Производство анодної массы
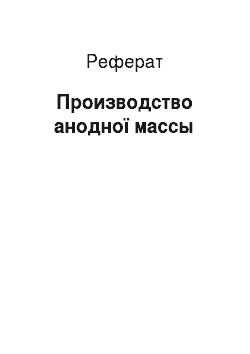
Завантаження матеріалу виробляється через завантажувальну вирву 9. Для нормального процесу роздрібнення потрібно певна сила тертя між шматками матеріалу і поверхнею валків, під впливом якої шматки затягуються у робочий простір між валками. Щоб якось забезпечити це основна умова, діаметр валків вибирають залежно від крупности матеріалу та її властивостей (вологості, характеру поверхні і є ін.) Для… Читати ще >
Производство анодної массы (реферат, курсова, диплом, контрольна)
Электроды у сенсі цього терміну називають провідники, службовці для підвода електричного струму до середовища, оскільки впливає. Ця середовище то, можливо водним розчином, розплавленим чи твердим раскалённым веществом.
Електроди можна виготовляти із різних токоподводящих матеріалів, наприклад заліза, міді, вугілля й др.
Однією з найбільшим споживачем електродів є алюмінієва промисловість. Електроди працює тут на досить жорстких експлуатаційних умовах (висока температура, агресивна середовище як розплавлених солей тощо.), тому вони мають задовольняти наступним основним вимогам:
1) витримувати високу температуру.
2) гарну електропровідність, малу пористість і достатню механічну прочность.
3) мати хорошою стійкістю проти окислення киснем повітря і разъедания різними хімічними веществами.
4) утримувати мінімум домішок.
5) мати правильну геометричну форму.
6) вистачити дешёвыми.
Найповніше наведеним вимогам відповідають електроди з вуглецевих материалов.
Сировину, що застосовується для вуглецевих изделий.
Для виробництва вуглецевих виробів застосовують сировину двох видов:
1) твёрдые углеродистые матеріали, що є основою (скелет) электрода.
2) сполучні углеродистые матеріали, які заповнюють проміжки між зёрнами вуглецевих матеріалів і з'єднують (цементують) ці зерна між собою при коксовании електрода у процесі обжига.
Основним елементом, що становить тверді і сполучні углеродистые матеріали, служить вуглець. Нині відомі лише дві аллотропические форми твердого вуглецю: алмаз і графіт. Так званий аморфний вуглець (вугілля, антрацит, кокс, сажа тощо.) є графіт мелкокристаллической структури. Під упливом високих температур кристали графіту укрупнюються. Найбільш різке і найбільш інтенсивне зміна розмірів кристалів графіту в вугіллі спостерігається при t вище 2000оС.
Технологічна схема виробництва анодною массы.
Дробление.
Для роздрібнення прожарених коксов застосовують високопродуктивні молотковые і валковые дробарки. Як допоміжного обладнання окремих випадках використовують щёковые дробилки.
Молотковые дробилки.
У цехах анодною маси молотковые дробарки застосовуються для попереднього роздрібнення коксу перед прокаткою, і навіть для роздрібнення прокаленного матеріалу. Процес роздрібнення там відбувається за принципом удару й часткового истирания матеріалу обертовими із швидкістю талями (молотками, билами). Загальна схема пристрої і принцип дії молотковій дробарки показаний малюнку 2.
Усередині міцного сталевого корпусу обертається на горизонтальному валу ротор з прикреплёнными щодо нього молотками. Вступники через загрузочное отвір шматки матеріалу розбиваються обертовими у бік їхнього руху молотками і роздробленими вивантажуються через щілини колосникової ґрати, помещённой під ротором.
За кількістю встановлених роторів молотковые дробарки поділяються на однороторные і двухроторные, за способом закріплення молотків — зі вільно закреплёнными і жорстко закреплёнными на роторе молотками. Залежно від конструкції розвантажувальною частини різняться дробарки з колосниковыми решётками і них, з цілком відкритою виходу дроблённого продуктом низом.
Конструкція однороторной многорядной дробарки показано малюнку 3. Основний частиною молотковій дробарки служить обертався ротор. Він з валу 11 з нерухомо укреплёнными ньому дисками 13 і 14. Диски мають отвори, якими пропущені стрижні 12. На стрижні вільно прикріплять молотки 1. Ротор заключён в сталевої корпус 10. Усередині стінки корпусу захищені в сталевої корпус 10. Внутрішні стінки корпусу захищені від зносу броньовими плитами. Під ротором розташована колосниковая ґрати 4, що складається з колосників трапецеидального сечения.
Руда вступає у дробарку через прямокутне отвір у верхній частині корпусу. Ударами молотків шматки руди дробляться і відкидаються на броньові плити. Дрібні шматки провалюються через зазори колосникової ґрати, причому більше великі додрабливаются у вузькому зазорі між молотками і колосникової гратами. Значимість цього зазору можна регулювати з допомогою спеціального приспособления.
Валковые (вальцевые) дробилки.
Здрібнення матеріалів валковых дробилках виробляється між двома обертовими назустріч одне одному валками шляхом розчавлювання і часткового истирания. Измельчаемый матеріал захоплюється силою тертя в щілину між валками і дробиться до величини зерна, відповідного ширині цієї щілини. Залежно від характеру поверхні робочих валиків розрізняють дробарки з гладенькими, зубцюватими і рифлёными валками. За принципом дії і конструктивного оформленню валковые дробарки найефективніші для середнього та малого роздрібнення (від 50 до 1 мм). Можливо, проте, застосування таких дробарок, особливо з зубцюватими валками, й у великого дробления.
На малюнку 4 показано двухвалковая дробарка з гладкою поверхнею валків. Для валка 1 і 2 однакового діаметра закріплені на обертових назустріч одне одному валах 3. Цапфы однієї з валів перебувають у нерухомих підшипниках 4, іншого — в рухливих підшипниках 5. Останні можуть переміщатися в горизонтальному напрямку допомогою натяжних болтів 6 і гайок 7. За рахунок переміщення підшипника 5 горизонтальної площині виробляється регулювання зазору між валиками. Підшипники 5 утримуються з допомогою пружин 8, які є запобіжним пристроєм. Потрапивши між валками не дробящегося матеріалу (металу, твердої породи) валок 2 відходить і величину щілини зростає до розміру, достатнього для проходження цієї предмета. Тим самим було охороняються від загартовування і поломки основні вузли дробилки.
Завантаження матеріалу виробляється через завантажувальну вирву 9. Для нормального процесу роздрібнення потрібно певна сила тертя між шматками матеріалу і поверхнею валків, під впливом якої шматки затягуються у робочий простір між валками. Щоб якось забезпечити це основна умова, діаметр валків вибирають залежно від крупности матеріалу та її властивостей (вологості, характеру поверхні і є ін.) Для коксов при гладких валках, зсунутих впритул до іншому, діаметр валків може бути приблизно 20 разів більше діаметра найбільших шматків, вступників на дробление.
Щёковые дробилки.
У щёковой дробарці матеріал раздавливается між двома щоками. По конструкції щік дробарки різняться з і з цими двома рухливими щоками; характером руху щоки — з простим рухом щодо осі її підвісу і з складним рухом. У разі кожна точка щоки описує замкнуту криву, оскільки рухлива щока кріпиться безпосередньо на эксцентриковый вал; в дробилках ж із простим рухом вона підвішена на окремої оси.
На малюнку 5 представлена дробарка з одного рухомий щокою та складних її рухом. Руда завантажується в дробарку згори у просторі між нерухомій 9 і рухомий 12 щоками і броньовими плитами 5. Рухлива щока підвішена на осі 6 і наводиться в рух (гойдається) з допомогою шатуна 3, насадженого головне (эксцентриковый) вал 1. Шатун соединён шарнірно з підвісної щокою 12 у вигляді распорных плит 4. Прихід головного валу здійснюється за допомогою шкивов.
При русі шатуна вгору рухлива щока наближається до нерухомій й відбувається розчавлювання матеріалу. При зворотному русі шатуна рухлива щока відступає від нерухомій і роздроблений матеріал під впливом власної ваги вивантажується з дробарки. До рухомий щоці шарнірно прикреплена потяг 10; з допомогою цієї тяги і пружини 11 рухлива щока відтягується від нерухомій під час руху шатуна вниз.
Загрузочное вікно дробарки називається зевом. Ширина й довжину зіва, виражені в міліметрах, характеризує розміри дробарки. Ширина випускний щоки дробарки регулюється зміною товщини прокладок, які закладаються між задньої стінкою рами 8 і спеціальним упором 7, який спирається права распорная плита.
Щоки дробарки піддаються сильному зносу, тому їх поверхню покривають съёмными бронеплитами з стійкої до истиранию марганцовистой стали. Для кращого розчавлювання руди поверхню броньових плит оснащена рифами, причому виступи на рухомий щоці розташовуються проти западин на неподвижной.
Кульові мельницы.
Для отримання тонких класів шихти (менш 0,074 мм) застосовуються кульові млини. Пилова фракція в млинах виходить шляхом истирания тонкого шару коксу між двома твёрдыми поверхнями, рухливими одна щодо інший і створюють тиск, достатні розколювання частинок материала.
Принцип роботи кульової млини барабанного типу ось у чому. Вихідний матеріал — подрешёточная фракція (відсів), отримувана після рассева на виброгрохоте — надходить у обертався барабан, заповнений на 35−40% обсягу сталевими кулями. Пройшовши відстань від завантажувального устрою до розвантажувального, матеріал стирається до необхідної величини. При обертанні барабана кулі, що прилягають до стінок барабана і срібло на деякій відстані від нього, безупинно піднімаються, а які перебувають ближек осибарабана безупинно скочуються вниз. Через війну всю масу обертання навколо більш-менш стабільного центру. Перебуваючи між кулями, матеріал безупинно піддається раздавливанию і истиранию.
Осьове пересування та розвантаження матеріалу відбуваються рахунок підпора із боку свіжого харчування, котрий витісняє вміст млини до її разгрузочному кінцю. Для цього він в кульових млинах діаметр розвантажувального отвори робиться трохи більшим, ніж завантажувального. Що Настає різницю рівнів завантаження сприяє переміщенню материала.
Основний тип млини, найчастіше застосовують у цехах анодною маси, представлений малюнку 5. Циліндричний барабан 1 млини закритий з торців кришками 2; кришки мають пустотілі цапфы 3 з підшипниками, у яких обертається барабан. Внутрішня поверхню барабана і торцевих кришок футерованы броньовими износостойкими плитами 4, які кріпляться до стінки барабана болтами 5. Для рівномірного прилегания плит до барабану іноді між плитами і корпусом барабана прокладають прогумовану тканину. Така прокладка послаблює гомін лісу і охороняє барабан мельницы.
Харчування млини виробляється через жодну з порожніх цапф 6 з допомогою шнекового питателя. Розвантаження здійснюється через іншу порожнисту цапфу 7. Млин наводиться у обертання від електродвигуна 10 через редуктор 11, малу провідну 9 ще більшу відому 8 шестірню. Змащування головних підшипників і підшипників приводного валу здійснюється від автоматично діючої циркуляционной системи рідкої мастила, що з маслених насосів 12, бака-отстойника 13, фільтрів і трубопроводів 14.
Використовувана литература.
1. Сушков А.І., Троїцький І.А. «Металургія алюмінію», вид. Металургія, Москва 1965 г., 517стр.
2. Янко Э. А., Воробьёв Д. Н. «Виробництво анодної маси», вид. Металургія, Москва 1975 р., 125 стр.
3. Мережа Internet.