Технология виготовлення болтів методом холодної штамповки
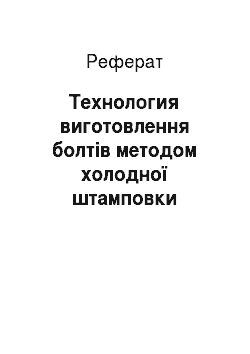
Під час підготовки до штампування нержавіючих сталей може застосовуватися омеднение. На Дружковском кордовому заводі омеднение металу, йде на холодну штампування болтів (з редуцированием стрижня); проводиться у разі наступній технології: а) травлення; б) промивання у гарячій й холодною воді; в) омеднение; р) промивання у холодній воді; буд) нейтралізація (вапнування); е) сушіння. Після… Читати ще >
Технология виготовлення болтів методом холодної штамповки (реферат, курсова, диплом, контрольна)
смотреть на реферати схожі на «Технологія виготовлення болтів методом холодної штампування «.
КЛАСИФІКАЦІЯ БОЛТОВ.
ПЛАНИ БОЛТІВ І ТИПОРАЗМЕРЫ.
До болтам ставляться стрижні з гвинтовій канавкою з одного боку і голівкою іншою, службовці для разъемных сполук окремих частин машин і конструкцій з допомогою гайки.
За формою голівки болти поділяються на болти з багатогранної голівкою, частіше лише від шестигранної, і болти з фасонной голівкою (напівкруглої, потаємними, клеммные, заставні, стикові і др.).
Найбільшого поширення набула отримали болти з шестигранної голівкою, що застосовуються в з'єднаннях, відчувають навантаження різного характеру: статичні, циклічні, динамічні (ударного характеру). Болти з шестигранної голівкою використовують як тяжелонагруженные деталі в двигунах внутрішнього згоряння (шатунные болти), в ходовий частини гусеничних тракторів (башмачные болти), у фланцевых з'єднаннях судин, які перебувають під тиском, і др.
Болти з шестигранної голівкою различаются:
1. По діаметру різьблення і безрезьбовой частини стержня.
Стандарти включають болти з діаметром різьби від 1,6 до 160 мм. Найбільше застосування мають болти з діаметром різьби до 48 мм. Стандарти для цієї «болти виділено на самостійну группу.
По діаметру гладкою (безрезьбовой) частини стрижня болти поділяються на: а) болти з діаметром гладкою частини стрижня, рівним зовнішньому діаметру різьби (ГОСТ 7796—70, ГОСТ 7798–70, ГОСТ 7805–70, ГОСТ 7808–70 та інших.); б) болти з діаметром гладкою частини стрижня, приблизно рівним середньому діаметру різьби (ГОСТ 7795—70, ГОСТ 7811— 70, ГОСТ 15 590–70). Ці болти підвищення центрирования стрижня в отворі скрепляемых деталей мають спрямовує подголовок довжиною щонайменше половини диаметра.
2. По довжині стрижня і довжині резьбы.
Довжина стрижня болтів коливається широтою діапазону від 1,0 d до 10—30 d (d—диаметр резьбы).
Абсолютна довжина резьбовой частини стрижня збільшується зі збільшенням діаметра стрижня, а відносна довжина — зменшується і як від 5 d до 2 d. Розрізняють болти різьблені до голівки і мають безрезьбовой ділянку стержня.
3. За розміром «під ключ» S.
Існують болти з розміром «під ключ» P. S= 1,5—1,6 d і з зменшеним P. S = 1,3—1,4 d. Болти з зменшеним розміром «під ключ» мають відповідно меншу опорну поверхню й тому можна застосовувати в з'єднаннях із зниженими вимогами до міцності на смятие під головкой.
Болти з шестигранної голівкою виготовляються у кількох виконання: основне (рис. 1, а) (без отворів чи заглиблень), з отворами в стрижні чи голівці (рис. 1,6, в) чи з заглибленням у голівці «(рис. 1, р, буд). Болти з отворами в голівці чи стрижні застосовують у з'єднаннях, потребують запобігання самоотвинчивания. Стопорение здійснюється з допомогою шплінтів (дроту), вставляемых в отвір, просвердлене в стрижні чи голівці болта. Поглиблення в голівці виконується для полегшення оформлення шестигранника у процесі безвідходної висадки головки.
[pic] [pic] [pic] [pic].
[pic] р буд Рис. 1. Види болтів з шестигранної головкой Головка болта може мати опорну шайбу (рис. 1, а). При виготовленні голівки болтів із опорною шайбою зменшується величина усунення осі опорною поверхні щодо осі стрижня і знижується можливість появи заусенцев на опорною поверхні. 4. По точності виготовлення (підвищеної, нормальної, грубої). Болти різного рівня точності відрізняються: а) точністю виконання розмірів (діаметра, довжини, висоти голівки та інших.); б) величиною відхилення від правильної геометричній форми (несоосности голівки і стрижня, резьбовой і безрезьбовой частин стрижня, неперпендикулярности опорною поверхні голівки щодо осі стрижня, ухилу граней тощо. буд.); в) дефектами зовнішнього вигляду (зрізами чи відколами металу межах, заусенцами на опорною поверхні, выкрашиванием ниток різьблення і др.).
Дефекти зовнішнього вигляду і величини відхилень від правильної геометричній форми для болтів з діаметром різьби до 48 мм регламентуються ГОСТ 1759–70.
Болти з фасонной голівкою залежно від виду голівки і подголовка призначаються переважно для сполуки конструкцій дерев’янний і листового металу. Стандарти на болти з фасонной голівкою охоплюють болти з діаметром різьби від 5 до 24 мм довжиною від 2 d до 30 d. Залежно від форми та розміру голівки та певного типу подголовка болти виготовляють: з напівкруглої головкою та вусом (рис. 2, а); з напівкруглої головкою та квадратним подголовном (рис. 2,6); з потаємними головкою та вусом (рис. 2, в); з потаємними головкою та квадратним подголовком (рис. 2, г); шинні (з потаємними голівкою) D=1,7—1,8 d, де D—диаметр головки.
Стандарти на болти з напівкруглої голівкою включають болти з полегшеної голівкою .D=1,7—1,8 d, із нормальною голівкою D=2,2—2,3 d і збільшеною голівкою (.D=3,0 d). Потаємні голівки бувають полегшені і нормальные.
[pic] Рис. 2. Види болтів з фасонной головкой.
Болти з фасонной голівкою виготовляють грубої точності різьблені великого кроку по ГОСТ 16 093–70.
Болти зі збільшеним діаметром голівки (понад 2d) застосовують переважно для кріплення дерев’яних конструкцій, оскільки велика опорна поверхню під голівкою зменшує ймовірність смятия деревини. Болти з діаметром голівки менше двох d застосовують у основному задля сполуки конструкцій з металла.
Болти заставні, клеммные і стикові застосовують для рейкових скріплень залізничної колії. Клеммные і заставні болти виготовляють одного діаметра різьби — 22 мм з великим кроком (переважно гарячої штампуванням). Стикові болти виготовляють гарячої штамповкой.
МАТЕРіАЛ І КЛАСИ МІЦНОСТІ БОЛТОВ.
Механічні властивості кріпильних виробів з діаметром різьби до 48 мм матеріали їх регламентуються ГОСТ 1759–70. Для болтів встановлено групи матеріалів: углеродистые і леговані стали; коррозионно-стойкие, жароміцні, жаростойкие і теплоустойчивые стали; кольорові сплави. Здебільшого застосовують болти з вуглецевих і легованих сталей; болти, одержані із матеріалів другої і третьої групи, застосовують у спеціальних випадках при жорсткі вимоги до жаропрочности, коррозионной стійкості, габаритам і вазі соединений.
Болти виготовляють що з спокійних, що з киплячих сталей. З огляду на, що киплячі стали схильні до хладноломкости,.
ніж стали спокійній виплавки, їх застосування кріпильних виробів обмежена. З вуглецевих і легованих сталей в ГОСТ 1759–70 передбачено виготовлення болтів дванадцяти класів міцності, з коррозионно-стойких, жароміцних і жаростойких сталей шести груп, і кольорових металів також шести груп матеріалів. Класи міцності охоплюють діапазон тимчасового опору від 30 до 160, кгс/мм2. Під класам міцності розуміється комплекс механічних властивостей, до складу якого тимчасове опір, межа плинності, відносне подовження після розриву, твердість, напруга від пробної навантаження, а низки класів — ударну в’язкість. Тимчасовим опором у називається ставлення максимальної навантаження Рmах, яку витримує матеріал (болт) в останній момент наступу руйнації, «до початкового поперечному перерізу Fo. Межа плинності Від є найменше напруга, у якому деформація матеріалу не викликає помітного збільшення растягивающей навантаження Рт. Межа плинності визначається на спеціальних зразках. Часто при розтягненні зразків діюча навантаження змінюється до моменту руйнації, у своїй користуються значенням умовного краю плинності. Ударне в’язкість матеріалу характеризується повної роботою, витраченої на деформацію і руйнування спеціального призматичного зразка, з одностороннім надрізом (виточкою), діленої на площа перерізу в надрезе. Зразки вытачиваются з болтів з видаленням різьби. Відносне подовження — цей показник збільшення довжини зразка після розриву для її початковій длине.
Клас міцності болтів позначається двома числами. Перше число, помножена на 10, визначає величину мінімального тимчасового опору (кгс/мм2). Друге число, помножена на 10, визначає ставлення краю плинності до тимчасовому опору (%), а твір чисел визначає величину мінімального краю плинності (кгс/мм2). Запровадження класів міцності полегшує вибір, і розрахунок резьбовых сполук, дозволяє регламентувати зусилля попередньої затяжки, значно підвищує надійність і довговічність поєднанні. Групи матеріалів позначаються двозначним числом, перша цифра якого вказує вид матеріалу, а друга цифра — міцність. При оформленні замовлень продукції, соціальній та різної конструкторської документації болти позначаються по умовної схемою. Умовне позначення болтів включає: найменування деталі, виконання, діаметр різьби, крок різьби, полі допуску різьби, довжину болта, клас міцності чи групу, марку стали чи сплаву, позначення виду покриття, товщину покриття і номер размерного стандарту. Для спрощення позначення часто застосовуваних деталей в умовної схемою не вказуються великий крок різьби, полі допуску 8g, виконання 1, марка углеродистой сталі та кольорового сплаву. Додатково в умовному позначення може відзначати застосування спокійній (буквою З) чи автоматною (буквою А) сталей. Наприклад, болт по ГОСТ 7796–70 виконання 2, має діаметр різьби 1Й мм з кроком 1,25 мм полі допусків 6 g, при довжині 60 мм класі міцності 5.8 (записується без точки) з цинковою покриттям (вид покриття 01) завтовшки, 9 мкм позначається: болт 2 М 12Х1,25—6 ХбО.58,019 ГОСТ 7796–70. ГОСТ 1759–70 рекомендує технологію виготовлення болтів залежно від їх класу міцності. У виробничих умовах болти виготовляються холодної чи гарячої штампуванням і точінням без термічної обробки чи з термічної обробкою після отримання кріпильних виробів однією з перелічених вище способів. Болти, виготовлені холодної штампуванням без термічної обробки, мають знижені пластичні властивості внаслідок наклепа, отриманого при холодної деформації. Розмір краю плинності матеріалу болтів у своїй наближається до величині тимчасового опору і у більшості випадків 0,8— 0,9 Gs. Тому зазначеним методом можна виготовляти лише болти класів міцності 4.8, 5.8, 6.9 та низці випадків 8.8. Нерідко ці самі болти можуть бути виготовлені й холодною штампуванням, але з обов’язковим отжигом вихідного металла.
Высокопрочные болти з среднеуглеродистых і легованих сталей (класи міцності 8.8, 10.9 і 12.9, 14.9) виготовляються з загартованістю і отпуском.
ВИХІДНА ЗАГОТІВЛЯ ДЛЯ ХОЛОДНОЇ ШТАМПУВАННЯ БОЛТОВ.
ВИМОГИ, ЗАПРОПОНОВАНІ До ЯКОСТІ МЕТАЛЛА.
Стабільність технологічного процесу штампування і якість штампуемых болтів багато чому визначаються якістю вихідного металу. Холодна штамповка пред’являє специфічні вимоги до вихідному металу. Матеріал, застосовуваний для холодної штампування, повинен мати високої пластичністю, мати рівномірні механічні властивості і хімічний склад і мати поверхневих й міністром внутрішніх дефектов.
Деформируемость металу у холодному стані, т. е. його спроможність перетерплювати пластичне формоизменение без руйнації, залежить багатьох чинників: якості поверхні заготівлі; хімічного складу; структури; механічних властивостей і технологічних параметрів процесу штамповки.
Дефекти поверхні металу заготівлі є однією з основних причин виникнення надривів і тріщин при холодної штампування. Вони можуть утворюватися різних стадіях переробки металу, починаючи з розливання сталі та закінчуючи калібруванням перед высадкой.
Дефектами розливання є газові бульки, розташовані всередині чи поверхні металу, неметалеві включення, пористість та інших. Газові бульки виникають зазвичай, у киплячою стали, вони в спокійній утворюється нерівномірно розташована пористість. При прокатці дефекти зливків сприяють освіті лежить на поверхні прокату тріщин, заходів, глибоких рисок, волосовин, які потрібно видаляти перед процесом холодної деформации.
Дослідження впливу глибини та конфігурацій поверхневих дефектів на деформируемость углеродистой стали проводять шляхом опади зразків з штучно нанесеною тріщиною різної глибини, різним кутом і радіусом при вершині. Встановлено, що дефекти (волосовины, ризики, полони і ін.) глибиною 0,05 мм більше за висадці з більшими на ступенями деформації розкриваються, створюючи трещины.
Для зниження шлюбу при холодному пресуванні необхідно видаляти дефекти з поверхні оброблюваного металу. Тому поверхню зливків перед прокаткою необхідно зачищати. На металургійних заводах зачистку проводять механічним чи вогняним способом.
При нагріванні зливків перед прокаткою необхідно домагатися найменшого обезуглероживания. На обезуглероженной поверхні внаслідок її зниженою твердості при прокатці утворюються глибші ризики та царапины.
Кількість дефектів, які виникають при прокатці, залежить також від рівня зносу валків. Принаймні зносу лежить на поверхні струмків прокатних валків з’являються надриви металу, виступи, поглиблення тощо. буд. Ці нерівності віддруковуються на гарячому металі і загортаються наступних переходах, що зумовлює порушення сплошности металу. Поверхневі дефекти можуть утворитися при калибровке металу перед штампуванням. До таких дефектів ставляться ризики та подряпини, мають іноді велику протяжність за довжиною. Усунення цих дефектів сприяють: якісне травлення (при незадовільному травленні на металі залишаються частки окалини, які б освіті рисок і подряпин на волочильном інструменті і металі); застосування волок з правильної геометрією робочого каналу; застосування якісної мастила при калибровке.
Пластичність стали, багато чому визначається її хімічний склад. Так, збільшення змісту вуглецю в стали знижує її пластичність і деформируемость, призводить до збільшення прочностных характеристик. Стали з змістом вуглецю ^0,25i% необхідно пом’якшіться збільшення пластичності. Практично почав із змістом вуглецю З 0,5% можна штампувати тільки після попереднього подогрева.
Підвищений вміст кремнію в стали різко знижує її пластичність; при деформировании в холодному стані викликає значний розігрів заготівлі, знижує стійкість інструмента, підвищує зусилля штампування і призводить до утворення трещин.10 702—63. «Сталь для холодної висадки», ГОСТ 1050–74. «Сталь углеродистая якісна конструкційна», ГОСТ 360–71. «Сталь углеродистая звичайного якості», ГОСТ 4543–71 «Сталь легована конструкційна». Сортамент каліброваного металу регламентують ГОСТ 10 702–63, ГОСТ 7417–75. Переважна застосування «штампування має сталь по ГОСТ 10 702–63.
Калиброванная сталь для штампування болтів приходить у натартованном (наклепанном) стані. Наклеп виникає, з допомогою обжатия при волочении гарячекатаної сталі. Твердість нагартованной стали, величини тимчасового опору і відносного звуження нічого не винні перевищувати норм, встановлених відповідними стандартами.
Поверхня калиброванной стали має бути чистою, гладкою, світлої чи матовій без тріщин, волосовин, заходів, полон, окалини. Допускаються окремі дрібні ризики механічного походження на межах «/4 «граничних відхилень на діаметр, і навіть окремі вм’ятини і рябизна в межах полусуммы допусков.
Макроструктура має мати усадочной мушлі та рыхлости, тріщин, бульбашок, расслоений, неметалічних включень і флокенов, видимих без застосування збільшувальних приладів під час перевірки на вітрах чи протравлених образцах.
Слід зазначити, що показники, нормируемые стандартами, й у частковості, ГОСТ 10 702–63, в повному обсязі задовольняють вимогам до металу, призначеному для холодної висадки. Так, величина відносного звуження для низки сталей нормується меншою 50%, випробування на осадку передбачено лише до Va початкової висоти, немає вимоги обов’язкової зачистки поверхні і є др.
ПІДГОТОВКА МЕТАЛУ До ШТАМПОВКЕ.
Метал, готовий до штампування, повинен мати чисту і блискучу поверхню, вільну окалини, жирових та інших забруднень, я утримувати міцно утримувану лежить на поверхні технологічну смазку.
Підготовка поверхні заготівлі включає операції: очищення поверхні від окалини, жирових та інших забруднень; нанесення подсмазочного шару (носія мастила); нанесення технологічної смазки.
Прокат чи термічно оброблений метал тримає в поверхні окисную плівку — окалину, що має бути видалена попередження передчасного зносу технологічного інструменту та отримання чистої і точної заготівлі. Основним способом видалення окалини з заготовок, виділені на холодної штампування болтів, є травление.
Травлення вуглецевих сталей виробляють головним чином розчині, що містить 8—20% сірчаної кислоти, за нормальної температури 50—80°С протягом 10—120 хв, чи концентрованої соляної кислоті при 20— 30° З протягом 5—30 хв. Тривалість травлення залежить від марки стали, діаметра і стану поставки (дротики, бунти) металу і концентрації раствора.
Травление міді, латуні Л63, Л62 роблять у розчині, що містить 3—10% H2S04 за нормальної температури 20—40° З. Травлення алюмінієвих сплавів проводять у розчині з 5—10% їдкого натра і з наступним зануренням в розчин з 10—15% азотної кислоти (пассивированием). Після травлення видалення травильного шламу і кислоти метал промивають в гарячою та холодною воді. Промивання сталевих заготовок у гарячій воді виробляється за нормальної температури 50—70° З протягом 1—2 хв, холодна промивання здійснюється водою під тиском 5—7 атм. протягом 1—2 хв. Для нейтралізації залишків сірчаної кислоти і зменшення коефіцієнта тертя при калибровке й холодною штампування метал піддається вапнуванню в розчині, що містить 3—5% вапна (СаО), за нормальної температури 100° З (2—3 занурення). Допускається вироблення розчину до концентрації СаО 0,5— 1%. На поверхні металу мусить бути суцільна плівка вапна. Нейтралізацію кислоти можна робити у водному розчині мила з концентрацією 0,5—0,8 г/л за нормальної температури розчину 70—80° З протягом 2—3 хв. Після нейтралізації із метою попередження корозії метал піддається сушінню при температурі 100—120° З протягом 15—20 мин.
На підвищення надійності зчеплення мастила з деформируемым металом заготівлю доцільно покривати подсмазочным шаром. Подсмазочное покриття сприяє зниження тертя при штампування і підвищує стійкість штампового інструмента. Особливо ефективно, застосування подсмазочного шару при штампування болтів з редуцированием стержня.
Нанесення подсмазочного шару виробляється перед волочінням чи ж після волочіння (перед штамповкой).
Найбільшого поширення набула одержало нанесення подсмазочного шару перед волочінням, бо за цьому шар носія мастила виходить більш рівномірним за «товщиною і надійно зчепленим із головною металом. Заготівлі з вуглецевих і низьколегованих сталей найчастіше піддають фосфатированию. Фосфатирование залежить від обробки металу в 2,5— 3%- ном розчині кислої фосфорнокислої солі цинку, температура розчину 60—80° З. Тривалість фосфатирования дорівнює 5—15 хв. Фосфатне шар може деформуватися без руйнації разом з основним металом. Фосфатне покриття діє і як безперервний розмежує прошарок поміж контактними поверхнями інструменту та заготівлі, зменшуючи тертя, запобігаючи налипання металу на інструмент і добре утримуючи мастильне речовина. Фосфатирование в 1,2—1,3 разу знижує зусилля деформирования.
Процес підготовки металу з нанесенням фосфатного шару складається з наступних операцій: 1) травлення при фосфатировании волоченого металу — знежирення); 2) промивання водою; 3) фосфатирование; 4) промивання водою; 5) вапнування чи омыление; 6) сушка.
Фосфатне покриття вважається якісним, коли після волочіння зберігається дзеркальний колір (від чорного до сірого), у своїй ніж темнішою колір волочіння, краще покрытие.
Під час підготовки поверхні заготовок з нержавіючих сталей (12Х18Н9Т, 12Х18Н10Т та інших.) замість фосфатирования використовують известково-солевое покриття. Воно не вимагає додаткових операцій для хімічного руйнації плівки, образующейся лежить на поверхні нержавіючої сталі у процесі травлення (пассивирования), і дозволяє працювати на високих швидкостях при волочении.
Нержавіючі і жаростойкие стали готуються до штампування за такою технології: 1) травлення, 2) промивання у гарячій воді, 3) пассивирование, 4) промивання у гарячій воді, 5) нанесення известково-солевого покриття, 6) сушіння, 7) калибровка.
Известково-солевое покриття має істотними недоліками. Куховарська сіль прискорює процес корозії металу, в сиру погоду вбирає вологу і утрудняє процес волочіння. З іншого боку, вапно дуже порошить, засмічує повітря та приміщення цехи і цим погіршує умови труда.
Під час підготовки до штампування нержавіючих сталей може застосовуватися омеднение. На Дружковском кордовому заводі омеднение металу, йде на холодну штампування болтів (з редуцированием стрижня); проводиться у разі наступній технології: а) травлення; б) промивання у гарячій й холодною воді; в) омеднение; р) промивання у холодній воді; буд) нейтралізація (вапнування); е) сушіння. Після калібрування метал піддається вторинному мед нению. Омеднение виробляється у розчині, що містить 120—150 г/л мідного купоросу, 50—60 г/л сірчаної кислоти і 2—3 г/л столярного клею за нормальної температури розчину 18—22°С протягом 1—1,5 хв (дворазове занурення). Омеднение вважається задовільним, якщо поверхню металу покрита суцільний мідної плівкою без відшарування, рыхлости і просвітлювання основного металу (через плівку). Омеднение поступається фосфатированию за паливною ефективністю зниження коефіцієнта тертя, ще, під час мідного покриття важко контролювати його властивості. Позитивні результати при штампування важко деформируемых сталей дають лаковые покриття та обробка в розчині щавлевої кислоти (оксалатирование). Зазначені покриття застосовуються і за штампування кольорових сплавів. На калібрований метал перед штампуванням чи процесі штампування наноситься технологічна змащування. Як мастила часто використовується мильна емульсія. Хороші результати дає застосування розчину сульфіду молібдену в машинному олії. Останніми роками знаходять використання у процесах штампування спеціальні смазки—укринолы. На московському заводі «Станконормаль» використовується смазочнощо охолоджує рідина з урахуванням парафіну (СОЖ В23 До) і укринол 5/5, дозволяють штампувати метал без фосфатного покриття. Для отримання заготівлі з необхідними для штампування болтів розмірами 5 d необхідно збільшувати гарантований зазор, т. е. додатково занижувати розміри резьбы.
ТЕХНІКА БЕЗПЕКИ НА РОБОЧОМУ МІСЦІ ПРЕССОВЩИКА.
Правила техніки безпеки в цеху і робоче місце прессовщика встановлюються спеціальними інструкціями і Правилами, знання й дотримання яких періодично контролюється адміністрацією цеху. Правила техніки безпеки поділяються на загальні, застосовні усім ділянках цеху, і спеціальні, справжні лише даного робочого места.
Найважливіші із правил следующие:
1. Необхідно утримувати чистими робоче місце, недопущення наявності сторонніх предметів у зоні обслуговування автоматов.
Не можна залишати на станині автомата або близько неї технологічний і інший інструмент, котрі можуть потрапити до мобільні частини пресу КПРС і призвести до аварії, і травмування. 2. Не слід допускати загромождения проходів сторонніми предметами, сировиною чи готової продукцією, і навіть їх забруднення (олією, СОЖ). 3. Слід носити й містити спецодяг в справному состоянии.
4. Під час роботи устаткування пресувальник повинен бути своєму робоче місце. Не варто переходити в інший ділянку без дозволу руководителя.
5. За виконання роботи по прямий спеціальності (під час простоїв чи ремонту преса) необхідно ознайомитися правила безпечного виконання нової работы.
Перед пуском преса в роботу необхідно забезпечити чистоту робочого місця і перевірити готовність преса до пуску.
Запрещается:
1. Працювати на устаткуванні: а) за відсутності огороджень, передбачених даним автоматам, або за їх несправному стані; б) при несправних гальмівних, блокуючих і запобіжних пристроях; в) при несправному электрооборудовании та не заземлення; р) при несправному кріпленні технологічного інструмента; буд) при збільшених зазорах в направляють высадочного ползуна.
Великий знос направляють высадочного повзуна веде до підвищення несоосности пуансонов і матриць і може викликати поломку інструменту небезпечними наслідками. При несправному кріпленні інструмента може статися його виліт з гнізда, поломка автомата і травмування прессовщика. 2. Виробляти настроювання і кріплення інструмента під час роботи механізмів чи неповної їх зупинці. Перевірка правильності установки технологічного інструмента повинна здійснюватися спеціальними міткам, а інструменті чи становищу крепящих гайок і стопорів. Налаштування пресів і пробна штамповка заготовок повинна перевірятися на мінімальної швидкості, на одиночних ходах автомата. Для перевірки взаємодії механізмів й налагодження інструмента на пресах, не оснащених микроприводом чи толчковым включенням, повинні прагнути бути встановлено штурвали чи устрою для ручного повороту маховика. 3. Розкривати електрообладнання автоматів. 4. Вмикати автомат, не заручившись відсутності сторонніх предметів в робочих зонах. Пресувальник може розпочати роботу тільки після усунення всіх недоліків. Працюючи на прессах-автоматах треба пильнувати за справним состоянием:
1) інструмент наладки автомата;
2) пульту управління механізмами автомата (роботи кнопок включення і вимикання, світловий сигнализации);
3) огороджень механізмів преса, блокуючих і запобіжних устройств;
4) токоведущих частин електроустаткування, заземлення оборудования;
5) гальмівних устройств.
За виконання ремонтних і налагоджувальних робіт необхідно застосовувати інструмент, готовий до цих работ.
Після закінчення робіт робоче місце має бути наведено до ладу, поставлені цього разу місце огорожі, відновлено запобіжні устройства.
Спостереження над роботою автомата слід вести або через захисні скла, або за їхню відсутність в захисних окулярах на безпечному расстоянии.
Особливістю роботи автоматів служить наявність багатою мастила інструменту та заготовок. Неприпустимо розбризкування СОЖ на нерухомі частини устаткування й робочу майданчик; вироби повинні вступати у коробку без винесення зайвої мастильно-охолодної рідини; із метою уникнення травмування заусенцами і гострими крайками металу його завдання слід в рукавицях. Для зниження впливу шуму рекомендується застосовувати противошумныс навушники, антифони, «беруши» і інші устройства.