Исследование горячеломкости ливарних сплавів з урахуванням систем Al-Si, Al-Cu, Al-Si-Cu
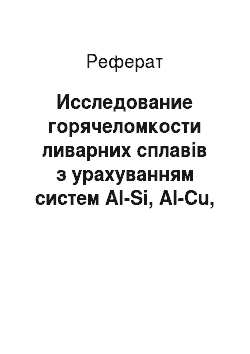
Кристаллизационная тріщина у принципі може повинна розвиватися у довжину як і інтервалі кристалізації, і за нормальної температури нижче солидуса. Тому природно постає запитання, як і у тому, що у кільцевої пробі вимірюється довжина тріщин суто кристаллизационного походження. Фрактологический аналіз численних кільцевих проб із різноманітних кольорових сплавів наочно показала, що у гнітючому вона… Читати ще >
Исследование горячеломкости ливарних сплавів з урахуванням систем Al-Si, Al-Cu, Al-Si-Cu (реферат, курсова, диплом, контрольна)
Введение
…3.
Глава 1. Огляд литературы.
1. Вплив складу і структури на горячеломкость при лиття сплавов…5.
1. Вплив форми і збільшення розмірів зерен на горячеломкость…5.
2. Вплив газосодержания сплавів на горячеломкость…9.
3. Вплив складу сплавів на горячеломкость…12.
4. Вплив зональної ликвации на горячеломкость…17.
5. Вплив домішок на горячеломкость…17.
2. Шляхи зниження горячеломкости сплавов…19.
1. Перший шлях зниження горячеломкости — вибір оптимального состава…19.
2. Другий засіб зниження горячеломкости — регулювання змісту основних компонентов…23.
3. Третій шлях зниження горячеломкости — регулювання змісту домішок в сплаве…23.
4. Четверте шлях зниження горячеломкости — введення у сплав малих технологічних добавок…23.
3. Ливарні проби на горячеломкость…26.
1. Перша група проб…26 1.3.1.1 Стандартна кільцева проба на горячеломкость…30.
2. Друга ж група проб…30.
3. Третю групу проб…32.
4. Характеристика деяких алюмінієвих сплавов…37.
1. Сплави з урахуванням алюминий-кремний…37.
2. Сплави з урахуванням алюминий-медь…39.
3. Сплави з урахуванням алюминий-кремний-медь…41 Глава 2. Експериментальна частина 2.1. Методика приготування досвідчених сплавов…43 2.2. Дослідження горячеломкости сплавів систем Al-Si, Al-Cu, Al-Si-Cu за показниками технологічних проб…43 2.3. Методика проведення диференціального термічного аналізу досліджуваних сплавов…51 2.4. Аналіз параметрів кристаллизационного процесса…54 Вывод…57 Литература…58.
ВВЕДЕНИЕ
Развитие сучасної науку й техніки показало, що важливою складовою технологічного продукування є якісні показники одержуваної продукції. Пріоритетними заходами є: збільшення міцності, збільшення діапазону робочих температур, збільшення терміну служби матеріалів. У цьому роботі буде розглянуто і досліджувана явище, яке безпосередньо з прочностными показниками одержуваних у виробничому процесі матеріалів. Ідеться про явище горячеломкости металів і сплавов.
Горячеломкость — схильність металів і сплавів до тендітному межкристаллитному руйнації за наявності рідкої фази на межі зерен. Таке руйнація поширене при лиття і зварюванні; воно зустрічається також за гарячої обробці тиском, термічній обробці і експлуатації виробів при підвищених температурах.
Усі метали і сплави у тому чи іншою мірою горячеломки. Добре відома красноломкость сталей і нікелевих сплавів, обумовлена оплавленням сульфидной эвтектики, є приватною випадком горячеломкости при гарячої обробці тиском. При термічній обробці сплавів горячеломкость проявляється у освіті закалочных тріщин через оплавлення кордонів зерен при пережоге. Незначні домішки металів, що утворюють легкоплавкие эвтектики на межі зерен, знижують жаропрочность і термостойкость легованих сталей, нікелевих та інших сплавів і може призвести до тендітному межкристаллитному руйнації виробів під час експлуатації при підвищених температурах.
При лиття і зварюванні горячеломкость сплаву проявляється у освіті так званих «гарячих» тріщин у зливках, фасонных отливках і зварних швах. Гарячі тріщини — одне з найбільш поширених як важко переборних видів шлюбу. Якщо оплавлення кордонів зерен при гарячої обробці тиском, термообработке і експлуатації виробів можна більш-менш легко запобігти, очищаючи метав від легкоплавких домішок, вводячи у нього малі добавки для зв’язування цих домішок в тугоплавкі сполуки чи, нарешті, просто обмежуючи температуру нагріву точкою солидуса кордонів зерен, то, при лиття і зварюванні плавленням перехід через інтервал кристалізації завжди неминучий. Тому горячеломкость найчастіше проявляється у двох останніх процесах. Проблема гарячих тріщин придбала особливо більшої гостроти у зв’язку з розвитком виробництва нових високоміцних і жароміцних сплавів, оскільки області складів на діаграмах стану, відповідні максимальної міці й жаропрочности, часто збігаються із ділянкою складів найбільш горячеломких сплавів. До того ж шлюб по гарячим тріщинам частіше виникає при найпрогресивніших видах лиття: безупинному лиття зливків і литві деталей в постійні формы.
Різко виражена горячеломкость сплавів при лиття і зварюванні сильно ускладнює, а часто чинить і практично неможливим запровадження у серійне виробництво нових сплавів із цінними експлуатаційними властивостями. У неперервному зв’язку з цим необхідний такий науково обгрунтований підхід до розробки нові й поліпшенню існуючих сплавів, у якому поруч із отриманням високої міцності, жаропрочности та інших експлуатаційних властивостей забезпечувалася б висока опірність сплавів освіті гарячих трещин.
Як показано нижче, гарячі тріщини при лиття більшості промислових кольорових сплавів є кристаллизационными — вони зароджуються і розвиваються в «ефективному» інтервалі кристалізації. У цьому вся інтервалі кристаллиты утворюють каркас з распределённой усередині нього рідкої фазою, і сплав має основним властивістю твердого тіла зберігати раніше додану йому форму. Такий стан сплавів було умовно названо твёрдо-жидким. Вище деякою температурі в інтервалі кристалізації рідка фаза повністю відокремлює друг від друга кристаллиты, і сплав має основним властивістю рідкого тіла — підвищеної плинністю. Цей стан сплаву на відміну попереднього, було умовно названо жидко-твёрдым.
Суперечливість проблеми гарячих тріщин зумовлено переважно тим, що горячеломкость — властивість технологічне як і всяке технологічне властивість, є комплексним, сложносоставным, залежать від перебігу в металі одночасно кількох «елементарних» процесів. Будь-яка технологічна проба на горячеломкость, як би вона була пристосована до місцевих умов конкретної виробничої завдання, не може у чистому вигляді виявити ті елементарні процеси та відповідно ті «складові» властивості сплаву, комплекс визначає його горячеломкость. Для визначення властивостей сплаву, що у твердорідкому стані, зазвичай непридатні методи і установки, використовувані для вивчення сплавів в твердому чи рідкому стані. Необхідно застосовувати методи і прилади, спеціально призначені з вивчення тих властивостей сплаву в твёрдо-жидком стані, сукупність визначає його горячеломкость.
На схильність сплаву до утворення кристаллизационных тріщин, як і схильність до іншого руйнації, визначальний влив мають надавати механічні властивості в температурному інтервалі освіти цих тріщин. Тому, за аналізі горячеломкости основну увагу слід звернути на вивчення механічних властивостей і закономірності пластичної деформації і руйнації сплавів в твёрдо-жидком стані. Але аналіз горячеломкости, в загальному разі, не можна зводити до вивчення лише механічних властивостей: горячеломкость, що виявляється при лиття і зварюванні, залежить також термічного стискування, лінійної усадки в інтервалі кристаллизации.
ГЛАВА 1. ОГЛЯД ЛИТЕРАТУРЫ.
1.1. ВПЛИВ СОСТАВА І СТРУКТУРЫ НА ГОРЯЧЕЛОМКОСТЬ ПРИ ЛИТТЯ СПЛАВОВ.
1.1.1. Вплив форми і середніх розмірів зерен на горячеломкость Здрібнення зерна — це з добре відомих способів усунення шлюбу по гарячим тріщинам у зливках, фасонных отливках і зварних швах. Зменшення розмірів зерен і особливо перехід від столбчатой структури до равноосной в литом сплаві, по-перше, звужують температурний інтервал тендітності і підвищують відносне подовження у ньому, а, по-друге, знижують температуру початку лінійної усадки в ефективному інтервалі кристалізації. Підвищення відносного подовження і зменшення лінійної усадки при подрібнюванні зерна діють у одному напрямку: обидві ці чинника, посилюючи одне одного, збільшують запас пластичності сплаву в твёрдо-жидком безпечному стані і цим знижують горячеломкость. Вплив форми і середніх розмірів зерна на горячеломкость в чистому вигляді який завжди можна виявити, оскільки одночасно з їхнім зміною під впливом тих чи інших чинників може змінитися, й микростроение кордонів зерен, і навіть інтервал кристалізації, темп кристалізації і газосодержание.
Найпростіше виявлення форми і дрібних розмірів зерен на горячеломкость виявляється за зміни перегріву розплаву. Зі збільшенням перегріву розплаву зерно укрупнюється і равноосная структура прагне перейти в столбчатую, у результаті запас пластичності в твёрдо-жидком стані знижується, а горячеломкость зростає (малюнок 1).
Збільшення тривалості чекання розплаву він може призвести до значному укрупнення збіжжя і посиленню горячеломкости. Збільшення тривалості чекання в електропечі з 20 хвилин до 10 годин укрупнило збіжжя та призвело до появи тріщин в зливку полунепрерывного лиття з сплаву АК6. Випробування на розрив зразків, вирізані з зливків, виявили сильне зниження подовження в твёрдо;
[pic].
Рис. 1 Залежність показника горячеломкости (ПГ) сплаву алюмінію із чотирьох% Cu від розміру зерна (?) при різному перегрів расплава.
жидком безпечному стані і розширення інтервалу тендітності при выстаивании розплаву. Посилення горячеломкости зі збільшенням тривалості чекання розплаву іноді пов’язують із підвищенням газосодержания. Але, по-перше, досліди показують, що, залежно від природи сплаву, його вихідного газосодержания і атмосфери печі выстаивание може лише дозволило підвищити, а й підвищити газосодержание. Саме ця спостерігалося у щойно згаданому прикладі зі сплавом АК6. Досліди проводились цехових умовах. Шихта складалася з відходів пресового цеху, загрязнённых олією, і свежерасплавленный метал мав підвищену газосодержание. Десятичасовое выстаивание розплаву знизило зміст водню з 0.30 до 0.19 см3 /100 р, збільшило щільність зливків з 2.786 до 2.797 і зменшило середню товщину кордонів зерен лежить на поверхні проб, відлитих на дзеркальну плиту, з 6.8 до 4.6 мкм. По-друге, якщо газосодержание і підвищується, то горячеломкость повинна падати, а чи не зростати. Оскільки зазвичай горячеломкость зі збільшенням тривалості чекання зростає, це означатиме, що або выстаивание знижує газосодержание, або ж выстаивание підвищує газосодержание, але сприятливо впливає цього чинника на горячеломкость перекривається негативним дією укрупнення структуры.
Через неминучих коливань температури розплаву, різного змісту домішок і неконтрольованих включень й на інших причин у різних плавках одного сплаву виходить різна структура. Горячеломкость багатьох сплавів чуйно реагує на коливання розміру зерна, одержувані у різних плавках (малюнок 2). Одержання мелкозернистой структури зниження горячеломкости часто досягається модифицированием сплаву малими добавками, наприклад запровадженням титану в алюмінієві сплави. Слід зазначити також, що запровадження модифікатора може лише подрібнити зерно, а й змінити кількість і характер розподілу рідкої фази на межі зерен, а останній чинник іноді має вирішальний і обов’язково сприятливо впливає на горячеломкость.
Зниження горячеломкости при вібрації під час кристалізації частково завдяки подрібнюванню зерна, проте питому вагу цього чинника важко сказати, оскільки вібрація одночасно посилює залечивание трещин.
На розмір зерна, як відомо, сильний вплив надають домішки і легирующие елементи. Виливки з чистих металів зазвичай мають столбчатую структуру, а у разі підвищення змісту домішок і легуючих елементів зерно найчастіше подрібнюється. Та заодно, зазвичай, сильно змінюється структура кордонів зерен, й ролі розміру зерна стає второстепенной.
Одержання стійкою мелкозернистой структури шляхом зниження температури розплаву, обмеження тривалості його чекання і запровадження модифікаторів є дуже простою й хорошо.
[pic].
Рис. 2 Залежність показника горячеломкости (ПГ) сплаву міді з 3% Sn і 0.5% Fe від розміру зерна (?), отриманого у різних плавках.
зарекомендовавшим себе практиці способом зниження горячеломкости. Проте слід зазначити, що здрібнення зерна який завжди допомагає усунути шлюб по кристаллизационным тріщинам в виробничих умовах. Приміром, при полунепрерывном лиття зливків сприятливе дію подрібнення зерна проявляється переважно на алюмінієвих сплавах з середньої і низької горячеломкостью.
1.1.2. Вплив газосодержания сплавів на горячеломкость Наявний виробничий досвід дозволяє зробити суворих висновків щодо вплив газосодержания розплаву на горячеломкость, позаяк у цехових умовах при фасонном і заготовительном лиття кольорових сплавів контроль газосодержания звичайно виробляють. З іншого боку, разом з зміною змісту газу можуть змінюватися інші чинники, що впливають горячеломкость і не учитываемые. Уявлення металургів про який вплив газосодержания на горячеломкость частіше грунтуються не так на систематичних дослідженнях, а на традиційному ставлення до газу як до шкідливого компоненту в сплаві. Це є одним із причин розповсюдженого переконання, що газ, який потрапляє розплав, посилює горячеломкость. Разом про те окремі дослідження говорять про обратном.
Дослідження проводили на алюмінієвих сплавах марок B95, Д16 і АМц, технічному алюмінії марки А00 і подвійних сплавах алюмінію з міддю і кремнієм. Газосодержание розплаву визначали приближённо, методом Дардела, заснованого на реєстрації залишкового тиску, щоб у вакуумної установці лежить на поверхні рідкої проби під лупою зі збільшенням в 5 раз з’являється перший газовий пузырёк. Можна вважати що з алюмінієвого під вакуумом виділявся лише водень, зміст якого визначали по номограмме. Відразу ж, після виміру газосодержания, з свежерасплавленного металу під температурою 720−740° відбирали мірну порцію визначення горячеломкости по кільцевої пробі. Діаметр сталевого стрижня кокиля підбирали кожному за сплаву те щоб можна було визначити, що не напрямі змінюється горячеломкость під час введення газу розплав. Потім з вихідного металу відбирали порцію розплаву, яку обробляли водяникам пором в окремому тиглі, котрий у інший печі. Проходячи через алюмінієвий розплав, водяну пару розкладалися, і розплав збагачувався воднем. З обробленого водяникам пором розплаву відбиралися за однією пробі на газосодержание і горячеломкость. Після цього повторно відбирали проби на газосодержание і горячеломкость з залишку вихідного розплаву, не обробленого пором; потім знову відбирали порцію розплаву в обробці парою й т. буд. Середні результати по 10−12 чередующимся пробам з вихідного і обробленого пором розплавів представлені у таблиці 1. Після опрацювання водяникам пором горячеломкость сплавів В95, Al з 4.5% Cu і Al з 0.8% Si різко зменшилася, у дюралюмина Д16 слабко знизилася, а й у сплаву АМц і алюмінію марки А00 мало змінилася. У жодного із досліджених сплавів був виявлено навіть натяку до посилення горячеломкости після обробки водяникам пором, тоді як проба на газосодержание завжди показувала значне збільшення кількості водню в расплаве.
З таблиці 1 видно, що й зі збільшенням газосодержания розплаву різко знижується горячеломкость, то одночасно помітно зменшується лінійна усадка.
Таблиця 1. Горячеломкость і лінійна усадка алюмінієвих сплавів з різним змістом водню в расплаве.
| |Зміст Н2|Горячеломкость| | | | | |, |Повна линейная|Интервал | | |При |% |усадка, % |кристал- | |Сплав |720°, см3/100г| | |лизации, З | | | | | | | | | | | | | | | | | |А |Б |А |Б |А |Б | | |В95 |0.45 |>0.8 |90 |0 |1.75 |1.55 |150 | |Al з 4.5% Cu |0.42 |>0.8 |70 |15 |1.88 |1.65 |100 | |Al з 0.8% Si |0.06 |>0.8 |86 |50 |1.74 |1.54 |77 | |Д16 |0.15 |0.31 |66 |55 |1.69 |1.62 |132 | |АМц |0.46 |>0.8 |90 |90 |1.97 |1.95 |1 | |А00 (99.7% |0.04 |0.65 |33 |27 |1.95 |1.84 |0 | |Al) | | | | | | | |.
А — вихідний сплав; Б — сплав після обробки водяником пором. Порівнювати між собою показники горячеломкости різних сплавів не можна, оскільки вони визначалися під час використання стрижнів різного диаметра Если ж горячеломкость знижується дуже слабко чи залишається незмінною, то лінійна усадка також незначне чи мало змінюється. Зменшення лінійної усадки при обробці розплаву водяникам пором (таблиця 1) саме собою невелика (максимум 0.2%), але це можна порівняти і з величиною лінійної усадки в інтервалі кристалізації, і з величиною відносного подовження в інтервалі тендітності вище солидуса. Разом про те жодного разу спостерігалося, що підвищену газосодержание розплаву знижувало пластичність сплаву в твёрдо-жидком стані. Навпаки, під час введення водню до сплаву В95 шляхом занурення в ванну промислової печі вологого азбесту спостерігалося зростання відносного подовження в інтервалі тендітності, бо за зазначеної обробці розплаву зерно измельчалось.
Отже, причиною зниження горячеломкости у разі підвищення газосодержания розплаву є збільшення запасу пластичності в твердорідкому стані результаті зменшення лінійної усадки в інтервалі кристаллизации.
Неоднакове вплив обробки пором на горячеломкость різних сплавів пояснюється різним завдовжки перехідною області у отливках. З кільцевих виливків алюмінію і сплаву АМц газ порівняно вільно віддалився при кристалізації, тому підвищення газосодержания мало змінило ні лінійної усадки, ні горячеломкости. Сплави В95, Al з 4.5% Cu і Al з 0.8% Si характеризуються широкої областю затруднённого виділення газу отливках, тому обробка їх розплавів водяником пором значно знизила лінійну усадку в інтервалі кристалізації і горячеломкость. Сплав Д16 при однакових умов обробки пором поглинав значно менше водню, ніж інші сплави (таблиця 1); цим пояснюється слабке зменшення його горячеломкости, попри порівняно широку перехідну область в отливке.
Підвищення газосодержания розплаву необов’язково супроводжується зниженням горячеломкости, оскільки можуть діяти інші чинники. Наприклад, газосодержание зазвичай зростає збільшенням перегріву розплаву, а горячеломкость у своїй не знижується, а навпаки, росте. Останнє обумовлена тим, що негативний вплив укрупнення зерна перекриває позитивний вплив зростання газосодержания на горячеломкость. Аналогічне явище можна зустріти і за збільшенні тривалості чекання розплаву. Цікаво, що у отливках з деяких сплавів спостерігається зникнення тріщин при великому перегрів розплаву. Наприклад, на кільцевих пробах з бронзи з 3% Sn під час досягнення температури розплаву 1280 ° кристаллизационные тріщини повністю зникали, але з’являлися газові раковини. Як бачимо, сильне газопоглощение перекрило тут вплив укрупнення зерна на горячеломкость. Зустрічаються випадки, коли щільні оливки із різних сплавів бувають всуціль вражені тріщинами, а пористі виливки з тієї ж сплавів виходять без трещин.
Якщо запровадження газу розплав зменшує горячеломкость, то природно було б очікувати посилення горячеломкости при дегазації розплаву. Дегазацію виробляли методом вакуумирования. Мірну порцію розплаву відбирали з лабораторного міксера і переливали в графітовий тигель вакуумної печі. Дегазація здійснювалася протягом 2.5−5 хвилин при розрідженні 0.4−0.6 мм рт. ст. і за температурі, на 100 ° перевищує точку ликвидуса. Що Спостерігалося в оглядове скло спучування дзеркала розплаву під впливом інтенсивно що виділяються газів вказувало те що, що дегазація справді происходила.
Парні кільцеві проби по черзі відливалися з вихідного і вакуумированного розплавів (по сім-вісім пар кілець з кожного сплаву). Середні показники горячеломкости наведені у таблиці 2. Досліди повністю підтвердили припущення про посилення горячеломкости під впливом вакуумної дегазации.
Таблиця 2. Горячеломкость і лінійна усадка алюмінієвих сплавів доі після вакуумирования сплава.
| |Горячеломкость, % |Повна лінійна усадка, % | | | | | |Сплав | | | | |Вихідний |Вакуумированный|Исходный |Вакуумированный| | |сплав |сплав |сплав |сплав | |В95 |60 |74 |1.61 |1.73 | |Д16 |44 |86 |- |- | |Al з 0.7% Si |16 |47 |1.81 |1.88 | |Al з 3.5% Cu |58 |100 |- |- |.
Поруч із горячеломкость вимірювали лінійну усадку. Якщо за запровадження газу розплав лінійна усадка знижувалася, то після вакуумної дегазації свежерасплавленного вона зростала, що є причиною зменшення запасу пластичності в твёрдо-жидком безпечному стані й зростання горячеломкости.
1.1.3. Вплив складу сплавів на горячеломкость Дослідження залежності горячеломкости від складу в кількісної формі було вперше виконано Вэрэ з прикладу системи Al — Si. За даними, при додаванні кремнію до алюмінію горячеломкость зростала, досягала максимуму при змісті 1.6% Si і за переході цю концентрацію стрибком падала нанівець. Хоча наявність такого стрибка надалі був підтверджено, але робота Вэрэ відіграла важливу роль: у ній вперше по експериментальним даним побудували графік «горячеломкость — склад», показавши, що з збільшенні концентрації другого компонента горячеломкость проходить через максимум та практично зникає при досягненні деякого критичного кількості эвтектики. Така закономірність в якісному вигляді була помічена ще попередніх роботах. За даними Шейера, в системах Al — Cu і Al — Zn найсильніше були вражені тріщинами кокильные зразки сплавів, містять близько 1% другого компонента, зі збільшенням концентрації якого схильність до освіті тріщин явно зменшувалася, а при змісті міді понад вісім% і цинку вище 50% тріщини не з’являлися. Розглянемо детальніше вплив складу на горячеломкость сплавів эвтектической системи, проводячи зіставлення експериментальних даних із діаграмою стану. Бо за лиття і зварюванні завжди розвивається дендритная ізоляція, то що природно, що неравновесность кристалізації враховувалася починаючи з ранніх робіт, котрі аналізували залежність горячеломкости від состава.
Від рівноважної діаграми стану так звана нерівноважна діаграма відрізняється зрушеної убік компонента концентрационной кордоном появи эвтектики і, зрушеної лінією солидуса, і навіть зниженою температурою эвтектической кристалізації. Переохолодження эвтектики порівняно невелике і зазвичай значно менше ефективного інтервалу кристалізації. Тож аналізу горячеломкости воно істотного значення, зазвичай, немає, і далі враховуватися не буде. Зрушення кордони появи эвтектики від точки граничною розчинності убік ординати компонента істотно впливає на склад сплаву з максимальною горячеломкостью та її завжди доводиться враховувати. У системах з урахуванням алюмінію і магнію вже за часів повільному охолодженні сплавів з піччю наявний значний зрушення кордону появи эвтектики від точки граничною розчинності, а при охолодженні зразків у інтервалі кристалізації з середньої швидкістю порядку 100 град/мин эвтектика переважно систем з’являється при змісті лише десятих часткою відсотка другого компонента.
Ефективний інтервал кристалізації при додаванні до чистого металу другого компонента зростає, сягає максимуму на концентрационной кордоні появи эвтектики і далі поступово зменшується нанівець у точці збіги температури початку лінійної усадки з эвтектической горизонталлю. Горячеломкость тим більше коштів, що більше ефективний інтервал кристалізації, і тому склад сплаву повинен збігатися з кордоном появи эвтектики. Це становище зіграло значної ролі до вивчення залежності горячеломкости від складу, бо вона дозволило зв’язати опірність сплавів освіті тріщин з діаграмою гніву й, у першому наближенні, передбачити область складів найбільш горячеломких сплавів. Але вже у роботі А. А. Бочвара і З. И. Свидерской зазначалося, що у системі Al — Cu сплав з максимальною горячеломкостью містив, за даними мікроскопічного аналізу, невеличке кількість эвтектики. Подальше накопичення експериментальних даних показало, що в багатьох системах максимум — на кривою «горячеломкость — склад» кілька зрушать, проти кордоном появи эвтектики, убік більшої концентрації легирующего элемента.
Причину розбіжності максимумів горячеломкости й ефективного інтервалу кристалізації можна було зрозуміти, з урахуванням впливом геть горячеломкость пластичності і лінійної усадки і залежності цих властивостей від складу сплаву. Розглянемо за приклад систему Al — Cu. Горячеломкость і концентрационную кордон появи эвтектики визначали самих і тієї ж зразках — кільцевих пробах за середньої швидкості охолодження в інтервалі кристалізації 350 град/мин. Якщо алюміній чистотою 99.96%, то сплав з максимальною горячеломкостью містить 0.7% Cu, а кордон появи эвтектической складової проходить при 0.2% Cu. У малолегированных сплавів Al — Cu в частині інтервалу кристалізації залишається дуже мало рідкої фази в вигляді ізольованих включень, які викликають межкристаллитного руйнації. Тому в цих сплавів нижню межу температурного інтервалу тендітності перебуває значно вища неравновесного солидуса (эвтектической температури), а сам інтервал тендітності значно вже ефективного інтервалу кристалізації. Зі збільшенням змісту міді інтервал тендітності розширюється. Разом про те, у сплавів, містять до 1% Cu, відносне подовження всередині інтервалу тендітності перебуває в дуже низький рівень і слабко від складу. Оскільки підвищення змісту міді до 0.7 — 1% не змінює відносного подовження в інтервалі тендітності, але розширює його й збільшує у ньому лінійну усадку, то запас пластичності в твёрдо-жидком стані знижується. При збільшенні змісту міді понад 1% інтервал тендітності ще продовжує розширюватися, та заодно, завдяки збільшення кількості рідкої фази на межі зерен, значно зростає відносне подовження, їм запас пластичності повышается.
Отже, пояснення розбіжності максимумів горячеломкости і ефективного інтервалу кристалізації зводиться ось до чого. У сплаву алюмінію з 0.2% Cu, розташованого на концентрационной кордоні появи эвтектики, ефективний інтервал кристалізації максимальний, але температурний інтервал тендітності менше, ніж в трохи більше легованих сплавів. Тому, за практично однаковому подовженні в інтервалі тендітності найменшим запасом пластичності в твёрдо-жидком стані, тобто. максимальної горячеломкостью, має сплав алюмінію з 0.7% Cu, у якому більше другого компонента, ніж сплав з максимальним ефективним інтервалом. Це становище справедливо більшість систем эвтектического типу (малюнок 3). Наприклад, у системі Al — Zn максимум горячеломкости доводиться на 6% Zn, а максимум ефективного інтервалу кристалізації - на 3% Zn (кордон появи эвтектики визначено на шлифах з кільцевих проб). Точнісінько визначити склад найбільш горячеломкого сплаву можна тільки прямими дослідами. Але у практичному відношенні важливо, що у микроструктуре можна орієнтовно оцінити порівняно вузьку область складів, де можна очікувати появи максимуму горячеломкости. Це — область сплавів з концентрацією легуючих елементів більшою, ніж кордоні появи эвтектики у цих нерівноважних умовах кристалізації, область, де сплави містять трохи більше десятих часткою відсотка нерівновагової эвтектики.
[pic].
Рис. 3 Розбіжність максимумів ефективного інтервалу кристалізації і горячеломкости у системі эвтектического типа.
Розглянемо, що не інтервалі концентрацій взагалі з’являється горячеломкость. Сплави, перебувають у області складів від «критичної» точки до эвтектической, начебто, взагалі би мало бути горячеломкими, оскільки ефективний інтервал вони нульовий, а кристалізація эвтектики, що протікає при постійної температурі, як така має викликати освіти усадочных тріщин. Тоді як на складних фасонных отливках можна зустріти кристаллизационные тріщини у цій групі сплавів. Через градієнта температур усадка одних частин виливки, встигли повністю затвердіти, викликає розтягнення сусідніх більш гарячих ділянок, що є ще стадії кристалізації эвтектики. Розтягнення ділянок, де є залишкова рідка фаза, можуть призвести до утворення кристаллизационных тріщин. Отже, сплави із нульовим ефективним інтервалом кристалізації можуть виявляти горячеломкость, тобто. не існує абсолютно негорячеломких сплавов.
Склад сплаву з максимальною горячеломкостью у системі дуже постійний: він слабко від рівня перегріву розплаву, швидкості охолодження і геометрії виливки. З підвищенням температури кокиля спостерігається лише незначна тенденція до зрушення максимуму горячеломкости убік менш легованих сплавів. Мінімальна концентрація другого компонента, коли він експериментально фиксируемая горячеломкость зникає, навпаки, залежить та умовами лиття. Інтервал концентрацій, у якому можна знайти горячеломкость, розширюється з збільшенням ступеня перегріву розплаву, збільшенням швидкості охолодження і збільшенням діаметра кільцевої проби. Останні два чинника роблять пробу більш жорсткої, оскільки збільшують градієнт температур і посилюють локалізацію усадочных деформацій, і тому сприяють виявлення горячеломкости до великих концентрацій легирующего елемента. Збільшення перегріву розплаву діє в самому напрямку, оскільки розширює область складів сплавів, у яких утворюються столбчатые кристаллы.
Пояснюючи причину зниження горячеломкости попри збільшення кількості эвтектики в сплаві, перше місце часто ставлять здатність эвтектической рідини заліковувати які утворюються тріщини. З цим погодитися, так як эвтектика не має якогось особливого, різко відмінній від неэвтектической рідини здатністю заповнювати виникаючі тріщини. Зниження горячеломкости попри збільшення кількості эвтектики в сплаві завдяки зростанню запасу пластичності в твёрдо-жидком стані, а останній збільшується як у результаті підвищення подовження в інтервалі тендітності, і зменшення лінійної усадки. Головною причиною цього є збільшення кількості рідкої фази, кристаллизующейся до останньої чергу при постійної температурі. Такий фазою може бути лише эвтектика, а й рідина перитектического складу і фаза, кристаллизующаяся у точці мінімуму з діаграми плавкости неперервної низки твердих розчинів. Інший чинник, сприятливо котрий простежується на пластичності і лінійної усадки в твёрдо-жидком стані - здрібнення зерна, в особливості звуження зони столбчатых кристалів, те що зі збільшенням кількості эвтектики в сплаве.
1.1.4. Вплив зональної ликвации на горячеломкость Під час вивчення системи Al — Cu було знайдено, що крім звичайної максимуму горячеломкости при 0.7% Cu, розміщеного поблизу концентрационной кордону появи эвтектики, існує ще одне максимум при 4% Cu. Микроструктурный аналіз показав, що у розривних зразках й у кільцевих пробах серцевина сильно збіднена міддю, а поверхневі шари збагачені нею проти нормальної структурою сплаву із чотирьох% Cu. За інших алюминиевомедных сплавах зворотна ізоляція була виявлено. Поява другого максимуму горячеломкости пояснили розвитком зворотної ликвации.
Зональна сегрегація найбільш розвивається у сплавах, значно більше легованих, ніж сплав з максимальним ефективним інтервалом кристалізації. За відсутності її такі сплави повинні мати порівняно невеличкий горячеломкостью. Зональна ізоляція призводить до утворення в литві ділянок, обеднённых легирующим елементом до концентрацій, відповідних складам сплавів із високим горячеломкостью. Неоднорідність мікроструктури виливки зумовлює також велике розкид значень горячеломкости у різних опытах.
1.1.5. Вплив домішок на горячеломкость Домішки надають різноманітне і найчастіше дуже сильний дію на горячеломкость. Роль домішок неодноразово обговорювалася стосовно найрізноманітнішим сплавів. Нижче на прикладах коротко розглянуті основні випадки впливу домішок на горячеломкость у зв’язку з зміною властивостей сплавів в твёрдо-жидком состоянии.
Домішки впливають на горячеломкость переважно через зміна пластичності. Вони можуть розширити і звузити інтервал тендітності, збільшити і зменшити відносне подовження у ньому. На розвитку лінійної усадки в інтервалі кристалізації домішки звичайно сказываются.
Розглядаючи дію шкідливих домішок, які розширюють інтервал кристалізації, необхідно пам’ятати, що зниження горячеломкости відбувається за незначного зниження, а й за підвищення їхньої концентрації в сплаві. Одні говорили і самі домішки, залежно від цього, що не металі чи сплаві вони знаходяться, можуть як посилювати, і знижувати горячеломкость. Продемонструємо на прикладі подвійний системи Al — Cu. Алюміній марки AВ00 (99.96% Al) мало схильний до утворення кристаллизационных тріщин, а алюміній марки A00 (99.7% Al) дуже горячеломок. Ускладнення зумовлені тим, що з кристалізації алюмінію чистоти 99.7% на межі зерен утворюється тонкий шар рідкої фази, збагаченої кремнієм і залізом. Цей шар створює інтервал тендітності в твёрдо-жидком стані величиною близько 14°, у якому виникають кристаллизационные тріщини. Протилежно ведуть себе сплави системи Al — Cu. Сплави, приготовлені більш брудному алюмінії, менш горячеломки. Але вони товщі прошарку рідкої фази в інтервалі тендітності і тому трохи вища відносне подовження порівняно з сплавами, приготовлені чистою алюминии.
У сплавів, приготовлених на алюмінії чистоти 99.96%, максимум горячеломкости спостерігається при змісті міді 0.7%, і якщо використовувати алюміній чистоти 99.7% - при змісті 0.3% Cu. Як бачимо, у тому разі потрібно менше легирующего елемента, аби досягти критичного кількості легкоплавкой складової (максимуму горячеломкости), оскільки вихідний метал вже містить деяке його количество.
Аналогічно позначається чистота алюмінію на горячеломкости сплаву АЛ19. З використанням алюмінію марки АВ000 (99.99% Al) показник горячеломкости цього сплаву по кільцевої пробі при діаметрі стрижня 48 мм становить 95%, а під час роботи на алюмінії марки А00 (99.7% Al) — 70%. Відповідно, у разі середня ширина рідких межзёренных прошарків при 590° дорівнює 3.4 мкм, тоді як у другому — 4.9 мкм (обидва значення виходили заниженими, оскільки виміру проводили на закалённых шлифах).
Одні домішки в сплаві можуть посилювати, інші у тому сплаві зменшувати горячеломкость, оскільки вони по-різному впливають на солидус, кількість і форму розподілу легкоплавкой складової. Домішки, що входять до твёрдый розчин, мало ликвирующие до кордонів зерен і незначно розширюють інтервал кристалізації, на горячеломкости мало позначаються. Зміна температури солидуса сплаву і кількості легкоплавкой складової, розглянуте вище на кількох прикладах, — це головний напрямок впливу домішок на горячеломкость. Але може бути зустрічатися та інші випадки, у тому числі найважливіше зміна форми та розміру зерен і форми виділень интерметаллидов. Так, підвищення змісту домішки алюмінію бронзі Бр. ОЦСН3−7-5−1 з 0.01 до 0.1% збільшило показник горячеломкости по кільцевої пробі з 65 до 100%, так як він сприяло освіті столбчатой структури. Дуже цікаво дію зміни домішки заліза в сплаві АМц. При додаванні 0.2% Fe в сплав алюмінію з 1.5% Mn включення Al6Mn подрібнюються, нижню межу інтервалу тендітності піднімається до температури солидуса, сам інтервал тендітності звужується з 20 до 6°, у результаті показник горячеломкости по кільцевої пробі при діаметрі стрижня 30 мм знижується зі 100 до 40%.
1.2. ШЛЯХУ ЗНИЖЕННЯ ГОРЯЧЕЛОМКОСТИ СПЛАВОВ.
Величезний виробничий досвід минулого і проведені у багатьох країнах лабораторні дослідження впливу хімічного складу й інших чинників на схильність сплавів до утворення гарячих тріщин дали змоги останні десятиліття виявити основних напрямів зниження горячеломкости. Нижче на підставі цього накопиченого досвіду з урахуванням даних про природу гарячих тріщин і закономірностей впливу складу і структури на пластичність і лінійну усадку в твёрдо-жидком стані коротко розглядають шляху зниження горячеломкости сплавів (але з виливків, позаяк у цьому разі довелося б розцінювати різноманітні заходи з усунення тріщин в виробах, що носять суто технологічний характер).
Горячеломкость сплаву залежить від пластичності і лінійної усадки їх у твёрдо-жидком стані перебуває й від нашої здатності розплаву заліковувати виникаючі тріщини. Знижувати горячеломкость сплаву можна через підвищення його пластичності в твёрдо-жидком стані, зменшення лінійної усадки кристалізації і крізь посилення залечивания тріщин расплавом. З положень цих трьох чинників пластичність найсильніше реагує зміни складу і структури сплаву, а здатність розплаву заліковувати тріщини — найбільш слабко. Тому найдійовіші металургійні способи зниження горячеломкости засновані на підвищенні пластичності сплаву в твёрдо-жидком стані перебуває й частково зниженні лінійної усадки в інтервалі кристаллизации.
Підвищити пластичність і знизити лінійну усадку в інтервалі кристалізації шляхом зміни складу і структури сплаву — це значит:
1. Звузити температурний інтервал тендітності рахунок підвищення його нижньої межі і (чи) зниження верхньої границы.
2. Підняти рівень відносного подовження в усьому інтервалі тендітності, зокрема і культурний рівень мінімального удлинения.
3. Звузити ефективний інтервал кристалізації рахунок зниження температури початку лінійної усадки і (чи) підвищення точки солидуса.
4. Зменшити темп наростання лінійної усадки при зниженні температури в ефективному інтервалі кристаллизации.
Можно виділити чотири шляху зниження горячеломкости сплавов.
1.2.1. Перший шлях зниження горячеломкости — вибір оптимального складу по основним компонентами розробки нові й поліпшенні існуючих сплавів. Обираючи легирующие елементи і встановлюючи їх концентрації, бажано забезпечити малий темп кристалізації у верхній частини інтервалу «ликвидус — солидус» і великий темп у нижній частині цього інтервалу, щоб отримати можливо більше рідкої фази до кінця кристалізації. Цим досягається, по-перше, зниження температурної кордону між жидко-твёрдым і твёрдо-жидким станами, а паралельно із нею зазвичай опускається і верхня кордон інтервалу тендітності. По-друге, збільшення відносного кількості рідкої фази до кінця кристалізації сприяє розвитку тут межзёренной деформації при утрудненої усадки і, отже, підвищує подовження в інтервалі тендітності. Найпростіший спосіб досягнення цього полягає у зростання кількості складової кристаллизующейся останнє при постійної температурі. Такий складовою є эвтектика, перитектическая складова, твёрдый розчин, кристаллизующийся у точці мінімуму з діаграми стану, і чистий метал. Зниження горячеломкости шляхом збільшення кількості эвтектики широко використовується розробки алюмінієвих і магнієвих сплавів. Збільшення кількості перитектической складової можна використовуватиме зниження горячеломкости багатьох мідних сплавів. У системах з безперервну низку твердих розчинів через дендритной ликвации кристалізація часто закінчується точці мінімуму на кривою ликвидуса чи у точці плавлення більш легкоплавкого компонента. Зміна складу сплаву убік цих точок має збільшити кількість рідкої фази поблизу солидуса і знизити горячеломкость. Такий спосіб зниження горячеломкости можна використовувати розробки сплавів, які стосуються системам з безперервну низку твердих розчинів, наприклад сплавів з урахуванням Ni, Nb, Pt і др.
На пластичності багатокомпонентних сплавів в твёрдо-жидком стані позначається як складова, кристаллизующаяся останнє при постійної температурі (наприклад, потрійна эвтектика), а й складова, що настає всередині інтервалу кристалізації (наприклад, подвійна эвтектика). Сумарна кількість подвійний і в потрійній эвтектик бажано вибирати таким, щоб температура переходу із жидко-твёрдого в твёрдо-жидкое стан перебувала у сфері первинної кристалізації, а в інтервалі виділення подвійний эвтектики. Тоді сплав матиме порівняно невеличкий температурний інтервал тендітності і високе подовження в нём.
Розглянутим вище способом зниження горячеломкости, на жаль, які завжди вдається скористатися, оскільки може погіршити експлуатаційні властивості. Нагадаємо, що склади високоміцних і жароміцних сплавів часто перебувають у області, де горячеломкость дуже висока, а допускаемое кількість эвтектической чи перитектической складової в деформируемых і багатьох ливарних сплавах суворо ограничено.
Інший засіб зниження горячеломкости у тому, щоб за розробці сплаву спробувати спочатку підняти його солидус, не підвищуючи ликвидуса і температури початку лінійної усадки. І тому зовсім необов’язково сильно змінювати хімічний склад. Наприклад, в потрійний системі (малюнок 4) з з'єднанням AmBn, що утворюється по перитектической реакції, кристалізація всіх сплавів трикутника AmBn — B — З закінчується эвтектической точці Є, а сплавів трикутника A — AmBn — C.
— в перитектической точці Р. Температура плавлення потрійний эвтектики може бути значно нижчі від температури четырёхфазного перитектического рівноваги. При дуже незначному збільшенні концентрації компонента На сплавах, що є поблизу лінії AmBn — З, вони з трикутника AmBn — B — З потрапляють у трикутник A — AmBn — З (наприклад, сплав змінює свій склад від точки 1 до точки 2). У цьому потрійна эвтектика зникає, і солидус сплаву сильно підвищується, а температура ликвидуса і температура початку лінійної усадки мало змінюються; у результаті дуже звужуються ефективний інтервал кристалізації і інтервал тендітності. Можуть вживатись і інші виходи значного звуження інтервалу тендітності при порівняно невеличкому зміні складу. Наприклад, легування сплаву магнію з 4.5% Zn добавкою 0.8% Zr підвищує солидус з 344 до 550°. Одночасно верхня межа інтервалу тендітності знижується на 30° тому, що цирконій сильно змаліє зерно. Через війну, невеличка добавка цирконію, мало яка зраджує мікроструктуру, звужує інтервал тендітності в 25 раз.
Ще одну можливість зниження горячеломкости можна використовувати при розробці нових сплавів — запровадження добавок, які розширюють прикордонну зону твердого розчину, обогащённую легирующими елементами. Такі добавки збільшують товщину рідких прошарків на межі зерен в інтервалі тендітності, підвищуючи відносне подовження у ньому без помітного збільшення кількості эвтектики. Саме такими діє добавка 0.3% Mn і 0.1% Ti до сплаву алюмінію із сьомої% Cu. Сплав алюмінію із сьомої% Cu, 0.3% Mn і 0.1% Ti має умовний запас міцності в твёрдо-жидком стані ЗП = 0.52%, а й у сплаву з 7% Cu ЗП = 0.35%. Такий спосіб зниження горячеломкости дуже перспективний, оскільки не пов’язане з значним збільшенням кількості эвтектической чи перитектической складової. Але, на жаль, поки що важко пророкувати, які елементи у якому кількості необхідно вводити, щоб розширити прикордонну ликвационную зону в первинних кристалах твердого раствора.
Усі розглянуті вище способи зниження горячеломкости засновані на звуження ефективного інтервалу кристалізації і інтервалу тендітності і підвищенні відносного подовження в інтервалі тендітності. Розраховувати на зниження горячеломкости рахунок зменшення термічного коефіцієнта лінійного стискування годі й говорити, оскільки останній, как.
[pic].
Рис. 4 Потрійна система з подвійним з'єднанням, що утворюється по перитектической реакции.
правило, можна значно зменшити, тільки дуже сильно змінивши склад сплаву. 1.2.2. Другий засіб зниження горячеломкости — регулювання змісту основних компонентів не більше допусків Держстандарту чи технічних умов. Тут застосовні самі прийоми, що й за розробці нового сплаву, але рамки зміни хімічного складу суворо обмежені. Проте й тісних межах Держстандарту, регулюючи зміст основних компонентів, можна значно збільшити кількість рідкої фази та нижньої частини ефективного інтервалу кристалізації, істотно знизити температуру початку лінійної усадки чи підняти температуру солидуса.
До кожного стандартного сплаву, якщо лиття його спостерігається чистий шлюб по кристаллизационным тріщинам, необхідно встановити оптимальний в межах допусків за Держстандартом склад, відповідний мінімуму горячеломкости. Цей шлях зниження горячеломкости ще недостатньо широко використовується, і тут є приховані резерви зменшення шлюбу з усадочным тріщинам в виробництві зливків і фасонных виливків. 1.2.3. Третій шлях зниження горячеломкости — регулювання змісту домішок в сплаві. Зміна змісту домішок може дуже спричинити нижню межу інтервалу тендітності величину відносного подовження в ньому, мало впливають верхній кордоні інтервалу тендітності і температурі початку лінійної усадки.
Найбільш шкідливі легкоплавкие домішки, що утворюють на межі зерен плівки великий довжини, оскільки вони різко розширюють температурний інтервал тендітності. Давно відомий засіб зниження горячеломкости видаленням легкоплавких домішок з сплаву. Якщо повністю позбутися такий домішки не вдається, можна знизити зміст її рівня, щоб він лежить у вигляді ізольованих включень, а чи не як плівок. У цьому разі, хоча точка початку плавлення сплаву не підвищується, нижню межу інтервалу тендітності може значно піднятися над солидусом. Коли це здійснити не вдається, можна звернутися до штучному збільшення легкоплавкой домішки в сплаві. Такий спосіб зниження горячеломкости грунтується у тому, що потовщення легкоплавких плівок полегшує межзёренную деформацію і підвищує відносне подовження у нижній частині інтервалу хрупкости.
Послаблення шкідливого впливу легкоплавкой домішки шляхом підвищення її концентрації в сплаві - цікавий спосіб. Але він порівняно рідко може бути використана через шкідливого впливу цієї домішки на експлуатаційні властивості сплаву. 1.2.4. Четверте шлях зниження горячеломкости — введення у сплав малих технологічних добавок. Під технологічними добавками розуміють такі малі добавки, основна мета введення стало зниження горячеломкости. Технологічні добавки можуть різко підвищити нижню межу інтервалу тендітності, значно опустити верхню його кордон і направлення температуру початку лінійної усадки, і навіть підвищити відносне подовження в інтервалі хрупкости.
З давніх-давен зниження горячеломкости використовується спосіб запровадження добавок, що пов’язують шкідливі домішки на більш тугоплавкі сполуки (наприклад, запровадження магнію для знешкодження сірки в нікелі). У цьому нижню межу інтервалу тендітності різко підвищується, верхня мало змінюється і інтервал тендітності сильно сужается.
Інший добре відомий засіб зниження горячеломкости технологічними добавками полягає у вступі модифікаторів зерна. Здрібнення збіжжя і особливо усунення столбчатой структури знижують температуру початку лінійної усадки й верхній кордон інтервалу тендітності і підвищують відносне подовження в усьому інтервалі. Саме такими діє невеличка добавка титану до багатьох алюмінієвим сплавам.
Модифікатори мікроструктури зовсім не використовують як технологічні добавки, спеціально призначені зниження горячеломкости. Разом про те цей спосіб боротьби з кристаллизационными тріщинами представляють практичну цінність. Наприклад, запровадження 0.1% Zr в алюминиево-магниевый сплав піднімає нижню межу інтервалу тендітності і звужує цей інтервал тому, що включення эвтектической рідини виходять більш дисперсными.
Однією з дуже цікавих способів зниження горячеломкости високоміцних сплавов-растворов лежить введення таких технологічних добавок, які утворюють на межі зерен протяжні прошарку нерівновагової эвтектической чи перитектической складової, причому при нагріванні сплаву під загартування чи спеціальну гомогенизацию ця складова розсмоктується. Останнє умова є найважливішим, позаяк у іншому разі погіршуються експлуатаційні властивості. Отже, майже все кількість эвтектики, образующееся під час введення технологічної добавки, має бути неравновесным. Наприклад, добавка 0.5% Ce до жаропрочному сплаву АЛ19 зменшує показник горячеломкости по кільцевої пробі з 75 до 10% (діаметр стрижня — 44 мм), не погіршивши механічних властивостей при 300° (нерівноважна эвтектика в сплаві АЛ19 з добавкою церію значною мірою розсмокталася при східчастому нагріванні під загартування до 525° протягом дев’яти годині і до 535° протягом 12 годин). Це малоизученное напрям зниження горячеломкости високоміцних сплавів може дуже перспективным.
Ще одна можливість знизити горячеломкость запровадженням технологічних добавок полягає у утолщении рідких прошарків, отже, підвищення відносного подовження всередині інтервалу тендітності, не було за рахунок збільшення кількості эвтектики, а результаті розширення прикордонних ликвационных зон твердого розчину. У напрямі поки що незроблене, хоча вона він може виявитися перспективным.
Шлях використання малих технологічних добавок одна із найважливіших, оскільки він у принципі дозволяє сильно знизити горячеломкость, не погіршуючи експлуатаційних властивостей сплава.
Підвищення газосодержания розплаву можуть призвести до зниження температури початку лінійної усадки, зменшенню темпу її наростання під час падіння температури в ефективному інтервалі кристалізації і тим самим знизити горячеломкость. Було запропоновано вводити в алюмінієвий розплав водень в таких кількостях, щоб помітно знизилася горячеломкость, а пористість збільшувалася б незначно. Хоча це спосіб мислення та був випробуваний заводських умовах з позитивний результат, але навряд він може знайти скільки-небудь помітний промислове застосування, оскільки звичайно прагнуть повніше дегазувати розплав підвищення герметичності і механічних властивостей. Проте корисний вплив газу на горячеломкость необхідно мати у очах і, якщо виріб важко давалися без кристаллизационных тріщин, то ми не слід повної дегазації, залишивши в розплаві що у нього природним шляхом газ (за умови отримання необхідних експлуатаційних свойств).
1.3. ЛИВАРНІ ПРОБЫ НА ГОРЯЧЕЛОМКОСТЬ Для оцінки горячеломкости сплавів не розроблено загальновизнаних проб. Іноді «нові» проби в цілому або майже зовсім повторюють ті, які було запропоновано значно раньше.
Ливарні проби на горячеломкость важко розділяти на класи, тому що й дуже багато. Проте в більшості усіх існуючих проб можна назвати три основні групи відповідно до тим, що за показник горячеломкости чи протилежну їй характеристику — опірність освіті тріщин. 1.3.1. У першій групі проб показником горячеломкости є розмір тріщин за незмінної геометрії виливки. Оскільки жёсткость проби постійна, то розміри тріщин можуть характеризувати горячеломкость сплаву. Було розроблено надзвичайно проста кільцева проба, що у різних модифікаціях швидко набула популярності для дослідження кольорових сплавів. Сплав заливається без спеціальної литниковой системи просто у відкриту порожнину форми — найпростіший кокіль зі сталевим стрижнем. На поверхні кільцевої виливки вимірюється сумарна довжина тріщин, що є показником горячеломкости. Згодом ця проба була ще більше спрощена тим, що став вимірювати не сумарну довжину тріщин, а відносну довжину основний трещины.
Як засвідчили докладні дослідження подвійних і потрійних систем з урахуванням алюмінію, проведені наприкінці 40-х років у Бирмингемском університеті, кільцева проба має досить високою чутливістю до невеликим змін складу і хорошою воспроизводимостью результатів дослідів. Кільцева проба надзвичайно проста, производительна, вимагає порівняно невеликого витрати металу і дозволяє в лабораторних умовах швидко налагодити масові дослідження. На малюнку 5 показаний кокіль для виливки кільцевої проби. Для кожної серії порівнюваних сплавів діаметр сталевого стрижня доцільно підбирати в попередніх дослідах те щоб найбільш горячеломкий сплав цієї серії давав максимально довгу тріщину (але з довші, ніж периметр радіального перерізу кільця), а найменш горячеломкий сплав давав максимально коротку тріщину. У межах одного серії порівнюваних сплавів діаметр сталевого стрижня кокиля може бути постійним (як і, як зовнішній діаметр і висота кільця). Тоді проба всім сплавів цієї серії має постійної жёсткостью (постійної ступенем локалізації усадочных деформацій), і сплави можна порівняти за довжиною тріщин лежить на поверхні кільця. Необхідно підкреслити, що не можна порівнювати за довжиною тріщин сплави із різних серій дослідів, без урахування діаметр стрижня кокиля, оскільки при.
[pic].
Рис. 5 Кокіль для кільцевої проби на горячеломкость.
1 — съёмный склянку; 2 — стрижень різних діаметрах стрижня кільцеві проби мають різною жёсткостью. Чим більше діаметр стрижня, то більше вписувалося жёсткость проби. Саме тому, наводячи інформацію про горячеломкости, необхідно вказувати діаметр сталевого стрижня, використаного при литві кільцевої проби. Найчастіше досить шести повторних дослідів (заливок), щоб надійно визначити показник горячеломкости (сумарну довжину всіх тріщин чи відносну довжину основний тріщини). Довжину тріщини, що буває дуже звивиста, зручно вимірювати з допомогою простого пристосування: укреплённое на кінці рукоятки зубцювате колесо котиться вздовж тріщини і підраховує число повних його оборотів, а при неповному обороті - число зубів, коснувшихся поверхні кольца.
Кристаллизационная тріщина у принципі може повинна розвиватися у довжину як і інтервалі кристалізації, і за нормальної температури нижче солидуса. Тому природно постає запитання, як і у тому, що у кільцевої пробі вимірюється довжина тріщин суто кристаллизационного походження. Фрактологический аналіз численних кільцевих проб із різноманітних кольорових сплавів наочно показала, що у гнітючому вона найчастіше на своєї довжині тріщини лежить на поверхні кільця мали кристаллизационное походження. З іншого боку, даних про запасі пластичності в твёрдо-жидком безпечному стані і результати виміру довжини тріщин на кільцевих пробах, зазвичай, дуже добре узгоджуються. Отже, за рідкісними винятками, (наприклад, сплави з дуже високою крихкістю в твердому стані), на кільцевих пробах вимірюється довжина саме кристаллизационных тріщин. Не отже, що це одержувані з допомогою кільцевої проби сплави схильні до освіті холодних тріщин. Вже згадана кільцева проба має порівняно невеличкий жёсткостью, і тому холодні тріщини на ній щодо кольорових сплавів з’являються дуже рідко. Саме освіту радіальної кристаллизационной тріщини призводить до розрядці усадочных напруг у кільці і вже цим зменшує ймовірність утворення холодної тріщини у ньому. У той самий час при безупинному лиття, як у охлаждаемом водою зливку виникають дуже серйозні термічні напруги, в кокильных отливках складної конфігурації і за зварюванні, коли спостерігається сильна концентрація усадочных напруг, типові холодні тріщини можуть з’явитися в тих сплавів, які мають, відповідно до кільцевої пробі, проявляється лише горячеломкость.
Відносна довжина основний тріщини на кільцевих пробах змінюється при зміні складу сплаву приблизно таке ж, як сумарна довжина всіх тріщин. Поруч із розвитком тріщини завдовжки відбувається її розкриття, збільшення ширини. Довжина й відповідна середня ширина змінюються з складом якісно однаково. Тому площа тріщини лежить на поверхні кільця (твір її довжини на середню ширину) змінюється з складом якісно як і, як і довжина тріщини. Але вимір площі тріщини істотно підвищує трудоёмкость роботи з кільцевої пробою. Більшість досліджень цілком достатня чутливість кільцевої проби з виміром довжини тріщин. На поверхні виливки вимірюється довжина макротрещины, яка може об'єднувати численні межкристаллитные мікротріщини. Чим більший останніх, тим довші яка вимірюється тріщина. Тому довжина макротрещины в певній мері відбиває опірність сплаву появі осередків руйнації. Цілком очевидно, що довжина макротрещины відбиває опірність сплаву її розвитку. Отже, прийнята кільцева проба дає комплексний показник горячеломкости, що характеризує як опірність сплаву освіті, і розвитку кристаллизационных тріщин. З практичного точки зору, ця комплексність дуже цінна, оскільки для виробничника важливий як наявність тріщин, а й їхні розміри: короткі неглибокі тріщини можна заварити, і виливок не бракується. До пробам, у яких показником горячеломкости служать розміри, іноді ставляться як до примітивним і протиставляють їх понад складним; і нібито більш науково обгрунтованим методам оцінки горячеломкости, наприклад, по критичного напрузі. Тоді як кільцева і що подібна їй проби, відрізняючись виняткової простотою, не поступаються, а вони часто й перевершують по чутливості багато складніші методи оцінки горячеломкости, у цьому однині і метод визначення критичної навантаження. Достовірність даних, отриманих складнішими методами, часто перевіряють за збігу з результатами визначення розмірів тріщин більш простих кільцевих пробах.
Застосування кільцевої проби дозволило багатьом дослідникам нагромадити великий експериментальний матеріал про залежності горячеломкости кольорових сплавів від складу і структури, причому отримані дані чудово узгоджуються з виробничим досвідом, ні з результатами підрахунку умовного запасу пластичності в твёрдо-жидком стані. Недоліком кільцевої проби є мала її жёсткость, яка дозволяє досліджувати ливарні сплави зі порівняно невеличкий горячеломкостью, наприклад, більшість силуминов. Недоліком всіх проб із постійною жёсткостью є вузькість діапазону обумовленою горячеломкости. Якщо проба недостатньо жорстка, вона Демшевського не дозволяє розрізнити за величиною горячеломкости малогорячеломкие сплави, оскільки вони взагалі дадуть тріщин. Якщо ж проба занадто жорстка, вона Демшевського не дозволяє класифікувати сплави із високим горячеломкостью, позаяк у цьому випадку тріщини призводять до повного розриву з усього перерізу виливків. Тому, за роботі, наприклад, з кільцевої пробою необхідне даної сплавів підбирати діаметр стрижня, тобто. ширину кільцевої виливки при постійному зовнішньому її діаметрі, те щоб проба могла «розрізняти» за величиною горячеломкости всі ці сплави. Останнє умова взагалі неможливо виконати, тоді як досліджувану групу входять сплави з дуже високою і дуже низької горячеломкостью. Тоді доводиться порівнянні сплави розділяти на дві підгрупи і застосовувати до них пробу з підвищеної і зниженою жёсткостью.
1. Стандартна кільцева проба на горячеломкость.
Стандартна кільцева проба на горячеломкость (малюнок 6) є відливку як пласких кілець, заповнених від однієї литника (1). Кільце (2) завтовшки 5 мм має переважають у всіх пробах і той ж зовнішній діаметр, рівний 107 мм. Для виготовлення форми використовувалася формовочная суміш, що складається з кварцевого піску із шостої% бентонита і трьох% воды.
Внутрішня поверхню кілець оформляється завжди металевими стрижнями (3). Отже, в литві створюються умови, сприятливі для освіти усадочных напруг внаслідок механічного гальмування лінійної усадки із боку стрижня. З іншого боку, для освіти термічних напруг застосовують холодильники (4), які збільшують перепад температурах литві. Внаслідок цього виникаючі деформації локалізуються щодо одного місці - місці підвода металу до литві, де закінчується процес кристалізації. Тут й утворюється тріщина, якщо вимушена деформація перевищила значення граничною деформационной здібності сплава.
Холодильники і стрижні виготовлені зі сталі. Один із сторін холодильника, яка зтикається з виливком, було покрито шаром кварцевого піску зі сполучною речовиною завтовшки 1 мм. Ширина кілець в радіальному напрямі може змінюватися від 5 до 47.5 мм з допомогою металевих стрижнів різних діаметрів. Критерієм горячеломкости служить максимальна ширина кільця (в мм), коли він з’являється тріщина. Чим більше ця критична ширина кільця, то більше вписувалося сплав схильний до освіті гарячих трещин.
1.3.2. У другій групі проб показники горячеломкости відбивають й розміри тріщин, й розміри зразка. Одночасний облік обох цих характеристик виробляється у тому, щоб зробити проби чутливішими й разом про те, здатними охопити ширший діапазон горячеломкости.
Особливо цікава проба Хала. На відміну всіх відомих проб, може бути використана з оцінки горячеломкости тугоплавких сплавів з урахуванням титану, цирконію, ніобію тощо. п. Характерні особливості цієї проби: плавка в підвішеному стані малих навесок (2.4 см3) і заливання металу у мідну форму у атмосфері гелію чи аргону (малюнок 7).
В зразку, який має вигляд шпильки з головками, через усадки металу і розширення мідної форми виникають розтягують деформації. Зі збільшенням зовнішнього діаметра изложницы, тобто. зі збільшенням її маси, вона менше нагрівається при заливці металу і від розтягує зразок. Отже, жёсткость проби зростає збільшенням довжини шпильки.
[pic].
Рис. 6 Кільцева проба на горячеломкость. 1 — воронка; 2 — кільця перемінної ширини; 3 — металевий стрижень; 4 — холодильник Проте й зменшенням зовнішнього діаметра форми З. Кожна форма характеризується умовним номером N, відповідним певним значенням Проте й С:
N… 4 5 6 7 8 9 А, дюйм… 23/4 29/16 23/8 23/16 2 113/16 З, дюйм… ¾ 3/4 ¾.
¾ 3/4 ¾.
N… 10 11 12 13 14 15 16 А, дюйм… 15/8 15/8 15/8 11/2 13/8 11/4 11/8 З, дюйм… ¾ 1 11/4 11/4 11/4 11/4 11/4.
На поверхні зразка, Поворачиваемого у спеціальній тримачі, По отсчетному лімбу вимірюється кутова величина концентричних тріщин (осьової їх складової нехтують). Результати вимірів кожному за сплаву видаються у вигляді графіки «відносна довжина тріщин (%) — номер ливарної форми». Що це номер, тим менше розтягують деформації і коротше тріщини. За показник горячеломкости вибирається номер форми, при якому відносна довжина тріщини дорівнює 40%.
Проба Хала (CPT-Test — cast-pin tear test) має задовільною чутливістю і дає змогу виробляти порівняно швидкі й недорогі випробування тугоплавких сплавів на горячеломкость.
3. У третій групі проб показником опірності освіти тріщин є критична навантаження затвердевающий зразок. Тут можна назвати дві підгрупи: проби із заздалегідь доданої постійної навантаженням і проби, у яких усадка гальмується безупинно зростаючій навантаженням (пружиною). У пробах із постійною навантаженням всю її швидко передається на зразок, коли починається лінійна усадка. У той самий час у виробничих отливках усадочные напруги виникають поступово з розвитком затруднённой усадки. Тому цілком логічно використання проб, у яких усадка гальмується пружиною і навантаження безупинно зростає від нуля до деякою критичної величини в останній момент освіти тріщини. Ця деталь відзначається по появі максимуму на кривою «усилие.
[pic].
Див. Мал.7 Мідна форма для проби Хала сопротивления усадки — час", бо за освіті тріщини зусилля остаточно (за повної розриві) чи тимчасово падає. У цих методів лежить схема досвіду Бриггса і Гезелиуса (малюнок 8), измерявших зусилля, яке виникало під час гальмування усадки зразка пружиною. Зразок в вигляді стрижня заливається в піщану форму, в порожнину якої із двох торців вставлені шпильки. Одна шпилька жорстко укріплена в опоке, іншу з'єднана з пружиною. Затвердевающий метал «схоплює» шпильки, і живий взірець з однієї торця виявляється жорстко що з опокой, і з іншого — сполученим через шпильку з пружиною, що робить усадку затруднённой. Навантаження на зразок вимірюється по прогибу пружини з допомогою механічного індикатора, проградуированного в одиницях силы.
Результати досліджень з допомогою приладів, у яких усадка гальмується пружиною, сильна мірою залежить від жёсткости пружини. Чим жорсткіше пружина, то швидше по закінченні заливання утворюється тріщина і тих менші надходження до народних обранців навантаження. Отже, абсолютне значення критичної навантаження залежить тільки від властивостей сплаву, а й від жёсткости пружини. Особливо важливим є те, що жёсткость пружини по-різному б'є по критичної навантаженні, певній різними сплавах. Через війну можна отримати різну залежність опірності освіті тріщин від складу. Так, зі збільшенням жёсткости пружини, у низці сплавів Fe — З сталь з 0.2% З з найменш горячеломкой стає найбільш горячеломкой.
Було виявлено, що за наявності у сплаву предусадочного розширення, в виробничих отливках стрижень, дедалі ширший при заливанню металу, чинить опір усадки щойно вона починається, а установці з пружиною навантаження прикладається до зразком із запізненням. Зумовлено останнє тим, що під час предусадочного розширення пружина з цього становища oa вигинається у безвихідь oc, а від початку усадки, коли він повертається у початкове положення, зразок не навантажений (малюнок 3). Зразок навантажується тільки тоді, як пружина проходить через вихідне становище oa і відхиляється у безвихідь ob. Через холостого ходу пружини критична навантаження залежить від величини предусадочного розширення, й одержують результати випробувань іноді розходяться з виробничим досвідом та оцінкою горячеломкости по пробам, які належать до першим двом группам.
Однією з показників горячеломкости є відносна кількість тріснутих виливків. Такий спосіб незручний в лабораторних умовах, оскільки достовірні дані можна отримати роботу лише за велику кількість повторних заливок. У той самий час у заводських умовах, як під контроль потрапляють сотні виробничих виливків, статистичний метод оцінки горячеломкости за відносною числу тріснутих виливків дає дуже гарні результаты.
[pic].
Див. Мал.8 Схема досвіду з гальмуванням усадки пружиной Была також зроблено спробу оцінити горячеломкость за величиною мінімальної твердості стрижневою суміші, починаючи з якої у кільцевої литві з’являються тріщини. Цю методику не знайшла застосування, оскільки виявилася малочувствительной і незручною в исполнении.
Ось ще одне приклад виміру горячеломкости. Зразки як брусов відливалися в піщану форму, в порожнини якої з торців були вставлені шпильки. З самого торця шпилька, «схватываемая» затвердевающим металом, жорстко з'єднувала кожен зразок з опокой, і з іншого торця шпилька вільно проходила через отвір в опоке. На кінці шпильки із зовнішнього боку опоки була насаджена гайка, і зазор з опокой дозволяв проходити вільної усадки зразка. Величина цього зазору, отже, і рівень труднощі усадки встановлювалися заздалегідь і було різними для різних зразків. Горячеломкость оцінювалася по критичної величині зазору, відповідної появі тріщин. Розглянута проба виявилася малочувствительной й надалі не знайшла применения.
Жодна з проб може бути визнана універсальної і придатної на вирішення будь-яких завдань, що з вивченням горячеломкости при лиття. Такий універсальної проби, очевидно, взагалі неможливо розробити, хоча б оскільки у одному досвіді принципово не можна відтворити умови різних способів лиття (в піщану форму, в кокіль, безперервного тощо.) За позитивного рішення різних завдань висуваються різноманітні і часто протилежні вимоги до пробі на горячеломкость.
4. ХАРАКТЕРИСТИКА ДЕЯКИХ АЛЮМІНІЄВИХ СПЛАВОВ.
1. Сплави з урахуванням системи алюміній — кремній Сплави Al — Si є распространёнными ливарними алюмінієвими сплавами. Це з хорошим комплексом ливарних властивостей. Эвтектическая точка (11,7% Si) з діаграми стану (малюнок 9) зміщена до чистого Al, тому основою эвтектики ?+Si є? — твёрдый розчин. Якщо виділення кремнію в эвтектике перебуває у вигляді великих утворень, то пластичність сплаву різко погіршується зі збільшенням частки эвтектики в структуре.
Модифікування натрієм (використовуються також Li, K, Sr) різко змаліє включення кремнію в эвтектике, внаслідок підвищується комплекс пластичних властивостей, що, своєю чергою, призводить до відсутності схильності до утворення гарячих тріщин. Невелика кількість тендітного кремнію в эвтектике і модифікування структури використовувати сплави з найкращим комплексом ливарних властивостей (сплав АЛ2 (АК12)). Доэвтектические сплави з 5−9% Si та інші добавками також знаходять широке застосування (АЛ4 (АК9ч), АЛ9 (АК7ч)). У подвійних сплавах Al — Si, які отримали назву прості силумины, через відсутність интерметаллидов ефект зміцнення від виділення вторинних фаз дуже незначний і немає практичного значення. У неперервному зв’язку з цим подвійні сплави ставляться до термічно не упрочняемых і мають невисокими прочностными свойствами.
Домішки заліза в сплавах Al — Si утворюють складне з'єднання? (Al — Fe — Si) як тендітних пластин, які різко знижують пластичність. Негативний вплив заліза ефективно знижує добавка 0.2 — 0.5% Mn. У присутності марганцю замість? (Al — Fe — Si) утворюється фаза? (Al — Fe — Si — Mn) як компактних равноосных полиэдров, меншою мірою які впливають пластичність. Механічні властивості силуминов помітно відрізняються що за різних засобах лиття, наприклад, при лиття в піщану форму механічні властивості гірше, ніж при лиття в кокіль або за лиття під тиском. Пояснюється це тим, що вища швидкість кристалізації призводить до подрібненню структурних составляющих.
Сплав АЛ2(АК12) (11.7% Si) — єдиний промисловий подвійний сплав системи Al — Si. Він характеризується невисокими механічними властивостями, які залежно та умовами лиття і дрібних розмірів перерізу виливки сильно коливаються. Эвтектический склад сплаву (10 — 13% Si) — забезпечує йому відмінний комплекс ливарних властивостей: найвищий жидкотекучесть серед усіх алюмінієвих сплавів, відсутність схильність до освіті тріщин и.
[pic].
Див. Мал.9 Діаграма стану Al — Si пористости. З сплаву отримують щільні, герметичні виливки з концентрованої усадочной раковиною. Лінійна усадка вбирається у 0.8%. Сплав широко використовується всім способів лиття на різноманітні форми, застосовується у модифікованому стані, без термічної обробки. АЛ2(АК12) характеризується високої коррозионной стійкістю. Сплав АЛ2(АК12) застосовують особливо широко для лиття під тиском, і навіть для великогабаритних отливок.
1.4.2. Сплави з урахуванням системи алюміній — мідь Для аналізу структуроутворення в ливарних сплавах Al — Cu використовується ділянку діаграми стану від Al до першого хімічного сполуки? (CuAl2) (малюнок 10).Отметим ряд особливості діаграми состояния:
1. Значна гранична розчинність в твердому стані (Cp =.
5.65% Cu) і її швидке зменшення зі зниженням температури визначають можливість упрочняющей термічної обробки сплавов.
(гарт + старіння). Упрочняющей фазою є дисперсні вторинні виділення CuAl2. Частина міді зберігається у твердому розчині і додатково упрочняет сплав по растворному типу. Підвищена міцність і жаропрочность — основні гідності сплавів Al — Cu.
2. Эвтектическая точка зрушена до интерметаллиду (Cэ = 33%), тому эвтектика понад половину (за обсягом) складається з тендітного і твердого сполуки CuAl2. Через війну сплави эвтектического складу (з найкращими ливарними властивостями) не придатні для використання через високе тендітності. З іншого боку, значне зміст міді призводить до помітному збільшення щільності: від 2.7 для чистого Al до 3.3 г/см3 для сплаву з десятьма% Cu. Зазначені обставини обмежують концентрацію добавок міді в ливарних сплавах з нижньої боку 1.0 — 1.5% (задля забезпечення достатнього растворного зміцнення), з верхньої боку 6 — 8% (щоб уникнути зайвої тендітності через освіти CuAl2).
3. Невисока температура плавлення эвтектики (tэ = 548 °З) разом із великим значенням Порівн призводить до утворення з промисловою сплавах широкого інтервалу кристалізації (? tкр? 100 °C).
Такі сплави відрізняються зниженою жидкотекучестью, схильністю до пористости й освіті гарячих тріщин, у яких сильно розвинена сегрегація; нерівноважна эвтектика проявляється вже за часів 1.5 — 2.5% Cu. Отже, з прикладу сплавів Al — Cu ми зустрічаємося із характерною ситуацією, коли щоб одержати необхідного комплексу механічних властивостей доводиться пожертвувати ливарними технологічними свойствами.
[pic].
Рис. 10 Частина діаграми стану Al — Cu.
Сплав (АЛ7) (Cu 4.5%) упрочняется по растворному типу, і навіть рахунок дисперсних виділень фази CuAl2. З іншого боку, домішки заліза і кремнію утворюють нерозчинні залізовмісні фази, котрі виділяються як ободків на межі дендритных осередків. Термічна обробка залежить від загартуванню від 515 °C у гарячій води та штучному старінні при 150 °C протягом 2 — 4 годин. Сплав АЛ7 має підвищену усадку (1.4%), схильний до утворення гарячих тріщин і тому рекомендується для лиття на кокіль. Він застосовується для лиття середньо навантажених деталей, невеликих по размеру.
Сплав АЛ19 (АМ5) (Cu 4.9%; Mn 0.8%; Ti 0.2%). Марганець і титан утворюють складні интерметаллидные фази: Ti (Al12Mn2Cu) і TiAl3 (домішки заліза жорстко обмежені). Ці фази що з CuAl2 формують твёрдый каркас по кордонів дендритных осередків і надають сплаву підвищену жаропрочность. Термічна обробка відрізняється вищими температурами (гарт від 545 °C, старіння при 175°С). Порівняно високий вміст міді в сплаві (до 5.5%) призводить до освіті в литом стані нерівновагової потрійний эвтектики. У зв’язку з цим нагрівання при загартуванню проводять східчасто — і при 530 °C для розсмоктування нерівновагової эвтектики. Це типовий прийом при термічної обробці низки ливарних сплавів, схильних до сильної дендритной ликвации. Нижче наведені значення тривалої (100ч.) міцності деяких Al ливарних сплавів за нормальної температури 300 °C (таблиця 3):
Таблица 3.
|Сплав |АЛ8 |АЛ2(АК12) |АЛ4(АК9ч) |АЛ7 |АЛ5(АК5м) | |? 100, | | | | | | |Мпа |15 |25 |30 |30 |65 |.
По цих показників сплави системи Al — Cu значно переважають сплави системи Al — Si. Усі сплави Al — Cu мають знижену проти іншими алюмінієвими сплавами коррозионную стійкість і потребують ретельної захисту від корозії шляхом нанесення лакофарбових покрытий.
2. Сплави системи алюміній — кремній — мідь Цю систему немає потрійних сполук, а фази? , CuAl2 і Si утворюють потрійну эвтектику складу 63.50% Al, 31.5% Cu, 5% Si з температурою плавлення 525 °C, що часто-густо є у промислових сплавах (АЛ6, АЛ12). Сплави типу силумін незалежно кількості споживаного кремнію зберігають в? — твердому розчині досить багато міді (від 4.75 до 5.5%), в нас саме зміст кремнію в потрійному? — твердому розчині коливається від 0.1% до 1.5%. Найтиповішими представниками потрійних сплавів системи Al — Si — Cu є сплав АЛ6, який широко використовується для виготовлення приладів та агрегатів. АЛ6 має найкращими механічними властивостями, але гіршими ливарними, ніж нормальний силумін. Застосовується в литом стані без термічної обработки.
ГЛАВА 2. ЕКСПЕРИМЕНТАЛЬНА ЧАСТЬ.
1. МЕТОДИКА ПРИГОТУВАННЯ ДОСВІДЧЕНИХ СПЛАВОВ Для приготування досвідчених сплавів використовувалася електрична піч опору шахтного типу потужністю 10 кВт з выемным графито — шамотовым тиглем ёмкостью 10 марок. Як шихтовых матеріалів использовались:
1. Al чушковой марки А99.
2. Силумін чушковой Сил 00.
3. Электролитическая мідь марки М 00.
4. Лигатура подвійна Al — Ti чи сіль K2TiF6.
5. Лигатура подвійна Al — Zr чи сіль K2ZrF6 Спершу тигель завантажувався Al і саме його розплавлювання, за нормальної температури 760° З, послідовно вводилися мідь і силумін. Що стосується застосування модифікаторів, насамперед вводилися відповідні лигатуры чи солі, за нормальної температури 780° З. Склад отриманих сплавів контролювався хімічним аналізом. Температура заливання металу становила 700° З. Контроль температури здійснювався з допомогою термопари хромель — алюмель (ХА).
Метал розливався в заздалегідь приготовлені форми спеціальних технологічних проб визначення горячеломкости.
2.2. ДОСЛІДЖЕННЯ ГОРЯЧЕЛОМКОСТИ СПЛАВІВ СИСТЕМ Al — Si, Al — Cu, Al — Si — Cu ПО ПОКАЗАННЯМ ТЕХНОЛОГІЧНИХ ПРОБ Для оцінки горячеломкости сплавів системи Al — Si було обрано концентрації 0.25, 0.5,1.0, 1.5, 2.0, 3.0, 5.0% Si. Були выплавлены відповідні склади досліджуваних сплавів і відлиті технологічні проби. Загальний вид виливки по кільцевої пробі показаний малюнку 11.
На малюнку 12 представлена крива зміни горячеломкости сплавів системи Al — Si залежно від змісту другого компонента. Очевидно, що максимум горячеломкости відповідає сплаву, який містить 0.25% Si. При подальшому збільшенні концентрації кремнію горячеломкость знижується й при змісті більш 2% стає рівної нулю. Зниження горячеломкости завдяки зменшенню лінійної усадки в інтервалі кристалізації (внаслідок збільшення кількості рідкої фази, кристаллизующейся при постійної температурі). Збільшення кількості эвтектики в сплаві створює також сприятливі умови для интердендритного харчування і, отже, для залечивания виникаючих тріщин рідиною эвтектического состава.
Рис. 11 Виливок технологічної проби на горячеломкость.
[pic].
Рис. 12 Зміна горячеломкости сплавів системи Al — Si.
На тому самому малюнку (12) наведено значення горячеломкости сплаву, що містить 0.25% Si з добавкою модифікатора, за який використовувався Zr у кількості 0.1%. Очевидно, що модифікатора не впливає на зниження горячеломкости.
На малюнку 13 представлено зміна горячеломкости сплавів системи Al — Cu залежно від змісту міді. Максимальної горячеломкостью має сплав, у якому 0.5% Cu.
Модифікування сплаву даного складу як і, як і попереднього разі, не призводить до зниження горячеломкости.
При збільшенні змісту міді у цій системі після точки максимальної горячеломкости зниження горячеломкости протікає більш помірковано, ніж у системі Al — Si. Після деякого зниження, при змісті міді, рівному 4%, знову спостерігається збільшення горячеломкости, і тільки при концентраціях міді вище 4% має місце помітне зниження горячеломкости. Поява другого максимуму горячеломкости пояснюється тому випадку розвитком зворотної ликвации (микроструктурный аналіз показав, що у кільцевих пробах серцевина сильно збіднена міддю, а поверхневі шари збагачені нею по порівнянню із нормальною структурою сплава).
У потрійний системі Al — Si — Cu (малюнок 14) зі збільшенням концентрації кремнію і міді істотне зниження схильність до освіті гарячих тріщин після досягнення максимуму горячеломкости (42.5 мм) обумовлюється переважно впливом кремнію (освітою эвтектической складової). Вже за змісті обох легуючих елементів у кількості вище 3%, горячеломкость знижується рівня (15−22.5 мм), що дозволяє гарантовано отримувати позбавлені гарячих тріщин складні по конфігурації виливки методами лиття на постійні металеві формы.
Ефективний інтервал кристалізації при додаванні до чистого металу другого компонента зростає, сягає максимуму на концентрационной кордоні появи эвтектики і далі поступово зменшується нанівець у точці збіги температури початку лінійної усадки з эвтектической горизонталлю. Горячеломкость тим більше коштів, що більше ефективний інтервал кристалізації, і тому склад сплаву повинен збігатися з кордоном появи эвтектики. Це становище зіграло значної ролі до вивчення залежності горячеломкости від складу, бо вона дозволило зв’язати опірність сплавів освіті тріщин з діаграмою стану й у першому наближенні, передбачити область складів найбільш горячеломких сплавів. Поява эвтектики і розподіл її на межі кристаллитов в вигляді тонких прошарків істотно охрупчивает сплав, знижуючи його механічні властивості, і, отже, його спроможність опиратися які виникають напругам. З іншого боку, у сплавів з найбільшим ефективним інтервалом кристалізації лінійна усадка у тому інтервалі отримує максимальное.
[pic].
Рис. 13 Зміна горячеломкости сплавів системи Al — Cu.
[pic].
Рис. 14 Зміна горячеломкости в сплавах системи Al — Si — Cu.
развитие і максимальні напруги. У досліджуваних сплавів максимальної горячеломкостью мають сплави наступних складів: Al — Si 0.25, Al — Cu 0.5, Al — Si 0.25 — Cu 0.25. Величина горячеломкости цих сплавів різниться незначно й у межах 37.5 — 42.5 мм за показниками використовуваної кільцевої технологічної пробы.
Модифікування найбільш горячеломких сплавів титаном і цирконієм або надає, або надає незначне впливом геть зниження горячеломкости цих сплавів. Певне послаблення горячеломкости (сплав потрійний системи) можна пояснити тим, що з подрібнюванні зерен зростає кількість стиків з-поміж них, але це своєю чергою збільшує міцність їхнього нерозривного зв’язку. З іншого боку, з'єднання зерен між собою відбувається за більшій кількості твердої фази, отже, лінійна усадка отримує пізніший розвиток виробництва і до кінця кристалізації сягає менші за розміром, ніж в немодифицированного сплаву. Проте, ці дві чинника, очевидно, неспроможні значною мірою компенсувати виникаючі високі за своїм значенням усадочные напруги при кристалізації цих сплавов.
Вивчення мікроструктури показало, що характер виникнення і розвитку гарячих тріщин всіх досліджуваних сплавів приблизно однаковий, особливо в малих концентраціях легуючих елементів. Гарячі тріщини розгортаються за прошаркам эвтектической складової сплаву, располагающимся на межі зерен. При дуже високому вмісті легуючих елементів мікроструктура відрізняється кількістю і формою розподілу эвтектики. Як приклад малюнку 15 приведено мікроструктура сплавів системи Al — Si — Cu у місцях утворення та розвитку гарячих тріщин. На малюнку 15 чи 15 б представлена мікроструктура сплаву Al — Si 0.25 — Cu 0.25 відповідно немодифицированного (чи модифікованого (б). Структура цих сплавів характеризується незначним змістом легкоплавкой складової. Модифікований сплав має як дрібне зерно і більше тонке розподіл эвтектики на межі зерен. Таке розподіл эвтектики при невеличкому її кількості неспроможна сприятливо зашкодити горячеломкости і є причиною незначного дії модифікування на зниження горячеломкости. Подальше підвищення змісту кремнію і міді в сплаві до 1% не призводить до суттєвого зміни структури (малюнки 15 у і 15 р). Проте треба сказати, що з подальшим збільшенням змісту кремнію і міді в сплаві з’являється все більше эвтектической складової. Збільшення кількості рідкої фази до кінцю кристалізації призводить до затруднённой усадки, що у своє чергу призводить до збільшення пластичності сплаву у тому інтервалі кристалізації. До того ж, складаються сприятливі умови для залечивания тріщин эвтектической рідиною. На малюнках 15 буд і 15 е видно ділянки частково залікованих тріщин, але в малюнку 15 ж — повністю залеченная велика гаряча трещина.
а) б) в) г).
буд) е).
ж).
Рис. 15 Мікроструктура сплавів системи Al — Si — Cu з гарячими тріщинами: а) Si — 0.25, Cu — 0.25;б) Si — 0.25, Cu — 0.25 з модифікатором; в) Si — 0.5, Cu — 0.5;г) Si — 1.0, Cu — 1.0; буд) Si — 2.0, Cu — 2.0;е) Si — 3.0, Cu — 3.0; ж) Si — 4.0, Cu — 4.0.
2.3. МЕТОДИКА ПРОВЕДЕННЯ ДИФЕРЕНЦІАЛЬНОГО ТЕРМІЧНОГО АНАЛІЗУ ДОСЛІДЖУВАНИХ СПЛАВОВ Для підтвердження даних, отриманих методом дослідження досвідчених сплавів по кільцевої пробі, використали метод диференціального термічного аналізу, що дозволяє проаналізувати зміна темпу кристалізації сплавів і намагається пов’язати його зі зміною складу сплавов.
Установка для диференціального термічного аналізу (Д Т А) (малюнок 16) складається з нагрівальною електричної печі з тепловим екраном, які забезпечують ідентичність помещённого у ньому зразка і еталона. Гарячі спаи простий і диференціальної термопар кріпилися на зразку з допомогою прижимного устрою, що забезпечувало хороший контакт на протязі всього інтервалу кристалізації. Сигнал від термопар надходив на дзеркальні гальванометры типу М17. Відхилення дзеркальця фіксувалося по записи на фотопапері світлового зайчика. Основне перевагу даної системи — її мала інерційність. Використовувалися термопари групи ПХЕ, діаметр 0.5 мм, холодні спаи яких були термостатированы в посудині Дьюара з тающим льодом. Повна ідентичність гарячих спаев забезпечувалася їх виготовленням за загальним зрізу. Особливістю даної методики ДТА є регулювання чутливості гальванометров, яка забезпечувала окреслення диференціальної кривою єдиної площі (малюнок 17). Це дозволило оцінити теплоту плавлення образца:
Qпл. = ?ni=1 Si.
и визначити температурну залежність відносної теплоти на момент досягнення температуры:
ti = ?Q/Qпл.= ?i1 Si/?n1 Si? 100%.
В ролі еталона використовувалася электролитическая мідь, не яка має фазових перетворень буде в діапазоні досліджуваних температур. Маса еталона (mэт.) розраховувалася з умови рівності теплосодержащего еталон і образца:
mэт. = mобр.? Cобр. /Cэт.
де mобр. — маса зразка досліджуваного сплаву, Повне Зібр. і Сет. — питома теплоёмкость зразка і эталона.
Розрахунок відносної теплоти (?Q/Qпл.) і темпу плавлення? (?Q/?ti) вівся за площами диференціальної кривою термограммы, які были.
[pic].
Рис. 16 Принципова схема пирометра М. С. Курнакова 1 — диференціальний гальванометр; 2 — простий гальванометр; 3 — посудину Дьюара; 4 — диференційна термопара; 5 — проста термопара; 6 — зразок; 7 — эталон.
[pic].
Рис. 17 Термограма досвідченої плавки сплаву системи Al — Si — Cu.
получены при ДТА (рис.17). Під відносної теплотою розуміється відсоткове співвідношення теплоти, поглощённой на момент досягнення у зразку температури ti (?Qi), і кількості теплоти, поглощённому при расплавлении зразка (Qпл.). Відносна теплота? Q/ Qпл. визначалася зі ставлення площі, описаної диференціальної кривою на момент досягнення температури ti (?ni=1 Si) й Бессарабської площі, описаної диференціальної кривою за повної расплавлении зразка (досягнення температури tliq) (?ni=1 Si). Під темпом плавлення? розумілося ставлення зміни теплоти (?Qi), поглощённой в інтервалі температур, до величині цього інтервалу. Для спрощення розрахунків величина? ti вибиралася постійної і становить 10° З. За отриманими результатам було побудовано температурні залежності зміни відносної виробництва тепла й темпу плавлення, які можна інтерпретувати як кінетику освіти рідкої фази в кокильном зразку за його расплавлении чи як кінетику виділення твердої фази при затвердевании сплаву за умов лиття на кокіль. Саме цими даними і слід керуватися у процесі перевірки результатів дослідження вищевказаних сплавів методом кільцевої пробы.
2.4. АНАЛІЗ ПАРАМЕТРІВ КРИСТАЛЛИЗАЦИОННОГО ПРОЦЕССА Для аналізу кристаллизационного процесу було виконано ДТА сплавів системи Al — Si із вмістом Si: 0.25, 0.5, 1.0, 3.0 і 5.0%. Основні параметри кристаллизационного процесу зазначені у таблиці 4:
Таблиця 4. Параметри кристаллизационного процесу сплавів системи Al — Si.
|№ |Зміст |Теплота |tsol, °C|tliq, °C|tкр. | | |Si,% |кристалізації| | | | |1 |0.25 |-352.2 |627.4 |643.2 |15.8 | |2 |0.5 |-341.6 |627.0 |642.8 |15.8 | |3 |1.0 |-360.3 |551.6 |638.6 |87.0 | |4 |3.0 |-347.0 |550.0 |625.6 |75.6 | |5 |5.0 |-302.7 |549.0 |612.9 |63.9 |.
Дальнейший аналіз приведених даних показал:
1. Сплави, містять 0.25 і 0.5% Si, мають вузький інтервал кристаллизации.
(~16°C). На кривих ДТА тих сплавів не зафіксовано эвтектическое перетворення, тобто. теплове перетворення пов’язано тільки з кристалізацією ?-твердого розчину кремнію в алюмінії. Параметри кристаллизационного процесу цих двох сплавів практично одинаковы.
2. У сплавах із вмістом Si 1.0% і від зафіксована кристалізація эвтектической складової, причому що більше в сплаві кремнію, тим більше коштів эвтектики. Тому інтервал кристалізації цих сплавів значно більше, позаяк у цьому випадку беруть участь двоє перетворення — кристалізація твердого розчину і эвтектики, що протікає тих складових що за різних температурах. Привертає увагу те що, що зі збільшенням змісту кремнію з 1.0 до 5.0% інтервал кристалізації зменшується з 87 до 64° З. Це з тим, що зі збільшенням кремнію ликвидус сплавів піддається суттєвому зниженню, а солидус залишається практично незмінним, оскільки кристалізація цих сплавів завершується кристалізацією эвтектики (? + Si) при постійної температуре.
По кривим ДТА було спрямовано і графічно інтерпретовані криві зміни темпу кристалізації досвідчених сплавів (малюнок 18). Для сплавів 0.25 і 0.5% Si темп кристалізації збільшується практично лінійно і становить максимальних і великих по абсолютну величину значень у температури солидус. Аналогічно повинна розвиватись агресивно та лінійна усадка в інтервалі кристалізації, що сумарно з наявністю тонких прошарків рідкого металу між кристалами, які ослаблюють їх зв’язок, призводить до збільшення горячеломкости.
Характер зміни темпу кристалізації сплавів із вмістом кремнію від 1.0 до 5.0% істотно відрізняється. Досягнувши максимуму на початку кристалізації, коли лінійна усадка не отримала свого розвитку, темп кристалізації потім поступово знижується тільки з наближенням до температурі солидус. І лише в сплавів, містять 3.0 і 5.0% Si, поблизу температури солидус темп кристалізації знову кілька збільшується. Але це відбувається практично за незмінної температурі кристалізації эвтектической складової, коли лінійна усадка призупиняє своє розвиток виробництва і знову починає збільшуватися тільки після повного затвердіння сплаву. Такий характер кристалізації повинен сприятливо позначатися зниженні горячеломкости, що підтверджено результатами досліджень цього сплаву з допомогою кільцевої пробы.
[pic].
Рис. 18 Зміна темпу кристалізації сплавів системи Al — Si.
ВЫВОД.
У цьому роботі була вивчена проблема дослідження горячеломкости сплавів систем Al — Si, Al — Cu, Al — Si — Cu. Зокрема, було досліджувана вплив хімічного складу цих сплавів освіту гарячих тріщин, були наочно показані склади самих горячеломких сплавів і побудовано криві залежності горячеломкости від состава.
Зазначено впливом геть горячеломкость кількості эвтектической рідини в сплаві, у разі збільшення кількості эвтектической рідини спричиняє зростання запасу пластичності в твёрдо-жидком стані (через підвищення подовження в інтервалі тендітності і зменшення лінійної усадки), а також щодо збільшення интердендритного харчування, що зумовлює явища залечивания гарячих трещин.
Також виявлено, спроба модифікування найбільш горячеломких сплавів не дає бажаних результатів, мало впливаючи на зниження горячеломкости.
З метою підтвердження результатів, отриманих з допомогою кільцевої технологічної проби на горячеломкость, було виконано дослідження зміни темпу кристалізації. Побудовано графіки, дозволяють будувати висновки про залежності темпу кристалізації від складу сплавів і підтверджено взаємозв'язок темпу кристалізації із заснуванням гарячих тріщин. У разі результати дослідження із застосуванням методу ДТА (диференціального термічного аналізу) цілком підтверджували результати по горячеломкости, отримані з допомогою кільцевої пробы.
1. Новиков І.І. «Горячеломкость кольорових металів і сплавів» — Изд-во.
Наука, Москва 1966 г.
2. Новиков І.І., Золоторевский В. С., Портной В. К. Рб. «Алюмінієві сплави», вып.1 Ливарні сплави. — Оборонгиз, 1963 г.
3. Макарин В. С., Нікітін С.Л. Освіта гарячих тріщин в отливках/Методические вказівки до лабораторної роботу з курсу.
«Теоретичні основи ливарного виробництва». — друкарня МАТИ,.
1986 г.
4. Новиков І.І., Корольков Г. А., Семенов А.Є. Ливарне производство.
1958 г, № 1,7.
5. Новиков І.І., Корольков Г. А., Золоторевский В. С. — Рб. МИЦМиЗ.
«Металургія й технологія кольорових металів», вып.33, Металлургиздат,.
1960 г.
6. Бочвар А. А., Жадаева О. С. Ювілейний збірник праць Моск. Ін-та кольорових металів і золота, вып.9, Металлургиздат, 1940 г.
7. Новиков І.І., Золоторевский В. С., Лісовська Т. Д. Рб. «Дослідження сплавів кольорових металів» вып.4, Вид-во АН СССР, 1963 г.
8. Корольков А.І. Ливарні властивості металів і сплавів — Москва, Наука,.
1967 г.
9. Новиков І.І., Корольков Г. А. Спосіб усунення гарячих усадочных тріщин при кокильном лиття кольорових сплавів, О.С. 109 264 від 31 мая.
1957 г. 10. Добаткин В.І. Зливки алюмінієвих сплавів, Металлургиздат, 1960 р. 11. Могилёв В. К., Лев О. И., Колобнев І.Ф. Довідник ливаря -.
Москва, 1974 г. 12. ГОСТ 1583–89 Сплави алюмінієві ливарні. Технічні умови. Виду стандартів. Москва, 1993 р. 13. Нікітіна М. Ф., Нікітін С. Л. Ливарне виробництво, № 2, 1983 г.