Обработка різанням
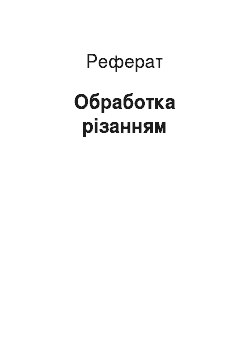
Основным ріжучим елементом будь-якого інструмента є ріжучий клин (рис. 1.1, а). Його твердість і міцність мають серйозно перевершувати твердість і міцність оброблюваного матеріалу, забезпечуючи його ріжучі властивості. До інструменту прикладається зусилля різання, однакову силі опору матеріалу резанию, і повідомляється переміщення щодо заготівлі зі швидкістю ?. Під впливом докладеної зусилля… Читати ще >
Обработка різанням (реферат, курсова, диплом, контрольна)
Обработка резанием
Обработка різанням універсальний методом розмірної обробки. Метод дозволяє обробляти поверхні деталей різної форми і середніх розмірів з точністю із найбільш використовуваних конструкційних матеріалів. Вона має малої енергоємністю і високої продуктивністю. У результаті обробка різанням є основним, найбільш які у промисловості процесом розмірної обробки деталей.
Сущность і схеми способів обработки
Обработка різанням — це процес одержання деталі необхідної геометричній форми, точності розмірів, взаєморозташування і огріхи поверхонь з допомогою механічного обрізання з поверхонь заготівлі ріжучим інструментом матеріалу технологічного припуска як стружки (рис. 1.1).
Основным ріжучим елементом будь-якого інструмента є ріжучий клин (рис. 1.1, а). Його твердість і міцність мають серйозно перевершувати твердість і міцність оброблюваного матеріалу, забезпечуючи його ріжучі властивості. До інструменту прикладається зусилля різання, однакову силі опору матеріалу резанию, і повідомляється переміщення щодо заготівлі зі швидкістю ?. Під впливом докладеної зусилля ріжучий клин врізується в заготівлю та, руйнуючи опрацьований матеріал, зрізує із поверхні заготівлі стружку. Стружка утворюється внаслідок інтенсивної упругопластической деформації стискування матеріалу, що призводить до його руйнації у що краючою крайки, і зрушенню у зоні дії максимальних дотичних напруг з точки ?. Розмір? залежить від параметрів різання і властивостей оброблюваного матеріалу. Вона становить ~30° до подання руху резца.
.
Внешний вид стружки характеризує процеси деформування і руйнувань матеріалу, що відбуваються при різанні. Розрізняють чотири можливих типу які виникають стружок: сливная, суставчатая, елементна і стружка надлому (рис. 1.1, б).
Рис. 1.1. Умовна схема процесу резания:
а — 1 — опрацьований матеріал; 2 — стружка; 3 — подача мастильно-охолоджувальних коштів; 4 — ріжучий клин; 5 — ріжучий край;? — кут зсуву, що характеризує становище умовної площині зсуву (П) щодо площині різання;? — головний передній кут ріжучого клину; Рz — сила різання; Рy — сила нормального тиску інструмента на матеріал; С? u, С? l — довжини пластичного і пружного контактів; С?, Сa — довжина зон контактного взаємодії по передній й задньої поверхням інструмента; LOM — область головного упругопластичного деформування при стружкообразовании; FKPT — область вторинної контактної упруго-пластичнеской деформації металу; h — глибина різання; М — товщина зони пластичного деформування (наклепа) металла.
В процесі різання ріжучий клин, відчуваючи інтенсивне тертя, контактує з матеріалом стружки і обробленою поверхнею в контактних зонах. Для зниження сил тертя і нагріву інструмента застосовують примусове охолодження зони різання смазочно-охлаждающими середовищами (SOS), подаючи до зони різання спеціальними устройствами.
Детали і навіть інструменти закріплюються у спеціальних органах верстата чи пристосуваннях. Верстат, пристосування, інструмент і деталь утворюють силову систему (СНІД), передавальну зусилля і рух різання від приводу верстата ріжучому інструменту і детали.
Реальные схеми різних способів опрацювання різанням, використовуваний інструмент, і навіть види руху інструменту та заготівлі у процесі опрацювання наведено на рис. 1.2. Залежно від використовуваного типу інструмента способи механічного оброблення поділяються на лезвийную і абразивную.
Рис. 1.2. Схеми способів обробки резанием:
а — гостріння; б — свердління; в — помел; р — стругання; буд — протягання; е — шліфування; ж — хонингование; із — суперфиниширование; Dr — головне рух різання; Ds — рух подачі; Ro — оброблювана поверхню; R — поверхню різання; Rоп — оброблена поверхню; 1 — токарському різець; 2 — свердло; 3 — фреза; 4 — строгальный різець; 5 — протяжка; 6 — абразивний коло; 7 — хон; 8 — бруски; 9 — головка.
.
Отличительной особливістю лезвийной обробки служить наявність у оброблюваного інструмента гострої що краючою крайки певної геометричній форми, а абразивною обробки — наявність по-різному орієнтованих ріжучих зерен абразивного інструмента, кожне у тому числі є микроклин.
Рис. 1.3. Конструкція і елементи лезвийных ріжучих инструментов:
а — токарського різця; б — фрези; в — сверла;
1 — головна ріжучий край; 2 — головна задня поверхню; 3 — вершина леза; 4 — допоміжна задня поверхню леза; 5 — допоміжна ріжучий край; 6 — передня поверхню; 7 — крепежная частина инструмента.
.
Рассмотрим конструкцію лезвийных інструментів, використовуваних при різанні (рис. 1.3). Інструмент складається з робочої частини, що включає ріжучі леза, що утворюють їх поверхні, ріжучі крайки і крепежной частини, настановленим встановлення і закріплення робочих органах станка.
Основными способами лезвийной обробки є гостріння, свердління, помел, стругання і протягання. До абразивною обробці ставляться процеси шлифования, хонингования і суперфиниша. У основу класифікації способів механічної обробки закладено вид використовуваного інструменту та кінематика рухів. Так було в ролі інструмента при точении використовуються токарні різці, під час свердління — свердла, при фрезеровании — фрези, при строгании — строгальные різці, при протягування — протягання, при шліфуванні - шліфувальні кола, при хонинговании — хоны, а при суперфинише — абразивні бруски. Будь-який спосіб обробки включає два руху (рис. 1.2.): головне — движене різання Dr — і допоміжне — рух подачі Ds. Головне рух забезпечує з'їм металу, а допоміжне — подачу до зони обробки наступного неопрацьованого ділянки заготівлі. Ці руху здійснюються з допомогою переміщення заготівлі чи інструмента. Тому, за оцінках рух інструмента переважають у всіх процесах різання зручно розглядати при нерухомій заготівлі як сумарне (рис. 1.4).
.
Рис. 1.4. Схеми визначення максимальної швидкості що краючою крайки інструмента ?е, форми поверхні різання R і глибини різання h при обработке:
а — гострінням; б — сверлением; в — фрезерованием; р — строганием; буд- простяганням; е — хонингованием; ж — суперфинишированием.
Тогда повна швидкість переміщення (ve) довільній точки Мрежущей крайки складається з швидкості головного руху (v) і швидкості подачі (vs):
ve = v + vs (1.1).
Поверхность різання R представляє собою поверхню, яку описує ріжучий край чи зерно під час здійснення сумарного руху, що включає головне рух і рух подачі. При точении, свердлінні, фрезеровании, шліфуванні поверхні різання — просторові линейчатые, при строгании і протягування — плоскі, збігаються з поверхнями головного руху; при хонин-говании і суперфинишировании вони збігаються з поверхнями головного движения.
Поверхности Ro і Roп називаються, відповідно, оброблюваної поверхнею заготівлі та обробленою поверхнею деталі (див. рис. 1.2).
В процесах точения, свердління, фрезерования і шлифования головне рух і рух подачі виконуються одночасно, а процесах стругання, хонингования рух подачі виконується після головного движения.
2. Параметри технологического процесса резания.
К основними параметрами режиму різання ставляться швидкість головного руху різання, швидкість подачі й глибина резания.
Скорость головного руху різання (чи швидкість різання) визначається максимальної лінійної швидкістю головного руху що краючою крайки інструмента. Ця швидкість виявляється у м/с.
Если головне рух різання обертальне, як із точении, свердлінні, фрезеровании і шліфуванні, то швидкість різання визначатиметься лінійної швидкістю головного руху найвіддаленішу осі обертання точки що краючою крайки — максимальної лінійної швидкістю головного руху (див. рис. 1.4):
v = ?D/2 (2.1).
где D — максимальний діаметр оброблюваної поверхні заготівлі, визначальний становище найбільш віддаленій від осі обертання точки що краючою крайки, м;? — кутова швидкість, рад/с.
Выразив кутову швидкість? через частоту обертання шпинделя верстата, одержимо:
v = ?nD (2.2).
При строгании і протягування швидкість різання v визначається швидкістю переміщення строгального різця і протягання у процесі різання щодо заготовки.
При хонинговании і суперфинишировании швидкість різання визначатиметься з урахуванням осьового переміщення (див. рис. 1.4, е, ж) инструмента.
Скорость різання надає найбільший вплив на продуктивність процесу, стійкість інструменту та якість обробленою поверхности.
Подача інструмента визначається її швидкістю vs. У технологічних розрахунках параметрів режиму при точении, свердлінні, фрезеровании і шліфуванні використовується поняття подачі на один оборот заготівлі So і полягає в мм/об. Подача на оборот чисельно відповідає переміщенню інструмента під час одного обороту:
So = vs / n (2.3).
При строгании подача визначається перебіг різця. При шліфуванні подача може указуватися перебіг чи подвійний хід інструмента. Подача на зуб при фрезеровании визначається числом зубів Z інструменту та подачею на оборот:
Sz = So / Z (2.4).
Глубина різання, А визначається відстанню по нормальний від обробленою поверхні заготівлі до оброблюваної, мм. Глибину різання задають за кожен робочий хід інструмента. При точении циліндричною поверхні глибину різання визначають як полуразность діаметрів до р: після обробки:
h = (Dur — d) / 2 (2.5).
где d — діаметр обробленою поверхні заготівлі, мм. Розмір подачі й глибина різання визначають продуктивність процесу мають вплив на якість оброблюваної поверхности.
К технологічним параметрами процесу належать геометрія ріжучого інструмента, сили різання, продуктивність обробітку грунту і стійкість инструмента.
Геометрические параметри ріжучого інструмента визначаються кутами, утвореними перетином поверхонь леза, і навіть становищем поверхонь ріжучих лез щодо оброблюваної поверхні, і напрямом головного руху. Зазначені параметри ідентичні щодо різноманітних видів інструмента, що дозволяє розглянути їх у прикладі різця, використовуваного при точении.
Углы різця по переднім і заднім поверхням вимірюють у певних координатних площинах. На рис. 2.1, а зображені координатні площині при точении, але в рис. 2.1, б кути різця в статике.
Главный передній кут? — кут між передній поверхнею леза і площиною, перпендикулярної до площині різання; головний задній кут? — кут між задньої поверхнею леза і площиною різання; кут заострения? — кут між передній й задньої поверхнями. З принципу побудови кутів слід, що.
? +? +? = ?/2.
Угол нахилу що краючою крайки X — кут у площині різання між що краючою кромкою і основний плоскостью.
Углы у плані: головний кут у плані? — кут в основний площині між слідом площині різання і напрямом подовжньої подачі; допоміжний кут в плані? «- кут в основний площині між допоміжної що краючою кромкою і обробленою поверхностью.
.
Рис. 2.1. Геометричні парамеры токарського резца:
а — координатні площині; б — кути різця в статике;
1 — площину різання Рп; 2 — робоча площину Рs; 3 — головна несуча площину Рt; 4 — основна площину Pv.
Геометрические параметри ріжучого інструмента істотно впливають на зусилля різання, якість поверхні, і знос інструмента. Тож з збільшенням кута у інструмент легше врізується у матеріал, знижуються сили різання, поліпшується якість поверхні, але підвищується знос інструмента. Наявність кута, а знижує тертя інструмента про поверхню різання, зменшуючи його знос, але надмірне його збільшення послаблює режущую крайку, сприяючи її руйнації при ударних нагрузках.
Силы різання Р є сили, які діють ріжучий інструмент у процесі упругопластической деформації і руйнувань срезаемой стружки.
Силы різання призводять до вершині леза або до точці що краючою крайки і розкладають по координатным осях прямокутної системи координат xyz (рис. 2.2). У цьому системі координат вісь z спрямована за швидкістю головного руху, і її позитивне напрям відповідає напрямку дії оброблюваного матеріалу на інструмент. Вісь у спрямована по радіусу окружності головного руху вершини. Її позитивне напрям також відповідає напрямку дії металу на інструмент. Напрям осі x вибирається з умови освіти правої системи координат. Значення зусилля різання визначається кількома чинниками. Воно зростає зі збільшенням глибини h різання і швидкості подачі p. s (перерізу срезаемой стружки), швидкості різання ?, зниженням переднього кута? ріжучого інструмента. Тому розрахунок зусилля різання проводиться у разі емпіричним формулам, які встановлені кожного способу обробки (див. довідники з обробки різанням). Наприклад, для стругання ця формула має вид Р = СphXpsYpXn де коефіцієнти Порівн, Хр, Yp, n характеризують матеріал заготівлі, різця й посвідку обработки.
Мощность процесу різання визначається скалярним твором:
N = Pve (2.6).
Выразив цей витвір через проекції по координатным осях, одержимо:
N = Pz vz + Pyvy + Pxvx (2.7).
.
где vx, vy, vz — проекції на осі координат швидкість руху точки докладання рівнодіючої сил різання. У практичних розрахунках використовується наближена залежність N = Pzv. Це спрощення обумовлена тим, що складові Ру і Рх повної сили різання малі проти Р2, а швидкість подачі щодо швидкості різання не перевищує 1 — 0,1%.
Рис. 2.2. Схема дії сил різання на режущую крайку інструмента у точці, має максимальну швидкість переміщення ?е, при обробці: а — гострінням; б — сверлением; в — фрезерованием; р — строганием; буд- простяганням; е — хонингованием; ж — суперфинишированием.
Производительность обробки при різанні визначається кількістю деталей, виготовлених в одиницю часу: Q = /Тт. Час виготовлення однієї деталі одно Тт = Т.ін + Тт + Ткп, де Те — машинне час обробки, затрачуване на процес різання, визначається кожному за технологічного способу; Тт — час підвода і відводу інструмента при обробці однієї деталі; Гвсп — допоміжне час встановлення і настройки инструмента.
Таким чином, продуктивність опрацювання різанням насамперед визначається машинним часом Т. е. При токарной обробці, хв: Те = La/(nsoh), де L — розрахункова довжина ходу різця, мм; а — величина припуска на обробку, мм.
Отношение a/h характеризує необхідну число проходів інструмента при обробці за глибиною різання І. Тому найбільша продуктивність буде за обробці за глибиною різання h = а, найбільшої подачею s0 і максимальною швидкістю різання. Проте за увеличениипроизводительности знижується качесто поверхні і є підвищується знос інструмента. Тому, за обробці різанням вирішується завдання для встановлення максимально припустимою продуктивності при збереженні необхідного якості поверхні, і стійкості инструмента.
Список литературы
[1] - Матеріалознавство й технологія металів. Під ред. Г. П. Фетисова М.: Вищу школу, 2001.