Методи очищення промислових газових викидів
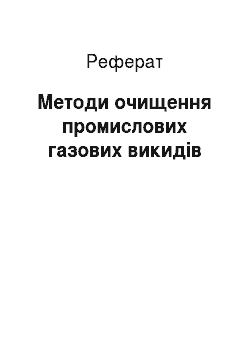
Абсорбционные методи характеризуються безперервністю і універсальністю процесу, экономичностью і можливість вилучення великих кількостей домішок з газів. Недолік цього методу тому, що насадочные скрубберы, барботажные і навіть пінні апарати забезпечують досить високий рівень вилучення шкідливих домішок (до ГДК) і повну регенерацію поглиначів лише за великому числі щаблів очищення. Тому… Читати ще >
Методи очищення промислових газових викидів (реферат, курсова, диплом, контрольна)
ПЛАН КУРСОВОЙ РАБОТЫ:
1. Запровадження стор 3 2. Класифікація газоподібних промислових викидів стор 3 3. Очищення газів від аерозолів стор 4 4. Укладання стор 12 5. Список літератури стор 13.
До етапу розвитку людського суспільства, зокрема індустрії, у природі існувало екологічну рівновагу, тобто. діяльність людини не порушувала основних природних процесів або дуже незначно впливала ними. Екологічний рівновагу у природі з збереженням природних екологічних систем існувало мільйони і після появи особи на одне Землі. Я з тим остаточно в XIX ст. Двадцяте століття ввійшов у історію як століття небувалого технічного прогресу, бурхливого розвитку науки, промисловості, енергетики, сільського господарства. Одночасно як супроводжуючий чинник зростало, і продовжує зростати шкідливе вплив індустріальної діяльності на довкілля. У результаті маємо значною мірою непередбачувана зміна екосистем і лише образу планети Земля. Нині зі зростанням і бурхливим розвитком промисловості велике увагу приділяється її екологічної обгрунтованості, саме проблемі очищенні і утилізації відходів. У цьому роботі розглядається одне із видів відходів промисловості - газові викиди підприємств. Вперше як проблему газові викиди так можна трактувати з прикладу лондонського «смогу» (від анг. smoke — дим), під яким спочатку розуміли суміш сильного туману і диму. Такого типу зміг спостерігався вже у Лондоні вже з більш 100 років тому. Нині то це вже ширший термін — з усіх великими і індустріально розвиненими мегаполісами крім дымотуманного смогу виділяють і фотохімічний зміг. Якщо причиною смогу першого типу в основному спалювання вугілля й мазуту, то причиною другого — викиди автотранспорту. Звісно ж, усе це погіршується деяким кумулятивним дією великого кількості домішок. Zb, при дымотуманном смозі сірчистий газ дає аерозоль сірчаної кислоти (з низки кислотних дощів) який, природно, набагато реактивней за своєю дією. Не дивно, що на даний час пильна увага приділяється проблемі видалення першопричин виникнення таких небажаних явищ, як викиди у повітря. У цьому роботі тематика проблеми свідомо обмежена рамками промислових газових викидів, оскільки саме промисловість є джерелом небезпечних і дуже небезпечних домішок і складових явищ типу «смогу». У газоподібних промислових викидах шкідливі домішки можна розділити на дві групи: а) зважені частки (аерозолі) твердих речовин — пил, дим; рідин — туман б) газоподібні і парообразные речовини. До аэрозолям ставляться зважені тверді частки неорганічної і органічного походження, і навіть зважені частки рідини (туману). Пил — це дисперсная малостійка система, що містить більше великих частинок, ніж дими і тумани. Рахункова концентрація (число частинок один см3) мала проти димами і туманами. Неорганічна пилюку у промислових газових викидах утворюється під час гірських розробках, переробці руд, металів, мінеральних солей і добрив, будівельних матеріалів, карбідів та інших неорганічних речовин. Промислова пил органічного походження — це, наприклад, вугільна, деревна, торф’яна, сланцева, сажа та інших. До димам ставляться аэродисперсные системи з малої швидкістю осадження під впливом сили тяжкості. Дими утворюються під час спалювання палива та її деструктивної переробці, соціальній та результаті хімічних реакцій, наприклад при взаємодії аміаку і хлороводорода, при окислюванні парів металів в електричної дузі тощо. Розміри частинок в димах набагато меншою, ніж у пилу й туманах, і вони становлять від 5 мкм до субмікронних розмірів, тобто. менш 0,1 мкм. Тумани складаються з крапельок рідини, які виникають при конденсації парів чи розпорошення рідини. У промислових выхлопах тумани утворюються головним чином із кислоти: сірчаної, фосфорної та інших. Друга група — газоподібні і парообразные речовини, які у промислових газових выхлопах, значно більше численна. До неї належать кислоти, галогены і галогенопроизводные, газоподібні оксиди, альдегіди, кетоны, спирти, вуглеводні, аміни, нитросоединения, пари металів, пиридины, меркаптани і ще компоненти газоподібних промислових відходів. Нині, коли безвідходна технологія перебуває у періоді становлення й цілком безвідхідних підприємств ще немає, основним завданням газоочистки служить доведення змісту токсичних домішок в газових примесях до гранично допустимі концентрації (ГДК), встановлених санітарними нормами. У цьому таблиці вибірково наведено ГДК деяких атмосферних загрязнителей.
|ВЕЩЕСТВА |ГДК, мг/м3 | | |макр. разова | | |середньодобова | |Аміак |0,2 |0,2 | |Ацетальдегід |0,1 |0,1 | |Ацетон |0,35 |0,35 | |Бензол |1,5 |1,5 | |Гексахлоран |0,03 |0,03 | |Ксилолы |0,2 |0,2 | |Марганець та його сполуки |— |0,01 | |Миш'як та його сполуки |— |0,003 | |Метанол |1,0 |0,5 | |Нітробензол |0,008 |0,008 | |Оксид вуглецю (ЗІ) |3,0 |1,0 | |Оксиди азоту (враховуючи N2O5) |0,085 |0,085 | |Оксиди фосфору (враховуючи P2O5) |0,15 |0,05 | |Ртуть |0,0003 |0,0003 | |Свинець |— |0,0007 | |Сірководень |0,008 |0,008 | |Сірковуглець |0,03 |0,005 | |Сірки діоксид SO2 |0,5 |0,05 | |Фенолу |0,01 |0,01 | |Формальдегід |0,035 |0,012 | |Фтороводород |0,05 |0,005 | |Хлор |0,1 |0,03 | |Хлороводород |0,2 |0,2 | |Тетрахлорид вуглецю |4,0 |2,0 |.
При змісті повітря кількох токсичних сполук їх сумарна концентрація має перевищувати 1, тобто. с1/ПДК1 + с2/ПДК2 + … + сn/ПДКn = 1 де c1, с2, …, сn — фактична концентрація забруднювачів повітря, мг/м3; ПДК1, ПДК2, …, ПДКn — гранично припустиму концентрацію, мг/м3. При неможливості досягти ГДК очищенням іноді застосовують багаторазове розведення токсичних речовин чи викид газів через високі димові труби розсіювання домішок у верхніх шарах атмосфери. Теоретичне визначення концентрації домішок в нижніх шарах атмосфери залежно від висоти труби й інших чинників пов’язані з законами турбулентной дифузії в атмосфери і поки розроблено в повному обсязі. Висоту труби, необхідну, щоб забезпечити ГДК токсичних речовин, у нижніх шарах атмосфери, лише на рівні дихання, визначають по наближеним формулам, например:
[pic].
де ПДВ — гранично припустимий викид шкідливих домішок у повітря, який би концентрацію цих речовин, у приземному прошарку повітря не вище ГДК, г/с; М — висота труби, м; V — обсяг газового викиду, м3/с; (t -різницю між температурами газового викиду і навколишнього повітря, °З; A — коефіцієнт, визначальний умови вертикального і горизонтального розсіювання шкідливих речовин у повітрі, с2/3- (ОС)1/3 (наприклад, для району Уралу, А = 160); F— безрозмірний коефіцієнт, враховує швидкість седиментации шкідливих речовин у атмосфері (для Cl2, HCl, HF F = 1); т — коефіцієнт, враховує умови виходу газу з гирла труби, його визначають графічно чи наближено по формуле.
[pic].
де wг — середня швидкість виході з труби, м/с; DT — Діаметр труби, м. Метод досягнення ГДК з допомогою «високих труб» служить лише паліативом, бо охороняє атмосферу, а лише переносить забруднення вже з району до інших. Відповідно до характером шкідливих домішок розрізняють методи очищення газів від аерозолів і зажадав від газоподібних і парообразных домішок. Усі способи очищення газів визначаються першу чергу фізико-хімічними властивостями домішок, їх агрегатным станом, дисперсностью, хімічний склад і ін. Розмаїття шкідливих домішок з промисловою газових викидах наводить до великого розмаїттям методів очищення, застосовуваних реакторів і хімічних реагентов.
Очищення газів від аерозолів. Методи очищення з їхньої головної засади можна розділити на механічну очищення, електростатичну очищення й очищення з допомогою звуковий і ультразвукової коагуляції. Механічна очищення газів включає сухі і мокрі методи. До сухим методам относятся:
1) гравітаційне осаждение;
2) інерційний і відцентрове пылеулавливание;
3) фільтрація. У багатьох промислових газоочистительных установок комбінується кілька прийомів очищення від аерозолів, причому конструкції очисних апаратів вельми багато. Гравітаційне осадження грунтується на осадженні зважених частинок під дією сили тяжкості на своєму шляху запиленого газу з малої швидкістю без зміни напрями потоку. Процес проводять у відстійних газоходах і пылеосадительных камерах. Для зменшення висоти осадження частинок в осадительных камерах встановлено з відривом 40−100 мм безліч горизонтальних полиць, разбивающих газовий потік на плоскі струменя. Продуктивність осадительных камер П = SwО, де P. S — площа горизонтального перерізу камери, чи загальна площа полиць, м2; wO — швидкість осадження частинок, м/с. Гравітаційне осадження дієво тільки до великих частинок діаметром більш 50−100 мкм, причому ступінь очищення становить чи .вище 40−50%. Метод придатне тільки для попередньої, грубої очищення газів. Інерційний осадження грунтується на прагненні зважених частинок зберігати початкове собі напрямок руху за зміни напрями газового потоку. Серед інерційних апаратів найчастіше застосовують жалюзийные пылеуловители з великою кількістю щілин (жалюзі). Гази обеспыливаются, виходячи через щілини та міняючи у своїй собі напрямок руху, швидкість газу на вході у апарат становить 10−15 м/с. Гідравлічне опір апарату 100 — 400 Па (10 — 40 мм вод. ст.). Частинки пилу з d < 20 мкм в жалюзійних апаратах не уловлюються. Ступінь очищення залежно від дисперсности частинок становить 20−70%. Інерційний метод можна лише для грубої очищення газу. Крім малої ефективності недолік цього — швидке стирання чи забивання щілин. Відцентрові методи очищення газів засновані на дії відцентровій сили, виникає під час обертання очищаемого газового потоку в очисному апараті чи під час обертання частин самого апарату. Як відцентрових апаратів пылеочистки застосовують циклони різних типів: батарейные циклони, обертові пылеуловители (ротоклоны) та інших. Циклони найчастіше застосовують у промисловості для осадження твердих аерозолів. Газовий потік подається в циліндричну частина циклону тангенциально, описує спіраль по до дну конічній частини й потім рухається вгору через турбулизованное ядро потоку у осі циклону для виходу. Циклони характеризуються високої продуктивністю за газ, простотою устрою, надійністю в роботі. Ступінь очищення від пилу залежить від розмірів частинок. Для циклонів високої продуктивності, зокрема батарейных циклонів (продуктивністю більш 20 000 м3/ч), ступінь очищення становить близько 90% при діаметрі частинок d > 30 мкм. Для часток отримують за d = 5(30 мкм ступінь очищення знижується до 80%, а при d = 2(5 мкм вона не перевищує 40%. Діаметр частинок, що вловлюються циклоном на 50%, можна визначити по емпіричну формуле.
[pic].
де (- в’язкість газу, Па*с; DЦ — діаметр вихідного патрубка циклонів, м; NОБ — ефективне число оборотів газу циклоні; wг — середня вхідні швидкість газу, м/с; (год, (р — щільність частинок і є, кг/м3. Гідравлічне опір високопродуктивних циклонів становить близько 1080 Па. Циклони широко застосовують при грубу неуважність і середньої очищенні газу від аерозолів. Іншим типом відцентрового пылеуловителя служить ротоклон, що з ротора і вентилятора, вміщеного в осадительный кожух. Лопаті вентилятора, обертаючись, направляють пилюку у канал, який веде до приймач пилу. Фільтрація полягає в проходженні очищаемого газу через різні фільтруючі тканини (бавовну, шерсть, хімічне волокно, скловолокно та інших.) чи через інші фільтруючі матеріали (кераміка, металокераміка, пористі перегородки з пластмаси та інших.). Найчастіше для фільтрації застосовують спеціально виготовлені волокнисті матеріали — скловолокно, шерсть чи бавовну з азбестом, асбоцеллюлозу. Залежно від фільтруючого матеріалу розрізняють тканинні фільтри (зокрема рукавные), волокнисті, з зернистих матеріалів (кераміка, металокераміка, пористі пластмаси). Тканинні фільтри, найчастіше рукавные, застосовуються за нормальної температури очищаемого газу не вище 60−65°С. Залежно від гранулометрического складу пылей і початковій запорошеності ступінь очищення становить 85−99%. Гідравлічне опір фільтра (Р близько 1000 Па; витрата енергії ~ 1 кВт*ч на 1000 м³ очищаемого газу. Для безупинної очищення тканини продувают повітряними струменями, які створюються різними пристроями — соплами, розташованими проти кожного рукави, рухливими зовнішніми продувочными кільцями та інших. Зараз застосовують автоматичне управління рукавными фільтрами з продувкой їх імпульсами стиснутого повітря. Волокнисті фільтри, мають пори, рівномірно розподілені між тонкими волокнами, працюють із високою ефективністю; ступінь очищення (= 99,5(99,9% при швидкості фильтруемого газу 0,15−1,0 м/с і (Р=500(1000 Па. На фільтрах з стекловолокнистых матеріалів можлива очищення агресивних газів за нормальної температури до 275 °C. Для тонкого очищення газів при підвищених температурах застосовують фільтри з кераміки, тонковолокнистой вати з нержавіючої стали, які мають міцні й сталістю до змінних навантажень; проте їх гідравлічне опір велике — 1000 Па. Фільтрація — дуже поширену прийом тонкого очищення газів. Її переваги — порівняльна низька вартість устаткування (крім металокерамічних фільтрів) та висока ефективність тонкого очищення. Недоліки фільтрації високе гідравлічне опір та швидке забивання фільтруючого матеріалу пилом. Мокра очищення газів від аерозолів полягає в промиванні газу рідиною (звичайній водою) при максимально розвиненою поверхні контакту рідини з частинками аерозолю і, можливо більш інтенсивному перемішуванні очищаемого газу з рідиною. Цей універсальний метод очищення газів від частинок пилу, диму й туману розмірів є найпоширенішим прийомом заключній стадії механічного очищення, особливо газів, які підлягають охолодження. У апаратах мокрою очищення використовують різноманітні прийоми розвитку поверхні дотику рідини і є. Вежі з насадкою (насадочные скрубберы) відрізняються простотою конструкції і експлуатації, сталістю у роботі, малим гідравлічною опором ((Р=300(800 Па) та порівняно малим витратою енергії. У насадочном скруббере можлива очищення газів з початковій запиленістю до 5−6 г/м3. Ефективність одному щаблі очищення для пылей з d > 5 мкм вбирається у 70- 80%. Насадка швидко забивається пилом, особливо в високої початковій запорошеності. Зрошувальні циклони (відцентрові скрубберы) застосовують очищення великих обсягів газу. Вона має порівняно невеличке гідравлічне опір — 400−850 Па. Для частинок розміром 2−5 мкм ступінь очищення становить ~50%. Відцентрові скрубберы высокопроизводительны завдяки великий швидкості газу; у вхідному патрубке (г=18(20 м/с, а сечении скруббера (р = 4(5 м/с. Пінні апарати застосовують очищення газу від аерозолів полидисперсного складу. Інтенсивний пінний режим створюється на полицях апарату при лінійної швидкості газу його повному сечении 1−4 м/с. Пінні газоочистители мають високої продуктивністю за газ та порівняно невеликим гідравлічною опором ((Р однієї полки близько 600 Па). Для часток отримують за діаметром d >5 мкм ефективність їх уловлювання в одній полиці апарату 90−99%; при d < 5 мкм (= 75(90%. На підвищення (встановлюють двохі трехполочные апарати. Скрубберы Вентури (див. рис. 1) — високоінтенсивні газоочисні апарати, але хто з великим витратою енергії. Швидкість газу звуження труби (горловині скруббера) становить 100—200 м/с, а деяких установках — до 1200 м/с. Під час такої швидкості очищаемый газ розбиває на дрібні краплі завісу рідини, впрыскиваемой за периметром труби. Це призводить до інтенсивному зіткнення частинок аерозолю з краплями і уловлюванню частинок під впливом сил інерції. Скруббер Вентури — універсальний малогабаритний апарат, який би уловлювання туману на 99—100%, частинок пилу з d = 0,01(0,35 мкм — на 50−85% і частинок пилу з d = 0,5−2 мкм — на 97%. Для аерозолів з d = 0,3−10 мкм ефективність уловлювання визначається основному силами інерції і можна оцінити по формуле.
[pic].
де До — константа; L — обсяг рідини, поданого в газ, дм3/м3; (- інерційний параметр, віднесений до швидкості газу горловині; при ((90% (є однозначної функцією перепаду тиску в скруббере.
Головний дефект скруббера Вентури — великий витрата енергії із подолання високого гідравлічного опору, що у залежність від швидкості газу горловині їх може становити 0,002−0,013 МПа. Поза тим, апарат не відрізняється надійністю в експлуатації, управління ним складне. Основна хиба всіх методів мокрою очищення газів від аерозолів — це освіту великих обсягів рідких відходів (шламу). Отже, а то й передбачені замкнута система водооборота і утилізація всіх компонентів шламу, то мокрі способи газоочистки сутнісно лише переносять забруднювачі з газових викидів в стічні води, т. е. з атмосфери в водойми. Электростатическая очищення газів служить універсальним засобом, придатним будь-яких аерозолів, включаючи тумани кислот, і за будь-яких розмірах частинок. Метод грунтується на іонізації і зарядку частинок аерозолю при проходженні газу через електричне полі високої напруги, створюване коронирующими електродами. Осадження частинок відбувається на заземленных осадительных електродах. Промислові электрофильтры складаються з низки заземленных пластин чи труб, якими пропускається очищаемый газ. Між осадительными електродами підвішені дротові коронирующие електроди, яких підводиться напруга 25−100 кВ. Теоретичне вираз для ступеня уловлювання аерозолів в трубчастих электрофильтрах має вид.
[pic] що й — швидкість дрейфу частинок до электроду; l — довжина електрода; r — радіус осадительного електрода; (р — швидкість очищаемого газу. На рис. 2 наведено ідеальні криві залежності ступеня уловлювання аерозолів в электрофильтре від розмірів частинок. Криві у цьому малюнку відповідають різним значенням твори рЕЕО, де р — коефіцієнт, для непроводящих частинок р = 1,5(2, для які проводять частинок р=3; Є — напруженість електричного поля; eО — критичне значення напруженості поля. Фактична залежність ступеня уловлювання аерозолів (від діаметра частинок d для промислових электрофильтров визначається експериментально. Очищення ускладнена прилипанием частинок до электроду, аномальним (зниженим) опором шару пилу на електродах і др.
При очищенні від пилу сухих газів электрофильтры можуть працювати у широкому діапазоні температур (від 20 до 500 °З) і тисків. Їх гідравлічне опір невелика — 100−150 Па. Ступінь очищення від аерозолів — вище 90, досягаючи 99,9% на багатопільних электрофильтрах при d > 1 мкм. Недолік цього — великі витрачання коштів зведення і зміст очисних установок істотний витрата енергії створення електричного поля. Витрата електроенергії на електростатичну очищення — 0,1−0,5 кВт на 1000 м³ очищаемого газу. Звукова і ультразвукова коагуляція, і навіть попередня електризація поки мало застосовують у в промисловості й перебувають у основному на стадії розробки. Вони на укрупненні аерозольних частинок, що полегшує їх уловлювання традиційними методами. Апаратура звуковий коагуляції складається з генератора звуку, коагуляционной камери, й осадителя. Звукові і ультразвукові методи застосовні для агрегирования мелкодисперсных аерозольних частинок (туману сірчаної кислоти, сажі) перед улавливанием іншими методами. Початкова концентрація частинок аерозолю для звуковий коагуляції мусить бути щонайменше 2 г/м3 (для частинок d = l (10 мкм). Коагуляцию аерозолів методом попередньої электризации виробляють, наприклад, пропусканием газу через электризационную камеру з коронирующими електродами, де відбувається зарядка і коагуляція частинок, та був через скребачка, у якому газожидкостный шар служить осадительным електродом (рис. 3). Осадительным електродом може бути пінний шар в пінних апаратах, шар газожидкостной емульсії в насадочных скрубберах і інших мокрих газопромывателях, у яких грати й інші відповідні деталі би мало бути заземлены.
Очищення газів від парообразных і газоподібних домішок. Гази в промисловості зазвичай забруднені шкідливими домішками, тому очищення широко застосовується на заводах та підприємствах для технологічних і санітарних (екологічних) цілей. Промислові способи очищення газових викидів від газоі парообразных токсичних домішок можна розділити втричі основні группы:
1) абсорбція жидкостями;
2) адсорбція твердими поглиначами ;
3) каталитическая очищення. У менших розмірах застосовуються термічні методи спалювання (чи дожигания) горючих забруднень, спосіб хімічного взаємодії домішок з сухим поглиначами і окислювання домішок озоном. Абсорбція рідинами застосовується у промисловості для вилучення з газів діоксиду сірки, сірководню та інших сірчистих сполук, оксидів азоту, парів кислот (НСl, HF, H2SO4), діоксиду і оксиду вуглецю, різноманітних органічних сполук (фенолу, формальдегід, леткі розчинники та інших.). Абсорбционные методи служать для технологічної та санітарної очищення газів. Вони грунтуються на виборчої розчинності газоі парообразных домішок в рідини (фізична абсорбція) чи виборчому добуванні домішок хімічними реакціями з активним компонентом поглинача (хемосорбция). Абсорбционная очищення -безперервний і, зазвичай, циклічний процес, оскільки поглинання домішок зазвичай супроводжується регенерацією поглотительного розчину та її поверненням на початку циклу очищення. При фізичної абсорбції (й у деяких хемосорбционных процесах) регенерацію абсорбента проводять нагріванням і зниженням тиску, в результаті чого відбувається нього десорбція поглинутою газової домішки і його концентровано (рис. 4). Деякі формули до розрахунку абсорбційних і хемосорбционных процесів наведені у гол. 4. Показники абсорбционной очищення: ступінь очищення (ККД) і коефіцієнт массопередачи k залежить від розчинності газу абсорбенте, технологічного режиму на реакторі (w, Т, р) та інших чинників, наприклад від рівноваги і швидкості хімічних реакцій при хемосорбції. У хемосорбционных процесах, де у рідкої фазі відбуваються хімічні реакції, коефіцієнт массопередачи збільшується в порівнянню з фізичною абсорбцією. Більшість хемосорбционных процесів газоочистки оборотні, т. е. у разі підвищення температури поглотительного розчину хімічні сполуки, які утворилися при хемосорбції, розкладаються з регенерацією активних компонентів поглотительного розчину і з десорбцией поглинутою з газу домішки. Цей прийом покладено основою регенерації хемосорбентов в циклічних системах газоочистки. Хемосорбция особливо застосовна для тонкого очищення газів при порівняно невеличкий початковій концентрації примесей.
Абсорбенты, застосовувані у промисловості, оцінюються за такими показниками: 1) абсорбционная ємність, т. е. розчинність извлекаемого компонента в поглотителе залежно від температури і тиску; 2) селективність, характеризуемая співвідношенням растворимостей поділюваних газів і швидкостей їх абсорбції; 3) мінімальне тиск парів щоб уникнути забруднення очищаемого газу парами абсорбента; 4) дешевизна; 5) відсутність коррозирующего дії на апаратуру. Як абсорбентів застосовують воду, розчини аміаку, ядучих і карбонатних лугів, солей марганцю, этаноламины, олії, суспензії гидроксида кальцію, оксидів марганцю і магнію, сульфат магнію та інших. Очисна апаратура аналогічна вже розглянутим апаратурі мокрого уловлювання аерозолів. Найбільш поширений насадочный скруббер, застосовуваний очищення газів від діоксиду сірки, сірководню, хлороводорода, хлору, оксиду і діоксиду вуглецю, фенолів тощо. буд. У насадочных скрубберах швидкість масообмінних процесів мала через малоинтенсивного гідродинамічного режиму цих реакторів, працюючих при швидкості газу (р = 0,02(0,7 м/с. Обсяги апаратів тому великі й установки громіздкі. Задля чистоти викидів від газоподібних і парообразных домішок застосовують і інтенсивну массообменную апаратуру — пінні апарати, безнасадочный форсуночный абсорбер, скруббер Вентури, працюючі за більш високих швидкостях газу. Пінні абсорбери працюють при (р = 1(4 м/с і забезпечують порівняно високу швидкість абсорбционно-десорбционных процесів; їх габарити у кілька разів менше, ніж насадочных скрубберов. При достатньому числі щаблів очищення (многополочный пінний апарат) досягаються високі показники глибини очищення: декому процесів до 99,9%. Особливо перспективні очищення газів від аерозолів і шкідливих газоподібних домішок пінні апарати зі стабілізатором пінного шару. Вони порівняно прості по конструкції і працюють у режимі високої турбулентності при лінійної швидкості газу до 4−5 м/с. Прикладом безвідходної абсорбционно-десорбционной циклічною схеми може служити поглинання діоксиду вуглецю з відведених газів розчинами моноэтаноламина із наступною регенерацією поглинача при десорбции СОа. На рис. 5 приведено схема абсорции СО2 в пінних абсорберах; нього десорбція СО2 проводиться також за пінному режимі. Установка безвідхідна, оскільки чистий діоксид вуглецю після скраплення передається споживачеві як товарного продукта.
Абсорбционные методи характеризуються безперервністю і універсальністю процесу, экономичностью і можливість вилучення великих кількостей домішок з газів. Недолік цього методу тому, що насадочные скрубберы, барботажные і навіть пінні апарати забезпечують досить високий рівень вилучення шкідливих домішок (до ГДК) і повну регенерацію поглиначів лише за великому числі щаблів очищення. Тому технологічні схеми мокрою очищення, зазвичай, складні, многоступенчаты і очисні реактори (особливо скрубберы) мають більше об'ємів. Будь-який процес мокрою абсорбционной очищення відпрацьованих газів від газоі парообразных домішок доцільний лише тоді його циклічності і безвідходності. Але й циклічні системи мокрою очищення конкурентоспроможні тільки тоді ми, що вони суміщені з пылеочисткой і охолодженням газу. Адсорбционные методи застосовують щодо різноманітних технологічних цілей — поділ парогазових сумішей на компоненти із фракцій, осушка газів й у санітарної очищення газових вихлопів. Останнім часом адсорбционные методи виходять першому плані як надійне засіб захисту атмосфери від токсичних газоподібних речовин, що забезпечує можливість концентрування і утилізації цих речовин. Адсорбционные методи засновані виборному добуванні з парогазовой суміші певних компонентів з допомогою адсорбентів — твердих высокопористых матеріалів, які мають розвиненою удільної поверхнею Sуд (Sуд — ставлення поверхні до масі, м2/г). Промислові адсорбенти, частіше всього застосовувані в газоочистке, — це активоване вугілля, силикагель, алюмогель, природні і синтетичні цеоліти (молекулярні сита). Основні вимоги до промисловим сорбентам — висока поглинальна здатність, вибірковість дії (селективність), термічна стійкість, тривала служба без зміни структури та властивостей поверхні, можливість легкої регенерації. Найчастіше для санітарної очищення газів застосовують активний вугілля завдяки одній його високої поглотительной спроможності російських і легкості регенерації. Адсорбцію газових домішок зазвичай ведуть у поличкових реакторах періодичної дії без теплообмінних пристроїв; адсорбент розташований на полицях реактора. Коли необхідний теплообмін (наприклад, потрібно отримати при регенерації десорбат в концентрованому вигляді), використовують адсорберы із вбудованими теплообменными елементами або виконують реактор в вигляді трубчастих теплообмінників; адсорбент засипаний в трубки, а межтрубном просторі циркулює теплоносій. Очищаемый газ проходить адсорбер зі швидкістю 0,05−0,3 м/с. Після очищення адсорбер переключається на регенерацію. Адсорбційна установка, що перебуває з кількох реакторів, працює у цілому безупинно, оскільки одночасно одні реактори перебувають у стадії очищення, інші — на стадіях регенерації, охолодження та інших. (рис. 6). Регенерацію проводять нагріванням, наприклад випалюванням органічних речовин, пропусканием гострого чи перегрітого пара, повітря, інертного газу (азоту). Іноді адсорбент, втративши активність (екранований пилом, смолою), повністю заміняють. Найперспективнішими є безперервні циклічні процеси адсорбційної очищення газів у реакторах з які йшли чи зваженим шаром адсорбенту, які характеризуються високими швидкостями газового потоку (значно вище, ніж у періодичних реакторах), високої продуктивністю за газ і інтенсивністю роботи (див. рис. 7).
Загальні гідності адсорбційних методів очищення газів: 1) глибока очищення газів від токсичних домішок; 2) порівняльна легкість регенерації цих домішок з перетворенням в товарний продукт чи поверненням у виробництві; в такий спосіб здійснюється принцип безвідходної технології. Адсорбционный метод особливо раціональний видалення токсичних домішок (органічних сполук, парів ртуті та інших.), які у малих концентраціях, т. е. як завершальний етап санітарної очищення відведених газів. Недоліки більшості адсорбційних установок — періодичність процесу пов’язана з цим мала інтенсивність реакторів, високу вартість періодичної регенерації адсорбентів. Застосування безперервних способів очищення в движущемся і киплячому шарі адсорбенту частково усуває ці недоліки, але вимагає високоміцних промислових сорбентів, розробка яких більшість процесів ще завершено. Каталітичні методи очищення газів засновані на реакціях у присутності твердих каталізаторів, т. е. на закономірності гетерогенного каталізу (див. гол. 5). Через війну каталітичних реакцій домішки, перебувають у газі, перетворюються на інші сполуки, т. е. на відміну розглянутих методів домішки не беруться з газу, а трансформуються в нешкідливі сполуки, присутностей: яких припустимо в выхлопном газі, або у сполуки, легко удаляемые з газового потоку. Якщо які утворилися речовини підлягають видалення, то потрібні додаткові операції (наприклад, вилучення рідкими чи твердими сорбентами). Важко провести межу між адсорбционными і каталитическими методами газоочистки, бо такі традиційні адсорбенти, як активоване вугілля, цеоліти, служать активними каталізаторами багатьом хімічних реакцій. Очищення газів на адсорбентах-катализаторах називають адсорбционнокаталітичної. Цей прийом очищення відпрацьованих газів дуже перспективний через високої ефективності очищення від домішок й можливості очищати більше об'ємів газів, містять малі частки домішок (наприклад, 0,1—0,2 в об'ємних частках SO2). Але методи утилізації сполук, отриманих при каталіз, інші, ніж у адсорбційних процессах.
Адсорбционно-каталитические методи застосовують очищення промислових викидів від діоксиду сірки, сірководню і серо-органических сполук. Каталізатором окислення діоксиду сірки в триоксид і сірководню в сірку служать модифікований добавками активоване вугілля й інші вуглецеві сорбенти. У присутності водяної пари лежить на поверхні на результаті окислення SO2 утворюється сірчана кислота, концентрація якої у адсорбенте становить, залежно кількості водяної пари при регенерації вугілля від 15 до70%. Схема каталітичного окислення H2S в підвішеному шарі високоміцного активного вугілля приведено на рис. 8. Окислювання H2S іде за рахунок реакции.
H2S + ½ О2 = Н2О + P. S Активаторами цієї каталітичної реакції служать водяну пару і аміак, добавляемый до очищаемому газу у кількості ~0,2г/м3. Активність каталізатора знижується у міру заповнення його пір сірою економікою та коли маса P. S сягає 70—80% від безлічі вугілля, каталізатор регенерують промиванням розчином (NH4)2S. Промывной розчин полисульфида амонію розкладають гострим пором із отриманням рідкої серы.
Становить великий інтерес очищення димових газів ТЕЦ чи інших відведених газів, містять SO2 (концентрацією 1−2% SO2), в підвішеному шарі високоміцного активного вугілля із отриманням як товарного продукту сірчаної кислоти і сірки. Іншим прикладом адсорбционно-каталитического методу може бути очищення газів від сірководню окисленням на активному вугіллі чи цеолитах у зваженому шарі адсорбента-катализатора. Широко поширений спосіб каталітичного окислення токсичних органічних сполук і оксиду вуглецю у складі відведених газів з застосуванням активних каталізаторів, які потребують високої температури запалювання, наприклад металів групи платини, заподіяних на носії. У промисловості застосовують також каталітичне відновлення та гідрування токсичних домішок в вихлопних газах. На селективних катализаторах гидрируют ЗІ до CH4 і Н2О, оксиди азоту — до N2 і Н2О etc. Застосовують відновлення оксидів азоту в елементарний азот на палладиевом чи платиновому катализаторах. Каталітичні методи одержують всі популярнішими завдяки глибокої очищенні газів від токсичних домішок (до 99,9%) при порівняно невисоких температурах і звичайному тиску, і навіть за дуже малих початкових концентраціях домішок. Каталітичні методи дозволяють утилізувати реакційну теплоту, тобто. створювати энерготехнологические системи. Установки каталітичної очищення прості в експлуатації і малогабаритны. Недолік багатьох процесів каталітичної очищення — освіту нових речовин, які підлягають видалення з газу іншими методами (абсорбція, адсорбція), що ускладнює встановлення та знижує спільний економічний ефект. Термічні методи знешкодження газових викидів застосовні за високої концентрації горючих органічних забруднювачів чи оксиду вуглецю. Найпростіший метод — смолоскипове спалювання — може бути, коли концентрація горючих забруднювачів близька до нижньої межі запалення. І тут домішки служать паливом, температура процесу 750—900 °З повагою та теплоту горіння домішок можна утилізувати. Коли концентрація горючих домішок менше нижньої межі запалення, необхідно підбивати певна кількість теплоти ззовні. Найчастіше теплоту підводять добавкою пального газу та його спалюванням в очищаемом газі. Горючі гази проходять систему утилізації тепла й викидаються в атмосферу. Такі энерготехнологические схеми застосовують за досить дуже високому вмісті горючих домішок, інакше зростає витрата який додається пального газу. Для повноцінної очищення газових викидів доцільні комбіновані методи, у яких застосовується оптимальне кожному за конкретного випадку поєднання грубої, середній і тонкого очищення газів і парів. На перших стадіях, коли зміст токсичною домішки велике, більш підходять абсорбционные методи, а доочищення — адсорбционные чи каталитические.
Найбільш надійним й найбільш економічним способом охорони біосфери шкідливих газових викидів є перехід до безотходному виробництву, або до безвідхідним технологіям. Термін «безвідходна технологія» вперше запропонований академіком М. М. Семеновим. Під ним мається на увазі створення оптимальних технологічних систем із замкненими матеріальними і енергетичними потоками. Таке виробництво на повинен мати стічні води, шкідливих викидів у повітря i твердих відходів та на повинен споживати воду з природних водойм. Звісно ж, поняття «безвідходне виробництво» має низку умовний характер; це ідеальна модель виробництва, позаяк у реальних умов не можна цілковито ліквідувати відходи і позбутися тяжіння виробництва на довкілля. Точніше слід називати такі малоотходными, дають мінімальні викиди, у яких збитки природним екосистемам буде мінімальний. Нині визначилося кілька основних напрямів охорони біосфери, які у кінцевому підсумку ведуть до створення безвідхідних технологій: 1) розробка і впровадження принципово нових технологічних процесів і систем, які працюють у замкнутим циклом, дозволяють виключити освіту основного кількості відходів; 2) створення безстічних технологічних систем і водооборотних циклів з урахуванням найефективніших методів очищення стічних вод мовби; 3) переробка відходів виробництва та споживання ролі вторинної сировини; 4) створення территориально-промышленных комплексів з замкнутої структурою материльных потоків сировини й відходів всередині комплекса.
Розробка та впровадження принципово нових технологічних процесів і систем, які працюють у замкнутим циклом, дозволяють виключити освіту основного кількості відходів, є основним напрямом технічного прогресса.
1. Основи хімічної технології: Підручник для студентів хим.-технол.спец. вузів / І.П. Мухленов, А.Є. Горштейн, Е. С. Тумаркина; Під ред. И.П.
Мухленова. — 4-те вид., перераб. і доп. — М.: Высш. школа, 1991. — 463 з.: мул. 2. Глінка Н. Л. Загальна хімія. Вид. 17-те, испр. — Л.: «Хімія», 1975. — 728 з.: мул. 3. Кузнєцов В.В., Усть-Качкинцов В.Ф. Фізична і колоїдна хімія. Учеб. посібник для вузів. — М.: Высш. школа, 1976. — 277 з.: мул. 4. Хромів С.П., Петросянц М. А. Метеорологія і кліматологія: Підручник, 4-те вид.: перераб. і доп. — М.: Вид-во МДУ, 1994. — 520 з.: мул. ———————————- Рис 1. Реактор повного змішання — скруббер Вентури: 1 — сопло; 2 — горловина; 3 — камера змішання; 4 — розділова камера Рис 2. Криві залежності ступеня уловлювання пилу в электрофильтре від розмірів частинок: 1 — pEEo = 160; 2 — pEEo = 80; 3 — pEEo = 40;
Рис 3. Схема мокрого пылеулавливания с попередньої электризацией: 1 — камера электризации; 2 — коронирующий електрод; 3 — пінний апарат; 4 — газожидкостный (пінний) шар; 5 — заземленная решітка; I — очищаемый газ; II — вода; III — очищений газ; IV — слив шлама Рис. 4. Схема установки для абсорбционно-десорбционного методу поділу газів: 1 — абсорбер; 2 — десорбер; 3 — теплообмінник; 4 — холодильник.
Рис. 5. Схема абсорбционной очищення газів від СО2 із отриманням товарного діоксиду вуглецю: 1 — холодильник; 2 — повітродувка; 3 — пінний абсорбер; 4 — насос; 5 — теплообмінник; 6 — пінний десорбер; 7 — кип’ятильник десорбера; I — газ на очищення; II — вода; III — очищений газ; IV — діоксид вуглецю споживачеві; V — пар
Рис. 6. Схема адсорбційної газоочистной установки: / — фільтр; 2, 3 — адсорберы; 4 — конденсатор; 5 — сепаратор; / — очищаемый газ; // — очищений газ; ///—водяну пару; IV — неконденсируе. уые пари; V—сконденсированный адсорбтив у сховищі; VI — водний конденсат.
Рис. 7. Катионитовый фільтр: 1 — катионит; 2 — песок.
Рис. 8. Схема каталітичної очищення газу від сірководню в підвішеному шарі активного вугілля: 1 — циклон-пылеуловитель; 2 — реактор зі зваженим шаром; 3 — бункер з питателем; 4 — сушильная камера; 5 — елеватор; 6 — реактор промивання каталізатора (свердло); 7 — реактор екстракції сірки (шнек-растворитель); I — газ на очищення; II — повітря з добавкою NH3; III — розчин (NH4)2Sn на регенерацію; IV — розчин (NH4)2S;
V — регенерований уголь;
VI — свіжий активний вугілля; VII — очищений газ; VIII — промивні воды.