визначається за такою формулою, м3: де КУ=1,2;
КТ=1,1…1,6;
ВП — витрата води на виробничі потреби, м3/ч, ВП=10…30;
СБ — витрата води на побутові потреби, споживання, м3/ч, ВБ=0,15…0,45.
8.3. Визначення витрати води На оновлення запасу в пожежному резервуарі, ЧПСШ, м3/ч.
Витрата ЧПСШ визначаємо по формуле:
де qПОЖ=5…10 л/с;
Т — час заповнення резервуара, Т=24 ч.
8.4. Визначення діаметра труби водогінної мережі, dТР, м.
де V — швидкість руху води, V=1,0…1,5 м/с.
Приймаємо діаметр труби водогінної мережі рівний 0,10 м.
9. Технологічна схема приготування модифікованого битума.
Сама схема наводиться наприкінці РПЗ. Модифікований бітум — органічне в’язке, отримане шляхом змішування бітуму з сипучим модифікатором і олією. Його приготавливаю для одержання органічного в’язальника з найбільш найкращими характеристиками (міцність, морозостійкість, пластичність та інших.) проти звичайним битумом.
Призначення олії — понизити еластичність бітуму, що підвищило б його опір впливу негативних температур. Самий модифікатор підвищує прочностные характеристики бітуму та її сдвигоустойчивость.
У технологічну схему приготування модифікованого бітуму входять такі елементи, як ємності для зберігання матеріалів (олії, бітуму); ємність для зберігання готового модифікованого бітуму; дозатор олії; чотири насоса; стрічковий конвеєр; диспергатор; дозатор.
Олія з ємності подається в дозатор з допомогою насоса. З дозатора олію вступає у диспергатор. До неї ж по ленточному конвеєра подається сипкий модифікатор і з ємності бітум. Щоб усе це якісно перемішати, необхідно затратити 6−8 годин. Тож прискорення процесу перемішування в технологічну схему включений дезінтегратор. З допомогою насоса з диспергатора в дезінтегратор подається суміш бітуму з олією і сипучим модифікатором. Потім ця суміш, пройшла обробку в дезинтеграторе, знову подається в диспергатор, де знову піддається перемішуванню. І цей цикл повторюється протягом години, після чого ж ми отримуємо модифікований бітум. Його можемо по битумопроводам подавати на розлив в битумовозы, а за її відсутність емкость.
1. Проектування виробничих підприємств будівництва: уч. посібник для вузів: Вищу школу, 1975. -351 с.
2. Асфальтобетонные і цементобетонні заводи: Довідник/ У. И.
Колышев, П. П. Костін. — М.: Транспорт, 1982. -207 с.
3. Вейцман М. І., Соловйов Б. М. Бітумні бази й цехи. — М.:
Транспорт, 1977. -104 с.
4. Проектування АБЗ: Методичні вказівки/ М. Аннабердиев. -.
Ростов-на-Дону, 1972. -17 с.
———————————- [pic].
[pic].
[pic].
[pic].
[pic].
[pic].
[pic].
[pic].
[pic].
[pic].
[pic].
[pic].
[pic].
[pic].
[pic].
[pic].
[pic].
[pic].
H.
R.
L.
[pic].
[pic].
[pic].
[pic].
[pic].
[pic].
[pic].
[pic].
[pic].
[pic].
[pic].
[pic].
[pic].
[pic].
[pic].
[pic].
[pic].
[pic].
8AC=>: 2. !E5:0.
Малюнок 2. Схема блока.
Рисунок 1. Розміри склада.
[pic].
[pic].
[pic].
[pic].
[pic].
[pic].
[pic].
[pic].
[pic].
[pic].
[pic].
[pic].
[pic].
[pic].
[pic].
[pic].
[pic].
[pic].
[pic].
[pic].
[pic].
[pic].
[pic].
[pic].
[pic].
[pic].
[pic].
[pic].
[pic].
[pic].
[pic].
[pic].
[pic].
[pic].
[pic].
[pic].
[pic].
[pic].
[pic].
[pic].
[pic].
[pic].
[pic].
[pic].
[pic].
[pic].
[pic].
[pic].
12,100.
14,000.
10,000.
4,800.
0,000.
1,500.
— 2,000.
L.
1. Силос 2. Донний выгружатель 3. Нижній свердло 4,5 Реверсивний привід 6. Элеватор
7. Верхній шнек;
8. Видаткову емкость.
Схема 1. Схема подачі мінерального порошку шнеком і элеватором.
[pic].
[pic].
[pic].
[pic].
[pic].
[pic].
[pic].
[pic].
[pic].
олію силиконовое.
Д.
ДСТ.
1. Робоча емкость;
2. Видаткову емкость;
3. Электронагреватель;
4. Дезинтегратор;
5. Лопатеві мешалки;
6. Гвинтовій конвейер;
7. Насос;
8. Вентилятор.
Схема 2. Приготування модифікованого битума.
[pic].
[pic].
[pic].
[pic].
[pic].
[pic].
111 774 РПЗ.
Лист.
111 774 РПЗ.
Лист.
———————————;
111 774 РПЗ.
Лист.