Лиття
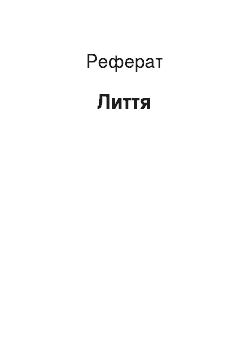
Расширяется сферу застосування лиття під тиском магнієвих сплавів. Поруч із використанням цих сплавів для корпусних деталей пишучих машинок, приладів, біноклів, фотоі кіноапаратури, бензопил вони успішно застосовують у авіаційної техніці для деталей, несучих певну навантаження. Наприклад, фірма Volkswagen (ФРН) виготовляє з магнієвих сплавів диски коліс спортивних автомобілів, а Мелітопольський… Читати ще >
Лиття (реферат, курсова, диплом, контрольна)
Литье
Введение
.
Процесс лиття під тиском має як ніж вікову історію. Головними його перевагами є можливість отримання заготовок з мінімальними припущеннями на механічну обробку чи ні неї й мінімальної шорсткістю необроблених поверхонь, забезпечення високої продуктивності і низької трудоёмкости виготовлення деталей.
В 1940 г. завод «Червона Пресня» виготовив машину мод. ЛД-7 із вертикальною камерою пресування — це були початком вітчизняних який буде необхідний лиття під тиском устаткування. Пізніше цим самим заводом освоєно виробництво машин із горизонтальним холодної камерою пресування. Машини подібного типу знайшли найбільшого поширення в промисловості. Це простотою і надійністю конструкції такий камери. Крім тою, в машинах із горизонтальним холодної камерою пресування втрати теплоти рідким металом і гідравлічне опір по дорозі його руху на порожнину прес-форми менше, ніж у машинах із вертикальною камерою, в результаті винятку литникового ходу. Це дозволяє знизити температуру заливання сплаву, зменшити пористість і зробити ефективну подпрессовку виливки по закінченні заповнення форми. Машини із горизонтальним камерою пресування мають вищу продуктивність, ніж машини із вертикальною камерою, так як поршень виштовхує пресс-остаток в останній момент розкриття прес-форми без додаткових витрат времени.
Отечественное машинобудування випускає машини з «холодною горизонтальній камерою пресування з натугою замикання 1000— 35 000 кН. Більшість сучасних машин має механізм пресування з мультиплікацією тиску робочої рідини під час подпрессовки.
Дальнейшее вдосконалення машин для лиття під тиском спрямоване шляхом підвищення швидкостей руху прессующего поршня з бесступенчатым регулюванням швидкості в різних етапах заповнення прес-форми за одночасного зниження гідравлічного удару в останній момент переходу від заповнення до подпрессовке. Вітчизняна промисловість випускає переважно машини лиття під тиском із холодної горизонтальній камерою пресування і автоматизовані комплекси і лінії їхній базі. Молдавське ПО «Точлитмаш» спеціалізується на випуску машин з натугою замикання до 6000 кН, а ПО «Сиблитмаш» — до 35 000 кН.
За кордоном машини лиття під тиском і автоматизовані комплекси їхній базі випускають фірми Vihorlat Snina (ЧССР), Litostroj (Югославія), фірма Buhler (Швейцарія), JDRA, Itallpress (Італія), Frech (ФРН), Ube, Toshiba (Японія), Lester, Gabler (США).
Сущность лиття під давлением.
Выполняют машинним способом в металеві форми, звані пресс-формами. Заповнення металом прес форми здійснюють її змикання через литниковые канали, які з'єднують робочу порожнину прес-форми з камерою пресування машини для лиття під тиском. Зовнішні обриси виливки утворюються робочої поверхнею зімкнутій прес-форми, а внутрішні отвори та порожнині отримують з допомогою металевих стрижнів, які беруть із затверділої виливки в останній момент розкриття прес-форми. Стрижні мають механічно привід як рейок, шестерні, зубатих секторів, клинів, эксцентриков, кинематически що з механізмом розкриття прес формы.
Металл заливають до камери пресування і запрессовывают всередину робочої порожнини прес-форми. Після кристалізації виливки відбувається розкриття прес-форми для вилучення виливки, у своїй окрема частка продовжує залишатися нерухомій, інші ж частини відводяться гідроприводом. Виливок утримується в рухомий частини й переміщається із нею до зустрічі з выталкивателями, які виштовхують відливку з рухомий частини прес-форми. Виливок то, можливо залучена з розкритою прес форми з допомогою маніпулятора чи робота. Щоб запобігти зварювання робочої поверхні прес-форми з виливком і полегшення вилучення виливки порожнину прес-форми покривають складами як паст чи распыляющих рідин, містять порошки металів, графіт, сульфід молибдена.
Преимущественно використовують сплави на основі міді, алюмінію, цинку, свинцю, сурми, які мають незначне теплове вплив на прес-форми. Розпал і деформація прес-форм призводять до втрати точності й діють чистоти поверхні виливків. Задля збереження сталості розмірів прес-форми роблять водоохлаждение. Останнім часом дедалі ширше починають використовуватися тугоплавкі сплави, наприклад, стали, потребують дуже дорогих прес-форм з жаропрочными вставками з сплавів з урахуванням молібдену. Внутрішні порожнини в відтинках повчають з допомогою латунних стрижнів. Після кристалізації сталевої виливки латунний стрижень залишається всередині неї, при высокотемпературном отжиге він виплавляється з виливки, залишаючи по собі полость.
Опивки, отримані литьём під тиском, відрізняються чистотою поверхні і є точністю, відповідної 4 класу. Допуски на розміри перебувають у межах від ±0,075 до ±0,18 мм. Виливання під тиском економічно доцільно для крупносерійного й масового виробництва точних виливків з легкоплавких сплавів. Трудоёмкость виготовлення виливків литьём під тиском в ливарних цехах знижується в 10−12 раз, трудоёмкость механічної обробки знижується в 5−8 раз. Цей спосіб лиття знайшов широке використання у автомобільної, авіаційної, електротехнічній, приладобудівної, санитарно-технической галузях промышленности.
Часто виливки, виготовлені литьём під тиском, армируют для зміцнення. Конструктивні елементи з деяких інших більш міцних чи износостойких сплавів попередньо отримують механічної обробкою чи холодної листовий штампуванням і вкладають у пресс-форму перед заповненням її металом. При лиття рік тиском цинкових сплавів прес-форми витримують без руйнації та втрати точності 1 млн. заповненні металом, магнієвих сплавів — 250 тис. заповнень, алюмінієвих сплавів — 100 тис., мідних ставов — 5000 заполнений.
Процесс формування опивки проходить 3 етапу:
сплав із швидкістю (до 50 м/с) за короткий час (0,01 — 0,6 з) заповнює порожнину прес-форми, переміщуючись з повітрям і парами мастила, які у порожнини форми, створюючи металловоздушную смесь;
в момент закінчення заповнення прес-форми відбувається короткочасний сильна гідравлічний удар, притискає метал до поверхні прес-форми, і поверховий верстви виливки (0,2 мм) виходить дуже щільним і мелкокристаллическим; рухлива половина прес-форми під впливом гидроудара відходить і литві по разъёму прес-форми утворюється заусенец;
кристаллизация виливки приміром із великий швидкістю, що зумовлює недостатнього харчуванню виливки рідким расплавом, але дефектів усадочного походження на отливках немає, т. до. гази в порах перебувають під великим тиском і, розширяючись, сприяють повного заповнення порожнини прес-форми металом, підвищуючи точність виливки, проте механічні властивості металу і і його пластичність ухудшаются.
Газовые пори, які під щільною ливарної кіркою, неможливо виконувати термічну обробку виливків з кольорових сплавів, бо за високих температур гази розширюються і пори збільшують свій обсяг, створюючи бульки і вспучины лежить на поверхні виливків. Для зниження пористости виливків на практиці порожнину прес-форми і розплавлений метал вакуумируют чи повітря робочої порожнини прес форми заміщають киснем, який змішується з металом, а утворює тонкі окисные плівки лежить на поверхні виливки, не знижуючи її качества.
Машины для лиття під тиском бувають 2 типів — компресорні і поршневі. Найбільшого поширення набула отримали поршневі машини з «холодною й одержання гарячої камерою пресування. Гаряча камера пресування перебуває всередині тигля з розплавленим металом, а холодна — окремо від розплавленого металу і розташовується горизонтально чи вертикально. Сучасні машини для лиття під тиском мають повністю автоматизований робочий цикл з сучасним програмним управлінням, автоматизовані регулювання зусилля змикання прес-форм, зміна швидкості пресування, блокування вузлів у разі несправностей в машине.
Поршневые машини з «холодною горизонтальній камерою пресування (рис. 1, а) мають пресс-форму, що складається з 2 частин. Половина прес-форми 1 кріпиться до рухомий плиті машини, а половина 3 — до нерухомій 4. Стрижні, що утворюють порожнини в отливках, частіше перебувають у рухомий половині для зручності їхнього отримання з виливки. Рухлива полуформа 1 з великим зусиллям притискається до нерухомій 3. Потім доза рідкого металу 5 заливається до камери пресування 7 і впрессовывается плунжером 6 в робочу порожнину прес-форми 2. Після кристалізації сплаву рухлива частина прес-форми 1 відходить, і виливок выталкивателями 8, які кріпляться на плиті, розташованої за рухомий полуформой, виштовхується на конвеєр чи тару.
Общий вид машини для лиття під тиском із холодної горизонтальній камерою пресування наведено на рис. 1, р. Нерухома частина прес форми кріпиться до плити 4, а рухлива — до плити 3, яка переміщається по котрі спрямовують штангам 2 гідроприводом з рычажным механізмом. Запрессовывание металу у ливарну форму виробляється плунжером 5, що входить у камеру пресування, що у плиті 4 Плунжер 5 переміщається в осьовому напрямі гідроприводом 6. Гідросистема машини для плавності роботи II підтримки постійним високого тиску має отримувач 7. Усі механізми і агрегати машини об'єднані жорсткої станиною 8. На рис. 1 показано виливок блоку циліндрів, отримана машиною такого типа.
Поршневые машини з «холодною вертикальної камерою пресування (рис. 1, б) мають прес форму, аналогічну за конструкцією прес формі попередньої машини, що складається з рухомий частини 1 і нерухомій 3, але метал вступає у неї з вертикальної камери 6. У камері пресування 6 переміщаються верхній плунжер 4 і нижня п’ята 7. Верхній плунжер виходить поза межі камери пресування, а отвір заливається доза металу 5 на поверхню п’яти 7, яка перекриває отвір литниковой системи 8, з'єднуюче робочу порожнину 2 прес-форми з камерою пресування 6. Потім верхній плунжер 4 починає стискати метал, й під цим тиском п’ята 7 опускається і це відкриває отвір литниковой системи 8. Метал під великим тиском і із швидкістю впорскується в робочу порожнину 2 прес-форми.
.
.
Рис 1. Схеми процесів й престижний автомобіль для лиття під давлением.
а — із горизонтальним холодної камерою пресування, б — із вертикальною холодної камерою пресування, в — із гарячою камерою пресування; р — машина із горизонтальним холодної камерой.
Для створення надлишкового тиску необхідна доза металу, кілька велика, ніж потрібно виливки, тому між верхнім плунжером і п’ятої залишається прес залишок як циліндра. При піднятті верхнього плунжера нижня п’ята також починає підніматися вгору, зрізує прес залишок і виводить його з межі камери пресування, та був опускається в початкове положення (до перекриття отвори литниковой системи). Рухлива частина прес форми 1 відходить, і виливок витягається з допомогою выталкивателей 9. Після вилучення виливки і закриття прес-форми цикл повторюється знову.
Поршневые машини із гарячою камерою пресування (рис. 1, в) оснащені тигельної піччю 9, у якій протягом робочого зміни перебуває розплавленим метал 7. Сама камера пресування 8 вміщена в тиглі у розплавленому металі. Коли прессующий плунжер 6 піднято, то розплавлений метал через отвори в камері заповнює її, а при русі плунжера 6 вниз перекриваються впускні отвори і метал під тиском вступає у робочу порожнину 2 прес-форми, приєднаної до камери пресування через перехідною мундштук 5. Після кристалізації сплаву в порожнини 2 рухлива полуформа 1 відходить, штовхачі 10 наштовхуються на нерухому плиту зв виливок виштовхується. Потім рухлива полуформа 1 стуляється з нерухомій 3, закріпленої на плиті 4, а плунжер 6 піднімається, камера 8 заповнюється з тигеля метллом 7, та циклу повторюється. На таких машинах можна одержувати дрібні й складні виливки з цинкових, олов’яних, свинцово-сурьмянистых та інших легкоплавких сплавов.
2. Виливання під низьким давлением.
Применяют щоб одержати великих тонкостінних корпусних заготовок з легкоплавких сплавів. Розплавлений метал 1 (рис. 2) з плавильного тигля 2, який нагрівається электронагревателями 3, під тиском інертного газу чи повітря 0,1—0,8 кгс/см2 (0,01—0,08 МН/м2) вичавлюють по металлопроводу 4 в робочу порожнину форми 5, де він кристалізується у просторі між формою 6 і стрижнем 7. Стрижень може бути зі звичайної стрижневою піщаної суміші. Тиск інертного газу має бути невисоким через ту причину, що загальна площа дзеркала розплавленого металу у тиглі 2 в багато разів більше площі металлопровода 4. Незначне переміщення металу у тиглі викликає високе піднесення рідкого металу всередині металлопровода і в ливарної формі. Після кристалізації виливки, тиск інертного газу знімається, ливарна форма, розкривається і з неї витягають відливку.
.
Рис. 2. Установка для лиття під низьким давлением.
3. Основні характеристики процесса.
При лиття під тиском основними чинниками, визначальними формування виливки, є тиск у камері пресування і пресс-форме, швидкість руху поршня і впуску рідкого металу у форму, параметри литниково-вентиляционной системи, температури що заливається металу і форми, режими змащування і охолодження робочої порожнини форми і камери прессования.
Совокупность таких параметрів, як тиск у потоці металу, швидкість руху металу, засунений, виникає внаслідок утрудненого видалення повітря і газоподібних продуктів згоряння мастильного матеріалу, утворює гідродинамічний режим формування виливки. Температури що заливається сплаву і форми, тривалість заповнення і подпрессовки, і навіть темп роботи визначають теплової режим процесса.
От правильного вибору технологічних режимів заповнення і подпрессовки, визначальних конструкцію прес-форми, тип і потужність машини для лиття під тиском, залежить якість отливок.
Гидродинамический режим формування отливки.
Создает кінетику заповнення, газовий режим форми, характер розподілу газових включень в литві і якість рельєфу її поверхні. Тиск серед металу виникає й унаслідок опору руху металу під час проходження його через тонкі перерізу порожнини прес-форми і обтіканні стрижнів, при поворотах, сужениях і расширениях потоку. Що стосується відсутності опору величина гідродинамічного тиску серед визначається противодавлением повітря і газів, видалення яких утруднено через неможливість виконання вентиляційних каналів великого сечения.
Чёткость оформлення рельєфу і шорсткість поверхні виливки залежить від кінетичній енергії потоку. У момент закінчення його руху створюється гидродинамическое тиск на стінки пресс-формы:
Рф = pм Vф где pм — щільність рідкого металу;
Vф — швидкість потоку в пресс-форме.
Высокая швидкість впускаемого потоку (швидкість впуску) відповідає отриманню тонкостінних великогабаритних виливків складних обрисів. Високі швидкості впуску і потоку в пресс-форме створюють у результаті швидкого переміщення прессующего поршня. Для подолання опору затвердевающей нього в тонких перетинах оформляющей порожнини, і навіть опору газів, залишених у литві, необхідно високе гідростатичний тиск. Воно передається від прессующего поршня через литниковый який досі живить канал. Чим пізніше затвердіє живильник, тим тривалішою від дію тиску. Процес передачі гідростатичного тиску в порожнину прес-форми називається подпрессовкой. Використання утолщенных живильників дозволяє здійснити подпрессовку і харчування виливки рідким металом під час кристалізації і тим самим усунути усадочные раковины.
Максимальное зусилля подпрессовки має розвиватися прессующим механізмом машини над початок затвердіння виливки, а майже відразу по закінченні заповнення пресс-формы.
Характер руху металу у оформляющей порожнини залежить від швидкості випуску, співвідношення товщини питателя і виливки, в’язкості й поверхневого натягу що заливається сплаву, теплових умов його стосунків з стінками прес-форми. За підсумками швидкісних киносъёмок процесу руху металу у прозорою пресс-форме встановлено, що з лиття з малими швидкостями випуску можливо заповнення навіть ламинарным потоком, зі середніми швидкостями — суцільне турбулентне заповнення. При високих швидкостях випуску потік розбивається, заповнення стає дисперсним. Проте заповнення порожнини форм ламинарным, турбулентним чи дисперсним потоком можливе лише за отриманні зразків чи виливки простий формы.
Большая частина виливків, які у машинобудуванні й приладобудуванні, має складну конфігурацію з стовщеннями, бобышками, припливами і переходами, тому навіть дисперсное заповнення в чистому вигляді спостерігається рідко. Реальне заповнення виливків складної конфігурації - послідовне перетворення дисперсного потоку, що утворився місці удару струменя об стіну фори, на суцільний турбулентной підпор.
Таким чином, частина порожнини форми заповнюється дисперсним потоком, а віддалені від питателя перерізу порожнини заповнюються суцільним турбулентним потоком. Співвідношення дисперсних і турбулентных потоків залежить від швидкості впуску, товщини виливки і труднощі конфігурації, головним чином числа поворотів в порожнини формы.
Тепловой режим процесу формування виливки при лиття під давлением.
Обеспечивает рухливість сплаву як і період заповнення форми, і у процесі подпрессовки. Він пов’язані з високої інтенсивністю теплового взаємодії рідкого металу зі стінками масивною пресс-формы.
Процесс охолодження металу можна розділити на 2 періоду. 1 — охолодження рідкого металу під час руху їх у литниковой системи та оформляющей рідини. Аналізуючи цей етап важливо правильно вибрати тривалість заповнення, щоб запобігти освіту неслитин, пористости і оксидних полон. 2 період — затвердіння металу після заповнення прес-форми. Аналізуючи цей етап необхідно створити умови для спрямованого затвердіння металу виливки. Дотримання принципів спрямованого затвердіння залежить від технологічності конструкції виливки, температури що заливається сплаву і температури пресс-формы.
Тепловой режим визначає як якість виливків, а й стійкість форми. Одне з основних причин руйнації поверхневих шарів матриць і пуансонов й поява на отливках про слідів розпалу формы—это виникнення температурних напруг у вкладці. Довговічність прес-форми, як за результатами досліджень У. Т. Рождественського, залежить від величини максимальних температурних напруг і коефіцієнта лінійного температурного розширення матеріалу прес-форми. Крім того, знижуючись через активного силового взаємодії між охлаждающимся сплавом і нагревающимися робітниками частинами формы.
Тепловой режим, визначальний умови формування виливки, пов’язані з високої швидкістю затвердіння рідкого металу, яка зростає при охолодженні форми водою чи терморегулирующей рідиною. Терморегулювання робочої порожнини прес-форми необхідне стабілізації і вирівнювання теплових умов у різних за товщині перетинах отливки.
Для забезпечення свариваемости окремих потоків металу до його затвердіння із метою попередження неслитин, пористости і оксидних полон тривалість заповнення має перевищувати частки секунд. Під час розробки теплового режиму велике значення має тут розрахунок тривалості заповнення форми. Як уже відзначалося вище, виливки складної конфігурації заповнюються послідовно дисперсно-турбулентным потоком. У цьому вся разі тривалість заповнення Тзап визначається за умови, що дисперсний характер руху відповідає першому періоду заповнення, а турбулентний — другому. За тривалістю заповнення, певної на підставі розгляду теплових умов у формі, підраховують технологічну швидкість прессования:
Vпр = mотл/(рм Fпр тзап) где mотл — маса виливки;
Fпр — площа поперечного перерізу камери прессования.
При створенні сприятливих теплових умов, які забезпечують збереження жидкотекучести металу у литниковых каналах та порожнині форми, особливо у найтонших її перетинах, можливо здійснити подпрессовку. Найбільш ефективно вона використовується машинами із горизонтальним камерою пресування. Подпрессовка у процесі кристалізації сплаву стискує газові включення, зменшує усадочную пористість і покращує структуру металла.
Эффективность подпрессовки залежить від тривалості досягнення максимального значення тиску у процесі кристалізації сплаву. Чим менший цей час, то вище її ефект. Сучасні гідравлічні схеми машин лиття під тиском дозволяють домогтися зниження часу подпрессовки до 0,016 з. З розрахунку гідродинамічного і теплового режимів процесу визначають параметри прессующего механізму машини лиття під тиском. Машини для лиття під тиском повинен мати механізм чи систему подачі робочої рідини в прессующий циліндр, що забезпечує заданий кінцеве тиск при подпрессовке. Найчастіше при цьому використовують мультиплицирующие механізми, що дозволяють як підвищити тиск, а й зменшити пікове тиск гідравлічного удара.
Раскрытие і закриття прес-форми здійснюються запирающим механізмом, який одночасно використовують і для виштовхування виливки. У середовищі сучасних конструкціях машин лиття під тиском застосовують замикаючі механізми чотирьох типів: гідравлічні, гидрорычажные, гидроклиновые і комбіновані (гидроклинорычажные).
Наиболее поширені гидрорычажные замикаючі механизмы.
4. Номенклатура виливків, отриманих литьём під давлением.
Литьё під тиском займає одне з чільних місць у ливарному виробництві. У виконанні вітчизняної й зарубіжної практиці цим чином отримують виливки, по конфігурації і розмірам найближчі до готовим деталей з цинкових, алюмінієвих, магнієвих і мідних сплавів. Виготовлення виливків зі сталі, чавуну, титанових та інших тугоплавких сплавів ще одержало широко він, що переважно низькою стійкістю котрі оформляють частин 17-ї та високої вартістю матеріалів для пресс-форм.
Производство виливків з алюмінієвих сплавів у різних країнах, становить 30—50% загального випуску (щодо маси) продукції лиття під тиском. Наступну за кількістю розмаїттям номенклатури групу виливків представляють виливки з цинкових сплавів. Магнієві сплави для лиття під тиском застосовують рідше, що їх схильністю до освіті гарячих тріщин і більше складними технологічними умовами виготовлення виливків. Проте треба сказати, що виливки з магнієвих сплавів майже 1,5 разу легше виливків з алюмінієвих сплавів і від обробляються різанням, причому магній не налипає лежить на поверхні сталевих прес-форм і приваривается до них. Одержання виливків з мідних сплавів обмежена низькою стійкістю пресс-форм.
Номенклатура випущених вітчизняної промисловістю виливків дуже різноманітна. В такий спосіб виготовляють литі заготівлі самої різної конфігурації масою від кількох основних грам за кілька десятків килограмм.
Современные конструкції машин лиття під тиском, створюють тиску метал до 800 МПа і швидкості пресування до 7 м/с, дають змогу одержувати великогабаритні складні по конфігурації виливки, наприклад блок циліндрів автомобіля «Москвич» масою 18,6 кг. Ці виливки виготовляють з сплаву системи алюминий—кремний—медь машиною з натугою замикання 20 000 кН. У отливках безліч литих отворів, товщина стінки 4—5 мм. Вони проходить випробування на герметичність при тиску 15 МПа. Пресс-форма на таку виливки важить близько 2 т. Застосування ефективної подпрессовки дає можливість отримувати дуже щільні герметичні деталі, такі, як алюмінієвий корпус опалювальної батареї. Заповнення цієї тонкостенной великогабаритною виливки металом супроводжується активним захопленням газів з порожнини прес-форми, проте високе тиск (вище 400 МПа) забезпечує високий рівень стискування повітряних і газових включень. Застосування такий виливки як знижує масу опалювальної системи, покращує теплообмін, заощаджує енергоресурси і метал, підвищує продуктивності праці знижує собівартість продукції, а й облагороджує интерьер.
Некоторые виливки мають складні криволінійні поверхні і є канали, які за заданих точності й діють шерехатості й економічної доцільності неможливо знайти виконані ніякими іншими засобами, інакше як литтям під тиском, наприклад голівка блоку циліндрів і диск вентилятора компресора. Ці виливки мають значну товщину стінки (до 12 мм), що дозволяє вживати спрямоване затвердіння, при збільшеною товщині питателя, що створює оптимальні гідродинамічні і теплові умови подпрессовки.
Разработанные у вітчизняній промисловості технологію й устаткування лиття під тиском дають змогу одержувати виливки, товщина стінки що у певних місцях дорівнює 1 мм, наприклад деталі фотоапаратури. На спеціально створеної спеціалізованої машині й з застосуванням вакууму, термостатирования форми та інших технологічних прийомів отримано виливки з товщиною стінки 0,6 мм.
Расширяется сферу застосування лиття під тиском магнієвих сплавів. Поруч із використанням цих сплавів для корпусних деталей пишучих машинок, приладів, біноклів, фотоі кіноапаратури, бензопил вони успішно застосовують у авіаційної техніці для деталей, несучих певну навантаження. Наприклад, фірма Volkswagen (ФРН) виготовляє з магнієвих сплавів диски коліс спортивних автомобілів, а Мелітопольський завод «Автоколірлив» — деталі мотора автомобілів. Литьём під тиском можна одержувати виливки із зовнішнього чи внутрішньої різьбленням: смушкові гайки і гвинти, колпачковые гайки з фігурними головками, штепсельні разъёмы. Лита різьблення також має як постійний профіль, що є негативним відбитком резьбовой вставки прес-форми, виконуваної з точністю, значно яка перевершує звичайну точність обробки на резьбонарезных верстатах. Якість поверхні литої різьби вище, ніж механічно нарізаною, оскільки робочі поверхні прес-форми шліфують і полірують. Литьём під тиском можна виготовляти виливки зі спеціальним різьбленням, яку практично неможливо бій, яку практично неможливо отримати іншим способом, наприклад прямокутну чи спіральну різьблення трикутного профілю для ниппелей, ввинчиваемых в гнучкі шланги.
Литьём під тиском можна одержувати виливки із різною арматурою зі сталі, чавуну, міді, бронзи та інших матеріалів. Армування виливків пустотелыми вкладками чи криволинейными трубками дає змогу отримувати канали та порожнині найскладнішої конфигурации.
Наряду з конструкторськими завданнями, армування допомагає розв’язати ряд технологічних проб ніж. Наприклад, використання арматури як холодильників дозволяє регулювати процес затвердіння масивних частин виливки. Армування виливків сталевими і чавунними елементами дає економію дефіцитних кольорових сплавів. Армоване виливання під тиском дозволяє у часто замінити складання окремих вузлів изделий.
Отливки з алюмінієвих, магнієвих і мідних сплавів, як і і виливки з чавуну, сталі та титанових сплавів, отримують на машинах з «холодною камерою пресування. Виливки з цинкових сплавів виготовляють переважно машинами із гарячою камерою прессования.
Отливки з цинкових сплавів найчастіше використав виробництві автомобілів і товарів народного споживання (дверні і меблеві замки, затискачі застібок «блискавка», деталі швейних машин). У автомобільну промисловість з цинкових сплавів виготовляють деталі приладів та декоративні деталі типу ручок, решіток, корпусів фар. Завдяки хорошим ливарним властивостями і високої механічної міцності цих сплавів їх можна робити великі й тонкостінні деталі. Наприклад, панель обличкування радіатора автомобіля Dodge (США) має багато 9 кг і довжину 1790 мм при товщині стінки 1,8 мм. У виконанні вітчизняної промисловості найбільшої деталлю з цинкового сплаву, виготовленої на машині із гарячою камерою пресування, є решітка радіатора автомобіля «Жигулі». Виливок має багато 2,7 кг, довжину 1054, ширину 270 мм середню товщину стінки 1,25 мм.
В час процес лиття під тиском розвивається у трьох напрямах, обумовлених конфігурацією виливків та вимогами до качеству:
литьё з низькими швидкостями впуску через товсті живильники, щоб забезпечити заповнення прес-форми суцільними потоками і ефективну подпрессовку; застосовують щоб одержати товстостінних виливків нескладної конфігурації, яких пред’являють високі вимогами з міці й герметичности;
литьё з високими швидкостями впуску через тонкі живильники із заснуванням дисперсного заповнення; застосовують щоб одержати тонкостінних виливків складної конфігурації, яких пред’являються високі вимогами з якості поверхні і є чіткості рельефа;
литьё зі середніми швидкостями випуску з освітою совмещённых турбулентных і дисперсних потоків; вимагає подпрессовки, застосовується щоб одержати виливків з нерівній завтовшки стінок, пористість зменшує установкою фільтрів, промывников чи зміною газового режиму пресс-формы.
В вона найчастіше щоб одержати виливків використовуються універсальні машини для лиття під тиском, але, виходячи з вимог до отливкам і з умов виробництва, можна застосовувати спеціалізовані машини лиття під тиском. Наприклад, машини з вакуумними пристроями, з пристроями для продувки кисню зі здвоєним поршнем, для лиття стали чи щоб одержати одній, дуже складної чи специфічною виливки, наприклад, машини для сходинки ескалатора, машини для заливання ротора електродвигунів.
Заключение
.
Важнейшей передумовою подальшого підвищення кількості виливків та ефективності лиття під тиском є створення автоматизованих комплексів, гнучких виробничих систем і роторних ліній лиття під тиском, гнучких автоматизованих производств.
Программами технічного переоснащення передбачається інтенсивне відновлення парку устаткування, застосування ЕОМ для управління процесами і виробництвом, жорсткість вимог техніки безпеки, поліпшення умов праці, підвищення уваги до охорони оточуючої среды.
Список литературы
«Литьё під тиском» Авт. Беккер, М. Л. Заславський, Ю.Ф. Ігнатенка, М.: МАШИНОБУДУВАННЯ, 1998.
«Экономические основи технологічного розвитку» І.Н. Васильєва, М.: МАШИНОБУДУВАННЯ, 1995.
«Технологии металів і конструкційні матеріали» під ред. Б.А. Кузьміна, М.: МАШИНОБУДУВАННЯ, 1989.