Воздух робочої зоны
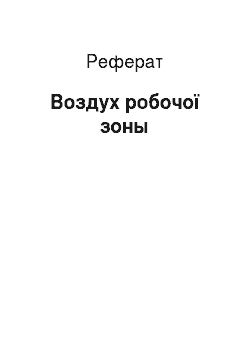
Фільтр має корпус 1, фільтруючі елементи 4, бункер 5, систему імпульсної регенерації 3. Фільтруючий елемент містить чотири пари вертикально розміщених фільтруючих осередків 2. Осередок містить похилі непроникні перегородки, верхні і нижні сітки. Між сітками засипають частки шаром 150 мм розміром 3−5 мм дробленого матеріалу зі магнезита, доломіту, гравію тощо. Перегородки і сітки утворюють канали… Читати ще >
Воздух робочої зоны (реферат, курсова, диплом, контрольна)
Російський Університет Дружби Народов.
Екологічний факультет.
Реферат за курсом «Захист природних ресурсов».
на тему.
Очищення й технологічних газів, димових відходів та вентиляційних выбросов.
Керівник: Хаустов А.П.
Виконав студент гр.
ОСМ-202 Глущенка И.А.
Москва.
Очищення переробка технологічних газів, димових відходів та вентиляційних викидів 3.
Механічні («сухі») пылеуловители 3.
Пористі фільтри 6.
Электрофильтры 12.
Апарати мокрого пылегазоулавливания 14.
Скрубберы (газопромыватели). 14.
Комбіновані методи лікування й апаратура очищення газів 20.
Література 23.
Очистка переробка технологічних газів, димових відходів та вентиляційних выбросов.
Захист довкілля забруднень включає, з одного боку, спеціальні методи лікування й обладнання очищення газових і рідких середовищ, переробки відходів та шламів, вторинного використання тепла й максимального зниження теплового забруднення. З іншого боку, при цьому розробляють технологічні процеси та устаткування, відповідальні вимогам промислової екології, причому техніку захисту довкілля застосовують на всі етапи технологій. Запропоновані до розгляду в лекціях 5, 6 і аналогічних сім методи лікування й устрою захисту довкілля згруповані на кшталт очищаемой середовища (газова, рідка, тверда, комбінована) чи вдруге використовуваного відходу залежно з його характеристик.
Газоподібні промислові відходи містять у собі не які вступили до реакції гази (компоненти) вихідного сировини; газоподібні продукти; відпрацьований повітря окисних процесів; стиснений (компрессорный) повітря транспортуванню порошкових матеріалів, для сушіння, нагріву, охолодження і регенерації каталізаторів; для продувки опадів на фільтрувальних тканинах і інші елементи; індивідуальні гази (аміак, водень, діоксид сірки і ін.); суміші кількох компонентів (азотоводородная суміш, аммиачноповітряна суміш, суміш діоксиду сірки і фосгену); газопилові потоки різних технологій; що відходять димові гази термічних реакторів, топок та інших., і навіть відходи газів, які утворюються при вентиляції робочих місць і приміщень. Крім цього, все порошкові технології супроводжуються інтенсивним виділенням газопылевых відходів. Пылеобразование відбувається у процесах подрібнення, класифікації, змішання, сушіння і транспортування порошкових і гранулированных сипучих матеріалів [1, 2].
Задля чистоти газоподібних і газопылевых викидів з метою їхнього знешкодження чи вилучення їх найдорожчих і престижних дефіцитних компонентів застосовують різне очисне обладнання та відповідні технологічні приемы.
Нині методи очищення запилених газів класифікують на такі группы:
I. «Сухі» механічні пылеуловители.
II. Пористі фильтры.
III. Электрофильтры.
IV. «Мокре» пылеулавливающие аппараты.
Механічні («сухі») пылеуловители.
Такі пылеуловители умовно діляться втричі группы:
— пылеосадительные камери, принцип чиїх робіт грунтується на дії сили тяжкості (гравітаційної силы);
— інерційні пылеуловители, принцип чиїх робіт грунтується на дії сили инерции;
— циклони, батарейные циклони, які працюють пылеуловители, принцип чиїх робіт грунтується на дії відцентровій силы.
Пылеуловительная камера є пустотілий чи з горизонтальними полками у внутрішній порожнини прямокутний короб, у нижній частини якого є отвір чи бункер для збору пилу (рис. 1.).
[pic].
Рис. 1. Пылеосадительные камери: а — порожниста: б — з горизонтальними полками; в, р — з вертикальними перегородками: / - запилений газ; // - очищений газ; /// - пил; 1 — корпус; 2 — бункер; 3 — штуцер для удаления;
4 — полки; 5 — перегородки.
Швидкість газу камерах становить 0,2−1,5 м/с, гідравлічне опір 50−150 Па. Пылеосадительные камери придатні для уловлювання великих частинок розміром щонайменше 50 мкм. Ступінь очищення газу камерах не перевищує 40−50%. Тривалість проходження т© газами осадительной камери при рівномірному розподілі газового потоку з її перерізу составляет:
[pic].
де Vk, — обсяг камери, м3; Vгоб'ємний витрата газів, м3/с; L — довжина камери, м; Уширина камери, м; Мвисота камери, м.
У інерційних пылеуловителях зміни напрями руху газів встановлюють перегородки (рис. 2). У цьому поруч із силою тяжкості діють сили інерції. Пилові частки, прагнучи зберегти напрям руху після зміни напрями руху потоку газів, глушаться в бункері. Газ в інерційному апараті надходить зі швидкістю 5−15 м/с. Ці апарати від звичайних пылеосадительных камер великим опором і високим рівнем очищення газу [З].
[pic].
Рис. 2. Інерційні пылеуловители з в різний спосіб подачі й розподілу газового потоку: а — камера з перегородкою; б — камера з дедалі ширшим конусом; в — камера з заглубленным бункером.
Значну увагу під час проектування пневмотранспортных та інших пристроїв пылеочистки необхідно приділяти вузлам відділення матеріалу від транспортуючому повітря — разгрузочным і пылеулавливающим пристроям (циклонам, фильтрам тощо.). Залежно від способу відділення матеріалу в системах пневмотранспорта використовують об'ємні розвантажувальні пристрої і відцентрові циклони. Вибір тієї чи іншої типу устрою залежить від конкретних умов праці установок й виконання вимог, що висуваються до його роботі: найбільше значення коефіцієнта осадження матеріалу, мінімальне опір розвантажувального устрою, надійність в эксплуатации.
Перевага віддається відцентровим циклонам, виконуючим це й роль пылеулавливающего апарату. Ефективність уловлювання пилу в циклонах підвищується із зменшенням діаметра корпусу, та заодно знижується їх пропускну здатність. Задля більшої відповідної продуктивності пневмотранспортной установки невеликі циклони групують в батарею. Коефіцієнт пиловловлювання батареї циклонів становить 0,76−0,85 і кілька підвищується зі збільшенням вхідний швидкості (з 11 до 23 м/с). Використання замість циклонів вихрових пиловловників забезпечує уловлювання частинок пилу розміром 5−7 мкм.
Повітря після розвантажувальних пристроїв, чи циклонів, насичений субмикронными частинками, повинен спрямовуватися на доочистку в пылеуловители. При виборі типу пылеуловителя за умов роботи таких установок враховують такі показатели:
— ступінь пиловловлювання, рівну відношенню кількості пилу, затриманої пылеуловителем, до кількості пилу, котра міститься повітря за його вступі до пылеуловитель;
— опір пылеуловителя, від якого економічність процесу пылеулавливания;
— габаритні розміри і безліч пылеуловителя, надійність і простота його обслуживания.
Циклони рекомендується використовуватиме попередньої очищення газів і встановлювати перед високоефективними апаратами (наприклад, фільтрами чи электрофильтрами) очистки.
Основними елементами циклонів є корпус, вихлопна труба і бункер. Газ вступає у верхню частина корпусу через вхідний патрубок, приварений до корпусу тангенциально. Уловлювання пилу відбувається під дією відцентровій сили, виникає під час руху газу між корпусом і вихлопної трубою. Вловлена пил ссыпается в бункер, а очищений газ викидається через вихлопну трубу (рис. 3).
Залежно від продуктивності циклони можна встановлювати по одному (одиночні циклони) чи об'єднувати до груп з цих двох, чотирьох, шести чи восьми циклонів (групові циклоны).
Існують батарейные циклони. Конструктивною особливістю останніх і те, що закручування газового потоку і уловлювання пилу у яких забезпечується розміщеними в корпусі апарату циклонными елементами [4].
Нижче приведенатехническая характеристика найбільш поширеного на виробництві циклону ЦН-15:
— допустима запиленість газу, г/м3: для слабослипающихся пылей — трохи більше 1000; для среднесливающихся пылей — 250;
— температура очищаемого газу, °З — трохи більше 400;
— тиск (розрідження), кПа (кг/см2) — трохи більше 5 (500);
— коефіцієнт гідравлічного опору: для одиночних циклонів — 147; для групових циклонів — 175−182;
— ефективність очищення (від пилу dm = 20 мкм, при швидкості газопилового потоку 3,5 м/с і діаметрі циклону 100 мм), % - 78.
[pic].
Рис. 3. Циклон типу ЦН-15П:
1 — конічна частина циклону; 2 — цилиндрическая частина циклону; 3 — винтообразная кришка; 4 — камера очищеного газу; 5 — патрубок входу запиленого газу; 6 — вихлопна труба; 7 -бункер; 8 — люк; 9 — опорний пояс; 10 — пылевыпускное отверстие.
Для розрахунків режимів і вибору марки (конструкції) циклону необхідні такі вихідні дані: кількість очищаемого газу при робочих умовах Vг, мЭ/с; щільність газу при робочих умовах р, кг/м3; динамічна в’язкість газу при робочої температурі (; дисперсний склад пилу, задаваемый двома параметрами dm і lg (r; запиленість газу С (х, г/м3; щільність частинок рч, кг/м3; необхідна ефективність очищення газу (.
Конструкцію і режимні параметри циклону розраховують методом послідовних наближень по методикам [3−5] чи використовуючи більш сучасний математичний апарат [б].
Пористі фильтры.
Задля чистоти запилених газів дедалі більшого поширення отримує на останніх щаблях суха очищення рукавными фільтрами. Ступінь очищення газів у яких за дотримання правил технічної експлуатації сягає 99,9%.
Класифікація рукавных фільтрів можлива за такими признакам:
— формі фільтрувальних елементів (рукавные, плоскі, клиновые та інших.) і наявності у яких опорних пристроїв (каркасні, рамные);
— місцеві розташування вентилятора щодо фільтра (всасывающие, працюючі під розрідженням, і нагнетательные, працюючі під давлением);
— способу регенерації тканини (встряхиваемые, із другого продувкой, з імпульсної продувкой і др.);
— наявності і малої форми корпусу розміщувати тканини — прямокутні, циліндричні, відкриті (бескамерные);
— числу секцій встановленні (однокамерні і многокамерные);
— виду використовуваної тканини (наприклад, стеклотканевые).
Як фільтрувальних матеріалів застосовують тканині з природних волокон (бавовняні і вовняні), тканині з синтетичних волокон (нитроновые, лавсановые, поліпропіленові та інших.), і навіть стеклоткани. Найпоширеніші лавсан, терилен, дакрон, нитрон, орлон, оксалон, сульфон. Останні два матеріалу представляють полиамидную групу волокон, які мають термостойкостью за нормальної температури 250−280 °З. Для фільтрувальних тканин найхарактерніше саржевое переплетення. Застосовують також нетканые матеріали — фетры, виготовлені свойлачиванием вовни і синтетичних волокон.
Розглянемо докладніше групу матеріалів з нетканих иглопробивных фільтрувальних полотен, найперспективніших у виробництві порошкових матеріалів. Таллинской фірмою «Мистра» пропонуються полотна марок «Фільтра- 220», «Фильтра-330», «Фильтра-550» від використання в аспирационных чи вакуумних рукавах і кишенькових (мешочных) фільтрах очищення газів, пиловловлювання технологічних продуктів, соціальній та системах вентиляции.
Нетканые иглопробивные полотна характеризуються такими показниками (табл. 1):
Таблиця 1 Технічні показники фільтрувальних полотен.
|Наименование |"Фильтра-550″ |"Фильтра-330″ | |Поверхнева щільність, г/м2 |550±28 |330±17 | |Ширина, див |150±3 |145±3 | |Толщина, мм |2±0,3 |1,3±0,2 | |Найменування |"Фильтра-550″ |"Фильтра-330″ | |Повітропроникність, дм3/м2 з), |150±50 |250±50 | |при перепаде тиску 50 Па | | | |Розривна навантаження, М, щонайменше |1000 |400 | |за довжиною по ширині | | | |Подовження при розриві, % по длине|80 90 |80 90 | |по ширині | | | |Нормована вологість, % |1 |1 |.
Промислові випробування матеріалу «Фильтра-550» у виробництві сепарированного крейди показали ступінь очищення 99,9% при уловлюванні пилу, 75% якої становить фракція з діаметром частинок 1−5 мкм.
Термін служби фильтровального матеріалу упродовж як мінімум року. Верхній межа робочих температур становить 140−150 °С.
У «Містрі» створено і більше термостойкое полотно, що використовується при температурі до 210−220 °З. Залежно від виду тканини допустима питома газова навантаження становить 0,6−1,2 м3/(м2*мин) для бавовняною чи шерстяний; 0,5−1 -для синтетичної; 0,3−0,9 м³ /(м2*мин) — для стеклоткани.
Доставка рукавний фільтр працює так. Повітря під тиском вступає у верхню розподільну коробку і у з матерії вертикальні рукави. Пройшовши крізь рукави й залишивши з їхньої поверхні пил, очищений повітря відбуває о атмосферу (приміщення). Рухлива рама з дротяною сіткою при піднесенні і опусканні стискує рукави в поперечному сечении, завдяки чому пил скидається в пылесборник і видаляється гвинтовим конвеєром. Недоліком таких фільтрів є незадовільна очищення фільтруючій тканини, у результаті значно зростає опір фільтра і знижується його КПД.
Найбільшого поширення набув усмоктувальний рукавний фільтр, який складається з низки рукавів, ув’язнених у герметично закритий корпус. Підлягає очищенні повітря подається через нижню приймальню коробку в рукави, заглушені згори, проникає крізь тканину рукавів і видаляється з корпусу через канал. Рукави фільтра очищаються від пилу з допомогою спеціального встряхивающего механізму. Недоліком всасывающих фільтрів є значний підсос повітря через неплотности (10−15% від обсягу що надходить на очищення воздуха).
Розробка і промислове виготовлення дешевих фільтрувальних тканин, які мають високою ефективністю при достатньої механічної міці й стійкості в кислих і лужних середовищах, наприклад, при хімічному полировании кришталю, відкривають шляхи до ширшого їх застосування. Так, фільтруючий матеріал «Бекинокс» (Великобританія) виготовляють як у вигляді штапелю, так і у вигляді довгих ниток різного діаметра із нержавіючої сталі. Цей матеріал при швидкості фільтрації 180 м3/(м2*ч) має опір 1200 Па й саму ефективність, як і текстильні тканини. Вона має високої абразивною сталістю, температуростойкостью (до 500 °З), регенерується будь-яким відомим способом і добре зарекомендувало себе при фільтрації газів, містять SO2.
У Франції при очищенні відведених газів з температурою 400−500С застосовують рукавные фільтри з металевого фетру, основа якого є металеву сітку, нарощенную шаром тонкої металевої нитки певної товщини і щільність. По швидкості фільтрації, аэродинамическому опору, кількості споживаної енергії фільтр ідентичний рукавному фільтрові з полиэфирного волокна.
Для випадку, коли висока фільтруюча спроможність повинна поєднуватися з високої теплостойкостью і стійкістю до агресивної хімічної середовищі, фірма «Дюпон» (США) пропонує три виду матеріалів (повсть і тканини) для фільтрації сухих частинок: номекс (арамидное волокно), тефлон (фторуглерод) і тефэр-войлок, зроблений із суміші тефлону (85%) зі стекловолокном (15%). Вони витримують робочу температуру 100−250 °С.
Невелика кількість тонких скляних волокон в тефлоне зменшує його пористість і підвищує улавливающую здатність. Тефлонові волокна, стійкі до истиранию, своєю чергою захищають скловолокно від механічних ушкоджень. Високі експлуатаційні характеристики матеріалу тефэр пояснюються протилежними трибоэлектрическими властивостями обох волокон суміші, які створюють електростатичні заряди під час роботи. Це сприяє високої ефективності уловлювання повстю субмікронних частинок. Проте, за даними фірми, якщо фтористоводородная кислота, наприклад, при хімічному полировании кришталю не повністю нейтралізується, то димових газах рекомендується користуватися 100%-ным тефлоном.
Вітчизняної промисловістю нині розроблено такі тканинні фільтри [4]: і з імпульсної продувкой кожного каркасного рукави (ФРКИ та інших.). Регенерація здійснюється під впливом імпульсів стиснутого повітря і відключення секцій; з комбінованим пристроєм регенерації - механічним струшуванням і зворотної посекционной продувкой (ФРУ та інших.) в) із другого посекционной продувкой (ФР та інших.) р) з регенерацією механічним струшуванням (ФР-6П та інших.). Регенерація рукавів здійснюється вручну чи з допомогою електромеханічного устройства.
У довіднику [7] докладно розглянуті фільтри загальнопромислового призначення, серійно випущені спеціалізованим заводами. Переважна розвиток отримали фільтри ФРКИ і ФРІ (рис. 4). Швидкість фільтрування у тих апаратах на 20−30% вище, ніж у фільтрах з механічною регенерацією і зворотної продувкой. При ефективної регенерації (короткими імпульсами тривалістю 0,1−0,2 з) загальний термін їхньої служби рукавів у тих фільтрах вищий, рукави менше зношуються. Гідравлічне опір зазвичай підтримується лише на рівні 1000−1500 Па. Умовне позначення типорозміру фільтра: Ффільтр; Р — рукавний; До — каркасний; І - з імпульсної продувкой; цифра після буквених позначень — активна поверхню фильтрации.
[pic].
Рис. 4. Фільтр ФРКИ (ФРИ):
1 — бункер; 2 — корпус; 3 — диффу-эорсопло; 4 — кришка: 5 — труба що роздає; 6 — секція клапанів: 7 — колектор стиснутого повітря; 8 — секція рукавов.
У процесі фільтрації запилений газ проходить через тканину закритих знизу рукавів всередину, виходить через верхній колектор і видаляється з апарату. Кожен рукав в фільтрі натягнуть на жорсткий каркас і закріплено на верхньої решітці. Як фільтруючого матеріалу використовують лавсан і фетр. У табл. 2 наведено основні технічні характеристики фільтрів рукавных каркасних з імпульсної продувкой (ФРКИ).
Таблиця 2 Технічні характеристики рукавных фільтрів |Показники |ФРКИ-30 |ФРКИ-60 |ФРКИ-90|ФРКИ-180 |ФРКИ-360 | |Поверхня |30 |60 |90 |180 |360 | |фільтрації, м2| | | | | | |Показники |ФРКИ-30 |ФРКИ-60 |ФРКИ-90|ФРКИ-180 |ФРКИ-360 | |Кількість рукавів |36 |72 |108 |144 |288 | |Висота рукава,|2 |2 |2 |3 |2 | |м | | | | | | |Кількість |6 |12 |18 |24 |48 | |электромагнитн| | | | | | |ых клапанів | | | | | | |Кількість секцій |1 |2 |3 |4 |8 | |Найбільший |10 |20 |30 |60 |120 | |витрата стиснутого| | | | | | |повітря, м3/ч | | | | | | |Габаритні |1458×2060х|2820×2060х|4140×20|5480×2060х|5850×4370х | |розміри, мм |х3620 |х3620 |60х |х4620 |х4880 | | | | |х3620 | | | |Маса, кг |1300 |2500 |2500 |5500 |10 500 |.
Примітка. Діаметр рукави 130 мм, гідравлічне опір 1.2 Па тиск продувочного повітря 0,3−0,6 МПа, робочий тиск (розрідження) в апараті до 5 кПа.
Розрахунок рукавных тканинних фільтрів зводиться до визначення загальної поверхні фільтрації F і кількості жодних фільтрів чи секцій. Нормальна навантаження на 1 м фільтруючій поверхні для рукавных фільтрів становить 150−200 м /год. Опір фільтрів визначають по формуле:
[pic] де У — коефіцієнт, рівний 0,13−0,15 (великої ваги приймається для більш дисперсною пилу); Qв — витрата повітря на 1 м² тканини рукавів, м3/ч; n — приймається рівним 1,2−1,3 (менше значення приймається ще дисперсною пыли).
Працюючи нормального режимі опір нагнітальних фільтрів становить до 2 кПа, всасывающих — до 6 кПа. Загальну поверхню фільтрації (м2) визначають по формуле:
[pic] де Fpaб — поверхню фільтрації в одночасно працюючих секціях, м; Fрег ~ поверхню фільтрації в регенерируемой секції, м2; V — об'ємний витрата очищаемых газів (повітря) з урахуванням подсоса повітря на фільтр, м3/мин; Vnp — об'ємний витрата продувочного повітря, м3/мин; qфпитома газова навантаження, м3/(м2*хмин).
Кількість необхідних жодних фільтрів чи секций.
[pic] де F1 — поверхню фільтрації всіх рукавів, встановлених щодо одного фільтрі чи секції, м2.
Гідравлічне опір тканинного фільтра (Р, Па (уточнену значення), будь-якої миті часу ((, з) від включення фільтра в роботу визначають по формуле:
[pic] де (r — динамічний коефіцієнт в’язкості газу, Па*c; (n — пористість шару пилу; dm — середня площа частинок пилу, м; (т- - пористість тканини; С (х — початкова запиленість газу, кг/м3; (пщільність пилу, кг/м3.
Періоди роботи фільтра між регенерацією, струшуванням чи продувкой орієнтовно визначають залежно від вхідний запиленості газов:
|Входная запиленість, г/м3 |5 |10 |20 | |Періоди між регенерацією, хв |10−12 |8−9 |4−7 |.
Пиловловлювання в цехах підготовки й переробки порошкових матеріалів є технічної проблемою. Наприклад, все ланки погрузочнорозвантажувальних робіт — потенційні джерела пыления, інтенсивність яких залежить від технічного рівня використовуваного устаткування та технології перевантаження сипучих і кусковых матеріалів. Найповніше завдання боротьби з освітою пилу й її улавливанием вирішені для конвеєрних ліній і деяких видів переробного устаткування [1].
Нині очищення таких відведених газів від пилу застосовують одноступенчатую очищення в циклонах ЦН-15, ЦН-11 чи двоступеневу з використанням додаткового циклона-промывателя типу СИОТ чи ЛИОТ. Але вони не забезпечують необхідної рівня очищення газів, що пов’язані з зарастанием воздухопроводов у місцях відділення сухого газу від пилу й газу від крапель води. Тому додатково використовують пылеулавливающие установки, які включають сухі інерційні пылеуловители (циклони групові і батарейные), пористі фільтри (стрічкові, рамні, рукавные зі струйной імпульсної і зворотної продувкой, зернисті і др.).
Конструкція зернистого фільтра, представлена на рис. 5.
Фільтр має корпус 1, фільтруючі елементи 4, бункер 5, систему імпульсної регенерації 3. Фільтруючий елемент містить чотири пари вертикально розміщених фільтруючих осередків 2. Осередок містить похилі непроникні перегородки, верхні і нижні сітки. Між сітками засипають частки шаром 150 мм розміром 3−5 мм дробленого матеріалу зі магнезита, доломіту, гравію тощо. Перегородки і сітки утворюють канали трикутного перерізу, якими очищені гази через отвори в боковині відбуваються у короб. У каналах для проходу очищеного газу встановлюють перфоровані трубки, службовці для циклічною подачі стиснутого повітря з колектора. Фільтруючі осередки розділені перегородками втричі однакові частини. При імпульсної продувке нижні осередки працюють у режимі фільтрації, а верхні - як регенерации.
[pic].
Рис. 5. Зернистий фильтр
Поруч із очищенням пылвгаэовых потоків важливою завданням є й очищення і знешкодження димових газів від продуктів згоряння палива й інших газоподібних альтерогенов.
Для цього він часто застосовують метод адсорбції. У сухому способі очищення димових газів фільтрація очищаемых викидів відбувається після нерухомий (адсорберы періодичної дії) чи рухомий шар твердого поглинача — адсорбенту (адсорберы безперервного дії). Найбільш поширені адсорберы періодичної дії, у яких період контактування очищаемого газу з адсорбентом чергується з періодом його регенерации.
Конструктивно адсорберы (рис. 6) виконуються як вертикальних, горизонтальних або кільцевих ємностей, заповнених пористим адсорбентом. Вибір конструкції визначається швидкістю газової суміші, розміром частинок адсорбенту, необхідної ступенем очищення низку інших чинників. Вертикальні адсорберы застосовують при незначних обсягах очищаемого газу, а горизонтальні і кільцеві при продуктивності до десятків і сотень м3/ч.
[pic].
Рис. 6. Конструктивні схеми адсорберов: а — вертикальний; б — горизонтальний; в — кільцевої; 1 — адсорбер: 2 — шар активованого вугілля; 3 — центральна труба на шляху подання паровоздушной суміші при адсорбції; 4 — барботер на шляху подання гострого пара при десорбции; 5 — труба для виходу інертних стосовно поглотителю газів при адсорбції; б — труба для виходу пара при десорбции.
Під час проектування чи виборі конструкції адсорбера використовують такі вихідні дані: об'ємний витрата очищаемого газу (м/с), концентрацію удаляемой домішки (мг/м3) і тиск відведених газів (Па). У результаті розрахунку визначають необхідну масу адсорбенту, конструктивні розміри, гідравлічне опір апарату та палестинці час захисного дії адсорбера [8].
Электрофильтры.
Метод электроосаждения (уловлювання пилу в електричному полі) ось у чому. Частинки пилу (чи крапельки вологи) спочатку отримують заряд від іонів газу, утворювані в електричному полі високого напруги, та був рухаються до заземленному осадительному электрозаряду. Лопав на заземлений уловитель, частки прилипають і розряджаються. Коли осадительный електрод обростає шаром частинок, вони стряхиваются під впливом вібрації й збираються у бункері. Схема електричного осадження пилу представлена на рис. 7. [2].
[pic].
Рис. 7. Схема електричного осадження пыли:
1 — джерело електроживлення; 2 — коронирующий електрод; 3 — осадительный електрод; 4 -іон газу; 5- частка пыли.
Электрофильтры застосовуються там, де необхідно очищати дуже серйозні обсяги газу та відсутня небезпека вибуху. Ці установки (рис. 8) йдуть на уловлювання кажана золи на сучасних електростанціях, для уловлювання пилу в цементної промисловості, соціальній та металургії в потужних системах уловлювання диму, для пиловловлювання в системах кондиціонування повітря та інших суміжних галузях [4,9].
[pic].
Рис. 8. Двоступінчастий электрофильтр горизонтального потока:
1 — комплект стряхиватвлей для високовольтних і збірних електродів; 2 — окрема сблокированная дверцята оглядового люка; 3 — быстрооткрывающиеся панелі для вилучення дротяних електродів без відключення установки; 4 — розпірні стрижні між осадительными електродами; 5 — дырчатый розподільний екран; б — житло, встановлювана безпосередньо на опорних колонах: 7 — сблокированное високовольтна обладнання кожної електричної секції: в — майданчик розміщувати ізоляторів і газонепроницаемых ущільнювачів; 9 — скатная дах; 10 — клиновидные опори для дротяних електродів; 11 — пружно закріплені збірні електроди; 12— пластинчасті і щитковые електроди; 13- пружно закріплена високовольтна рама: 14 — люк оглядового проходу між ступенями.
Апарати мокрого пылегазоулавливания.
При очищенні газів від частинок пилу й на переробку газоподібних відходів з метою добування їх корисних компонентів чи його знешкодження успішно застосовуються методи лікування й устаткування, засновані за принципами мокрого пылеулавливания.
Доцільно поєднання сухою й наступної мокрою очищення, що у своє чергу може поєднуватися з адсорбційної доочищенням. Розвинена поверхню контакту фаз сприяє збільшення ефективності пиловловлювання. У промисловості використовують мокрі пылеуловители (промыватели) крапельного, плівкового і барботажного типів. Конструктивно апарати може бути порожніми, тарельчатыми, механічного і ударноінерційного дії (ротоклоны), і навіть швидкісного типу (труби Вентури та інші инжекторы).
Необхідно прагнути до створення мокрих промывателей з мінімальним гідравлічною опором, працездатних при низьких витратах води. Ефективність очищення пилу залежить від розмірів що вловлюються частинок і південь від інших властивостей пилу. Необхідність концентрування системи рідина — тверде тіло з поверненням очищеної води на пиловловлювання, накопичення в орошаемой рідини розчинних компонентів пилу ускладнює систему мокрого пиловловлювання. Загалом вигляді процес уловлювання пилу мокрим методом подається як перенесення твердої фази з газової середовища в рідку і видалення останній з апарату разом із твердої фазою [2,3]. Залежно від форми контактування фаз способи мокрою пылеочистки можна розділити на: 1 — уловлювання обсягом (шарі) рідини; 2 — уловлювання плівками рідини; 3 — уловлювання розпорошеною рідиною обсягом газу (рис. 9).
[pic].
Р і з. 9. Схеми основних способів мокрого пиловловлювання: а — обсягом рідини; б — плівками рідини; е — розпорошеною рідиною; 1.
— бульбашки газу; 2 — краплі рідини; 3 — тверді частицы.
Скрубберы (газопромыватели).
При объемно-жидкостном способі потік запиленого газу пропускають через певний обсяг рідини. З цією метою використовують пінні пылеуловители з провальними тарілками чи тарельчатые скрубберы, ефективність яких може становити 90−95%. На рис. 10 представлений тарельчатый скруббер.
[pic] [pic] |Рис. 10. Тарельчатый скруббер: |Рис. 11. Пылеуловитель ПВР: | |1 — каплеуловитель; 2 — тарілка. |1 — корпус; 2,4- перегородки; 3 — | | |водоотбойник; 5 — каплеуловитель; б| | |- вентиляційне агрегат; 7 — | | |пристрій для регулювання рівня| | |води |.
Уловлювання пилу плівками рідини характеризується тим, що контакт газу та рідини відбувається за українсько-словацьким кордоном двох середовищ без перемішування. Захоплення (власне уловлювання) твердих частинок тонкими плівками рідини відбувається на поверхнях конструктивних елементів. До цій групі пристроїв ставляться скрубберы з насадкою, мокрі циклони, ротоклоны тощо. На рис. 11 показано схема пылеуловителя вентиляційного мокрого (ПВМ).
Уловлювання пилу розпорошеною рідиною у тому, що орошающая рідина вводять у запилений обсяг (потік) газу распыленном чи дисперсном вигляді. Розпилення орошающей рідини проводиться за допомогою форсунок під тиском або енергії самого потоку газу. Перший спосіб розпорошення використовують у порожніх скрубберах (рис. 12), другий — в турбулентных промывателях і скрубберах Вентури (рис. 13).
[pic] [pic].
|Рис. 12. Порожній форсуночный скруббер|Рис. 13. Скруббер Вентури 1 — | | |каплеуловитель; 2 — диффузор; 3 — | | |горловина; 4 — конфузор; 5 — | | |пристрій на шляху подання води |.
Скрубберы Вентури (поєднання труби з каплеуловителем відцентрового типу) забезпечують очищення газів від частинок пилу практично будь-якого дисперсного складу. Залежно від фізико-хімічних властивостей вловлюється пилу, складу і температури газу вибирають режим роботи скруббера Вентури. Швидкість газу горловині то, можливо 30−200 м/с, а удільне зрошення 0,1−6 м3/м3. Ефективність очищення від пилу залежить від гідравлічного опору. Скрубберы Вентури ефективно працюють при припустимою запорошеності очищаемых газів 30 г/м3, граничною температурі очищаемого газу 400 °З, питомому зрошенні 0,5−2,5 м3/м3 і гідравлічному опір 6−12 кПа.
Характеристика труб типу ГВПВ (скребачка Вентури прямоточный высоконапорный) приведено в табл. 3. Конструкція часто доповнюється каплеуловителем циклонного типу (КЦ7), що забезпечує уловлювання крапель при змісті рідини трохи більше 1 м3/м3, температурі не вище 80 °C, концентрації краплинної вологи після сепарації 70 мг/м3. Гідравлічне опір 350 Па і продуктивність КЦТ 1700−82 500 м3/ч.
Таблиця 3. Технічні характеристики скруббера Вентури.
|Типоразмер |Обсяг |Діаметр |Витрата |Тиск | | |газів на |горловины,|орошаемо|жидкости | | |виході, | |і |перед | | |m «/m |MM |жидкости|форсункой, | | | | |, м3/ч |кПа | |ГВПВ-0,006 |1700−3500 |85 |1,18−3,2|180−370 | |ГВПВ-0,03 |9320−18 900|200 |6,5−13 |60−250 | |ГВПВ-0,08 |23 460−4760|320 |16,8−45 |80−570 | | |0 | | | | |ГВПВ-0,140 |41 400−8400|420 |28,8−46 |130−320 | | |0 | | | |.
Скрубберы Вентури типу СВ-Кк (комплект скруббер-сепаратор, чи два) мають такі характеристики: |Обсяг очищаемых газів, м3/ч|50 000−500 000 | | | | |Витрата орошаемой рідини, |65−400 | |м3/ч |до 120 | |Температура очищаемых |до 10 000 | |газів, °З |0,5−3,5 | |Концентрація зважених |4−12 | |частинок, мг/м3 | | |Питома зрошення, м3/м3 | | |Гідравлічне | | |опір, кПа | |.
Створено скрубберы відцентрові, вертикальні, батарейные СЦВБ-20, щоб забезпечити продуктивність за газ 9000−20 000 м3/ч за нормальної температури не вище 60 °З, запиленості трохи більше 10 г/м3 і гідравлічному опір скрубберов 1,7 кПа.
Мокру очищення газів із часточками 2−3 мкм робити в скрубберах відцентрового типу СЦВП, у яких рідина дробиться безпосередньо запиленим газом. Шлам, осідає у нижній частині скруббера, виводиться эрлифтом в контейнер, а осветленная рідина знову повертається у скруббер. Продуктивність таких апаратів 5000−20 000 м /год, допустима запиленість 2 г/м3, температура газів 80 «З, гідравлічне опір 2,4 кПа, витрата води на очищення 0,05 м3/м3.
Розроблено скрубберы ударно-инерционного типу з пылеуловителями вентиляційними мокрими. Продуктивність таких скрубберов 3000—40 000 м3/ч. Запиленість газів 10 г/м, гідравлічне опір апарату 0,8- 2 кПа, витрата води 10−40 р на 1 м³ очищаемого воздуха.
Для хімічної очищення газів від сполук фтору із вмістом до 1 г/м3 можна рекомендувати скрубберы з кульової рухомий насадкою і порожнисті. Очищення виробляють розчинами гидроксида чи карбонату натрия.
Ефективність очищення газів від пилу залежить від дисперсности, щільності, схильність до слипанию, сипкості, абразивности, смачиваемости, гигроскопичности, розчинності та інших. Проте основним параметром під час виборів пылеуловителя є розмір частинок. Необхідно знати дисперсний склад пилу, задаваемый як таблиць чи інтегральних кривих. Гранулометрический склад більшості видів пилу підпорядковується нормально логарифмическому закону розподілу частинок за величиною. Ступінь очищення газів визначають по формуле:
[pic] де x — діаметр частинок пилу, мкм; dso — діаметр частинок пилу, що вловлюються в апараті на 50%; lg (rстандартне відхилення у функції розподілу частинок за величиною; lg (т — стандартне відхилення до функцій розподілу фракційних коефіцієнтів очистки.
Інтеграл Ф (х) табулирован. В. М. Ужовым та інших. складена таблиця для визначення значень Ф (х), відповідних різним значенням x [10].
З достатнім точністю дисперсию (геометричне стандартне відхилення) можна розрахувати по формуле:
[pic] де d16, d64 — діаметри часток отримують за змістом фракцій менше 16 і 84%.
Для перебування значень lg ((необхідно мати досвідчені дані про очищенні в пылеуловителях певної конструкції два види різної пыли.
[pic].
Рис. 14. Номограмма визначення ефективності уловлювання пилу в апаратах мокрою очищення газов.
По номограмме (рис. 14) визначають ефективність уловлювання пилу в апаратах мокрою очистки.
Номограмма побудована для значень dm і d50 пилу стандартної щільності (р = 1000 кг/м3. Перерахунок значень dm і d50 від реальної щільності (р до стандартної роблять за формуле:
[pic].
Встановлено залежність ступеня пылегазоочистки від енерговитрат [10]:
[pic]где Кгпитома енергія дотику, кДж/1000 м3 газів; b і доконстанти, зумовлені з дисперсного складу пилу, дозволяє розрахувати ефективність уловлювання пилу. Вероятностно-энергетический метод розрахунку мокрих пиловловників грунтується на узагальненої зависимости:
[pic] отриманої для стандартної щільності пилу рг = 1000 кг/м3 і в’язкості газів (r=18*10−6Пас.
Ця залежність можна використовувати для вибору способів очищення принципової конструкції скрубберов.
Задля чистоти чи знешкодження газоподібних відходів чи технологічних газів з метою добування їх супутніх (корисних) газоподібних компонентів широко використовують метод абсорбції. Абсорбція полягає в безпосередньому взаємодії газів з рідинами. Розрізняють фізичну абсорбцію, засновану на розчиненні газу рідини, і хемосорбцию, в основі якої лежить хімічна реакція між газом і рідким поглотителем.
Абсорбционной очищенні піддають газоподібні відходи, містять один чи кілька добуваних компонентів. Залежно від використовуваного абсорбента (табл. 4) та її селективності можна назвати або один компонент, або послідовно кілька. Через війну абсорбції отримують очищений на газ і насичений розчин, що має бути легко регенерируемым з метою добування потім із нього корисних газів і повернення його на стадію абсорбції [2].
Таблиця 4. Абсорбенты, застосовувані очищення відведених газів |Що Поглинаються |Абсорбенты | |компоненти | | |Оксиди азоту |Вода, водні розчини і суспензії: NaOH, Na2C03, | |N2Оз, NO5 |NaHCO3, КІН, К2СОз, КНСОз, Са (ОН)2, СаСОз, Мg (ОН)2,| | |МgСОз, Ва (ОН)2, ВаСОз, NН4HСОз | |Оксид азоту NO |Розчини FeCl2, FeSO4, Na2S203, NaHCO3, Na2S0з, | | |NaHS03 | |Діоксид сірки SO2 |Вода, водні розчини: Na2SO3 (18−25%-ные), NH40H | | |(5−15%-ные), Са (ОН)2 Na2C03 (15−20%-ные), NaOH | | |(15−25%-ные), КІН, (NH4)2SO3 (20−25%-ные), ZnS03, | | |К2СОз: суспензії СаО, МgО, СаСО3, ZnO, золи; | | |ксилидин — вода у відсотковому співвідношенні 1:1, | | |диметиланилинС6Нз (СНз)2NН2 | |Сірководень H2S |Водний растворNa2СОз+Nа3АsО4 (Nа2НАsОз); водний | | |розчин Аs2О3 (8−10 г/л)+NНз (1,2−1,5 | | |г/л)+(NН4)3АsОз (3,5−6 г/л); моноэтаноламин | | |(10−15%-ный розчин); розчини К3РО4 (40−50%-ный | | |розчин); розчини К3Р04 (40−50%-ные), NH4OH, | | |К2СОз, CaCN2, натрієва сіль | | |антрахинондисульфокислоты | |Оксид вуглецю СО|Жидкий азот; медно-аммиачные розчини [Сu (NНз)]nх | | |хСОСН | |Діоксид вуглецю |Водні розчини Na2C03, К2СОз, NaOH, КІН, Ca (OH)2, | |С02 |NH4OH, этаноламины RNH2, R2NH4 | |Хлор Cl2 |Розчини NaOH, КІН, Са (ОН)2, Na2C03, К2СОз, МgСОз, | | |СаСОз, Na2S203; тетрахлоридметан CCI4 | |Хлористий водород|Вода, розчини NaOH, КІН, Ca (OH)2, Na2C03, К2СОз | |НСl | | |Сполуки фтору |Na2C03, NaOH, Са (ОН)2 | |HF, SiF4 | |.
Вимоги, яким має задовольняти абсорбционная апаратура, випливають із фізичного уявлення явищ массопереноса в системах газ — рідина. Оскільки процес массопереноса протікає лежить на поверхні розділу фаз, то конструкціях апаратів треба її максимально развивать.
Для поверхневих абсорберов властиве конструктивно освічена поверхню, відповідно до якої пленочном режимі стікає абсорбент (рідина). Найпоширенішою конструкцією таких противоточных абсорберов є добре відомі насадочные. Як насадки застосовують кільця Рашига, кільця Палля, сідла Берля і той насадку. Насадочные апарати складні, оскільки необхідно створити опорну грати, зрошувачі, забезпечити ефективне уловлювання крапель абсорбента.
У распиливающих абсорберах межфазная поверхню утворюється дрібними краплями шляхом роздрібнення, розпорошення рідини. У обсязі апарату з допомогою форсунок створюються краплі, що із газовим потоком.
У механічних абсорберах рідина розпорошується внаслідок підвода ззовні механічної енергії, наприклад, обертання валків чи спеціальних розпилювачів. Ці конструкції досить сложны.
У поверхневих і распыливающих абсорберах суцільний фазою є газ, а розподіленої - рідина. У барботажных абсорберах в суцільному потоці рідини розподіляється газ, яка досягається на про тарілках. Режим, де працюють такі абсорбери, називають барботажным.
Під час створення промислових систем очищення газів абсорбционными методами необхідно розрізняти схеми з однеі багаторазовим використанням абсорбента. Останній схемою абсорбція узгоджується з десорбционными процесами. Однократне використання абсорбента притаманно процесів з низькою вартістю поглинача чи коли відразу після поглинання утворюється готовий (цільової) продукт. Позаяк у очищаемом газі міститься незначне кількість улавливаемого компонента, то здійснюється циркуляція абсорбента, але не матимуть його регенерации.
Розрахунок процесів абсорбції полягає в матеріальному балансі, з якого визначають видаткові параметри по абсорбенту й розміри апаратів. Обсяг очищаемого газу Gi відомий, відомий також і початкова концентрація поглощаемого компонента в газовому потоці yi й у абсорбенте, подаваемом на очищення, x1. Необхідно знати кінцеву концентрацію x2 абсорбента, тобто ступінь насичення потоку абсорбента L поглощаемым компонентом. Тоді кількість поглощаемого компонента Gk визначають по формуле:
[pic] де у2 — концентрація компонента в отходящем газовому потоці. Загальне рівняння матеріального балансу має вид:
[pic]Конечное зміст поглощаемого компонента у2 в газовому потоці має бути узгоджується з рівноважної концентрацією їх у рідини, яку визначають по формуле:
[pic]где Хг* - рівноважна концентрація компонента в рідини, відповідальна його змісту у газовій фазі у2; т — константа фазового рівноваги (константа Генри).
Визначення ефективності реальних апаратів має грунтуватися на кінетичних закономірності процесів массопередачи, які можна записати через швидкість розчинення газу рідини під час через поверхню контакту фаз F, м2:
[pic]Каждая із незалежних змінних (До — коефіцієнт массопередачи і А — рушійна сила процесу) залежить багатьох параметрів (технологічних режимів, конструкцій апаратів) і може вимірюватися у різних одиницях. Широко застосовують вираз для коефіцієнта массопередачи Ks як ставлення його на площу поверхні контакту фаз або до площі насадки, тарілки. Якщо у своїй рушійна сила виражена через дельта, кг/м3, то одиниця виміру Ks — м/с.
Коефіцієнт массопередачи відносять також обсягу апарату, одержуючи об'ємний коефіцієнт массопередачи Кv, с-1 чи ч-1:
[pic] де, а — питома поверхню контакту фаз.
Оскільки інтенсивність перенесення маси газової фазі (приватний коефіцієнт массоотдачи вг) й у рідкої (приватний коефіцієнт массоотдачи рж) різна, ті значення (р і (ж визначають з різних залежностям, та його співвідношення щодо різноманітних процесів також різна. Тоді вираз загального коефіцієнта массопередачи через приватні має вид:
[pic].
Співвідношення між 1/(г і 1/m (ж дозволяє визначити частку опору у газовій і переробки рідкої фазі залежно від т, яка від абсорбента, ступеня його насичення, температури і др.
Значення (р і (ж знаходять по експериментальним залежностям, рекомендуемым для певних конструкцій масообмінних аппаратов.
Що стосується прямолінійною рівноважної залежності й постійності рг і pж по висоті абсорбера кількість переданої массы.
[pic]или.
[pic]Последнее вираз називають числом одиниць перенесення. За аналогією з записом коефіцієнтів массопередачи можна записать.
[pic]где Nг і Nж — число одиниць перенесення у газовій і переробки рідкої фазах соответственно.
Кількість одиниць перенесення через об'ємні коефіцієнти массопередачи:
[pic]где Van — обсяг апарату; P. S — площа поперечного перерізу; М — висота аппарата.
Тоді висота аппарата.
[pic] причому G/(Kv) відповідає висоті апарату, котрій число одиниць перенесення одно одиниці і називається заввишки одиниці переноса.
Кількість одиниць перенесення N можна визначити графічно. Площа, обмежена кривою такому графіці, відповідає загальної кількості одиниць перенесення, а кут її нахилу дозволяє визначити константи b і к.
Суттєвим недоліком сорбционных методів очищення (абсорбційних і адсорбційних) выбросных газів необхідно многократной регенерації поглинаючих розчинів чи часткової заміни твердого сорбенту, що ускладнює технологічну схему, збільшує капітальні вкладення і їхньої витрати на эксплуатацию.
Комбіновані методи лікування й апаратура очищення газов.
Комбіновані методи лікування й апаратура очищення газів є дуже економічніші і найбільш високоефективними. Розглянемо конструкції апаратів і технологічну схему очищення з прикладу очищення запиленого повітря і газів стекольного производства.
Для обеспыливания процесів сушіння, подрібнення, просіювання, змішування і транспортування сировинних матеріалів розроблений гідродинамічний пылеуловитель ГДП-М (рис. 15) продуктивністю по очищаемому повітрю від 3000 до 40 000 м3/ч. Принцип роботи апарату грунтується на барботаже запиленого повітря (газу) через шар піни, образующейся на газорозподільної решітці. Решотка у своїй занурена в пылесмачивающую рідина. Запилений газ вступає у подрешеточное простір і, витіснивши на грати частина води, утворює у ньому шар высокотурбулентной піни. Пройшовши через отвори, газ очищається від пилу в останній момент контакту з пылесмачивающей рідиною. Очищений газовий потік вступає у відцентровий каплеотделитель, та був викидається у повітря. Пылеуловитель має такі характеристики: |Продуктивність, м3/ч |3000−40 000 | |Питома навантаження за газ, м3/(м2ч) |6500 | |Гідравлічне опір. Па |1400−1900 | |Температура очищаемых газів, °З |до 300 | |Витрата води на очищення 1000 м³ газу, |15−50 | |л |2,5 | |Настановний обсяг, м3 |120 | |Маса, кг | |.
Апарат ГДП-М максимальної ефективністю володіє другого ступеня очищення (після циклонів) газів від дрібнодисперсної пыли.
[pic].
Рис. 15. Гідродинамічний пылеуловитель ГДП-М:
1 — вхідний патрубок; 2 — газорозподільна решітка; 3 — корпус; 4 -каплеотделитель; 5 — вихідний патрубок; 6 — регулятор подачі води; 7 — разгрузочное устройство.
[pic].
Рис. 16. Схема очищення технологічних выбросов:
1 — залізничний вагон; 2 — прийомний бункер; 3 — щековая дробарка; 4.
— элеватор;
5 — сикатив барабан; б — дробарка; 7 — ситобурат; 8 — стрічковий конвеєр; 9 — отстойник;
10 — бункер сировини; 11 — ваги: 12 — змішувач шихти; 13 — бункер шихты;
14 — дюбель; 75 — циклон ЦН-15; 76- пылеуловитель ГДП-М.
На рис. 16 показаний одне із варіантів принципової схеми комплексної очищення технологічних викидів складових цехів (дозировочно-смесительных відділень). Вловлена циклоном пил повертається у видатковий бункер відповідного сировинного матеріалу. Шлам, утворений під час роботи мокрого пылеуловителя, обстоюється і висушується, після що може використовуватися як добавка до шихті після відповідної коригування її складу. Осветленная воду з відстійника повертається для використання в пылеуловитель.
Показники, що характеризують ефективність схеми очищення (зміст пилу в очищаемых газах знижується до нормувальних меж), наведені у табл. 5.
Таблиця 5. Ефективність комбінованої схеми очистки.
|Материал|Технолог|Количест|Запыленность г/м3 |Ступінь очищення, | | |ический |у | |% | | |процес |очищаемо| | | | | |го | | | | | |повітря,| | | | | |м3/ч | | | | | | |на |после|на |циклоно|пылеулов| | | | |вход|цикло|выходе|м ЦН-15|ителем | | | | |е |новий | | |ГДП-М | | | | | |ЦН-15| | | | |Пісок |Сушіння |7000 |30 |6,5 |0,036 |78,3 |99,38 | | |Просеива|2900 |21,4|5,1 |0,016 |76,1 |99,68 | | |ние | | | | | | | | |Дроблени|11 200 |18,3|5,8 |0,042 |68,3 |99,2 | | |е і | | | | | | | | |сушіння | | | | | | | |Доломіт |Просеива|3600 |21,9|4,8 |0,018 |78 |99,6 | | |ние | | | | | | | |Мел |Сушіння |29 530 |14,9|3,9 |0,066 |73,8 |98,3 | |Карбонат|Пневмотр|1900 |5,6 |2,5 |0,023 |55,4 |99,08 | |натрію |анспорти| | | | | | | | |рование | | | | | | | |Содосуль|Сушка |4000 |21,8|6,1 |0,023 |71,9 |99,62 | |фатная | | | | | | | | |суміш | | | | | | | | | |Просеива|2800 |22,8|4,3 |0,014 |81 |99,67 | | |ние | | | | | | | |Сырьевые|Транспор|2500 |30 |3,6 |0,012 |88 |99,66 | |компо |тировани| | | | | | | |ненты |е і | | | | | | | | |смешиван| | | | | | | | |не | | | | | | |.
1. Калыгин В. Г., Попов Ю. П. Порошкові технології: екологічна безпека продукції та ресурсозбереження. М.: Вид-во МГАХМ, 1996. 212 з. 2. Бондарева Т. И. Екологія хімічних виробництв. М.: Вид-во МИХМ,.
1986.92 з. 3. Устаткування, споруди, основи проектування хіміко-технологічних процесів захисту біосфери від промислових викидів/ АІ. Родіонов, Ю.П.
Кузнєцов, В. В. Зенков, Г. С. Соловйов. М.: Хімія, 1985. 352 із чотирьох. Газоочистные апарати сухого і мокрого типів. Каталог. М.: ЦИНТИХИМНЕФ;
ТЕМАШ, 1984.92с. 5. Керівні вказівки з проектування, виготовлення, монтажу і експлуатації циклонів НИИОГАЗ. Ярославль, 1971. 6. Степанов Г. Ю. Зицер І.М. Інерційні воздухоочистители. М.:
Машинобудування, 1986. 184с. 7. Алієв Г. М.-А. Техніка пиловловлювання і очищення промислових газов.
М.: 8. Металургія, 1986. 544 з. 9. Охорона навколишнього середовища/ C.D. Белоd, Ф. А. Барбинов, А. Ф. Козьяков та інших. М.: 10. Вищу школу, 1991. 319 з. 11. Страус У. Промислова очищення газів. М.: Хімія, 1981. 616 з. 12. Ужов В. М., Вальдберг О. Ю., Мягков Б.І. та інших. Очищення промислових газів від пилу. М.: Хімія, 1981. 392 с.