Расчет одноступінчастого редуктора
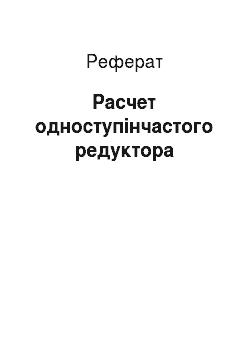
Недоліки зубчастих передач 1. Неможливість без ступенчатого зміни швидкості. 2. Високі вимоги до точності виготовлення й монтажу. 3. Шум на великих швидкостях. 4. Погані амортизаційні властивості, що негативно позначається на компенсацію динамічних навантажень. 5. Громіздкість на великих межосевых відстанях. 6. Потреба спеціальне устаткування і інструменті для нарізування зубів. 7. Зубчасті… Читати ще >
Расчет одноступінчастого редуктора (реферат, курсова, диплом, контрольна)
Технічне задание.
Вихідні данные:
Т = 18 Н*м.
(= 56 рад/с d = 0.55 м.
схема 1 1. Електродвигун 2. Пружна муфта 3. Редуктор з прямозубой конічній передачею 4. Відкрита конічна передача 5. Картофеле-очистительная машина Задание: Розрахувати одноступінчатий редуктор з прямозубой конічній передачею. Накреслити складальний чертёж редуктора, робочі креслення зубчастого колеса і відомого вала.
Призначення і порівняльна характеристика привода.
Цей привід використовують у картофелеочистительной машині. Прихід включає у собі електричний двигун, відкриту циліндричну косозубую передачу, одноступінчатий конічний редуктор, потрібного розрахувати і спроектувати у цьому курсовому проекте.
Редуктором називається механізм, що з зубчастих чи червячных передач, виконаний у вигляді окремого агрегату і службовець передачі потужності від двигуна до робочої машині. Кінематична схема приводу може включати, крім редуктора, відкриті зубчасті передачі, ланцюгову чи ремённую. Призначення редуктора зниження кутовий швидкості і підвищення обертального моменту відомого валу проти валом провідним. Редуктор складається з корпусу, у якому поміщають елементи передачі - зубчасті колеса, вали підшипники і т.д.
Зубчасті передачі Найчастіше використовують циліндричні і конічні передачі з прямими і косыми зубами. Крім цих передач використовують гвинтові, і передачі з шевронными і криволинейными зубьями.
Переваги зубчастих передач 1. Сталість передатного числа (для прямозубой циліндричною U=2(4, косозубой циліндричною U=4(6, для конічній U=2(3) 2. Висока нагрузочная здатність 3. Високий ККД (0.96(0.99) 4. Малі габарити 5. Велика довговічність, міцність, надійність, простота в обслуговуванні 6. Порівняно малі навантаження на вали і опоры.
Недоліки зубчастих передач 1. Неможливість без ступенчатого зміни швидкості. 2. Високі вимоги до точності виготовлення й монтажу. 3. Шум на великих швидкостях. 4. Погані амортизаційні властивості, що негативно позначається на компенсацію динамічних навантажень. 5. Громіздкість на великих межосевых відстанях. 6. Потреба спеціальне устаткування і інструменті для нарізування зубів. 7. Зубчасті передачі не захищають від небезпечних навантажень Конічні передачі проти циліндричними найбільш складні в виготовленні і монтажі т.к. їм потрібна велика точность.
1. Вибір електродвигуна і кінематичний розрахунок. 1.1 Визначаємо необхідну потужність двигателя.
N=N*((Вт) Т=Твых=Т3.
N=56*18=1008 Bт 1.2 Визначаємо КПД.
(=(р*(оп*пк р-редуктора.
(=0,97*0,96*0,9[pic]=0,679 оп-открытой передачи пк-подшипников качения 1.3 Визначаємо потужність двигателя.
[pic] 1.4 Вибираємо ел. Двигун з условия.
Nн (Nдв Nн=1.5 кВт 4А80А2У3 Nн=1.5 кВт nс=3000.
Номінальною потужності 1.5 кВт відповідає чотири виду двигунів (таблиця 1) таблиця 1 | N (| Типорозмір | nc, об./хв | | 1 | 4А80А2У3 | 3000 | | 2 | 4А80В493 | 1500 | | 3 | 4A90L693 | 1000 | | 4 | 4A100L893 | 750 |.
1.5 Визначаємо передатне ставлення двигателя.
[pic], де nдв — синхронна частота обертання, Об./хв; nвых — частота обертання вихідного валу механізму (вал З, див схему 1), Об/мин.
[pic] [pic].
[pic] [pic] 1.6 Задаёмся передаточным ставленням відкритої передачі u = 2(3 1.7 Визначаємо передатне ставлення редуктора Передатне ставлення редуктора повинно входити у проміжок для конічній прямозубой передачі U=2(3.
[pic], де U — передатне ставлення двигателя.
Uоп — передатне ставлення відкритої передачи.
Uр — передатне ставлення редуктора [pic] [pic] Зупинимо свій вибір двигуні N (1, і приймемо такі передавальні відносини: uдв = 5,6 uр = 2,8 uоп = 2 Ескіз двигуна при застосуванні 1. 1.8 Визначаємо крутящие моменти які діють валах передатних меанизмов. [pic].
[pic] 1.9 Визначаємо кутову швидкість на валах передатного механизма.
[pic] Перевірка: Nдв=Тдв*(дв.
Nдв=4,73*313,6=1483 Вт Двигун 4А80А2У3 1.10 Виконуємо зворотний пересчёт Т3, (3 з урахуванням обраного двигуна [pic] [pic] [pic] [pic] [pic] Перевірка Nдв=Тдв*(дв.
Nдв=4.19*56=1500 Вт Надалі вестимемо розрахунки з урахуванням отриманих значень 1.11 Визначення частоти обертання валів передатного механізму n1 = nc = 3000 об./хв [pic] Дані розрахунків сведём в таблицю: таблиця 2 | |Тi, Н*м |(і, рад/с |ni, об./хв | |Вал, А |4.78 |314 |3000 | |Вал У |9.08 |157 |1071 | |Вал З |24 |56 |535 |.
2. Геометричний прочностной розрахунок закритою передачі. 2.1 Вибираємо материал.
Для шестерні і колеса вибираємо сталь углеродистую якісну 45; У розділі ст 45, на яку допускаемое напруга на вигині для нереверсивных навантажень ((0(=122 МПа, допускаемое контактне напруга (((=550 МПа.
;
рис1. Передача конічними зубцюватими колесами 2.2 Визначаємо зовнішній ділильний діаметр (див. Мал.1) коефіцієнт КН (=1,2 коефіцієнт ширини віденця стосовно зовнішньому конусному відстані (ВRE=0,285.
[pic] (1(, де Тр — момент на вихідному валу редуктора (табл. 2); de2 — зовнішній ділильний діаметр, мм;
(((до — допускаемое контактне напруга, МПа; up — передатне ставлення редуктора;
Приймаємо по ГОСТ 12 289–76 найближче стандартне значення de2=100мм 2.3 Приймаємо число зубів на шестерне.
Z1=22 2.4 Визначаємо число зубів на колесе.
Z2=uр*Z1=2,8*22=62 (1(Визначаємо геометричні параметри звичайною зубчастою передачі 2.5 Зовнішній окружної модуль.
[pic] (1(2.6 Кут делительного конуса для (див. Мал.1): шестерні [pic] колеса [pic].
2.7 Визначаємо зовнішній діаметр шестерні і колеса (див. Рис.1).
[pic] 2.8 Визначаємо зовнішнє конусное відстань (див. Рис.1).
[pic] (1(2.9 Визначаємо середнє конусное відстань (див. Рис.1).
[pic], де b — довжина зуба 2.10 Визначаємо середній окружної модуль.
[pic] 2.11 Визначаємо середній ділильний діаметр шестерні і колеса (див. Мал.1) d=m*Z (1(d1=1.3*22=28.6 мм d2=1.3*62=80.6 мм 2.12 Визначаємо зусилля чинне в зацеплении окружне колеса.
[pic] шестерни.
[pic], де Т — крутний момент на вихідному валу; d — середній ділильний діаметр радіальне [pic] [pic], де Р — окружне зусилля, (- кут делительного конуса, (= 20(.
Перевірка коефіцієнт ширини шестерні за середнім диаметру.
[pic] (1(середня окружна швидкість колеса.
[pic] (1(ступінь точності n=7 Для перевірки контактних напруг визначаємо коефіцієнти нагрузок.
[pic] (1(, де КН (- коефіцієнт враховує розподіл навантаження за довжиною зуба; КН (- коефіцієнт враховує розподіл навантаження між прямими зубами; КНV — коефіцієнт враховує динамічну навантаження в зацеплении для прямозубых колёс.
[pic] (1(.
Перевірку контактних напруг виконаємо за такою формулою: [pic].
Перевірка зубів на витривалість по напругам изгиба.
[pic] (1(, де коефіцієнт нагрузок.
[pic], де КF (- коефіцієнт концентрації навантаження; КFV — коефіцієнт динамічності Y — коефіцієнт форми зубів вибираємо залежно від еквівалентних чисел зубів: для шестерни.
[pic] для колеса.
[pic] За цих значеннях ZV вибираємо YF1 = 3.976, YF2 = 3.6 Для шестерні отношение.
[pic] для колеса.
[pic] Подальший розрахунок ведемо для зубів шестерні, т.к. отримане ставлення для нього менше. Перевіряємо зуб колеса.
[pic].
3. Розробка эскизной компонування. 3.1 Попередній розрахунок валів редуктора.
Розрахунок виконуємо на крутіння по зниженим допускаемым напругам Крутящие моменти в поперечних перетинах валів: ведучого Тк1=Т1=9000 Нм відомого Тк2=Т2=24 000 Нм Діаметр вихідного кінця валу dв1 (див. рис. 3) визначаємо при допускаемом напрузі ((к (=25 МПа.
[pic] (1(діаметр під підшипниками приймемо dп1=17 мм; діаметр під шестірнею dк1=20 мм. Діаметр вихідного кінця валу dв2 (див. рис. 4) при допускаемом напрузі ((к (=25 МПа.
[pic] діаметр під підшипниками приймемо dп2=20 мм; діаметр під зубцюватим колесом dк2=25 мм. 3.2 Конструктивні розміри шестерні і колеса Шестірня Порівняно невеликі розміри шестерні стосовно діаметру валу дозволяють не виділяти маточину (див. рис. 3). Довжина посадкового ділянки lст (b=20 мм Колесо його розміри dае2=101.1 мм; b=20 мм діаметр маточини dст (1.6*dк2=1.6*25=40 мм; довжина маточини lст = (1.2(1.5)* dк2=1.5*25=37.5 мм lст = 35 мм товщина обода.
(0 =(3(4)*m=1.3*(3(4)=5 мм рис2. Конічне зубцювате товщина диска С=(0,1(0,17)*Rе=7 мм колесо 3.3 Kонструктивные розміри корпусу редуктора товщина стінок корпуси та кришки (= 0,05*Rе+1=3,65 мм; приймаємо (= 5 мм (1=0,04*Rе+1=3,12 мм; приймаємо (1 = 5 мм товщина фланців (поясів) корпуси та кришки: верхнього пояса корпуси та пояса кришки b=1,5*(=1,5*5=7,5 мм b1=1,5*(1=1,5*5=7,5 мм нижнього пояса кришки р=2,35*(=2,35*5=11,75 мм; приймаємо р=12 мм Діаметри болтів: фундаментальних d1=0,055*R1+12=12,3 мм; приймаємо фундаментальні болти з різьбленням М12 болтів, крепящих кришку до корпусу у підшипника, d2=(0,7(0,5)* d1 d1=(0,7(0,5)*12,3=8,6(6,15 мм; приймаємо болти різьблені М8 болтів, що з'єднують кришку з корпусом, d3=(0,7(0,5)* d1 d3=6(7,2 мм; приймаємо болти різьблені М6 3.4 Компонування редуктора.
Проводимо посередині аркуша горизонтальну осьову лінію — вісь ведучого валу. Намічаємо становище вертикальної осьової лінії - осі відомого валу. З точки перетину проводимо під (1 = 20(осьові лінії ділильних конусів і відкладаємо ними відтинки Re = 53 мм.
Конструктивно оформляємо по знайденим вище розмірам шестірню і колесо. Вычерчиваем в зацеплении. Підшипники валів розташуємо стаканах.
Попередньо намічаємо для валів роликоподшипники конічні однорядные. З огляду на невеликі розміри редуктора приймаємо легкі серію подшипников.
|Условное | d | D | B | З | Co | |позначення |мм |мм |мм |кН |кН | |підшипника | | | | | | |7203 |17 |40 |12 |14.0 |9.0 | |7204 |20 |47 |14 |21.0 |13.0 |.
Наносим габарити підшипників ведучого валу, намітивши попередньо внутрішню стінку корпусу з відривом 10 мм від торця шестерні і відклавши зазор між стінкою корпуси та центром підшипника 10 мм (розміщувати мазеудерживающего кільця). Другий підшипник розміщаємо з відривом від першого рівному 2.5*dв1=2,5*13=32.5 мм (2(, де dв1 — діаметр вихідного кінця ведучого вала.
Розміщаємо підшипники відомого валу, намітивши попередньо внутрішню стінку корпусу з відривом 10 мм від торця маточини колеса і відклавши відстань між стінкою корпуси та центром підшипника 10 мм.
Вимірюванням визначаємо відстані a1=30 мм; a2=48 мм; a3=33 мм; a4=64 мм.
4. Перевірка довговічності подшипников.
Ведучий вал.
Расчётная схема.
a1=30 мм а2=48 мм Рr1=203.5 Н.
Pa1=74 Н.
P=1678.3 Н.
Визначення реакцій опор в вертикальної плоскости.
[pic].
[pic].
[pic].
[pic] рис. 3 Расчётная схема ведучого вала.
[pic] Проверка:
[pic].
Визначення реакцій опор горизонтальної плоскости.
[pic].
[pic] Проверка:
[pic] Визначення еквівалентних нагрузок.
[pic] (3(, де X, Y — коефіцієнти радіальної і осьової навантажень відповідно; Kv — коефіцієнт враховує обертання кілець підшипників; Fr — радіальна навантаження, М; КБ — коефіцієнт безпеки; Кт — температурний коэффициент.
[pic], де Нi, Vi — реакції опор в горизонтальній і вертикальної площинах відповідно, Н.
[pic].
Осьові складові радіальних реакцій конічних подшипников.
[pic] (1(тут для підшипників 7203 параметр осьового навантаження e = 0.31 У нашому випадку S1(S2; Fa (0, тоді Pa1=S1=706.2 H.
Pa2=S1+Pa=271+74=345 H [pic].
X=0.4 Y=1.97.
[pic].
Расчётная довговічність, млн. об.
[pic].
Расчётная довговічність, ч.
[pic], де n = 1500 частота обертання ведучого вала.
Розрахунок відомого вала.
[pic].
Визначення реакцій опор в вертикальної плоскости.
[pic].
[pic].
[pic].
[pic] рис. 4 Расчётная схема відомого валу. [pic] [pic] [pic] Проверка:
[pic].
[pic] [pic].
Визначення реакцій опор горизонтальної плоскости.
[pic].
[pic].
[pic] [pic] [pic] [pic] Проверка:
[pic].
[pic].
Осьові складові радіальних реакцій конічних подшипников.
[pic] У нашому випадку S1(S2; Fa (0, тоді Pa1=S1=63 H.
Pa2=S1+Pa1=63+203.5=266.5 H.
Позаяк у ролі опор відомого валу застосовані однакові підшипники 7204, то довговічність визначимо ще навантаженого підшипника. [pic], у цій осьову навантаження слід учитывать.
Еквівалентна нагрузка.
Pэ=0.4*515.7+1.67*266.5=0.7 кН.
Расчётная довговічність, млн. об.
[pic] (1(.
Расчётная довговічність, год тут n = 536 об./хв — частота обертання відомого вала.
[pic].
Полученная довговічність більш необхідної. Підшипники приемлемы.
5. Уточнённый розрахунок валов.
Нормальні напруги від вигину змінюються по симетричному циклу, а касательные від крутіння по пульсуючому 5.1 Вибір матеріалу валу Попередньо приймемо углеродистую сталь звичайного якості, Ст5, для якої межа тимчасового опору (b=500 МПа 5.2 Визначення изгибающих моментів Ведучий вал.
У ведучого валу визначати коефіцієнт запасу міцності у кількох перетинах недоцільно, досить вибрати одне перетин з найменшою коефіцієнтом запасу, саме перетин на місці посадки підшипника, найближчого до шестірні (див. Рис.3). У цьому вся небезпечному сечении діють максимальні изгибающие моменти My і Mx і крутний момент Mz = Т2. Концентрація напруг викликана напрессовкой внутрішнього кільця підшипника на вал. a1=14 мм; а2=48 мм.
Рr=203,5 Н;
Ра=74 М ;
Р=1678,3 Н.
Vа=308,5 Н;
Vв=105 Н;
Hа=2727,2 Н;
Hв=1048,9 Н;
Ma=10,582 Н*м.
Побудова эпюры Мy (рис. 5).
0(y (a1 My=-Pa*x+Ma; y=0 My=Ma y=a1 My=- Pr*a+Ma=-50,468 Н*м.
0(y (a2 My=-Vв*y=-50,468 Н*м.
Побудова эпюры Мx (рис. 5).
0(x (a1 Mx=-P*x.
0(x (a2 Mx=-Hв*x x=0 Mx=0 x=a1 Mx=- P*a1=-50,349 Н*м x=0 Mx=0 рис. 5 Эпюры моментів x=a2 Mx=- Hв*a2=-50,349 Н*м Ведений вал а3=33 мм; а4=64 мм.
Рr=74 Н;
Ра=203,5 Н;
Р=595,5 Н.
Vа=133,4 Н;
Vв=-59,4 Н;
Hа=393,9 Н;
Hв=202 Н;
Ma=82,0105 Н*м.
Побудова эпюры Мy (рис. 6).
0(y (a3 My=Vв*y y=0 My=0 y=a3 My=Va*a3=44,022 Н*м.
0(y (a4 My=Vв*y y=0 My=0 y=a4 My=Va*a4=-38,016 Н*м.
Побудова эпюры Мx (рис. 6).
0(x (a3 Mx=-Ha*x x=0 Mx=0 x=a3 Mx=- Ha*a3=-129,657 Н*м.
0(x (a4 Mx=-Hв*x x=0 Mx=0 рис. 6 Эпюры моментів x=a4 Mx=- Hв*a4=-129,657 Н*м 5.3 Визначення сумарного изгибающего моменту у небезпечному сечении [pic] 5.4 Визначення осьового моменту опору перерізу [pic](1(5.5 Амплітуда нормальних напруг [pic] (1(5.6 Визначення полярного моменту опору [pic] 5.7 Визначення амплітуди касательного напруги [pic] 5.9 Визначення коефіцієнтів запасів прочности.
1 по нормальному напряжению.
[pic], где (v — амплітуда нормальних напруг; До (- ефективний коефіцієнт концентрації нормальних напруг; ((- масштабний чинник для нормальних напруг; (- коефіцієнт враховує вплив шорсткості поверхні (= 0.97(0.9.
2 по касательному напряжению.
[pic], де (-1 — межа витривалості стали за симетричного циклі крутіння; k (- коефіцієнт концентрації напруг; ((- масштабний чинник; (- амплітуда дотичних напруг, МПа; (- коефіцієнт, враховує вплив шорсткості поверхні; ((- коефіцієнт асиметрії циклу; (m — середнє амплітуди дотичних напруг, МПа. 5.10 Визначення загального коефіцієнта запасу прочности.
[pic].
6. Вибір типу кріплення валу на колесе.
Розрахунок сполук. 6.1 Вибір материала.
Як матеріалу шпонки приймемо сталь углеродистую звичайного якості Ст6, на яку допускаемое напруга на смятие (((см=70(100 МПа, допускаемое напруга на зріз (((ср=0,6*(((см=42 МПа 6.2 Геометричні розміри шпонки.
b=5 мм;
h=5 мм; t1=3.0 мм;
t2=2.3 мм; lш=lст2- (5(10)=28 мм, де lст2 — довжина маточини, мм lш — довжина шпонки, мм клавіша 5(5(28 ГОСТ 23 360–78 6.3 Перевірка шпонки на смятие.
[pic], де Т3 — крутний момент на валу З, Н*м (таблиця 2); dк — діаметр валу під колесо, мм; h — висота шпонки, мм; b — ширина шпонки, мм; lш — довжина шпонки, мм.
[pic] візьмемо з закруглёнными кінцями lp=28−5=23 мм беремо 20 мм 6.4 Перевірка шпонки на зріз [pic].
7. Вибір і аналіз посадок 1 Вибираємо посадки.
Приймемо посадки відповідно до таблиці 4 таблиця 4 |Зубцювате колесо на вал |[pic] | |Распорная втулка на вал |[pic] | |Торцевые кришки на ПК |[pic] | |Внутрішні кільця ПК на вали |[pic] | |Зовнішні кільця ПК в корпусі |[pic] | |Ущільнення на вали |[pic] |.
Виконаємо аналіз посадки Н7/m6 7.2 Визначення граничних відхилень отворів на колесі D=25 (Н7) ES=+21 мкм.
EI=0 мкм 7.3 Визначення граничних відхилень валу d=25 (m6) es=+21 мкм ei=+8 мкм 7.4 Визначення max значення натяга.
Nmax=es-EI=21−0=21 мкм 7.5 Визначення max значення зазору Smax = ES-ei = 21−8=13 мкм 7.6 Визначення допусков.
7.6.1. на отверстие.
ТD=ES=EI=21−0=21 мкм.
7.6.2 на вал.
Тd=es-ei=21−8=13 мкм 7.7 Визначення граничних размеров.
Dmax=D+ES=25+0.021=25.021 мм.
Dmin=D+EI=15 мм dmax=d+es=25+0.021=25.021 мм dmin=d+ei=25+0.008=25.008 мм 7.8 Побудуємо схему допусков.
8. Вибір муфт. Вибір ущільнень. 1 Вибір муфты.
Візьмемо муфту пружну втулочно-пальциевую (МУВП). Ця муфта є найбільш поширеної муфтою з неметаллическими пружними елементами — гумою; має хорошою еластичність, демпфирующей электроизоляционной способностью.
1 Поводить момент на валу электродвигателя.
[pic] 2 При ударної навантаженні приймаємо коефіцієнт режиму роботи муфти К=4 3 Расчётный поводить момент.
[pic] 8.1.4 По нормальний МН-2096;64 вибираємо муфту МУВП-16 (див. табл. 5) таблиця 5 | d, | D, |L, мм | D1, | z | dп, | lп,| lв,|(Мрас (| (,. | | |мм | |мм | |мм | | |Н*м |рад/с | |мм | | | | | |мм |мм | | | | 13 | 90 | 84 | 58 | 4 | 10 | 19 | 15 | 31.4 | 660 |.
8.1.5 Перевіряємо пальці на изгиб.
[pic] 8.1.6 Перевіряємо гумові чопи на смятие.
[pic] Обрана муфта задовольняє умові міцності 2 Вибір уплотнений.
Виберемо ущільнення підшипників качения залежно від окружної швидкості валов.
Ведучий вал.
[pic], де (- кутова швидкість ведучого валу, рад/с; d — діаметр вихідного кінця ведучого валу, мм.
Оскільки (1.