Разработка технологічного процесу зміцнення кулачка головного валу з допомогою лазерного излучения
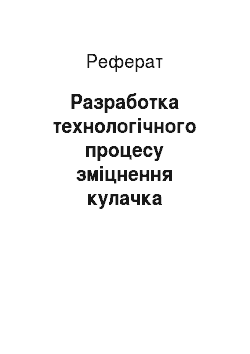
Таблиця 6.3 Значення нормувальних показників виробничої середовища |Чинники, |Нормируемые |Вигляд нормативного |Чисельні — |характеризующие|показатели, единицы|документа його |значення — |умови праці |виміру |номер |показника — |Запиленість |ГДК пилу, м2/м3 |ГОСТ — | — | |12.1.005−88 |6 — |Параметри |Оптимальні |Сан. ПиН |Для робіт — |мікроклімату |значення |2.2.4.548−96 |категории11 а… Читати ще >
Разработка технологічного процесу зміцнення кулачка головного валу з допомогою лазерного излучения (реферат, курсова, диплом, контрольна)
РРЕФЕРАТ.
Шорина Є. Д. Розробити технологічний процес зміцнення кулачка головного валу з допомогою лазерного випромінювання: Дипломний проект Димитровградский інститут технології управління і дизайну. № 1707.06.04. Димитровград, 2004 — 116с.: 14 мул. + 7 черт.
Лазер, гарт, карбюризатор, кулачок головного валу, зносостійкість, зміцнення, борирование, потік, такт.
У процесі виконання дипломного проекту проведено опис методів зміцнення. Вибрано спосіб мислення і технологія зміцнення кулачка. Проведено випробування до зносу матеріалу. Зроблений вибір устаткування, ріжучого і міряльного інструмента, розроблений технологічний процес. Розрахована ефективність виготовлення цієї деталі. Розробили ряд заходів із запобіганню нещасних випадків, дано рекомендації по правильному використанню та організації производства.
Зроблено висновки та рекомендації по зміцнення кулачка з допомогою лазерного излучения.
СОДЕРЖАНИЕ ВВЕДЕНИЕ 6 1. МЕТОДИ ЗМІЦНЕННЯ МАТЕРІАЛІВ 8 1.1. Термічна обробка 8 1.1.1. Химико-термическая обробка 8 1.1.2. Борирование 9 1.1.3. Плазмова обробка 11 1.1.4 Лазерна обробка 12 1.2 Лазерна установка 14 1.3. Термічна обробка матеріалів лазерним випромінюванням 16 1.4. Фізичні основи зміцнення лазерним випромінюванням 17 1.5. Вплив безперервного лазерного випромінювання на сплави з урахуванням заліза 19 1.6. Зміцнення кулачка головного валу 24 2. КОНСТРУКТОРСЬКА ЧАСТИНА 28 2.1. Призначення вузла «вал головний» автомата хладновысадочного 28 2.2. Вибір способу зміцнення кулачка головного валу 29 2.3. Пристосування для зміцнення 34 2.4. Технологія зміцнення 45 3. ДОСЛІДНИЦЬКА ЧАСТИНА 47 3.1. Лазерна обробка на CO2 — лазері 47 3.2. Випробування матеріалу до зносу 47 3.3 Дослідження зносостійкості покриття 49 4. ТЕХНОЛОГІЧНА ЧАСТИНА 51 Запровадження 51 4.1. Аналіз технологічності конструкції деталі «Кулачёк» 51 4.2. Вибір устаткування, ріжучого, допоміжного і міряльного інструментів 58 4.3. Розрахунок режимів різання 60 4.4. Нормування технологічного процесу 66 4.5. Розрахунок спеціального калибра-пробки контролю отвори (60Н7 +0,030 68 5. ЕКОНОМІЧНА ЧАСТИНА 72 Запровадження 72 5.1. Розрахунок параметрів потоку 72 5.2. Розрахунок собівартості виготовлення деталі 80 5.3. Техніко-економічні показники потоку 85 Висновок 87 6. БЕЗПЕКА ЖИТТЄДІЯЛЬНОСТІ 88 Запровадження 88 6.1. Загальні питання безпеки праці 89 6.2.Мероприятия щодо забезпечення нормальних санітарно-технічних умов 95 6.3. Заходи з запобіганню нещасливі випадків, гарантуванню безпеки експлуатованого устаткування й транспортних засобів 103 Висновок 109 ВИСНОВОК 110 ЛІТЕРАТУРА 111 ДОКЛАДАННЯ 115.
Обробка матеріалу сфальцьованим випромінюванням лазера є науковим і технічним напрямом технології машинобудування й інших сфер промисловості, що ще після 1960 року, коли було створено потужні імпульсні генератори монохроматического излучения.
Лазерна обробка матеріалів перестав бути ще які встановилися і закінченим розділом теорії та практики обробки матеріалів концентрованими потоками енергії. Однак у розробці теоретичних основ процесів впливу потужних світлових потоків на матеріали й у практичних цілях зазначених процесів досягнуто значні успехи.
Застосування різних типів лазерів у багатьох областях машино — і приладобудування і правильна їх експлуатація не можливі без чіткого уявлення про принципи роботи оптичних квантових генераторів про основних фізичних явищах, у яких происходящих.
Переваги і перспективність використання лазерів у машинобудуванні визначаються як прогресу у сфері власне лазерної техніки, але і вмілим, науково обгрунтованим вибором оптимальних кожному за конкретного застосування режимів роботи лазера і параметрів його излучения.
Промислова обробка матеріалів одним з областей найбільш використання лазерів, особливо — по появи лазерів високої потужності. Лазерний промінь застосовується для різання і свердління отворів, зварювання матеріалів і термообробки, обробки тонких металевих і неметалічних плівок, отримання ними рисунків і мікросхем. Доведення номіналів пасивних елементів мікросхем і нові методи отримання ними активних елементів з допомогою лазерного променя набули подальшого розвитку і застосовують у виробничих умовах. При що ж лазерна обробка матеріалів дозволяє збільшити ефективність і конкурентоспроможність по порівнянню коїться з іншими обработками.
1. МЕТОДИ ЗМІЦНЕННЯ МАТЕРИАЛОВ.
1.1. Термічна обработка.
Поверховим зміцненням називається зміцнення поверхневого шару деталі рахунок зміни його хімічного стану або структуры.
Для отримання сталі із найбільшою міцністю і твёрдостью необхідна термічна обробка — гарт. Термообробка — це сукупність операцій технології теплового на матеріал з єдиною метою зміни його структури та споживчих властивостей у потрібному напрямку. Зміцнення поверхні можна досягнути: химико-термической, плазмової, лазерної обробкою й др.
1.1.1. Химико-термическая обработка.
Однією із визначальних коштів поліпшення якості сталевих деталей — підвищення їх міцності, твердості і зносостійкості - є химикотермічна обробка, яка полягає в насиченні поверхні вуглецем, азотом, хромом, бромом та інші елементами. При запровадження у поверховий шар хрому, кремнію, алюмінію та інших елементів можна надати виробу стійкість проти корозії, жаростійкість, кислотоупорность та інші свойства.
У промисловості отримали стала вельми поширеною такі види химико-термической обработки:
— цементація — насичення углеродом;
— азотування — насичення азотом;
— цианирование — одночасне насичення вуглецем і азотом;
— диффузионная металлизация — насичення різними елементами (крім вуглецю й азоту), наприклад, хромом, бромом, алюмінієм та інші. Кожен із цих способів має свої особливості, переваги та недостатки.
1.1.2. Борирование.
Борирование — насичення поверхневого шару металевих виробів бором. До борированию вдаються, переважно, з метою підвищення поверхневою твердості виробів, їх зносостійкості, рідше — коррозионной стійкості і теплостойкости. Борированию піддають поверхні виробів із заліза, сплавів його основі, і навіть тугоплавких металів, використовуючи явище дифузії. Розрізняють борирование тверде, рідке, газовое.
При твердому борировании очищені вироби вміщують у герметичний чи негерметичный контейнер, засипаючи їх реакційної сумішшю, що з порошкоподібного боризатора (аморфного бору, карбіду бору, ферробора і ін.), інертної добавки (окису алюмінію, кварцевого піску, тонкоизмельченного шамоту), введеної задля унеможливлення спечення чи налипання суміші на поверхню виробів, і активатора (галогенида, зазвичай NH4Cl) у відсотковому співвідношенні приблизно 60:35 — 39:1 — 5. Вироби вкладають так, щоб навколо яких був шар реакційної суміші тощиной щонайменше 20 -30 мм. Хороше якість диффузионного шару досягається також за насиченні вуглецевих і легованих сталей в суміші карбіду бору та бури. Для отримання шару боридов завтовшки 0,1 — 0,3 мм насичення проводять при температурі 900 — 1000 оС протягом п’яти — 6 часов.
Різновидом твердого є вакуумне борирование, здійснюване в вакуумно-плотных контейнерах при остаточном тиску 10−3 рт.ст. При високих температур випаровування аморфного бору чи карбіду бору утворюються пари цього елемента, які конденсуються на оброблюваної поверхні, і атомарний бір дифундує в металл.
Рідинне борирование проводять за нормальної температури 850 — 1000 оС в розплавах різних солей з введенням у них борсодержащих компонентів. Рідинне электролизное борирование зазвичай ведуть у розплаві бури, ми інколи з добавкою карбіду бору. Сталеве виріб підключають як катода в ланцюг постійного струму, анодом служить попередньо борированный тигель з жаростойких і нержавіючих сталей. Задовільною стійкістю мають також просочені бурої графітові і керамічні тиглі. При расплавлении бура диссоциирует термічно, і навіть внаслідок накладення постійного електричного струму із атомів активного бору, диффундирующего в обрабатываемое виріб. Насичення проводять при щільності струму 0,15 — 0,25а/см2. Рідинне диэлектролизное борирование здійснюють в розплавах бури з додаванням карбіду бору. Хороші результати виходять при співвідношенні цих компонентів 60: 40. Дифузний шар можна створити й у розплавах солей NaCl і BaCl з додаванням карбіду бора.
Газове борирование проводять при термічному розкладанні газоподібних сполук бору — диборана (В2Н2), трёххлористого бору (ВСl3) та інших., частіше лише у суміші з воднем у відсотковому співвідношенні відповідно 1:25−100. При температурі вище 500 градусів диборан майже зовсім ращлагается на активний бір і водень, що й омивають насыщаемое виріб. При газовому борировании насичення протікає інтенсивніше, аніж за твердому чи рідкому: за 2−5 год. при температурі 800−900 градусів утворюється шар боидов завтовшки 0,1−0,2 мм. На виробах зі заліза і вуглецевих сталей дифузний шар відрізняється иглообразным будовою і складається з 2 фазромботического борида FeB (16,25%B) лежить на поверхні і що під ним тетрагонального борида Fе2 В (8,48%), микротвёрдость становить 1800 год 2000 і 1600 год 1800 кгс/мм2. Під шаром боридов перебуває перехідна зона, ця зона складається з твердого розчину бору та інших легуючих элементов.
Легування стали забезпечує отримання більш рівномірного за «товщиною боридного слоя.
Борирование викликає появу у поверхневих шарах виробів залишкових знімаючих напруг до 50 — 100 кгс/мм2, підвищує їх зносостійкість в розмірі 5 — 10 раз, збільшує коррозионную стійкість вуглецевих і низьколегованих сталей. Борирование підвищує усталостную міцність виробів. Коррозионнаяусталостная міцність виробів із вуглецевих сталей після борирования збільшується й більш. Недолік борирования — підвищена крихкість боридов, яку знижують, вводячи у реакційну суміш небагато міді, алюмінію та інших металлов.
1.1.3. Плазмова обработка.
Сутність обробки у тому, що плазму, має температуру 10 000 — 30 000 градусів, направляють на оброблювану поверхню заготівлі. В такий спосіб можна обробляти заготівлі з будь-яких матеріалів, виконуючи прошивание отворів, вирізку заготовок з листового матеріалу, стругання, гостріння. При прошивании отворів, краянні і вирізці заготовок, голівку ставлять перпендикулярно до заготівлі, при строгании і точении — з точки 40 — 60 0. Плазмові голівки застосовують також і зварювання, пайки, наплавки і шляхом створення захисних покриттів на деталях.
Принципово новим методом є метод отримання деталей безпосередньо з плазми. Він у тому, що у камеру голівки подається порошкоподібний конструкционный матеріал з одночасної подачею інертного газу за високого тиску. Під впливом іншого розряду конструкционный матеріал плавиться і до стану плазми. Струмінь плазми стискається в плазмотроне плазмообразующим газом. Виходячи з сопла голівки, промінь фокусується електромагнітної лінзою і направляється на екран. Системи вертикальної і горизонтальній развёрток забезпечують переміщення променя у всій площі экрана.
Плазму одержують у плазмових головках.
Дугового розряд 3 порушується між вольфрамовим електродом 4, виконаним як труби і охлаждённым проточній водою. У трубу подають газ (аргон, азот та інших.) чи суміш газів. Обжимаючи дугового розряд, газ при поєднанні з електронами іонізується і виходить із сопла голівки як яскраво світної струменя 2, що спрямована на оброблювану заготівлю 1.
1.1.4 Лазерна обработка.
Термічне зміцнення матеріалів і сплавів лазерним випромінюванням грунтується на локальному нагріванні ділянки поверхні під впливом випромінювання та наступному охолодженні цього поверхового ділянки зі сверхкритической швидкістю результаті тепловідведення теплоти у внутрішні верстви металу. У цьому час нагріву та палестинці час охолодження незначні, немає витримка за нормальної температури нагріву. Ці умови забезпечують високі швидкості нагріву і охолодження оброблюваних поверхневих участков.
Метод грунтується на тепловому вплив світлового променя високої енергії на поверхню оброблюваної заготівлі. Джерелом світлового випромінювання є лазер — оптичний квантовий генератор (ОКГ).
Створено конструкції твердотелых, газових і напівпровідникових ОКГ. Робота оптичного квантового генератора полягає в принципі стимулированного генерування світлового випромінювання. Для механічної обробки використовують твердотелые ОКГ, робочим елементом якого є рубіновий стрижень, що з окису алюмінію, активованого 0,05% Cr.
Рубіновий ОКГ працює у імпульсному режимі, генеруючи імпульси когерентного монохроматического червоного світла. Енергія світлового імпульсу ОКГ зазвичай невелика і як 20 -100 Дж.
Лазерну обробку застосовують для прошивания наскрізних і глухих отворів, різання заготовок на частини, вирізання заготовок з листового матеріалу, прорезания пазів тощо. Світловим методом можна обробляти будь-які материалы.
[pic].
Рис. 1 Схема плазмової голівки До вад светолучевого методу обробки можна віднести відсутність надійних способів управління рухом променя й необхідність переміщення заготовок, недостатню потужність випромінювання при значної потужності імпульсної лампи, низький ККД рубінових ОКГ, перегрів рубінового стрижня і труднощі його охолодження, порівняно не висока точність обработки.
1.2 Лазерна установка.
Сегментное собирающее дзеркало складається з кількох пласких дзеркало. Кут між окремими дзеркалами менше 180о, тому сукупність їх утворює увігнуту поверхню. Водночас направляють випромінювання у загальну точку. Зазвичай такі дзеркала виготовляються з полірованої міді чи молібдену, і за «підсумовуванні» випромінювання потужних лазерів вони розладнуються водой.
Лазерне випромінювання потрапляє на дзеркало, що складається з безлічі окремих дзеркал, де відбувається розподіл променя (рис. 1.2).
Кожен знову освічений промінь має однаковий діаметр протягом відстані від дзеркала до площині лінзи. І тут в плямі фокусування відбувається накладення інтенсивностей кожного окремого променя, що зумовлює підсумовуванню їх. Розподіл інтенсивності випромінювання від кожної елемента сегментного дзеркала, які зазвичай виконуються у вигляді прямокутників. З іншого боку, випромінювання малої потужності за українсько-словацьким кордоном лазерного променя, якого недостатньо, щоб викликати процес термоупрочнения, не втрачається, а, навпаки, з допомогою сегментного дзеркала додається в пляма фокусування. Отже, поширення інтенсивності в плямі фокусування вирівнюється, а прямокутна форма плями, у якому фокусується лазерне випромінювання, оптимальна щоб одержати однорідної зони закалки.
[pic].
Рис. 2.1. Лазерна установка.
1.3. Термічна обробка матеріалів лазерним излучением.
Поверхове зміцнення металевих деталей — перспективний технологічний процес, відкриває низку нових можливостей для підвищення експлуатаційних характеристик деталей машин, инструмента.
Поверхове зміцнення деталей променем лазера характеризується поруч переваг, саме: зміцненням локальних (за глибиною та ширині) обсягів деталей у місцях, їх зносу зі збереженням вихідних властивостей матеріалу в іншому обсязі, твердість у своїй перевищує 15 — 20% твердість посаді термообробки існуючими способами.
Зміцненням поверхонь важкодоступних порожнин, заглиблень, куди промінь лазера може бути введений з допомогою оптичних пристроїв; створенням «плямистого» поверхового зміцнення значних площ, у якому не утворюється суцільного тендітного шару, схильного до растрескиванию, деформированию, отслаиванию тощо.; отриманням заданих властивостей (механічних, хімічних та інших) оброблюваних поверхонь деталей шляхом їх легування різними елементами з допомогою випромінювання лазера; відсутністю деформацій оброблюваних деталей, обумовлених локальностью термообробки, що дозволяє практично повністю припинити фінішну обробку; відсутністю механічного на опрацьований матеріал, разом із бесконтактностью лазерного нагріву зумовлює простоту автоматизації процесу термообробки по контуру, зокрема деталей складної форми і др.
Лазерні методи зміцнення доцільні при обробці поверхонь складної конфігурації, деформування яких має бути зведено до мінімуму; при труднощі підвода теплоти до оброблюваної зоні деталі звичайними способами; при малих розмірах поверхні оброблюваних зон в порівнянні з розмірами деталей.
Широке впровадження методів лазерного зміцнення у різні галузі промисловості обумовлюється поруч сприятливих факторов:
— наявністю серійного лазерного високопродуктивного устаткування як імпульсного, і безперервного действия;
— порівняльної простотою лазерного зміцнення, яка зумовлює нескладний добір технологічних режимів обробки деталей;
— значної номенклатурою оброблюваних деталей, потребують локального упрочнения;
— великий техніко-економічній ефективністю, обумовленою достоїнствами лазерної термообробки і др.
Нерідко форми й розміри різних деталей неможливо використовувати наявні способи поверхового зміцнення для термообробки внаслідок появи значних напруг у поверхневих шарах, призводять їх до деформированию тощо. Тому міцність деталей, виготовлених, наприклад, з конструкційних сталей може поставки, зазвичай, невелика.
Методи лазерної обробки утворюють групи, засновані, відповідно, на нагріванні, плавленні і ударному нагружении матеріалу залежно від щільності випромінювання лазера і час його воздействия.
Нагрівання визначає такі процеси, як відпал матеріалів, і навіть найпоширеніший метод лазерного поверхового зміцнення у вигляді фазових перетворень в твердому стані поверхневих шарах металів і сплавів за дуже швидких нагріванні і наступному охлаждении.
Лазерне зміцнення, заснований на фазових перетвореннях в поверхневому шарі, вимагає мінімальної щільності потоку випромінювання лазера за максимального його воздействии.
1.4. Фізичні основи зміцнення лазерним излучением.
Більшість лазерних технологічних процесів полягає в тепловому вплив лазерного випромінювання на непрозорі середовища. Вплив променя лазера на непрозорі середовища можна умовно розділити сталася на кілька характерних стадий:
— поглинання світлового потоку і передачі його енергії тепловим коливань ґрати твердого тела;
— нагрівання речовини без його разрушения;
— розвиток випаровування речовини у зоні впливу променя лазера і разлёт продуктів разрушения;
— остигання речовини після закінчення дії лазерного излучения.
Поруч із зазначеними стадіями проходять диффузионные і хімічні процеси, а як і фазові перетворення, які надають значний вплив на характер впливу випромінювання лазера на материалы.
Кількість поглощённой енергії залежить від оптичних і теплофизических властивостей матеріалів, особливо металів і зі збільшенням довгі хвилі випромінювання уменьшается.
Відбивна здатність у потрібний оптичному діапазоні довжин хвиль становить більшість металів 70 — 95%, а коефіцієнт поглинання також досить великий і як ~ 105−106см -1.
Стадію нагріву матеріалів випромінюванням лазера можна вважати основний під час аналізу і дослідженні низки технологічних процесів, виконуваних без руйнації материалов.
Аналіз стадії й інших технологічних процесів, заснованих на виключно видаленні оброблюваного матеріалу, дозволяє визначити умови руйнації, наприклад, температурну кордон і направлення відповідний їй потік випромінювання лазера.
Після переходу енергії випромінювання лазера в теплоту починається процес нагріву матеріалу. Поглощённая світлова енергія передається від зони впливу «холодним» верствам з допомогою різних механізмів теплопровідності, у тому числі для металів в інтервалі температур від сотень до десятків тисяч градусів основним є електронна теплопроводность.
1.5. Вплив безперервного лазерного випромінювання на сплави з урахуванням железа.
Розглянемо основні найтиповіші структурні зміни у сплавах заліза в зонах впливу безперервного випромінювання лазера на СО2 з потужністю випромінювання 700 Вт — 1 кВт. Обробляли нерухомі зразки згодом впливу до 5 сек. і котрі переміщалися зі швидкістю до 1 м/мин і более.
У армко-железе внаслідок впливу випромінювання лазера на СО2 на нерухомий зразок в шарі завтовшки до 0,55 мм спостерігається здрібніння зерна до розмірів 10 — 15 мкм, що відбувається в найбільш шарі глибиною до 0,35 — 0,55 мм. У областях, що прилягають до кратору зустрічаються великі зерна. Здрібніння зерен є наслідком процесів аустенизации за умов розігріву і наступного розпаду аустеніту при охолодженні, у своїй виникають різні швидкості зародження і зростання зерен феррита, що обусловдено, ймовірно, різними розмірами зерен аустеніту, які виникають в безпосередній наближеності до рідкої фазі і віддаленні неё.
Микротвёрдость армко-железа Нm? 4000 мПа. Слід зазначити, що фронт расплавлений виражений не чётко.
У зонах тривалого впливу випромінювання лазерів на СО2 все досліджені сплави заліза у верхній частині, котрий іноді за шаром пористого розплаву спостерігається так званий шлак шар, який складається приемущественно з окислів заліза та інших продуктів химико-термического взаємодії безперервного випромінювання зі сплавами у атмосфері повітря і растворённых в металі газов.
При опроміненні маловуглецевої сталі у зоні впливу спостерігається грубозерниста видманштетова структура з микротвёрдостью, істотно не відрізнялася від исходной.
У зразках зі сталі 45 із вихідною структурою, що з перлитных зерен з ферритными прошарками, внаслідок тривалого впливу безперервного випромінювання довгою хвилі? = 10,5 мкм утворився разом із жужільним, шар розплавленого і пористого металу завтовшки до ~ 75 мкм. Цей шар і що прилягають до нього ділянки стали істотно обезуглерожены. У структурі стали спостерігається мартенсит, кількість якого збільшується з видаленням від кратера. На глибині 300 — 400 мкм розташований повністю закалённый шар, далі - шар, закалённый не полностью.
У попередньо закалённых зразках зі сталі 45 утворився шар завтовшки ~ 400 мкм, що з обезуглероженной зони лежить на поверхні і вдруге закалённой всередині, причому тут мартенсит більш мелкоигольчатый, ніж у матриці. Далі розташовується зона відпустки з продуктами розпаду мартенсита.
Структурні проблеми в зразках з нормализованной і попередньо закалённой стали У8 багато в чому аналогічні змін структури в зразках з стали 45 із тією лише відрізняємо, що у предворительно закалённой стали У8 в зоні гарту, що прилягає до розплаву наявне істотне растравливание кордонів зерен. Зазначимо, що у обезуглероженных зонах має місце разупрочнение. Так було в стали У8 твердість у тих зонах приблизно 2 рази менше, ніж у вихідної структуре.
У зразках зі сталі ХВГ структурні зміни подібні змін у зразках зі сталі У8, з тією різницею, що у закалённом шарі, як й у закалённой матриці, спостерігаються періоди округлої форми. Також чітко прозирає столбчатая структура раніше розплавленого слоя.
Рассмотрим результати досліджень сплавів з урахуванням заліза після обробки які йшли променем потужних лазерів на СО2. Дослідили зразки з сталей 20, 45, У8, У12 після обробки їх променем лазера на СО2 з потужністю випромінювання до 1 кВт. Швидкість переміщення зразків змінювалася буде в діапазоні 0,4 — 0,6 м/мин. Щільність потоку у зоні обробки змінювалася не більше 5?103 — 2?105 Вт/см2. Області обробки складаються з чітко виражених верств, які один від друга ступенем повноти фазових превращений.
У першому шарі температура стали перевищує верхню критичну точку Ас3 чи Асm для доэвтектоидных і заэвтектоидных сталей, відповідно перевищувала температуру плавки сталі. Микростуктура цього — мартенсит.
Другий шар відповідає нагріванню в межкритическом інтервалі температур, тут відтворена неповна гарт. Для доэвтектоидных сталей вона дає внаслідок збереження ферритных зерен знижену твердість в порівнянні з цим шаром. Для заэвтектоидных сталей твердість другого шару вище, ніж першого. Це пояснюють присутністю цементита в высокодисперсном вигляді, який додатково упрочняет сталь. Твердість у зоні (Рис. 7) обробки стали 20 сягає 7500 мПа при переміщенні зразків з v = 0,6 — 1,8 м/мин, чого досягти звичайній загартованістю. У цьому глибина зони зміцнення дорівнює 500 мкм.
У зразках зі сталі У12 на другий зоні, зоні термічного впливу, спостерігається неоднорідність структури, що підтверджено зниженою травимостью ділянок, розташованих дома сітки вторинного цементита. Зазначені ділянки характеризуються збільшеним кількістю аустеніту. Аналіз кривих розподілу твердості в зразках з сткли У12 показує, що мінімальної швидкості переміщення зразка твердості першого і другого шарів зони близькі, тоді як пі вищих швидкостях твердість другого шару помітно вище. Ця обставина визначається більш рівномірним розподілом вуглецю в аустените за довше лазерного нагріву. Твердість мартенситу при змісті вуглецю до 0,6% лінійно залежить від нього та практично залежить від нього при великому кількості вуглецю в стали.
Досліджували зразки зі сталі 35 із вихідною ферритно-перлитной структурою. Після впливу випромінювання лазера на СО2 обробка супроводжується оплавленням поверхні до швидкості 2,4 м/мин, а при швидкостях переміщення зразків ~ 2,6 м/мин і більше оплавлення не спостерігається. Зона лазерного впливу при швидкостях переміщення зразків 0,6- 1,8 м/мин складається з чотирьох шарів. Перший, оплавлений шар характеризується зниженою травимостью і микротвёрдостью Нм = 8 000 мПа, перевищує твердість сталі у вихідному стані 4 разу. Мікроструктура цього є мартенсит та деяка кількість залишкового аустеніту. У другому шарі мікроструктура — мартенсит з голками площею 2 — 4 разу великим, порівняно з першим. Третій шар — зона неповною гарту зі структурою з мартенситу, троостита, феррита. Четверте шар є також зоною неповної гарту, проте відрізняється від третього в повній відсутності троостита, наявністю ферритной сітки і високої твёрдостью.
Розподіл твердості за глибиною зони, підданою лазерної обробці що за різних швидкостях переміщення променя наведено на рис. 1.5.
Спостережувані розбіжності у структурі та твердості шарів зони в стали 35, оброблюваної безперервним випромінюванням лазера на СО2, пояснюють різними умовами їх нагріву і охлаждения.
1.6. Зміцнення кулачка головного вала.
Протягом останніх трьох — п’яти з’явилися потужні газові лазери, щоб забезпечити як безупинної генерації потужність порядку кількох кіловат. Завдяки цьому можна було здійснювати нову технологічну операцію — термічну обробку металевих поверхонь. Особливо важливо в обробці таких поверхонь, де потужний лазерний промінь має переваги чи де геометрія оброблюваних виробів створює труднощі, щоб застосування традиційного теплового методу. Лазерна обробка застосовується для гарту сталевих поверхонь, високошвидкісного отжига фольги, видалення плівок та інших поверхневих осаждений, і навіть вникания порошкового матеріалу в металеву поверхность.
Освіта тонкого твердого поверхневого шару сталі шляхом її підігріву і наступного швидкого охолодження відіграє у багатьох технологічних операціях. Обрабатываемыми деталями може бути зубчасті колеса, шпоночные канавки, зубчасті муфти, розподільні вали, кінці пальців штовхача, ножі різних машин, і навіть даний на зміцнення кулачёк. Оскільки припустимий знос сталі є малою величиною, то збільшення терміну служби кулачка досягається рахунок створення поверхового шару. Однією із поважних особливостей поверхового зміцнення є збереження якості основної маси металу, що також розігрівається разом із поверховим слоем.
Для кулачка головного валу основним процесом при загартуванню є нагрівання поверхні до температури, коли він зникає аустенитная структура. У цьому вуглець починає існувати як твёрдый розчин карбіду заліза в гамі заліза. Потім відбувається охолодження до температури, коли він не встигне утворитися стійке стан перліту з ферритом чи цементитом, а утворюється дуже міцний, твёрдый розчин карбіду в? — залозі, відомого як мартенсит. Необхідна швидкість охолодження залежить від складу сталі та має значення порядку 30 — 40 градусів до того часу, поки температура не досягне порядку 250 градусів. Для отримання зазначеної швидкості охолодження застосовують охолодні жидкости.
При лазерної загартуванню кількість енергії, спрямовані на метал, є достатнім для поверхового нагріву, а маса металу кулачка залишається холодної. І тут нагріта поверхню охолоджуватиметься рахунок теплопровідності з досить високої скоростью.
Для гарту кулачка зі сталі 18 ХГТ, застосуємо загартування за нормальної температури 780 — 800 градусів з наступним охолодженням. Лазерний промінь діаметром 5 мм, перемещаем поверхнею зі швидкістю 1,4 м/мин. Використовуємо безперервний СО2 — лазер потужністю 2,8 кВт. Під час такої обробці поверхневий пласт в результаті подвійного проходу променя СО2 — лазера став у тричі выше.
Температурну обробку кулачка можна робити у різних середовищах (вода, повітря, різні гази). Більше високе зміцнення стали має місце при її обробці в рідких средах.
При вплив імпульсу випромінювання на шлифовальную поверхню кулачка виникає вузька зона розплавленого металу, микротвёрдость якої відмінна від микротвёрдости основного металу. На поверхні микротвёрдость становить Н50 = 350, збільшується вглиб обьёма матеріалу, досягаючи Н50 = 450. У зоні термічного впливу микротвёрдость збільшується до Н50 = 45 год 500 і зменшується далі вглиб металу до Н50 = 158, та був микротвёрдость повертається до вихідному значению.
Повний цикл термообробки вимагає 1 — 2 з. Максимальна глибина упрочнённой лазером зони 1 — 2 мм. Такий глибини достатньо підвищення зносостійкості, міці й усталостной сопротивляемости.
Звичайні методи гарту, такі як поверхнева гарт часто викликають знеформлення металу, що необоротно псує виріб чи потребує великих витрат за доводку.
Цементація і азотування поверхні займають чимало часу, їм визначена висока щільність підтримки газового складу. Не можна обробляти великі площі. Спотворення кулачка також мінімальне в порівнянні коїться з іншими методами.
У порівняні з іншими джерелами тепла геометрія лазерного променя легко змінюється оптичними системами. Лазерний промінь передається на відстань, фокусується чи розширюється спеціальними лінзами. Таким чином, діаметром променя можна управляти дистанційно. Його навіть можна розділяти одночасно різні ділянки кулачка.
Гарт не вимагає спеціального охолодження. Поверхня обробленого кулачка залишається чистой.
2. КОНСТРУКТОРСЬКА ЧАСТЬ.
2.1. Призначення вузла «вал головний» автомата хладновысадочного.
Автомат хладновысадочный призначений виготовлення деталей з дроту методом холодної висадки. Автомат хладновысадочный складається з таких засадничих вузлів: головного валу, вузла подачі дроту, вузла подачі ножа, вузла висадки заклёпки, вузла відтинки, приводу, станини, електроустаткування, огорожі, разматывающего устрою, вузла правки і пневмооборудования.
Головний вал автомата хладновысадочного встановлюється на підшипниках до корпусу 1 (див. збір. чертёж). З правого боку валу кріпиться кулачёк 4 і шків 3, з другого боку в пазу валу 2 кріпиться ексцентрик 5. На ексцентрики 5 встановлюється підшипник 65 з хомутом 9 (див. Г-Г) і держатель 6 (див. А-А). У пазу держаки 6 кріпиться болт 10, у якому закреплён підшипник 64 з обоймою 15 (див. Д-Д).
Головний вал отримує обертання через клиноременную передачу від приводу і приводить у рух інші вузли: у вигляді кулачка 4 переміщається шток вузла відтинки дроту; опора 7, закреплённая на хомуті 9 (див. Г-Г), переміщає повзун вузла висадки заклёпки; обойма 15 через тягу повертає обгонную муфту вузла подачі дроту. Значимість ходу повзуна вузла висадки заклёпки регулюють шляхом переміщення ексцентрика 5 в пазу валу 2, а кут повороту обгонной муфти — переміщенням болта 10. Подачу дроту здійснюють двома роликами, які на плиті станини верстата. При робочому ході заготівля з дроту висувається в матрицю і опрессовывается; отримана заклёпка виштовхується пуансоном, який впливає завзята планка, далі заклёпка скидається під впливом кулачка на важіль вузла сбрасывания.
2.2. Вибір способу зміцнення кулачка головного вала.
Для збільшення твердості і зносостійкості деталей складної конфігурації, і навіть зниження собівартості деталі піддають зміцнення методом лазерного впливу, зміни властивостей поверхового шару, що врешті-решт дає можливість виготовляти деталі з більш дешевого сырья.
Зміна властивостей поверхневих шарів матеріалу з допомогою лазерного випромінювання можна робити внаслідок насичення поверхні легирующими елементами (Сr, A, B, C). Ці елементи, розчинившись переважно металі, в поєднані із ним утворюють новий шар особливими свойствами.
У порівняні з раніше відомими способами (азотування, цементація, наплавление та інших.) модифікація поверхні легированием при локальному лазерному нагріванні і високих швидкостях плавлення і кристалізації має цілу низку преимуществ:
— економією легирующего материала;
— мінімальний обсяг наступної механічної обработки;
— відсутністю потреби у наступної термообработке;
— досить хорошою контролируемостью процесса;
— високої швидкістю процесу високим якістю изделия;
— хорошою воспроиводимостью параметрів упрочняемого шару і др.
Процес лигирования дає змогу отримувати лежить на поверхні деталей з вуглецевих матеріалів микрообъёмы нових сплавів із наперед заданими властивостями і підвищуватиме їхній теплостойкость до 300 — 400 градусів. Рекомендується для поверхового легування вживати такі дешеві матеріали, як наприклад стали У розділі ст. 3, 45, У8А, У10А, і поверхні деталей, інструмента, виготовлених із них створювати микрообъёмы зі властивостями, зумовлені властивостями деталі, інструменту та т.п.
Поверхню матеріалу легуючий елемент наноситься різними способами:
— накочуванням (фольги з легирующего элемента);
— електролітичним осаждением;
— детонационным покрытием;
— плазмовим напылением;
— нанесенням обмазки і зв’язувальної речовини і т.д.
Лазерне термоупрочнение сталей полягає у формуванні на етапі нагріву аустенитной структури та її наступному на мартенсит на етапі охлаждения.
При лазерної обробці без оплавлення вирішальної стадією є нагрівання, т.к. при наступному высокоскоростном охолодженні фіксується перетворення при нагріванні. При нагріванні сплавів заліза у точці Ас1 діаграми стану залізо — вуглець починається перетворення перліту в аустенит.
Високошвидкісний нагрівання, характерний лазерної обробки, змінює кінетику освіти аустеніту. Подводимая теплова енергія перевершує по величині енергію, необхідну перебудови кристалічною ґрати, а сама перебудова приміром із деякою кінцевої швидкістю. У результаті цього перетворення здійснюється не изотермически, а деякому інтервалі температур від Ас1нач до Ас1кон, тобто усунення кінця аустенитного перетворення на область високих температур (рис. 2.1 область 1).
[pic].
Рис. 2.1. Діаграма стану Fe — Fe3 P. S У результаті високу швидкість нагріву диффузионные процеси перебудови ґрати объёмноцентрированного куба надлишкового феррита в грати гранецентрированного куба надлишкового аустеніту можуть закінчитися на лінії GS діаграми Fe — Fe3 P. S й відбувається зрушення точки Ас3 до області більш високих температур (рис. 2.1. область 2). Також усунення точки Асм і обумовлене цим микроплавление кордону цементита з аустенитом (рис. 1.4, область 3).
У розглянутих випадках процес диффузионного перерозподілу вуглецю в аустените, тобто гоиогенизация аустеніту, зміщується до області ще більше високих температур.
Лазерна обробка вирізняється малою часом впливу, внаслідок чого не встигає статися укрупнення зерна. Однак процес лазерного легування прагнуть здійснювати з нагріванням до максимально можливої температури, до температури плавлення із єдиною метою отримати достатню глибину упрочнённого слоя.
Обробка без оплавлення поверхні призводить до утворення неоднорідною аустенитной структури з наявністю у верхній частині зони впливу мартенситу, обумовленого закритическими швидкостями охолодження. Микротвёрдость оплавленого шару поповнюється 4000 мПа. Поруч із дифузією в рідкої фазі насичення поверхні лигирующими елементами реалізується також і шляхом дифузії в твердої фазі. З початком дії променя лазера на матеріал поблизу кордону руйнації виникає тонкий шар рідкого металу, товщина якого тим менше, що стоїть інтенсивність излучения.
Вузький шар розплавленого сплаву лежить на поверхні матеріалу то, можливо у процесі впливу променя лазера обогащён чи обеднён лигирующими елементами проти вихідним сплавом через різною пружності парів легирующего елемента і основного металу. Більшість легуючих елементів енергія зв’язку в сплаві нижче відповідної енергії зв’язку основного метала, що припадає на атом сплаву. Тому, за русі кордону руйнації можливо випаровування як атомів, що є лежить на поверхні кордону руйнації, а й частини домішкових атомів з шару деякою товщини з яких забезпечується перехід домішок до кордону руйнації. Товщина цього близька до товщині шару поглинання світлового випромінювання в металах, де ефективні температури і тиск дуже високі, і як наслідок коефіцієнт дифузії істотно увеличивается.
Швидкість рухливості легуючих елементів визначається температурою в рідкої фазі, часом зіткнення між твердої і переробки рідкої фазами, фізичної природою домішкових атомів і концентрацією домішок. Для великої кількості елементів, розчинність в рідкої фазі вище, ніж у твердої, тому перед кордоном рідкої фази утворюється шар зниженим змістом домішок. Після закінчення дії випромінювання припиняється рух кордону розділу рідка фаза — твёрдая фаза, і розпочинається кристалізація тонкої плёнки.
Саме тоді випаровування із поверхні перестає мати значення. Тож за мері кристалізації спостерігається зворотний перехід частини домішкових і легуючих атомів до зони, прилеглу до кратеру. Це має спричинить вирівнюванню числа домішкових атомів у зоні поблизу кратера, хоча повної компенсації недостачі легуючих домішок може і не через те, що температура у зоні обробки неістотно перевищує температуру плавления.
Отже, вихідного розподілу легуючих домішок у зоні, що прилягає до кратеру, має бути відмінно від кінцевого. Диффузионная глибина істотно залежить від температурного поля була в зоні кратера. У неперервному зв’язку з цим процес зміни змісту елементів при дії випромінювання лазера на метали то, можливо розбитий сталася на кілька стадий.
Перша стадія — нестаціонарний процес, що призводить до встановлення квазистационарного розподілу температури у зоні кратера. Наступна стадій — квазистационарный процес руйнації, у якому температурное полі матеріалу вважатимуться що встановилася. І на цій стадії відбувається встановлення диффузионного процесу накопичення домішок в рідкої плівці, пов’язаної з зоні обробки, чи її домішками, у вищій стадії процесу, відповідної кристалізації тонкої плівки розплаву після закінчення дії випромінювання, відбувається зворотний перенесення домішок з рідкої в тверду фазу, тобто збагачення поверхневого шару легирующими элементами.
При легировании СО2 — лазером потужністю 1 кВт, діаметр плями 0,59 — 1,8 мм швидкості сканування 12,7 год 1270 см/мин, час наплавления металу у даної точці вбирається у 0,1 год 1,5 с.
Приблизно стільки ж становить час кристалізації металу. На процес перемішування впливають високі градієнти температур, дію ударної хвилі тощо. Глибину проплавления можна змінювати від 0,05 до 5 мм, а ступінь легування не більше від 0,1 год 1 до 0,81 год 1.
2.3. Пристосування для упрочнения.
Поверхня деталі є складну геометричну форму. Це з конструктивної особливістю верстата. Від головного валу обертальне рух кулачка передається в возвратно-поступательное рух штока приводу вузла відтинки деталі автомата холодновысадочного. У результаті цієї роботи зносу піддається профіль кулачка.
Для збільшення терміну служби деталі ми розробили пристосування для лазерного легування (борирование) складного профілю кулачка на установці «Кардамон».
Пристосування є систему копіювання профілю кулачка. На устрої копіювання закріплена лінза, призначена для фокусування лазерного променя, з допомогою якої під час обертання кулачка і, відповідно, копіра витримується однаковое фокусне відстань до деталі діаметр плями залишається незмінним. У нашому випадку діаметр сфальцьованого променя становить dл = 2 мм; швидкість променя vл = 5 мм/с.
Произведём розрахунок довгі окружності кулачка, беручи до уваги плавні переходи його профиля:
З = ПD = 2ПR.
Разом Собщ = 402,1 мм.
Переведемо швидкість променя в одиниці СИ:
V = 5 мм/с = 5? 60/1000 = 0,3 м/мин.
Тоді частота обертання оброблюваної деталі составит:
[pic].
Виходячи із знайденою частоти обертання оброблюваної деталі лазером, спроектируем редуктор пристосування для лазерної обробки. Від електродвигуна у вигляді червячной передачі рух передається безпосередньо оброблюваної деталі, а у вигляді циліндричною прямозубой передачі рух передається на копір, який підіймає планку з лінзою, і ходовий гвинт для переміщення деталі щодо лазерного луча.
Проведемо розрахунок редуктора:
Він з червячной передачі й двох циліндричних прямозубых передач. Рух червячной передачі передається від безконтактного (крокового) моментного електродвигуна серії ДБМ-185−10−0,04−2, розвиває пускової момент щонайменше 7,8 Н? м, з кількістю пар полюсів — 8. Застосування силового крокового приводу для двигуна спрощує схему управління і дозволяє забезпечити регулювання частоти від 0,6 до 1 кГц, відповідно, і частоти обертання ротора крокового двигателя.
Розглянемо червячную передачу.
ККД червячной передачі з урахуванням втрат надходжень у опорах: [pic]. Передатне число однакову передатному відношенню [pic], причому І = 15.
Кількість витків черв’яка Z1 приймаємо залежно від передатного числа при І = 15, приймаємо Z1 = 2 [з. 55. (1)].
Кількість зубів червячного колеса:
Z2 = Z1 * І = 2 * 15 = 30.
Приймемо стандартне значення [т. 4.1 (1)].
Z2 = 32 у своїй І = Z2 / Z1 = 32 / 2 = 16.
Вибираємо матеріал черв’яка і віденця червячного колеса. Приймаємо для черв’яка сталь 45 з загартованістю до твердості щонайменше НRCэ 45 і наступному шлифованием.
Оскільки до передавання не пред’являються спеціальні вимоги, то цілях економії приймаємо для віденця червячного колеса бронзу БрА9ИСЗЛ (виливок в піщану форму). При тривалої роботі контактне напруга [Cн] = 155 МПа. (т. 4.9).
Допускаемое напруга вигину при реверсивною работе:
[СOF] = КFL [СOF]'.
У цій формулі КFL = 0,543 *98 = 53,3 МПа.
Поводить момент на валу червячного колеса:
[pic].
Приймаємо попередньо коефіцієнт діаметра черв’яка q = 10.
Визначаємо межосевое відстань з умов контактної выносливости:
[pic], де до= 1,2 — коефіцієнт нагрузки.
Модуль [pic].
Приймаємо по ГОСТ 2144–76 (табл. 4.2) стандартні значення m і q [pic].
Основні розміри червяка:
Ділильний діаметр черв’яка: d1 = q * m = 10 * 6,3 = 63.
Діаметр вершин витків черв’яка: dв1 = d1 + 2m = 63 + (2 *6,3) = 75,6 мм.
Діаметр западин витків черв’яка: d=d1 — 2,4 m = 63 — (2,4 * 6,3) = 47,88 мм.
Довжина нарізаною частини шліфованого черв’яка: в1 > (11 + 0,06 Z2) * m + 25 = (11 + 0,06 * 32) * 6,3 + 25 =106,4 мм.
Приймаємо в1 = 106 мм.
Ділильний кут підйому витка? при Z1 =2 і q = 10,.
? = 110 19'.
Основні розміри віденця червячного колеса:
Ділильний розмір червячного колеса: d2 = Z2 * m = 32 * 6,3 = 201,6 мм.
Діаметр вершин зубів червячного колеса: dв2 = d2 +2m = 201,6 + 2 * 6,3 = 214,2 мм.
Діаметр западин зубів: d = d2 — 2,4 m = 201,6 — 2,4 * 6,3 = 186,5 мм.
Найбільший діаметр червячного колеса: dам2 < dв2 +6m / Z1+2 = 214,2 + (6 * 6,3) / (32*2) = 215,3 мм.
Ширина віденця червячного колеса: в2 < 0,75 dв, = 0,75 * 75,6 = 56 мм.
Окружна швидкість червяка^.
[pic].
Перевірка міцності зубів червячного колеса на изгиб:
Коофициент форми зуба по табл. 4.5 [1].
YF = 2,32.
Напрям изгиба:
[pic] що менше обчисленого выше.
[COF] = 53,3.
Перейдём до розрахунком циліндричною прямозубовой звичайною зубчастою передачи.
Передатне ставлення, і = 1.
Частота обертання провідною шестерні n= 0,746 об/мин.
Поводить момент на провідному валу.
Т3 = Т2 = 256,4 * 103 М * м.
Вибираємо матеріал для зубів коліс. Для шестерні сталь 45, термообробка — поліпшення, твердість НВ = 230, для колеса сталь 45, термообробка — поліпшення, МВ 200.
Допущені контактні напряжения:
[pic].
[pic] - межа контактної витривалості при базовому числі циклів. По табл. 3.2 для вуглецевих сталей з твёрдостью поверхні зубів менш НВ 350 і термообработкой (улучшением).
[pic] = 2НВ +70.
Для шестерни:
[pic] = 2 * 230 + 70 = 530 МПа.
Для колеса:
[pic] = 2 * 200 + 70 = 470 МПа.
КHL = 1- коефіцієнт долговечности.
[Sн] = 1,10 — коэф. безопасности.
Для шестерні [pic].
Для колеса [pic].
Расчётное дозволене контактне напряжение.
[Сп] = 0,45 (481,8 + 427,3) = 409 МПа.
З компонування редуктора приймаємо межосевое відстань dw = 200 мм з стандартного низки чисел.
Нормальний модуль зачеплення приймаємо mn = 0,01 * dw = 0,01* 200 = 2 мм.
Кількість зубів шестерні і колеса будут:
[pic].
Уточнимо модуль.
[pic].
Основні розміри шестерні і колеса:
Ділильні діаметри: d1 = d2 = mn * Z1,2 = 2 * 100 = 200 мм.
Діаметр вершин зубів: dа1 = dа2 = d1 + 2mn = 100 + 2 * 2 = 104 мм.
Ширина колеса: в2 =? ва * dw = 0,4 * 200 = 80 мм.
Ширина шестерні: в1 = в2 + 5 мм = 85 мм.
Коефіцієнт ширини шестерні по диаметру:
? вd = в1 / d1 = 85 / 80 = 1,06.
Окружна швидкість коліс і рівень точності передачи.
[pic].
де [pic].
Під час такої швидкості коліс варто прийняти 8- ю ступінь точності ГОСТ 1643–81.
Коефіцієнт нагрузки:
Кн = Кн? * Kн? * Kнv.
Кн? = 1,10 при НВ < 350 [табл. 3.5 [1]].
Kн? = 1,16; Kнv = 1.
Кн = 1,10 * 1,16 * 1 = 1,276.
Перевірка контактних напряжений.
[pic].
Аналогічно здійснюватися розрахунок другий циліндричною звичайною зубчастою передачі пристосування для лазерного борирования.
Розроблена нами схема пристосування забезпечує необхідну частоту обертання оброблюваної деталі, а як і переміщення променя у всій оброблюваної поверхности.
Застосування крокового двигуна в пристосуванні дозволяє значно спростити його кінематичну схему.
Універсальність крокового двигуна у тому, що з роботу його з дискретним розімкнутим приводом, можливо, регулювати швидкість методом часткового регулювання швидкості до нуля.
[pic].
Рис. 2.2. Схема пристосування для лазерного борирования.
1. Зеркало.
2. Линза.
3. Кулачёк.
4. Ползун.
5. Плита.
6. Стойка.
7. Пружина.
8. Редуктор
[pic].
Рис. 2.3. Схема разомкнутого приводу з силовим ШД.
ДІ - генератор импульсов;
РІ - розподільник импульсов;
РОЗУМ — підсилювач мощности;
ПН — перетворювач напряжения;
МС — негативна зв’язок по току;
ШД — кроковий двигатель.
На рис 1.8. показано схема разомкнутого приводу з силовим шаговым двигуном. Воно складається з задає генератора імпульсів, розподільника імпульсів, перетворюючого однополярные напруги у трьох фазні системи, підсилювачів потужності, які живилися від широтно — імпульсного перетворювача напруги харчування ПН з жорсткої негативною зв’язком по току ТС.
Такі системи з розімкнутим шаговым приводом мають найпростішу структуру й у справжні час набули найбільшого поширення. Вони йдуть на управління металорізальними верстатами, газорезательными і зварювальними автоматами, координатографами, лентопротяжными і реєструючими пристроями, дистанційними передачами тощо. У цих системах дискретний вхідний сигнал надходить на кроковий привід і відпрацьовується двигуном в вигляді кутового перемещения.
Перейдём до розгляду лазерної установки «Кардамон», призначеної для поверхового зміцнення і наплавки металів і сплавів. Максимальне значення щільності потужності, достигаемой при фокусуванню випромінювання такого лазера становить 104 — 105 Вт/см2.
Установка «Кардамон» (Рис. 1.9.) складається з чотирьох газорозрядних труб довгою 6,5 м, розміщених в жорсткої сталевої трубі діаметром 53 див, оптично з'єднуються шістьма повністю що відбивають дзеркалами. Дзеркала кріпитися у спеціальних водоохлаждаемых гнёздах. Радіуси кривизни цих дзеркал 24 метри. У центральній частині труб розміщені безразрядные проміжки. Установка дбає про суміші газів (вуглекислого, азоту NO та гелю) з повільної прокачуванням газової суміші. Потужність безперервного випромінювання 800 Вт.
Зовнішньої оптичної системою лазера випромінювання фокусується в пляма діаметром від 2 до запланованих 4 мм. Висока локальна щільність енергії потоку дає змогу виробляти такі термічні операції у поверхні детали:
1) Гарт поверхневого шару нових деталей на глибину до 0,5 мм. Режим гарту забезпечується рухом деталі зі швидкістю 5−10 мм/с. [pic].
Рис. 2.4. Принципова схема установки «Кардамон».
1 — робоча камера; 2- дзеркало; 3- лінза; 4 — деталь; 5- газова система; 6 — пульт управління; 7 — генератор напруги; 8 — насосна система; 9 — пристосування; 10 — плита.
Пристрій подачі деталі під промінь забезпечує обертальне і поступальний спрямування широкому діапазоні скоростей.
2) Легування поверхні деталі бором. Режим легування забезпечується при швидкостях 5−10 мм/с. Застосовується нових деталей.
3) Оплавлення попередньо нанесённого на изменённую деталь порошкового шару завтовшки до 0,5 мм. Режим оплавлення забезпечується при швидкостях 4−5 мм/с.
2.4. Технологія упрочнения.
На розробку здійснення технологічного процесу лазерного борирования вирішити наступний комплекс взаємозалежних задач:
1) Виявити основні допоміжні режими обработки;
2) Виявити взаємозв'язок параметрів із елементами упрочненной поверхні материалов;
3) Розробити оптимальну схему обробки поверхности;
4) Вибрати оснастку;
5) Розробити схему базування деталі під лучом;
6) Вибрати обмазочные матеріали, які збільшують поглинання лазерного випромінювання, і кошти їх нанесения;
7) Забезпечити максимальну продуктивність процесу шляхом його механізації і автоматизации.
Технологія безперервного лазерного борирования має низку переваг по порівнянню з імпульсної лазерним обробленням. По-перше, немає обмеження з тривалості лазерного впливу. Це дозволяє продуктивність і геометричні розміри зміцнених зон, соціальній та ширшому інтервалі змінювати структуру й властивості зони обробки, так як можна здійснення процесу, і з плавленням, і без плавлення поверхні. По-друге, за довжиною усталених смуг немає зон багаторазового нагріву, і, отже, є можливість збільшення рівномірності властивостей по поверхности.
Що стосується застосування безперервного лазерного впливу необхідно вживати заходів до підвищення поглинання излучения.
До основними параметрами безупинної лазерної обробки относятся:
— потужність випромінювання (Вт);
— діаметр плями нагріву (мм);
— швидкість переміщення променя по деталі (мм/с).
Висока ефективність лазерної обробки буває у разі застосування спеціальних поглинаючих покриттів, які завдавав на поверхню деталі на місці її обработки.
Ця деталь обробляється безупинно, тобто промінь ковзає по поверхні постійно з певним діаметром плями. Це забезпечується тим, що лінза перебуває щодо деталі завжди однією відстані, т.к. фокус не меняется.
Закінчують процес лазерної обробки відновленням. Відновлення включає у собі промивання деталей від багна й олії; механічну обробку зношеною поверхні з допомогою шліфувальних машин; напилювання порошкового матеріалу; установку деталі в пристосування; установку режимів праці та швидкісних режимов.
3. ДОСЛІДНИЦЬКА ЧАСТЬ.
3.1. Лазерна обробка на CO2 — лазере.
Як засіб зміцнення, враховуючи вищевикладений матеріал і аналізуючи його пропонується лазерне легування (борирование) з застосуванням СО2 — лазера.
При лазерному борировании нормализованной стали марки 40Х безперервним випромінюванням СО2 — лазера у зоні оплавлення утворюється мелкодисперсный реечный мартенсит з микротвёрдостью 7000 — 8500 МПа.
Зона гарту без оплавлення складається з верхньої області, з однорідної структурою. У верхньої області формується мартенсит з микротвёрдостью, як у зоні оплавлення. У нижньої області з глибині не збільшується неоднорідність внаслідок і последовательности:
— мартенсит — тростит;
— мартенсит і тростичня сетка;
— тростично — ферритная сетка;
— феррит.
При лазерному борировании використовуємо СО2 — лазер з обрабатывающеё голівкою (лінзою). Поверхнева обробка здійснюється розфокусованим пучком — подвійний перехід із перекрывающимися краями. Обробку ведемо з допомогою сконструйованого нами пристосування методом копирования.
3.2. Випробування матеріалу на износ.
Випробування матеріалу — сталь 40Х (ГОСТ 1050−88) проводимо машиною СМЦ — 2. Машина варта випробування матеріалів до зносу та засобами визначення їх антифрикційних властивостей при терті ковзання і терті качения, при нормальних температурах з парами зразків диск — диск, диск — колодка і втулка — вал.
Машина моделі СМЦ складається з таких узлов:
1) Каретка — варта проведення випробувань без мастила и.
СО-смазкой з образцами:
— диск по диску при терті качения з проскальзыванием;
— дискколодка при терті скольжения.
2) Механізм навантаження призначений для установки зразка і мережеві додатки нагрузки.
3) Бабуся нижнього зразка варта установки зразка в каретку.
4) Датчик для виміру крутящего моменту (моменту тертя) машиною. Безконтактний індуктивний датчик і двох частин обертання ротора і статора (неподвижного).
5) Прихід електромеханічний зі східчастим регулюванням скоростей.
6) Пульт управління — виконується окремим вузлом, що можна встановлювати отдельно.
Машина СМЦ може працювати з двох схемам:
1) З замкнутим кинематическим контуром при фіксованому значенні коефіцієнта проскальзывания зразків у парі тертя диск по диску.
2) З відкритим кинематическим контуром, коли один зразків нерухомий, зокрема, за схемою вал — втулка.
Принцип роботи у обох випадках у тому, що зразки отримують відносне рух при заданої навантаженні. Водночас зношуються, а момент тертя на валу нижнього зразка вимірюється і записується. Машина не забезпечує безпосереднє вимір зносу у процесі испытания.
У нашому випадку випробування проводитимемо з круглими зразками «диск по диску» без смазки.
Встановлюють верхній і нижній зразки. Нижній зразок встановлюють на валу, верхній встановлюють, і зміцнюють іншою при відтягнутої у робочий становище каретці. Затягування зразків повинна бути достатньою, щоб уникнути проскальзывания при работе.
Після установки зразків каретку опускають до їх дотику. Вдягають навантажувальну скобу на кронштейн.
3.3 Дослідження зносостійкості покрытия.
Зразки піддавалися у протягом години при навантаженні 750 М, роблячи у своїй 30 000 оборотів. Матеріалом для робочого тіла служила сталь ШХ-15, твёрдостью 62…64 НRcэ.
Для перевірки процесу зношування при зовнішньому терті застосовують величину, званої інтегральної масової інтенсивністю изнашивания.
[pic].
(m — зменшення маси деталей внаслідок зношування поверхности;
? — шлях тертя, у якому стався износ;
Аа — номінальна площину зношування, площа контакта.
Натомість:? = Пdn; Аа = 0,1 (м2); де d = 38 мм; n = 30 000 про; P. S = 10−5 м2.
Перевіримо зразки зі сталі 40Х з різною термообработкой на износостойкость:
1) Сталь марки 40Х гарт + високий отпуск.
(m = 0,212 грн = 0,212 * 10−3 кг;
? = Пdn = 3,14 * 38 * 10−3 * 30 000 = 3579,6 м;
Аа = 0,1 * P. S = 0,1 * 10 * 10−3 * 10−3 = 10−6 м звідси J1 = 0,212 * 10−3 / 3579,6 * 10−6 = 0,059 кг/м3.
2) Гарт + низький отпуск.
(m = 0,102 * 10−3 кг;
J 2 = 0,0285 кг/м3.
3) Гарт + високий відпустку + лазерне борирование.
(m = 0,057 * 10−3 кг;
J 3 = 0,016 кг/м3.
4) Гарт + низький відпустку + лазерне борирование.
(m = 0,023 * 10−3 кг;
J 4 = 0,0064 кг/м3.
Результати досліджень зобразимо графічно на схемою зносостійкості покриттів і занесём в таблицю 3.1:
Таблиця 3.1. Зносостійкість покрытия.
|№ в. п |Термообробка стали 40Х |Маса зношеною |Інтенсивність | | | |поверхні (m * |зносу Jg, кг/м3 | | | |10−3 кг | | |1 |Гарт + високий відпустку |0,212 |0,059 | |2 |Гарт + низький відпустку |0,102 |0,0285 | |3 |Гарт + високий відпустку +|0,057 |0,016 | | |лазерне борирование | | | |4 |Гарт + низький відпустку + |0,023 |0,0064 | | |лазерне борирование | | |.
Вывод.
Після перевірки зразків у стали 40Х з різною термообработкой на зносостійкість, отримали максимальний результат при загартуванню з низьким відпусткою і лазерному борировании, де інтенсивність зносу составляет.
Jg = 0,0064 кг/м3.
.
4. ТЕХНОЛОГІЧНА ЧАСТЬ.
Ефективність виробництва, його технічний прогрес, якість своєї продукції великою мірою залежить від випереджаючого розвитку виробництва нового устаткування, машин, верстатів, апаратів, від всесвітнього впровадження методів техніко-економічного розвитку та аналізу, які забезпечують розв’язання технічних запитань і економічну ефективність технологічних разработок.
Прискорення НТП у машинобудуванні вимагає якнайшвидшого запровадження нових методів зміцнення робочих поверхонь інструмента, технологічної оснастки, деталей і творення механізмів, які працюють із великими нагрузками.
Необхідний постійний науковий пошуку нових і доопрацювання і вдосконалення вже випробуваних методів нанесення захисних і зміцнюючих покриттів, які за незначно дедалі більшого вартості інструмента, пристосування, і т.д., дають чималий економічний ефект, внаслідок багаторазового збільшення терміну службы.
4.1. Аналіз технологічності конструкції деталі «Кулачёк».
Технологическиё аналіз конструкції деталі забезпечує поліпшення техніко-економічних показників розроблюваного технологічного процесса.
Основні завдання, розв’язувані під час аналізу технологічності конструкції оброблюваної деталі зводяться до можливого зменшенню трудоёмкости і металлоёмкости, можливості обробки високопродуктивними методами, що дозволяє знизити собівартість її виготовлення без шкоди службового назначения.
Якісні оцінки технологічності конструкции:
1) Форма, точність ж розмірів та шорсткість поверхні, з погляду вибору методу отримання заготівлі та призначення поверхонь, які підлягають обробці резанием.
Використовуючи штамповану заготівлю, форма якої наближено до форми готової деталі, можна збільшити коефіцієнт використання металла.
2) Форма, точність ж розмірів та шорсткість поверхні, які підлягають обробці різанням, з погляду можливість застосування і продуктивних схем обработки.
Кулачок по зовнішньому профілю має складною конструкцією. Тому необхідно застосування спеціальних верстатів: копировально — фрезерного чи фрезерного верстата з числовим програмним управлением.
3) Доцільність термічної обробки щоб одержати необхідних прочностных характеристик детали.
Деталь у процесі експлуатації дбає про стирання профілем і внутрішньому діаметру (60Н7, у цій робочі поверхні можна піддати цементації із наступною загартованістю 57. 63 HRC ТВЧ.
Визначення типу производства.
Річна виробничу програму N = 1000 штук на рік, маса деталі становить 2,7 кг. Згідно з рекомендаціями [11] встановлюємо серійний тип производства.
У цьому виробництві виготовлення деталей здійснюється партіями, запускаемыми у виробництві одночасно. Це забезпечує повторюваність операцій та можливість використання спеціалізованого і спеціального устаткування, оснастки.
Розмір партії деталей определяется.
[pic], де t — число днів, куди необхідно мати запас деталей на складі при 5 — денний 2-х змінній робочого тижня задля забезпечення безупинної сборки;
[pic] - кількість робітників днів на рік. t = 8 — 10 днів [11] [pic] = 253 дня [11].
[pic],.
Вибір способу отримання заготівлі. Для умов виробництва вибираємо як заготівлі штампування на горизонтально кутої машині II класу точності. [1].
Розрахуємо масу заготівлі mз =? * vз, где.
? = 7,814 г/см3 — щільність металу [7] vз — Обсяг заготівлі, см3 vз = 3,14 * 8,02 * 2,6 + 3,14 * 6,052 * 0,6 — 3,14 * 2,82 *3,2 = 512,7 см³ mз =? * vз = 7,8 * 512,7 = 3998 грн = 3,998 кг.
Коефіцієнт використання металла.
Кім = mд / mз = 2,7 / 3,998 = 0,675.
Собівартість заготовки.
Sзаг = (З / 1000 * mз * Кт * Кс * Кв * Км * Кп) — (mз — mд) * Sотк / 1000, крб [5].
Ci = 18 900 руб/т вартість т заготівлі [5].
Sотх = 1788 руб/т вартість т отходов.
Кт, Кс, Кв, Км, Кп — коефіцієнти, залежать від класу точності, групи складності, маси, марки матеріалу і обсягу виробництва заготовки.
Кт = 1; Кс = 0,87; Кв = 1,14; Км = 1,18; Кп = 1.
[pic].
Рис. 4.1 Ескіз штампування Sзаг = (18 900/1000 * 3,998 * 1 * 0,87 * 1,14 * 1,18 * 1,0) — (3,998 — 2,7) * 1788/1000 = 86,2.
Маршрутний технологічний процесс.
000 Заготовительная.
Штамповка на ГКМ і зачистка від окалины.
005 Карусельно — фрезерная.
1 перехід фрезувати торець бобышки (130.
010 Токарная.
А Встановити в 3-х кулачковый патрон.
1 перехід підрізати торець начерно.
2 перехід підрізати торець начисто.
3 перехід розточити начерно.
4 перехід розточити начисто.
5 перехід зняти фаску 1×450.
015 Сверлильная.
А Встановити в приспособление.
1 перехід зняти фаску 1×450.
017 Сверлильная.
1 перехід центровать 4 отверстия.
2 перехід свердлитиме й зняти фаску.
3 перехід нарізати різьблення М8−6q на чотири отверстиях.
020 Копировально — фрезерная.
А Встановити на жорстку оправлення (60Н7.
1 перехід фрезувати зовнішнє контур
025 Слюсарна доведення профілю Ra = 0,8 мкм.
Розрахунок припуска +0,030.
Поверхня (60Н7.
Отвір обробляється чорновим розточуванням Н9 + 0,074.
Отвір обробляється чистовим розточуванням Н7 + 0,030.
Точність заготівлі +1,2 — 0,7 [10].
Додача розраховуємо аналітичним методом [10].
[pic].
[pic] - висота микронеровностей, що залишилися після виконання попереднього переходу, мкм.
[pic] - дефектний шар після попереднього переходу, мкм.
[pic] - сумарне значення просторових відхилень після попереднього переходу, мкм.
[pic] - похибка установки на виконуваному переході, мкм.
Черновое растачивание.
[pic] = 150 мккм; [pic] = 200 мкм;
[pic] = [pic], [pic] = 300 мкм [10].
[pic] - похибка усунення отвори, мкм.
[pic] - ексцентриситет отвори, мкм.
[pic] = 450 мкм; [pic] = 500 мкм; [10].
[pic] = [pic]=675 мкм.
Lt, min = 21 150 + 200 + [pic]=2 * 1090 мкм = 2180 = 2,2 мм.
Чистовое растачивание.
[pic] = 50 мккм; [pic] = 50 мкм; [10].
[pic] = 0,06 *[pic] = 0,06 * 675 = 40 мкм.
[pic] = 300 мкм [10].
Lt, min = 2150 + 50 + [pic]=2 * 402 мкм = 804 мкм = 0,8 мм.
Таблиця 4.1. Межоперационные розміри |Техноло|Элементы |Расчёт|Допус|Расчётн|Предельные|Прицельные | |р. |припуска, мкм |ный |до, мм|ый |розміри, |рипуска, мм| |перехід| |припус| |размер,|мм | | |и | |до, мм | |мм | | | |005карусельно-фрез|330 000 |10 |3,16 |1,48 |2 |1 |1 | |ерный 621 М | | | | | | | | |010 |315 000 |4,5 |3,0 |1,16 |2 |1 |1 | |токарно-револьверн| | | | | | | | |ый | | | | | | | | |015 свердлильний |230 000 |11 |1,42 |1,92 |2 |1 |1 | |2Г175 | | | | | | | | |020 |360 000 |7,5 |2,7 |2,17 |2 |1 |1 | |копировально-фрезе| | | | | | | | |рный 6М13К | | | | | | | |.
Оперативное час розраховується за формуле:
[pic], [pic] де [pic]- сума основного часу mпереходів, минуты;
[pic]- сума допоміжного часу mпереходів, минуты.
Тоді, оперативне час на операціях потоку: 005 карусельно-фрезерная [pic]мин; 010 токарная [pic]мин; 015 сверлильная [pic]мин; 020 копировально-фрезерная [pic]мин. Поштучна час визначається по формуле:
[pic] [pic] де авідсоток перерв України на технічне і організаційне обслуговування робочого місця, відпочивати та особисті потреби рабочего.
Тоді, поштучна час на операціях потоку: 005 карусельно-фрезерная [pic] хв; 010 токарная [pic]мин; 015 сверлильная [pic]мин; 005 копировально-фрезерная [pic]мин. Штучнокалькуляционное час розраховується за формуле:
[pic] [pic] де [pic]- подготовительнозаключне час, мин.;
Прозмір партії деталей, що визначається по формуле:
[pic][pic].
где [pic]- число днів, яким треба мати запас деталей складі, для легких деталей [pic]=5 дней.
Тоді, штучно-калькуляционное час на операціях потока:
005 карусельно-фрезерная [pic]мин; 010 токарная [pic]мин; 015 сверлильная [pic]мин; 005 копировально-фрезерная [pic]мин. Норма вироблення за зміну визначається по формуле:
[pic] [pic].
Тоді, норма вироблення на операціях потоку: 005 карусельно-фрезерная [pic]шт. 010 токарная [pic]шт. 015 сверлильная [pic]шт. 005 копировально-фрезерная [pic]шт.
Тривалість технологічного циклу при послідовнопаралельному вигляді руху предметів праці розраховується за формуле:
[pic][pic] де [pic][pic]- час суміщення між суміжними операціями потока:
[pic], [pic] де [pic]- час найбільш короткій з цих двох суміжних операцій; nрозмір партії деталей; pрозмір передавальної партії деталей. Тривалість операційного циклу визначається по формуле:
[pic] [pic] Тоді операційне час на операціях потока:
005 карусельно-фрезерная [pic]мин;
010 токарная [pic]мин;
015 сверлильная [pic]мин;
020 зубофрезерная [pic]мин;
5.2. Розрахунок собівартості виготовлення детали.
Собівартість продукції складається з витрат з наступним статтям калькуляции:
1) сировину й матеріали з відрахуванням отходов:
[pic][pic].
де [pic]- норма витрати матеріалу однією деталь, [pic]= 4,0 кг; приймаємо її рівної масі заготовки;
[pic]- маса деталі, [pic]=2,7 кг;
[pic]- вартість одного кілограма матеріалу, [pic]= 18,9 руб.;
[pic]- вартість одного кілограма реалізованих отходов,.
[pic]=1,8 руб.
2) допоміжні матеріали [pic]- нет.
3) енергія на технологічні нужды:
[pic][pic] де [pic]Мкількість машин;
[pic]- потужність електродвигуна, кВт (береться з таблиці 3.3);
[pic]- коефіцієнт завантаження електродвигуна по мощности;
[pic]- коефіцієнт одночасності роботи машин;
[pic]- ціна 1 кВт, [pic]= 1,13 руб;
[pic]- машинне час операцій потоку, часы.
4) вести виробничих робочих, включаючи додаткову зарплатню і відрахування на соціальні потреби — [pic] Основна вести робочих визначається по формуле:
[pic][pic].
где [pic]- норма обслуговування машин з кожної професії основних виробничих рабочих;
Мчисло машин кожної професії основних виробничих робочих; [pic]- коефіцієнт, враховує середній відсоток премії, [pic]=1,5; [pic]- годинна тарифна ставка робочих i-ой професії, [pic]фрезеровщика 5-го розряду = 19,3 крб.; [pic]токаря 4-го розряду = 17,45 крб.; [pic]сверлильщика 4 розряду= 17,2 крб.; [pic]зубофрезеровщика 5 розряду= 19,5 крб. [pic]- поштучна час виконання кожну операцію, часы.
Додаткова заробітна плата:
[pic] [pic].
Відрахування на соціальні нужды:
[pic].
Отже, вести виробничих робочих равна:
[pic].
5) амортизація устаткування й будинків [pic] розраховується за формуле:
[pic] де [pic]- амортизація устаткування, руб.;
[pic]- амортизація будинків, руб.
[pic] де [pic]- річна норма амортизації на повне відновлення i-го устаткування, [pic]=14%; [pic]- ціна одиниці i-го устаткування, крб. (береться з таблиці 3.3).
Знайдена сума амортизаційних відрахувань розрахована роком, тому необхідно перелічити в термін виконання замовлення — 20 дней:
[pic].
Тоді однією деталь:
[pic].
[pic].
где [pic]- річна норма амортизації на повне відновлення будинків, [pic]=5%; [pic]- ціна одного кв. м виробничої площі, крб. [pic]=4200 крб. [pic]- площа виробничого будинку, квадратні метры;
[pic] де lдовжина машини, метри, (береться з таблиці 3.3);
H — ширина машини, метри (береться з таблиці 3.3); a — проходи за довжиною, H=2 метри; h — проходи по ширині, h= 1 метр;
[pic]-коэффициент, враховує місця зберігання напівфабрикатів і тари, [pic]= 1,15.
Знайдена сума амортизаційних відрахувань розрахована роком, тому необхідно перелічити в термін виконання замовлення — 20 дней:
[pic].
Тоді однією деталь:
[pic].
Тоді амортизація устаткування й зданий:
[pic].
6) помешкання і утримання обладнання — [pic].
[pic] Тоді однією деталь: [pic].
7) цехові витрати — [pic].
[pic] 8) общефабричные витрати — [pic].
[pic].
Повна собівартість деталі, що складається з розрахованих вище витрат з статтям калькуляції, представленій у таблиці 5.4.
Таблиця 5.4. Повна собівартість продукции.
|Статья калькуляції |На одиницю |На обшир| | |продукції | | |1. Сировина і основні матеріали |73,26 |73 260 | |2. Енергія на технологічні потреби |3,09 |3090 | |3. Заробітну плату |21,48 |21 480 | |4. Амортизація устаткування й будинків |10,06 |10 060 | |5. Ремонт і змістом устаткування |12,5 |12 500 | |6. Цехові витрати |20,13 |20 130 | |7. Общефабричные витрати |6,71 |6710 | |Разом: повна собівартість продукції |147,23 |147 230 |.
Отже, повна собівартість продукції, розрахована за статтям калькуляції, дорівнює 147,23 рублей.
5.3. Техніко-економічні показники потока.
Техніко-економічні показники потоку і формули їх розрахунку представлені у таблиці 5.5.
Удільні капітальні видатки одиницю продукції, [pic] розраховується за формуле:
[pic].
З'їм продукції із першого [pic] виробничої площі, [pic]рассчитывается по формуле:
[pic].
Таблиця 5.5.
Техніко-економічні показники потока.
|Наименование показника |Ед.изм. |Значення | |1. Обсяг замовлення, [pic] |дет. |1000 | |2. Кількість машин, М |штук |4 | |3. Удільні капітальні видатки одиницю |руб./дет. |1453,7 | |продукції, [pic] | | | |4. З'їм продукції із першого [pic] виробничої |Дет/[pic] |20,6 | |площі, [pic] | | | |5. Собівартість одиниці виробленої продукції за статтями |Руб/дет. |147,23 | |калькуляції [pic] | | | |6. Прибуток від одиницю продукції, [pic] |Крб. |22,07 | |7. Ціна одиниці виробленої продукції, [pic] |Крб. |169,3 | |8. Обсяг реалізації, [pic] |Крб. |169 300 | |9. Термін окупності капітальних вкладень, |років |6,5 | |[pic] | | | |10. Фактичний коефіцієнт економічної | |0,16 | |ефективності капітальних вкладень, [pic] | | |.
Прибуток від одиницю продукції, [pic]определяется з рівня рентабельності продукції [pic]=15% по формуле:
[pic].
Ціна однієї деталі, [pic] буде равна:
[pic]=147,23+22,08=169,3 руб.
Обсяг реалізації, [pic]определяется по формуле:
[pic].
Термін окупності капітальних вкладень, [pic]определяется по формуле:
[pic].
Фактичний коефіцієнт економічну ефективність капітальних вкладень, [pic]определяется по формуле:
[pic].
Вывод.
У фундаменті економічної частини дипломного проекту було спрямовано основні параметри перериваного потоку, дозволяють найкраще організувати виробництво і труд:
. такт запуску деталі в хвилинах [pic]=9,6 мин;
. розрахункове і що ухвалене кількість робочих, з урахуванням часткового суміщення операцій на потоке;
. коефіцієнти завантаження робітників і оборудования;
. оперативне, поштучна, штучно-калькуляционное час операцій потока;
. норми вироблення з кожної операції потока;
. тривалість виробничого циклу виготовлення деталі при последовательно-параллельном вигляді руху предметів труда.
Собівартість виготовлення деталі, розрахована за статтям калькуляції, дорівнює 147,23 крб. Ціна одиниці виробленої продукції, розрахована з рівня рентабельності продукції, дорівнює 169,3 рублей.
Техніко-економічні показники роботи потоку свідчить про достатню ефективність його роботи: термін окупності капітальних вкладень 6,5 років, фактичний коефіцієнт економічну ефективність капітальних вкладень, [pic]=0,16.
6. БЕЗПЕКА ЖИЗНЕДЕЯТЕЛЬНОСТИ.
Безпека життєдіяльності - це комплекс заходів із забезпечення із гарантування безпеки життєвої діяльності в умовах виробництва. Охорона праці, є найважливішим розділом в безпеки життєдіяльності. Охорона праціце система законодавчих актів, соціально-економічних, організаційних, технічних, гігієнічних і лікувально-профілактичних заходів і коштів, які забезпечують безпеку, збереження здоров’я дитини і працездатність людини під час труда.
У цьому дипломному проекті розробляється технологічний процес виготовлення деталі «Кулачёк» головного валу на чотирьох станках:
1) Карусельно-фрезерный 621 М.
2) Токарно-револьверный 1416.
3) Свердлильний 2Г175.
4) Копіювально-фрезерний 6М13К.
Працюючи на верстатах робочі буде різним небезпечним i шкідливим чинникам. Оскільки ці чинники безпосередньо впливають на безпеку життєдіяльності виготовлення деталі у цьому дипломному проекті розробляється ряд заходів запобігання їх шкідливого впливу, дано рекомендації по правильному використанню та організації виробництва. До категорії 11б ставляться роботи з інтенсивністю енерговитрат 151−200 кал/2 (175−232 Вт), і навіть пов’язані із постійною ходьбою, переміщенням дрібних (до 1 кг) виробів стоячи чи сидячи і потребують певного фізичного напряжения.
Таблиця 6.1. Шкідливості й нерозумінням небезпеки проектованого производства.
|Наименование |Шкідливості, якщо мають місце відхилення від |Небезпеки | |технологічної |норм | | |операції верстата | | | |Підвищена |Органи дихання, кожный|Бронхит, астма, алергія, | |запиленість |покрив, слизова |дерматическая алергія, | | |оболонка |конъюнктивит | |Токсичні пари, гази, |Органи дихання, кожный|Отравление, пухлини шкіри, | |пил |покрив, слизова |опіки, дерматит | | |оболонка | | |Перенагревание |Весь організм |Тепловий удар | |Недостатня |Органи зору |Послаблення зору | |освітленість | | | |Наявність |Органи дихання, кожный|Заболевания органів | |мікроорганізмів і |покрив, |подиху і ін., алергія, | |бактерій | |виразки та інших. | |Підвищений шум |Органи слуху |Глухота, ослаблення слуху | |Підвищена вібрація |Весь організм |Виброболезнь, підвищення | | | |артеріального тиску | |М'язове переутомление|Весь організм |Плоскостопість, розширення | | | |вен, викривлення | | | |хребта |.
Таблиця 6.3 Значення нормувальних показників виробничої середовища |Чинники, |Нормируемые |Вигляд нормативного |Чисельні | |характеризующие|показатели, единицы|документа його |значення | |умови праці |виміру |номер |показника | |Запиленість |ГДК пилу, м2/м3 |ГОСТ | | | | |12.1.005−88 |6 | |Параметри |Оптимальні |Сан. ПиН |Для робіт | |мікроклімату |значення |2.2.4.548−96 |категории11 а | | | | | | | | | | | | |Температура, З° | | | | |t поверхонь, З° | | | | |Вологість, ?, % | | | | |V повітря, м/с | | | | | | |теплий |холодний | | | | |період | | | | | | |період | | | | |18−20 | | | | |17−19 | | | | |18−21 | | | | |16−20 | | | | |40−60 | | |Допустимі значення| | | | |t повітря, З° | |16−27 | | |t поверхонь, З° | |15−22 | | |Вологість, ?, % | |17−28 | | |V повітря, м/с | |16−24 | | | | |15−75 | | | | |15−75 0.1−0.4 | | | | |0.1−0.3 | |Підвищений шум |Рівень звукового |ГОСТ | | | |тиску, L, дБ |12.1.003−83 | | | | |з доп. 89 | | | | |CH 2.2.4/2. 1.8. |80 | | | |566−96 | | |Вібрація |Рівень |ГОСТ | | | |виброскорости, |12.1.003−90 | | | |Lv, дБ місцевої |СH 2.2.4/2. 1.8. |109 | | | |566−96 | | | | | | | | |загальної | |92 | |Висвітлення |Освітленість, |СниП 23−05−95 | | | |Е, лк |Міжгалузеві |1500 | | |коэф.пульсации |правила по ВІД |10−20 | | |Кп,% |при холодної |20−80 | | |Показник |обробці металів| | | |засліплення, | | | | |Росл.,% | | |.
Таблиця 6.4. Кошти індивідуальної захисту органів зору дихання, які видано рабочим.
|Наимен|Виды СИЗ, |Характеристика|Марки видавали засобів захисту | |ование|подлежащие до |небезпек | | |профес|выдаче по | | | |ці |нормам | | | |З т, а |Костюм |Частинки |Респіратори — «Астра-2» (захищає | |зв про год |вискознолавсан|металла, |від високодисперсних пылей при | |зв і до |овый (ГОСТ |олію, |концентраціях, перевищують ГДК у | |і |12.4.038−78), |графітова, |200 раз), противопылевые: Ф-62ш | | |Респіратор, |полімерна, |(захищає від пылей з діаметром | | |окуляри (ГОСТ |металева |частинок більш 2 мкм при | | |12.4.038−80) |та інших. пил |концентраціях, перевищують ГДК не | | | | |більш ніж 100 раз), У-2к | | | | |(захищає від пылей з діаметром | | | | |частинок більш 2 мкм при | | | | |концентраціях, перевищують ГДК не | | | | |більш ніж 10 раз), окуляри — 02 |.
Правильне проектування раціонально виконане висвітлення приміщень для підприємства надає позитивний вплив на працюючих, сприяє підвищення якості продукції, сприяє вищої продуктивність праці, забезпеченню її безпеки, знижує стомлюваність і травматизм з виробництва, зберігає високу працездатність у процесі труда.
Для виробничого приміщення ділянки при РМЦ, характерні зорові роботи верстатників і операторів на робочих місць по 11 а разряду.
Зважаючи на це, використовуватимемо змішане висвітлення, у якому поєднуватися природне, саме бічне однобічно висвітлення та штучне (робоче) освещение.
Для штучного — лампи денного світла типу ЛДЛДЦ, а безпосередньо на верстатах лампи розжарювання НВ-25.
До раціональному висвітлення диктуватимуться саме такі вимоги: дотримання нормативу освітленості, рівномірний розподіл світильників; до поля зору повинна бути прямий і відбитій блеклости. Для нормального функціонування виробничого процесу будуть передбачатися такі види висвітлення: ремонтне, чергове, аварійне і специальное.
Завдяки правильно решенному цветовому інтер'єру можна домогтися підвищення освітленості приміщення. Треба так підібрати забарвлення й оздоблення, щоб коефіцієнт відображення становив: для стель 65−70%, для стін 40−70%, для статей 16−45%, для устаткування 25−50%. Колірна гама буде такою: для стель — білий, для стін — ясно-сірий, для устаткування зелений; в поєднані із квітами безпеки: червоний (який забороняє), білий, чорне й синій (вспомогательные).
Вплинув самопочуття працюючих надає шум, створюваний устаткуванням. Сильний шум викликає перевантаження слухового апарату, слухове стомлення, знижує увагу, впливає на елемент центральної нервової системи, що ІСД може сприяти виникненню нещасного случая.
Рівень звукового тиску в металорізальних цехах робочому місці становить 83−87 дБ, при ПДУ-80дБ, для зниження шуму можна буде потрапити використовувати такі методи: зменшення галасу зчинив на джерелі, раціональна планування ділянки, акустична обробка приміщень, застосування коштів індивідуальної захисту (табл. 6.4.).
Причиною виникнення шуму є вібрація. Для зниження вібрації, воздействующей на працюючих, поруч з вище зазначеними прийматимемо такі методи: ослаблення вібрації в джерелі, застосування коштів виброзащиты; розташування верстатів на 1-му поверсі приміщення, на окремих фундаментальних плитах; застосування амортизаторів (гумової прокладки). Для працівників проектованого підприємства мусять діяти компенсації і пільги, затверджені законами РФ і статтями федерального закону про основи Охорони Праці РФ надбавки до зарплати за ступеня встановлення атестацією робочих місць, 3.1., 3.2.-12%; 3.4.-24%; пільгове харчування, безплатне молоко; додаткова відпустка; пільгове пенсійне забезпечення (з зменшенням виробничого стажу); санаторно-курортне лікування; пільгові пенсії; обов’язкові медогляди прийому роботу і періодичні. Поруч із вище викладеним, до створення у виробництві нормальних санітарно-гігієнічних умов велике значення мають необхідні санитарно-бытовые приміщення (табл.6.5.). Туалети в виробничих приміщеннях повинні прагнути бути розміщені не далі 75 м від робітника місця, біля предприятия-150 м. Їх обладнують шлюзом, умивальником і напольными чашами (унітазами) з розрахунку 1 чаша на 15 человек.
Одне з найважливіших заходів дотримання вимог техніки безпеки робітниками під час роботи на верстатах, стандартизованих в ГОСТ 1.26−77 «ГСС Порядок розробки та узгодження вимог безпеки в стандартах і технічних умовах» [9]: чистку, мастило, регулювання механізмів та встановлення деталей виробляти при зупиненому верстаті з виключеним електродвигуном; вимірювання, і інші робочі прийоми робити тільки при зупиненому верстаті; заборонено працювати на несправному верстаті тощо. Таблиця 6.5. Характеристика гардеробних приміщень та пристроїв залежно від груп виробничих процессов.
|Операции |Групп|Санитарная |Нормування |Тип |Специа| |технологическо|а |характеристи|санитарно-бытовых |гардер|льные | |го процесу |произ|ка |приміщень |обных,|бытовы| | |водст|производстве| |число |е | | |венны|нных | |отделе|помеще| | |x |процесів | |ний |ния і | | |проце| | |шафи |влаштуй| | |ссов | | |на 1 |ства | | | | | |челове| | | | | | |ка | | | | | |Нормиру |Розрахунковий | | | | | | |емое число |число | | | | | | |робочих | | | | |А1 |Верстат працює |0,8 | | |А2 |Помилка оператора |0,003 | | |А3 |Сторонній розташовано неподалік верстата |0,15 | | |А4 |Ремонт устаткування |0,25 | | |А5 |Випадкове торкання до корпусу |0,03 | | |А6 |Пробою фази |0,025 | | |А7 |Токопроводящие поли |0,5 | | |А8 |Поява нагрітих поверхонь |0,0015 | | |А9 |Іскріння електропроводки |0,025 | | |Б1 |Руйнування устаткування |0,0001 | | |Б2 |Відмова пожаровзрывозащиты |0,5 | | |Б3 |Перегружение устаткування |0,0024 | | |Б4 |Потрапляння частин тіла до зони різання |0,12 | | |Б5 |Потрапляння частин тіла до механізмів верстата |0,0375 | | |Б6 |Наявність потенціалу на корпусі |0,75 | | |Б7 |Наявність потенціалу на донизу |0,0125 | | |Б8 |Поява відкритого полум’я |0,0265 | | |В1 |Виробнича травма механічного |0,1551 | | | |характеру | | | |В2 |Поразка електричним струмом |0,1 324 | | |В3 |Виникнення пожежі |0,132| | | | |5 | | |Г1 |Нещасний випадок |0,1663 | |.
Позначення подій та його ймовірності представлені у таблиці 4.7.
Ймовірності залежних подій визначалися по теоремам складання і множення ймовірностей з урахуванням залежності ймовірності цих подій з імовірностями подій вищого уровня.
Можливість події Б3 равна:
Р (Б3) = Р (А1) • Р (А2) = 0,8 • 0,003 = 0,0024.
Можливість події Б4 равна:
Р (Б4) = Р (A1) • Р (А3) = 0,8 — 0,15 = 0,12 Можливість події Б5 равна:
Р (Б5) = Р (А3) • Р (А4) = 0,15−0,25 = 0,0375.
Можливість події Б6 равна:
Р (Б6) = Р (А5) • Р (А6) = 0,03 • 0,025 = 0,75.
Можливість події Б7 равна:
Р (Б7) = Р (А6) • Р (А7) = 0,025 • 0,5 = 0,0125.
Можливість події Б8 равна:
Р (58) = [1-(1-Р (А8)) • (1-Р (А9))]=[1-(1−0.0015)) • (1−0,025))] = 0,0265.
Можливість події В1 равна:
Р (В1) = [1-(1-Р (Б1)) • (1-Р (Б3)) • (1-Р (Б4)) • (1-Р (Б5))]=. = [1-(1- 0,0001) • (1 — 0,0024) • (1 — 0,12) • (1 — 0,0375)] = 0,1551.
Можливість події В2 равна:
Р (В2) = [1-(1-Р (В6))-(1-Р (В7))] = [1-(1−0,0125)).(1−0,75))] = 0,1 324.
Можливість події В3 равна:
Р (В3) = Р (Б2) — Р (Б8) = 0,5 • 0,0265 = 0,1 325.
Можливість події Г1 равна:
Р (Г1) = [1-(1-Р (В1)) • (1-Р (В2)).(1-Р (В3))] =.
= [1-(1−0,1555)•(1−0,1 324) • (1−0,1 325)] =0,1663.
Аналіз ймовірностей подій, що з нещасними випадками, дозволяє відзначити, що найбільше внесок у можливість появи від нещасного випадку вносить промисловий травматизм.
Вывод.
У розділі безпеки життєдіяльності дипломного проекту є повний аналіз загальних питань охорони праці, розгляд у них концепції нормування в машинобудівному виробництві. Як забезпечення нормальні умови праці під час виробництва деталі «кулачок», запропоновані й обгрунтовані заходи щодо запобігання нещасних випадків, забезпечення безпеки експлуатованого устаткування. Значення нормувальних показників на робочих місць мають реалізовуватись у обов’язковому порядку, відповідно до наведеним у таблиці 6.3.
У розділі наведено «Дерево події» і позначення подій та його вероятности.
ЗАКЛЮЧЕНИЕ
.
У цьому роботі розглянуть досліджені методи зміцнення материалов.
Для зміцнення деталі «Кулачок» обраний метод лазерного зміцнення проведене на установці «Кардамон».
Він обробки підвищує зносостійкість, усталостную міцність, відбувається мінімальне зношування формы.
У технологічної частини розроблений процес виготовлення цієї деталі, обрані оптимальні режими різання і ріжучий инструмент.
У фундаменті економічної частини розрахована ефективність виготовлення даної детали.
Розділ «БЖД» відбиває питання виробничої безпеки і охорони праці в проектованому предприятии.
1. Курсове проектування деталей машин. С. А. Чернавський, Москва,.
«Машинобудування», 1988 р. — 416 с.
2. Соспротивление матеріалів. П.О. Степін, Москва, «Вищу школу», 1983.
— 303 с.
3. Промислове застосування лазерів — Р. Кебнера, Москва,.
«Машинобудування», 1988 р. — 280 с.
4. Застосування лазерів у машинобудуванні і приладобудуванні. К. И. Крылов,.
В. Г. Прокопенко, О. С. Митрофанов, Ленінград, «Машинобудування», 1978 р. — 336 с.
5. Лазерна обробка матеріалів. І.Н. Рокалои, А. А. Ужов, О. Н. Кокора,.
Москва «Машинобудування», 1975 р. — 296 с.
6. Основа галузевих технологій і виробництва. Під редакцією В. К. Федюкина, Видавництво «Політехніка», 2002 г.
7. Технологія конструкційних матеріалів. А. М. Дальский, Н. П. Дубинин,.
Э.Л. Макаров, Е. А. Попов, Москва «Машинобудування», 1977 р. — 665 с.
8. Белькевич Б., Тимашков У. Довідкове посібник технолог, а машинобудівного заводу. Мінськ.: Білорусь, 1972. 415с.
9. Допуски і посадки. Довідник. Під. ред. У. Д. Мягков. М.:
Машинобудування. 1980. Т. 1. і Т. 2. 1032с. 10. Косилова А. Р., Мещеряків У. До., Калінін М. А. Точність обробки, заготівлі та припуски у машинобудуванні. Довідник. М.:
Машинобудування, 1976. 310 з. 11. Короткий довідник металіста. Під. ред. А. М. Малова М.:
Машинобудування, 1976. 767 з. 12. Курсове проектування за технологією машинобудування. Під. ред. А. Ф.
Горбацевича. Мінськ.: Вышейшая школа, 1975. 288 з. 13. Обробка металів різанням. Довідник технолога. Рік. ред. Р. А.
Монахова. М.: Машинобудування, 1974. 520 з 14-ма. Довідник молодого машинобудівника. Під. ред. У. У. Данилевского.
М.: Машинобудування, 1973. 648 з. 15. Довідник технолога-машиностроителя. Під. ред. А. Є. Коси-ловой і Р.
До. Мещерякова. Т. 1. М.: Машинобудування, 1972. 694с. 16. Довідник технолога-машиностроителя. Під. ред. А. М. Малова. Т. 2.
М.: Машинобудування, 1972. 568 з. 17. Шепс У. А., Шепс Еге. Р. Розрахунок припусков на мехобработку. Навчальний посібник. Саранськ, 1995 р, 80 із 18-ї. Методичні вказівки «Проектування технологічних процесів механічного оброблення технологічних машин» УлПи, Ульянівськ, 1990.;
32с. 19. Довідник. Режими різання металів. під. ред. Ю.В. Баранівського, М.:
Машне, 1972 — 660с. 20. Норми часу під час роботи на металорізальних верстатах. Методичні вказівки. ДИТУД, Димитровград, 1994;68с. 21. Общемашиностроительные нормативи режимів різання для технологічного нормування робіт на металорізальних верстатах. Частина 1 і 2. — М.:
Машинобудування, 1974. 22. Еженедельный інформаційний бюлетень з товарів та цінам: «Ціни» № 11 від 22 березня 2004 р. Поволжско-Уральский регіон. 23. Б. В. Белькевич, В. Д. Тимошков. Довідкове посібник технолога машинобудівного заводу.- Мінськ: Белорусь, 1972. 24. В. С. Стародубцева. Збірник завдань із технічному нормуванню у машинобудуванні. — М.: Машинобудування, 1974. 25. Н. А. Нефедов. Дипломне проектування в машинобудівних технікумах. — М.: Вищу школу, 1976. 26. Довідник технолога-машиностроителя в 2-х томах. Під ред. А.Г.
Касиловой, Р. К. Мещерякова.- М.: Машинобудування, 1985. 27. Організація і планування машинобудівного виробництва. Під ред.
Ю.В.Скворцова, Л. А. Некрасова. — М.: Вищу школу, 2003 р. 28. Організація, планування і управління машинобудівним виробництвом: Методичні вказівки до курсової роботи і економічній частині дипломного проекту. — Димитровград, 2003 р. 29. Конституція РФ — М.: Юридична література, 1993. — 46 з. 30. Трудової Кодекс Російської Федерації. — М.: Апарат уряду РФ,.
1999. — 38 з. 31. Безпека життєдіяльності. Виробнича безпека продукції та охорона праці./ В.п. Кукин, В.Л. Лапін, Н. Л. Понаморев та інших. Учеб. посібник для студентів — М.: Вищу школу, 2001 — 431 з. 32. Типові галузеві норми безплатної видачі спеціального одягу, спеціального взуття та інших засобів індивідуальної захисту працівникам машинобудівних і металообробних виробництв. 33. Система стандартів за безпеку праці. — М.: Госкомитт СРСР з стандартам, 1984 — 296 з. 34. Гігієнічні вимоги до мікроклімату виробничих помещений.
Санітарні правил і норми СнПИН 2.2.4.548 — 96. Затверджене постановою Госкомсанэпидемнадзора Росії від 1 жовтня 1996 г.
№ 21. 35. Правила устрою електроустановок (ПУЭ). Затверджено приказом.
Міністерства енергетики Російської Федерації № 204 від 08.07.2002 р. 36. Безпека життєдіяльності. Підручник для вузів. С.В. Бєлов, А.В.
Ильницкая, А. Ф. Козьяков та інших.; Під загальною редакцією С.В. Бєлова. 2-ге вид., испр. і доп. — М.: Высш. шк., 1999.-448с.
ПРИЛОЖЕНИЯ.
———————————- Рис. 1.3. Розподіл микротвёрдости за глибиною зон обробки безперервним випромінюванням лазера на СО2 в зразках: а — сталь 20, б — сталь 45, в — сталь У12 що за різних швидкостях переміщення зразків: 1 — 0,6 м/мин; 2 — 1,8 м/мин; 3 — 3,0 м/мин; 4 — 4,2 м/мин.
Рис 1.4. Розподіл твердості за глибиною зони обробки безперервним випромінюванням лазера на СО2 в зразках зі сталі 35 що за різних швидкостях переміщення променя: 1, 2, 3 — швидкість 10 мм/с; 4 — 40 мм/с (1, 4 -мартенсит, 2 — тростит, 3 — феррит) Рис. 1.5. Залежність глибини, ширини (чи твердості (б) зони обробки від швидкості переміщення променя лазера:
1 — перший шар (поверховий); 2 — четвертий слой Заготовка min = 55,13.
Заготовка max = 57,03.
Черновое растачивание min = 59,156.
Черновое растачивание max = 59,23.
Чистовое растачивание max = 60,030.
Чистовое растачивание min = 60,000.
Тd3=1,9.
Тd2=0,074.
Тd1=0,030.
Рис. 4.2. Схема полів допусків і межоперационных размеров.
(5.1).
(5.2).
(5.3).
(5.4).
(5.5).
(5.6).
(5.7).
(5.8).
(5.9).
(5.10).
(5.11).
(5.12).
(5.13).
(5.14).
(5.15).
(5.16).
(5.17).
(5.18).
(5.19).
(5.20).
(5.21).
(5.22).
———————————- ДП. 1707.170.04.ПЗ.