Технологія обладнання зварювання
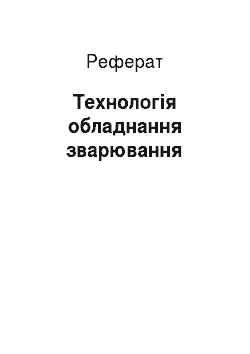
Газову зварювання застосовують під час виготовлення і ремонті виробів із тонколистовий стали; при ремонтної зварюванні литих виробів із чавуну, бронзи, алюмінієвих сплавів; при монтажній зварюванні стиків трубопроводів малих та середніх діаметрів (до 100 мм) з товщиною стінки до 5 мм фасонных частин до ним; під час зварювання вузлів конструкцій з тонкостінних труб; під час зварювання виробів… Читати ще >
Технологія обладнання зварювання (реферат, курсова, диплом, контрольна)
смотреть на реферати схожі на «Технологія устаткування зварювання «.
Російський державний професійно педагогічний университет.
Контрольна работа.
По предмета: «Технологія й устаткування сварки».
Варіант 9.
Виконав студент грн. ЗСМ 411.
Соколов М. В.
Перевірив Преподаватель.
_________________.
Екатеринбург.
1.Описать конструкцію і принцип действия.
універсальних газових горелок.
(із зазначенням марки і технічних характеристик) для.
зварювання, різання і підігріву металів. 3.
2. Створити вибір технології газової сварки.
легованої стали З0ХГСА. При рассмотрении.
цього питання виявити зв’язок обраного режима.
(попереднього, супутнього і последующего.
підігріву) з складом стали, структурными.
змінами у металі шва і зоні термического.
впливу. Результати оформити як таблиць. 9.
3. Умови й підвищити вимоги до разрезаемому металу, що визначають можливість перебігу процесу резки.
Розрахувати витрата ріжучого кисню при ручний кисневою краянні стали завтовшки 50−100мм і 500 мм. 13.
4. Список літератури 16.
1.Описать конструкцію і принцип дії універсальних газових горілок (з зазначенням марки і технічних характеристик) для зварювання, різання і підігріву металлов.
Горілка — цей прилад, призначене щоб одержати полум’я необхідної теплової потужності, ж розмірів та форми. Усі існуючі конструкції газо-плазменных горілок можна класифікувати наступним образом:
1) за способом подачі пального газу смесительную камеру — інжекторні і безынжекторные;
2) за проектною потужністю полум’я — мікро потужності (10—60 дм3/ч ацетилену); малої потужності (25—400 дм3/ч ацетилену); середньої потужності (50—2800 дм3/ч ацетилену) і великої потужності (2800— 7000 дм3/ч ацетилена);
3) за призначенням — універсальні (зварювання, різка, пайка, наплавлення, підігрів); спеціалізовані (лише зварювання або тільки підігрів, закалочные і пр.);
4) за кількістю робочих пламен — одноплемінні і многопламенные;
5) за способом застосування — для ручних способів газопламенной обробки; для механізованих процессов.
Інжекторні пальники. Кисень через ніпель / инжекторной пальники відбувається під надлишковим тиском 0,1—0,4 МПа (1 — 4 кгс/см2) і з великою швидкістю виходить із центрального каналу інжектора 8 (рис. 1). У цьому струмінь кисню створює розрідження в ацетиленових каналах рукоятки 3, за рахунок якого ацетилен подсасывается (інжектується) в смесительную камеру 10, звідки яка утворювалася пальна суміш направляють у мундшук 13 і виході згоряє. Інжекторні пальники нормально працюють при надмірному тиску що надходить ацетилену 0,001 МПа (0,01 кгс/см2) і выше.
Підвищення тиску пального газу перед горілкою полегшує роботу інжектора і покращує регулювання полум’я, хоча за умовах доводиться прикривати вентиль пального газу на горілці, що може спричинити до виникненню ударів і зворотних ударів полум’я. Тому, за використанні инжекторных горілок рекомендується підтримувати їх тиск ацетилену (під час роботи від балона) не більше 0,02—0,05 МПа (0,2—0,5 кгс/см2).
Рис. 1. Инжекторная горелка:
[pic].
1 — кисневий ніпель; 2 — ацетиленовий ніпель; 3 — рукоятка; 4 — киснева трубка; 5 — вентиль для кисню; 6 — корпус; 7 — вентиль для ацетилену; 8 — інжектор; 9 — накидная гайка; 10 — смесительная камера; 11 — наконечник; 12 — з'єднувальний ніпель; 13 — мундштук.
Інжекторні пальники розраховують в такий спосіб, що вони забезпечували певний запас ацетилену, т. е. за повної відкритті ацетиленового вентиля пальники витрата ацетилену збільшувався би за порівнянню з паспортним для инжекторных горілок — щонайменше ніж 15%; для инжекторных резаков — не менш як на 10% максимального паспортного витрати ацетилена.
На рис. 2 показані за приклад конструкції инжекторных горілок середньої потужності ГС-3 й малої потужності ГС-2 для зварювання металів. Пальники постачають набором змінних наконечників, різняться витратою газу та предназначаемых для зварювання металів різною товщини. Номер необхідного наконечника вибирають відповідно до необхідної теплової потужністю полум’я, що у дм3/ч ацетилену. До ручці пальники ГС-3 можна приєднувати і інші наконечники, наприклад многопламенные для підігріву, для пайки, вставні різаки для різання металла.
Рис. 2. Зовнішній вигляд і розріз горелок.
[pic] а) — типу ГС-3; б) — типу ГС-2; 1 — трубка наконечника; 2 — смесительная камера; 3 і п’яти — ущільнювальні кільця з олію термостойкой гуми; 5 — маховичок; 6 — кульковий клапан; 7 — пластмасова рукоятка; 8 — ацетиленовий ніпель; 9 — корпус; 10 — инжектор;
11 — накидная гайка; 12 — мундштук.
Для зварювання і наплавки металів великий товщини, нагріву та інших праць, потребують полум’я великої потужності, використовують інжекторні пальники ГС-4 з наконечниками № 8 і 9-те: № наконечника 8 9.
Витрата газів, дм3/ч: ацетилену… 2800—4500 4500—7000 кисню… 3100—5000 5000—8000.
Товщина свариваемой стали, мм… 30—50 50—100.
У наконечниках ГС-4 інжектор і смесительная камера встановлено безпосередньо перед мундштуком. Горючий газ подається в інжектор по трубці, розташованої всередині трубки подачі кисню. Цим попереджується нагрівання пального газу та суміші відбитій теплотою полум’я, що знижує ймовірність зворотних ударів полум’я і ударів під час використання полум’я великої потужності. Горілка ГС-4 може працювати на пропан бутане, навіщо оснащена двома наконечниками з сетчатыми мундштуками, розрахованими на витрати: № 8 — пропан бутану 1,7—2,7, кисню 6—9,5 м3/ч; № 9 — пропан бутану 2,7—4,2, кисню 9,5— 14,7 м3/ч.
Рис. 3. Наконечник з подогревателем для зварювання на пропан бутане.
[pic].
1 — мундштук; 2 — подогревающая камера; 3 — підігрівник; 4 — сопла подогревателя; 5 — трубка займистою суміші; 6 — які підігрівають пламена.
Мундштуки горілок малої потужності або мають водне охолодження виготовляють з латуні ЛС59−1. У пальниках середньої потужності мундштуки для кращого відводу теплоти виготовляють з міді МОЗ чи хромистой бронзи Бр Х0,5, до котрої я негаразд чіпляються бризки розплавленого металу. Для отримання полум’я правильної форми та сталого його горіння вихідний канал ні мати заусенцев, вм’ятин та інших дефектів, а внутрішня поверхню каналу повинна бути суто оброблена. Зовні мундштук рекомендується полировать.
Пальники для газів замінників від ацетиленових тим, що обладнані пристроєм для додаткового підігріву і перемішування газової суміші до виходу їх із каналу мундштука. Серійно випущені пальники ГЗУ-2−62 і ГЗМ-2−62М при цьому мають підігрівник і подогревательную камеру, розташовані на наконечниках між трубкою підвода займистою суміші і мундштуком (рис. 3). Частина потоку суміші (5—10%) виходить через додаткові сопла подогревателя і згоряє, створюючи смолоскипи, які підігрівають камеру з коррозионно-стойкой стали. Температура суміші виході з мундштука підвищується на 300—350° З повагою та відповідно зростає швидкість згоряння температура основного зварювального полум’я. Пальники можуть працювати на пропан-бутан-кислородной і метан-кислородной суміші; ними можна зварювати стали завтовшки до 5 мм (у випадках до 12 мм) з задовільними показниками продуктивністю і якістю зварювання. Наконечники цих горілок розраховані ми такі витрати газов:
№ наконечника 0 1 2 3.
Витрата, дм3/ч: пропан-бутану 15—40 30−70 70—140 140−240 кисню 50—140 105—260 260—540 520−840.
№ наконечника 4 5 6 7.
Витрата, дм3/ч: пропан-бутану 240—400 400—650 650—1050 1650—1700 кисню… 840—1400 1350—2200 2200—3600 3500—5800.
При перекладі пропан-бутан горілок, розрахованих до роботи на ацетилене, слід брати наконечник, на два номери більший, і ввертати в нього мундштук, однією номер більший, а інжектор — однією номер менший, аніж за зварюванні металу тієї ж товщини на ацетиленокислородной смеси.
Спеціальні наконечники. Для зварювання у важких умовах нагріву, наприклад великих чавунних виливків з підігрівом, застосовують спеціальні теплоустойчивые наконечники НАТ-5−6 і НАТ-5−7. У цих наконечниках мундштук і трубка обладнані теплоизоляционной прошарком з азбесту, розлученого на воді чи рідкому склі, і вкриті згори кожухом зі сталі Х25Т. Вони можуть довго працювати без ударів і зворотних ударів. Для цих робіт використовують також звичайні наконечники, забезпечені додаткової трубкою для підвода охолодного воздуха.
Безынжекторные пальники. На відміну від инжекторных у цих пальниках зберігається постійний склад суміші протягом усього часу роботи пальники, незалежно від неї нагріву відбитій теплотою полум’я. У, инжекторных ж пальниках нагрівання мундштука і смесительной камери погіршує инжектирующее дію струменя кисню, унаслідок чого надходження ацетилену зменшується і суміш збагачується киснем. Це спричиняє оплескам і зворотним ударам полум’я, — доводиться переривати зварювання і охолоджувати наконечник.
Безынжекторные пальники, у яких ацетилен і кисень вступають у змішувальне пристрій під рівними давлениями, при нагріванні не змінюють складу суміші, оскільки за нагріванні мундштука як і зменшується надходження газів у горілку, воно однаково як кисню, так ацетилену. Отже, відносне їх в суміші, т. е. склад суміші, постійний. На рис. 4, а показано схема безынжекторной пальники, на рис. 4, б — схема устрою для харчування безынжекторной пальники ГАР (рівного давления).кислородом і ацетиленом через постовий беспружинный регулятор ДКР (див. рис. 23). Горілка ГАР комплектується сім'ю наконечниками на витрати ацетилену 50—2800 дм3/ч. Кожен наконечник має смесительную камеру з цими двома калиброванными отворами: центральним для кисню і бічним для ацетилена.
Рис 4. Безынжекторная горелка.
[pic].
1 — мундштук; 2 — трубка наконечника; 3 — вентиль кисню; 4 — ніпель кисню; 5 — ніпель ацетилену; 6 — вентиль ацетилену; 7 — редуктор кисневий; 8 — редуктор ацетиленовий; 9 — регулятор ДКР; 10 — шланги; 11 — горілка ГАР.
Камерно-вихревые пальники. Для деяких процесів газопламенной обробки — нагріву, пайки, зварювання пластмас тощо. п. непотрібен високої температури ацетиленокислородного полум’я. Для цих процесів можна використовувати камерно-вихревые пальники, працівники пропано-воздушной суміші. У цих пальниках замість мундштука є камера згоряння, у якому надходять пропан й повітря під тиском 0,05—0,2 МПа (0,5—2 кгс/см2). Пропан подається до камери через центральний канал, а повітря, викликає також вихреобразование, надходить по многозаходной спіралі, які забезпечують «закручення» газової суміші в камері згоряння. Продукти згоряння виходять крізь концевое сопло камери згоряння із швидкістю, створюючи полум’я досить високої температури (1500—1600° З). Пальники дають змогу одержувати полум’я з температурою 350—1700° С.
Пальники спеціальні. До таких горілкам ставляться, наприклад, многопламенные очищення металу від іржі та фарби; газо-воздушные для пайки і нагріву, працівники ацетилене газах замінниках; керосино кисневі для распыленного рідкого пального; многопламенные кільцеві для газопрессовой зварювання; для поверхневою гарту; для полум’яною наплавки; для зварювання термопластов і з другие.
Принципи пристрої і конструкції їх багато в чому аналогічні що використовуються для зварювальних горілок. Відмінність складається переважно; в теплової потужності і розмірах полум’я чи суми пламен (при многопламенных пальниках), і навіть розмірах і втрачає формі мундштука. 2. Створити вибір технології газової зварювання легованої стали З0ХГСА. Зблизька цього питання виявити зв’язок обраного режиму (попереднього, супутнього і наступного підігріву) з складом стали, структурними змінами у металі шва і зоні термічного впливу. Результати оформити як таблицы.
Газова зварювання характеризується високими значеннями введеної в виріб удільної енергії ?і сягаючими величин порядку 200—400 Дж/мм2, більшої зоною теплового впливу, меншою продуктивністю, ніж дуговая сварка.
Газову зварювання застосовують під час виготовлення і ремонті виробів із тонколистовий стали; при ремонтної зварюванні литих виробів із чавуну, бронзи, алюмінієвих сплавів; при монтажній зварюванні стиків трубопроводів малих та середніх діаметрів (до 100 мм) з товщиною стінки до 5 мм фасонных частин до ним; під час зварювання вузлів конструкцій з тонкостінних труб; під час зварювання виробів з алюмінію та її сплавів, міді, латуні і свинцю; при наплавленні латуні і бронзи на деталі із сталі й чавуну; при наплавленні твердих і зносостійких сплавів, і навіть під час зварювання ковкого і високоміцного чавуну із застосуванням прутків з латуні і бронзы.
Газової зварюванням можна зварювати майже всі метали, використовувані в техніці. Чугун, мідь, латунь, свинець легше піддаються газової зварюванні, ніж дугового. Простота устаткування, незалежність джерела енергопостачання, можливість широкого регулювання швидкості нагріву і охолодження металу під час зварювання дозволяють застосовувати той процес при ремонтних і монтажних роботах. Сталь завтовшки понад 6 мм газової зварюванням з'єднують редко.
Таблиця 1.
Вплив домішок на властивості металу шва і майже шовной зоны.
|Наимено|В каком|Взаимод|Дефекты|Причины|Допусти|Максима|Характе|Свари| |вание, |вигляді |ействие|сварной|образов|мость |льно |рные |ваемо| |химичес|находит|с |констру|ания |(желате|допусти|свойств|сть | |київ |ся |кислоро|кции |тріщин |льону |моє |а |метав| |символ |примесь|дом | | |нежела|содержа|основно|ла | |примеси|в |металу| | |тельна)|ние |го | | | |металле|сварочн| | |присутс|примеси|металла| | | | |ой | | |твия |в % |при | | | | |ванни, | | |домішки| |наявності| | | | |шлаку, | | |в | |даної | | | | |газу | | | | |домішки| | |1 |2 |3 |4 |5 |6 |7 |8 |9 | |30ХГСА |75−100 |Св-08 | | | | | | | | | |Св-08А | | | | | | | | | |Св-18ХГ| | | | | | | | | |СА | | | | | | | | | |Св-18ХМ| | | | | | | | | |А | | | | | | | 3. Умови й підвищити вимоги до разрезаемому металу, що визначають можливість перебігу процесу різання. Розрахувати витрата ріжучого кисню при ручний кисневою краянні стали завтовшки 50−100мм і 500 мм.
Подвергаемый газової краянні метал повинен відповідати ряду певних умов (требований).
Температура плавлення металу повинна перевищувати температури запалення їх у кисні (температури початку інтенсивного окислення металу). Інакше метал під впливом подогревающего полум’я різака буде плавитися і примусово віддалятися кисневою струменем без необхідного окислення, що характеризує процес газової різання. За цих умовах шлак не утворюється, і расплавляемый метал, важко удаляемый кисневою струменем, буде утворювати на крайках реза напливи. У цьому продуктивність процесу вкрай низька, рез великий ширини і виключно неровный.
Низкоуглеродистая сталь цій умові задовольняє. Температура її плавлення становить ~ 1500° З, а температура запалення в кисні 1350—1360° З. Проте якщо з підвищенням змісту вуглецю в стали здатність її піддаватися газової краянні падає (оскільки температура плавки сталі знижується, а температура запалення в кисні зростає). З іншого боку, в які виникають при краянні шлаках зростає кількість не окисленого заліза, сильно затрудняющего процес різання через освіти ґрата (сплаву шлаку з металом), важко відокремлюваного від крайок реза. Тим паче не піддається газової краянні чавун, зміст вуглецю у якому становить більше однієї, 7%.
Температура плавлення металу повинна перевищувати температури плавлення утворених у процесі різання окислов.
Низкоуглеродистая сталь утворює три окисла заліза: FeO з температурою плавлення 1270° З, Fe3O4 з температурою плавлення 1538 °C і Fe2. O3 з температурою плавлення 1562 °C. Допускаючи, що неї ці окисли заліза є у шлаку, температура плавлення що його середньому нижчий 1500° З, вважатимуться, що низкоуглеродистая сталь задовольняє і до цього умові, тим паче, що у поверхні її за нагріванні не утворюється плівки тугоплавких окислів, що перешкоджають контакту кисневою струменя з металом. Проте низку металів і сплавів, наприклад алюміній, магній, сплави цих металів, і навіть высоколегированные стали, містять високий відсоток хрому, цій умові різання не задовольняють. При нагріванні цих сплавів у процесі різання з їхньої поверхні утворюється плівка тугоплавкого окисла, ізолююча метал від контакту з кислородом.
Тепловий ефект освіти окисла металу має бути досить високим. Це умова диктується тим, що з краянні стали, подогревающее полум’я різака повідомляє металу порівняно не велику частина теплоти — близько 5—30% її загальної кількості, який виділяється у процесі різання. Основне ж кількість теплоти (70—95%) виділяється при окислюванні металла.
Низкоуглеродистая сталь утворює при краянні три окисла заліза, які виділяють при нашій освіті у середньому близько 627 — 666, 8 кДж/моль (150—160 ккал/г-мол). Цього кількості теплоти вистачає, для перебігу ефективного процесу газової різання стали.
Інша працювати з різкій міді її сплавів. Крім високої тепло продуктивності міді, сильно затрудняющей початок процесу різання, головною причиною, що робить газову різання міді неможливою, є низька тепловиділення при окислюванні, оскільки за освіті СиО виділяється теплоти всього 156, 8 кДж/моль (37, 5 ккал/г-мол), а при освіті Си2О 169, 7 кДж/моль (40, 6 ккал/г-мол). Цього кількості теплоти спершу і підтримки процесу різання міді недостатньо, у зв’язку з ніж процес газової різання цього металу невозможен.
Консистенція які виникають окислів Має бути рідкої, т. е. з’являються при краянні шлаки мали бути зацікавленими жидкотекучими. Це умова добре виконується при краянні низькоі среднеуглеродистой стали, низьколегованої сталі та титанових сплавов.
Газова різка сплавів, містять великий відсоток кремнію плі хрому сильно утруднена чи неможлива. Приміром, неможлива різка сірого чавуну, що містить великий відсоток кремнію (до 3,5—4,5%), окис якого (SiO2) сильно підвищує вязкость.
Теплопровідність металу мусить бути можливо низькою. У протилежному разі буває важко, котрий іноді неможливо (за високої масі высокотеплопроводного металу) досягти концентрованого нагріву металла.
Низкоуглеродистая сталь, теплопровідність якої невелика {коефіцієнт теплопровідності? = 0,63 Дж/(см. сК) [?, = 0,12 кал/(см. -з-° З]}, не викликає труднощів ні з початковий момент, ні з процесі різання. У цьому вся разі підігрів металу у початковій точці реза до запалення здійснюється швидко, без помітного відводу теплоти в масу разрезаемого металла.
Що ж до початкового підігріву до запалення таких металів, як мідь і алюміній, то тут для цих металів через високе теплопровідності початковий підігрів пов’язані з великими труднощами в більшості випадків стає можливим лише після попереднього підігріву разрезаемых аркушів чи заготовок до досить високої температури (міді до 700—800° З, алюмінію до 300—500° З). Висока теплопровідність міді алюмінію — одне з причин, утрудняють і унеможливлюють газову різання цих металлов.
Аналізуючи наведені вище умови газової різання, можна констатувати, що всього цього умовам добре задовольняє чисте залізо і низкоуглеродистая сталь. З підвищенням змісту вуглецю в стали здатність її піддаватися газової краянні падає.
Список литературы
.
1. А. І. Акулов, Р. А. Бельчук, У. П. Демянцевич «Технологія й устаткування зварювання плавлением».
2. Р. Б. Євсєєв, Д. Л. Глизманенко «Обладнання ГЕС і технологія газопламенной обробки металів і неметалевих материалов».
3. Р. Л. Петров «Зварювальні материалы».